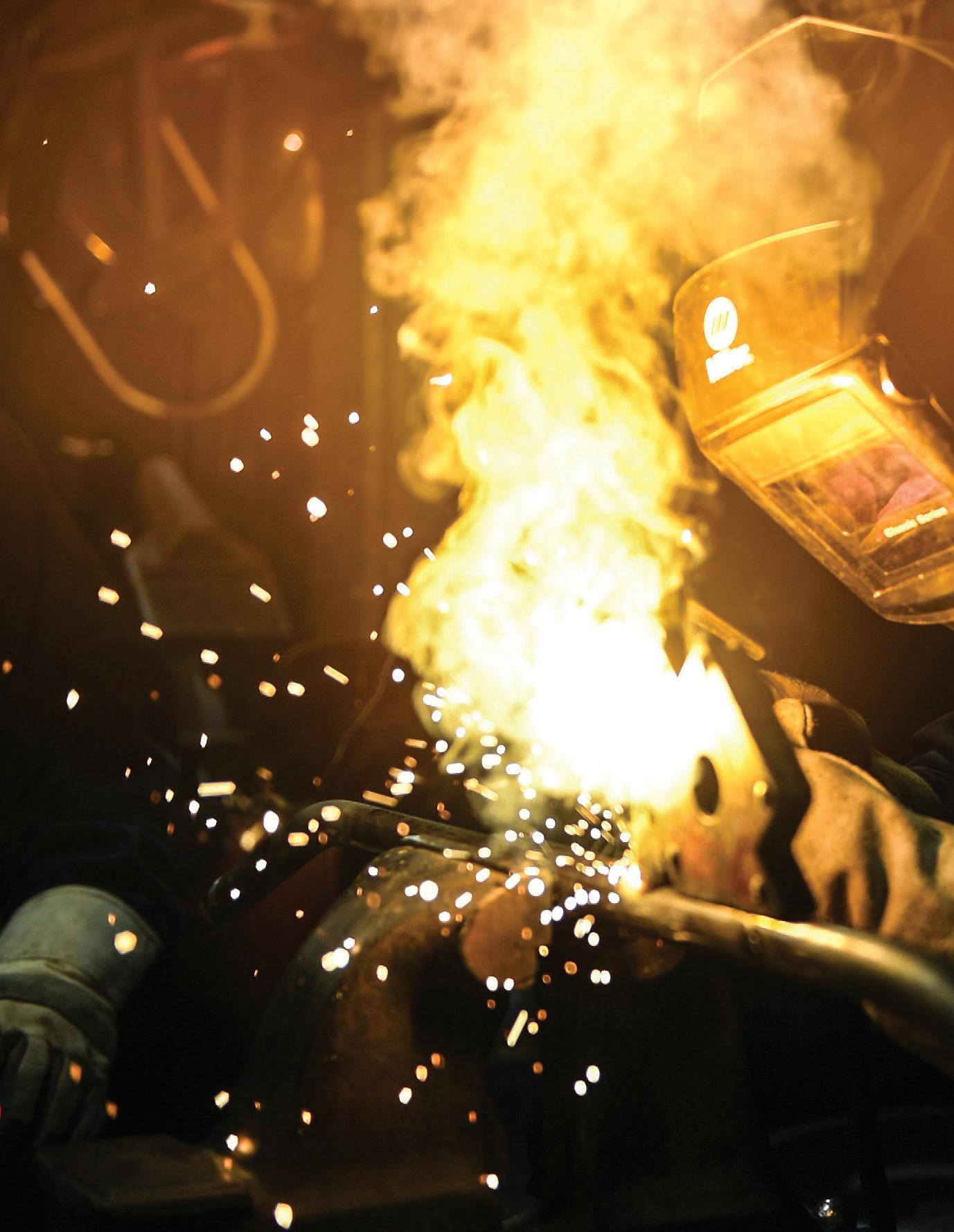
4 minute read
Assault Craft Unit FIVE's on-site LCAC Weld School
Story by Expeditionary Strike Group THREE Public Affairs Photo by Mass Communication Specialist 3rd Class Justin Whitley
CAMP PENDLETON, Calif. (NNS) -- In a predominantly steel trade, Hull Maintenance Technicians (HT) assigned to Assault Craft Unit FIVE (ACU-5) are in for quite a surprise when faced with the challenge of welding on the Landing Craft Air Cushion (LCAC) all-aluminum hull. Fortunately, ACU-5 is home to a specialized seven-week weld school centered on the unique intricacies of aluminum welding that prepares these Sailors for such a challenge.
