
14 minute read
EVENTS
WHAT IS LEAN THINKING?
Dave Luehr’s Elite Body Shop Solutions webinar featuring Rich Altieri
Dave Luehr the CEO Of Elite Body Shop Solutions.
BY MADDY KYLIE

Rich Altieri, the founder of Auto Body Management Solutions finds a particular Karate Kid quote helpful in defining ‘lean thinking’.
When it comes to understanding the concept of ‘Lean Thinking,’ Rich Altieri finds a Karate Kid analogy particularly helpful.
In the 1984 film, Miyagi initially teaches Daniel how to do karate by making him wax his car, and by repeating the popular phrase: “wax on, wax off.”
Altieri, the founder of Auto Body Management Solutions and associate mentor at Elite Body Shop Solutions reworked the phrase by saying, “hands on the car, hands off the car.” When your hands are on the car you are adding value and are doing what customers are paying you to do, but when your hands are off the car it’s waste, he said in a Dave Luehr Elite Body Shop Solutions webinar on Aug. 25.
According to Altieri, defined value is “any activity, labour, parts and materials that physically moves the damaged vehicle towards its pre-damaged condition, done correctly the first time and are willing to pay for it.”
And, waste is any activity, labour, and materials customers don’t value and don’t pay for. However, he noted that not all waste is bad, some is actually essential, for instance, meetings, training, and customer service are considered essential waste, because the customer is necessarily paying for it but it is needed to keep the business running.
It’s the non-essential waste and what he often calls “the junk in the trunk” you have to look out for, which could be missing parts, rework of any kind, discovery of additional damage during production, missing hardware, etc.
Altieri also showed some shocking data about how time is actually spent in a shop. He says that the average body shop only spends about two hours in 24-hour day doing defined value work, which is the actual repairs of the vehicles; the other 10 hours is spent on essential waste, and the rest (12 hours) is spent on non-essential waste.
He noted that many technicians believe that they spend six hours a day doing actual repairs, but based on his 15 years of experience helping shops understand the concept of lean thinking with PPG, even the best-of-the-best shops are only doing two to three hours of defined value work in a 24-hour day.
The good news, however, was that he offered a few tips and tricks on how shops can use their time more effectively.
There are three ways to improve value added touch time and cycle time, he said. You can lower your WIP (have fewer jobs in progress), increase delivery rate (more vehicles per day) or increase labour hours.
He says the best way to start doing this is to figure out where you’re at now—in terms of WIP, delivery rate, and labour hours, — so you can see how much change needs to be made. Then make it happen.
He also noted that continuous work is very essential in improving productivity. In a perfect world the same technician would work on the same vehicle until its complete because it dramatically speeds up the process, he says.
At the end of the webinar Altieri gave some advice on the next steps on what participants should do now with all the knowledge they’ve obtained.
He said shop owners should have a lunch and learn session with their staff and play the recorded version of this webinar, so they understand what you are trying to achieve. Next, you should start gathering information on your daily car count, delivery rate, and cycle times, then review them with your team and figure out ways to improve them and plan a specific plan of action.
For those who were unable to attend the live event can watch the recorded webinar by joining the Elite Body Shop Academy for free at elitebodyshopsolutions.com.
FALL FESTIVITIES
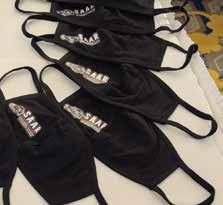
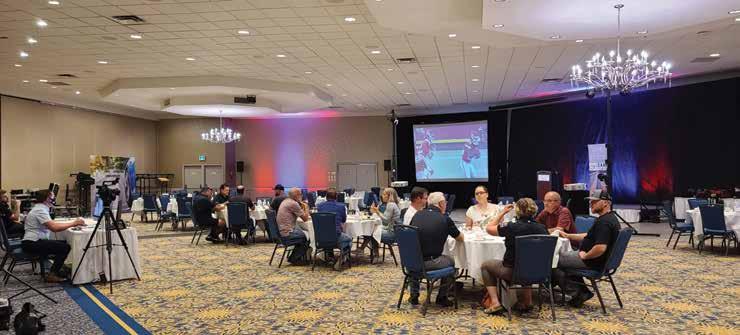
SAAR’s Fall Conference proves a smashing success
BY ALLISON ROGERS
The Saskatchewan Association of Automotive Repairers (SAAR) held its annual Fall Conference on September 11 and 12, featuring a host of helpful sessions for the Prairie province’s collision repairers.
This year’s Fall Conference was held both in-person and online as SAAR executive director Tom Bissonnette led the event. Sessions were broadcasted via Zoom for all attendees to enjoy.
