Zero-Emissions
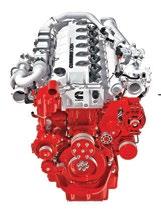
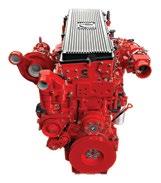
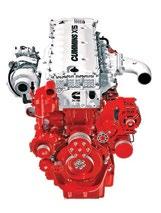
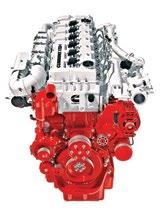
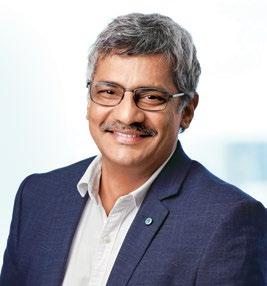
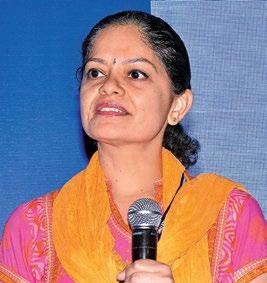
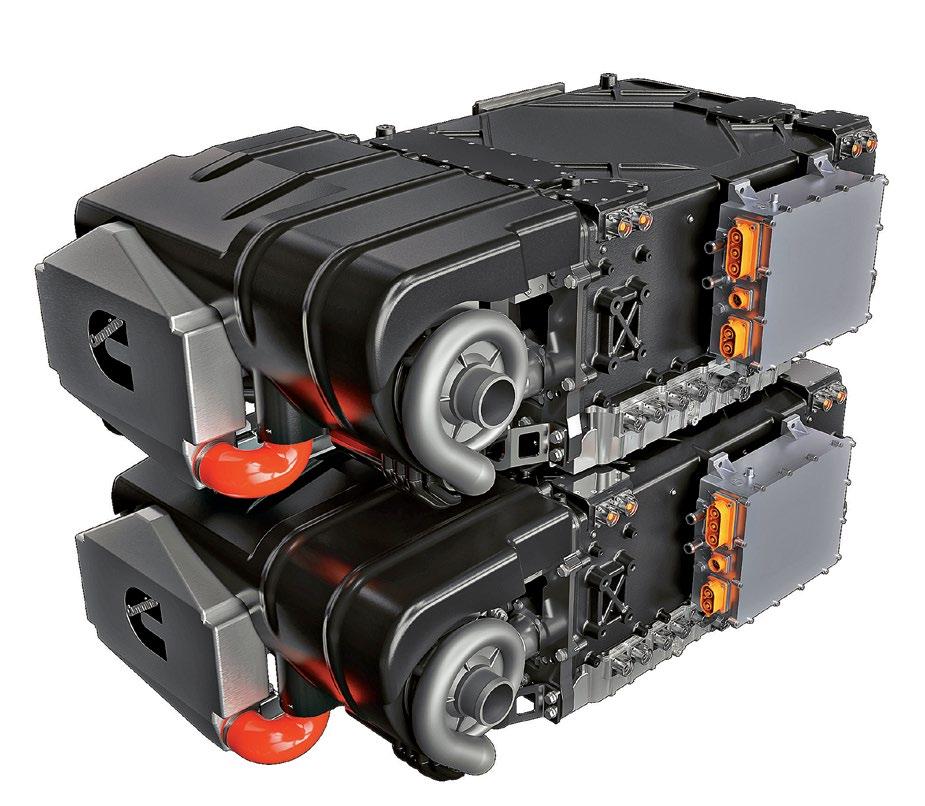
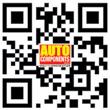








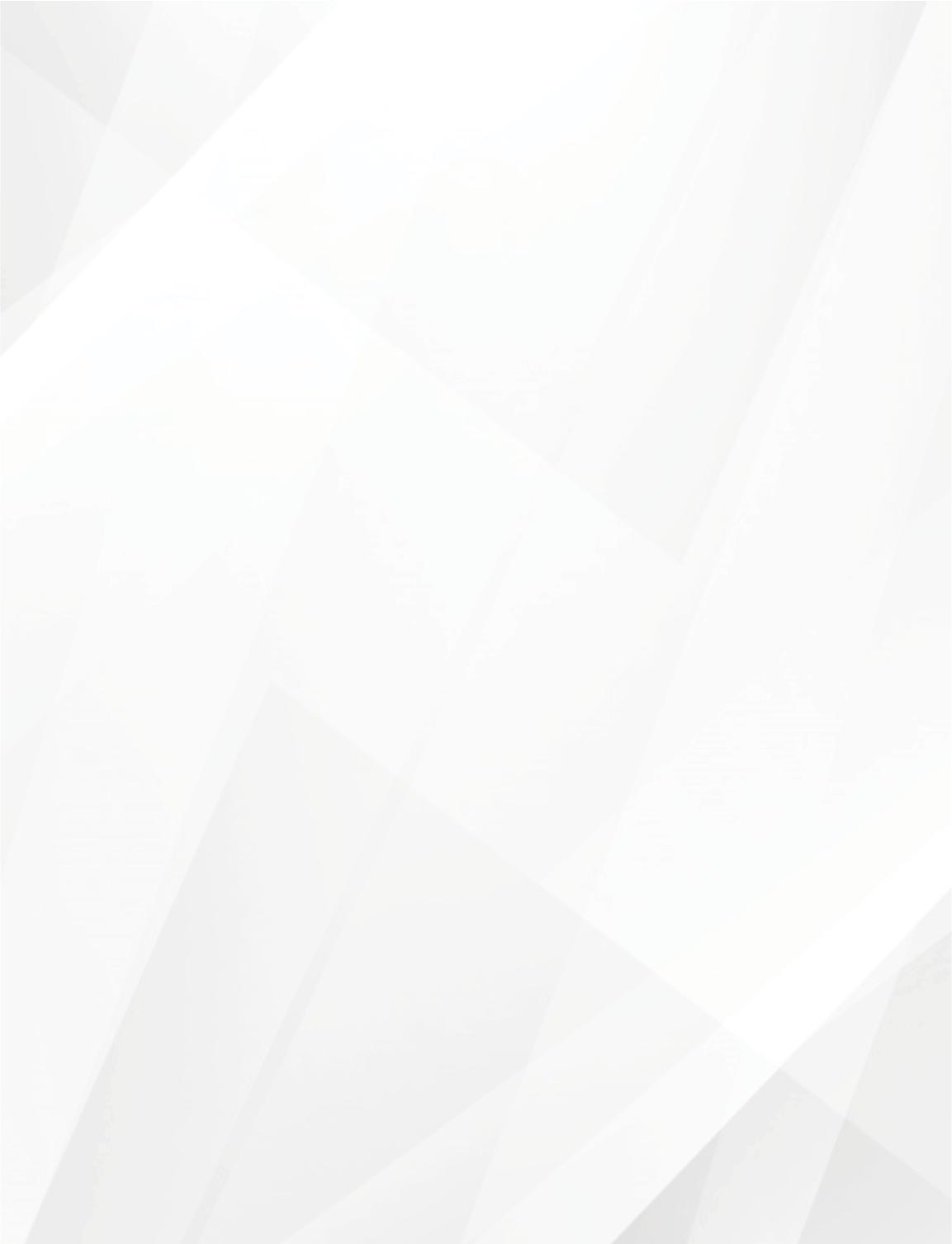



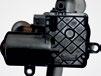
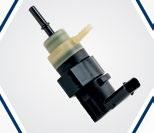
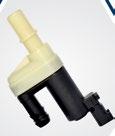
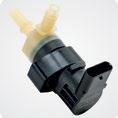

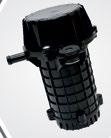
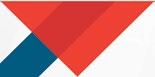
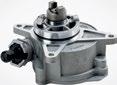
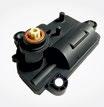
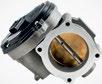
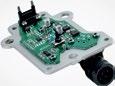




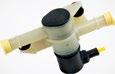
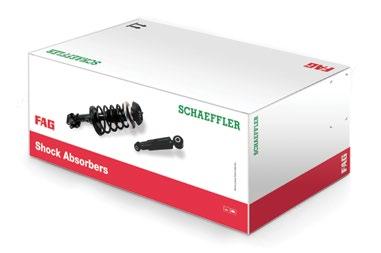
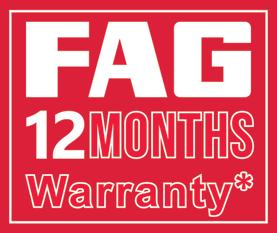

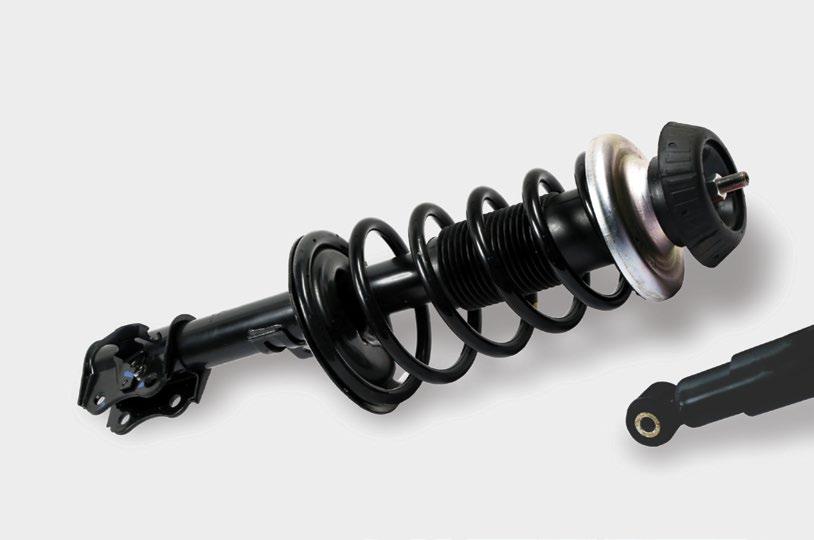
Cummins Inc continues to optimise its engines. Ashish Bhatia looks at the products worked upon to attain net-zero emissions in a serious push.