Advertisement
“Aluminum differs from steel in many ways even though the basic principles are the same,” said Mr. Kirt Martin, ACU-5 weld school instructor. “Thermal expansion of aluminum is approximately twice that of steel. Hot cracking – as we call it – can occur as the weld solidifies with aluminum if not done carefully,” Martin adds. Martin, a contractor with MS Corp and professional welder of 27 years continues: “The Gas Tungsten Arc Welding process used for aluminum takes a little more dexterity than other welding processes and requires a bit of a faster pace.”
With the LCAC capable of speeds of 50 knots the ‘Swift Intruders’ of ACU-5 are no strangers to a fast pace. Precisely placing the 110-ton hovercraft gently inside the belly of amphibious assault ship underway at 12 knots with a 60-ton payload on deck takes lots of skill and a little bit of luck. Sometimes rough seas result in minor fender benders while attempting this
highly technical aspect of the mission. In the war of LCAC aluminum versus ship’s steel, steel wins every time. This is where ACU-5s HTs come in.
With six courses taught on-site and a throughput of 36 students each year, there is no shortage of LCAC metal experts ready to answer that call. After 12 hours of classroom lectures and 67 hours of arc-time per student, LCAC hull maintenance teams come together and demonstrate the skills they learned in ACU-5s weld course, ultimately returning almost any hull component