Fall festivities ramped up with a meeting between SAAR and Saskatchewan Government Insurance (SGI) executives Ciaran Downes, senior director of national appraisal operations for SGI, Ryan Smith, vice president of SGI’s claims and salvage operations, and Lyle Andrusiask, director of appraisal image audit and accreditation.
The team took two hours to discuss ImageDesk audits while answering questions on the Safe and Quality Repair Program, which requires Saskatchewan facilities to reach I-CAR Canada Gold Class certification by Mar. 1, 2021, in case they suffer slashes to labour rates.
Currently, SGI has no plans to extend the deadline for Gold Class accreditation.
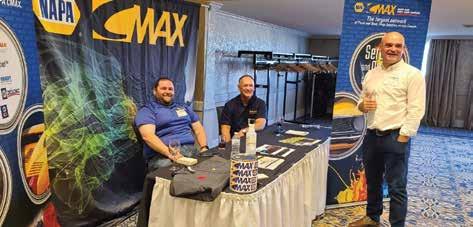
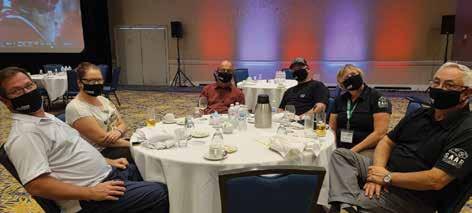
All in-person attendees were given their own masks, and SAAR members sported them with style.

Jeff Francis, Wedge Clamp’s technical sales manager, brought the company’s 3D measuring system to SAAR’s Fall Conference, along with a host of other Wedge Clamp products.

Fred Castonguay of Stephenson Equipment brought Chief Automotive’s host of autobody products for SAAR members to enjoy, including his one of his favourites—the MI200 spot welder from Chief.
During his session, I-CAR Canada director Andrew Shepherd started the Saturday session by delivering a brief update on the province’s progress toward I-CAR Gold certification and delivered surprising stats on how many shops have yet to hit Gold Class status.
According to I-CAR Canada, 25 facilities have reached Gold Class certification and 19 have met Gold Class Aluminum standards, while a further 10 stands at ‘Gold Class in Progress’ status.
Nonetheless, Shepherd has few fears that those still seeking the seal will meet it come March. He says, the required program can be completed in as little as six weeks.
“We’re on the doorstep,” said Shepherd.
A few shop owners shared their concerns about securing their spots in the welding classes required for the certification.
Fortunately, Saskatchewan Polytechnic is prepared to offer COVID-compliant welding courses to help those still reaching for Gold Class meet their goal come March.
The college has resumed on-campus training, and instructors will be working seven days a week to help facilities reach their Gold Class certs.
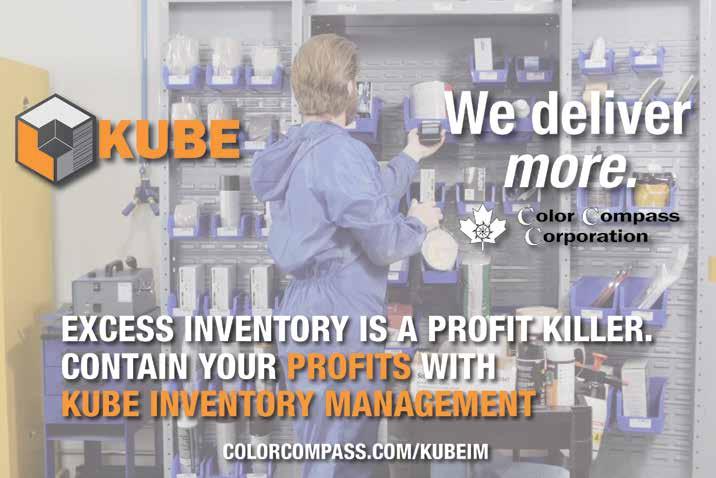
UNDERSTANDING ADAS Level5Drive shares the ins and outs of ADAS calibration
Understanding how to calibrate today’s advanced-driver assistance systems (ADAS) is critical in collision repair operations. If you disagree, ADAS experts John Marlowe and Giuliano Bernabei can prove you’re wrong.
The two-man team, founders of ADAS calibration centre Level5Drive in Burlington, Ontario, have made it their mission to provide the automotive aftermarket with valuable ADAS knowledge while helping streamline ADAS calibrations.
ADAS are the fastest-growing segments in automotive electronics, and John predicts that the coming years will see virtually every car manufacturer feature ADAS in its vehicles. Startlingly so, a recent survey from the U.S.-based Equipment and Tools Institute found that 38 percent of new car dealer shops are not equipped to manage the repair and diagnosis of ADAS and passive safety systems; that number jumps to 74 percent for independent repair shops surveyed.
