
6 minute read
Off-site solutions facilitate timely completion of luxury residential scheme
The construction programme for Turkington Rock’s The Paddock in South Dublin, built over the past year by Vision Contracting, benefitted greatly from an early decision to use precast concrete elements for the build.
Described as Ireland’s first interior design-led luxury residential property developer, Turkington Rock is a collaboration between interior designer Helen Turkington and developer Keith Craddock (Red Rock Developments).
Advertisement
Helen Turkington has worked on some of the most exclusive homes in Ireland and across Europe, while Keith Craddock’s Red Rock Developments has built a reputation for creating exquisite family homes.
Turkington Rock has assembled a unique collection of development sites in south Dublin to create newly-built family homes to the highest specification.
THE PADDOCK The Paddock on Bushy Park Road, Terenure, Dublin, is the latest residential development for the innovative partnership. Built over the past year by main contractor Vision Contracting, the high specification residential scheme of eight contemporary houses is finished to Nearly Zero Energy Buildings (NZEB) standard, with precast concrete panels and floors by O’Reilly Concrete. The decision to go with off-site construction for the structure of the houses was influenced by the fact that the development was on a tight site in a busy residential community. But this decision took on even greater significance when the Covid-19 pandemic struck, as it meant that movements to and from site and numbers working on site could be kept to a minimum without impeding project progress to any great degree.
LUXURY HOMES The Paddock is a mix of four- and five-bedroom houses, some over a single-storey basement, with south facing rear gardens. Landscaped private courtyards and balconies also form part of the bespoke design.
Each house is finished with an external brick façade. All are fitted with underfloor heating driven by air to water heat pumps and have HRV ventilation, along with triple-glazed windows and doors. The A-BER rated houses have airtightness levels of between 2 and 3 m3/ hr/m2.
OFF-SITE SOLUTION According to Paul Daly, Site Manager, Vision Contracting, achieving the airtightness performance criteria was helped by the fact that precast concrete panels and floors were precision-fabricated off site.
“The brief to Vision Contracting at the outset of this project was to deliver an exceptionally high-quality finish together with the highest standard of energy efficiency,” Paul Daly explains. “The client supplied a design, which we analysed. We then presented them with solutions that would meet their energy performance requirements and facilitate the smooth construction of the scheme.”
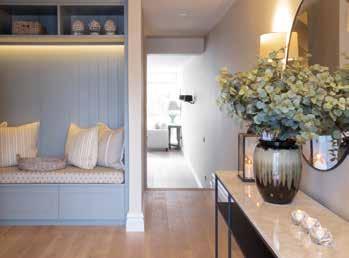
The site was tight and located in a busy residential area with a school nearby.
“By using precast concrete frames for all the houses, we were able to substantially reduce traffic on site as well as speed up work on site,” Daly continues. “This also helped when we introduced new Covid-19 procedures on site. The delivery of the panels was timed not to interfere with commuter movement in the area. Also, as the precast frames were precision made, the required level of airtightness was more easily achieved than would have been the case with more traditional building methods.”
TURKINGTON ROCK The client, Keith Craddock, Turkington Rock and Red Rock Developments, says that The Paddock is a unique high-end residential development and the site logistics demanded an innovative construction approach to meet the scheme’s quality and programme requirements.
“I have worked with Vision Contracting on a number of residential projects over the past four years and I knew from the outset that they would deliver for Turkington Rock on all aspects,” he comments. “The precast basement and off-site manufactured structure solution were a key part of the overall project’s success. This would not have been possible without Vision Contracting’s involvement. Their unrelenting attention to detail and focus on workmanship has helped deliver the quality homes that we require for our purchasers.”
ADDRESSING COVID-19 CHALLENGES The building programme was planned to last 12 months. Paul Daly says that the project had made great progress when the first lockdown hit in March.
“We then worked closely with the client and our teams to get the site ready to reopen in May after the first lockdown,” he explains. “When we were shut down in January of this year, the programme only had about four weeks to run. This achievement was made possible by the client making decisions quickly, and us having an experienced project team and supply chain that adapted quickly to the new working procedures. They all put in outstanding performances on the job.”
VISION CONTRACTING Colm Fehily, Director, Vision Contracting, says that The Paddock is a great project for Vision Contracting to have in its portfolio as demand for high-specification luxury homes grows
“This was a great showcase project for us,” Colm Fehily explains.