onboard the landing craft to like new condition in accordance with Military Standard 248 and the LCAC Welding and Inspection manual. The training drastically enhances occupational standards for HTs and takes a methodical approach to specialized training, negating a ‘learn as you go’ approach, which many other on-the-job training scenarios have to offer.
“Our weld school teaches the student how to weld on aluminum and stainless steel, which is specific to the LCAC community. The students get a lot of one-on-
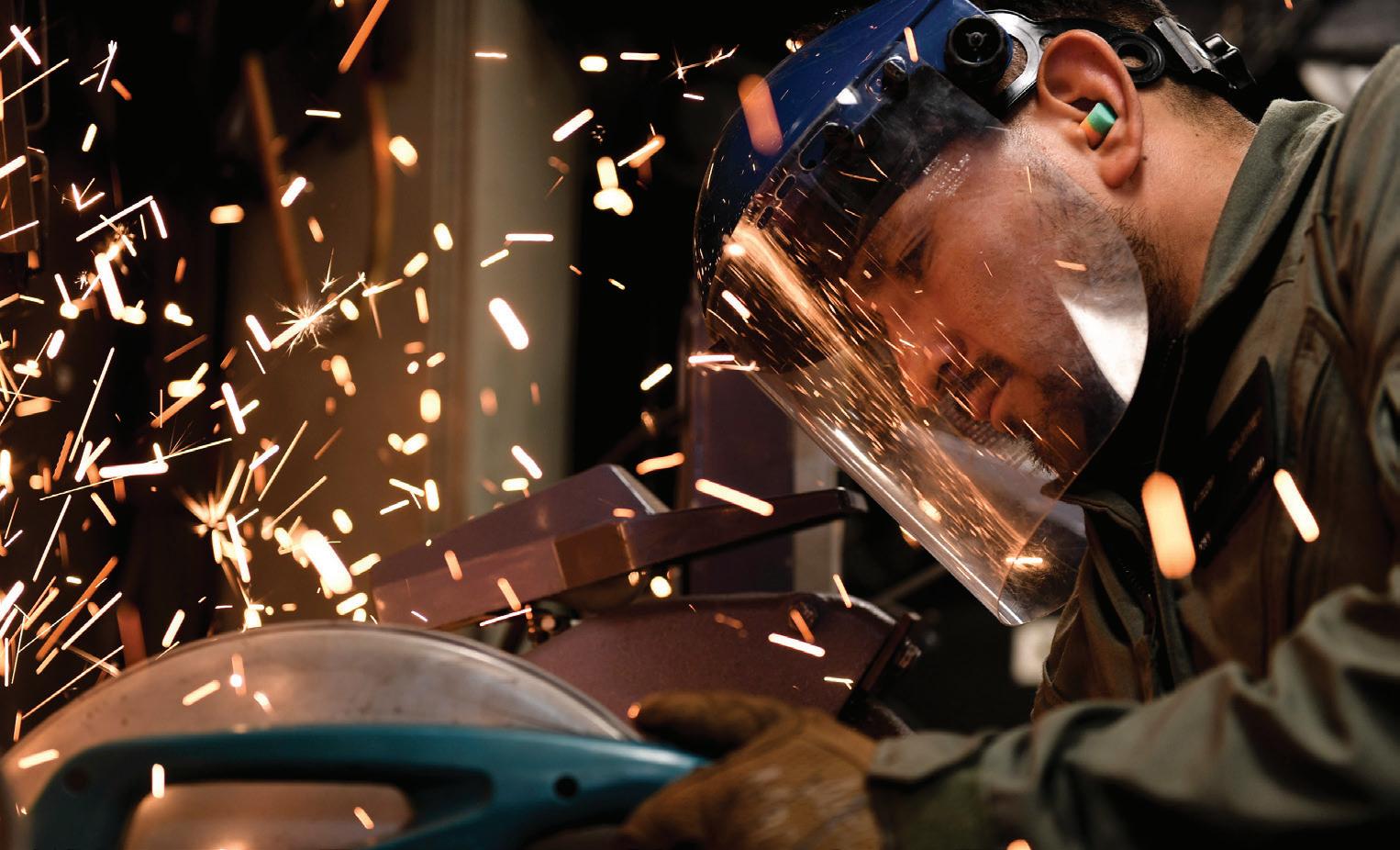
one interaction with the instructor where they learn structural design, repairs, and fit-up, as well as how to break-down, clean and troubleshoot a welding machine,” noted Master Chief Hull Maintenance Technician Art Ponce, ACU-5 maintenance department leading chief petty officer.
Although predominantly HTs with 50 percent of enrollees coming directly from HT “A” School, weld school students come from various backgrounds and possess different experience levels, with Marines counted among those matriculated in the course in the past. The course has even certified service members with the Marines’ Wounded Warrior Battalion. While the training’s focus is LCAC hull repairs, seats are also available to fleet HTs depending on quota availability.
A recent addition to the weld course is a full-sized LCAC section, which adds a unique sense of realism to the students’ experience. The mock-up, a donation from the LCAC Program Office, comes from a decommissioned craft and serves as a place for students

