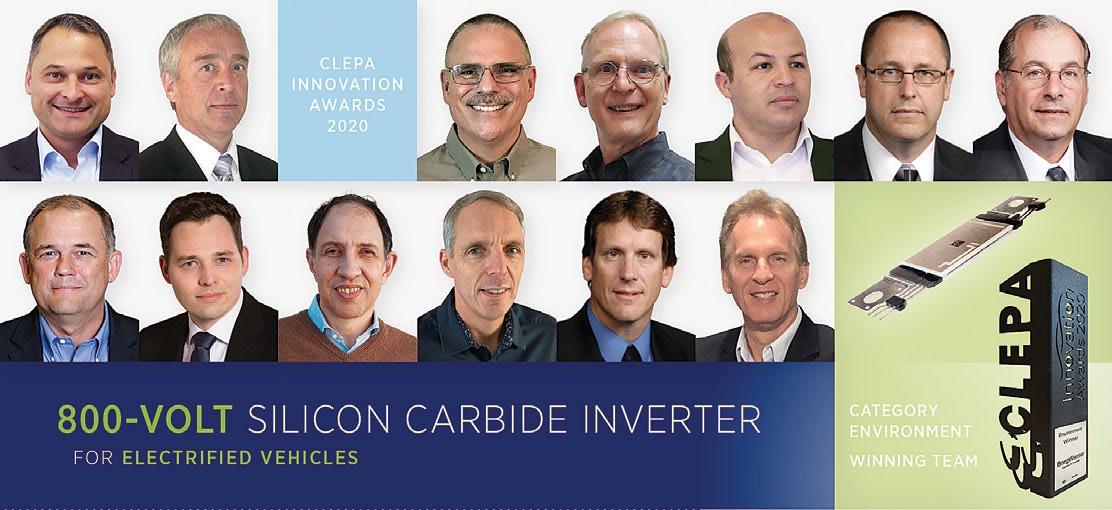
23 minute read
Mobilised
BorgWarner’s dual-sided-cooled inverter is the first-to-market inverter using a silicon carbide-based power switch. Ashish Bhatia looks at the inverter designed for an 800V application.
Advertisement
D
riven by the climate change commitments made by the Indian Government during the COP21 Summit, Paris to reduce emission intensity by 33-35 per cent by 2030 from the 2005 levels, electric mobility continues to be high on the agenda for governments globally. The government’s the world over are relying on the technological prowess of automotive component manufacturers and their tier suppliers to achieve the ambitious goal of zero emissions by 2030. The industry together with the government is working towards reorienting businesses to meet modern-day needs and to do its bit to reverse climate change through such innovative and advanced next generation solutions. BorgWarner has taken it upon itself to improve upon the erstwhile generation of inverters used for electric vehicles. In electric vehicles, an inverter is a device that converts Direct Current (DC) power to the Alternating Current (AC) power known to be used in an electric vehicle motor. It has the capability to change the speed at which the motor rotates as it adjusts the frequency of AC.
First-to-market
With its ‘Dual-Sided-Cooled Silicon Carbide Inverter’, the company is claimed to have introduced the first-to-market inverter using a Silicon Carbide (SiC)-based power switch for an 800 volt application, The BorgWarner component is claimed to deliver increased efficiency for enhanced voltage flexibility, improved recharging times, better range and smaller battery size for cost reductions. For instance, the inverter’s SiC technology is claimed to extend electric vehicle range by c.5 per cent and enable faster charging times at 800 volt in comparison to the 400 volt systems. The Viper power module boasts of dualsided cooling for enhanced thermal management.
The use of SiC helps extend PHEV and BEV besides contributing to the range extension and faster charging also delivering a better solution with more power. Its advantages include a smaller package that is also cost effective. The patented technology has won many accolades including being adjudged as the ‘Innovative E-Mobility Solution’ for which the company was adjudged as the ‘Supplier Of The Year’ at the Auto Components India 2021 Awards earlier this year. Notably, it eliminates the need for wired bonds or connections often blamed for the cause of quality and reliability issues. It also optimises switching and conduction to deliver up to 70 per cent reduction in power loss.
In effect, the Original Equipment Manufacturers (OEMs) can look forward to room for creating more compelling consumer propositions for hybrid and electric vehicles. The additional room is believed to have the potential to lead to a broader acceptance of e-mobility in compliance with the government-mandated emissions targets. The patented capabilities are aimed at giving manufacturers the propulsion system design flexibility and performance in line with the strategy to capitalise on the market pull. The resultant vehicle mix and volumes could help meet the increasing emissions regulations.
BorgWarner’s Bengaluru Technology Centre is known to have contributed to the design of the product under multiple competencies including systems, software, test and verification, electrical analysis and simulation, mechanical analysis and simulation. On the software front, critical features design and development confirming to the ASPICE model, for example, the bootloader, functional safety mechanisms, control features, diagnostics, cybersecurity – HSM etc were worked upon. The centre also contributed to the hardware and factory test software for testing the control board hardware besides being involved on the unit level software testing of all the features. On the systems engineering front, the centre is known to have contributed to the requirements definition and the algorithm development for key critical features for example critical temperature sensing and diagnostics of the SiC MOSFET. It is known to have been involved in testing and verification, software qualification, integration and regression tests on the test simulators for various key features referred to above. The process involved continuous integration and qualifying the SW on the product against customer specifications. The team carried out continuously system test cases development on Motor sim and Dyne benches to confirm the superior performance of the SiC based Inverter product functionality. It also involved the automation of suite of software tests for most of the control features. In case of electrical analysis and simulation, the tech centre contributed to the worst case analysis and simulation of different electrical hardware circuit blocks aimed at the verification of hardware design for meeting the specified requirements. Multiple design and part changes were suggested to lower BOM cost and improve design. The EMI simulations were carried out to ensure emission outcomes were within specified standards. In case of the mechanical analysis and simulation, the centre contributed to ensuring that the product meets the customer specifications, both thermal and structural simulations by means of computed aided simulations known to have been performed for the product. The thermal and vibration characterisation studies were carried out on the modelled SiC MOSFET packages leading to the improvement of the overall performance under different loading conditions and hence adding to the reliability. ACI
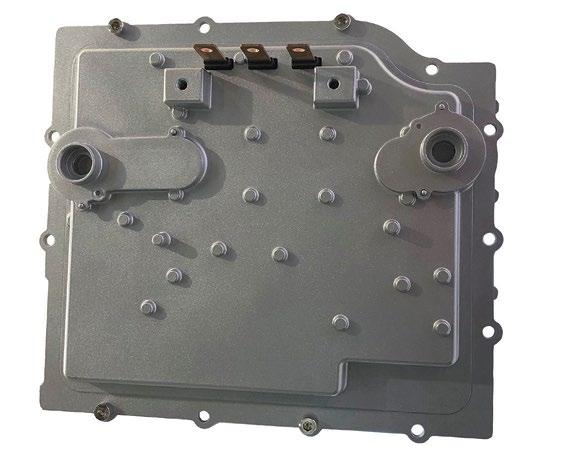
Key Benefits Of 800 volt Silicon Carbide Inverter
c Viper power module includes dual-sided cooling for enhanced thermal management. c SiC helps extend PHEV and BEV range by approximately five per cent and enables faster charging times - delivering a better solution with more power, in a smaller package and for less cost. c Award winning, patented technology eliminates the need for wired bonds or connections that can be the cause of quality and reliability issues. c Optimises switching and conduction to deliver up to 70 per cent reduction in power loss.