Facilities that may be capable of completing ADAS calibrations can land themselves—and their customers—in hot water if they fail to fully understand the systems.
Luckily for the Canadian sector, John and Giuliano are here to help. The duo sat down with Collision Repair to help the industry better understand when calibrations are required, the critical performance of the operation and what you need to offer them in-house.
Q: If there is nothing on the dash, does that mean that you don’t need a recalibration?
John Marlowe: Absolutely not—that is a huge misunderstanding.
Very often these systems are out of calibration, even without a dash light or a DTC indicating so. The systems will set a light if the sensor has been unplugged, and if the system has been physically impacted or damaged you are also likely to get a dash light. In some cases, the sensor can determine when it’s so far off the mark that it can’t be functional—it can set a diagnostic trouble code for that.
But there are a lot of instances where you have a vehicle going down the road with a misaligned sensor and, when there’s a vehicle 25 feet in front of it it’s detecting it fine. But once you get on the highway and are travelling at high speeds, it may not detect a vehicle in the time required to properly slow down using the adaptive cruise control. There are tons of examples for situations like that, and these are the stories that cause people to lose confidence in their ADAS systems.
Q: What is the average time it takes to do a calibration on a vehicle?
JM: It takes Giuliano and I about 90 minutes, but for other centres it really depends on the facility’s capabilities. In imagining what they go through trying to maintain their cycle times, trying to keep everything on the level it needs to be on—I can’t see anyone completing calibrations faster than we do.
A shop’s target is probably about 90 minutes per calibration. For us at Level5Drive, we try and make this as easy as we can for the shop, so we pick up, we deliver, we take care of it all.
Q: How current is ADAS vehicle data if an aftermarket scan tool is used? How long do you wait for a new-modelyear vehicle to perform a calibration?
JM: As with all things when we’re dealing with the secondary market there is always a delay with the software coming to companies like us or any other collision repair [centre] that is using a tool like the launch scanner or any non-OE scanners. Having said that, we have data for 2021 models that we can calibrate. They are maintaining currency at a level I haven’t seen before.
Q: How have manufacturers reacted to third parties performing calibrations on their vehicles? Does it affect the warranty at all?
JM: Manufacturers are understandably unable to look at us and say “Hey go to them and go do that, those guys are great.” They can’t, for obvious reasons.
However, by and large, the ones we’ve spoken to understand that we really are fighting the same fight. We really are making the customer experience what it should be for their customers and try to maintain that level of trust and that level of happiness with their ADAS systems. We’re really contributing to that in a way that their own service departments may not be able to do. Will OEMs be coming to us saying “You guys are great, do our cars!”, probably not going to happen—but the OEM saying, “Don’t go to those guys,” is also not going to happen. We’re too much on the same team. Dealership service departments suffer the same constraints as a collision repair shop trying to add ADAS calibration as part of their business.
Q: How much space do you require for in-house calibrations?
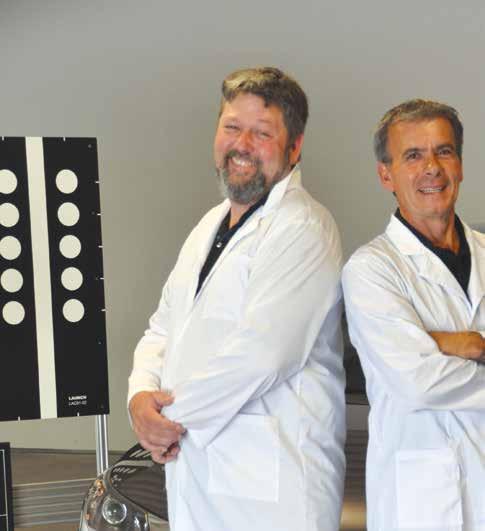
JM: It really depends on the calibration that you’re doing and what type of vehicle it is. For example, in some Mercedes products, if you have a place to park the car that’s flat and level, you can put the target board right against the front bumper, so you don’t need a great deal of room for some of these things.
Other jobs, for example, some Honda products, you need 10 metres (30 ft.) in front of the vehicle as well as significant distance on the sides. You need to be adaptable to many different requirements and have ample space if you’re going to do them in-house.
Q: Have you ever encountered difficulty while trying to calibrate a system once an aftermarket sheet metal part, bumper or glass has been installed?
JM: Yes, we have, in fact. The manufacturers are not saying something that’s untrue when they state that you can’t calibrate with aftermarket parts. We have had bumper covers that have been a bit of a challenge and certainly, windshields are a little bit unpredictable sometimes. Some appear to be just fine.
Even on a repaired bumper where the blind spot detection might be on the corner—which it usually is—if the mill buildup is too great it won’t read through that. So you have to go back and put another bumper on it—an OEM bumper to be able to calibrate it properly.
