
47 minute read
COMPONENTS
Image for representative purposes only.
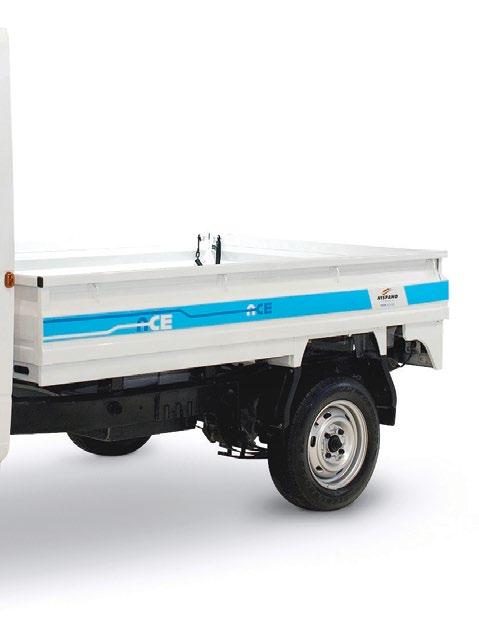
Advertisement
can be put into the fuel-cell in a quick process to add to the efficiency. Log 9, according to Singhal expects to benefit from the solution being independent of lithium and cobalt besides eliminating the need for costly infrastructure.
Opined Singhal, the fact that it is a primary energy generation mechanism that does not act as an energy storage hub like the conventional batteries do is a big plus for the company. Add to it, claimed Singhal, that the cost doesn’t scale up in proportion to the increase in the energy capacity of the fuel-cell. Claimed to have been inspired by the 1990 NASA space exploration, the use of graphene by Log 9 is validated by the several studies deeming it a “material of the future”. Singhal is of the firm opinion that aluminium fuel-cell could significantly change the landscape of emobility once it matures to a large scale deployment in the future. “This technology can revolutionise the clean energy, electric mobility and transport sectors not only in India but across the globe,” he mentioned. Notably,
Upfront Akshay Singhal, Founder - Log 9 Materials Scientific Pvt. Ltd.
Q. As a startup, you thrive on challenges. How did you brave the challenges thrown your way in the pandemic?
A. Yes indeed, development was affected by the pandemic. The resources and manpower we had at our disposal had to be repurposed during the lockdown, contributing across the different portfolios. And once the lockdown was lifted we got the developments in the pipeline for the future on course.
Q. Have you emerged stronger or felt the need to add to the efficiencies much ahead then you envisioned during the pre-covid (Q3 FY2020) period?
A. I think the whole coronavirus experience brought in a commercial sense. The team began to take a holistic approach, from the development cycle to marketing and eventually the commercialisation. In a sense, we adapted to the new normal of conducting our business.
Q. How did your investors support you in your endeavour?
A. They have been supportive of all the steps we took. Fortunately, we count ourselves among the few companies who did not resort to layoffs or salary cuts.
Q. Is it true that early-stage seed funding has dipped? How has funding on the whole impacted the financial health and valuation of your company?
A. Yes, it is true that there was a dip initially. Post-July-August 2020 we touched base with our investors and since then there has been a revival.
Q. Elaborate on the application of graphene in automotive (especially at the component level for instance in the battery and aluminium fuel cell) and problem areas solved by you?
A. It has a lot of applications in panels, lubricants and in batteries owing to characteristics like high conductivity or high surface area. Even the lithiumion batteries make use of graphene to increase their efficiency levels. It is used majorly in the aluminium fuel cell where the most crucial component is the air cathode wherein graphene helps enhance the overall efficiency.
Q. How evolved are the graphene processing and patterning technologies today?
A. Graphene is like a family of materials. There are a lot of variations when we talk about graphene in terms of structure and its chemical properties, the type of graphenes and the protocols. It depends on how you use a particular variant suited for the application since not all variants are suited to all applications. We need to find the right property for the right application. For instance, in aluminium fuel-cells, you require conductivity of graphene, surface and hydrophobicity (water-hating).
Log 9 staff members (45 of them), claimed Singhal, actively use the fuel-cells to generate electricity. Log 9, cited Singhal, is pursuing Original Equipment Manufacturers for a trial. In fact, two automotive companies, hinted Singhal, are in talks with the startup to deploy the solution as an alternative to their EVs. “We aim to
The ‘Ranger’ powered by the Log 9 metal-air battery similar to the fuel-cell.

start with a light commercial vehicle platform like the Tata Ace before moving on to heavy commercial vehicles,” he disclosed.
Need-based use case
To cater to the different duty cycles in the Indian automotive market spanning light to heavy commercial vehicles, Log 9 advocates the need for a customised approach over a ‘one-size fits all’ approach. “Every platform has different requirements and operational conditions so a one fit for all approach doesn’t work. The vehicle duty cycles suited to the long-haul are of more relevance to us,” reiterated Singhal. Sharing a case study of a light commercial vehicle powered by a lithium-ion battery pack with a 150-200 km range on a single charge, explained Singhal, the battery pack typically weighs 200 kg. If its range were to be extended to 1200-2000 km, the battery pack would proportionately be heavier at approximately one-tonne. “It is here that we step in to provide the desired range with a light-weight battery pack,” he said. The Log 9 solution can give the same range with a lighter 300 kg pack making for a compelling case, he claimed. Beyond automobiles, the company is also exploring the potential of serving for stationary energy resources. Vehicle homologation is also on the anvil. ACI
NOW ON STANDS


INDIA’S NO. 1 TWO WHEELER MAGAZINE, BY FAR!
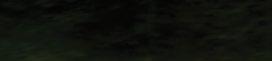

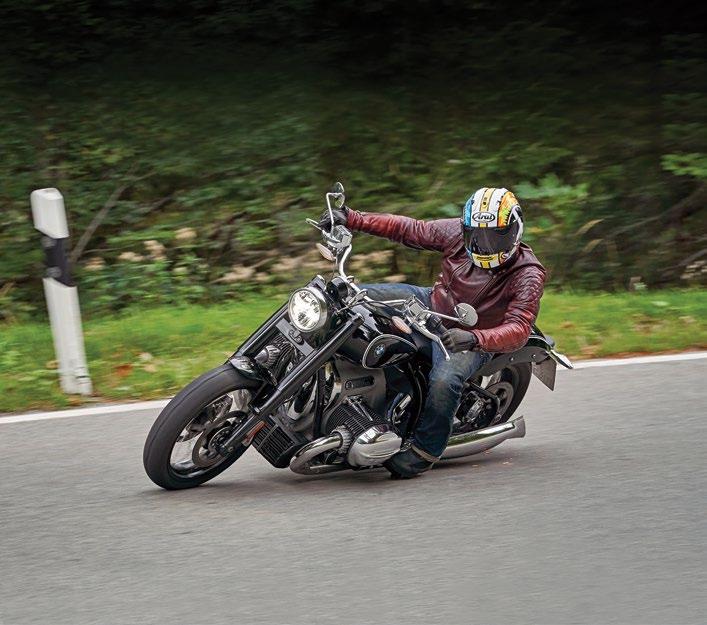
BMW R 18 R 18 Bavaria’s biggest boxer ridden VOLUME 16 ISSUE 04 NOVEMBER 2020 EXCLUSIVE!
WWW.BIKEINDIA.IN
PUBLISHING
C M Y K
Triumph Tiger 900 Rally Ducati Scrambler 1100 PRO and Sport PRO FIRST RIDE Yamaha Fascino 125 Royal Enfi eld Classic 350 ROAD TEST Odisha by Road – II Hero Xtreme in Odisha – II FEATURE Exclusive! Triumph Trident - India’s most accessible Triple
` 100
Intelligent Battery Analytics
ION Energy is optimising EV powertrains and energy storage systems through advanced battery management systems. Story by: Deepti Thore
ION Energy Inc (ION) is on a mission! A mission voltage to high to improve the life and performance of lithium- voltage applications. ion batteries. Be it battery packs powering EV Lead-acid or Nipowertrains or Energy Storage Systems (ESS) that MH battery packs, are in vogue with economies the world over- however, are the committing to going fully electric by the turn exceptions in terms of the decade. Co-founded by Akhil Aryan in of compatibility. 2016, Mumbai headquartered ION has conducted ION counts extensive research to conclude, by 2022 itself, Airbus, Ola, global battery manufacturing capacity could hit Tata Motors, 400 GWh. The company is betting big on the Wamtechnik, demand of Battery Management System (BMS) Okinawa Scooters compatible with Lithium Cobalt Oxide (LiCoO2), (i-Praise Electric Lithium Manganese Oxide (LiMn2O4), Lithium Scooter), Tork Nickel Manganese Cobalt Oxide (LiNiMnCoO2), Motorcycles, and Akhil Aryan, Lithium Iron Phosphate (LiFePO4), Lithium Electric Motion among Cofounder & CEO, ION Energy Inc. Nickel Cobalt Aluminum Oxide (LiNiCoAlO2) others in its clientele, a and Lithium Titanate (Li2TiO3) spanning low testimony of its market penetration. With over 25,000 BMS deployments (out of which 15,000+ electric two and three-wheelers in India and Europe), are electric across two-wheeler EVs (12V) to electric excavators (xV) to a micro-grid storage system (1080V), ION’s technology, claims Akhil Aryan, Co-founder & CEO, ION Energy Inc., is directly responsible for helping companies save up to 40 per cent on electronics. “The industry being in its nascent stage, tier 1 and 2 automotive OEMs look for high-quality BMSs at a very competitive cost, and ION has managed to strike an optimum balance between low cost and high quality,” he averred.