Mobilised Valeo Electric Powertrains
Valeo partners has partnered with Omega Seiki Mobility. Prateek Pardeshi looks at the scope of the partnership involving electric powertrains for the latter’s vehicle range. P
Powertrains are the building blocks of a vehicle. In line with the Omega Seiki Mobility (OSM) strategy to build a powertrain suited to the duty cycles of three-wheelers for cargo transportation, the Original Equipment Manufacturer (OEM) has found its powertrain partner in Valeo India (Valeo). Valeo has signed a Memorandum of Understanding (MoU) with Omega Seiki Mobility (OSM), part of the Anglian Omega Group, under which the company will provide electric
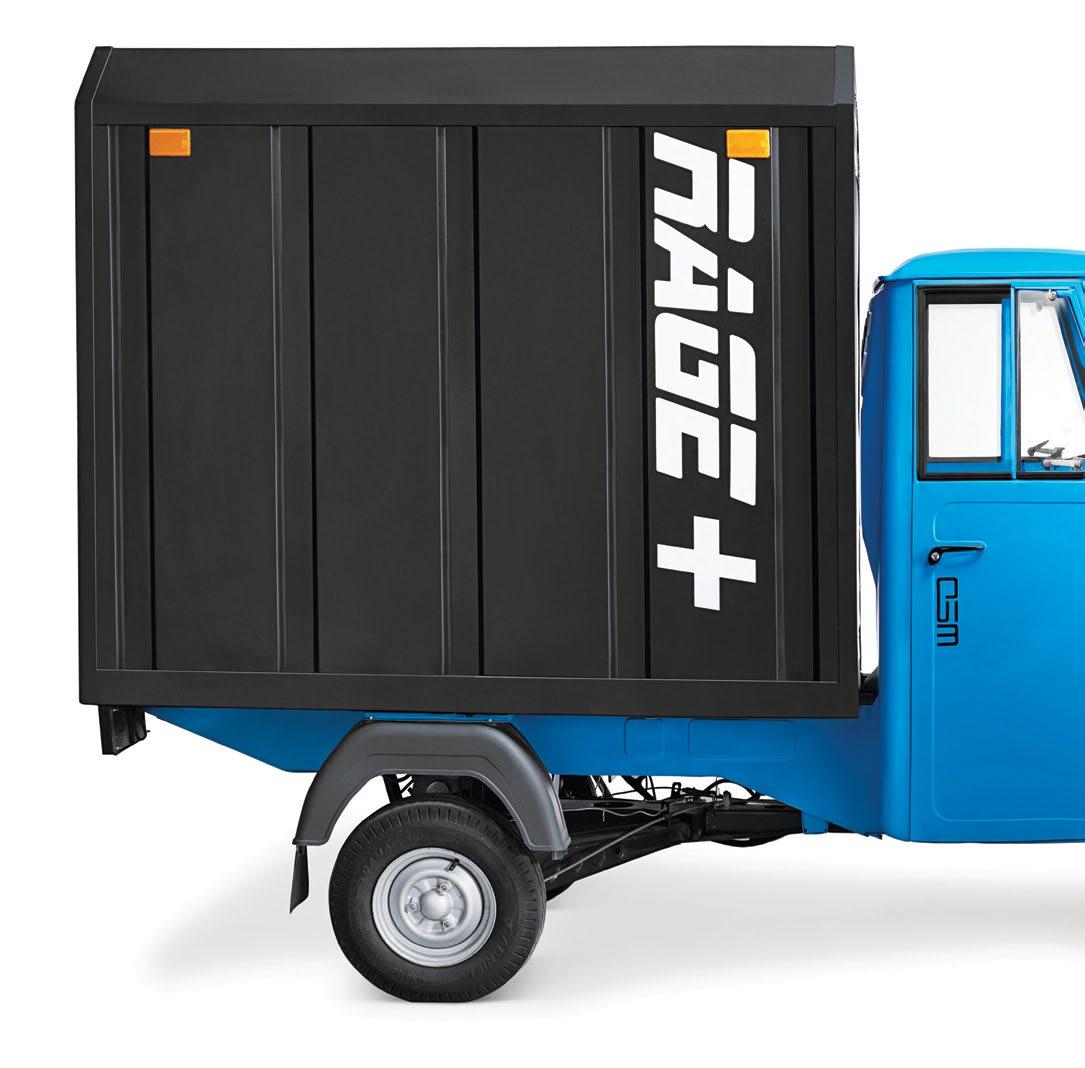
powertrains for the OSM electric vehicle range. The two partners aim to deliver on the carbon emission reductions through the collaboration. Here, Valeo expects OSM to leverage its expertise deemed suited to the target segment of small commercial vehicles. Averred Jayakumar G, Group President, Valeo India, “Omega Seiki will benefit from our deep understanding of not only the electrification technologies but also the unique needs of integrating electric powertrain in the small mobility format of vehicles.” “I am positive that Valeo’s advanced technologies, our strong engineering combined with manufacturing expertise in India will help us to strengthen our partnership and succeed together in this rapidly growing segment,’ he stated.
48V e-powertrain
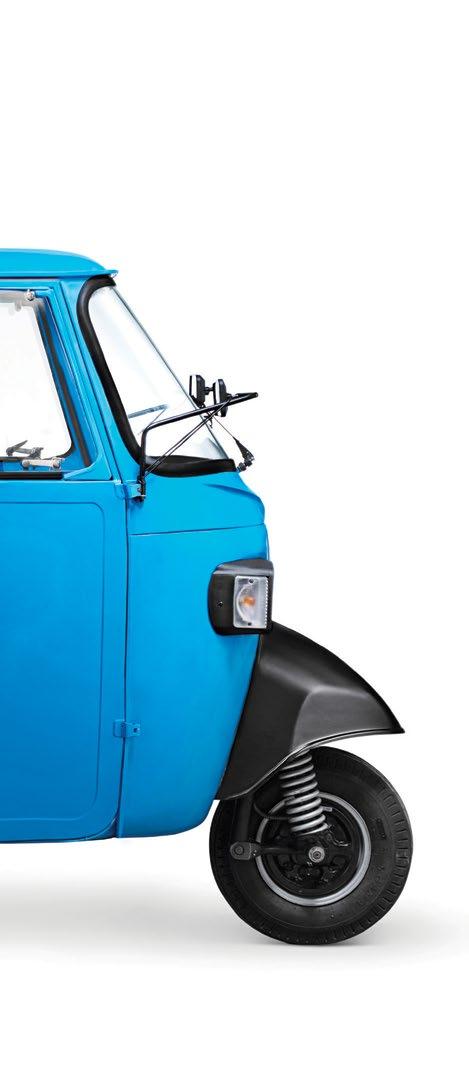
Valeo will provide its 48 volt electric powertrain system from its manufacturing plant, in Pune. The powertrain is known to constitute a reducer, an integrated motor and an inverter to go along with the Powertrain Control Unit (PCU) for OSM’s cargo three-wheelers range comprising of ‘Rage+’ and ‘Rage+ Frost’. The vehicles under the Rage+ brand, for instance, have already been deployed by several major e-commerce and logistics companies in India.
