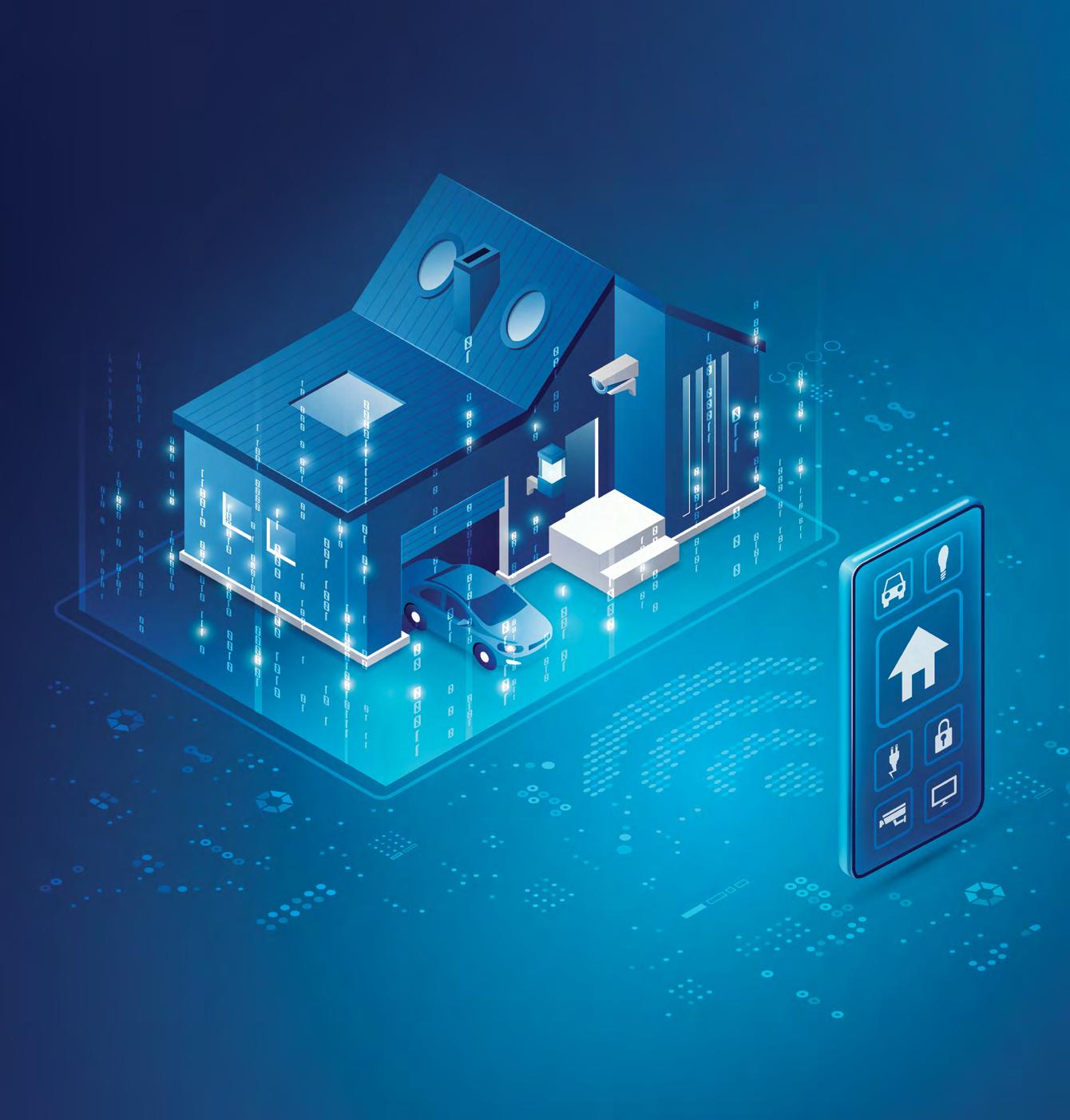
21 minute read
INNOVATION
ANDROID BUILDING
Real estate leaders come out in support of Netix Global’s Novus Partner Program to empower ‘Android Building’ approach in region
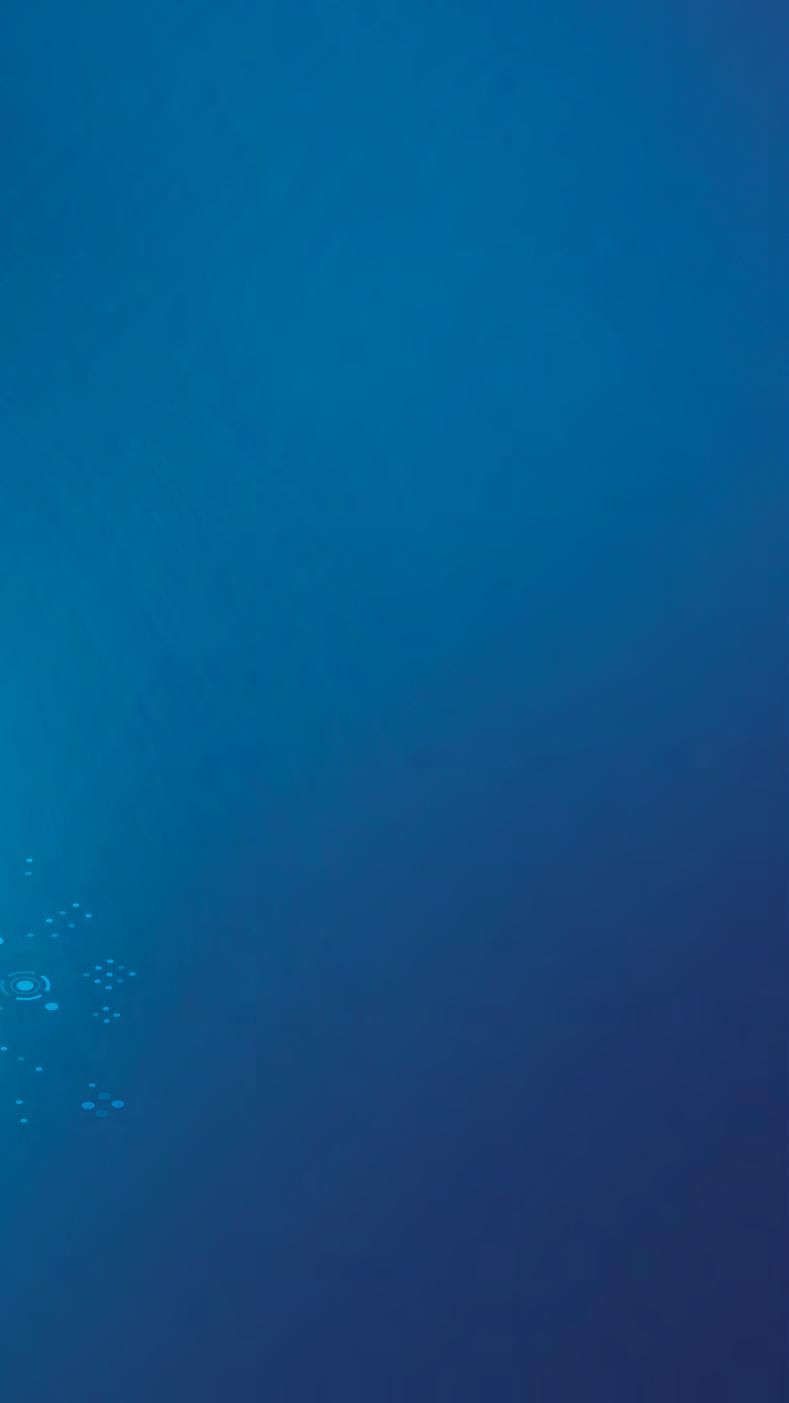
Netix Global BV - a subsidiary of SB Group International, and leading vendor-neutral iIBMS automation solutions provider - has been acclaimed for its Novus Partner Program, by top Middle East real estate industry stalwarts. The initiative aims to lead the Brownfield Revolution in Middle East Real Estate, and empower an ‘Android Building’ approach, in the region.
