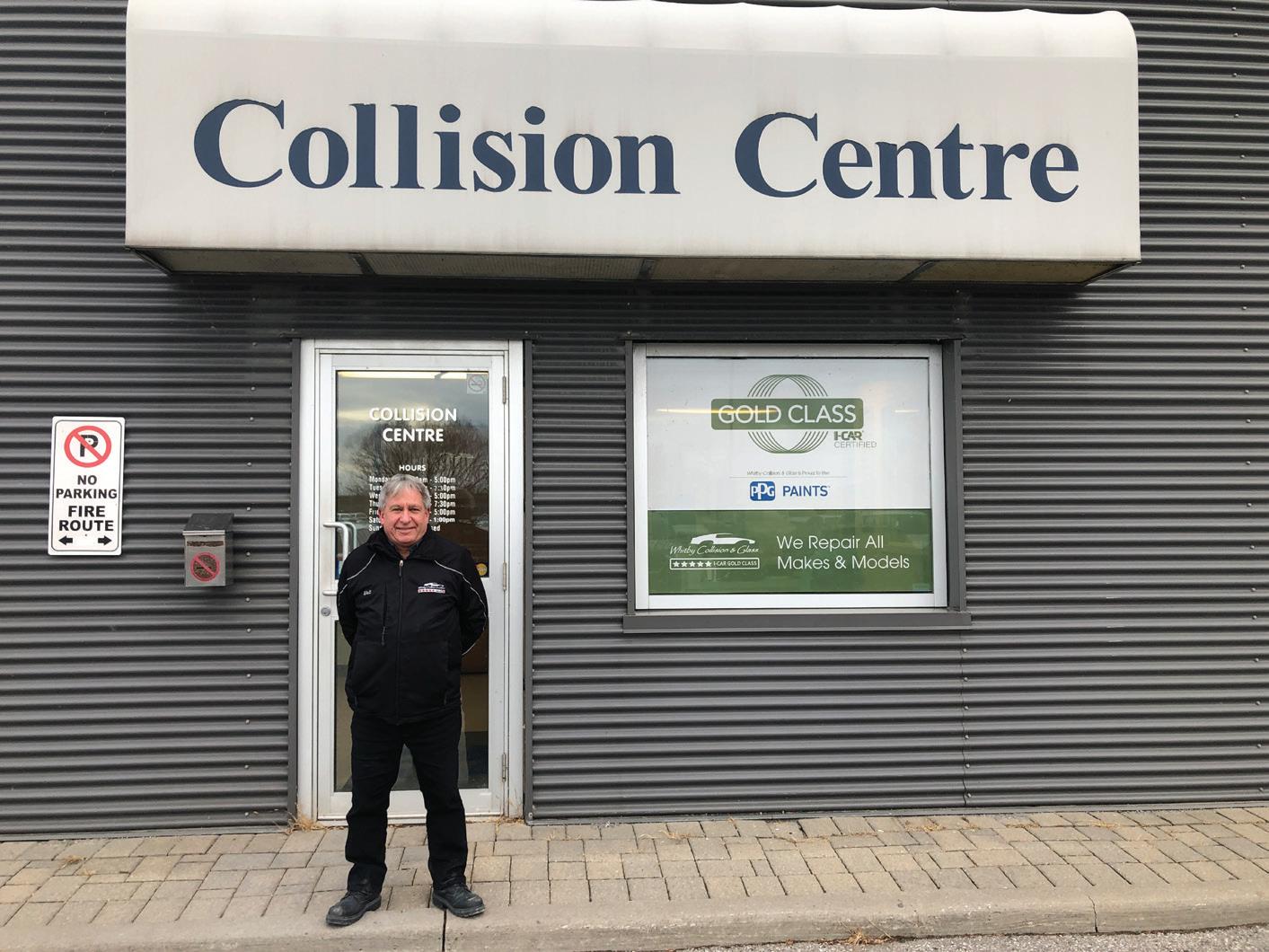
32 minute read
45-YEAR CAREER
from Bodyworx 7#1
THE CONSTANT REPAIRER
After more than four decades in the industry, Whitby Collision and Glass’ GM has seen it all—and knows what to expect next
BY ALLISON ROGERS
If you’ve walked through the doors of Whitby Collision and Glass in the last 45 years, you’ve likely encountered Walt Sabadin. Walt has been a fixture in the facility since he was 15 years old—but his infatuation with cars and the automotive sector were ignited long before the seasoned repairer acquired his first industry job.
Walt—who grew up in Ajax, Ontario—has always loved cars. He recalls “messing around” with the other neighbourhood kids, painting their bicycles and toy cars to pass the time. He continued to cultivate his interest in his youth, tinkering with electronic parts and learning how to drive a manual transmission. “I had a knack for it,” Walt tells Bodyworx Professional. “My dad would always tell me, ‘you’re gonna be a technician when you’re older.’ And that was just when I was a little guy!” When it came time to attend high school, Walt knew he was destined for a career in automotive repair. Ajax High School offered a wealth of trades-related courses in the 1970s—and he took full advantage.
“I took just about every class that I could. Engine rebuilding, transmission rebuilding, electrical diagnosis, small engines, welding, soldering, woodworking, refinishing, machine drafting—absolutely anything that had to do with vehicles.”
His dedication paid off. In 1974, a 15-yearold Walt was offered part-time hours cleaning cars at Whitby Collision and Glass.
“I used to ride my bike there every day after school, washing cars until the place closed every night. In the summers I was full-time, just doing detailing and cleaning cars at first.” After his first summer, a service manager approached a teenage Walt and asked if he
In addition to growing the business, Walt played a key role in designing Whitby Collision and Glass’ current facility.
could help with some general mechanical work. He obliged, keeping his part-time hours during the school year and returning as a mechanic that summer.
The bodyshop manager later asked if he was willing to try his hand at bodywork. Walt accepted and soon began sanding and prepping cars.
“When I finished high school, I kept that job and eventually started to get into painting as well. Then I did my apprenticeship, got my license and worked as a flat rate painter until the late 1970s.”
Back then, Whitby Collision and Glass was a smaller operation—but business was booming. The shop kept growing—and Walt’s responsibilities on the floor and behind the scenes alongside it.
“After I began helping with payroll, I found myself doing more than I could handle, so we hired a prepper—he’d prep the cars and I painted them. When we grew again, we hired a painter. After that, I was full-time in the office and management became a two-man operation. I served as assistant manager for a little bit before becoming the bodyshop manager and, eventually, general manager.” At that time, the shop was still writing handwritten estimates—but Walt sensed the incoming waves of technology and wanted to arm himself with computer-based knowledge. So, he enrolled in computer learning courses at Durham College.
This was not out of character for Walt, either—he always aims to address industry challenges head-on. In his 45-year career, he says he’s “seen it all,”—and adapting is not a choice.
“I’ve seen changes across the board—from basic collision repair to painting to direct repair