“We are thrilled to partner with Valeo. This association will allow us to address the core issue of reducing carbon load in the atmosphere, along with providing a sustainable solution for our product line-up,” stated Uday Narang, Chairman, Omega Seiki Mobility in the company release.
RAGE+ Powertrain
Parameters Specifications
Top Speed
45 kmph
Range
Battery Type
70-80 kms per charge
Li-ion 48V
Battery Capacity 7.5 kWh Charging Time 3-4 Hours Acceleration (Boost mode) 13 sec Regen at IDC 15 per cent Rated Power 4.8 kW
Battery Warranty Three Years or 80,000 kms (whichever is earlier)
Rage+
The Rage+ three-wheeler cargo vehicle with a Gross Vehicular Weight (GVW) of 0.96-tonne and an open carrier box offers a range of 70-80 kilometres on a single charge as per company claims. It translates to a running cost of 0.50 rupees per kilometre Powered by an IP65 certified 7.5 kWh battery pack with a battery swap option, the vehicle is claimed to be charged in a time span of three to four hours using a fast charger. Range+ customers can look forward to a battery life of 2,000 cycles coupled with a three-year or 80,000 km warranty. On the safety front, customers can look forward to inclusions like regenerative braking, roller-cage support structure keeping in mind driver safety, a superior strengthened chassis claimed to be suited to Indian road conditions, and hydraulic braking. Both the front and the rear get are claimed to be fitted with heavy-duty shock absorbers that include a damper plus helical at the front and independent suspensions and dampeners at the rear. The company also offers a reefer variant christened ‘Rage+ Frost’ unveiled earlier this year and aimed at pharmaceuticals and food delivery aggregators.
Go-to-market strategy
In addition, Valeo’s engineers will look to provide the technology integration support aimed at helping OSM accelerate the execution of its go-to-market strategy leading to faster commercialisation of the product offering. In relation to the technology used by OSM for their vehicles to be coupled with the Valeo e-powertrain, added Dr Deb Mukherji, Managing Director at Omega Seiki Mobility,
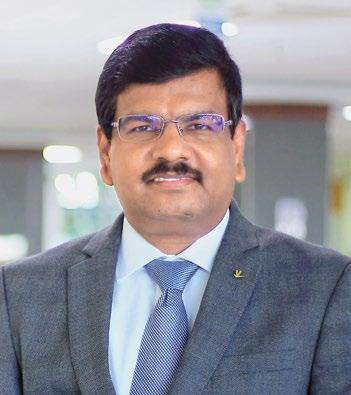
Jayakumar G, Group President, Valeo India
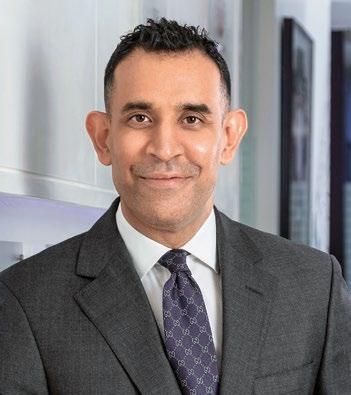
Uday Narang, Chairman, Omega Seiki Mobility