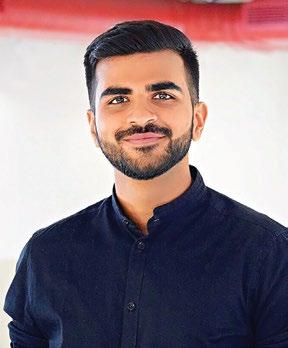
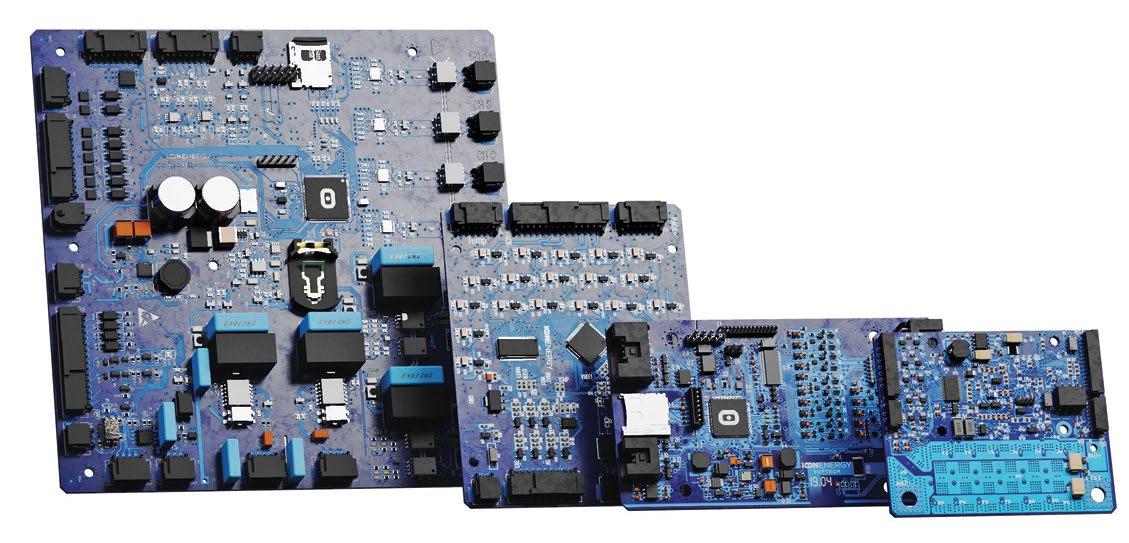
Battery Management System
An efficient BMS unarguably guarantees a reliable and efficient battery pack. Explained Aryan, “ION’s approach, a software-first, full-stack one leverages advanced electronics, machine learning software and AI with its domain expertise in energy storage.” Notably, ION’s business model enables customers to buy or build custom BMS models. The BMS supports passive cell balancing claimed to ensure uniformity in the State of Charge (SOC) and voltages of the individual cells which maximise the capacity of the battery pack and improves life. Balancing the current range varies across the variants of its BMS units.
ION offers three BMS variants: FS-CT (Compact) designed for low voltage battery systems from 7.5V to 42V, FS-LT (Light) designed for battery systems from 12V to 100V and FS-XT (Extended) designed for high voltage battery systems from 13V to 900V offered with a one-year warranty. The FS-CT is known to connect from six to 100 cells in series. The FS-LT connects from six to 25
Key Features of the BMS
q q q q q q q
State of Charge (SOC) Estimation State of Health (SOH) Estimation Paralleling Cell Balancing Communication Capabilities Data Logging Over the Air Updates
cells in series and using a modular architecture, it is said to manage applications from 12V to 110V and is compatible with multiple battery chemistries. For instance, in electric scooters and rickshaws, known to run on 48V to 60V lithium-ion battery packs. It is also tested for EMI/EMC tests as per AIS004 guidelines to meet a critical requirement for electric vehicles. It also offers resistance to electromagnetic disturbances and enables safe functioning in environments with heavy electrical noise. The FS-XT especially designed for automotive and high precision applications uses a distributed BMS. It consists of a System Management Unit (SMU) or a Master Unit known to connect up to 40 Battery Monitoring
FS-LT (Light) Unit (BMU) or Slave Units. Each Slave Unit can further monitor six to 18 cells in a series configuration. It can also connect up to 18 batteries in a parallel configuration. The FSXT boasts of high-voltage safety features such as IMD Integration, HV Interlock Lines, HV Measurement Channels and Weld Check.
The BMS manages the flow of current through a Power Distribution Unit (PDU) and is known to support both solid-state and electromechanical based PDUs. Aryan drew attention to the Telematics Control Unit (TCU) for remotely accessing battery asset status, health, and data for more in-depth analysis. “The TCU seamlessly interfaces the BMS with Edison Analytics to provide real-time data about battery health, status, warranty, and in the case of utility-scale Battery Energy Storage Systems (BESS), in energy dispatch,” he mentioned. The BMS with CAN Bus 2.0 A and B interface for charger control and system interface supports all baud rates ranging from 125 kbps to 1 Mbps. It also supports both standard and extended CAN IDs. The BMS is compatible with CAN-based chargers including Zivan, TC charger, Bassi charger and Dilong charger.
The BMS is backed by ION Lens, a smartphone application to interface remotely with ION BMS interface via Bluetooth. Through it, critical information of the battery like SOC, current, temperature and individual cell voltages can be accessed besides configuring and editing the configuration files. ION, additionally, offers services to help the companies design and engineer battery packs as per their specifications. It looks at various stages spanning cell selection, thermal management electro-mechanical assembly, structural design and the design analysis. Said Aryan, “The services extend to prototyping, quality analysis and testing as part of the end-to-end solutions involving a short-run production, supply chain

Key Features of Edison Analytics
q q q q q
Advanced analytics and insight into your fleet from a single dashboard Alert on any abnormal battery performance for timely action Data science to suggest corrective measures to prevent battery degradation Improve battery life Roll out Over-The-Air (OTA) updates
and consistent assembly line set-up.” Successfully tested and validated hardware for IEC 61 000 (EMI / EMC) and IEC 61439-1:2011, the company, cited Aryan, is additionally helping its partners achieve certifications like IEC 62133, Basic UN38.3 and ARAI AIS 048 in Indian Automotive Industry.
Edison Analytics
Through a CAN view, desktop software suite ION facilitates two-way communication with the BMS. “This paves the way for system configuration, real-time data visualisation, authentication and data transfer to the company’s battery intelligence platform - Edison Analytics,” explained Aryan. The BMS is also equipped with onboard memory storage known to log every data point of the battery pack collected. It is claimed to facilitate battery data archives of up to 20 years. To overcome the challenge of managing the data quantum, ION as per Aryan is relying on compression algorithms tailored to battery data acquisition. Physical parameters, events, errors relating to the performance of the battery pack are part of the data pool generated, he informed. The cloud-connected battery intelligence platform Edison Analytics allows engineers to access the data pool and help customers gain invaluable insights into the life and overall performance metrics of the battery.
Through it, customers can look forward to configuring the BMS to inturn match their application’s requirements with the battery’s capabilities. For instance, users can customise over 190 parameters relating to power distribution, ignition controls, balancing, charger control etc. “Our off-the-shelf products are ready-to-be-deployed and generally have all the latest features and hardware developments. If the customer needs custom features, it can take anywhere from a week to 6 months, depending on the type of feature update. For example, the software takes a week to 2-3 months and the hardware takes anywhere from a month to six months; these timelines depend entirely on the complexity and urgency of the requested features,” he claimed.
Battery Energy Storage Systems
The energy mix has evolved with the emergence of Variable Renewable Energy (VRE) sources. Battery Energy Storage Systems (BESS) are known to have enabled power system operators and utility providers to store energy for use at a later point and time thus enhancing the grid flexibility. With the global BESS markets displaying a lithium-ion battery monopoly, the need for intelligent management and operations is being felt. By modelling impedance (DC) the BESS is claimed to be capable of predicting if the batteries can fulfil the demand from the grid over their ageing. Among advantages are warranty validation, troubleshooting, bidding and energy arbitration, and record keeping. Explained Aryan, “At ION, we are overcoming the limitations of traditional systems and analytical tools to maximise the potential of these batteries.” “Our battery management and intelligence platform help operators optimise the cycle life and get better RoI on their BESS deployments,” he stated.