Sanjeevv Bhatia, Chairman of SB Group International and CEO of Netix Global BV; Priyesh Bhatia, General Manager of ODS Global; Ganesh Khanolkar, Managing Director of Exenture India & ODS India, DOS of Teknoware and Netix; Jehad Abu Shamiyeh, CEO of Electro Power Systems, Kingdom of Saudi Arabia; Vivek Wagh, Business Development Director, SB Group International, Oman, Africa & South East Asia; and Jagdish Rajan, CEO, Garnet Technologies, part of JBK Qatar; have come together as Platinum Partners, as part of the newly launched Netix Novus Partner Program.
IoT, AI and cloud-based applications are rapidly transforming Middle East real estate. Research indicates(1) that digitalization efforts will grow the KSA smart cities market to $14.75 billion by 2027, at a CAGR of 19.6%. In the past, this potential has been limited – for all practical purposes – to Greenfield developments. The Netix Novus Partner Program aims to create digital parity across the real estate sector, through an ecosystem of tech-empowered service providers, to implement these technologies in Brownfield projects as well.
Research released by Ernst & Young(2) believes automation can double the KSA economy of the KSA to $1.6 trillion, by adding an additional $293 billion by 2030. But, in the past, this potential was undermined by legacy, vendor-locked, OEM-led BMS. The Netix Novus program overcomes these limitations with an interoperable, open-protocol ecosystem, based on a new generation of IoT, AI, and Machine Learning, enabled building automation and management systems. In addition, Netix is also bringing the 7 Series line of centralized emergency lighting control panels, from Finnish vehicle and emergency lighting manufacturer Teknoware Oy, to the region; to enable features such as remote monitoring and control, automatic status reports, selectable output circuits, and a universal diagnostics portal. >>>
Priyesh Bhatia, General Manager, ODS Global Vivek Wagh, Business Development Director, SB Group International Jehad Abu Shamiyeh, CEO, Electro Power Systems Ganesh Khanolkar, Managing Director of Exenture India & ODS India Jagdish Rajan, CEO, Garnet Technologies, part of JBK Qatar
“The pre-launch response to the program has been great, and partners across Saudi, Oman, Qatar, UAE and India have already come on-board”, says Sanjeevv Bhatia, CEO of Netix Global BV. “Netix has already shaken hands with Garnet, part of JBK - a market leader in Qatar with 27+ years of experience in ELV, BMS and Security Services; as well as Electropower, a market leader in the Kingdom of Saudi Arabia, with a strong presence of 20 years in the Gulf region, across Yemen, Qatar, Jordan, Dubai, and Bahrain, as well”.
The Novus Partner Program was inspired by the successful implementation of Netix’s by Dubai-based ODS Global – who are now the program’s first Platinum Partner. ODS has won the maintenance of the Building Management System (BMS) 18 properties and 5 vertical communities by Emaar, across Downtown Dubai and Dubai Creek Harbour. Netix’s retrofit solutions enabled ODS Global to avoid replacing the entire system and help Mazaya save 75% of costs. Netix’s IoT and AI-based open protocol solutions also played a crucial role in ODS Global being awarded a three year maintenance contract for the building automation systems of 24 DAMAC Properties towers; the upgrade and maintenance of 3 Mazaya Towers’ buildings; and system integration projects at the Jafza Convention Centre, the BVLGARI Resort in Jumeirah Bay, the Pullman Hotel, and the Emirates Airlines Staff Accommodation in Dubai.
Set in the backdrop of major regional initiatives - such as the KSA’s Vision 2030, which identifies real estate as an important sector – real estate stakeholders are backing the shift to the kind openprotocol models that the Novus program will enable. “We are very excited to join forces and accelerate the revolution of the industry. Netix Global’s open protocol, plug and play approach offers the
About Sanjeevv Bhatia
Aceaseless and ambitious serial entrepreneur, Sanjeevv Bhatia is the CEO of Netix Global BV, a vendor neutral iIBMS automation solutions provider, with a strong focus on solutions for sustainable smart buildings, smart cities and energy efficiency, including an intelligent Integrated Command & Control Center (iICCC) for remote monitoring & management of facilities. He is the force behind an impressive portfolio of companies, offering cutting edge products and services across the Middle East, Europe, Asia Pacific and the USA. Managing Director and Partner at Teknoware Middle East, and CEO of ODS Global DMCC, Exenture Global BV, Netix Global BV and Exenture Films India Pvt Ltd, Sanjeevv’s urge to address unmet needs through innovation has found expression in an array of market leading ventures. A Master of Business Administration (MBA, Marketing and Finance) from the Southern New Hampshire University, Sanjeevv’s career of more than 20 years has been a meteoric rise, built on a strong work ethic, vision, and focus on people and partnerships.
perfect solution to the inflexible systems the building automation industry is struggling with currently. Netix’s ‘Android Building’ approach will empower continuous innovation and improvement, and transform the real estate landscape in the Kingdom”, says Jehad Abu Shamiyeh, CEO of Electro Power Systems, KSA.