The facility invests in state-of-the-art equipment and is certified by several OEMs.

programs. But the biggest thing is keeping up with them,” he says.
“Take OEM certifications—it’s a huge thing today and will be moving forward,” added Walt. “Or the rise of autonomous technology, or collision avoidance systems and their corresponding repairs and calibrations. All these changes can be called challenges but following them is not a choice. You have to adapt to survive as a business.”
That’s what the team at Whitby Collision and Glass has done—adapted to survive. The business outgrew its old location in the early 2000s, moving to its current location in 2003. It boasts a spacious garage, the latest tools and equipment and is OEM certified with Volkswagen, Audi, Toyota, Kia, Chrysler, Jeep, Fiat, Ram, SRT, Dodge and Mopar.
On top of that, the shop is the only I-CAR Gold Class Certified facility in Durham Region. “We always want to make sure we’re at the top of our game, assuring that we stay up to date with training and OEM factory standards,” says Walt.
Now, like any good manager, Walt wants to pass on his wisdom and help build the same path for others.
“I’ve always held an interest in helping the younger techs build their careers. I always say the new young professionals entering this trade should strive to be at the top of their game. I like to see that and enjoy helping the young passionate techs succeed, coaching them and watching them move up in the industry. I’m really proud of the team we have on the floor today.”
One question remains—why has Walt spent his entire career at Whitby Collision and Glass? “That’s easy,” he laughs. “The family-owned atmosphere.”
As Walt, who played a key role in designing the current facility and growing the business, that family atmosphere allows him to draw a great sense of satisfaction from the business’s successes.
“Watching the company grow throughout my career has made me feel like an owner here. Plus, we’re a family and most of the people I have hired though my career are still with us.” Walt adds. “I’m very proud of that.”
FAST FACTS
Whitby Collision and Glass features: • 3 large vehicle hoists • A paint room with countless colour selections to ensure a perfect match • Welding machines galore—the shop says there’s always one available! • State-of-the-art ventilation system • UV Fast Lane technology to ensure speedy drying times
JINKIES! JEEPERS!
Check out Len Boschman’s nostalgic build for the International RATical Rod Build Off Drive Off
BY ALLISON ROGERS The actual Scooby-Doo Mystery Machine

Len is the owner of MacGregor, Manitoba’s Four Way Motors.

The build Len Boschman is currently working on is sure to make you scream, “zoinks!” Len, the owner of MacGregor, Manitoba’s Four Way Motors, is one of three Canadian participants in this year’s International RATical Rod Build Off Drive Off, a competition that sees unique builds from all across the globe travel to SEMA.
Len had a friend’s 1961 Ford Econoline sitting on his property since 1996—and he’s converting the classic into the Scooby-Doo gang’s iconic Mystery Machine for the 2020 Build Off.
Every year, the Build Off features Rat Rods that can only be described as works of art. From the 1930s-themed custom rod Manitoba’s Jason Groulx snagged first-place with in 2013, which featured authentic antique bullet holes and a tommy-gun shifter, to ‘Big Bandit’, a motorhome-truck hybrid that earned Ontario’s Tyler Turnton the Build Off crown in 2018.
There’s two catches in the competition. First, builders only have nine months to build their vehicles—from January 1 to October 25. Second, the vehicles have to make the 1,500 mile (2,414 kilometre) trek from Speedyway Motors in Lincoln, Nebraska, to the SEMA Show Las Vegas. The Mystery Machine project started nearly two years ago, after Len built a Chevy Blazer K5 for SEMA 2018. The Blazer started as a four-door Yukon before Len topped it off with a regular truck cab, shortened the box, and sectioned in the floor panel from the Yukon. Finally, he built a removal fibreglass roof from a camper shell.
The vehicle sparked buzz at the 2018 SEMA Show and Len was approached by Bryan Dagel, founder of the Build Off, who asked if he was interested in participating in the 2020 competition.
From there, Len said yes, and decided to tag along for the 2019 Drive Off ride—“just to see what could be in store,” he said. “And boy, am I glad I did.” Len rode alongside teams from Saskatchewan, Florida, Louisana, England, New Zealand, Australia and more from the 1,500-mile outset. As the lights of Las Vegas drew nearer, the builds began encountering problems.
Len’s initial rendering for the build.
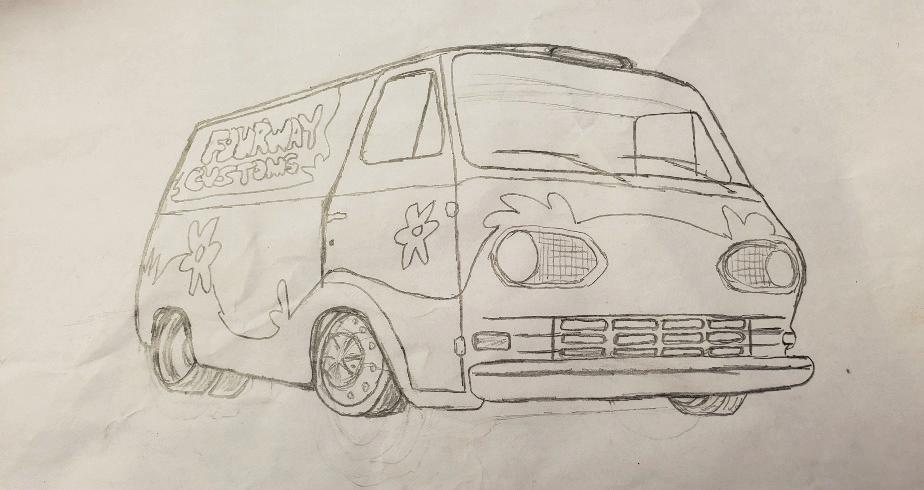

The 1961 Ford Econoline pre-tear down.
This year’s Build Off participants and staff— Len, along with Tyler Turton from Zombie Body Shop in Selkirk, Manitoba, and Reg Garnett from Asylum Hot Rods in Huntsville, Ontario are the only Canadian teams.