Ashok Leyland has taken a step for cleaner engines. Prateek Pardeshi looks at the latest in its lineup.
608, Trade World, 6th floor, C wing, Kamala Mills
Compound, Senapati Bapat Marg, Lower Parel (W), Mumbai - 400013, India.
Tel +91 9321546598, Email us at a.bhatia@nextgenpublishing.net
Executive Editor
Ashish Bhatia
Editorial Advisory Board
H. S. Billimoria, Aspi BhathenaHead - Design & Production Ravi Parmar
Correspondent: Deepti Thore, Prateek Pardeshi Sumesh Soman
Asst Art Director
Ajit Manjrekar
Production Supervisor Dinesh Bhajnik
Publisher Marzban JasoomaniAssociate Publisher & General Manager (North & East)
Ellora Dasgupta
General Manager – South Girish Shet
Deputy General Manager – North & East Chanchal Arora (Delhi)
Regional Advertising Manager
Raghul Krishnan R (Bengaluru)
Regional Manager
Rajesh Gogate (Mumbai)
Manager Circulation - North and East Kapil Kaushik (Delhi)
Subscription Supervisor
Sachin Kelkar Tel +91 9321546598
Apple Newsstand & Magzter Queries: help@magzter.com
Territory Sales Incharge (Circulation)
Srinivas Gangula (Hyderabad) Cell +91 09000555756
Territory Sales Incharge (Circulation)
Vidyasagar Gupta (Kolkata)
REGIONAL MARKETING
Next Gen Publishing Pvt. Ltd.
09804085683
608, Trade World, 6th floor, C wing, Kamala Mills Compound, Senapati Bapat Marg, Lower Parel (W), Mumbai - 400013, India, Mumbai -400013.
Tel +91 22 9321546598
26 B, First Floor, Okhla Industrial Estate, Okhla Phase III, New Delhi - 110020, India
Tel +91 11 42346600/78, Fax +91
S.No.261/G.L.R.No.5,
All of us at NGPPL are deeply grieved and shocked to record the sudden and untimely demise of our dear and respected Cyrus Pallonji Mistry in an unfortunate road accident.
A civil engineer from Imperial College, London and a a management graduate from the London Business School, Cyrus used his education along with his entrepreneurial mindset to help the Shapoorji Pallonji Group reach new heights in the engineering, construction and asset development businesses.
Cyrus kept a low profile like other members of his family. Although introverted, he was a humble, simple and kind individual and a very patient listener. Approachable to all, Cyrus was known for his ethics and integrity. Above all, he was a fine human being.
Cyrus’ sudden demise is a big loss to the Shapoorji Pallonji family, Group and all of us. We pray to the almighty that his soul rests in eternal peace.
Good thoughts, good words, good deeds!
With 30 per cent of the components in a vehicle under direct threat of extinction, the focus will continue to be on leveraging parts localisation, commonality, modularity and scalability.
Views
he auto components industry wants to stay ahead of the curve. Building on the momentum from the last fiscal, the component manufacturers with their tier suppliers want to be ready for the next wave of opportunity. With no clear roadmap on the single dominant technology of the future, it is clear that a one fit for all approach won’t work. Instead of succumbing to disruptions all around with the non-traditional automotive companies forcing a change in approach, the well-established players have taken up the challenge as a gateway to new opportunities. The conditional support from the government to manufacturers invested in Advanced Automotive Technology (AAT) has also made a case for this transition. Component manufacturers are looking to strike the right balance between staying true to their DNA for profitability and investing in the sunrise sectors for future growth. Both are driven by advancements in technology and require the industry to significantly scale up its R&D budgets. The success or failure though will eventually be dictated by the pursuit of the lowest total cost of ownership. With 30 per cent of the components in a vehicle under direct threat of extinction, the focus will continue to be on leveraging parts localisation, commonality, modularity and scalability including on the smallest components. Watch out for the detailed coverage of the 62nd ACMA Annual Session 2022 in our upcoming issue where the stakeholders of the industry, spoke upfront.
Ashish Bhatia Executive Editor | a.bhatia@nextgenpublishing.netPublishing
6th floor, C wing, Kamala Mills Compound, Senapati Bapat Marg, Lower Parel (W), Mumbai - 400013,
Published by Marzban Jasoomani on behalf of Next Gen Publishing Pvt. Ltd., 608, Trade World, 6th floor, C wing, Kamala Mills Compound, Senapati Bapat Marg, Lower Parel (W), Mumbai - 400013, India. Printed at Uchitha Graphic Printers Pvt. Ltd., 65, Ideal Industrial Estate, Mathuradas Mills Compound, Senapati Bapat Marg, Lower Parel, Mumbai 400013, India., India. Published at Next Gen Publishing Pvt. Ltd., 608, Trade World, 6th floor, C wing, Kamala Mills Compound, Senapati Bapat Marg, Lower Parel (W), Mumbai - 400013, India.
All readers are recommended to make their own independent enquiries before sending money, incurring expenses or entering into commitments in relation to any advertisement appearing in the publication. Auto Components India does not vouch for any claims made by advertisers for their products and services. The editor, publisher, printer and employees of the publication shall not be held liable for any consequence in the events of such claims not being honoured by the advertisers. All disputes are subject to the exclusive jurisdiction of competent courts and forums in Mumbai only.
The Cabinet recently approved the amendments to the development of semiconductors and the display manufacturing ecosystem in India. The amendments entail a 50 per cent financial support to the project cost on a pari-passu basis for the technology nodes under the scheme for setting up semiconductor fabs in India. It also
The Minister of State, Ministry of Heavy Industries, Krishan Pal Gurjar met with the German delegation led by the Minister of Economic Affairs, Science and Digital Society of the Free state of Thuringia, Germany, Wolfgang Tiefensee. In the bilateral meeting, it was asserted that the synergies between India and Germany were crucial to the area of Green Hydrogen. The work on multiple aspects here was deemed crucial to India’s efforts on ensuring energy security. The two nations are synergising on Research and Development (R&D) in the areas like exploring alternate EV battery chemistries like sodium-ion and aluminium-air etc. It also expands to ensure a robust supply chain of rear earth metals like nickel and cobalt. The Indo-German Green Hydrogen Task Force will explore cooperation in the production, utilisation, storage and distribution of green hydrogen. The two will build enabling frameworks for projects, regulations and standards, trade and joint R&D projects.
entails a 50 per cent support under the scheme of setting up display fabs. A 50 per cent fiscal CapEx support was also extended under the scheme for setting up compound semiconductors, silicon photonics, sensors fab and semiconductor ATMP/OSAT facilities in the country. This will also apply to the discrete semiconductor fabs. It is
expected that the amendments will expedite investments and a facility will be commissioned in the near term. The 45nm technology nodes and higher have been identified to have high demand driven by industries like automotive, power and telecom-based applications. Together, they constitute 50 per cent of the overall projected demand.
India has committed to reaching USD 300 mn worth of electronics manufacturing and exports by 2025-26. Minister of State for Electronics and Information Technology, Rajeev Chandrashekhar, speaking at a gathering at Tirupati, in Andhra Pradesh said, “The Government is keen on supporting startups and entrepreneurs keen on investing in these sectors and is committed to working in partnership with all the states.” In his visit to the electronics manufacturing cluster in Tirupati for the first lithium cell manufacturing plant, he drew attention to the commitment of rupees 25 lakh crores, a 24x growth over the 2014 projections. The commercial production and formal opening are slated for the near term. The plant is said to have a 270 Mwh and 20,000 cells of 10Ah production capacity. Set up by Munoth industries with an outlay of Rs.165 crores, it is one of the two centres being built in the temple town.
In the wake of the recent road accident involving the unfortunate demise of businessman Cyrus Mistry, the country has realised the importance of occupant safety and is pursuing it with renewed vigour. With Union Minister Nitin Gadkari among other senior stakeholders of the industry calling it a personal loss, the road safety blueprint of the country is undergoing
scrutiny. Among the mandates for passengers is the compulsion to fasten rear seat belts. Original Equipment Manufacturers (OEMs) are required to look at alert systems in the wake of a passenger failing to secure the seat belt akin to the systems installed for the front passengers. This comes on the close heels of the Government asking OEMs to install
six airbags which is the case for the export models. Seat belt reminders or alarms will be required in the M and N category vehicles, with an audio-video warning if the seat belts, including the rear ones, are not worn, according to the draft proposal. There will also be a speed alert system to detect excessive speeding and a manual override for the central locking system.