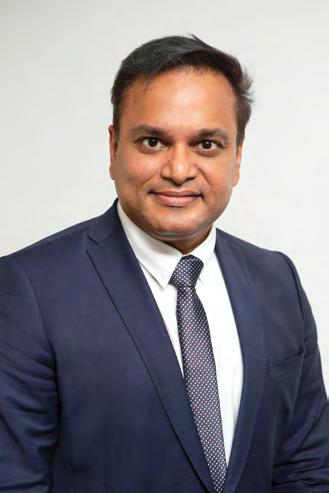
About Netix Global BV
Headquartered in Schiphol-Rijk (Netherlands), Netix Global BV is a vendor-neutral iIBMS automation solutions provider, with a strong focus on sustainable smart buildings, smart cities, and energy efficiency. The company’s global presence currently extends from Europe to the Middle East, USA, India, Singapore, with upcoming debuts in the United Kingdom, Egypt, Qatar, KSA, Canada and Australia, as well as active opportunities being pursued in broader markets. Building on the strengths of an open framework and IoT technology driven approach, Netix Global BV is a premier provider of bestin-class building automation systems, solutions and services. The company’s comprehensive industry expertise ranges from design, engineering, integration, connectivity, testing, commissioning, and maintenance of smart building eco-systems, and their components. Netix Global BV’s products and services include an Integrated Control Command Center (ICCC); NETIX Uniview SUPRA, a feature-rich supervisory software suite built on the Niagara platform; Managed services offering predictive maintenance for both buildings & machinery; Push to Talk global Mobile Apps that replace traditional Walkie Talkies; Smart Metering solutions and more. Underscoring the confidence that Netix Control Solutions stands out, as a class part, are the team behind this promising venture, who boast a collective experience featuring stints with Honeywell, Johnson Controls, Siemens, and Delta Controls. For more information please visit: https://www.netixglobal.com/
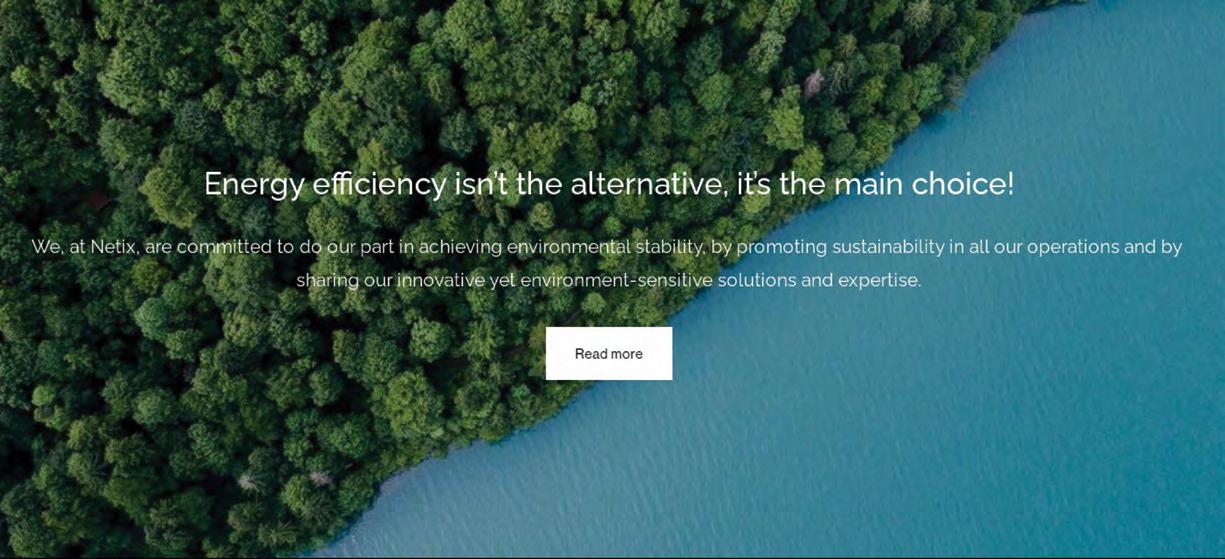
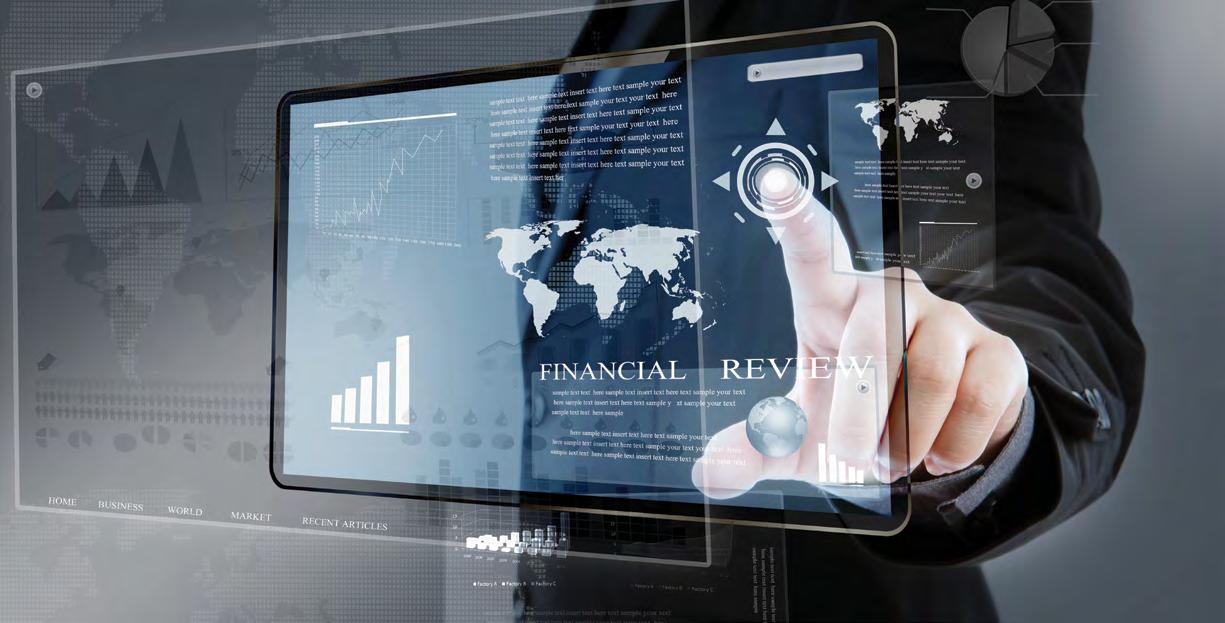
FUTURE OF FM OPERATIONS AND DATA-DRIVEN SERVICE DELIVERY
The 2020s are an era we have approached with apprehension, excitement, uncertainty and ingenuity as technology races forward at breakneck speed. While the professional landscape has changed in the recent past, we still do the same work, but in a different environment and under different circumstances. As a result of this change, we see the role of FM service delivery and property operations as a whole, become more and more prominent, transitioning from an operational level to a data-driven strategic path. This raises many questions on the future of facility operations and how operatives can stay nimble and flexible enough to respond to these changes? Will COVID-19 mean the end of the firefighting mode in operations? How will relationships with service providers change? Will the pandemic alter the way we measure O&M (operations and maintenance) SLAs and KPIs? How do we design an operational roadmap that can help overcome these challenges? Together with four facility experts from leading ecosystem organizations, we investigated the future of strategic dataled facilities management. We asked Prabhu Ramachandran, Founder & CEO, Facilio Inc., a leading AI-based property operations platform that manages over 70m sq. ft of commercial real estate portfolio globally, to weigh in on how technology is reshaping the future of real estate operations through powerful outcome-focused solutions.