“With a global technology leader like Valeo on board, we would be providing our customers with new generation powertrains which are efficient, use latest technologies in motors, electronics and IoT, and at the same time are cost-effective too.” “That is the essence of any disruptive technology. We are very excited to be working with Valeo to introduce a new range of powertrains in the Indian market,” he expressed.
The go-tomarket strategy of this collaboration entails Valeo offering quick charging and an efficient range. It also entails keeping the Total Cost of Ownership (TCO) low to maximise operator Return on Investment (RoI). To deliver on its promise, Valeo will fall back on its globally tested 48 volt affordable systems, known to have been launched in 2020. It expects the fully integrated compact 48 volt electric powertrain system to aid in OSM’s requirement of building affordable small electric commercial vehicles. Besides three-wheelers, the Scops of the MoU extends to twowheelers aimed at both the first and last-mile connectivity requirements pan India. Going beyond the current scope Valeo and OSM will further collaborate for the latter’s upcoming vehicle models to be manufactured in India. “OSM is taking a holistic approach to not only provide innovative technology in the vehicles but also deliver high-performance vehicles at reasonable running cost through the claimed, state-of-the-art internal research and development and alliances put in place,” concluded Narang. ACI
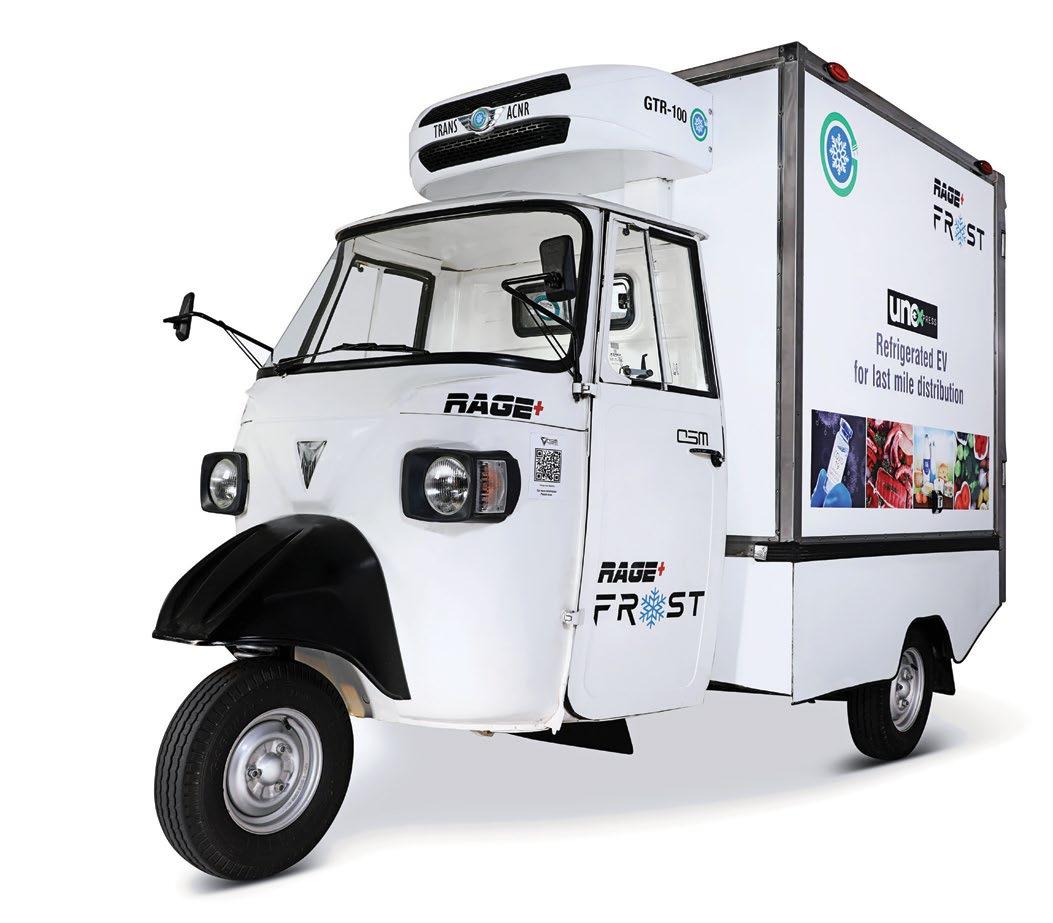
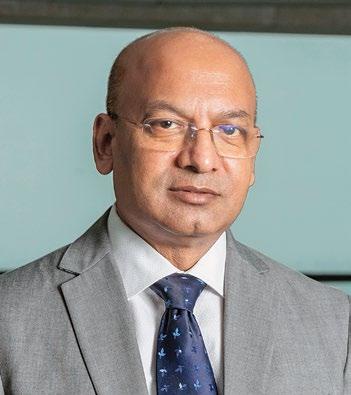
Dr Deb Mukherji, Managing Director, Omega Seiki Mobility,
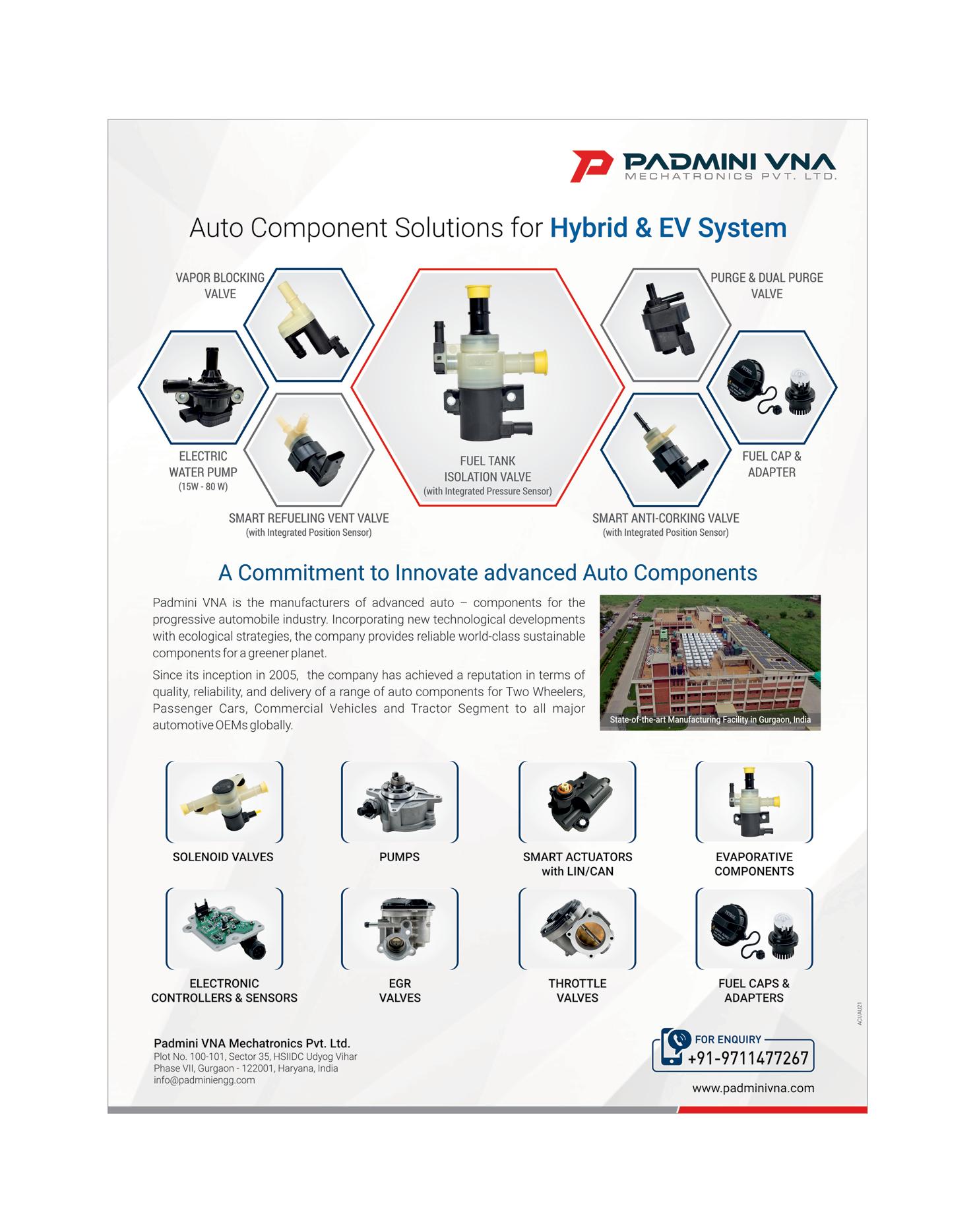
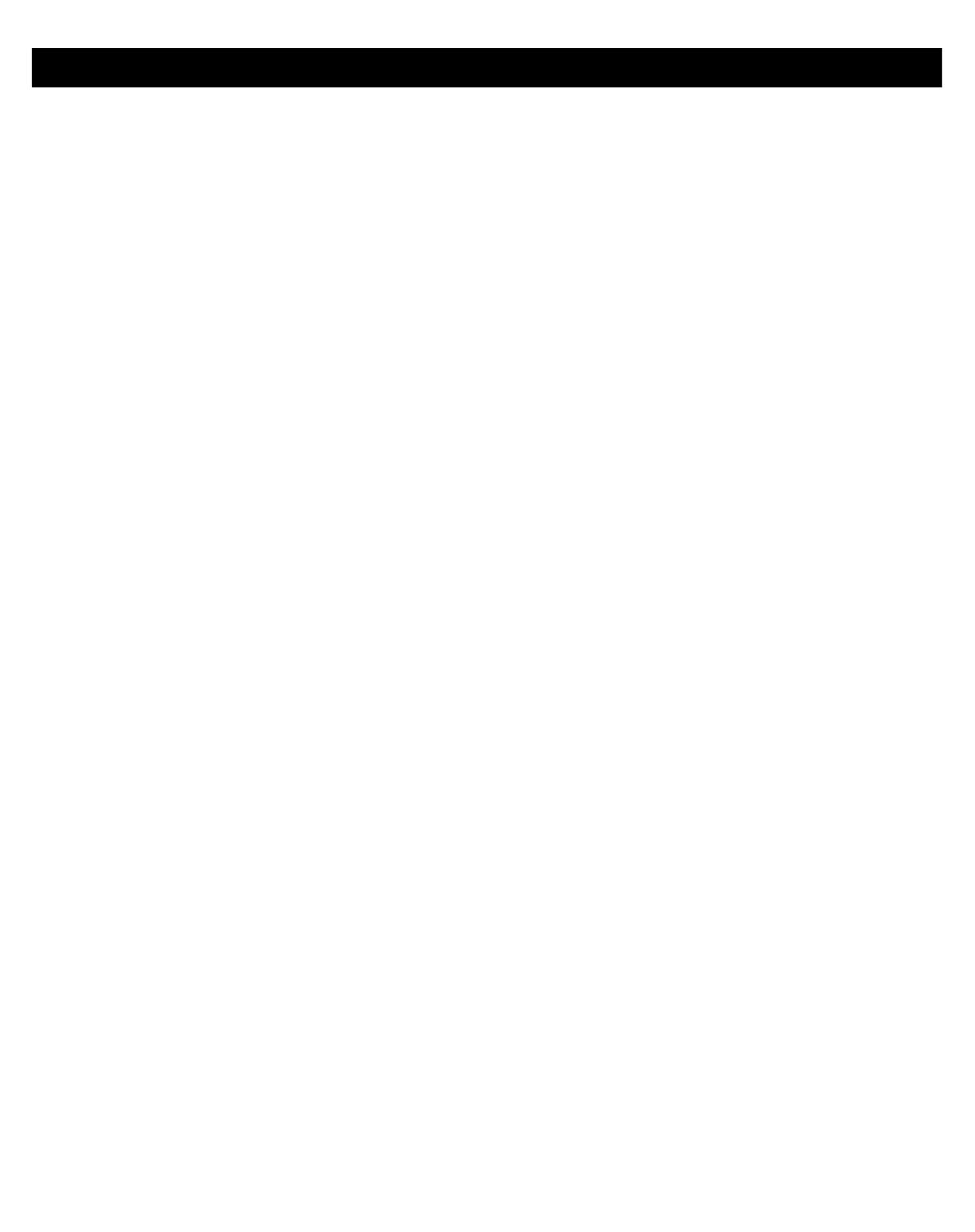
Mobilised Kistler Measurement Systems
Into dynamic pressure, force, torque and acceleration measurement technology, Kistler Group is banking on cutting-edge solutions. Team ACI looks at the modular and application-specific services.
K
nown for expertise in dynamic pressure, force, torque and acceleration measurement technology, Kistler Group is claimed to offer cutting-edge measurement solutions which form the basis of its modular and application-specific services. Finding applications in automotive development and industrial automation besides other emerging sectors, the Swiss corporation is focused on electrified drive technology, autonomous driving, emission reduction and Industry 4.0. Around 2,200 employees at more than 60 facilities across the globe are dedicated to the development of these new solutions and their localisation.
Test stands