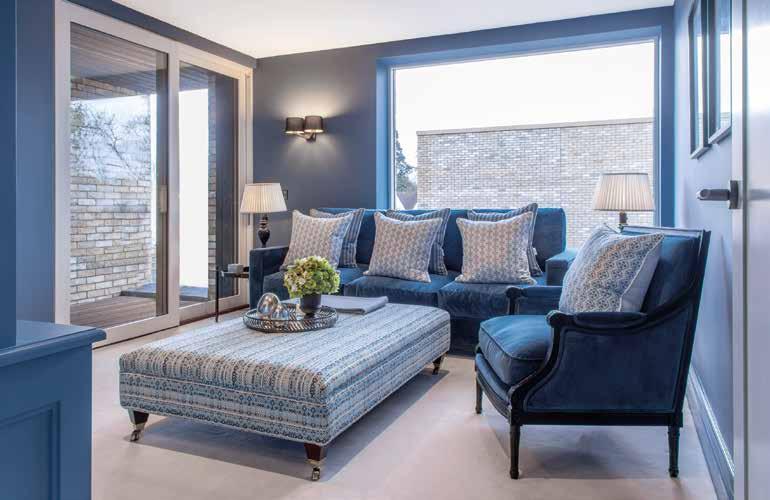
PROJECT TEAM
Client: Red Rock Developments Main Contractor: Vision Contracting Structural Engineer: Garland Consultancy Cost & Quantity Consultant: Duke McCaffrey Consulting
SPECIFICATIONS
Fully concrete built from precast wall and floor panels manufactured off site NZEB standard of construction Underground basements with secant piling embankment retention system with full Bentonite – Geotextile waterproofing system provided by Cetco Ireland.
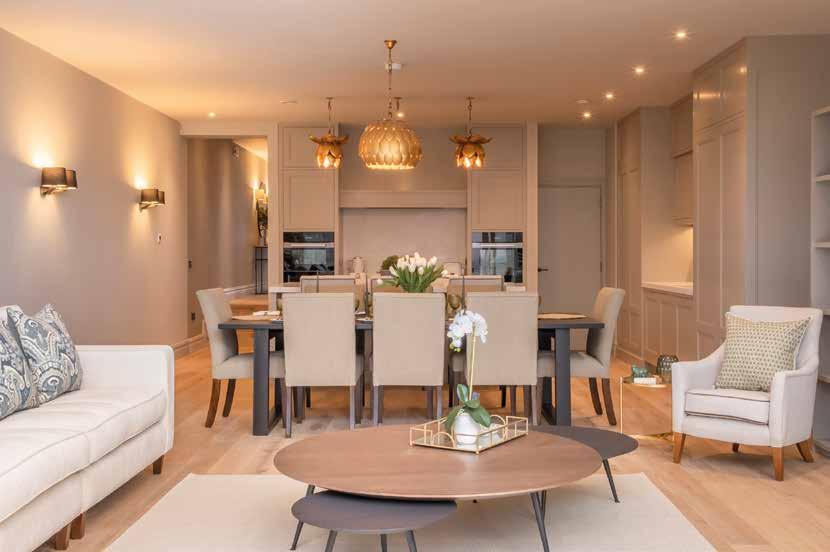

“Following the last housing crash, the market for this type of house was slow to recover. But it has now started to open up. The Paddock is a prime example of a new form of modern low-energy luxury homes. We are delighted with the finished scheme and how everyone pulled together to deliver it so successfully.”
Fehily says that the mix of its work has to some degree, protected it from too much exposure in the past year.
“While we have several developments in various sectors in Dublin and on the east coast, we also have a good mix of work across other regions, with a spread in pharma, residential, retail, educational, industrial and commercial areas. We are looking forward to bringing the projects we couldn’t work on back on site in the coming weeks. We also have a lot of new work on our order books for the coming year.
Vision Contracting has completely changed how it operates its sites and projects as a result of Covid-19, with many of the new procedures and practices here to stay.
“Sites will have less traffic and people on them,” adds Fehily. “Project and personnel management have become much more efficient, and monitoring and reviewing work has also greatly improved. One benefit to come as a result of the Covid pandemic is the introduction of remote meetings. We no longer have groups of people travelling from all over the country to attend a meeting. We are now achieving efficiencies across the board that we could not have possibly imagined 18 months ago. The Irish construction sector as a whole has achieved so much in the past year, and we in Vision Contracting are delighted to have been able to play our part in that,” Colm Fehily concludes.
Scan the QR code to view a video of the development
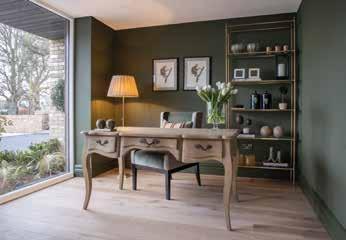