What are the barriers to innovation in real estate operations & FM services today?
Legacy CaFM software has evolved considerably since their inception; expanding in scope to include inventory and asset management, cost analysis, and vendor management, etc. At a rudimentary level, CaFM adopters have successfully pivoted from paper-based systems, to cloud-supported digital applications as much as possible. However the new reality of property operations demands products and services that are more flexible, scalable, and interoperable. Property operations are left grappling with time to switch between tools, chasing people for information exchange, dealing with multiple contractors and subcontractors, and receiving outdated reports.
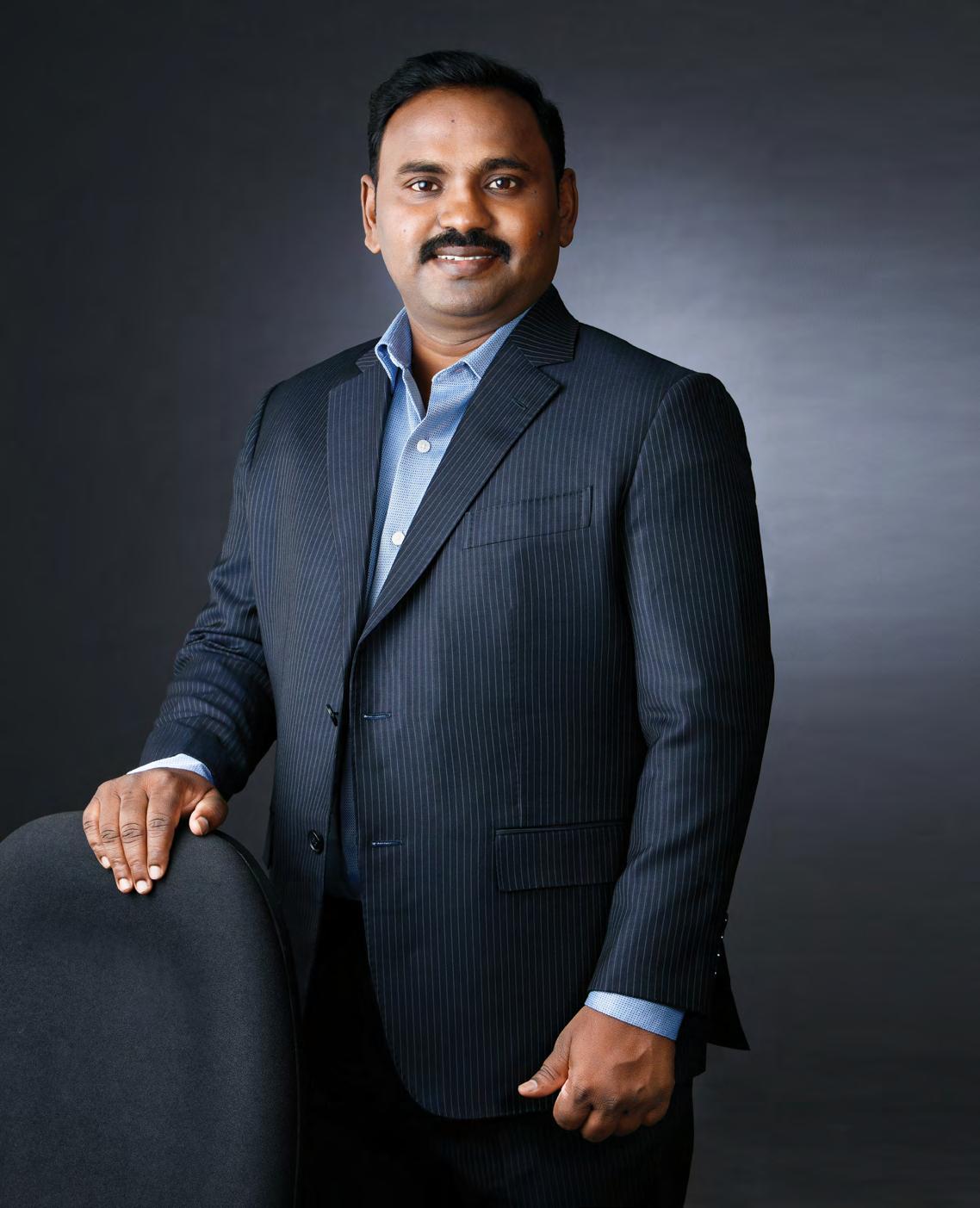
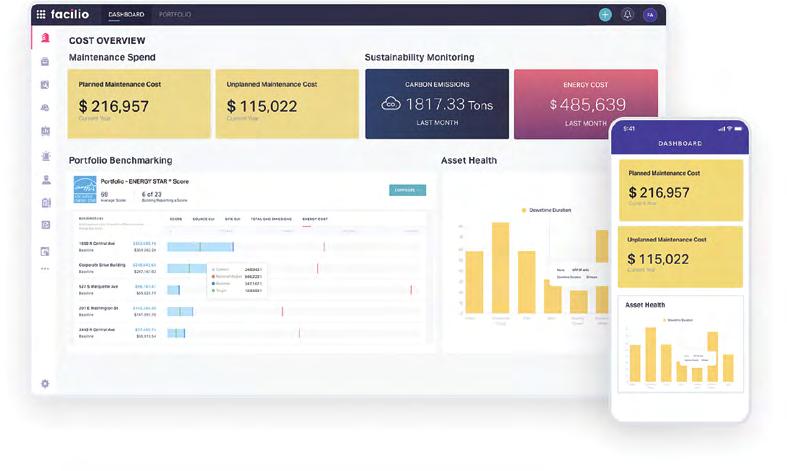
Many of the legacy solutions are horizontal solutions, and not really built specifically for real estate. As a result, they are often underutilized. Commercial real estate portfolios can be complex, often involve multiple asset types, and frequently leverage single purpose automation technologies utilized in a siloed manner, which can result in a fragmented view of the portfolio and a lack of useful information. The cost of leaving this issue unaddressed is that O&M leaders are left dealing with blind spots, having to resort to reactive firefighting, and limited ammunition for innovation
In contrast, imagine the ease of automating & digitizing multiple interactions, workflows, processes, and information exchange; within a single platform and a single place - without the integration bottlenecks and heavy price tags, typically associated with legacy and regular market solutions. The emerging data-driven O&M software platforms are designed to address issues for all stakeholders and optimize all functions at the same time, while creating results where they matter most, which is the delivery of exceptional customer experiences
How will a data-driven approach bridge this technology gap?