The Test stands from the company are aimed at electrical drive systems and components on the development, production and quality assurance front. For instance, Kistler’s test stand systems are used in the development, quality control and production. The objective being to optimise the efficiency of test equipment and ensure that innovation can continue to advance. Claimed to precisely tailor to each customer’s requirements, the company takes special care to calibrate its measuring chains. The portfolio comprises test stand systems for electrical machines, generators and drive systems. Kristler has positioned itself as a one-stop solutions provider offering individual components to complete solutions in the spectrum.
Research and Development test stands
Aimed at Research and Development (R&D), the extensive range of electrical and mechanical characterisation methods offer a flexible platform. Through an open architecture, Kistler is claimed to facilitate an easy changeover of products. The test sequence on offer is adjustable and forms the base of a wide range of options to test different products like climate chambers. Kistler offers a large installed base at global certification and calibration laboratories.
End-of-line test stands
The end-of-line test stands are claimed to have been optimised for tact time, footprint, availability. It extends to the fully automated test cells including the loading process. A modular setup is said to aid in the scalability of capacity. High end measuring devices are claimed to provide superior speed and accuracy. Care has been taken to enable product tracking and complete documentation through the process. The end-of-line test stand is a certified QC tool for the end of the production line. The company has leveraged extensive experience in automotive electrical drive train production.
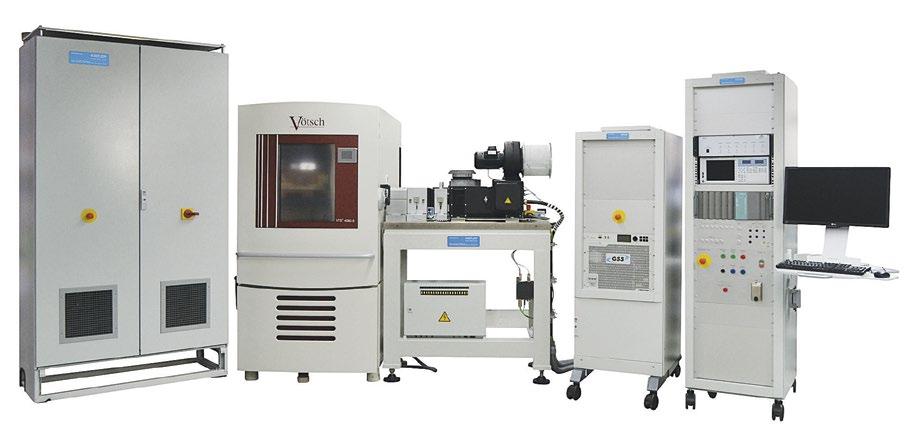
Benefits of Kistler test stand systems
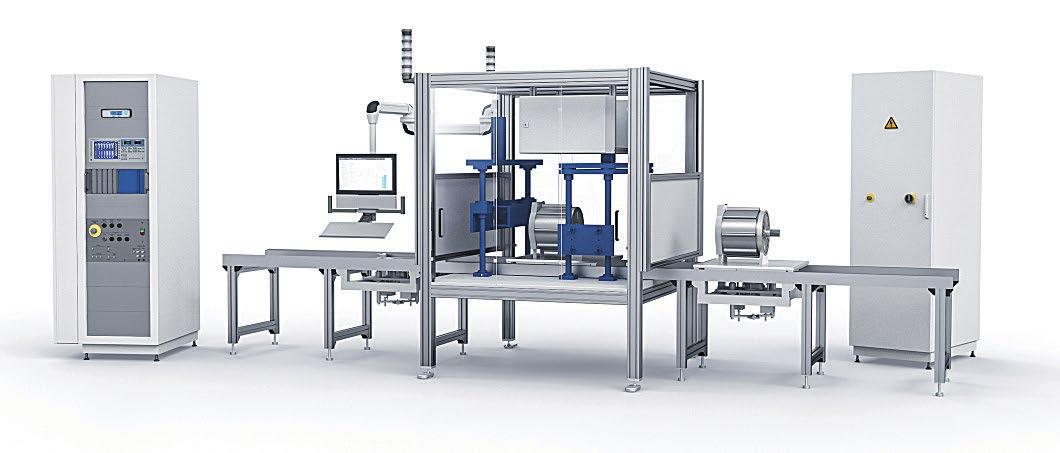
The company’s test stand systems are claimed to offer a host of benefits to end customers as listed below:
l Efficient quality control l Process reliability l The basis for developing high-quality products and boosting productivity l Enhanced efficiency and performance for electrical drive systems l Reduced testing costs l Flexible and modular customisable components, or complete systems from one single source Extensive range of services l Products that are simple to integrate.