On optimal battery efficiency contradicting the pursuit of economies of scale argued to be crucial in bringing battery costs down, Aryan opined that both go hand-in-hand. “Eventually, the benefit has to roll into the total cost of ownership to the end customer,” he concluded. ION is witnessing strong traction in the EU and is expected to make announcements on the lines in the coming months. 100 per cent localised, ION is aiming to go beyond its offerings to contribute to the EV infrastructure as a whole, in 2022. ACI
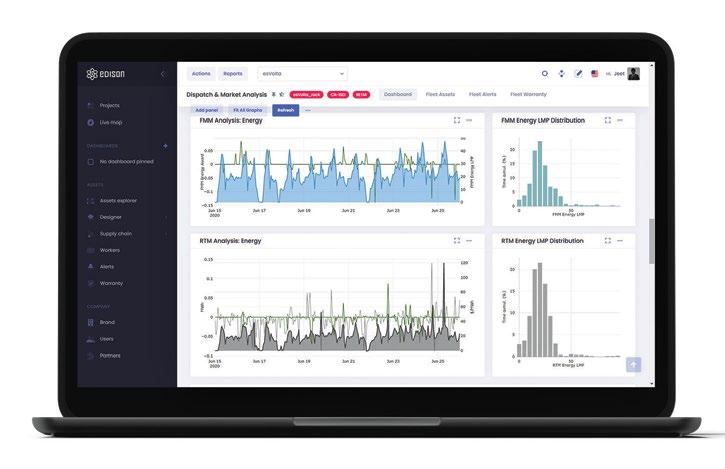

The Commercial
Story by: Ajay Kapur, Chief Executive Officer, Vedanta Aluminium & Power Business
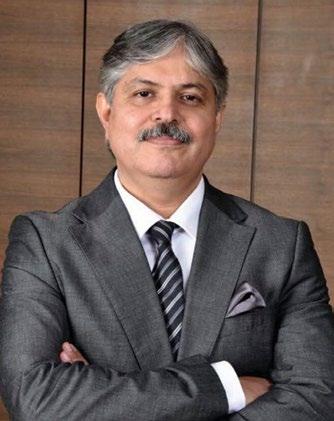
A
luminium is the second most used metal in the world after steel. It has the potential to become the most important commercial metal in the future. Aluminium holds strategic importance for the economy as the commercial metal of choice for all kinds of transportation, power, aerospace, defence, infrastructure and packaging needs. Backed by rich bauxite deposits, India has the secondlargest aluminium production capacity in the world after China. Vedanta’s Aluminium Business produces more than half of India’s aluminium at an estimated output of 1.9 Million Tonnes Per Annum (MTPA) in FY20. Most developed countries have already designated aluminium
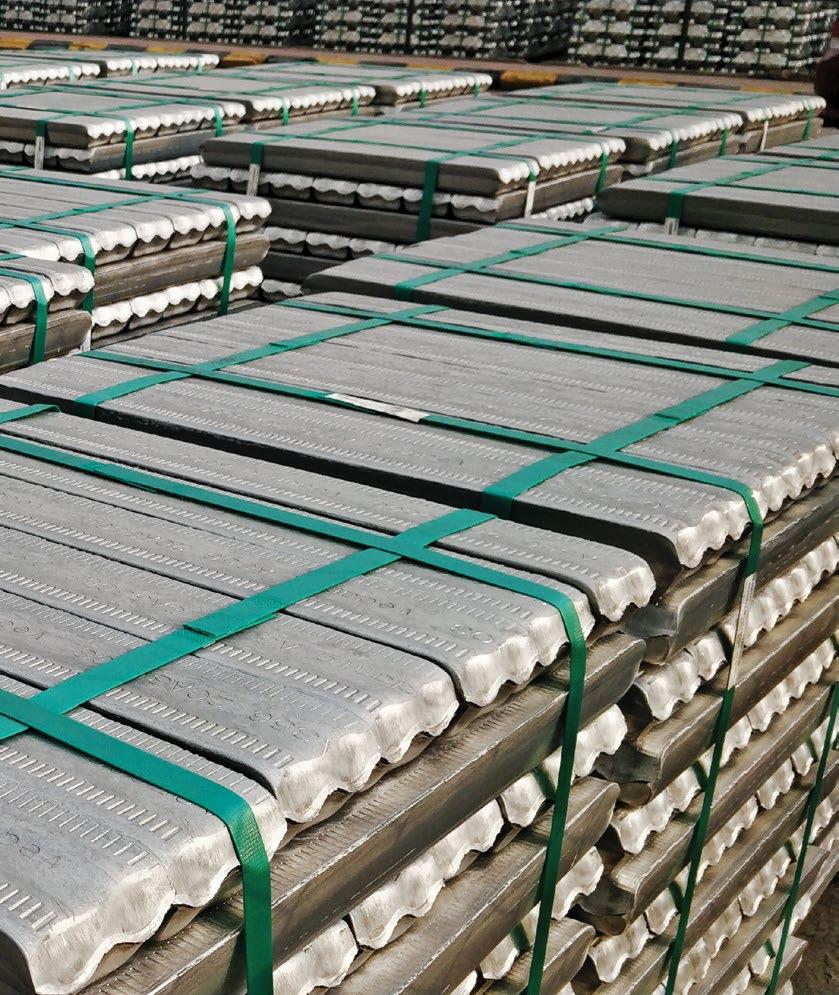
Ajay Kapur, CEO, Vedanta Aluminium & Power Business
as a core industry. Given the role, aluminium plays in supporting the core sectors and in the success of government’s visionary initiatives like ‘Make in India’, ‘Smart Cities’, ‘Power for All’, and the indigenous space programme, use of this metal in India is only going to increase with time.
Aluminium in the automotive industry
Aluminium in automobiles has been used for several years and its consumption in new vehicles is increasing steadily. Over the past several years, usage of aluminium in automobiles and light-weighting of trucks has witnessed the highest growth in comparison to other aluminium applications, in any segment of use.
High strength to weight ratio, lightweight, corrosion resistance, supreme formability, high ductility and conductivity, stylish finish and infinite recyclability, coupled with the fact that bauxite (aluminium ore) mining is sustainable and eco-friendly, are some of aluminium’s unique selling properties which have made it a metal of choice for some of the most iconic automakers. High performance and elegance need not come at the cost of high fuel consumption, high maintenance and environmental impact, and aluminium ensures this to a great degree.
Aluminium remains the fastest-growing automotive material over competing materials and

The first smelter for primary foundry alloy production
is entering its most unprecedented growth phase. This is mainly because the global economy is swiftly moving towards a cleaner, greener, and more sustainable lifestyle.
Demand drivers
Aluminium is the second most used metal in the auto industry today. Its usage has been rapidly increasing because it offers an environmentfriendly and cost-effective way to increase performance, boost fuel economy and reduce emissions while maintaining or improving safety and durability.
Aluminium is substantially lighter than its counterparts, offering a significant reduction in weight. The metal has a higher strength-to-weight ratio compared to traditional materials that enables it to absorb twice the crash energy of mild steel, ensuring vehicular performance enhancements do not come at the cost of safety.
This has a direct impact on fuel consumption, range, and carbon emissions making it the top choice for automobiles. Coming to Electric Vehicles (EV), the need for lightweight battery casings and heat exchangers in electric vehicles, combined with autonomous vehicles’ demands for high visibility and structural integrity, is expected to further boost the use of aluminium in cars, trucks and buses going forward. Further, thanks to the metal’s thermal and anticorrosion properties, aluminium is ideal for battery frames. Aluminium is also likely to witness an increase in demand on account of growth in infrastructure for serving EVs since the metal is commonly used as a housing material for EV charging stations as well.
With stricter safety and emission norms alongside the demand for light-weighting and electric vehicles, we foresee, the aluminium industry segments like extrusion, casting and rolling playing major transformational roles soon. Additionally, nearly 90 per cent of all the aluminium used in a vehicle is recycled at the end of its lifecycle, ensuring value at the end of the vehicle’s lifecycle as well.
According to WardsAuto and DuPont Automotive survey, every kilogram of aluminium used reduces the weight of a car by a kilogram, if not more. This makes it the first preferred material of choice among engineers and designers to help meet the expected fuel economy and emission standards by 2025.
Aluminium in auto components
For more than a decade now, concerns about fuel efficiency have encouraged OEMs to replace steel with aluminium in vehicle bodies, doors, trunks, hoods, bumpers, crash boxes, brakes, cables, and wheels. With the advent of EVs, OEMs worldwide are focussing on exploring and applying new uses of aluminium in the emerging industry.
Today, globally, transportation accounts for the largest share of aluminium consumption at 27 per cent. According to experts, this will increase exponentially with the average aluminium content in a car reaching 250 kg by 2025. India is behind the global benchmark when it comes to aluminium usage in vehicles. Aluminium consumption in the Indian auto sector is only about four per cent, against 11 per cent in the USA and 14 per cent in Europe.
Aluminium alloys are used by the domestic auto industry majorly as alloy wheels. Around 95 per cent of two-wheelers include aluminium, averaging at seven kilograms per bike, taking the total consumption of aluminium alloy in this segment to 115 Kilo Tonnes Per Annum (KTPA). On the other hand, only 20 per cent of four-wheelers use aluminium, majorly in high-end models, which max out at 40 kg per car.
This presents immense scope for domestic producers like Vedanta Aluminium, to tap into the emerging market in the automotive sector. Currently, India’s foundry market for automotive components is small (only 10 per cent of total foundry market — 10 million of cast iron + aluminium) in comparison to USA’s foundry market, which is at 14 million tonnes per annum, of which 3.3 million is aluminium (24 per cent). With an increasing focus on higher
performance with better safety and lower emission, this gap is going to shrink in the coming years.
