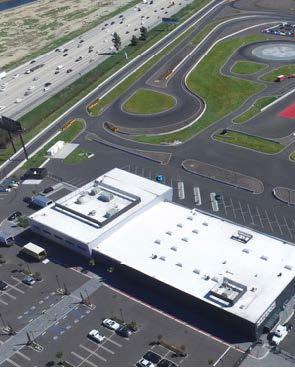
7 minute read
AMPCO Contracting
They Can Really Dig It
AMPCO Contracting, with Headquarters in Anaheim, has grown from a small start-up into a premier provider of pre-construction services in less than 20 years.
Written by Kevin Doyle Produced by Stephen Marino
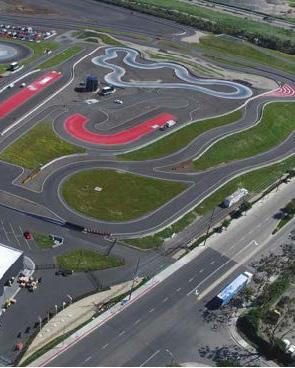
Established in 2004, AMPCO Contracting of Anaheim, CA has grown from a small start-up to become a premier provider of preconstruction services – demolition, abatement and earthwork – throughout the state in less than 20 years.
“I’m originally from Massachusetts and we started working out of my house, bidding projects,” explains President Andrew Pennor, who worked for another company for several years before making that leap of faith.
“I was doing all of the Sales and Estimating, so I figured I might as well just do it for myself. We wound up getting a couple of decentsized projects