Measurement instrumentation
For the process monitoring and quality assurance coupled with test bench and drive technology, the company is said to have aligned with the increasingly higher standards for precision in industrial manufacturing. Aimed at addressing the rising time pressure, the company has taken special care to offer a reliable suite of measuring systems. It is said to have done so with continuous collaboration with research and industry partners. The company is offering a wide range of high-precision torque sensors said to pave the way for innovative solutions in industrial measurement and system technology.
To achieve a significant improvement on the fronts of safety, reliability and efficiency – in production, as well as R&D, the company has specially focussed on undertaking intensive testing of the mechanical and electrical characteristics of its electrical machinery. It has aligned the complete test bench with the latest technological developments in an attempt to ensure maximum precision and reliability. Playing on its capabilities in measurement and system technology, Kistler is drawing on its wide range of torque sensors to cater to each and every application. Integrated Torque measurement in the production process, process monitoring to ensure zero-defect production are some of the benefits on offer. The company ensures controlled quality costs by detecting deviations at an early stage. Through flexible measuring equipment, it is claimed to optimise process efficiency. ACI
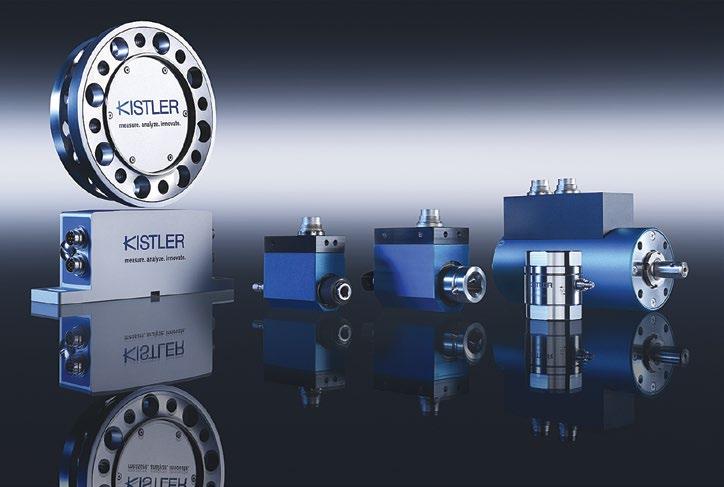
The esla Opportunity For More Indian Suppliers
Considered to be the flagbearer of EVs, Tesla, Inc has a strong supplier base supporting operations in each of its markets. Ashish Bhatia looks at this ecosystem and the underlying opportunities for more suppliers in India.
I
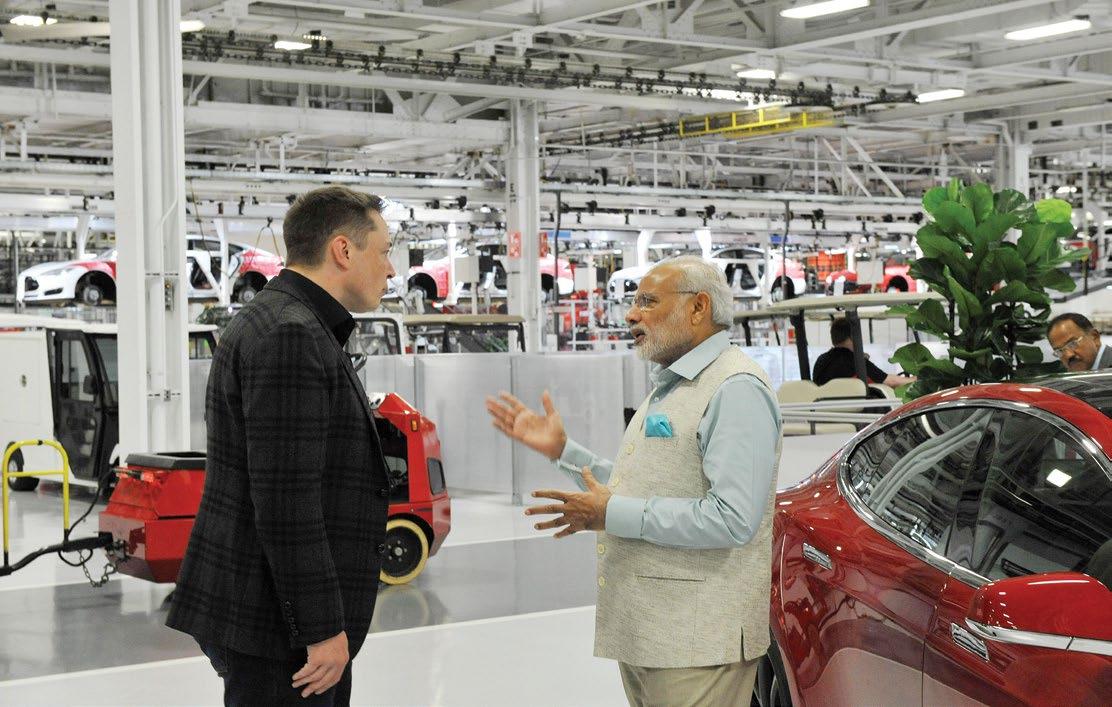
t is well known that Tesla Inc. is gearing to establish a base in India after the country rolled out a red carpet for the EV flagbearer. The inperson plant visits at the Tesla headquarters, in Palo Alto, California, by the top brass of the country led by Prime Minister Narendra Modi, in 2015, have since been followed by several state heads also extending an invite to Tesla Co-founder and Chief Executive Officer, Elon Musk for setting up the company’s India headquarters. States like Gujarat, Maharashtra, Andhra Pradesh, Tamil Nadu and Karnataka were among the front runners then giving hope to more domestic suppliers apart from the many that are known to supply to the company for its global markets. The speculations were put to rest only earlier i this year when in January, the company registered as ‘Tesla India Motors and Energy Pvt. Ltd.’ with the Registrar of Companies at Bengaluru, Karnataka. Now that Tesla is officially in India, the company, in phase one of its India strategy, is expected to import the Model 3 series. If it succeeds with imports and the sales strategy next year, it will want to establish a manufacturing plant in the next phase. The objective being to increase localisation of content per vehicle and succeed in this new market. More domestic manufacturers stand to benefit if it were to happen as envisaged. Musk, in a characteristic manner, took to social media platform Twitter to reiterate this intent in what was a reply to his follower asking to expedite the India launch. The reply was no coincidence and is believed to have followed an official note drafted to the concerned ministries. Citing the import duty in India as the highest in the world for a large country, Musk sought a tax cut even if it were to be granted in the form of a temporary relief to the new entrant. Calling out the treatment to clean energy vehicles as unfair, the tweet further read, “Moreover, clean energy vehicles are treated the same as diesel or petrol, which does not seem
MODERN AUTOMOTIVE BATTERY
FUTURE AUTOMOTIVE BATTERY
Structural Batteries Improve Mass And Range
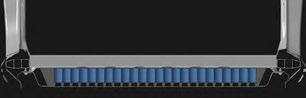
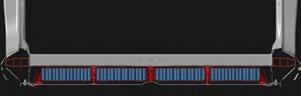
STORAGE
EXCESS STRUCTURE
STORAGE
Revolution In Body + Battery Engineering
10% MASS REDUCTION 14% RANGE INCREASE OPPORTUNITY 370 FEWER PARTS
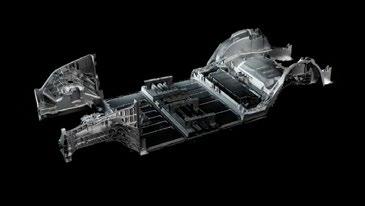
entirely consistent with the climate goals of India.”It remains to be seen though how the government responds to it though.