Our ideal would be to not calibrate vehicles with aftermarket parts on them, but the reality is that they’re going to go somewhere else if we don’t do them. At least we can ensure that the process was followed correctly.
Q: Do systems have to recalibrate after a repair, wholly replaced or R&I’d?
JM: In most cases, we would strongly recommend that you consider a calibration.
If you’re looking at a sensor that is now uncovered, there are so many variables you can introduce. Did it get touched while the protective part was off, like a bumper cover for example. Did it get knocked while it was being installed? You may change the installed position of the part so when this piece was calibrated initially it’s looking through a piece of plastic on a bumper cover that is however many millimetres thick, you’ve now placed it in a different position and maybe it’s no longer looking through the exact same place. It might not return the exact same data that it used to.
The rule of thumb is, if you’re looking at an exposed sensor, you’re probably going to want to calibrate it.
Q: Do you think there should be specific compulsory certifications for technicians who are calibrating ADAS?
JM: Ultimately, yes, I think it needs to be its own class, it’s very own segment of the industry. We should have some method of identifying people who possess the skills to be able to do this. Right now, I don’t know that we have a whole lot of faith in our trade system and the level of training that we brought our existing technicians to. Certainly, I think we need to have a fresh-start segment for ADAS calibrations that may extend into other electronic options on the vehicle.
JM: As far as what’s new coming down the pipe, there’s been a lot more focus on stereoscopic measuring on the front cameras, so they have new capabilities that move us a little closer to level three driving when the camera itself is able to measure more accurately.
Also, while there are no production vehicles using LIDAR as of yet, that is coming. Likely they will have limited functionality initially, but you are going to start seeing cars with LIDAR soon. What’s new with ADAS is the cars that it’s on.
Look at Nissan—its least expensive 2020 entry-level model uses ADAS. The big news is the number of vehicles it is present on now. We’re not far from every new car having it—we’re probably less than three years from that.
JM: It really depends on each facility’s situation. If you’re looking to offer calibration services as an add-on to your existing collision repair business, there are success stories out there. There are people doing great with it.
There’s a lot of thought you’re going to need to put into it. Your facility has to be absolutely set for it. You can’t make compromises—it can’t be, ‘meh, sort of, pretty good’. You have to have the correct facility to be able to do it and you have to have a technician that is willing and able to follow the processes correctly and document the way that we need to.
We’re always happy to answer any questions or work with facilities on offering calibrations.

This is a generic list of some circumstances that will require ADAS calibration. The OEM documentation is our gold standard, but there are a number of conditions that also require consideration. The short version is, if you can’t state with 100% certainty that the vehicle’s ADAS equipment is correctly calibrated and will perform under ALL expected conditions, then you need to have it calibrated. A test drive is not a diagnostic.
• Rear camera unplugged • T/gate adjusted or repaired • DTC or not performing properly • Required by OEM statement
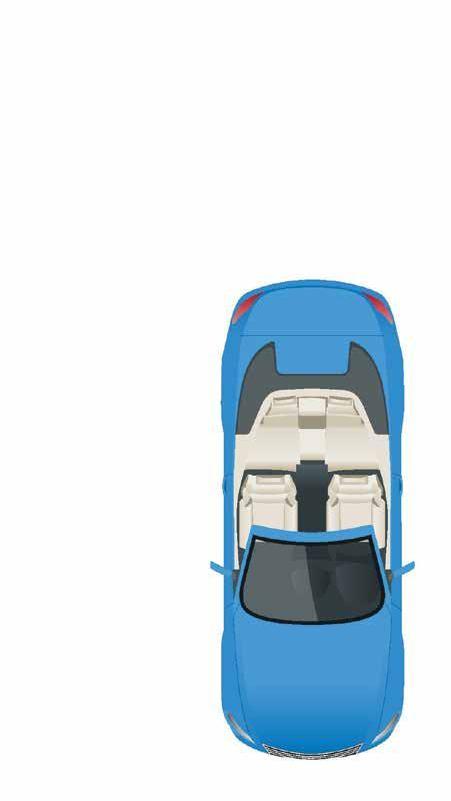
• Rear bumper cover removed • Rear impact • 1/4 panel deformed near BSM • DTC or not performing properly • Required by OEM statement • Sensor uplugged
• Windshield removed • Camera bracket impacted or bent • Camera unplugged • Wheel alignment performed • DTC or not performing properly • Directed by OEM statement • Frame/unibody damage
• Door removed or adjusted • Mirror removed or unplugged • Pillar/door frame damaged • DTC or not performing properly • Directed by OEM statement
• Front bumper cover or grille removed • Wheel alignment performed • Front impact • Frame/unibody damage • DTC or not performing properly • Directed by OEM statement • Sensor unplugged