The Executive Committee of the Society of Indian Automobile Manufacturers (SIAM), the industry’s apex body elected Vinod Aggarwal, Managing Director and Cheif Executive Officer, Volvo Eicher Commercial Vehicles Ltd. (VECV) as the new President for 2022-23. He succeeds Kenichi Ayukawa san, Executive Vice Chairman and Whole Time Director, Maruti Suzuki India Ltd who completed a successful term involving the two pandemic marred fiscals. The election of new office bearers took place during the executive committee meeting, which took place following SIAM’s Annual General Meeting. After taking over as SIAM President, Aggarwal said, “We are grateful to the government for its constant focus on improving the infrastructure through significant investments and such policies that modernise this industry. I am humbled by the opportunity to contribute to the new era of Amrit Kaal, working closely together with the SIAM members.” The new office bearers include Shailesh Chandra, Managing Director of Tata Motors Passenger Vehicles Ltd and Tata Passenger Electric Mobility Ltd, as the Vice President for 2022-23. Satyakam Arya, Chief Executive Officer and Managing Director, Daimler India Commercial Vehicles (DICV) was elected as the Treasurer. Sunjay Kapur continues as the President at Auto Component Manufacturers Association (ACMA) for the next year.
The Gujarat Government signed a Rs.1.54 lakh crore Memorandum of Understanding (MoU) with the Vedanta-Foxconn Group. Hailed as a significant development for the manufacture of semiconductor and display fab in the country it had other states like Maharashtra rue the loss of the investment of such a scale. Expected to boost the economy and employment, it is expected to help create a huge ecosystem of ancillaries and in turn, help the Micro Small and Medium Enterprises (MSMEs). Chief Minister Bhupendra Pal hailed it as a significant investment to further the Atmanirbhar Bharat vision of the government.
BorgWarner has inaugurated its second plant in Thiruvallur District near Chennai, India. The new plant provides extensive manufacturing, assembly and storage space. With the two sites known to operate in proximity, the company is expected to increase production efficiency and strengthen the company’s position in the region. The assembly of highperformance engine control
and Variable Camshaft Timing (VCT) systems will be centralised in the new
Kalyani Powertrain Ltd. (KPTL), a wholly owned subsidiary of Bharat Forge Ltd. is known for its critical chassis and powertrain components. KPTL has partnered with Harbinger Motors Inc. (Harbinger). Regarded well for its expertise in the medium-duty commercial electric vehicle industry, the two partners will collaborate on electric drivetrain solutions for the commercial vehicle market. ‘ElectroForge’, the new JV entity will leverage the strengths of both the partners to offer best-in-class drivetrains developed for the Class 3 through 8 markets, aimed at delivering superior efficiency and cost competency. At KPTL Pune, India facility, ElectroForge will leverage cutting-edge technology to deliver high-power, low-mass drivetrains with a new architecture tailored specifically for the durability and performance requirements of commercial vehicles. The JV adds to the existing product portfolio at Bharat Forge in power electronics and lightweight solutions for EVs.
facility. It will also provide space for warehousing and shipping. “The current
expansion was necessary; we needed the extra space to meet our increasing customer demand in India as a major local manufacturer,” said Pei Wang, Vice President and General Manager Asia, BorgWarner Morse Systems. With the opening of this plant, BorgWarner finds itself ideally positioned to meet the ever-growing business needs of the automotive industry, not only in India but also in the entire Asian market.
FPT Industrial, an Iveco Group subsidiary, dedicated to the design, production and sale of powertrains involving heavyduty engines for on-road and off-road vehicles, applications has picked up a minority stake in Blue Energy Motors (BEM), a Pune-based startup. The partnership saw its first fructification in the form of a new LNG truck launched at the hands of Union Minister, Nitin Gadkari at the company’s plant. The truck is known to be powered by the FPT N67 NG series of BSVI-compliant engines. Commenting on the launch, Sylvain Blaise, President of Iveco Group, Powertrain Business Unit, said “We are pleased and proud that Blue Energy Motors has chosen us for this major evolution in Indian commercial transport.” Claimed to be the most powerful natural gas engine on the market, it is compatible with CNG, LNG and biomethane. The N67 NG uses stoichiometric combustion to assure bestin-class fuel consumption and lower NVH levels. It lowers TCO by up to 40 per cent with a 28 per cent CO2 emissions reduction.
Bridgestone India has launched the Sturdo range of tyres for the passenger vehicle segment. According to the company, this new range of tyres has a special tread compound that extends tyre life by up to 29 per cent over its current offerings while also improving the ride quality on uneven roads. The
tyres are available in 27 sizes ranging from 12-inches to 16-inches with multiple variants. It is targeted at hatchbacks, sedans, and specific SUV models. The brand claims that the Sturdo tyre range has been developed for Indian roads. Speaking on the occasion, Parag Satpute, Managing Director, Bridgestone India, said,
Heraeus Noblelight announces two new dedicated members in India, Avnish Kumar and Surya Nautiyal, to provide additional sales, sales support and marketing. Avnish Kumar, Associate Sales Manager, is located in New Delhi and comes from the laser technology industry. Surya Nautiyal, Associate Sales Manager, is located in Mumbai and comes from the optics industry. They will work closely with Heraeus Noblelight’s longtime distributor, to meet the growing demand for UV curing technology/IR heater as Indian manufacturers across a wide range of industries, including automotive, seek to become more automated and process driven. Jim McMahon, Head of HNA Sales stated, “We are seeing significant demand driven not only by overall manufacturing growth in India, but also by a shift from labour-intensive to automated processes to minimise uncertainties and maximize productivity. Heraeus Noblelight’s infrared, UV curing and optics/ flash technology solutions help manufacturers automate production for better quality and increased capacity with the added bonus of sustainability.”
“Bridgestone has globally been on the forefront of tyre technology, and this is now showcased in India through our new offering in the passenger car segment- Bridgestone Sturdo. The Sturdo range has up to 29 per cent longer tyre life and is beneficial to the end user from the perspective of the economics of owning the tyres.”
Tata Motors launched the 5W30 synthetic engine oil developed to boost the performance of the new-generation BSVI diesel engines. The new 5W30 synthetic engine oil is claimed to have undergone extensive testing under varied and stringent conditions for over three years. Claimed to have been driven for more than 10 lakh kilometres, clocking more than 35,000 hours at the powertrain testing facilities, it uses a rich combination of high-performance polymer with a state-of-the-art additive technology blended in group III base oil. On this occasion, Rajendra Petkar, President and Chief Technology Officer at Tata Motors said, “Effective and efficient engine oil is one of the most convenient and costeffective ways of reducing a vehicle’s carbon emissions. The cumulative impact of such simple measures judiciously taken across all commercial vehicles plying on roads will result in an exponential improvement in carbon footprint reduction. Our team at the Engineering Research Centre (ERC) has been coengineering and developing lubricant formulations in-house, while closely working with strategic partners from the field of additive manufacturing.
Harman has built an OEfitted solution with a focus on enhancing vehicle safety. The introduction of ‘Ready Care’ is said to equip OEMs with advanced technology to improve driver safety and wellbeing. Armin Prommersberger, Senior Vice-President, Automotive Product Management at HARMAN International said “Safety remains a top concern for consumers when considering a new vehicle purchase – and now, with Ready Care, OEMs can improve vehicle safety in a significant new way. Ready Care is a set of solutions – cognitive distraction, stress-free routing, and personalised comfort –that can work together or
independently to improve safety and reduce driver stress. Banking on newly developed machine learning algorithms, the steps involve
gathering and processing data from in-vehicle cameras and sensors to monitor a driver’s state. It generates customised in-vehicle cabin
prompts to trigger a range of behavioural responsesincreasing awareness, and is claimed to alleviate stress or induce ease and relief.
In a bid to accelerate the transition to EVs, California could ban ICE-powered vehicles as early as 2035. This could have a ripple effect on other states that follow California standards. The regulators put in place a plan to restrict and ban the sale of gasoline cars. Looked at as the beginning of the end of the ICE-age, the restrictions proposed by California Air Resources Board, if allowed to come into force could see nearly a third of the United States following suit. Notably, there are interim restrictions proposed too. By 2026, 35 per cent of the passenger vehicles sold must produce zero emissions; the number must climb to 68 per cent by 2030. Others call it “extremely challenging” to meet.
It will ride on factors like inflation, charging ecosystem, supply chains,
critical mineral availability and the pricing metrics.
In an UpFront conversation, Renuka Srinivasan, Sales Director (SIMULIA)Dassault Systèmes speaks to Sumesh Soman on the importance of crash test simulation and how active and passive safety is now becoming sought after in the Indian automotive market.
Q. What is the future of crash test optimisation in the Indian automotive industry? How is it linked to Dassault Systemes in India?
A. Crash worthiness is gaining significance within the automotive sector as consumers are now more conscious of safety. The Government of India, assisted by bodies like the Automotive Research Association of India (ARAI), already have stringent regulations in place on ehicular safety. The crash regulations have also expanded to consider both occupant and pedestrian safety. With the emphasis on electric vehicles, we can expect newer regulations specific to the newer energy sources that these vehicles are using, whether it is batteries, fuel cells or even hydrogen fuel. Regulations will also be needed for charging stations, swapping points and for recycling of used batteries.
