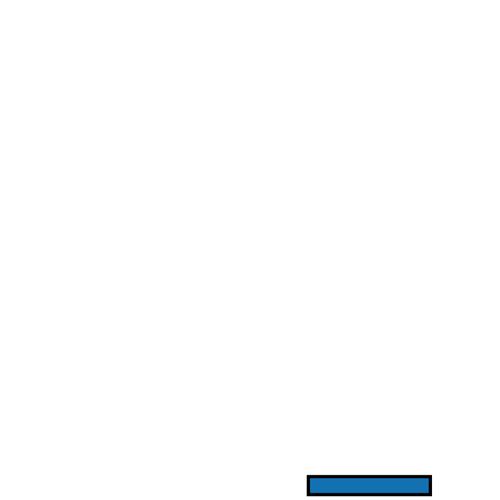
7 minute read
It’s All in the Family
recessions quicker because different facets of the economy are affected at different times in the recession,” JP said. “I started this business in the middle of a recession and didn’t even realize it.”
In addition to diversification and customization of services, the values held by JP and Mark have stayed consistent - family, community, employee satisfaction and customer service. Of all the lessons learned to pass along to the next generation of Herman Manufacturing, perhaps the most important are the unchanging values that have made their business stand the test of time, the first of which is family.
Advertisement
“It’s important to me to have this business be in Wells and stay in Wells and to give employment to people and my family if they want it,” JP said.
Of the nearly 50 people JP and Mark employ at Herman Manufacturing, many are from Wells, and others are drawn from the surrounding communities of Blue Earth, Austin, and Albert Lea. As a family-owned and family-run business, it also employs many members of the extended Herman family.
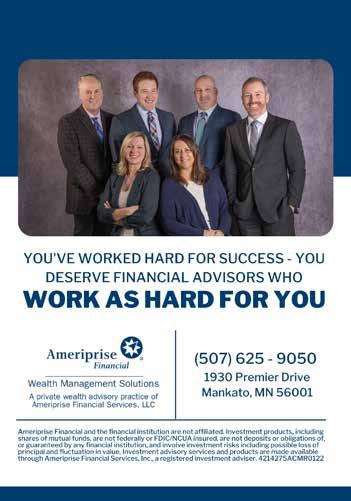
“If I can find work for my family, I will,” JP said.
Currently, there are ten family members in the business. Each family member has a role to play in the business, although neither JP nor Mark wants to put a label on those roles.
“I don’t like titles,” JP said. “Just do your job.”
Learning the business from the ground up is something of a tradition as well.
“We have several generations of family working in the business,” Mark said. “This ensures that the company will continue into the future, when according to JP, it will still be family-run.
For the duration of the business, each generation of the family has trained the next. For example, Helen Herman, JP and Mark’s mother, trained JP’s wife, Cindy, as a bookkeeper. Now Cindy is training her grandson’s partner to do the same.
JP has realized in recent years that he needs to take all the business knowledge he’s stored away in his mind and convert it into accessible information and training for the family members that will carry on his legacy. According to JP, when his grandson Zack Kuhns saw him up in a cherry picker in one of the shops, he hollered: “Grandpa, be careful. I have an awful lot I have to learn from you yet!”
While the business has grown significantly over the last 44 years, it remains something of a mystery to the region.
“We don’t make anything with our name on it. Everything we make is for somebody else,” JP said.
Although residents of the region may not fully understand what Herman Manufacturing does in its machining and welding shops, everyone in the Wells area knows that the two brothers who run the business are equally passionate about their commitment to the community.
Born and raised in Wells, JP and Mark came back after a brief leave to the Twin Cities to run Herman Manufacturing and raise their families.
“We want to be an important business in our community by providing jobs for the area residents,” Mark said.
The brothers are also active in the community. Mark has spent many years on the United South Central School Athletic Boosters Board, was on the St. Casimir’s Catholic School Board and coached several sports teams through the years. In addition to 23 years as a volunteer ambulance driver, JP has represented his community on the City Council and the Economic Development Commission. However, he noted with amusement that some might claim he’s bad for economic development due to his tendency to buy up any available business property.
Because family is important to JP and Mark, they provide flexibility to their employees so they can also dedicate time to their families and achieve work-life balance. This policy has proven to be a key component of employee satisfaction.
“We have always been a family-oriented company,” Mark said.
Employees at Herman Manufacturing enjoy flexible start and stop times for their shifts with the expectation that they will put in the required hours for their jobs. This flexible scheduling allows employees to create a schedule that works best for them and their families, with flexibility for school pick-ups, appointments and other essential activities. It also works out well for the business because when some employees start early while others finish late, it essentially creates a shift and a half of production hours.
“I want the employees to live their job around their life,” JP said. This includes employees being able to attend events and appointments for their families during work hours.
At Herman Manufacturing, they are conscious of the comfort and health of their employees. Each of the seven buildings is air-conditioned, and air quality is maintained with special masks, testing and machines that clean the air around the welding machines creating a healthy work environment.

Customer service has been another steadfast commitment for the Herman Manufacturing team. It’s easy to see why they have retained customers for over 40 years. JP, Mark, and Zack divide their customer base between the three of them in order to cultivate quality one-on-one relationships with their customers.
“It is a small business type attitude,” JP said. “Between the three of us, we make it flow altogether, but as far as from the outside in, customers are dealing with the same guy all the time, and they know if they need something, we can help them.”
They also always give their customers a fair price, are upfront and honest with them, don’t require a lead time and, perhaps most importantly, strive to be a resource for their customers.