The new generation of data-driven FM software takes a workflow-driven approach to the O&M lifecycle. It creates a real-time and targeted context for maintenance schedules, which is easily accessible by stakeholders anytime, anywhere, with complete mobility. This real-time and across-the-board access creates optimal and multi-party stakeholder engagement, and with good data, benchmarking becomes easier, resulting in significantly improved service quality and delivery.
We can see the difference that access to quality, realt-ime data has made to sectors like e-commerce—in which players like Amazon have redefined the standards of delivery services; ride-sharing apps like Uber—which created immediate and quantifiable value for both end-users and drivers. The commercial real estate industry has a similar opportunity to introduce unprecedented services, efficiencies, and operational agility, by leveraging data. With a unified software platform that enables the basic requisites of maintenance management, a modern integrated O&M approach enables portfolios to set up unique workflows and approvals—algining provider services with end customer’s business processes, offering mobility, service desk, visitor management, contractor management, budget, stakeholder portals, real-time executive insights, and more.
Drivers of this change The sudden and dramatic nature of the COVID-19 pandemic was a wake-up call for O&M teams, making them realize the limitations of the legacy tools and processes they were using. At the same time, building occupants also became aware of the flexibility and adaptability limitations they were dealing with, leading to them wanting greater control over their environment, as well as up to the minute information and frictionless services. Transformationally, the spotlight was on operational resilience, and O&M teams emerged as a foundational strategic function, to empower building owners and operators, and create a mechanism to address the concerns of tenants and occupants.
The industry has realized that it needs to shift to a more proactive and agile model, with nimble and empowered FM teams as a fundamental building block in a strong operations strategy. Earlier, owners would keep on acquiring new buildings to gain customers, and a huge focus was on the >>>
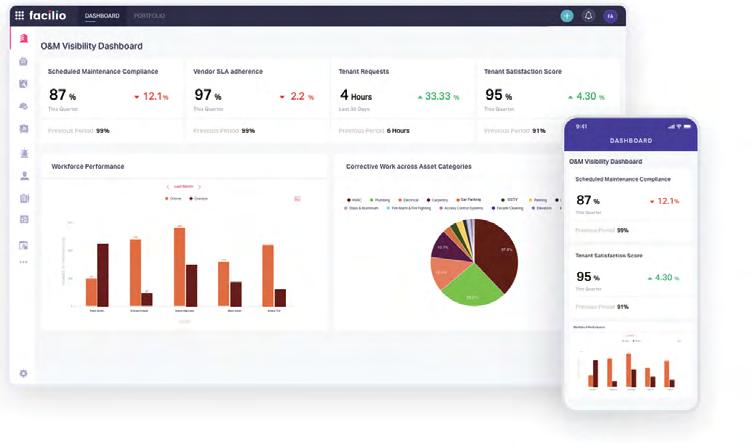
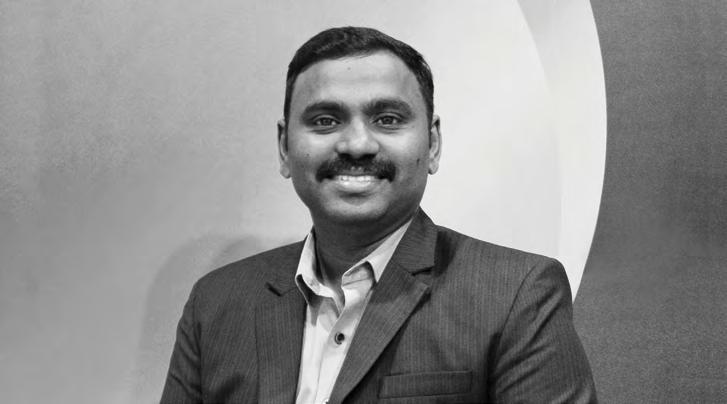
sales side of real estate. The focus is now on increasing the square feet leased by becoming more operationally efficient, and ensuring that tenants are happy, at a lower cost to the business. Owners also have a need to be more agile, to differentiate themselves, with end-user experience firmly at the core of measuring service quality, and brand identity.
From an innovation standpoint, how can you take this to the next level for larger efficiency gains across a portfolio?
Real estate portfolios are also setting themselves up for smart building success, when they choose a connected approach to CaFM operations. In its current form without real-time information from buildings, CaFM is vastly underutilized and at the risk of becoming redundant. The key is to create a Connected Ops environment where the software platform provides a hardware-agnostic approach to connect real-time building data, with core O&M functions. Besides streamlining workflows, you can now optimize them for maximum performance.
Failure to do this will relegate CaFM to its most basic version - that of keeping maintenance-related logs. If the value of the technology is to be optimized, it must have access to a common database that includes systems data points; like asset performance, energy usage metrics, FDD data, etc. The data quality - or the lack thereof - will have a direct bearing on deep-dive analysis, maintenance schedule, and therefore on service quality and associated cost. Such transparency in building operations favours multiple stakeholders, and O&M leaders most of all; giving them real-time access to vital information - such as asset health, vendor accountability budget versus cost analysis, a single record of information, resource utilization, and overall gaps in operations - paving the way for fundamentally improving property operations.
Centralized and connected operations are another key area that will take portfolio scale efficiency gains to the next level. For instance, if a CRE business has procured 10 different applications, this constitutes a huge investment. By contextually integrating these functionalities onto a common centralized platform, the value unlocked becomes exponentially greater. So, such a centralized Command Center allows businesses to optimize resources, operate with greater flexibility, and identify innovation gaps, through a single-window and granular real-time view, of their operations.
Benefits of a data-driven approach to customers
Putting it simply, a data-driven approach is just the smarter and more cost-efficient way to operate properties. And this is measurably apparent across the entire spectrum of metrics and business outcomes. Our customers have reported workforce productivity improvements of up to 15 percent; a reduction in complaint escalations of up to 90 to 95 percent; and an up to 50 percent reduction in asset downtime.