“These vehicles didn’t have any heating, and some of them didn’t even have wipers,” said Len. “And you bet we encountered freezing rain and snow.”
But inclement conditions were the least of the group’s worries.
“One team ended up blowing a transmission on the way, and another ran into suspension and braking problems on three occasions. Some vehicles needed to drive with oil pan heaters under the cars because the mornings were so chilly.” Still, no matter the problem, the road to Las Vegas rides on.
“The biggest thing is that, in order to succeed in the competition, you have to complete the journey. So, even if you have to trailer your vehicle, it has to be taken back to where it broke down and continue the journey from there,” Len told Bodyworx Professional. Another condition of the Build Off is a little more hands-off—the teams can’t have any professional help from all-star builders. “That’s another part of the competition. You can’t have any professional, high-class help. This is designed for the shop owners, the gearhead guys who don’t really do crazy builds for a living—it’s more of a hobbyist thing. A lot of Vegas builders craft impeccable vehicles—don’t get me wrong. But could they do a 1,500-mile journey like that without any work being done on them? I’d say good luck to some of them.”
Len’s business, MacGregor’s Four Way Motors, has been at the same location since its inception in 1967 when his father and uncle started the business. Len acquired it in 2001 and runs the facility alongside his wife, offering the small community of MacGregor, Manitoba autobody and mechanical services, as well as towing and recovery and car sales. The shop is part of a direct repair program and repairs all types of vehicles—from classics to Teslas. Four Way Motors has been home to the 1961 Ford Econoline since 1996—but before that, it operated on the Distinct Early Warning (DEW) Line spanning from Alaska to Greenland. The line was constructed on Canadian soil by U.S. authorities in the 1950s to detect any enemy bombers descending over the North Pole, but was shut down in the 1980s.
The Econoline was the work vehicle of Len’s friend Dennis Williams. In 1996, Williams’ employers told him to scrap the vehicle in favour of a newer one. Instead, he chugged the van all the way to Four Way Motors, where it’s been ever since.
“He told me, ‘I want you to restore this someday.’ He’s since passed away, and when I was offered the opportunity, I decided to approach his family. They donated the van to us and that in itself is a huge honour.”
The idea for the Mystery Machine design came from the mind of Mike Hawco, who’s working alongside Len on the build.
“He said, ‘this will get people talking,’ and so far he’s been right,” said Len.
Despite comments from rotten naysayers preaching that the iconic Scooby-Doo Mystery Machine has been done to death, Len maintains that he’s achieved his first goal—everyone’s talking about it.
“You can think that, but hey—you’re talking about it,” said Len.
The build has made waves on social media, in local news, and among suppliers. Len says he’s been astounded by the support offered to him so far.
“BD Diesel has hopped on and given us a bunch of parts,” said Len. “And I just received confirmation that Axalta’s with us, too. Brett
Team Four Way has built a custom chassis for the build.

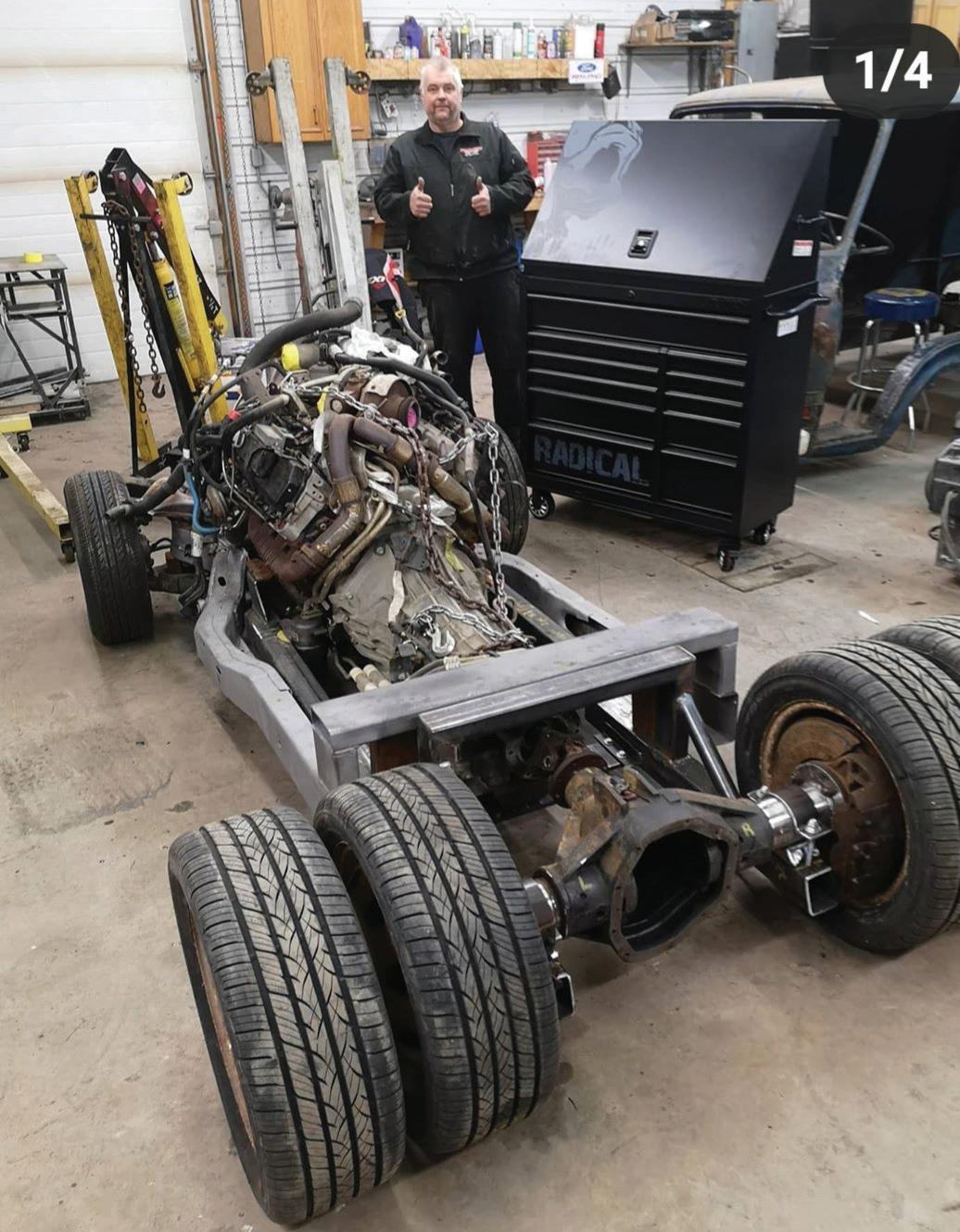
Len has been astounded by sponsor support—NAPA even sent him its whole RADICAL tool line!
MacNeil from 3M was here a few weeks ago and said they’d help out, and Can Am Auto Glass is giving us all the glass for the build. “NAPA has been supporting us from the get-go. Chris Kinghorn, regional vice president for NAPA Ontario sent us out the RADICAL tool line—the box, the cabinets, the jack stands, creepers, new floor jacks—everything!” said Len. Toyo Tires has also joined the team, providing the Mystery Machine’s dually tires.
Since the Econoline was built without side doors, Len plans to open up the side panel and unveil a sort of working display rack for his sponsors. From the side panel, SEMA spectators will be able to view the engine and transmission.
GRB Studios is also capturing every step of the build on camera said Len, and all his sponsors will be splashed across the various episodes.
So far, Len’s team has gutted the vehicle, cutting out the floor panel and stripping everything from the inside. They’ve custom-built the chassis and mounted the engine, transmission and differential. “The steering is in it now, and we’re just in the process of building the floor pans,” said Len. “We’re working on the back section and the interior, then we’ll start on the steering column and the brakes. We’ll start on the body mods in mid-to-late April—we’re expecting three weeks for those.”
He estimates that, when it’s all said and done, between 2,000 hours and 2,500 hours will have gone into the Econoline’s transformation. “There’s just so much to it. We’ve got nine months, but we obviously have our day jobs to worry about. It’s a nights and weekends project, really.”
And time is of the essence. “Time is going to be the deciding factor,” said Len. “Will we be able to wet sand, polish and detail the living snot out of this thing? I really hope so. With Axalta on board, I really want to showcase the materials.”
And, with the SEMA Show slowly inching up on the calendar, Len is on the hunt for an indoor sponsor.
“Inside is really where we want to be—it’s where you get the most exposure,” he said. Now, just over a third of the way through the nine-month timespan, Len is stunned by the support offered by not only his sponsors but the Canadian automotive community.
“Everybody has just come together amazingly. I cannot believe the reaction all of this is getting—it’s truly incredible. It’s like an automotive family, really.”
Stay tuned to Four Way Motors’ Facebook page for updates on the build, or visit his International RATical Rod Build Off Drive Off builder profile at rodrides.com/user/lenboschman.

