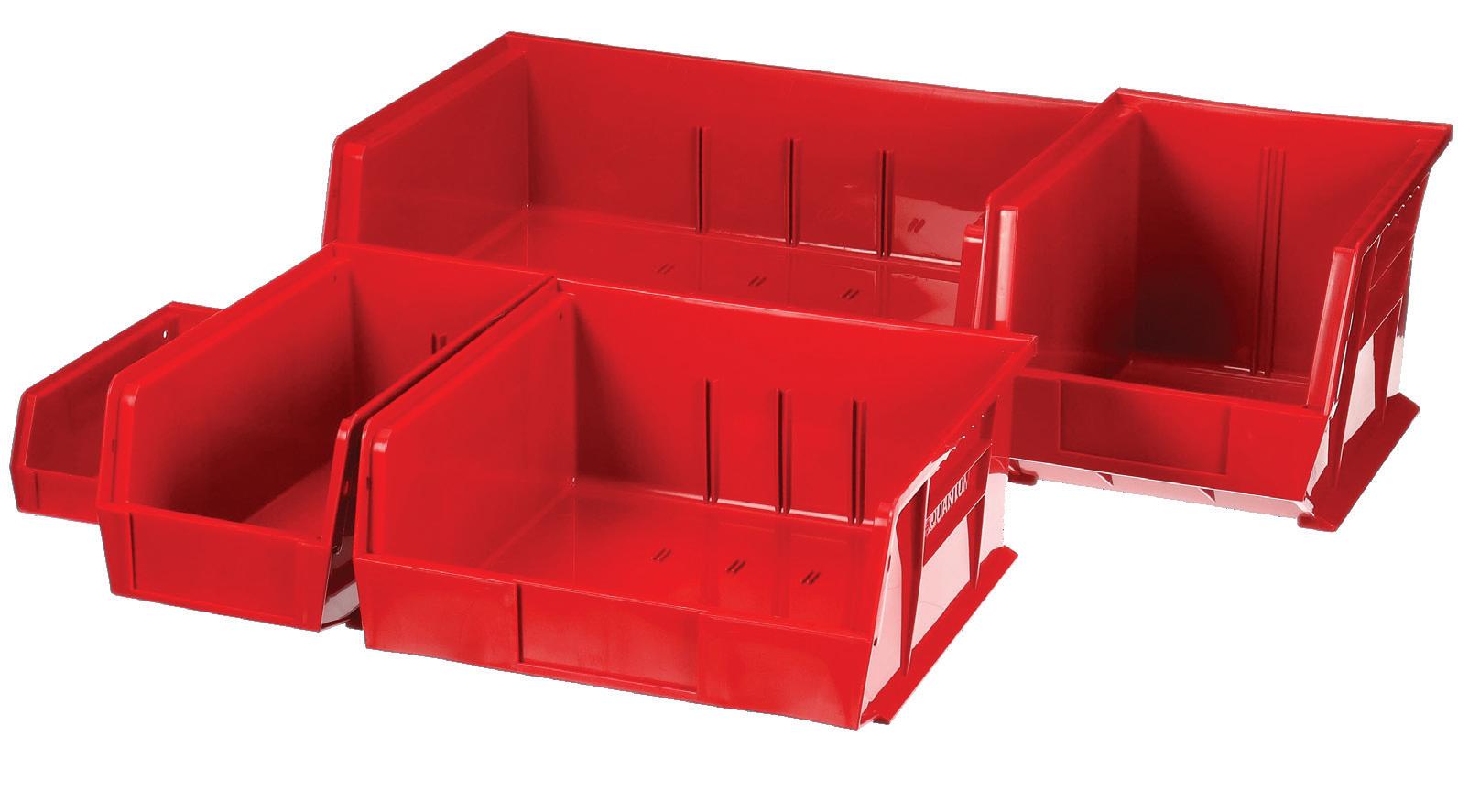
2 minute read
STACKED TEAM
Story by ALLISON ROGERS
When you look at your ducks, would you consider them to be in a row?
Anyone in this industry is more than aware of the many moving parts that come with running a collision centre; a bodyshop’s gears run consistently, and even the slightest slowdown sends a ripple of interruptions throughout the process, at the cost of patience and precious dollars.
We’ve all heard, in this day and age, tales of how technology can streamline operations and optimize efficiency across the board —but how often are we privy to information on how a business has integrated technologies to do so?
3M™RepairStack™Performance Solutions, officially unveiled last year at the SEMA Show, is a three-pronged hardware and software system that offers bodyshops high-tech inventory management, integrated invoicing capabilities and up-to-the-moment performance analytics, all under one umbrella.
The product has generated buzz around the industry for its ability to offload and automate inventory management as well as its capabilities in collecting detailed data to help in-the-know shop owners make key business decisions.
Collision Repair magazine recently spoke to Andy Boyd, digital platform leader of connected bodyshops for 3M Automotive Aftermarket.
One of RepairStack ™ ’s most attractive features is automated inventory management with automatic ordering and inventory tracking for both 3M and non-3M materials.
“RepairStack™is designed to transform storage,” said Boyd. “It’s for the shop owner who is looking to add bottom line improvements and use technology to aid in managing inventory across the shop.”
RepairStack™shops stock their cabinets with the materials of their choice, and each material has a barcode associated with it. The user scans the barcode via the provided scanning tool—an iPod Touch with an attached scanner—and selects the quantity of material used and removes the material for use. The cabinet is unlocked via Bluetooth—you can even see which of your staff pulled the materials.
Users set minimum and maximum inventory levels. When product hits the minimum level, it automatically sends an order to your distributor.
The second of the RepairStack™pillars— integrated invoicing.