A vehicle crash is a highly complex, nonlinear event involving large physical deformation of the structure in a fraction of a second. Dassault Systemes’ leading solver technologies allow simulation of the vehicle crash including advanced material behaviour, energy absorption and “dummy” simulation. Our technology is used for design exploration in the ideation or conceptual stage and also for high-fidelity predictive crash simulation during the detailed design phase. The model-based approach on the 3DEXPERIENCE platform from Dassault Systemes, allows for a “single source of truth,” with multiple departments working on the same models and data to cut development
time and avoid wasting resources.
As a software OEM, we understand how vehicle behaviour and performance during a physical (regulatory) test can be simulated effectively and the interpretation of these simulation results. We are always open to participating in standing committees organised by regulatory bodies and sharing our knowledge in this regard.
Q. With EVs thrown into the mix, how will it affect crash test from that of an ICE vehicle?
A. Given the rapid growth of the electric vehicle market, regulations will also evolve accordingly. For example, the Union Ministry of Road Transport and Highways (MoRTH) recently announced additional safety requirements for batteries which will come into effect from October 01, 2022.
Besides structural impact, one also has to consider two aspects which are far more critical when we consider EVs. The first one is the battery itself. Regulators will now have to take into consideration aspects like electrolyte leakage, battery discharge post an event, etc. While we have learned over time to negotiate the dangers associated with flammable fluids for non-electric vehicles and made those vehicles exponentially safer, we now must negotiate the electrical vehicle space similarly.
The second aspect is the overall electrical safety of the vehicle. An electric vehicle contains an electric powertrain with a high voltage bus and a rechargeable energy storage system. Post a crash, automatic disconnect and or isolation of the electric circuit is required. The overall electric protection system should not
be compromised. The electrical safety of the vehicle is of high importance so that passengers and first responders in the case of a crash are not impacted.
Q. While at its nascent stage, how will the crash worthiness simulation contribute to OEMs? How reliable is the data when compared to a tangible crash test?
A. In the case of ICE engines, vehicle manufacturers have been doing crash simulations for several years. As crash regulations have become more stringent, automotive OEMS have increased their virtual exploration of the vehicle structure, materials and restraint systems to improve the crash worthiness of their automobiles. Simulation allows OEMs to understand the impact of a design change – say, thickness change of sheet metal – on the vehicle performance and to virtualy test the vehicle. Vehicle requirements targets – safety, performance, fuel efficiency (or range for eV), and cost – can sometimes be contradictory and OEMs rely on simulation to explore the design options and arrive at an optimal solution.
Dassault Systemes simulation apps. have been used to simulate various types of crash simulations (e.g. frontal impact, side impact, etc.) by automotive OEMs. We have developed
and validated the technology against physical tests, starting from crushing simple metal tubes to crash of full vehicles including restraints and dummies. A combination of advanced material models, robust and efficient solver technology, as well as Industry best practices (Industry Process Experiences or IPEs), allows us to provide predictive crash simulation. We continuously innovate and update our software to include the latest advances in materials, high-performance computing and automotive technology. Our solutions allow for high-fidelity (i.e. detailed) models of full vehicles to be run on a large number of cores either on-premise or on-cloud, resulting in an accurate and predictive crash simulation – so the OEM can be confident that they will pass the physical crash test the first time itself.
Q. With OEMs now focusing on safety as one of the key parameters for a vehicle, explain the role of crash test simulation in today’s age and trend. A. Consumers have become very conscious of safety ratings. In addition, automotive OEMs have become more conscious of their “Brand image” and the need to avoid any costly recalls. All of this means crash worthiness has become more important, overall. Crash worthiness is about designing a path where the structure can deform safely, absorbing the excess energy, while still leaving space for the occupant inside. This needs to be considered right from the initial design of the vehicle itself. During the ideation or conceptual phase, the OEM wants to explore multiple design variations and the need is for a simple model that
can provide results in a short time. To ensure a rapid crash worthiness assessment, Dassault Systemes offers a highly abstracted model and meta data from Machine Learning. The detailed design phase addresses how much the simulation can predict the real behaviour of the vehicle and ensure the physical test is passed the very first time. Our simulation technology in both cases (conceptual as well as detailed design) can immensely benefit and support automotive OEMs.
Q. What are the advantages of crash worthiness simulation over a tangible test along with its application for passenger as well as commercial vehicles?
A. There is always a race to be the first to bring one’s vehicle into the market. To achieve that, development time must be reduced, while still passing the regulations. This is where simulation really makes a difference. A virtual test (i.e. a simulation of the physical regulatory test on the computer) can help assess the vehicle’s performance. Changes can then be incorporated into the design in advance, and the changed configuration tested. Thus, this helps manufacturers discover any failures ahead of time, and be confident that they will pass the regulatory tests the first time itself.
Passing regulations is only one step. This needs to be done while keeping in mind cost-related criteria. There is always a trade-off while designing a vehicle. Some safety features may adversely impact the fuel efficiency or range. Finding the best balance for a car design involves making trade-offs between several factors. With help of our 3DEXPERIENCE platform, these trade-offs can be simulated allowing for various factors (parameters) to be studied to make informed designrelated decisions.
Q. Since there’s no engine under the hood of the vehicle, an EV crash could be different from an ICE
vehicle. Explain how the crash and simulation will affect the occupants considering the impact on the battery as well?
A. EV vehicles are structured differently. For instance, the battery is usually located on the floor of the vehicle, resulting in a lower centre of gravity when compared to an ICE vehicle. Fire hazards need to be considered in the case of both types of vehicles. However, OEMs have years of experience dealing with safety hazards related to ICE vehicles. Manufacturers now need to do the same with battery-powered vehicles.
Currently, auto manufacturers are learning how to deal with these hazards in different geographic environments as well. Alongside this, understanding battery resilience is also important, which is why nail penetration tests should be conducted alongside a variety of other tests like fire, vibration, drop, etc. In addition, aspects like automatic switch off battery post a crash, safe discharge of a battery post an event, electrolyte leakage, and electric safety of the vehicle (when some components could have got exposed due to the crash) are all aspects that OEMs and regulators consider.
Q. What are the challenges faced by Indian OEMs to make products in even shorter time frames?
A. As I mentioned earlier, there is always a rush to be the first in the market. In the case of EVs, manufacturers aim to grab the highest market share but are also working with technology that is new and evolving. With ICE vehicles, OEMs have developed a formal Design Verification Plan (DVP) ( or best practices) over a couple of decades. While many of these DVPs would apply for EVs also, new DVPs will be needed for new components, e.g. an eDrive. In addition, some existing components could be modified for EVs. For example, regenerative braking allows the excess energy during the braking to be used to charge the battery (i.e. kinetic energy converted to chemical). The proportion and importance of software (e.g. Battery monitoring system or BMS) is also increasing, and is a key differentiator in vehicle performance. Lastly, in some cases, OEMs are also working with new vendors (e.g. a battery or motor supplier) and need to develop a trustbased partnership with them for a collaborative vehicle design.
On the other hand, consumers expect a vehicle performance (riding experience) that is similar to an ICE vehicle, while still expecting all safety precautions to be met. Further, the government has also been announcing newer regulations to address some of the aspects unique to EVs.
In summary, OEMs are working with newer vehicle technology, and yet need to meet stringent (and evolving) regulations, meet sophisticated consumer expectations, while meeting reduced project development timelines. This is where Dassault Systemes, with our global exposure from working with EV leaders worldwide, and our industry-proven technology, is assisting Indian OEMs. Besides software, we also provide Industry process experiences as well as services (or outcome-based engagements) to assist our customers to meet these challenges. ACI
OEMs have years of experience dealing with safety hazards related to ICE vehicles. Manufacturers now need to do the same with battery-powered vehicles.
Cummins Inc. continues to optimise its engines. Ashish Bhatia looks at the products worked upon to attain net-zero emissions in a serious push.
Cummins Inc. has been at the forefront of all clean developments in Internal Combustion Engines (ICE) and non-ICE range. Taking the mega exercise beyond Euro6 and Bharat Stage VI emission compliance norms, for instance, the engine manufacturer is invested for the long haul. The mission is to attain net-zero emissions by 2050 through an even cleaner portfolio than what it held on to in the past. According to Jennifer Rumsey, President and newly appointed Chief Executive Officer of the global power leader Cummins Inc., any negative climatic impact can’t be undone and hence must be rectified proactively. “We have to act now. Carbon once emitted into the atmosphere can’t be taken back and we can make the greatest impact by focusing on a dual path approach. Our estimated impact of doing just that is an additional 1.4 gigatonnes of cumulative carbon reduction – the equivalent of removing all trucks from the road for three years,” averred Rumsey. It doesn’t come as a surprise then that through its Destination Zero™ strategy, Cummins is committed to continuing advancements in the ICE technology while building a non-ICE product range.
On the one hand, the efforts are directed to making ICE
cleaner while on the other hand, the company wants to stay true to its DNA. It wants to live up to its reputation of offering further advancements with the new generation of products. The focus is on enhancing efficiency as well as compatibility with cleaner fuels like hydrogen, bio-diesel and Hydrotreated Vegetable Oil (HVO). Beyond this, resources will be allocated for continued innovation on fronts like hydrogen fuel cell and battery technology expected to drive advancements in capability, lower costs and boost the development of the required, supporting infrastructure. The idea is to lower emissions in the present day by finding a suitable match in technology readiness with infrastructure readiness. It is expected to lay the foundation for a mass-scale adoption at an opportune time when there is a market pull for the company’s walk down the technological agnostic path. “We power some of the world’s most demanding and economically vital applications. There is no single
technology that will work for all of our customers. We must advance solutions in a way that secures a sustainable future for the industries that keep the world running. That’s why we have developed a company with the broadest range of ultra-low and zeroemission technologies dedicated to the commercial vehicle industry,” explained Rumsey.