The Econoline used to man the DEW Line in the Northwest Territories and sports a gorgeous 60-year old patina.
PAINTER’S PERSPECTIVE


Kirk Anderson shares how his past, shaped his future
From a young age Kirk was always surrounded by some element of the collision repair industry. His dad owned a facility for many years, and his two brothers are licensed technicians. Taking a food services co-op in high school, he initially pursued a career in the culinary arts. However, with his first child being a newborn, he knew he couldn’t balance his time between family and career path which, at this point demanded his focus lean toward work. When he looked at alternate career options, he felt limited in scope, as he was diagnosed with Type 1 Diabetes. His parents, being as supportive as they are, persuaded him to join the family business.
After becoming a licensed technician, his dad suggested he learn the art of painting and for the last 18 years he hasn’t stopped.
Well, that’s not entirely true. During this time, Kirk lost interest in painting. Not because he didn’t enjoy it—it was the environment around him which didn’t make it ‘fun’ anymore.
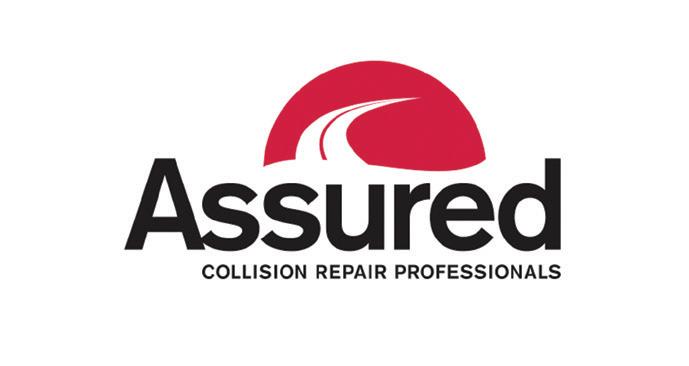
Given his expertise, he easily attained a role with MAX Auto Supply as a paint representative. Other than day-to-day duties, he ran seminars, and shared his painting philosophy with others–“you have to get good, before you get fast... and understand your paint job is as only good as your prep work.”
One day, Kirk was trouble shooting issues with one of our paint booths at Brampton North and he ended up painting a few panels, while doing so, he got that ‘feeling’ again. Just like that, Kirk was taken back to a time where he was the master of a canvas, in this case a panel or two.
That evening, he shared this experience with his wife - wondering if he should go back to painting. To our benefit, his wife supported him. After a short meeting with Tony Raposo, he was layin’ down base at our North York location, now he works out of our Assured Markham location. One element which makes his experience different now, is the people who surround him. They support him and vice versa –the strength of this relationship can clearly be seen in the morning huddle. Kirk does have aspirations of managing his own facility someday, but for now he is happy helping his team and sharing his skills, experience and philosophy.
PUT YOUR BEST COAT FORWARD
All the painting hardware your business needs to complete quality paint jobs while staying safe!
It takes more than a bucket of paint and a quick spit-shine to achieve a quality paint job. In reality, it takes a village of painting hardware and safety equipment specially designed to deliver quality, long-lasting results. If you desire to create truly professional results, the proper automotive paint supplies and equipment are absolutely essential. With recent and rapid technological advancements taking the industry by storm, paint hardware and tools have undergone updates that allow them to adapt to more complex vehicles and paint jobs.
Ultraviolet drying technology has made significant improvements recently. As UV drying technology comes of age, devices promising to provide light-speed paint drying times and far more efficient painting procedures have started to hit the collision repair scene. This advanced technology is said to take the waiting out of the painting process, delivering near-instant curing of all three pre-paint steps: body filler, glazing and priming. Ask any collision repair shop owner about how to increase their productivity and you will likely hear about the need to reduce pre-paint wait times. Recent advancements in curing systems have led to new, compact UV lamps designed to dry body filler, glaze and primer within mere seconds. This new technology could bring revolutionary results to the industry with its aim to eliminate pre-paint wait times and inconsistencies in primer application. Instead of having vehicles sit for several days while you wait for the primer to dry, UV drying lamps promise to achieve complete curing in just 30 minutes. Further, unlike the less efficient UV curing lighting standards of the past decade, new technology involves powerful handheld devices designed to cover larger areas and cure within seconds. Prior generations of UV systems have been known for their bulk and weight, making the units more difficult to operate and hold still for the three to five minutes they take to cure a pre-paint job. New devices are more ergonomically designed, easier to move and handle and are typically about the size of a person’s hand.
While increasing the number of vehicles that can be repaired without adding bays is a