The program is designed to streamline blueprinting and billing by automating scanning and invoicing via two-way integration with your bodyshop management system. The inventory management system captures inventory usage and helps to assure all procedures and materials are precisely documented to their respective ROs, says 3M.
“That’s huge for material reimbursement,” explained Boyd.
There were 90 Canadian customers on the RepairStack™platform when Collision Repair magazine spoke to Boyd at the end of March. In the States, there were more than 2,500 users on the platform. Top-performing users have seen significant results when recovering material costs—in fact, Boyd said that, in the U.S., users on the platform have the potential to recover over $1,500 per month.
RepairStack™integrates with CCC, Axalta
ProfitNet, and Body Shop Connect (Canada) today. 3M is pursuing ongoing integrations with leading body shop management software, distributor and paint company order portals, and more.
Compare month-to-month spending; view invoice records according to RepairStack™’s precise inventory tracking; monitor material usage by tech—there are boundless opportunities.
Boyd says the ideal user is a shop owner dedicated to working on their business: someone who keeps a keen eye on the bottom lines, follows standardized operating procedures and is consistently driven toward better results.
“The ideal [RepairStack™] user wants to be better. It’s like a gym membership—you have to want results.”
While that tends to be heavy-lifters or multi-shop operators, Boyd maintains that there are no restrictions to who can use the highly customizable platform.
Not only are there ample on-demand training modules to teach staff the ins and outs of RepairStack™ itself—there are plans to integrate the 3M Academy Training platform with RepairStack™, offering both paid and free courses on collision repair practices.
“At 3M, we’ve been creating automotive products since the dawn of the automobile. We’re simply looking to provide continued, dedicated support for the connected bodyshop.”

Q: What if I buy from more than one jobber?
3M says RepairStack™ allows for flexibility to fit your shop demands.
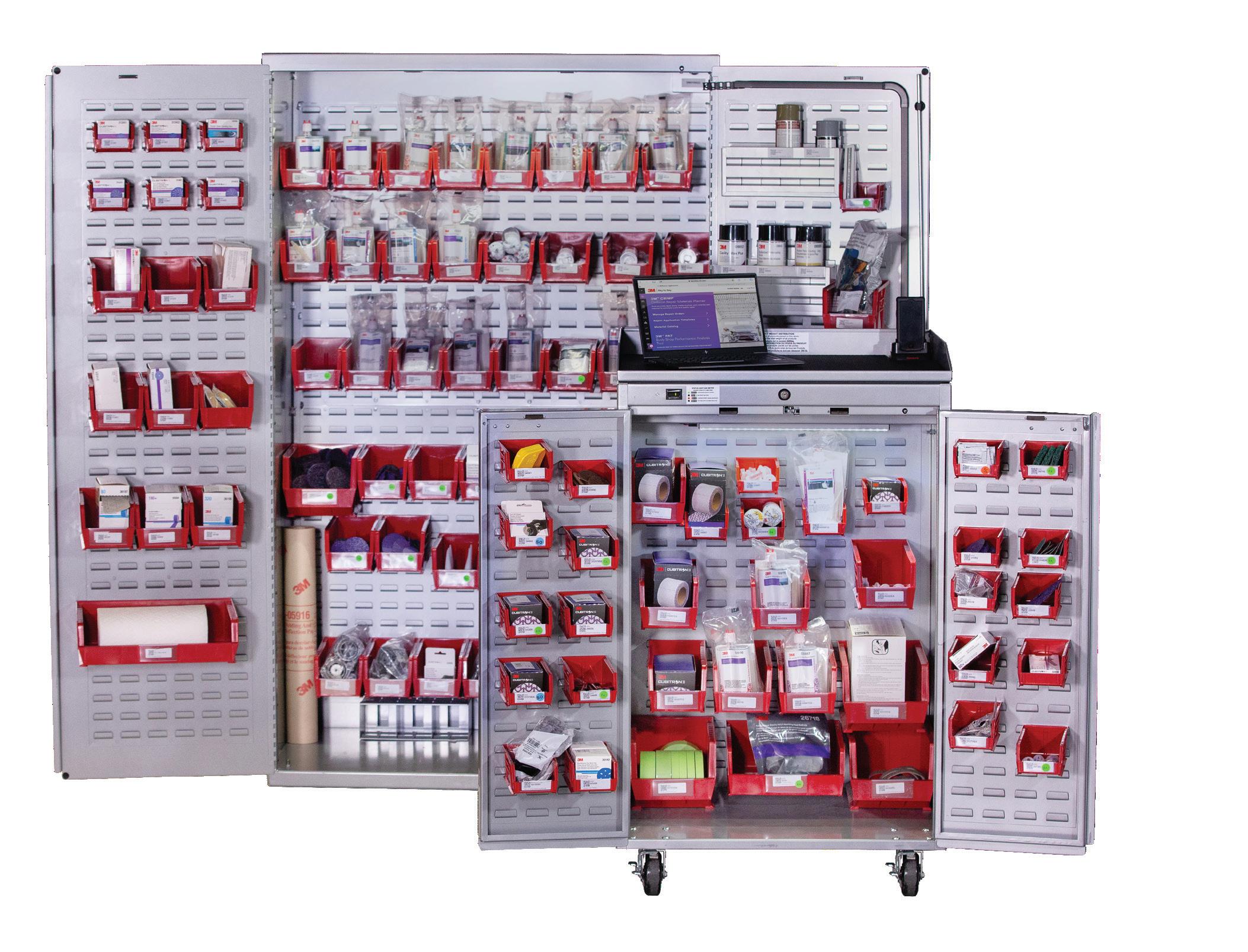
When supplies are removed from the cabinet, the user simply scans the barcode and RepairStack™ keeps track of your material supply levels. Materials are automatically reordered when they hit the user’s designated minimum level, customizable to your shop’s needs.