The reliance on a modern O&M solution for decision-making has increased significantly in recent years. And considering a major chunk of building life cycle costs can be attributed to workflows around maintenance, approvals, service requests, and occupant experience, this is not in the least bit surprising. The consensus around adopting integrated, data-driven O&M software has now crossed the tipping point within the industry; and the impact on operational bottom lines, asset performance, and end-user experiences, will be profound.
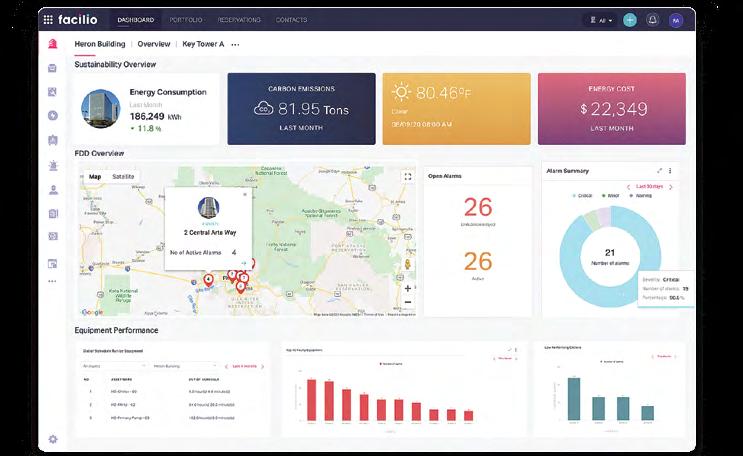
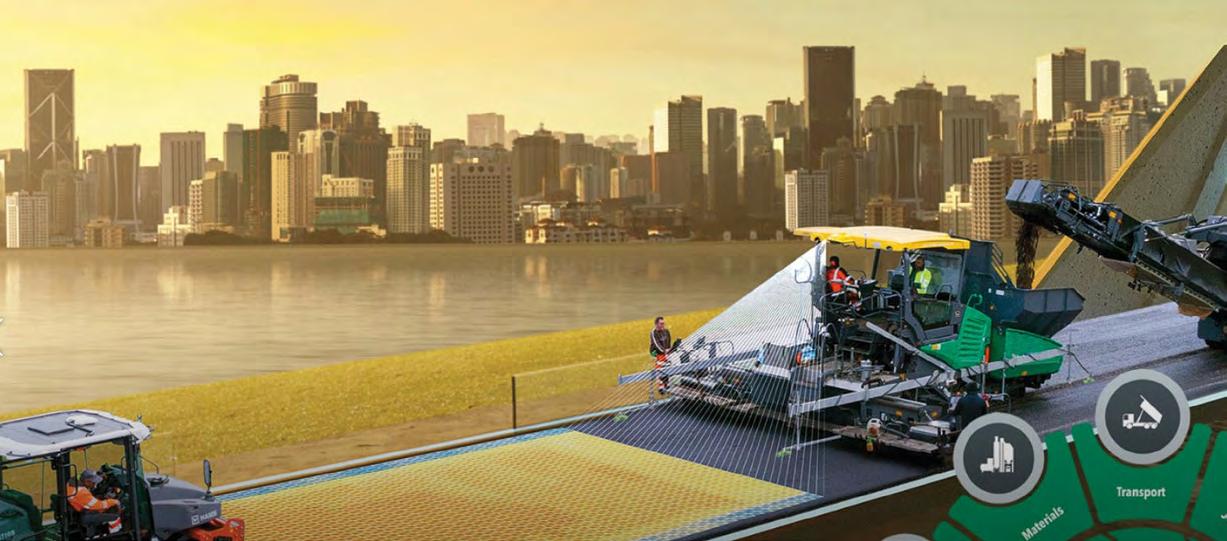
SMART ROAD CONSTRUCTION
OPTIMUM COORDINATION AND MAXIMUM EFFICIENCY WERE REQUIRED FOR PAVING A WIDTH OF 11.5 M IN THE GUBRIST TUNNEL: AS A DRIVER OF DIGITAL JOB SITES, CONTRACTOR MARTI AG SOLOTHURN BAUUNTERNEHMUNG PUT ITS MONEY ON VÖGELE’S WITOS PAVING PLUS SOFTWARE-BASED PROCESS OPTIMISATION SOLUTION. THIS NETWORKS ALL THOSE INVOLVED IN THE PROCESS IN REAL TIME AND DELIVERS NUMEROUS BENEFITS, ESPECIALLY ON BIG CONSTRUCTION PROJECTS.
It is one of the most complex infrastructure projects in Switzerland: 2022 sees the opening of the third bore of the Gubrist tunnel, 3.2 km long, as part of Zurich’s northern by-pass. With a diameter of 16 m, it is the largest tunnel bore in the country and is intended to relieve the chronic congestion of this section of road by providing three extra carriageways towards St. Gallen/Bern.
The demands on the road construction process were correspondingly high: despite the complex tunnel logistics, parallel working and heavy traffic, approximately 20,000 t asphalt had to be paved within a tight schedule and meet stringent quality standards.
This was why contractor Marti AG Solothurn Bauunternehmung decided to approach the project using a digital road construction solution. “As one of the largest contractors in Switzerland, the Marti Group has been active in driving digitalisation in all areas of construction for years - from structural to civil engineering. For a project of this scale, it was obvious that we should use a solution which enables us not only to visualise planning digitally, but also to control job site processes actively,” says Cedric Berrut, civil engineering operations manager.
NETWORKED SYSTEM SOLUTION FROM THE PAVER MANUFACTURER Vögele’s WITOS Paving Plus product was the one selected. This software-based process optimisation solution networks all those involved in the project from the construction manager to the mixing plant manager to the paving supervisor and on to the paver operator and consists of a total of five modules: these allow job site planning, provision of mix, transport of mix, asphalt paving and subsequent process analysis to be managed by one single system in real time. Among other things, this facilitates just-in-time delivery to the site and continuous paving with no paver stoppages. The paving team can react specifically to disruptions to the process. “One advantage from our point of view is that as an integrated solution from the manufacturer of the machine, WITOS Paving Plus matches the paver perfectly,” adds Berrut. “This gives us immediate access to all the machine data.”