huge win for collision repair shops, there are said to be even more additional benefits to completing pre-paint dry times more quickly. Any time a car is not being actively worked on in a shop can potentially impact an insurance company’s evaluation. The longer a car sits in the shop without being worked on, such as during dry times, it could lower a shop’s score and risk diminishing a valuable source of insurance referrals.
This year has seen significant updates to colour matching technology, spray booths, spray guns, painting tapes and protective equipment. Find the cure to all your painting problems by flipping through the following pages of paint hardware products!
“Advancements in UV curing systems have recently resulted in a new mobile solution for collision repair shops that deliver near-instant curing to enable operators to complete their pre-paint steps without costly delays. Some collision repair shops and distributors even find that advanced UV systems can eliminate the pre-paint wait time.”
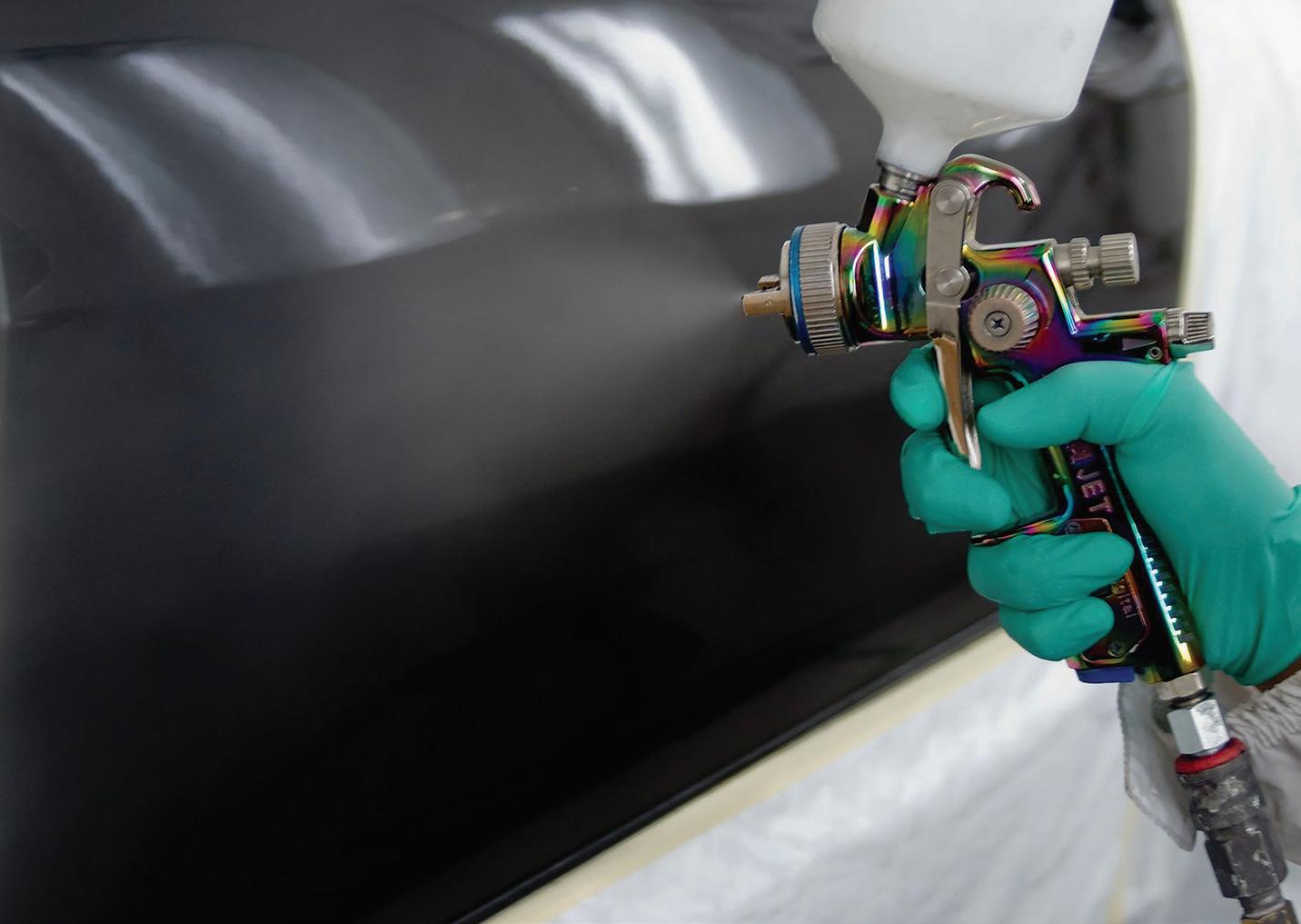
— Stephen Armstrong, automotive trade writer
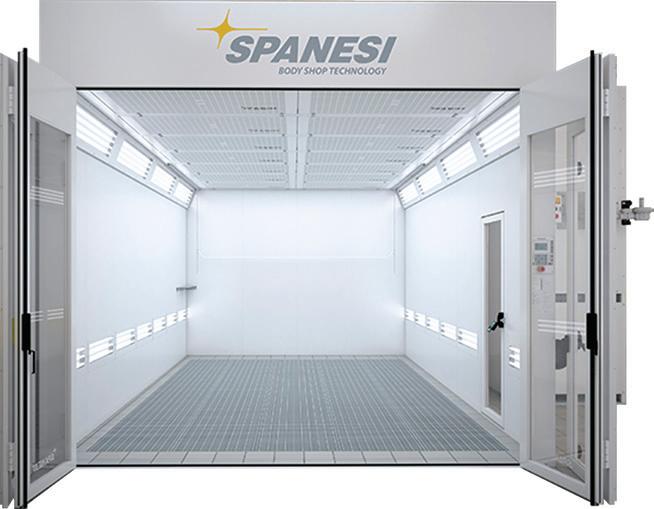
With a diverse and wide range of spray booth, preparation area, aluminum bay and mixing room options, Spanesi is said to provide facility layout services that allow customers to visualize their installations long before work begins. Spanesi spray booths are said to be capable of recycling up to 90 percent of heated air during the bake mode. Utilizing highquality double-wall insulated panels, Spanesi is a leader in the reduction of energy costs associated with your paint department operations, according to the company. Spanesi spray booths are waterborne-ready.
spanesi.com
ACQUIRE QUANTUM EFX AXALTA COATING
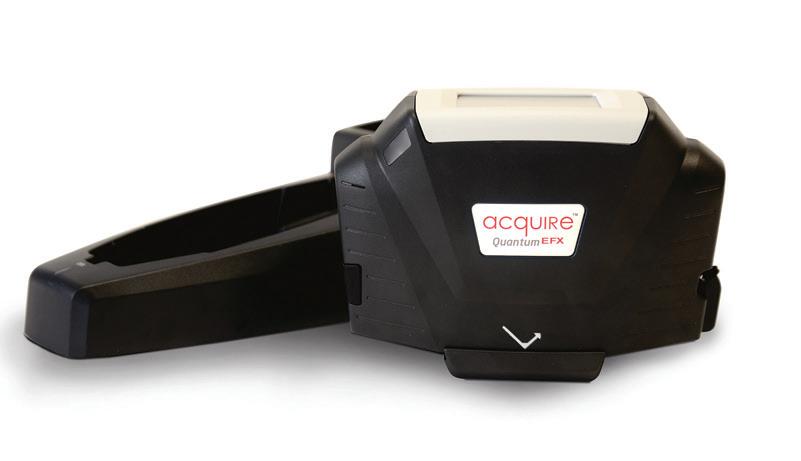
Axalta Coating Systems’ new fifth-generation spectrophotometer—the Acquire Quantum EFX—is compact, quick, and easy to use. Able to read metallic pearl, effect colours and more, the Acquire Quantum EFX integrates Axalta’s Acquire Color System and is re-engineered to fit comfortably in one hand. The Acquire Quantum EFX includes a top-mounted touchscreen, designed for high visibility as well as a “smart cradle,” designed for charging and making connecting with a PC more simple. Painters who struggle with hardto-reach places may greatly benefit from this compact and easy to use, Wi-Fi enabled tool.
axalta.com
PREMIUM GUNWASH REXALL LABORATORIES AND CHEMICALS