In fact, Vedanta Aluminium was the first in India to supply Primary Foundry Alloy (PFA) to the domestic auto sector. Until then, the country’s entire PFA demand was being met through imports, even though India has the world’s second-largest aluminium production capacity. Looking at the promise of the auto market and its import dependency, Vedanta Aluminium decided to tap into the opportunity and develop 240 Kilo Tonnes Per Annum (KTPA) indigenous capabilities at its stateof-the-art facilities in Jharsuguda (Odisha) and BALCO (Chhattisgarh) to meet that demand.
Internal combustion engine
Today, usage of high-performance aluminium alloys in crankcases, cylinder blocks, heads and pistons are commonplace. Aluminium alloys are the preferred material for ICE components due to characteristics like low density, high thermal conductivity, simple fabrication techniques (casting and forging), easy machinability, high reliability and recyclability. Proper control of the chemical composition, processing conditions and final heat treatment results in a microstructure which ensures the required mechanical and thermal performance, in particular the high thermal fatigue resistance.
Aluminium will continue to play a significant role in the continued evolution of ICEs along the lines of reduction in piston weight, increase of mechanical and thermal load capacity, lower friction, improved scuffing resistance, etc., as well as basic requirements like durability, low noise level and reduced fuel consumption.
Aluminium commodity outlook
Aluminium prices have strengthened during the second quarter of FY21 with recovery in the global economy, resilient Chinese demand and a weaker US dollar. Entering the third quarter, market experts predict that the prices shall drift lower as the global economic recovery goes back to its initial rebound phase. Analysts estimate that the upward momentum of LME shall fall through Q3FY21 and average out at USD 1,750 per tonne. On the demand side, outside China, North East Asia market and the US market are in the rebound phase. Globally aluminium production will increase by one per cent YoY in CY2020, with a 1.6 per cent contraction ex. China and three per cent growth in China along with an estimated surplus of 3.8 Mt in CY2020.
There has been a spike of 17 per cent in the London Metal Exchange (LME) price of aluminium, from USD 1460 per tonne in March’20 to USD 1721 per tonne in August’20. Parallelly, there has been a steady increase in demand for automobiles globally. With the Indian Inc. pulling out all the stops to emerge competitive in the postCovid global order and efforts by the central govt. to revive the economy, aluminium has a big role to play in achieving the coveted V-shaped recovery of the Indian economy from approximately two per cent to seven per cent by next year.
Future potential
India is yet to fully explore applications of aluminium in the automotive industry akin to its global peers. There is immense potential for usage of aluminium in other auto parts like engine, suspension, front end carrier, instrument panel support, rear frame, chassis and many more.
In developed countries, around 21 PFAs are used in the automotive segment to achieve light-weighting in the form of various auto parts and components. On the other hand, in India, we majorly use PFAs only for manufacturing alloy wheels and to some extent, for cylinder heads. There is scope for Indian aluminium manufacturers to expand their aluminium alloy portfolio for supporting the manufacturing of cylinder heads, ABS brakes and certain other applications, replacing traditional materials.
Vedanta’s aluminium business produces more than half of India’s aluminium estimated at 1.9 Million Tonnes Per Annum (MTPA) in FY20.
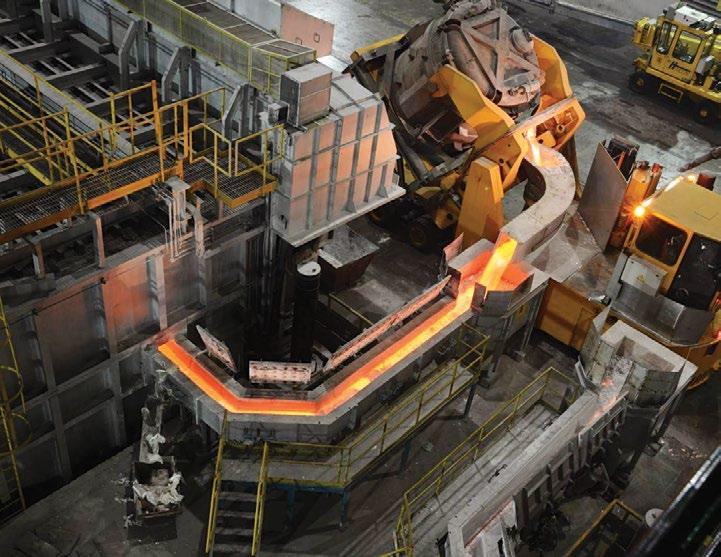
As the market for aluminium alloys in the automotive segment expands with the inclusion of newer applications, aluminium manufacturers must also look for opportunities to leverage their technical expertise and R&D capabilities to develop products customised to the needs of the market. In this direction, they could explore collaborations with the downstream industry, to unlock the entire potential of aluminium used in the auto sector and cater to the rapidly evolving aluminium requirements of the Indian automotive industry. Staying ahead of the curve, Vedanta Aluminium is already developing indigenous capabilities at its state-of-the-art smelters in Jharsuguda and BALCO to create new products and product customisations attuned to emerging needs of the auto sector.
Challenges
One of the biggest challenges faced by the Indian automotive market is increasing imports of auto components from China and other countries. The size of the auto components imports was USD 17.6 bn in FY19. Asia, the largest source of imports for Indian autocomponents, had a share of 61 per cent followed by Europe at 29 per cent; North America at eight per cent; Latin America and Africa at one per cent each in FY19. China with 27 per cent enjoyed the status of the largest exporter in the Indian automotive market.
Way forward
Aluminium is crucial to realise the vision of ‘Make in India’. It can play a pivotal role in the changing face of the automotive sector. This makes it pertinent to acknowledge and recognise it as a core sector and leverage the potential of the entire aluminium value chain, from mining to end-users in critical sectors of national importance like transportation, defence, aerospace, aviation, infrastructure, electrification, housing, etc. With an array of impressive products which cater to key industries, homegrown brands like Vedanta are striving to bolster the country’s self-reliance in all things aluminium, laying the foundation for India’s greener and sustainable future. ACI -----------------------------------------The views expressed by the author are his personal opinions and do not necessarily reflect the views of the ACI magazine.
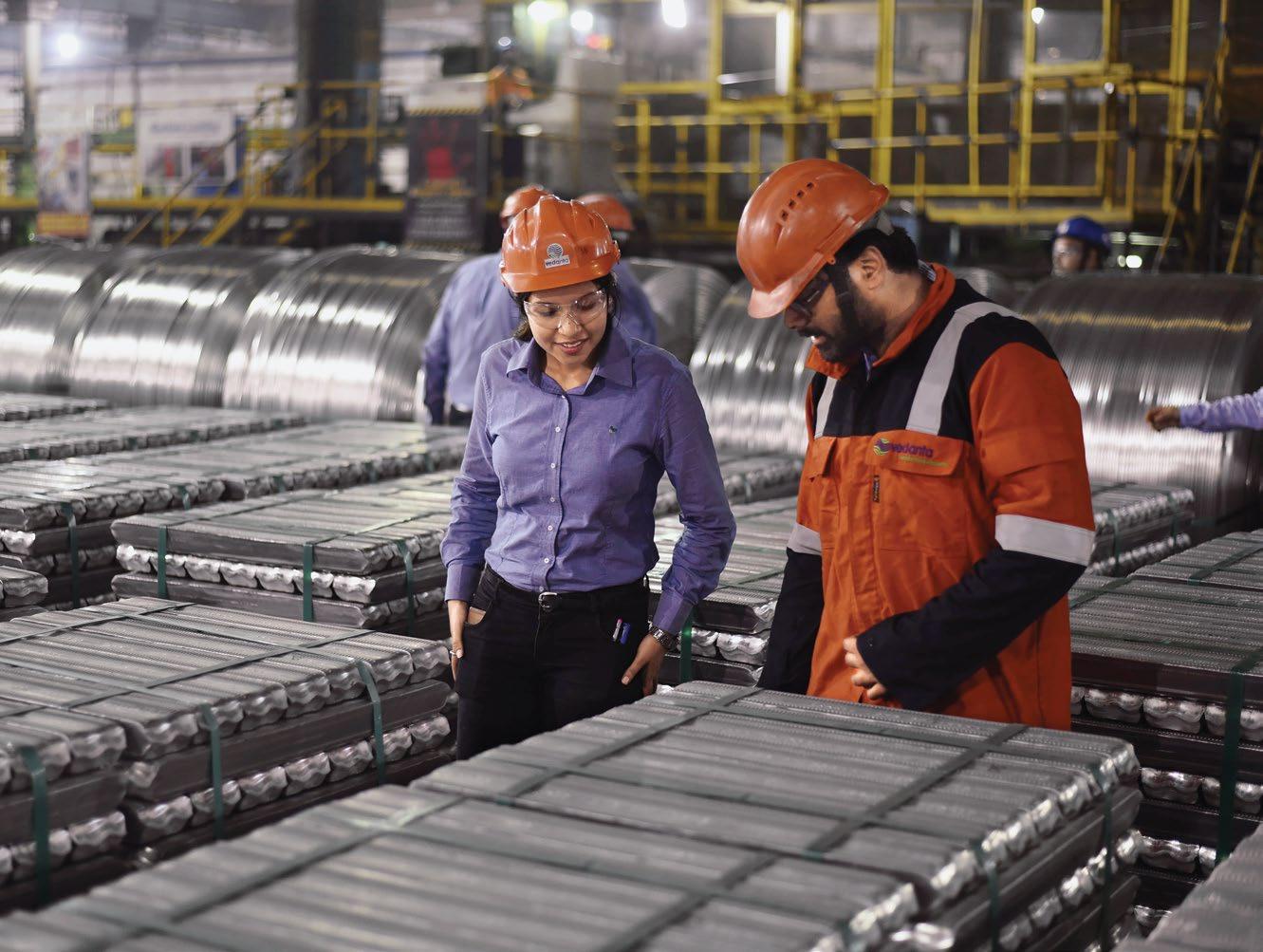
Getting Back To Top Gear: The road ahead for Indian auto component manufacturers
As car sales gradually regain momentum, how can auto component manufacturers ensure and sustain not just recovery but growth?