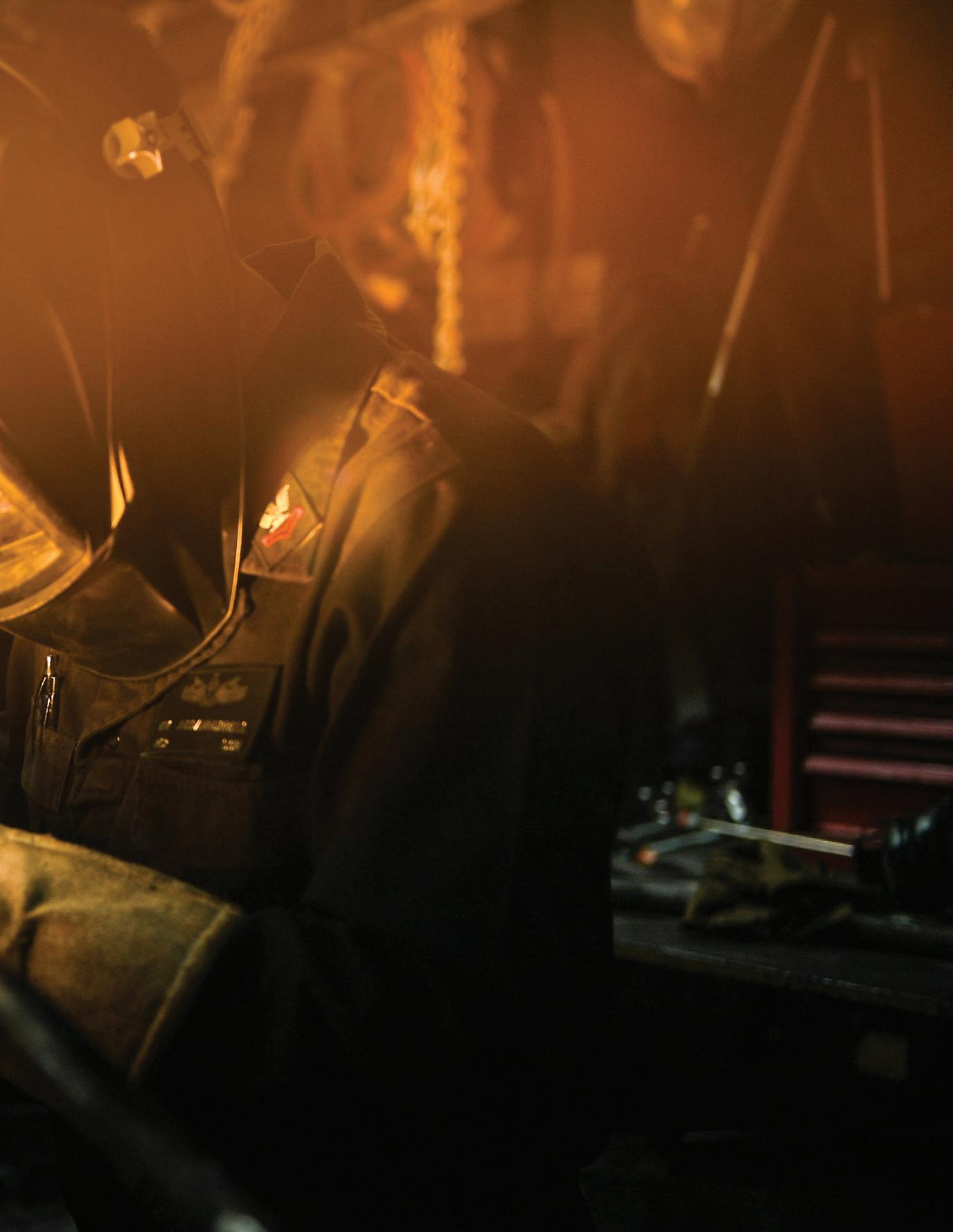
to practice their skills in a controlled environment and make mistakes without sacrificing re-work or equipment costs on an otherwise fully commissioned LCAC. This approach drastically reduces waste and provides highly trained HTs to the LCAC fleet who are ready to produce excellent results from the start.
“Welding on a life-sized piece of LCAC introduces the Sailor to the real world interaction they deal with out in the field,” Ponce continued.
While most graduates remain at ACU-5 upon certification, some go on to exercise their skills at Naval Beach Unit (NBU) 7 in Sasebo, Japan, greatly enhancing LCAC hull repair capabilities for forward-deployed LCAC in the U.S. 7th Fleet area of responsibility.
“ACU-5 offers a unique opportunity where we take a Sailor used to welding on a different medium and not only introduce them to the concept of welding aluminum, but train them to a high degree of confidence in their skillset,” explained Capt. Chris Nelson, commanding officer, ACU-5. “There is a tremendous return on investment when you consider the positive effect our training has on the quality of the end product.”
When asked what the best part of his job is, “The ability to pass on the experience passed on to me, and the knowledge and experience I have gained from working on the craft for so many years,” said Martin. *