INTELLIGENT PROCESS CONTROL AND THE LATEST MACHINE TECHNOLOGY For the contractor, there was another new feature about the job site: at 11.5 m, this was the widest paving project without joints ever completed in Switzerland. As a consequence, Marti also added two more Vögele machines to its vehicle park: the MT 3000-2i Offset PowerFeeder and the SUPER 2100-3i Road Paver in combination with the SB 300 Fixed-Width Screed. Combined with the Highway Class paver, the second-largest screed from this manufacturer achieves pave widths of up to 13 m and was therefore ideal for paving this three-lane section without joints. Over a stretch of road totalling 3.2 km, an 8 cm-thick foundation, base and binder course and a 4 cm-thick surface course were to be paved in two sections. “So on the one hand, we had to use a powerful combination of machines (feeder, paver and screed) which delivers an absolutely even result even across a large width, whilst on the other hand relying on intelligent process control to guarantee the smoothest possible processes,” says Berrut.
WITOS PAVING PLUS SIMPLIFIES LOGISTICS Paving the Gubrist tunnel required planners, construction managers and the paving team to take account of a number of logistical challenges: the mixing plant for Marti AG Solothurn Bauunternehmung is in Walliswil bei Niederbipp, some 100 km away. In order to avoid jams on this busy stretch of road and to minimise delays due to parallel working in the tunnel, Marti decided to pave at night. Vögele’s process optimisation solution simplified the logistical coordination of this process: the planning and control module allows planners to record and monitor all the key parameters, the machines required, quantities of material and their scheduling. The system transmitted to the mixing plant the number of trucks calculated, then compared this number with the data at the plant and calculated from this the cycling of the trucks and their arrival times on site. “Planning and production of mix were much more accurate,” reports Berrut. “This enabled us to match paving and compaction processes perfectly to suit material deliveries.”
CONTINUOUS PAVING, BETTER UTILISATION The job site module gave paving supervisor, construction manager and paver operator a real-time overview of paving progress, laydown rate and mix delivery throughout the entire project. The tablet PC or paver operator’s console enabled them to detect deviations from the plan in terms of paving time, paving distance or mix quantities and react if necessary. “This enabled us to ensure continuous paving and thus the appropriate quality,” says Berrut. Evaluation in the analysis module furthermore resulted in a significant reduction in waiting times as a result of cycling, as well as in fewer mix trucks than on comparable job sites. “Ultimately, this means reduced material and transport costs, fewer emissions, better utilisation and at the same time, better quality.”
PRACTICAL SYSTEM WITH GREAT POTENTIAL Another benefit of WITOS Paving Plus: the system can be used even under difficult conditions such as those prevailing in the Gubrist tunnel. In order to ensure reliable data transmission, Marti used a GSM network which was routed into the tunnel by additional antennas. “The project showed that WITOS Paving Plus is a practical solution with great potential for us,” adds Berrut. “It integrates well in our digital infrastructure and provides data we can use for our BIM models. This is a key point which we are going to expand on in collaboration with Vögele.” In future, Marti intends using the system for all projects involving regional and national roads and relatively large projects.
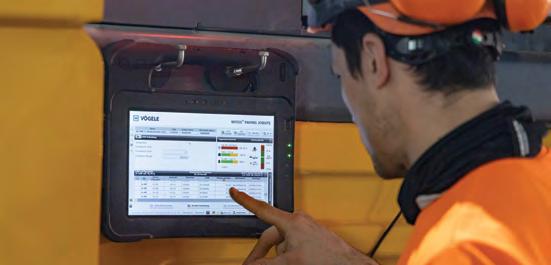
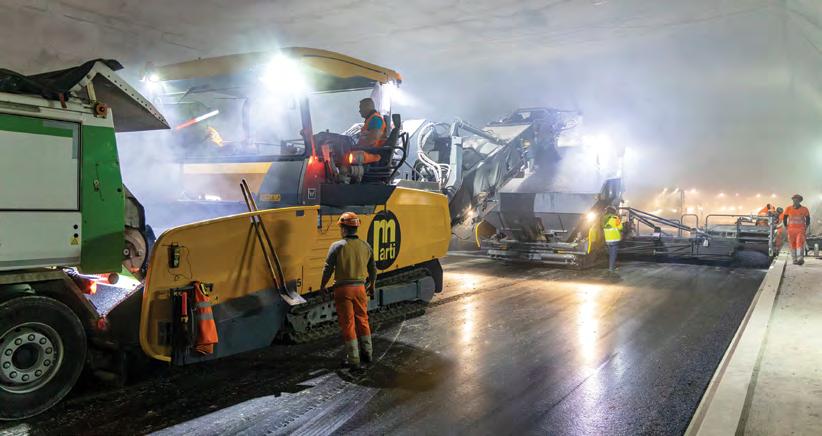