Story by: Shivanshu Gupta - Senior Partner at McKinsey & Company and Barathram A - Associate Partner at McKinsey & Company.

Special Reads India’s automotive industry was in top gear between 2009 and 2018 – automotive sales grew at nine per cent per year, and the auto component industry grew at over 12 per cent. Building on this performance, the Automotive Mission Plan 2016–26 (a joint vision of the government and the auto industry) set ambitious goals for the sector. According to the plan, the sector could contribute 12 per cent to GDP (over the current seven per cent) and add 6.5 crore additional jobs to the current 3.7 crores by 2026. Instead, slowing sales and shifting supply chains over the past couple of years started to squeeze margins. Adding to the industry’s woes, the global pandemic necessitated a country-wide lockdown in 2020 that continues to have a deep impact on lives and livelihoods. And yet, the picture is not that bleak. With the country gradually opening up and wholesale figures for August 2020 offering a ray of hope with a 14 per cent increase in passenger vehicle sales and a three per cent increase in two-wheeler sales YoY, auto component manufacturers could rev their motors and move back into
Shivanshu Gupta, Senior Partner, McKinsey & Company, Chennai
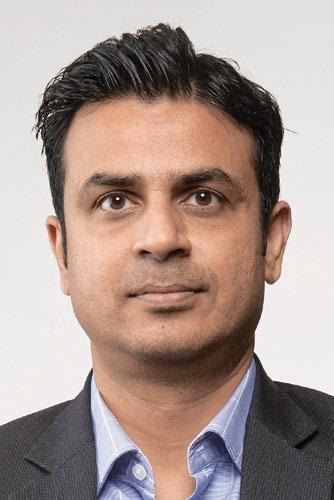
top gear. Making tactical changes to their existing capabilities and considering fresh approaches could allow them to thrive in the next normal.
A recent McKinsey report, Shaping the new normal – India’s auto component industry, outlines actions for auto component manufacturers to foster their own growth – which could critically
Barathram A, Associate Partner, McKinsey & Company, Chennai
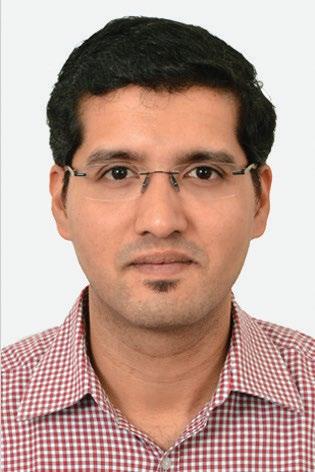
bolster India’s GDP. The three proposed priorities are to localise, optimise and digitise.
Localising to ramp up domestic manufacturing of relevant highvalue parts could be a vital growth area for the industry. Cutting down on imports of engine components and bearings, parts that are also exported in huge quantities, would echo the country’s mission for an
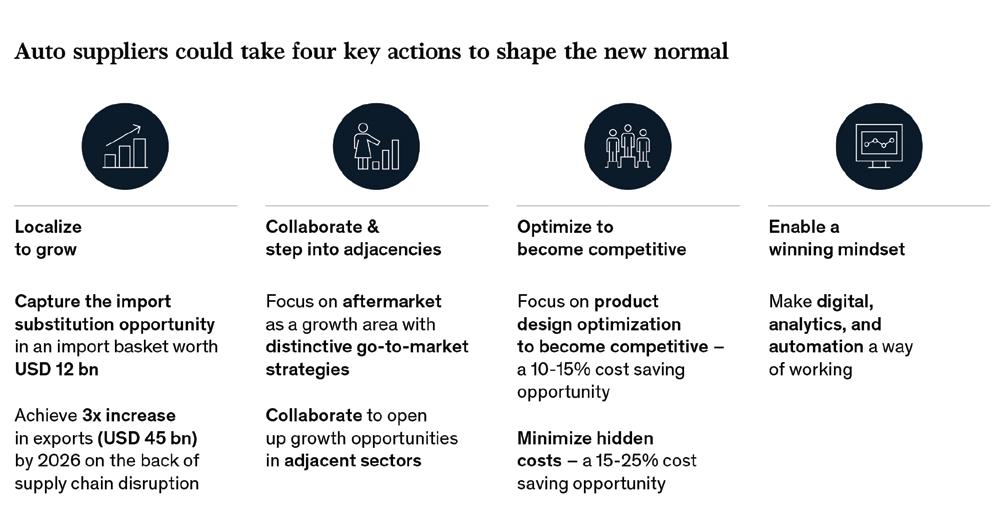
Atmanirbhar Bharat (self-reliant India). Component manufacturers could also collaborate with global suppliers looking to relocate their manufacturing operations to India, helping to capture a USD 12 billion import substitution opportunity. For example, a large global, industrial player is looking to move over USD one billion of their spend into India and is hunting for suppliers who can nimbly respond to their requirements by quickly innovating and building scale.
Making the most of these supply chain shifts could help India triple its export volume by focusing on product categories where it has a competitive edge (e.g. shafts, brakes and clutches) and building capabilities to manufacture high-value items such as gear-box parts and Heating, Ventilation and AirConditioning (HVAC) products.
Another growth area could be to localise aftermarket service through collaborative partnerships that focus on the greatest demand hotspots. The automotive aftermarket has proved resilient in past downturns since people postpone buying new vehicles and settle for repairing the ones they already own. While serving the vast aftermarket across India is daunting, McKinsey’s micromarket planner analysis discovered that only 1,275 micro-markets of the 20,000 pan-India contribute the top 50 per cent of all aftermarket service demand, and 43 per cent of overall demand comes from urban districts. Auto component manufacturers could zero in on the ones among these that are easiest to service through an on-ground partner (such as a service centre). A tyre manufacturer observed high growth in aftermarket sales in June and July of 2020 after it focused heavily on being agile, selling the right products and prioritising the right micro markets.
Optimising to manage costs is an obvious priority when margins are strained. But what might be the best and most valuable ways to do so? Optimising product design, especially in the expensive manufacturing processes for Bharat Stage-VI components, could cut down a quarter of total costs. One such area where direct material cost could be optimised is in the production of catalytic converters – manufacturers could save up to six per cent of the incremental cost they incurred when transitioning to BSVI by relaxing the internal test cycles and integration of CAT systems.
Manufacturers could also tighten processes to cut down on hidden costs, saving another 15 to 25 per cent, especially in areas including real estate, IT, insurance, logistics, packaging etc., which are traditionally overlooked as organisations focus on saving material costs. On freight logistics, for example, companies could save by setting up a full freight tender with the best per-tonne, per-kilometre rates, reducing less-thanload shipments and ensuring freight cost chargebacks, among other things.
And finally, digitising could be the critical enabler that helps achieve all of these goals faster, and at lower costs. Until now, India had not really embraced digital, approaching it as an optional investment and only making minor tweaks where required. But going forward, “digital” can no longer be a mere buzzword – there is an urgent need to assimilate these tools into current processes to drive change and compete from a position of strength. Harnessing new technologies, investing in specialised talent and boosting R&D spending could be the differentiator that helps Indian auto component manufacturers to not just become more relevant globally, but also to successfully take on the global competition on home turf. A leading auto component manufacturer has recently embraced an AI-driven digital solution on the shop floor of the manufacturing plant for encouraging social distancing and managing attendance. This step could help them keep their employees safe and avoid a partial or full shutdown.
The automotive industry has been going through a rough period. But it is possible to dream big again. A concerted effort to operate with localise-optimisedigitise in mind could make all the difference to the performance of auto component manufacturers, aiding not just the recovery of the industry but also making critical contributions to the GDP of the country in difficult times. ACI -----------------------------------------Shivanshu Gupta is a Senior Partner in McKinsey’s Bengaluru office and Barathram A is Associate Partner at McKinsey’s Chennai office. -----------------------------------------The views expressed by the authors are their personal opinions and do not necessarily reflect the views of the ACI magazine.