If the company’s demands are met, however, and the company is able to localise eventually for sustenance and or building India as its global Research & Development (R&D), and manufacturing hub, Indian component suppliers could win big! The company last put in place a strong leadership team with automotive honchos and continues to hire for both blue and white-collar positions across the country to get its execution right. It hints at wanting to be in the scheme of things for the long-haul.
The supplier base
A look at Tesla’s global supplier base and country-specific strategies reveal how the company has put in place a robust ecosystem and built a strong supplier base to succeed in each of its markets. For starters, the company has always been discrete on who it partners with. But with first hand knowledge, we know of Indian suppliers catering to the company for years now. The secrecy, understandably is a means to retain the perceived early mover’s advantage by protecting its Intellectual Property (IP) to stay ahead of the competition.
The IP referred to includes electric powertrain and the expertise in
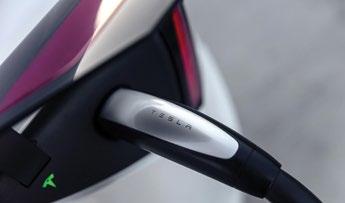
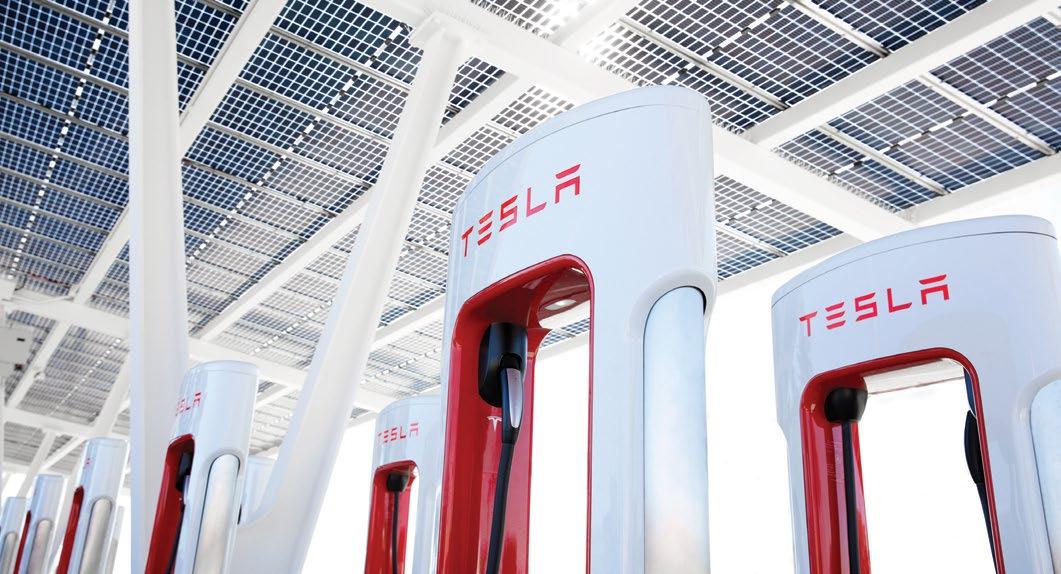
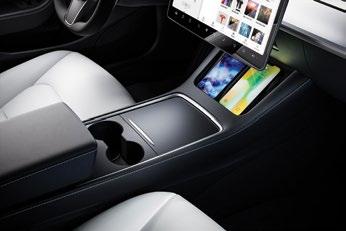
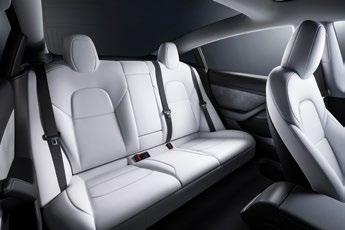
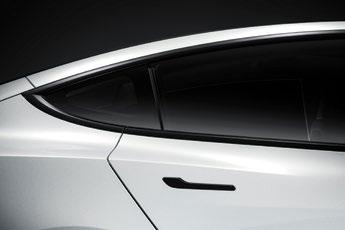
developing self-driving technologies. The Tesla powertrain also consists of power electronics, motor, gearbox, and control software. The company credits its pool of powertrain variants to years of R&D undertaken behind the scenes of all the attention it gets. On the flipside, teardown exercises by competition means maintaining secrecy around its supplier base was and will never be an easy task.
Besides the battery pack, electric motor and charger that the company is known to manufacture itself, its core vehicle technology competencies also include battery and powertrain engineering and manufacturing. The company takes pride in its ability to design vehicles claimed to utilise the unique advantages associated with an electric powertrain. On the front user interface, the company designs in a manner to incorporate the latest advances in consumer technologies, such as mobile computing. Indian technology companies in the space could leverage the opportunities if Tesla were to look at both established and new entrants out of the mix.
Tesla currently depends on component suppliers from across the United States, Europe and Asia including many homegrown suppliers of India to meet its other needs. Its supplier list includes AGC Automotive for windshields, Brembo for brakes, Fisher Dynamics for power seats, Inteva Products for the instrument panel, and Modine Manufacturing Co for the battery chiller. Sika supplies the acoustic dampers with Stabilus providing the liftgate gas spring. ZF Lenksysteme supplies the power steering mechanism. Continental provides the air conditioning lines while Magnetic Marelli provides the headlamp LEDs. NSK provides the wheel bearings and Wabco provides the twin compressor. Mumbai-based GoldSeal-Saargummi, for instance, supplied to Tesla Model X for some of the most complex products like the falcon wing doors. Sandhar Technologies, Bharat Forge, and Sona BLW are also known to be in the mix.