At the recently concluded IAA 2022, Cummins’ showcased a next-generation advanced diesel platform, X10. Deemed as a “practical” route to emissions
reduction and decarbonisation for applications that have a rather difficult path of switching to alternative power solutions. Claimed to be lightweight, the 10-litre compact engine boasts a high power density. It is built to provide a heavy-duty truck capability whilst meeting multiple future emissions regulations. Its Unique Selling Proposition (USP) is that customers can reduce emissions with a product considered to be a familiar, proven technology with backward integration, requiring no change to current operations, service or maintenance set-up. In a testimony to the company
building scalable and modular platforms, the company also showcased the X Series. The 15-litre, fuel agnostic product with a common architecture is claimed to have been optimised for a variety of low- and no-carbon fuels including bio-diesel and HVO, renewable natural gas, and hydrogen. Given that all the engines are derived from the same base, it is said to facilitate a high degree of parts commonality.
Here the hydrogen version of Cummins’ fuel agnostic platform is being looked at as the crucial, initial step to reaching zero emissions for medium and heavy-duty truck manufacturers. The focus is primarily on three key areas for hydrogen: the production of green hydrogen, the management and transportation of hydrogen, and the application of hydrogen in engines and fuel cells. The company displayed the Cummins’ B6.7H hydrogen engine in the driveline of a medium-duty truck. This was to demonstrate the technology’s compatibility with current
truck designs and with comparable performance, range and payload. Here, Hydrogen is required to be compressed into the available space and meet vehicle duty cycle requirements. Through its joint venture with NPROXX, known for high-pressure hydrogen storage for both stationary and mobile applications, the company will support the OEM integration process. The NPROXX hydrogen tanks were fitted to the medium-duty delivery concept vehicle. A 700-bar pressure highcapacity hydrogen storage system, it is claimed to offer a potential operating range of up to 500 kilometres.
The new zero-emissions products reveal included a next-generation fuel cell engine. It is claimed to meet the duty-cycle, performance, and packaging requirements of medium- and heavyduty trucks and buses, and is made available in 135 kW single and 270 kW dual modules. Cummins is known to collaborate with Scania in Europe and Daimler Trucks in North America for the development and integration of these next-generation fuel cells into demonstrator vehicles. According to Anjali Pandey, Vice President, Engine Business and Components Business, Cummins India, “While diesel has
been the dominant fuel source due to its versatility and ease of availability, Hydrogen engines have the potential to become a major milestone on the journey towards a zero-carbon economy because they employ technology that is available today.
On the non-ICE solutions front, the company is striving to meet the net-zero emissions objective with the Lithium Iron Phosphate (LFP) battery. Calling it proven battery chemistry, the development sans the use of rare earth metals like nickel and cobalt is expected to make it both affordable and sustainable. It boasts of faster charging, high power output and a 10 per cent longer life expectancy. As per company claims, the Cummins LFP batteries are designed to meet continuous operations duty cycles and help meet the demands of a lower Total Cost of Ownership (TCO). The company also has a set of NMC batteries. In this range, the BP95E is claimed to have a 30 per cent longer life than previous models. Those looking for a lightweight option can consider the BP30E, designed to cater to optimal utilisation of space. It is claimed to be compact enough to fit into the tightest space claims of most commercial vehicles.
Cumminshydrogen-fuel-cellengine-dual-module
To realise its ambition of a net-zero emissions portfolio by 2050, the company continues to scout for capable partners. With the strategic acquisition of Meritor, Cummins hopes to be able to expand its technical capabilities across the powertrain and related sub-systems. Meritor is said to bring versatility with its powertrain products and EV integration expertise. “We are
in a unique position to do something no one else can do in helping our customers navigate and succeed in the decarbonisation process with a range of technology options optimised to meet the needs of all stakeholders. We will continue to work hand-in-hand with our customers on zero-emissions solutions that further our shared goal of lessening our impact on the planet,” Rumsey concluded. Enroute to 2050, the company will stick to the “credible path” by “advancing” current solutions with reductions in NOx and CO2, a bridge through the phase that involves many solutions competing for segment by segment until the more cost-intensive, battery electric and fuel cell electric turn technologically and financially viable. The focus is also on the gradual decarbonisation of the grid for an overall ‘Well-to-Wheel’ impact. ACI
Ashok Leyland has taken a step for cleaner CEV engines. Prateek Pardeshi looks at the development aimed at gaining an early mover advantage.
The rollout of CEV Stage IV emission norms last year was deemed by many as the tipping point for manufacturers to deliver cleaner engines. Those like Ashok Leyland leveraged the Bharat Stage VI Research & Development (R&D) process and the learnings from the rollout of BSVI models to take an early mover’s advantage in CEVs. Dheeraj Hinduja, Executive Chairman, Ashok Leyland in a company release stated, “Ashok Leyland aims to make India’s CNG engine sector self-reliant, and to be one of the leaders in the ‘Make in India’ narrative.” Ashok Leyland showcased the CNG H-series four-and six-cylinder engine variants for its offhighway and CEV customers and launched it amidst much fanfare. At Excon 2k21, Ashok Leyland also displayed the six-cylinder A-series of diesel engine alongside. The company also displayed its aftermarket solutions including an Exhaust After Treatment System (EATS) at the trade fair. Speaking on improving fuel efficiency with the use of alternative fuels, Dr N Saravanan, Chief Technical Officer, Ashok Leyland Ltd. shared, “With the increasing need for better fuel efficiency and use of alternate fuels, we have a solid pipeline of such technologies.”
In the H-series four-cylinder CEV IV engine range, through three engines, the company will cater to power output requirements ranging from 74-130 hp at upto 2200 rpm. With all the three engines known to be suitable for scaling up to CEV Stage-V emission norms with SCR or DPF, the base engines are a testimony to the CV major being in the game for the long run. Offering the best-in-class power, these engines come with a 500-hours drain interval. Under its H series six-cylinder CEV Stage-IV range, the company will work with four engines on the desired power outputs. H4 airless EATS, DEF tank (airless), and H6 Air assisted EATS were on display too. The H series CNG engine stands out with the turbocharge resulting in a higher torque, ECU-controlled gas leak detection, improved cold-start capability, better fuel economy, durable engine valves and valve seats for CNG operation with better drivability, and claimed transient response. In the case of the A-series six-cylinder CEV Stage-IV engine, the company has the 300 hp A6C430022 and the 360 hp A6C436022 in its portfolio. ACI
In an exclusive upfront interaction, Rajesh R, Vice President of Defence and Power Solution Business, Ashok Leyland Ltd. speaks to Prateek Pardeshi on CEV engines taking a cleaner route.
Q. What is the ideology behind introducing CNG in CVs (haulage and people movers) and CEV segments?
A. For the CV industry, CNG already exists in our portfolio. However, for the CEV segment, I do agree it’s a new concept. We believe the migration will happen much faster than expected.
Q. Could you highlight the differentiators of CNG CEV engines?
A. Ashok Leyland has been a prominent player in the CV segment. The industry has been occupied with diesel-powered engines for a long time. We want to be a pioneer in the CNG CEV segment and leverage the learnings from the CV segment for the CE segment. CNG may not be used in some industrial applications, for example, the portable compressors per se as the latter can work on natural gas. In the terms of efficiency of the platform, CNG has a better TCO and better reliability. Speaking overall, it’d be a win-win for the customer. Looking at the long term prospects of the CNG migration, the customer will still have the option to choose between diesel and CNG.
Q. Is there a void in CNG infrastructure that needs to be addressed for it to succeed?
A. I don’t think there are availability constraints in the case of CNG. More and more mines already have diesel storage, and similarly, CNG filling stations can also be a possibility for them.
Q.Is the new H-series CEV CNG engine the same as the Ecomet CNG engine? How does the emission compliance vary?
A. It is not a one-on-one match as the power and torque of CEV as we know is more as compared to commercial vehicles. But yes, the base platform remains the same. Also, as of today, there are no emission compliance requirements for CEV CNG engines.
Q. How promising are the export opportunities in the CEV segment with this breakthrough?
A. Exports is a different ball game altogether, nevertheless, we would like to look at options where more company’s set shop in India. They also export some of the equipment built in India. As our country is considered a manufacturing hub for most of the companies and the whole equipment is exported to neighbouring markets, we see an opportunity to partner with them on a case-to-case basis. We are also looking at a self-service model that will take care of the requirements in those specific projects.
Q. What are the recent technical developments in the Defence segment?
A. We already have the Stallion which has come a long way from 4x4 to 6x6, and now in the Super Stallion, we have brought in the 12x12 combination. We are now looking at developing smaller platforms to cater to LCV requirements as it’s a large volume game. We don’t want to stop at soft cabs. We also want to develop armoured cabs in line with the light, bulletproof vehicles segment.