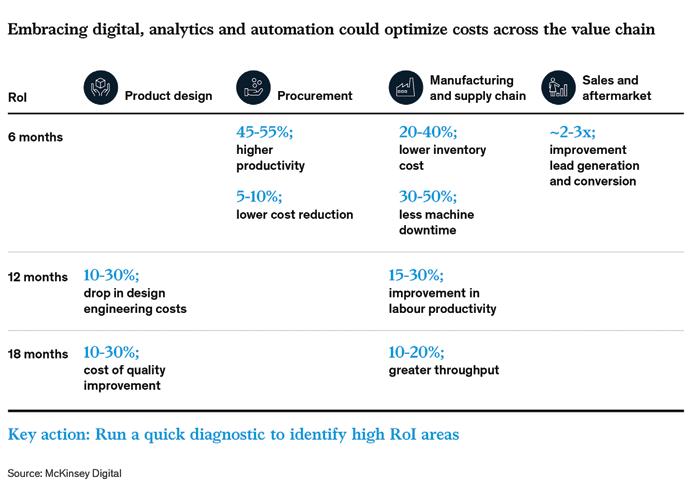
India Sustainability Leadership Summit 2020
Frost & Sullivan and TERI had the ‘Decade of Action’ in the spotlight at the India Sustainability Leadership Summit 2020.
Story by: Deven Lad Frost & Sullivan and The Energy and Resources Institute (TERI) got together for yet another edition of the India Sustainability Leadership Summit 2020 and the 11th edition of Sustainability 4.0 Awards. Hosted virtually against the backdrop of extraordinary circumstances, the summit got stakeholders of the automotive industry Sustainability 4.0 Awards Open to companies across manufacturing, logistics, hospitality, IT & ITES, KPO, BPO, banking, financial services & insurance, construction, telecommunications, and to think beyond the Covid-19 induced setbacks. The healthcare sectors in India and the Middle East, summit, instead, put the spotlight on jump-starting the Sustainability 4.0 Awards evaluation model the ‘Decade of Action’ for growth. Like every edition, comprised of four major parameters - people, the 2020 edition, as a platform, promoted sustainable planet, purpose, and partnership and 13 subbusiness strategies for the long term. Averred Ajay parameters evaluated by a team of experts from Mathur, Director General of TERI - The Energy Frost & Sullivan and TERI. & Resources Institute, and a member of the Prime Minister’s Council on Climate Change, “Longer- The winners: term sustainability is only possible by building up n Reliance Industries Limited, Navi Mumbai won linkages between the strategy of the organisation, its the ‘Sustainable Corporate of the Year Award’. governance and financial performance, environmental, n Genpact India Private Limited, Gurgaon won social, and economic governance. In other words, the the Leaders Award – Mega Large Business, entire ecosystem”. “Short-term profitability has to be Service Sector. nurtured together with the long-term sustainability for n Henkel Adhesive Technologies India Private recovering from the pandemic today as well as to put us Limited, Navi Mumbai won the Leaders Award – onto the path of a low-carbon future in a 2040 or 2050 Large Business, Process Sector. timeline,” he stated. n Ramky Enviro Engineers Limited, Delhi won Sustaining the transformation the Certificate of Merit – Challengers Category. n Faurecia Interior System India Private Limited, Ambassador Ajai Malhotra, Advisor (Climate Pune won the Certificate of Merit – Safety Change), Project Management Unit, TERI referred Excellence.
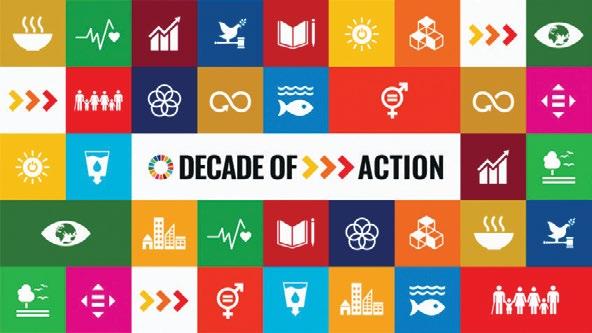
to the frailties, blaming the latter for contracting global economies, deepening existential divides, and the decline in global output, sparing none. “The World Bank estimates an additional over 49 million people to face extreme poverty. It makes attaining the Sustainable Development Goals (SDGs) a big challenge,” he opined. He cautioned that a global bounceback was crucial to stay on track to attain the SDGs. Sarwant Singh, Managing Partner and Regional Leader, Frost & Sullivan drew attention to recycling, refurbishing, remanufacturing, reuse and redistribution as crucial principles to be followed by the industry. To contribute to a circular economy, it is
Upfront Covid-19: Weighing on SDGs 2030
1. Has the pandemic put off the targets for SDGs 2030 in the near term given the existential crisis for businesses?
Vivekananda: Covid-19 has stalled the developmental activities across the world. The impact of this pandemic will be long-lasting, influencing all spheres of human lives and slowing all developmental activities including, ambitious and aspirational Sustainable Development Goals (SDGs). Covid-19 had negatively affected several goals including, SDG 1 (no poverty), SDG 2 (zero hunger), SDG 3 (good health and wellbeing), SDG 8 (decent work and economic growth), and SDG 10 (reduced inequalities). At the same time, the pandemic had brought temporary relief in areas related to SDG 12 (responsible consumption and production), SDG 13 (climate action), SDG 14 (life below water), and SDG 15 (life on land) with shortterm gains.
2. How has it impacted the automotive industry under the broad spectrum of energy that you oversee across the environment, engineering and manufacturing goals?
Naynish: There was no impact on the environment and engineering goals. OEMs are still launching new vehicles and showcasing engineering capabilities. However, there is an impact on manufacturing
Naynish Kulkarni, Associate Director, Mobility Practice, Frost & Sullivan
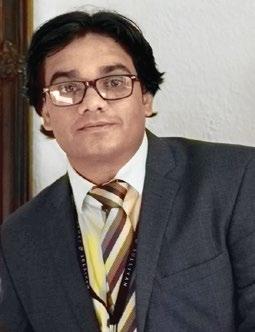
goals. Vehicle production has taken a big hit due to Covid-19. It is estimated that vehicle production will be half, compared to FY20. The commercial vehicle segment and the passenger vehicle segment have been highly impacted. Also, component manufacturers are not operating at their full manufacturing capacity. They are operating at about 40-50 per cent. A rise in Covid-19 cases in certain areas (auto hubs) makes it difficult for component manufacturers to even operate at reduced levels. They also have to shut down locations with positive cases, which is directly impacting their manufacturing goals.
3. Having assessed and benchmarked the best practices, what are the emerging trends over the last year? Would you say these have a shelf life again with companies required to go back to the drawing board?
Vivekananda Bhat, Industry Manager, Manufacturing & Process Consulting Practice, Frost & Sullivan

Vivekananda: We could see companies ambitiously working on reducing Scope 3 emissions, achieving water positivity, using more renewable energy, and enhancing stakeholder engagements. Despite the impact of Covid-19, this is likely to continue as most of the companies realised that the responsible utlisation of natural resources and creating a positive difference in the society needs to be an integral part of their business strategy.
4. How do you find the Government intervention to drive recovery in the automotive sector (including a focus on MSME) looking at the pandemic impacted quarter? How does India compare among other Asian countries in hindsight?
Naynish: There has been no separate policy or initiative to drive the auto sector recovery. However, the current economic package will bring much-needed relief to several stressed sectors and industries as a significant proportion of the industries in the auto component sector are MSME. The impact of Covid-19 on India and other Asian countries has been similar. The pandemic has been a bane to vehicle producers in Asia, but the industry’s reaction is just the tip of a supply chain disruption as heightened demand reduction of components such as steel coils and foams are in the offing. A bigger impact on the Indian automotive sector will be felt with the imports. Raw materials like steel plates, foams, and polypropylene, and finished products like electronic components are all imported from other countries.
5. Do you foresee consolidation or a higher degree of collaboration in the automotive supply chains?
Naynish:It is difficult to comment on the short term impact, but in the long run, consolidation is definitely on the cards. Effective collaboration with supply chain partners requires organisations to share valuable information in real-time (which may or may not be a comfortable option for manufacturers). Consolidation requires joint planning, process redesigning, as well as sharing some level of risk and rewards, besides collaborative decisions on several issues, etc.
crucial to build upon the aforementioned principles right from the design stage, he said in accord with the industry views. “From day one of designing the products, you can achieve it over the lifecycle of a vehicle and the ecosystem, for instance. Suppliers, manufacturers, retailers down to the landfill waste management could contribute to a linear economy,” he expressed.
On ‘innovating to zero’, the mega vision of shifting focus and development on products and technologies to attain the latters’ goals of bringing social innovation to the forefront, Singh was quick to highlight the 17 SDGs set by the United Nations and the underlying goals of innovating to zero gaining significance amidst a pandemic. “Sustainability is a circular economy where goods and services are produced in a sustainable manner and are the next big trillion-dollar economy,” he explained. He also cautioned the industry to brace itself for a two-speed economy where one economy could recover faster than the other case in point China, India and Europe.