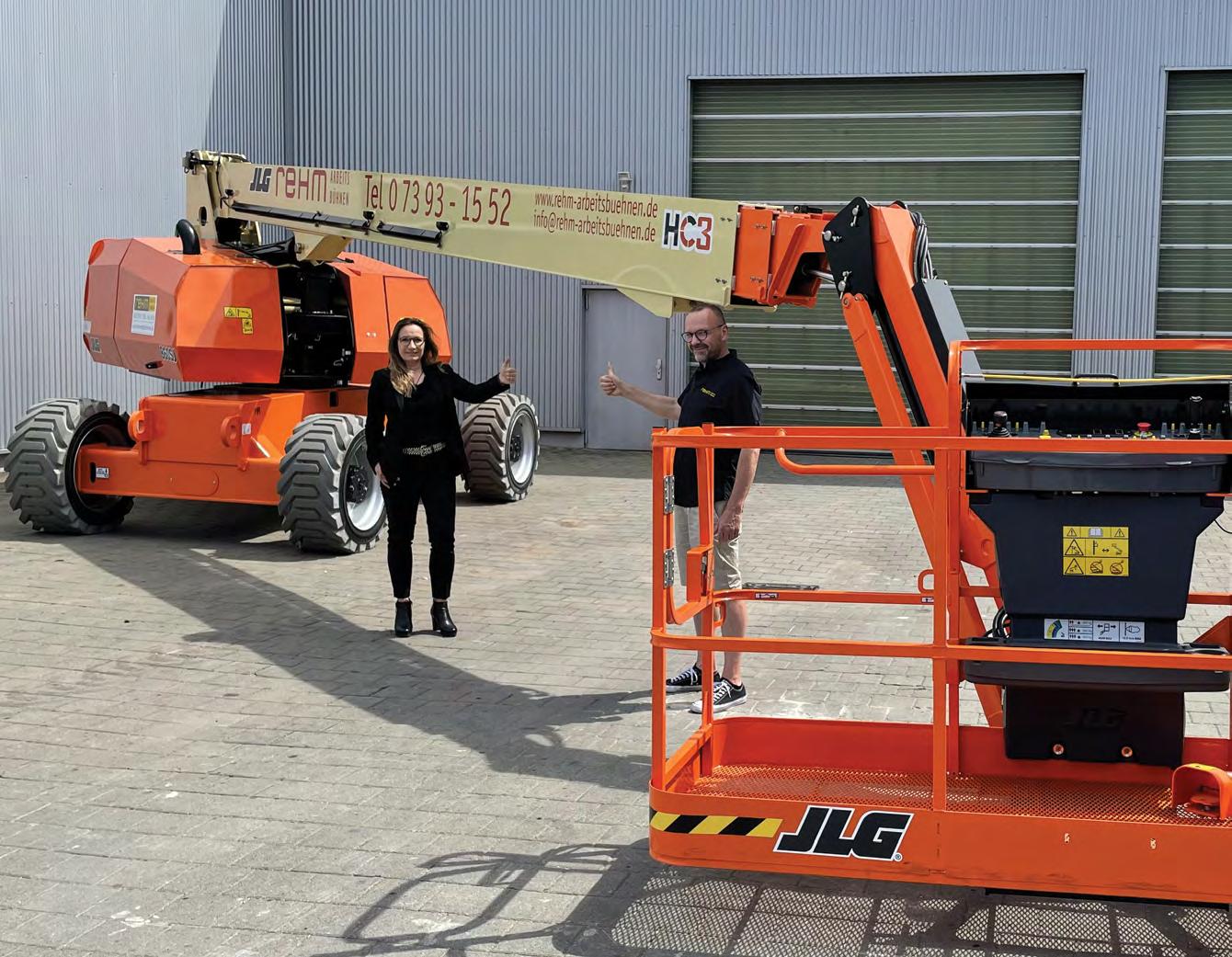
THE NEW JLG 860SJ HC3
FOR HEAVY LOADS AT GREAT HEIGHTS HAS ARRIVED IN GERMANY
JLG INDUSTRIES, INC., AN OSHKOSH CORPORATION COMPANY [NYSE:OSK] AND THE LEADING GLOBAL MANUFACTURER OF MOBILE ELEVATING WORK PLATFORMS AND TELESCOPIC MATERIAL HANDLERS, DELIVERS 860SJ HC IN GERMANY
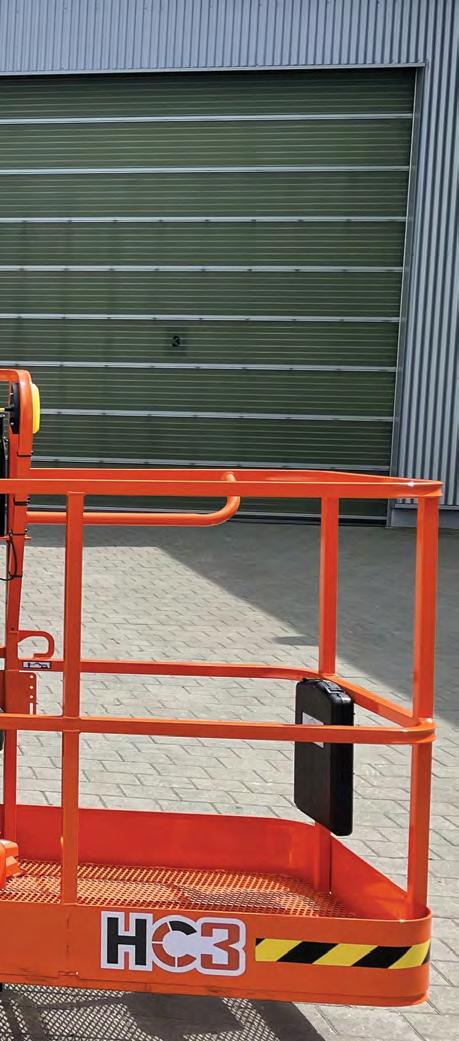
Professional access technology has had a successful home at Rehm in Munderkingen for more than 30 years. Well-known companies successfully carry out their construction pro-jects with the company’s working platforms, whether purchased or rented.
Today, the long-established Baden-
Württemberg company has a wide range of self-propelled working platforms with working heights from 6.60 m up to 43.15 m. The range includes platforms with electric, hybrid or diesel drive. JLG’s current range at Rehm includes the SL 153-22 DSP scissor lift, the Toucan 10 E-L and Toucan 12E+ vertical mast lifts and the 460SJ, 1200 SJP and 1350 SJP telescopic lifts.
“And yet,” says Uwe Rehm, Managing Director at Rehm Arbeitsbühnen, “we were always looking for another machine that would close the gap between our existing telescopic plat-forms up to 26.3 m working height and those with 38.5 m working height. A machine that also has something special and is made for heavy loads at great heights. That’s exactly what we found in the new JLG 860SJ HC3.”
LIFTING WITH NEW CAPACITY: UP TO 450 KG PAYLOAD ON THE PLATFORM With the new all-wheel heavy-duty telescopic platform, Rehm is up to date with today’s re-quirements. The new, powerful JLG 860SJ HC3 meets the increasing demand for more lifting capacity. In addition, this highperformance boom has maximum horizontal and vertical reach when difficult work around corners is required or confined work sites present a challenge. “We have had JLG machines in our rental programme since 1999. The decisive factor for choosing the new HC3 type was the increased payload of up to 450 kg. This is a real as-set for the customers and for us,” explains Uwe Rehm.
The HC3 strength lies in the “high capacity”, the “3” stands for three different platform loads to which the machine automatically adjusts. Working space and possibilities are expanded with the 860SJ HC3 for more flexibility and significant time savings: with its high load capaci-ty in the entire working area, up to three people including tools can be transported in one op-eration. For safe working at height, various components are reinforced for stability and durability purposes. All HC3 models also have an automatic load sensor (“loadsensing system”) that limits the range of use if the platform is overloaded. The control panel has also been im-proved. The displays detect the ambient light conditions and adjust the brightness accordingly for better visibility. And if the machine reaches the maximum side tilt of more than 5 degrees, a tilt alarm warns the operator.
A SUCCESSFUL COLLABORATION IN EVERY ASPECT Rehm Arbeitsbühnen has been working closely with JLG for over 20 years and trusts the continuous product innovations that JLG develops as a pioneer in the industry. “We are pleased that our customers always find the right, convincing solution for their numerous tasks in our range. JLG access platforms are extremely reliable, there are hardly any repairs or breakdowns. And regardless of whether it’s technology or sales, the contact is very cordial and reliable. And with the JLG 860SJ HC3, we already have the next rental trump card in our hands,” says Uwe Rehm. As a long-standing customer, Rehm was one of the first to receive the new JLG 860SJ HC3. For Ute Schnalzger, Sales Manager Rental JLG Germany, this is the best basis for continuing the longstanding Rehm business relationship in the future.