Q. Is an electric powertrain for the Dost on the cards?
A. I think it’s already in the pipeline. My team from Switch Mobility is already working on it.
Q. How are you tackling the supplychain bottlenecks?
A. It’s a global shortage, for instance, semiconductors and everyone is facing this issue. But we are trying to build alternates. In effect, it is an alternative chip that we are talking about. We are working closely with the manufacturers on how we can migrate, from being a one complete chip dependency to another design as an alternative. ACI
Daimler Truck Innovation Center India has commenced operations. Ashish Bhatia looks into the largest Daimler Truck AG centre outside Germany, acting on crucial fronts of mobility.
Daimler Truck Innovation Center India (DTIC) in Bengaluru has commenced operations. It is the most significant innovation and development centre outside Germany for Daimler Truck AG as a captive unit with ~1300 skilled engineers. Focused on crucial aspects of mobility like safety technology and innovation, the centre will act as the hub of research, product engineering, innovation and Information Technology (IT). The standalone entity in India, according to Raghavendra Vaidya, Managing Director and Chief Executive Officer, DTICI is vital to the future engineering and design roadmap at the Original Equipment Manufacturer (OEM). Addressing the needs of its domestic and global regions of interest, the centre, he pointed out, is well equipped with@atashishbhatia
state-of-the-art technologies and tools. It will act upon innovative research projects to help align with the crucial fronts of mobility. It comes as a critical development post-Daimler AG spun off its trucks business from MercedesBenz cars. The two-vehicle businesses were quite distinct, with different customers, technologies and financial requirements calling upon the need for a dedicated centre for innovation. According to Vaidya, DTICI is aligned with Daimler Truck, its ambition and its strategy globally, as it entered into a phase of complete disruption in the automotive industry. “The need for alternate powertrains and software-led innovation in the commercial vehicle industry is going to define the future of commercial vehicles,” he opined. Drawing attention to the significant engineering presence in India by way of the erstwhile setup, the decision to split the entire Daimler Group into two companies gave rise to the need for a standalone, deep engineering and
technical expertise. It was thought of as a way to realise ambitions of going towards zero-emission vehicles with either battery or hydrogen-based fuel cells.
DTICI is driven by the goal to lead the industry in software-led innovations. To attain it, Daimler decided to up the ante from being an engineering centre to evolving as an innovation centre, shared Vaidya. With India ticking all boxes, from the perspective of talent, ability and reach that the OEM commands globally, the company zeroed in on Bengaluru for the commissioning of the new centre. Notably, the new centre is the only innovation centre that works across all the regions and brands of Daimler Trucks like North America, Europe, Asia, and China. On the capex outlay for the centre, he explained, that since it’s not manufacturing intensive, the company is instead invested in building capability and people skill sets.
Most of the work done at DTICI is carried out in the digital format. The exceptions include some of the labs where it has in-house, hardwarein-loop testing or component test benches for the ECUs. In the case of product engineering capability, DTICI boasts capabilities across the board for engineering a commercial vehicle. Be it a truck or a bus, from mechanical engineering to electrical, electronics, and engineering. Electronics and software are a huge focus area. In effect, the centre is claimed to cover the entire gamut of engineering capabilities on the product engineering side. On the IT front, the centre covers the entire life cycle of engineering, after sales, and manufacturing. Beyond it, the centre also boasts of extremely deep expertise in advanced analytic and data science. The investments in product engineering extend to software and electronics where Daimler is invested
heavily, globally. Covering trucks for all their hardware and electronics, the capabilities are spread over five domains: software and electronics, HMI which is the head unit that the drivers interact with through connectivity and responsible for big data, and powertrain which controls the engines and makes the vehicle intelligent. Through body controls, it facilitates the interaction between intelligent tractors and trailers. Lastly, it also contributes to active safety and automation, which is the Advanced Driver Assistance System (ADAS) including extremely complex, software implementations like Active Brake Assist (ABA). Notably, of these, the vehicle connectivity domain is entirely owned and managed by India with global responsibility. It breaks away from the pack from the perspective of engineering centres vesting accountability to the headquarters.
With the division of Daimler Trucks and Mercedes-Benz cars division, the
task was cut out. To reposition and reestablish the digital infrastructure. “A lot of the digital infrastructure that we were sharing with the passenger cars is all gone. So we’ll have to set up our own digital infrastructure in engineering and manufacturing, after sales and so on. So the team are extremely involved in those projects, where we reestablish our digital infrastructure,” he explained. With prognostic capabilities, the centre hopes to make the factories more efficient by purely harnessing the power of data and using advanced systems.
At DTICI, the task is cut out; to answer complex questions with realworld solutions. Vaidya admitted to range prediction being a very complex problem, and one that nobody has solved. “All of us are trying to solve it and whoever is also the first will have a competitive advantage. So, there is a very fundamental problem-
solving paradigm we are entering into, because of zero-emission and because of the advances in software and electronics,” he mentioned. Moving on to scientific problems, the centre will overlook battery chemistry or for example how to build hydrogen-based solutions with a 10-year forward outlook. With engineering centres spread across Stuttgart, Germany, and Portland, USA including an engineering team in Tokyo to go along with the comparatively smaller hubs, at DTICI, teams are well aware of allocating resources consciously and avoiding duplication of work. As a crucial part of an integrated engineering team, it is determined to hold its own and build the right manufacturing capabilities without continuous access to the product or the production facilities, like software, electronics, design and so on. DTICI will also partner closely with Indian suppliers for product development and IT collaborations. ACI
In an upfront session, Raghavendra Vaidya, Managing Director and Chief Executive Officer, DTICI speaks to Ashish Bhatia about the innovation centre as the nerve centre for cracking complex problems at Daimler Truck AG, globally.
Q. What compelled the commissioning of an innovation centre outside Germany when Mercedes Benz Research and Development India (MBRDI) was to an extent looking at
trucks? Is it a follow-up to the global separation?
A. If you look at the Daimler Truck, ambition and strategy globally, we’ve entered into a phase of complete
disruption of the automotive industry. More specifically the commercial vehicle industry is led by two things, alternate powertrains and software-led innovation. These are the two things
that are going to define the future of commercial vehicles. And since we already had a significant amount of engineering presence in India by way of the earlier setup, which was an engineering centre for all of the dialogue. When it was decided to split the entire Daimler Group into two companies, it was very clear that we needed deep engineering and technical expertise to achieve these ambitions of going towards zero-emission vehicles with either battery or hydrogen-based fuel cells. To lead the industry in software-led innovations. And since we already had this, we decided to up the ante from being an engineering centre to being an innovation centre. India is a perfect place to do that from the perspective of talent, ability and reach that we have globally. So that is why the centre was set up. The other important fact about this innovation centre is, that this is the only innovation centre that works across all the regions of Daimler Trucks like North America, Europe, Asia, and China as well. All the regions and all the brands. So there is a lot of synergy and cross-pollination of ideas that we can establish between regions and between brands. So those are the over arching reasons why we set up this innovation centre in India and Bengaluru.
Q. Would it be fair to say it has now become the backbone of all Daimler Trucks innovations and developments, globally?
You’re absolutely right! There is a lot of work. There is a lot of disruption going on, there’s a lot of competition that is popping up everywhere which is not conventional competition that we’ve had. So we’ll have to accelerate the process of innovation, and hence a lot of work which needs deep engineering expertise. And what better place than India to bring all of these things together? So it does become a backbone for innovation and technical excellence on the product engineering
side and also to make sure that we drive this innovation across regions and products.
Q. How does it scale up to be the second largest centre? Does it topple the erstwhile second largest centre outside Germany?
A. Yes, it does. It is the second largest engineering centre outside of Germany, and outside of any home location that we have for demo. We have two to three engineering centres across the globe. These are, you know, near shore centres like we have one centre in Turkey, which is close to Germany, where we leverage the proximity of Turkey and then the language skills. We have a
very small centre in Mexico, which is close to North America. But this is the centre that caters to all of the global markets as the only centre covering the entire globe, all the regions and all the branches.
Q. What are the state-of-the-art capabilities that can be expected at the centre?
Vehicle connectivity domain is entirely owned and managed by India, which means the entire India team has the global responsibility of driving this.
A
. Absolutely. If you look at what we do in DTICI, it’s two things. One is product engineering, other is information technology. So when it comes to product engineering, we have capabilities across the spectrum of how we engineer a commercial vehicle, whether it’s a truck or a bus, starting with mechanical engineering, with electrical, electronics, and engineering, and with a huge focus on both electronics and software. So we cover the entire gamut of engineering capabilities on the product engineering side. And on the IT side, we covered the entire gamut like engineering, after sales, and manufacturing. And then we have extremely deep expertise in advanced analytic and data science. So the way I would put it is on the product engineering side, we go from sheet metal to software. And on the IT side, we’ve covered most of the domains. We also have very deep expertise in analytic and data science.
Q. If you could share the CapEx earmarked for the centre?
A. This is an engineering centre and all of our capabilities here are digital. So we don’t have test benches; we don’t have a manufacturing facility; we don’t have a prototype shop, which is very physical. So the investment here is really in building capability and people and in skill sets. Most of the work that we do here is digital, except for some of the labs where we have the hardware in loop labs or component test benches for the ECUs. Outside of that, it’s mostly digital. So our biggest investment and our biggest asset are our engineers.