when we first started,” Pennor adds, bringing to mind the old axiom “you miss 100 percent of the shots you don’t take” attributed to Wayne Gretzky.
Today the company employs 150 individuals and experienced a breakthrough year in 2017 when it was named one of the Top 10 Fastest Growing Companies in Orange County by the Orange County Business Journal. Pennor says, “we’ve kind of gone from there – we have done some of the largest demoprojects in California for sure.” Pennor says the company began buying heavy equipment necessary to bid on earthwork projects in 2006, then added staff to deepen the expertise of that part of the overall operation. He also added a separate landscaping business, Earthscapes, in 2016 that brings in around $10 million annually.
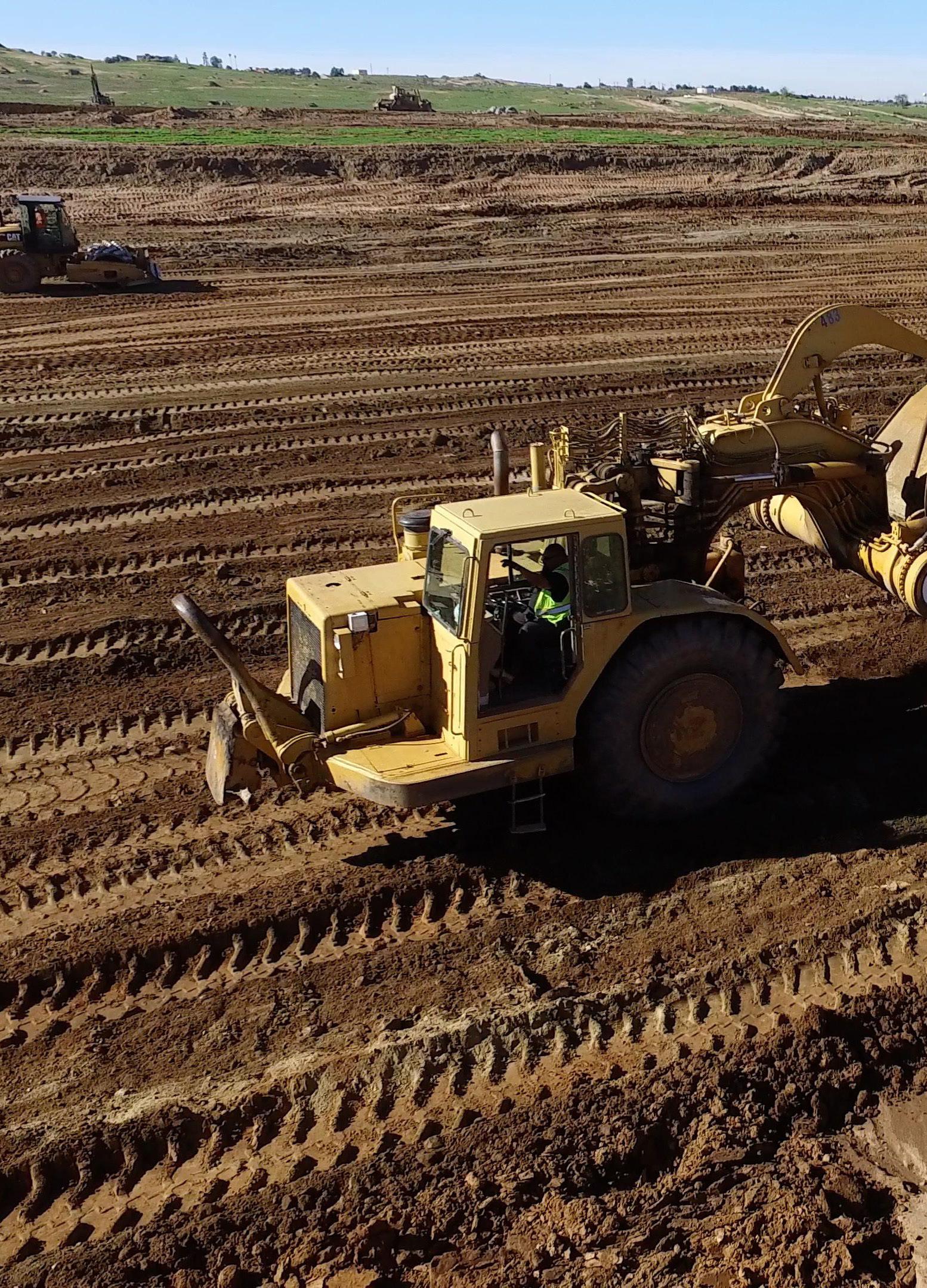
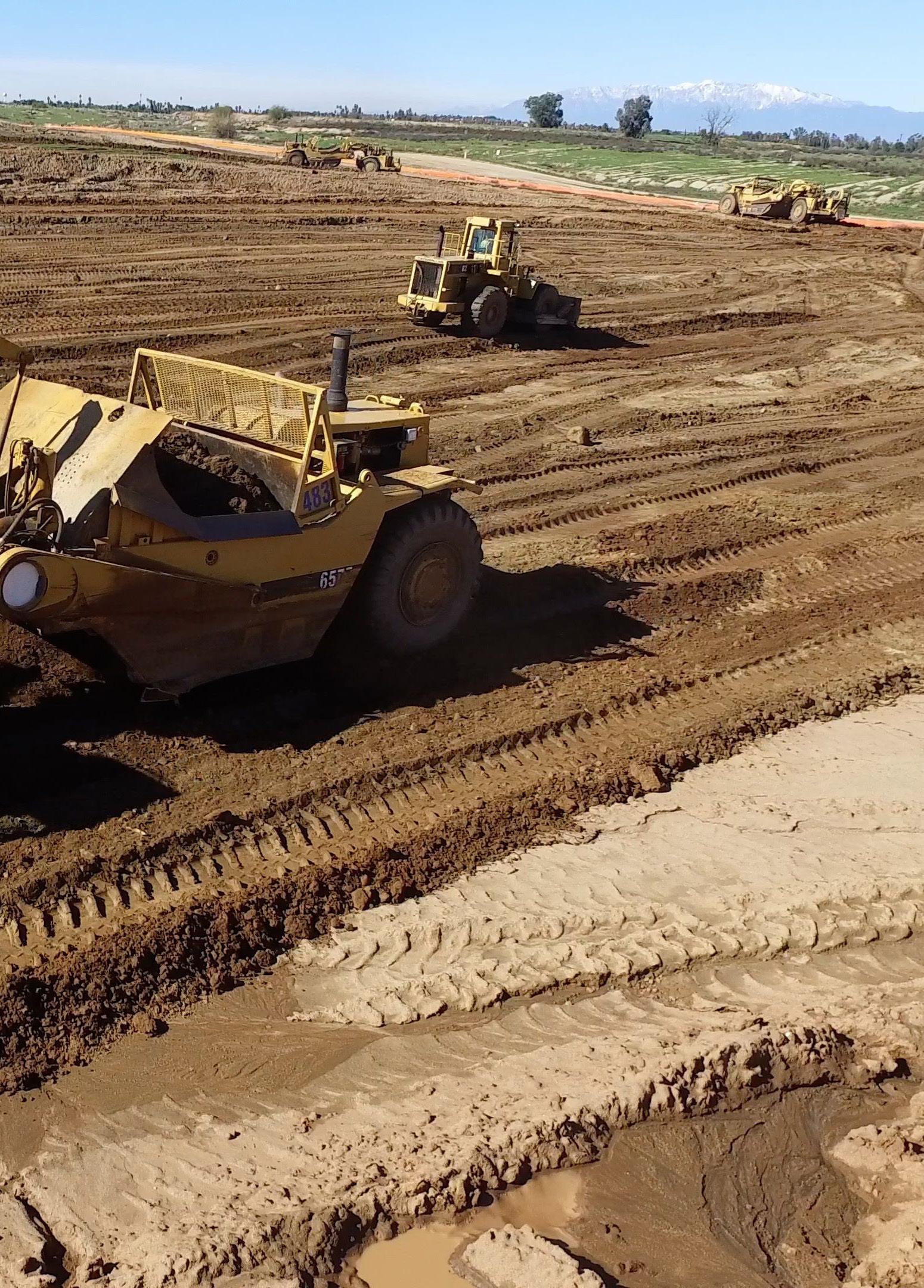
The reason the company has been able to separate from its competitors is clear to Pennor.