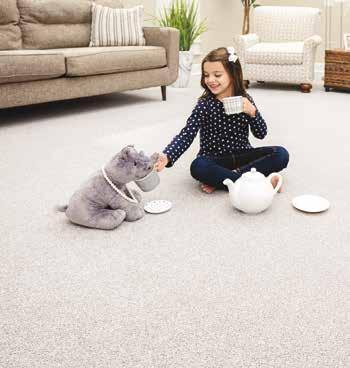
“If you don’t have a source or know a source, send it to JP, and he will do it or tell you who can,” said Cindy. “JP bends over backwards to keep his customers happy.”
Mark agrees: “We go above the expectations that our customers have for us.”
Being a resource for customers also means being a good business partner to other businesses in the machining and welding industry. Collaborating instead of competing is key to Herman Manufacturing’s success.
“We have strived through the years to not have anyone be our competitor,” JP said.
“They do work for us, and we do work for them,” Cindy said. “If there is something that we can’t do, we’ll send it on to somebody that does work for us or that we do work for.”
One good example is the partnership Herman Manufacturing shares with Winnebago Manufacturing.
“We send parts back and forth all the time,” JP said. “We do stuff that they don’t do, and they do stuff that we don’t do. So I am a customer to them, and I am also a supplier to them.”
These types of partnerships allow the company to be more versatile. It can offer so much more to its customers because of the many partnerships it has developed, bidding on work that is partly done in-house and partly outsourced. As a result, it makes the company a one-stop shop for its customers.
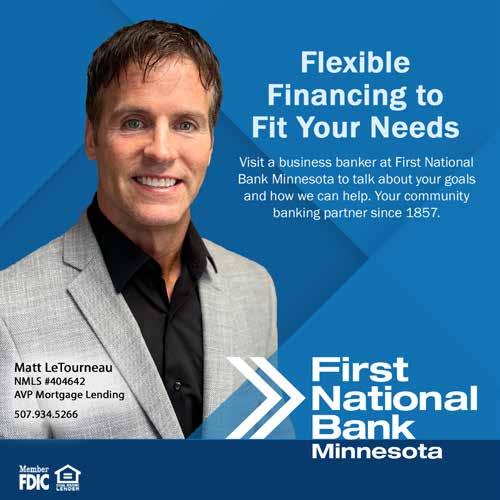
“The more versatile you can become, the more work you can do,” JP said. That also includes outsourcing services such as powder coating or painting.
JP believes Herman Manufacturing’s strength lies in its ability to do so many different things for its customers, which is undoubtedly true. Still, it could be argued that its greatest strength is its commitment to long-held principles in a world that is changing fast. The values of family, community, employee satisfaction and customer service are modeled from the top down. For years to come, these values will continue to allow this humble business to fly under the radar as it provides quality service and an employee-friendly work environment to southern Minnesota.
5 YEARS AGO
JAN/FEB 2018
Our 2018 Business Person of the Year was Dennis Terrell, owner of Re/Max Dynamic Agents (Mankato). We learned that nurturing and lifting up those around him were what Dennis felt were the keys to his success. Other businesspeople honored this issue were David Milbrath of Prairie Plans Asset Management (Springfield), and the Redig family of Nordaas American Homes (Minnesota Lake).
10 YEARS AGO
JAN/FEB 2013
In 2013, Wayne Kahler of Kahler Automation (Fairmont) won the title of Connect Business Magazine Business Person of the Year. Runners-up were Paul Wilke, manager of the River Hills Mall (Mankato), and Brian Fowler, owner of Quality 1 Hr Foto and SPX Sports and Design (Mankato).
15 YEARS AGO
JAN/FEB 2008
Our 2008 Business Person of the Year was Jeff Thom of All American Foods (Mankato). Others honored were Clint Brown of Industrial Construction Services (St. James) and Wayne Kahler of Kahler Automation (Fairmont).
20 YEARS AGO
JAN/FEB
2003
Cover story: Dan Gislason of Gislason & Hunter (New Ulm). Profiled companies: New Hope Counseling & Mediation Center (Blue Earth) and Katolight (Mankato).
Southern Minnesota’s Premier Nursing Assistant Registry Test Site
For over a decade, South Central College (SCC) has been an approved test site for the Minnesota State Registry Test for Nursing Assistants, certifying qualified nursing assistants to work in long-term care facilities to meet our community’s health care needs.
According to employment data from the Minnesota Department of Employment and Economic Development, nursing assistants remain the sixth highestdemand job in Minnesota. Over the past year, SCC’s Customized Workforce Education division has provided Nursing Assistant certification exams for over 1,000 candidates at both North Mankato and Faribault campuses, including exams for hundreds of candidates who were trained under the Next Generation Nursing Assistant initiative.
The Next Generation Nursing Assistant initiative began in December 2021, at a time when long-term care facilities were experiencing severe staffing shortages amid the pandemic. At that time, Governor Tim Walz set a goal for the State of Minnesota to recruit and train 1,000 new nursing assistants using Federal American Recovery Plan funds to provide participants with free training, books, uniforms, and certification exams.
The state surpassed this goal in less than three months with the partnership of state agencies, higher education institutions, and long-term care providers. And in September 2022, Governor Walz announced another investment to continue Minnesota’s free nursing assistant training and testing program through February 2023 to further strengthen the state’s health care workforce pipeline.
“By bolstering our health care workforce and providing pathways to life-long careers, this initiative continues to benefit Minnesotans in the short- and long-term.
I’m proud to invest in a program that strengthens our health care workforce, eliminates barriers to entry into highdemand careers, and supports the health of our state,” said Governor Walz. “The success of this program is a testament to Minnesota’s ability to collaboratively address complex problems.”
As Southern Minnesota’s premier Nursing Assistant Registry Test site, South Central College will continue to offer Nursing Assistant certification exams at both campuses monthly, adding more test dates as needed to accommodate workforce demands.
To learn more, visit southcentral.edu/na