The list goes on to include other suppliers like ADAC, ABC Group, Angell-Demmel, Argent, Gentex, Harada, Hitachi Cable America, Hope Global, MacLean-Fogg, Magna International, Methode Electronics, Multimatic, Panasonic, Plastomer, PSM International, Riviera, T1 Automotive, Zanini Auto Group, TXU Corp., Universal Logistics Holdings, Inc., Affinia Group Intermediate Holdings Inc., Lithium Exploration Group, Inc., U.S. Lithium Exploration Group, Inc., Niocorp Developments, Ltd., Rare Element Resources, Ltd., Burlington Northern Sante Fe Corp., Cooper Industries, Ltd., Clarcor, Inc., Dana Corporation, Delphi Corporation, Flowserve Corp., NextEra Energy, Inc., Harman International Industries Inc., Lightwave Logic, Inc., Molex Inc., Metaldyne Performance Group Inc., Nortek, Inc., Rohm And Haas Company and Searchlight Minerals Corp.
Cost optimisation
Musk has admitted to cars getting increasingly complex compared to the Model T. The supply chain for battery’s, he tweeted, doesn’t exist at the desired scale and must be built in parallel. No wonder, he deems ideation as easy and production harder. Cost optimisation plays a key role here. Earlier in September 2020, Asian suppliers of Tesla were in the news after Musk is known to have pushed for lowering the cost of batteries. Batteries are estimated to account for 50 per cent of the total cost of an EV like is known to be the case with the Model 3, on its way to India. To put its point across, the company hinted back then at considering, producing its own cells to gain greater control over ballooning costs. The move is known to have compelled suppliers LG Chem Ltd., Contemporary Amperex Technology Co. Ltd. (CATL) and Panasonic Corp counted among the top tier battery suppliers to reevaluate their strategies. Prospective Indian battery technology company’s and suppliers are sure to have noticed the development and taken a cue to pace themselves right.
USA based electric vehicle and clean energy company CATL, for now, has signed on an extension deal with Tesla to supply batteries until 2025 as per a stock exchange filing. To be able to optimise the vehicle cost from USD 37,990 to USD 25,000 by 2023, the company will have to work out ways to bring down battery costs in line with Musk’s objective made public on the company’s ‘Battery Day’ event.
Until Tesla can ramp up its own production, however, the company will have to rely on its existing supplier pool. In India, Indian battery pack manufacturers like Gemopai, Benling India, Okinawa Autotech and Ampere Electric, Amara Raja Batteries, Epsilon
Advanced Materials Pvt. Ltd., and Green Evol Pvt. Ltd. (Grevol) among others in the pool must leevrage their low-cost, quality solutions to capitalise. Both established and new entrants looking to break into the Tesla supplier pool are required to carefully assess and meet the quality benchmarks set by the company. to succeed in their endeavour.
Quality Assessment
A battery solutions supplier, for example, will have to achieve high energy density at decreasing costs while also maintaining safety, reliability and long life in the extremely challenging and dynamic automotive environment like Tesla is claimed to have mastered. Highdensity energy storage, cooling, safety, charge balancing, structural durability, and electronics management are some of the other areas that need to be focused on. Tesla is open to evaluating new battery cells and optimising battery pack system performance to gain better control over the costs of its current and future vehicles. Indian suppliers are well equipped to step up their ga me and capitalise on the intent.
Suppliers in power electronics need to match up to Tesla’s ability to drive large amounts of electrical current in a small physical package with high efficiency and low cost. It must also enable a recharge on a wide variety of electricity sources including at the company’s ‘Superchargers’. Motor manufacturers must benchmark with Tesla’s design, making use of two electric motors to maximise traction and performance in an all-wheeldrive configuration. It is said to pave the way for digital and independent control over torque to the front and rear wheels. In effect, the claimed, near-instantaneous response of the motors, combined with low centres of gravity, provide drivers with controlled performance and increased traction control. The company is also working on the development of vehicle powertrain technology featuring three electric motors to improve overall performance. Supplier manufacturers into steel, aluminium, copper and rubber besides alternative materials for body and chassis also stand a chance to associate with the company as it looks at ways to benefit from the use of a variety of materials and production methods for optimising vehicle weight.
A testimony to existing suppliers coming good on all counts is the manufacturer’s warranty on all new and used Tesla vehicles in global markets. A new Tesla vehicle comes with a four year or 50,000 miles ‘New Vehicle Limited Warranty’ to give a perspective on what the global consumer gains. This is further subjected to separate limited warranties for a supplemental restraint system, battery and drive unit, and body rust perforation. In the case of the battery and drive unit on the new Model 3 and Model Y vehicles, the company offers an eight-year or 100,000-mile limited warranty for its ‘Standard’ or ‘Standard Range Plus battery’ and an eight-year or 120,000mile limited warranty for its ‘Long Range’ or performance battery. The extended Service plans cover the repair or replacement of vehicle parts for up to an additional four years or up to an additional 50,000 miles after the expiration of the New Vehicle Limited Warranty. It will be interesting to see the fine print of these nitty gritties in the Indian context and how more Indian suppliers capitalise on the prospects of a Tesla association. The company, for now, is content with setting up an assembly plant for CKD and SKD units in India as all the stakeholders look to test the waters before committing to the long haul. ACI
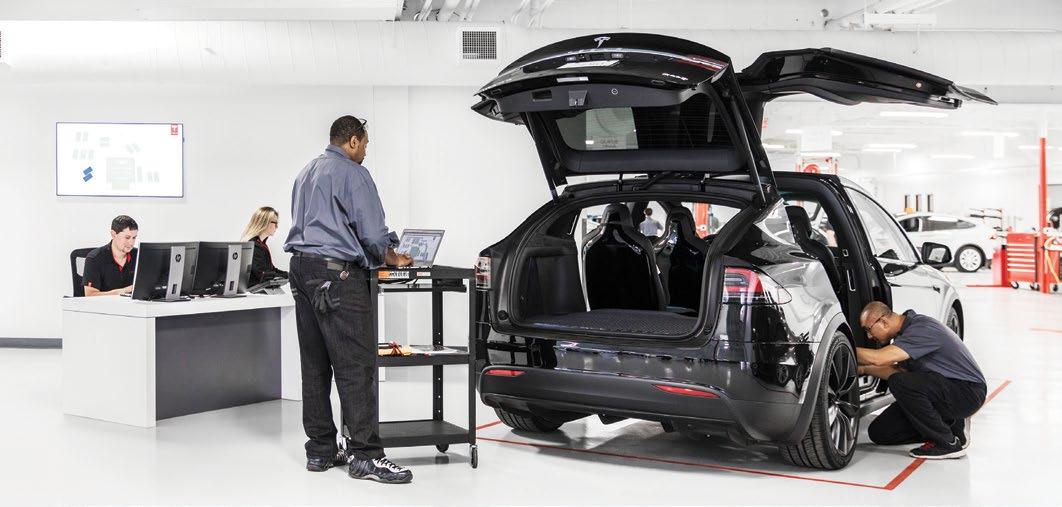