When it was decided to split the entire Daimler Group into two companies, it was very clear that we needed deep engineering and technical expertise
Q. Any exciting projects where work is underway at the centre?
A. On the product engineering side, let me focus on software and electronics and mission vehicles because these are the two areas where we are investing heavily, globally. So under hardware and electronics, all the electronics and software that goes into the truck and the bus, and makes the commercial vehicle intelligent. So we have five domains across software and electronics: HMI which is the head unit that the drivers interact with through connectivity, which is taking all the vehicle data and sending it to the cloud in real-time. We have the powertrain which is controlling the engines and making the vehicle intelligent. Through body controls, we make the facilities more intelligent, like, how the tractor and trailer interact with each other. And fifth, and the most important is active safety and automation, which is the Advanced Driver Assistance System (ADAS). Out of these, the vehicle
connectivity domain is entirely owned and managed by India, which means the entire India team has the global responsibility of driving this. This is huge. I would say a big shift from the regular engineering centres that you find everywhere where engineering work happens but the accountability is still with the headquarters. We have deep expertise in software development, for example, autonomous driving or ADAS. These are extremely complex, software implementations like the brake can brake by itself, called Active Brake Assist (ABA). It can identify a pedestrian or a bicycle that is going on the side because these trucks are really big and the driver cannot see such blind spots. So there are more sensors and cameras. So in the rest of the four domains, we have deep software development expertise. And there are lots of exciting projects going on in each one of them. So that’s on the vehicle software side.
On the IT side as you can imagine, when a company gets split, we’ll have
to reposition and reestablish the digital infrastructure. A lot of the digital infrastructure that we were sharing with the passenger cars is all gone. So we’ll have to set up our own digital infrastructure in engineering and manufacturing, after sales and so on. So the team are extremely involved in those projects, where we reestablish our digital infrastructure. The second is the advanced analytic and data science that I spoke about, where we are trying to harness the power of data, using machine learning algorithms where we can predict part failures, the part pricing or we can make the factories more efficient by purely harnessing the power of data and using advanced systems.
Q. How will you leverage Karnataka’s manpower and offer upskilling opportunities in line with the Daimler global benchmarks?
A. I don’t think it is any longer a secret that Bengaluru is the melting pot of digital skill sets. Most of the largest
engineering centres and digital centres are in Bengaluru. So no question about that. See, what do engineers look forward to when they come to work for Daimler? What they look forward to is working on some of the most sophisticated commercial vehicles. If you look at our trucks and buses in North America and Europe, these are some of the most sophisticated machines with extremely complex engineering, whether it is the powertrain whether it is transmission, whether it is the braking systems or the software and electronics. So they come to work for us to up their skill where they’re working on the best products. This is something that they won’t get anywhere else. Now, that also poses a challenge for us, because this is very complex engineering involved. And Daimler has been around for more than 20 years. We have many complex processes, which have been developed over decades. So we have a two-pronged approach, where we bring in engineers who already have the technical skills like software or electronics, along with a background in
automotive engineering. So they know their trade craft, and they know how to apply it in automotive engineering. We recruit engineers who come with their trade craft, whether it is computer science, electrical or electronics, or who have prior work experience in the automotive industry. So they have technical skills, but also the domain skill of how to apply that technology in the automotive industry. We recruit them, and that’s kind of getting there halfway. There is also a Daimler way of doing engineering. So that’s what we scale them up on. Like, how do we do active safety at Daimler? How do we do software at Daimler, and then once we upskill them, then they become part of the team. We also have a campus strategy where we bring very young engineers and interns as Graduate Apprentice Trainees and then we train them on the specific skill sets. And then most of them, like really smart kids, get trained on the job. And then over years, they kind of get their trade craft finetuned with an ability to understand the automotive industry. We conduct lateral hiring, and we also do campus hiring.
And a combination of them gives us the right skill sets to deliver the solutions.
Q. Which global markets and product mixes will it serve? What are the research, product engineering and IT capabilities that it will bring forth in a seemingly well-established, and proven ecosystem?
A. You are right, it is a seemingly well-defined and well-understood ecosystem, but there is a lot of disruption that’s going on. For example, all the OEMs of commercial vehicles or all other automotive of us have to get to zero emissions. We’ll have to get rid of combustion engines and go to battery electric vehicles, and in commercial vehicles, because of the range requirements, battery electric may not be good enough. So there are a lot of very fundamental engineering problems that need to be solved. Let me give you an example. So we have battery electric trucks, right, which are in production, plying on the roads in Europe and the US. One of the biggest and the most complicated problems we’re trying to solve is range prediction.
How does the driver know when he or she is going to run out of power? So, the range prediction is a very complex problem, nobody has solved it yet and all of us are trying to solve it and whoever is also the first will have a competitive advantage. So, there is a very fundamental problem-solving paradigm we are entering into, because of zero-emission and because of the advances in software and electronics. So these problems are not solved, and they are very complex engineering problems.
There are also scientific problems with battery chemistry or say how to build hydrogen. How do you know, distribute hydrogen, how do you make sure that the compressed hydrogen stays in a certain state? So, we move from where we are to where we will be in eight to 10 years. There are extremely fundamental scientific and engineering problems that need to be solved, right and all the OEMs are in the race of solving them. Whoever solves them and brings them to the market will have a competitive advantage.
Q. Will this have a direct bearing on the export ambitions from the Oragadam plant?
A. We do work with Mercedes Benz as one of our brands. And we do work on some of the engineering problems for foreign brands, whether it is on creating the next derivative or whether it is complying with BSVI or whether it is on connectivity solutions. The challenge here is that the products in each region are very different. What sells in India is very different from what we sell in Europe, what we sell in North America, or what we sell in Indonesia, for example. And our task or our ambition is to make this DTICI the melting pot of all the engineering problems. And we take one solution from one region and one product and try to adapt it to the other product.
Q. Will it be directly accountable for
on road performances beyond lab simulated results?
A. So let me answer that question in two parts. One is we have already taken accountability for let’s say, vehicle connectivity. And this is a combination of hardware and software, the hardware is the ECU or the CTP which is a Common Telematics Platform inside the truck, which is continuously collecting data from the truck and streaming it to the cloud. On the cloud, we are running a
lot of algorithms and understanding how the truck is behaving. We already have full accountability for that. On the aspect of hardware where one needs to build test benches. The question is are we going to build proto shops? Where we can build a prototype of the trucks? The answer is no, we will not do it. We will stay digital. We will stay focused on solving the problems through digital technologies. We do have limited, hardware capabilities, whether it is hardware in a loop or whether it is test benches for our electronic components, not the mechanic.
Q. Elaborate on the synergies that will be leveraged between the new centre and the existing global innovation centres. Any technology transfers and collaborations that you could speak of?
A. We have engineering centres, in our home locations, like there is an engineering team in Stuttgart, Germany. There is an Indian team in Portland, USA. There is an engineering team in Tokyo. And then there are little hubs. So we work as one team. We don’t duplicate stuff. We don’t solve the same problem in two places. But we try and work as an integrated engineering team, where we harness the capability of that location. For example, Turkey is right next to Germany, they have huge language skills. And there are very large manufacturing plants in Turkey, both for trucks and buses. So we use that as a backbone to build the right manufacturing capabilities. Similarly, Mexico and the other centres. At DTICI, we’re not away from most of the home locations. When we build capabilities here, which are digital, which can be successfully owned and executed, not having to have continuous access to the product or the production facilities, like software, electronics, design and so on. It is how we have structured across the globe. ACI
So, the range prediction is a very complex problem, nobody has solved it yet and all of us are trying to solve it and whoever is also the first will have a competitive advantage.
What sells in India is very different from what we sell in Europe, what we sell in North America, or what we sell in Indonesia, for example. And our task or our ambition is to make this DTICI the melting pot of all the engineering problems.
The industry is tackling supply chain bottlenecks with tools at its disposal. Deepti Thore looks at the advancements leading to improved decision making.
Indian Automotive supply chains have become very complex today. The need is to mitigate risks and reform multi-tier visibility to address bottlenecks with alternative procurement strategies. It is crucial to recalibrate supplier links and establish a committed crisis response capability. This can be achieved using specialised tools and established supply chain management techniques that make it possible to reduce errors and costs. The efforts to optimise the entire supply chain are dependent on the software layer dealing with logistics requirements like shipping status alerts and updates, order processing, lean inventory, warehouse management, specialised freight handling, bid and spend, supplier management, demand forecasting, analytics and reports, collaboration portals, security features, transportation and logistics, and compliance and auditing.
In an end-to-end coverage, from departure to destination, the automotive supply chain solutions are designed to give utmost control, reliability and transparency. Emerging and maturing supply chain technology offers a major competitive advantage to the stakeholders of the industry. By 2026, more than 75 per cent of commercial supply chain management application vendors will deliver embedded Advanced Analytics (AA), Artificial Intelligence (AI) and data science. By 2026, 25
per cent of Supply Chain Execution (SCE) vendors will have rewritten their core application to a microservices architecture, but only five per cent of supply chain organisations will have adapted to true composability. Through 2025, 25 per cent of supply chain decisions will be made across intelligent edge ecosystems. Through 2026, 80 per cent of companies will suffer a significant value loss owing to failure in merging digital supply chain twin and control tower initiatives.