Less flammable than acetone, this gunwash from Rexall Laboratories and Chemicals is said to clean a variety of painting equipment, from spray guns to lacquer painting tools. Comprised of a virgin mixture of solvents, the company says its premium gunwash is ideal for use in body shops and garages. It can be purchased from Rexall via the product code RX590266.
rexalllabs.com
SATA CLEAN RCS SATA CANADA
The SATA Clean RCS is a pneumatically-operated cleaning system designed to allow for quick and effective spray gun cleaning to be performed between jobs when using a disposable cup system, such as SATA RPS. Engineered to clean all material passages in a spray gun, the SATA Clean RCS is said to allow for consecutive colour changes with extremely short cleaning interruptions. Mounting in the spray booth or in the preparation room, the product is suitable for waterborne and solvent-based paint systems. It also boasts low solvent consumption rates, using just 0.1 litre of cleaning solvent per gun.
The IR-B06 and IR-B06-T infrared curing systems from B-Tec Systems feature low base heights and two stage drying with the option of either half or full power bake cycles available. Each cassette on the units feature separate switching so they can be turned on individually and B-Tec says the gas-filled struts make it easy to position them. The units include a 10m power cable, digital memory function that can store up to four drying programs, a visible ultrasonic distance indicator and a two-year warranty. The IR-B06-T also allows for temperature control and a drying area of 1,000x1,500m. Optional cassette covers are also available.

bteccleaners.com
SPECTRATEK INSTACURE AMH
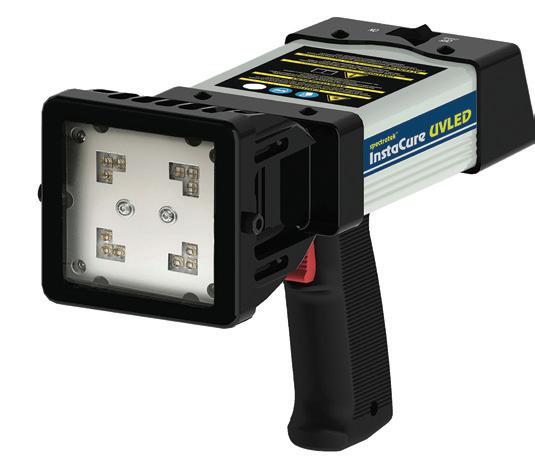
The Spectratek InstaCure UVLED is a cordless hand-held curing lamp, usable on all current ultraviolet light curable putties, fillers, base coats, top coats and clear coats. It is said to offer an almost instant full cure with no heat, according to AMH, along with a two hour battery life. This product has been tested on UV paint products from most major paint manufacturers, such as Akzo Nobel and BASF.
amh.ca
UVALEDTRONIC-M1 SYMACH

The UVALEDTronic-M1 from Symach is the result of research from the company’s R&D team to find the exact wavelength for the next generation of UV coatings. According to Symach, the wavelengths found in the UVALEDTronic-M1 are unique from the competition in the UV-A segment to achieve the fastest drying times on the market. Meant for use even between first and second coat, this product strives for greater speed of execution during the paint process with an estimated drying time of 20 seconds after the first coat and 40 seconds after the second coat.
symach.com
IRT RAIL SYSTEMS HEDSON

The IRT Rail Systems from Hedson strive to produce a high-versatility drying system. These infrared dryers are suspended in permanently installed rails, allowing for easy glides through the working area. Said to be able to move laterally and vertically in all directions, this selfstabilizing ray dispenser trails its electric power supply through the rails it is mounted to.
hedson.com
SCOPING THE SCENE Provincial skills competitions are ramping up



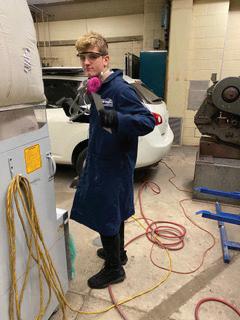
BY BILL SPEED
Toronto District School Board held its board-wide Skills competitions recently to determine which qualifying students are headed to the Skills Ontario competition to be held from May 4 through 6. For those of you that are having trouble finding skilled technicians, this is your opportunity to get in at the grass roots and start recruiting for the future. As a retired teacher of Auto Body in the TDSB, I saw seven auto body programs disappear over my 27-year career—and once a program is closed, it never comes back.
These programs are what piques the interest of our young people towards a career in the trades. If the industry doesn’t help support and encourage our young people, the Skills shortage will only get worse.
Many thanks to the industry judges and sponsors for their support in this competition, Provincial Skills and Skills Canada Nationals. Without your support we could not help to guide these students to their successes and possible career paths.
Bill Speed is a retired Danforth CTI teacher and currently works as a road appraiser with Action Appraisals.
TORONTO SKILLS COMPETITION RESULTS:
Collision Repair Gold Trent Sherry Silver Siddhant Sane Bronze Sunera Mehrun 4th Place Jordan Johnson Car Painting Gold Aaron Walker Silver Marcellus Lepage Bronze Joey Webb
Judges/Sponsors Kirk Edwards, BASF Damian Campbell, BASF Justin Sall, Fix Auto Mississauga Central Claudio Chiodo, Fix Auto Mississauga Central Bill Speed, Danforth CTI retired teacher, currently with Action Appraisals
SCOUTING SUCCESS
The auto repair industry is on the hunt for talent—and Centennial’s got it in droves
BY ALLISON ROGERS
The air was thick with ambition at Centennial College on March 4 during the eighth annual open house for the Trillium Automobile Dealers Association and autobody repair facilities, which gave aspiring apprentices the opportunity to explore the industry and network with potential employers. Students from Centennial College’s Autobody and Collision Damage Repairer program filled the room at Centennial’s Progress Ave. campus, prepped and primed for an afternoon of networking opportunities with notable names in collision repair. Present at the show were several groups from across the GTA scouting to fill apprenticeship opportunities, including Assured Automotive, AWIN Advanced Auto Body Centre, Bramgate Collision Centre, CSN Avenue, CSN 427 Auto Collision, Excellence Auto Collision, Fix Network Canada, Highland GM Chevrolet Buick GMC, MTB Transit Solutions, Ontario Chrysler Jeep Dodge RAM, Performance Auto Group, Pfaff Auto Group, R Ferri Automotive and Simplicity Car Care, Tropicana Employment Centre and Weins Canada.
Assured Automotive was out scanning the scene for potential tech talent, said Carl Mohammed, Assured’s business development manager.
“As we are looking to grow our network in size, we can only do this if we have talented employees to help us reach this target,” he told Bodyworx Professional. “The program at Centennial College creates students with the caliber of talent which we are looking for – this is why so many other organizations look forward to these events hosted by Centennial.
“What we look for in a potential Apprentice is their knowledge of our company and the industry in general. Do they have a sense in what area of the collision repair process they gravitate toward; prep, paint, body work, etc. Finally, we look to see how they engage us in a conversation. Given how repair processes are evolving, teamwork now plays even a bigger role in getting the job done–effective communication is key.”
According to Carina Martinez, Assured’s talent acquisition manager, Centennial’s talent pool proved “very strong.” Martinez was able to interact with students graduating this April—this year’s incoming group of apprentices—as well as students set to start their careers in April 2021.
For more information on Centennial’s Autobody and Collision Damage Repairer program, visit centennialcollege.ca.
Highland GM’s team was all smiles as they attracted new apprentices.