Recession and economic stimulus
Singh, in a pertinent observation, drew attention to the recessions being backed by economic stimulus. “This recession has an economic stimulus too and a large portion of the stimulus is reserved for building and developing sustainable technologies,” he mentioned. Singh gave example of France and Germany where the government doled out special incentives to boost the
Sarwant Singh, Managing Partner and Regional Leader, Frost & Sullivan

demand for electric vehicles. Of the opinion that it had the potential to change the transport network of the future, he said, “Last year 2.3 million electric vehicles were sold. In July 2020, they hit the peak after a big dip in MarchApril for most countries. There has also been a huge decline in interest for ICEs.”
This change, opined Sarwant, has brought multiple industries including the chemicals industry in the quest for more sustainable materials. It has also brought the energy industry together, he added.
Simon Stolp, Country Lead (India) - Energy and Extractives, World Bank explained macro-level fundamentals as an imperative to jumpstart the decade of action. “I think if we look at Covid-19 through that philosophical lens, we can see that there is actually an opportunity in this crisis to jumpstart that decade of action. This I think is wound up in the structure of the economic stimulus that will be distributed across the globe, including in India over the coming months and years,’ he explained. On the short term horizon, Stolp called
Shloka Nath, Executive Director, India Climate Collaborative Head of the Sustainability and Special Projects at Tata Trusts

upon the industry to focus on job creation. He also urged the need to support “shovelready” projects and cautioned against being bogged down by long lead times. Atul Bagai, Head India Country Office, UN Environment urged the industry and government alike to embed sustainability into the economic recovery weighed down by Covid-19.
PPP model
Shloka Nath, Executive Director, India Climate Collaborative Head of the Sustainability and Special Projects at Tata Trusts reinforced the need for PublicPrivate Partnerships (PPP). “It is crucial to overcome the Covid-19 crisis and to source additional finance to drive the transformation,” she emphasised. She called for the need for a structural economic recovery through the stabilisation of financial institutions and the use of information planes. She went on to highlight the Micro, Small and Medium Enterprises (MSME), hit hard by the pandemic and deemed to have been primed for transformation. “Capacity building for the adoption of
Ajay Mathur, Director General of TERI - The Energy & Resources Institute, and a member of the Prime Minister’s Council on Climate Change
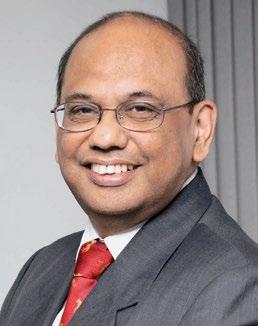
energy-efficient technologies and processes by MSME based on recommendations will set out,” she said.
She recommended a green finance task force be formed on the lines of the joint effort of the UK government in London. “The taskforce designs the overall roadmap for promoting finance. It advocates the necessary policy and regulatory changes,” she explained. Terming it essential to have coordination amongst policymakers, regulators, institutional investors and to create consumer awareness, she expressed it was time for sustainability needs to go from “niche to mainstream.” The need to build a rural economic resilience also found a mention. María Mendiluce, Chief Executive Officer, We Mean Business recommended active participation from corporate India and its supply chains to fight climate change. “Corporate India has the opportunity to come out of this pandemic as innovators, and champions or sustainable champions. The next 10 years are crucial, decisive, and will decide the future,” she concluded. ACI
A SIAM Environment Series Part 2 Environmentally Sound Management of ELVs in India
The second lecture of the two-part environment series provided an overview of the technological imperatives in design and material eco-efficiency of ELV recycling.
Story by: Deven Lad In part one (refer to the October 2020 issue of the magazine) of the two-part environment series, SIAM provided an overview of the supplier and the Original Equipment Manufacturer (OEM) function, regulations and policy, and the economic impact of recycling ELVs. Taking it forward, the second and the final lecture focussed manufacturing process on the whole. Dr Hans-Rainer Lotz, Recycling bei Volkswagen AG drew the attention of the Original Equipment Manufacturers (OEMs) to the possible means of turning recycling into an easier and less hazardous process. Averred Dr Lotz, “As per the directive of the European Parliament and the council on ELV (2000), on the technological imperatives in design and material treatment-related requirements include environmental and eco-efficiency of ELV recycling. The focus was on vehicular technical standards for pre-treatment ( removal of fluid designs supporting vehicle refurbishment. It outlined the and airbags ) and dismantling.” “Less use of hazardous role of material designers in incorporating the material substances in vehicles has been suggested by the directive advancements at the component design stage and in the with restrictions on Mercury (Hg), Cadmium (Cd), Lead

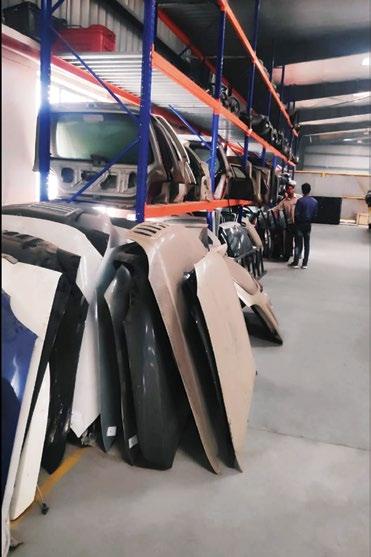

(Pb) and Chromium (Cr),” he cited. Dr Lotz admitted to the process challenging OEMs and also expensive to deal with.
Recycling at Volkswagen
As per the European Parliament directive, the design requirement for new vehicles must take into full account and facilitate the dismantling, reuse and recovery, including components and the materials used. Dr Lotz cited the Volkswagen policy - ‘Internal Standard 99000’ claimed to make dismantling an easy process, in compliance with the legal requirements. On challenges, he called upon the need for OEMs to liaise with material equipment manufacturers. There is a need to integrate the high-quality recycled materials and other parts to help the market mature, he opined. Citing the European parliaments’ European circle plastic alliance, he highlighted the Volkswagen groups’ commitment through active participation in group activities including supplier exhibits of recycled materials complying to group standards like the component and material coding suited to reuse and recovery. Dr Lotz also highlighted the International Dismantling Information System (IDIS) initiated by 10 European OEMs encompassing safety guidelines and key requirements.
CERO Recycling
Speaking on ELV infrastructure, Sumit Issar, Managing Director at Mahindra Intertrade Ltd., called upon the stakeholders to tap the potential of organised recycling. Issar projected the 2025 ELV volumes for two-wheelers to reach 91.6 million from 58.8 million, 36.4 million for cars and commercial vehicles up from 22.7 million. “India imports close to six to seven million tonnes of scrap steel every year due to the gap in domestic demand and supply. The unorganised process in India leads to unsafe disposal of hazardous waste and lacks the process and transaction transparency that needs to be addressed,” he explained. Adding that an efficient recycling process could have manifold
Hans-Rainer Lotz, Recycling bei Volkswagen AG
Ashim Sharma, Partner and Group Head, Business Performance Improvement Consulting (Auto, Engg. & Logistics) at Nomura Research Institute
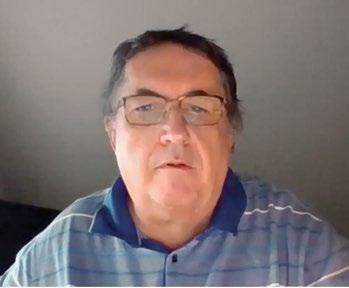
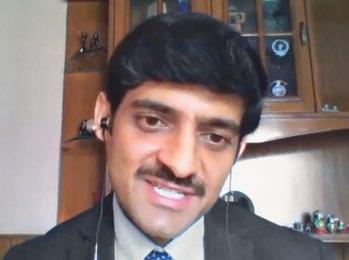
benefits; efficient recycling could help save energy, reduce emissions, conserve resources, preserve foreign exchange and create employment. For instance, CO2 emissions are reduced by 58 per cent through the use of ferrous scrap, pointed Issar.
Citing operations and the threeyear roadmap at CERO Recycling, a Joint Venture between Mahindra Accelo & MSTC (A Government of India Enterprise), mentioned Issar, the latter plans to invest in 25 shredding units across the country. The exercise would lead to a recycling capacity of 2,00,000 cars per month. Backed by an approximate Rs.1000 crore investment it will also help in job creation by way of the new shredding centres. Explained Issar, typically, a car was equivalent to 65 per cent steel, 10 per cent plastic, nine per cent aluminium, five per cent rubber and one per cent copper. Issar lauded the government for its efforts in helping formalise the sector.
Circular Economy in India
Ashim Sharma, Partner and Group Head, Business Performance Improvement Consulting (Auto, Engg. & Logistics) at Nomura Research Institute presented a comparison of the circular and linear economy while touching upon the ELV recycling scenario in India. “A circular economy focusses on collecting an ELV in an organised manner before recycling it and meeting the objective of maximum material recovery in an effort to minimise waste,” explained Sharma. “India will have more than 22 million ELVs by 2025 which translates to a potential of generating Rs.32,700 crore worth of scrap value by 2025,” he mentioned. An estimated 2.8 million four-wheelers at a scrap volume of three million tonnes and valued at Rs.14000 crore, 1.2 million heavy trucks and buses at a scrap volume of two million tonnes, valued at Rs.8000 crore are projected to make up the tally. In addition, 17.8 million two-wheelers at a scrap volume of 2.1 million tonnes valued at Rs.100,000 crore and 0.7 million three-wheelers at a scrap volume of 0.3 million tonnes valued at Rs.700 crore are projected to constitute the rest.