As per a study by V.Asokan and M.Shilpa, Research Scholar and Associate Professor respectively at the Department of Industrial Engineering & Management, Ramaiah Institute of Technology, Bengaluru, titled ‘Applications of Information Technology Tools For Supply Chain Management In Automotive Sector’, change has been brought in for an accelerated evolution. The enterprises’ adoption of efficient and effective policies, technologies, practices, outsourcing, globalisation, time to market and customisation are a testimony. Frequently used IT tools such as EDI, ERP, bar codes, inventory management, transportation management, and warehouse management systems have been reviewed and adopted.
Cloud-based tech solutions are also helping manufacturers manage a new suppliers claiming greater agility and resilience. The cloud’s main objective is to ensure everything in your supply chain works in harmony. This tool offers multiple entities access to data which results in decreased costs and increases supply chain velocity while introducing a layer of data security. There are companies like ‘Fleetx’ offering software solutions for fleet management or transport management for clients including the likes of Delhivery, Maersk, MRF, LetsTransport, Suzuki among others. The software
helps in digitisation of end-to-end logistics and fleet operations to improve efficiency, safety and reduce cost. Oracle’s NetSuite is cloud-based software used for Supply Chain Management. It enables companies to oversee the flow of goods from suppliers through manufacturing and into customers’ hands. It also keeps production running smoothly by ensuring all materials are available and in the correct locations, and accurately schedules machinery and labor resources. Spec India also has been delivering robust and comprehensive Supply Chain Software Solutions & Logistics Solutions which helps the
automotive industry overcome many supply chain challenges.
As per a McKinsey report authored by Knut Alicke, Cengiz Bayazit, Tim Beckhoff, Tacy Foster and Mihir Mysore, the supply chain upheavals show little sign of abating. Companies can address them by reconsidering outdated, short-term strategies and beginning the hard work of building structural resilience. This could be achieved in three stages: Firefighting, Integrating and streamlining operations, and Achieving structural resilience. In
terms of firefighting, one potential response to supply chain problems is to focus on short-term or day-today actions. These tactics can help to some degree, particularly for
identifying previously overlooked supply chain gaps. For integrating and streamlining operations, the need is to create a nerve centre. Simulating and planning for extreme disruptions,
and re-evaluating Just-In-Time(JIT) strategies; achieving structural resilience through ‘digital twin’ of the most critical parts; creating and testing ‘what if’ scenarios to identify vulnerabilities and increase data sharing with suppliers is also crucial.
The future of the automotive supply chain will be influenced by technology with machine learning and artificial intelligence-based systems poised to deliver the greatest business impact. It will not only improve transparency or solve problems quickly but also make more accurate predictions. The need of the hour is to build a digital roadmap to manage strategic, dynamic, and flexible partnerships with private and public stakeholders to improve supply chain visibility and decision-making capabilities in a more responsive and customer centric approach with new opportunities left to be tapped. ACI
India is the world’s second-largest producer of crude steel, with steel serving as an essential raw material for the automotive industry. Prateek Pardeshi assesses the scope of a gradual softening of prices and revival in favour of the automotive industry.
ndia surpassed Japan to become the second-largest producer of steel in the world in 2019. With an overall production of 118.134 Million Tonnes (MT), we are closing upon China far ahead as the leading crude steel production had a total production of 1032.8 MT in comparison. According to the Annual report 2021-22 published by the Ministry of Steel, the nation’s total finished steel consumption for the fiscal year 2021–22 was 111.8 MT, and that figure is expected to increase to about 160 MT by 2024–25; an estimated 250 MT by 2030–31. The Secretary of the Ministry of Steel, Pradip Kumar Tripathi drew attention to India attaining a milestone of 109 MT Steel production in 2019-20, before the pandemic set in. “We hope to increase the production of speciality steel from 18MT to 42 MT in the next 5 years through PLI Scheme. Our aim is to improve the cost competitiveness of the steel sector,” he said. To promote the steel industry interest, India has, in the past, leveraged forums like the Global Stainless Steel Expo held in Mumbai at Jio World Centre, in Mumbai. As of current, the automotive industry is hoping for prices to moderate in the absence of which operating margins are under pressure and any hike out will pass on the burden to the end customer. In this case, the tier suppliers are under pressure from Original Equipment Manufacturers (OEMs) to keep prices under check.
The automotive industry
accounts for nearly eight to nine per cent of the overall steel volumes. To cater to this side of the demand, the Ministry of Steel has held numerous discussions with the Engineering Export Promotion Council of India (EEPC), various automobile manufacturers, and Indian steel companies to better understand the possibility of competitively priced domestic manufacturing and procurement of auto-grade steel in India. Rasika Chaube, Additional Steel Secretary back then launched a vision document 2047. She is known to have directed stakeholders of the industry to work in the direction of turning a net. She committed to the Ministry’s resolve in helping to increase the consumption of steel and stainless steel. It is known that to produce automotive grade steel, transfer of technology for production
(In Million Tonne)
and other special steels could be facilitated by JVs with global leaders. It is expected of the steel industry that the domestic demand for automotivegrade steel would be met domestically. This extends to electric steel, special steel and alloys. Here the Production Linked Incentive (PLI) scheme for the production of steel with an Rs.6233 crore outlay with incentive slabs from four per cent to 19 per cent is expected to have a direct bearing on the consumers for automotive bodies and components. As per the Rashtriya Ispat Nigam Ltd. (RINL), the need of the hour is to improve the supply of niche products through the network of OEMs, tier2 and tier3 vendors. Research and Development (R&D) efforts must be aimed at the indigenous development of austempered ductile iron technology.
Item 2017 2018 2019 2020 2021
Production 101.455 109.25 111.344 100.256 118.134
Finished Steel
Production 93.737 100.574 104.062 92.231 111.858
Consumption 88.679 96.737 102.622 89.331 106.134
Import 7.828 7.295 7.44 4.463 5.001
Export 10.871 6.692 8.205 10.15 12.799
Source: JPC; *Provisional, January-December, 2021
As per the Ministry of Steel, Annual Report 2021-22, Crude steel production stands at 118.134 MT slightly higher than 2020 which was around 100.256 MT. Finished Steel production for 2021 stands at 111.858 MT, while in 2020 it was 92.231 MT. While the production is on the boom, consumption in 2021 was 106.134 MT while 2020 accounted for 89.331 MT. The import in 2021 was five MT slightly higher than the previous year 2020 accounting for 4.4 MT. Lastly, the export in 2021 stood around 12.7 MT and in 2020 it was 10.1 MT. Earlier in October 2021, a Memorandum of Understanding (MoU) was signed between the Ministry of Steel and the Russian Federation for cooperation in the field of coking coal, which is used in steel production. The MoU will benefit the Indian steel sector by diversifying coking coal sources, which may result in lower input costs for steel players due to long-term commitments to supply high-quality coking coal to India (up to 40 MT by 2035).
Promoting capacity expansion and working on meeting the increased steel consumption by the automotive industry comes with its own set of challenges. The answer lies in a greater degree of collaboration among ministries, according to Rasika Chaube, Additional Secretary, Ministry of Steel, Government of India. “Interacting with various ministries allows us to better understand their requirements. Similarly, we request our stakeholders to produce similar metals that will meet their needs,” she mentioned. Several ministries, including the Ministry of Oil and Natural Gas, and the Ministry of Rural Development have collaborated thus far. To aid the progress, the Ministry of Road Transport and Highways and the Ministry of Heavy Industry are expected to join hands too. Recently, Union Minister, Nitin Gadkari committed to speaking to the Ministry of Steel at the 62nd ACMA Annual Session, in New Delhi. Among the top concerns was the need to look at taxation on the input material, work on ways to offset the jump in prices and extending GST benefit on the scrappage of vehicles.
Chaube drew attention to only 60 per cent utilisation of capacity at steel manufacturers. “This means we have a huge scope of dealing with higher demand,she explained. She admitted to steel contributing to carbon neutrality
in comparison to the ferroalloy industry among other producers known to be carbon intensive in their value chain. However, the industry is gearing up for enhancements like green steel and green stainless steel to lower its carbon footprint. Here, the use of renewable energy sources with a potential of 40 per cent carbon emissions reduction was highlighted. The Ministry of Renewable Energy under the aegis of Prime Minister Narendra Modi is planning to meet a projected 500 gigawatts demand. Producers like JSW steel are known to have recently collaborated with German
firm SMS group to reduce its carbon footprint with a USD 100 bn outlay that others must follow suit.
The demand for stainless steel is expected to grow by 19.5-21 per cent to 3.7-3.9 MT in fiscal 2022, supported by a low base, a stable macroeconomic environment, and normalised government spending, according to the Vision document 2047. According to industrialist Abhyuday Jindal Managing Director at Jindal Stainless, the Ministry has taken a number of steps to advance the steel industry, including the release of the National Steel Policy 2017. Then, the focus is on aspects like scrap recycling, quality control, and local production to meet the demand. orders, and so on. He stated that, that the industry anticipates the steel ministry’s continued assistance in achieving the stainless-steel vision of 2047. The stainless steel industry in India has the sufficient production capacity, the stakeholders assure. According to K K Pahuja, President of Indian Stainless Steel Development Association (ISSDA) , the stainless steel industry is dedicated to contributing to nationbuilding by providing sustainable solutions across the board. ACI
Advertising in traditional media continues to enjoy high trust amongst consumers, with 86%* expressing confidence in print making it the most trusted medium.