The family-run Zanchin Automotive group was also in attendance.

AWIN was there to win over some A1 talent
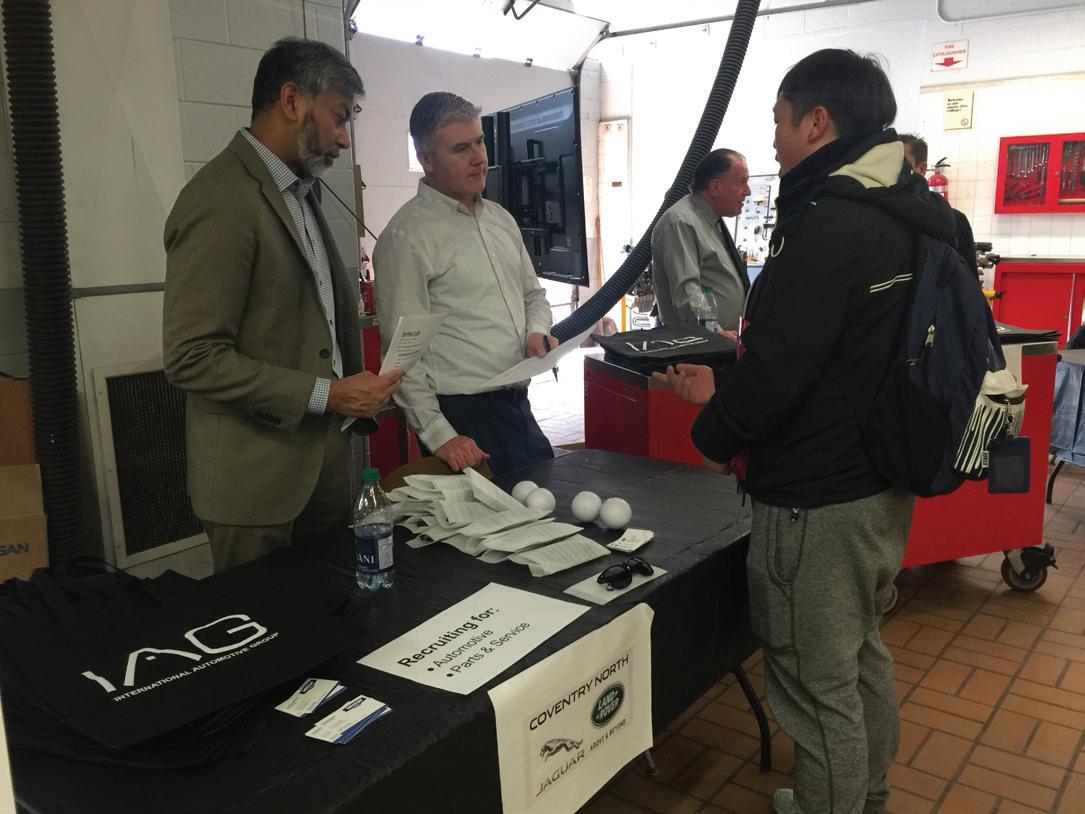
Bramgate Automotive’ collision centre was also there to scan the Centennial scene.
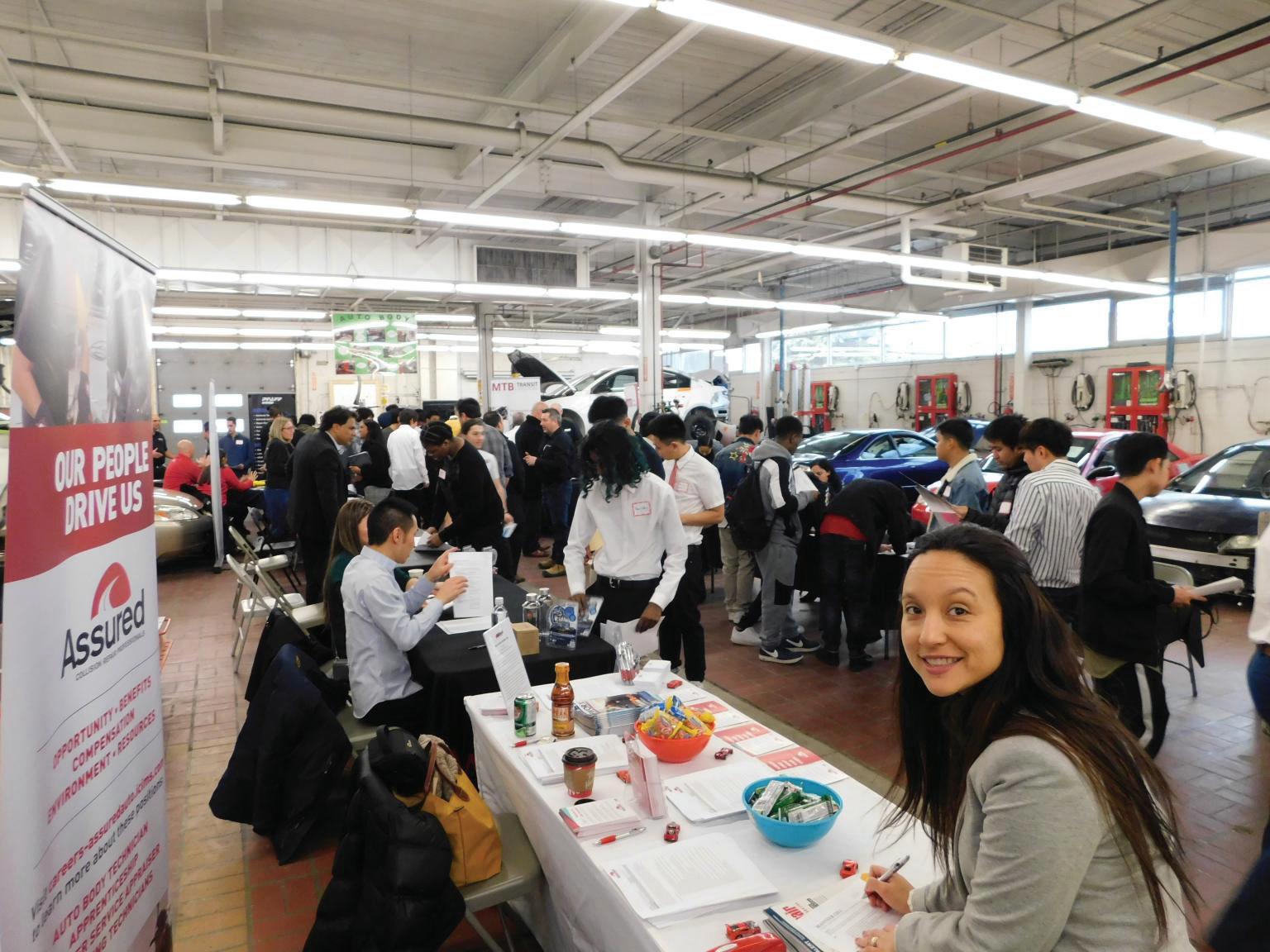
The team from Coventry North Jaguar Land Rover was also scouting the talent pool.