A win-win outcome
ELV recycling in India will result in both direct and indirect benefits for the environment. Citing the government focus on vehicular pollution, Sharma was quick to blame the production processes of virgin materials, especially the extraction oriented mining activities. “This involves significant emissions of greenhouse gases such as CO2. In comparison, the recycled materials are low on carbon footprint,” opined Sharma. “ELV recycling can be a major boost to new vehicle sales too besides directly reducing the waste dump in landfills and helping the country save valuable forex reserves,” he said. Citing key policy documents and guidelines released over the years with the objective of organising the market and harnessing its full potential, according to Sharma, pursuing
Sumit Issar, Managing Director at Mahindra Intertrade Ltd.
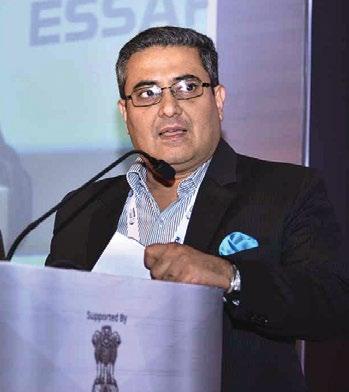
ELV recycling will lead to a win-win outcome for OEMs irrespective of policy developments. Calling upon the need for organised recycling and a constant outflow of ELVs, mentioned Sharma, “It will also lead to an improvement in inventory management at dealerships with the latter doubling up as collection centres.”
Benchmarking with the globe
The ELV recycling mechanisms across major global geographies are regulated by national-level legislation, with the industry-driven USA model an exception. Explained Sharma, China is closest to India in terms of ELV PARC however, the industry maturity is very low making the former an inappropriate reference point. “Europe and Japan are the best reference points for India. Around 70 to 80 per cent of vehicles are recycled in Europe and Japan,” he opined. Explaining that the large scale recyclers dominate the market including in the USA with the smaller informal sector constituting the rest. Taking a leaf out of the global case studies, Sharma drew attention to the consumer incentives and extended producer responsibility as being instrumental in the success attained. “Recycling process is For representation purposes only.
Dr Regina Kohlmeyer, Scientific officer, German Environment Agency- UBA
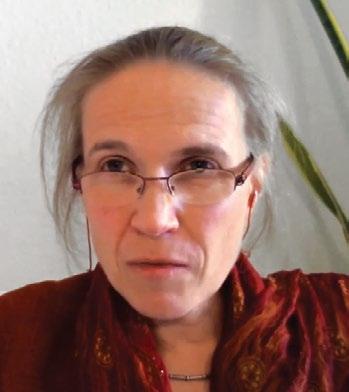
similar in both the models ( European and Japanese ) until the step of shredding. However, the post shredding treatment differs significantly,” he stated.
EU and Japanese recyclers target material recovery rates of 80-85 per cent, and it is the R&D progress that has played a major role in the high recovery rates, cited Sharma. As India looks to grow into an organised recycling market, Sharma called upon the need to learn from the advanced markets. To begin with, he urged the stakeholders to streamline the current ELV collection and dismantling process which he said was highly unorganised with a large number of small players using unscientific methods for processing. “The use of the aforementioned unscientific methods leads to severe environmental pollution besides endangering workforce safety and resulting in low levels of material recovery in contrast,” he warned.
Dr Regina Kohlmeyer from the German Environment Agency- UBA shed light on international policies and practices for eco-efficiency in the ELV management process. Speaking on the eco-efficient design, the ban on hazardous substances and heavy metals, Kohlmeyer cited the example of Toyota and Volvo. Toyota’s easy to dismantle wire harness innovation eliminates the need to interfere with other components. Volvo, for instance, is aiming for a 25 per cent plastic recycling capability for cars by 2025. Speaking of countries encouraging manufacturers to integrate an increasing quantity of recycled materials in vehicles, Kohlmeyer cited the need to adopt a design plus recycling approach. For instance, under the European circular economy plan 2020, a new framework for batteries will be proposed in the EU and benchmarked by other countries looking to follow suit.
Silvia Vecchione, Senior Environmental Policy Manager at the European Automobile Manufacturers’ Association (ACEA) called for the need to revise the European circular economy action plan 2.0. “The revision of rules will reduce virgin material consumption and eliminate waste generation and resulting pollution. A harmonised system could help in better management of information on substances of concern along the supply chain and can help in identifying them in waste streams,” she explained, stressing on the need for better enforcement.
Joshi Devaputhran Sikha, Director of Vikar Recycling Solutions drew attention to the online platforms like
ScrapMycar. Admitting to disposing of ELVs being a difficult process and a highly stressful one for the owner, Sikha stressed on the need to benchmark with the advanced markets and called for the need to devise a stress-free and transparent process suited to the country. ACI
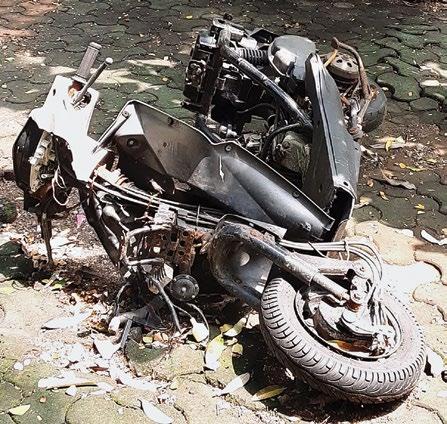
DEP MeshWorks Tyre Modelling
The Hex Meshing Tool from DEP MeshWorks enables rapid tyre modelling and performance optimisation across vehicular segments. Story by: Deepti Thore
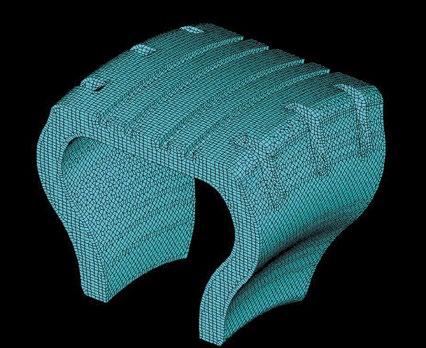
Tyre modelling has come a long way from just representing tyre data obtained from mathematical representation limited to static conditions. A testimony to it being more dynamic today than ever before is the proprietary software platform - ‘MeshWorks’ from Detroit Engineered Products (DEP). MeshWorks is claimed to enable a technologically superior tyre modelling technique for motorcycle tyres, passenger car tyres, and offroad tyres. Through hex meshing, a complex but standard collection of cubes, concept designs are used to analyse geographical and cartographic data. The latter is known to study the rules of the spatial arrangement of phenomena and their interrelationships, dependence, and development. According to Basant Sharma, Vice President, DEP, it is a tedious and time-consuming process to mesh or model the complexity of tyre geometry. Especially the treads. Of the opinion that the time spent to model tyre treads constituting the little grooves and ridges, crucial to braking and safe manoeuvring is directly responsible for the end quality. It also results in better simulation and comparison against the real-world scenario, he explained. He cites the amount of time a user can spend is usually very limited, and thus any automation in modelling and meshing are always welcome.
Overcoming shortcomings of conventional tools
It is well known that tyre modelling requires a lot of expertise and takes up several hours. Addressing this void, DEP
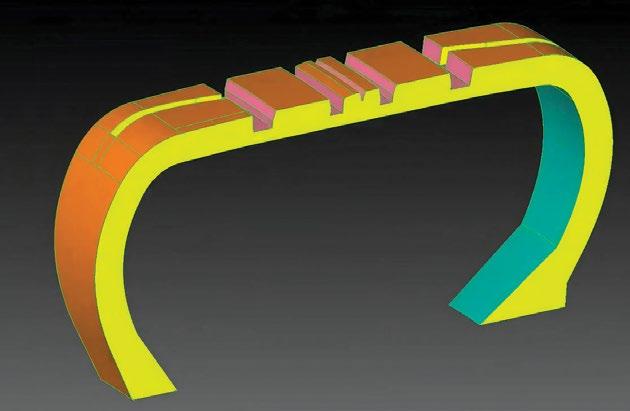
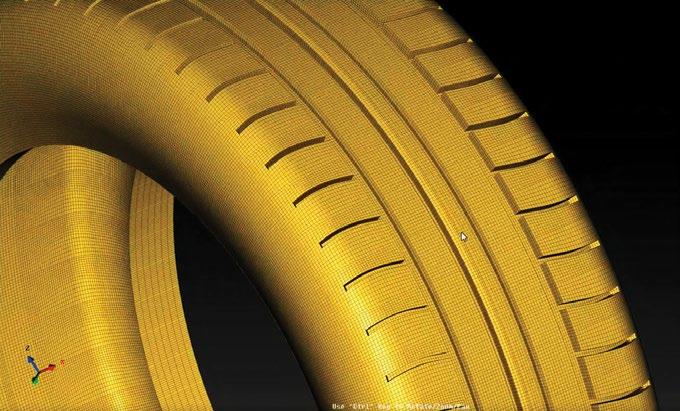