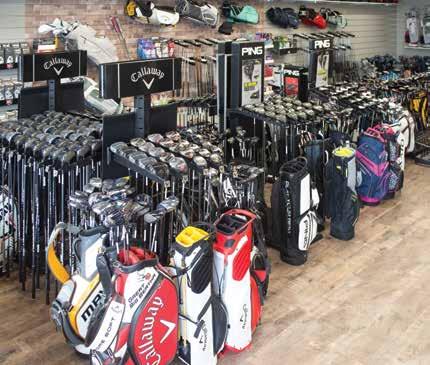
4 minute read
Player’s Corner Profile
assembly workshop, which does double duty as the ski and snowboard mounting, tuning and boot fitting area in the back of the shop, while working within the confines presented by the existing 3,000 feet of floor space.
“My dad has done such an amazing job in this place over the last 38 years just the way it was, but I told him that I wasn’t sure I could do this for the next 10 or 15 years if the shop stayed as is,” Nick adds. “It is tight in here and it’s always going to be tight. We’ve really grown the business, so I knew if we could utilize the space better, it would be more enjoyable for our customers and a better work environment for the staff.”
Along with the inherent space limitations, what made Goff’s assignment particularly challenging was finding a Yin and Yang balance between golf and snow sports, having to keep in mind that the shop does about 40 percent of its business in skis, snowboards, bindings, boots and boot fittings. After studying the store’s footprint, taking copious measurements and gathering input from Lenny, Nick and staffers, Goff came up with initial ideas on how to reorganize the space to function more efficiently for both camps. Several revisions later, a final design was determined, which basically rotated the interior clockwise about 45-degrees.
Entering through the front doors, customers now see three brand new fitting bays along the right side and the point of sale and payment register to their immediate left. That is now where gloves, tees, balls, headcovers and other incidentals are available. Corralled by a short wall, the putting area moved closer to the back of the store, while hard and soft goods (think clubs and bags during golf season; skis, boots and snowboards during winter months) occupy most of the remaining space. The left side serves as a ‘slot wall’ where seasonal merchandise is suspended by slot shelving.
Being a small, family-owned business, the shop couldn’t simply close during remodeling, so work was performed in stages by TB Custom Builders, a Castle Rock/Denver-based contractor with phase one focused on building the floor-to-ceiling fitting bays.
“The new bays have GC Quads, the $20,000 launch monitors you see when you watch ‘Live from the Masters’ on the GolfChannel,” Nick explains. “We chose them over Trackman because we think they work better indoors and align better with our space.”
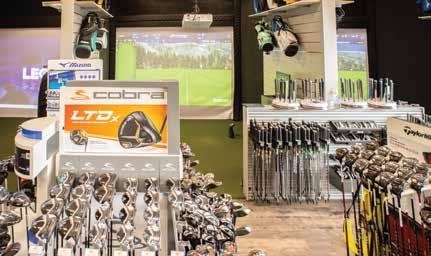
Despite having what he believes are six of the best club fitters in Colorado, it pained Nosewicz to see his guys having to maneuver around the cramped and poorly laid out workshop, likening it to episodes of chef
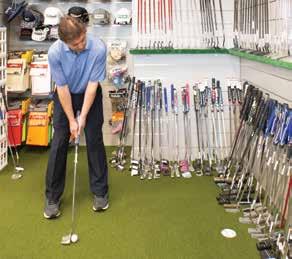
MAKING ROOM WITHOUT EXPANDING:
Lenny’s, the golf and ski shop on Denver’s Parker Road, has been refurbished to make the tight quarters more comfortable for staff and customers.
Gordon Ramsay’s ‘Hell’s Kitchen’ where contestants were all but tripping over each other to make dinner service work without patron-angering delays and disappointments. He credits a 2022 trip to Augusta National for a much-welcomed change to that vitally important area where clubs are built and repaired, as well as where bindings are mounted on skis and snowboards, edges and bottoms of those products are sharpened and repaired, and boots are adjusted.
“I was invited to The Masters last year and was able to tour the PING trailer,” Nick says. “I took a video of how they store their grips, shafts and club heads, and was impressed at how efficiently that limited amount of space worked....”
He shared his findings with Goff and his sensei of club fitting, T. Marcus Hughes, who goes simply by the letter ‘T’. Aside from being a lifelong friend, T has been at Lenny’s Golf & Ski for going on 25 years. With many of the PING-trailer-inspired ideas incorporated into the phase-two makeover, along with custom-built workbenches, component storage cabinets and drawers, and improved lighting, the workshop is organized and measurably roomier.
“Without T there’s no Lenny’s,” Nick continues. “Not only is he one of the best golfers in Colorado, but he also has kind of a cult following as a fitter, which is a reputation he’s really earned. Some of our customers only let T work on their equipment. We are so lucky to have him.”
With as many as three, four and even five techs at a time sharing the workshop space—some working on skis and snowboards, others doing golf associated work—the retrofitted area is vastly more efficient than its predecessor.
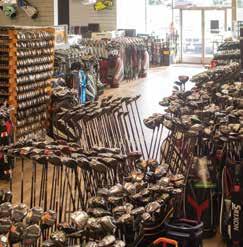
The final phase saw the installation of entirely new flooring, display and overhead bar and track lighting, including highly illuminating LED light panels, a new coat of paint and a modification of the drop-down ceiling to create more of an open feeling throughout the store. Nosewicz and Goff took cues from Jon ‘Fitzy’ Fitzgerald, a 15-year veteran of the Lenny’s team and sales manager to improve the retail experience. A skilled club fitter and savvy merchandiser, he brought his expertise to the floor—literally—so now customers can more easily browse the displays, soft goods and slot wall offerings. Though the store underwent significant changes to its interior, the Nosewiczs were acutely aware of the importance of keeping its legendary, ‘old fashioned’ service level and folksy environment.
“Lenny’s is very much like ‘Cheers’ where I feel like we are more than just a place to buy clubs or skis,” Nick says. “I think of it as a barbershop where people come to hang out and talk golf and look around. There are a lot of things we have going for us that will never change like that welcoming feeling from our staff when people walk in. I didn’t want to lose the Lenny’s vibe with the renovation and hopefully after this project that energy is only going to be enhanced for customers coming through the door.”