Carina Martinez, Assured’s talent acquisition manager, scopes the scene for potential apprentices.


TRICKS OF THE TRADE
Four simple steps to help you launch a collision career
1. Reflect on your goals Take a step back and consider where you are now versus where you want to be. Where do you see yourself after school? What is your career goal?
2. Research and explore The world is your oyster! There is a wealth of career opportunities in the automotive industry, including jobs in autobody repair, manufacturing and general administration. Find your fit and dive in!
3. Develop a plan What strategies and tools will you use in your job search—local training centres? Job boards? Online databases? Word of mouth? A plan will help you prepare and make your job search that much easier.
4. Take action Is your plan specific? Is it realistic? How will you stay motivated toward completing your goal? Ask yourself these questions before taking flight.
WRITE IT RIGHT… FROM THE START
The hidden dangers of rushing through estimations
BY KELLY ROBERTS
In this industry, we too often get off to a bad start with our customers.
When they ask, “When is my car going to be ready?” we hear, “Please get me my car back as quickly as possible so I don’t have to deal with this anymore.”
By trying to provide clients with that answer they think they need as quickly as possible, the collision industry—too frequently—sets itself up for failure.
Industry consultants teach “don’t over-promise and under-deliver.” This is sage advice, yet, who is listening to it?
In far too many repair shops in Canada, we rush through a haphazard triage process in order to provide vague answers as quickly as possible. Why?
I believe most, if not all shops do not agree with how this lack of process is the status quo—we all want better, and our collective clients deserve better.
As a result, our only-by-eye assessments tend to be performed under pressure in 10 minutes or less—only enough to determine the most obvious damage, and perhaps whether a temporary repair can be made to let the driver keep their car. Unfortunately, these cursory inspections are dangerously insufficient. Modern automobiles are engineered to absorb impacts and spread them throughout a vehicle—meaning damage most always isn’t going to be apparent.
Sufficient would be keeping any vehicle for a time to allow a proper triage process. Enough time to properly assess mechanical, electronics (avionics), structural and suspension and safety systems.
When we don’t, we’re risking our business, our relationship with insurers and our customer’s lives.
It is a model being used by more and more top-tier repair facilities—and the reason is quite simple. The benefits of pleasing the customer in the short term are far outweighed by the benefits of correctly assessing the damage, planning all necessary parts and procedures and documenting them all properly—from the start.
On the front end, it may cause a customer some disappointment if not delivered legibly and intelligently. On the back end, it measurably speeds the entire repair process, reduces the amount of downtime required—and thus cuts overall repair costs. In this industry, repairers tend to encounter undiscovered and undocumented damage in a high percentage of the vehicles they fix— damage missed in the original estimation.
It is news that no client—and no insurer— likes hearing.
It also causes procedural delays, and it wastes everybody’s time!
Had all the damage been appropriately assessed, all vehicle repairs would be scheduled much more tightly, capacity and throughput dramatically improved. It is profit 101.
It is, however, better than the alternative situation—allowing unsafe vehicles to go unregistered and uninspected to be driven down the roads. Some studies have found that, after thoroughly reviewing vehicles, the number with unsafe and undocumented hidden damage that is found on, is at least six-out of-10 vehicles leaving bodyshops “deemed” as safe to drive.
Of course, that isn’t just money being left on the table, that is unsafe vehicles being let on the road—and possible business-ending legal liability issues too.
Don’t get me wrong—in my long career of collision repairs, I fell into the same trap. I also
had a ‘holy heck’ moment—not so long ago. A Honda came into a shop where I was coaching, with what looked like light cosmetic damage to the front right side. It had a clean pre-scan, and no dash lights were reporting anything. When we looked under the front cover, however, I could see the driver’s side front impact sensor bracket had been disrupted—and the sensor fully compromised. I hate to think what could have happened if we’d let it roll onto the road.
It isn’t like auto insurers are really pushing us on this issue either.
In my conversations with insurers about the issues caused by rushing through initial assessments, they have all been hesitant to suggest that it is a pressing matter.
As more than one put it: “Nothing is going to change until someone is killed.”
Unfortunately, that standard isn’t one repairers should accept. For one thing, we face the most pressing legal risk—and, unlike auto insurers, very few repair facilities are likely to be able to recover from judgments in the tensof-millions. For another, there is no information available about whether or not missed repair procedures are killing people—or how often. Lastly, I never want to be the mechanism of another person’s untimely end.
If, as traffic analysts say, a single driver tapping their brakes on a busy highway can cause a traffic jam, what havoc can thousands of vehicles with undetected damage wreak? At the end of the day, the risks posed by damaged vehicles may be unknowable. I am not sure that matters.
As collision repairers, we are legally obliged to provide customers with the expert assessment of vehicle safety and drivability based on our professional capacities. For businesses involved in DRPs, that isn’t just a moral obligation, it is also a contractual one.
We cannot give safe and accurate professional opinions without conducting proper and thorough assessments of damage. Involved in the collision sector since 1989, Kelly Roberts is a vice president of sales at AirPro Diagnostics. During his career, in which he has been involved in many areas of the collision sector, team member, employee and owner/manager, Roberts been an advocate for the improvement of the collision repair industry and previously served on the Axalta National Business Council.
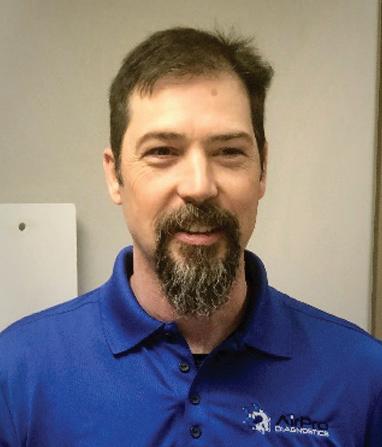

magazine
SCAN ME
YOUR KEY TO THE RECYCLING MARKET

In partnering with the Automotive Recyclers of Canada, Canadian Auto Recyclers magazine has showcased the most modern and progressive auto recycling facilities from across the country since 2006. Steeped in forward thinking practices and environmentally conscious programs, the publication offers a comprehensive look at the recycling industry and how it’s positively reshaping its image.
SUBSCRIBE TO CANADIAN AUTO RECYCLERS https://canadianrecycler.ca