“There is a lot of opportunity for autonomy here. You can make it as you want because we’re not micro-managing,” he says. “We’ve all worked together for a long period of time, so there’s a strong camaraderie amongst our team. I’m easy to get along with and I want everyone to be successful, to be able to buy a house and live the American Dream.”
“There is a lot of opportunity for autonomy here. You can make it as you want because we’re not micro-managing. We’ve all worked together for a long period of time, so there’s a strong camaraderie amongst our team. - Andrew Pennor, President
Major Remediation Projects
Porsche Test Experience:
The project for Watson Land Company & Porsche Cars North America included demolition of all infrastructure and buildings; removal of underground transit pipe and other miscellaneous structures; importing 500,000 cubic yards of material and fill to a total cover depth of six feet; installation of a DTSC-approved landfill cap, which included GCL membrane/HDPE landfill membrane to protect the test track and the Porsche Experience Center for years to come; and installation of an HDPE methane gas collection system throughout the site. AMPCO oversaw construction management and performed contractor assist work for the piling excavation, foundation, utility installation and paving trades.
Boeing Long Beach Buildings
58 and 59: this removal project consisted of 104,000sf of two former paint hanger buildings on a 3.3-acre site, including one more than 80 feet tall. AMPCO completed the abatement,
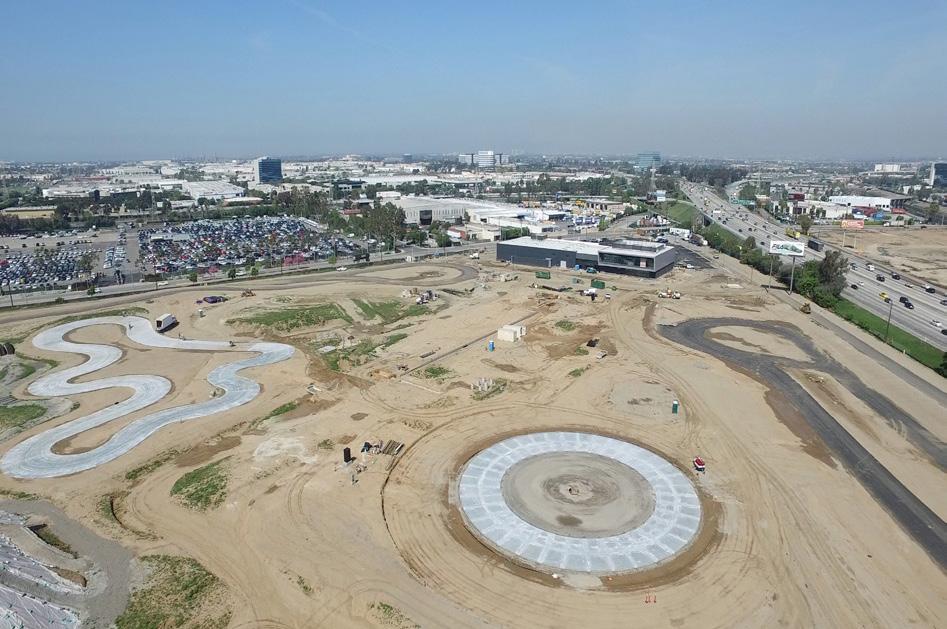
structural, and site demolition, including removal of asbestoscontaining materials (floor tile and mastic and pipe insulation), lead-containing materials (paint, ceramic tile), as well as solidified paint coatings.
“We’ve probably done more Boeing work than anybody,” Pennor points out.
Google Spruce Goose: AMPCO was contracted to complete the abatement of the interior lead paint and asbestos-containing materials at the historical site where famed aviator/actor Howard Hughes built the legendary Spruce Goose – the H-4 Hercules Flying Boat. The enormity of the project AMPCO took on included 285,000sf of buildings and structures – more than one million square feet of painted interior historical wood surfaces as high as 75 feet – on a 13-acre site. The company was directed to salvage as many historical components as possible while selectively demolishing building components, building slab and subgrade foundations in preparation for a new Google offices campus.
Safety Initiatives
Operating Procedure, meaning every employee is empowered and responsible to challenge unsafe work practices and situations. Field supervisors and superintendents are required to make sure every job site meets company safety standards and, if needed, have the authority to buy, rent, or build whatever is needed to ensure safety.
The company maintains full OSHA compliance with Project Managers, General Superintendents, Supervisors and Lead Men having completed OSHA 30 training. All employees are required to understand and comply with the company’s Illness and Injury Prevention Program (IIPP).
Potential project hazards are identified and communicated to engineering and an administrative control via an Activity Hazard Analysis that calculates the severity and probability of each hazard and provides an overall risk level.
Additionally, the Safety Division holds monthly training sessions while Field Supervisors conduct weekly site-specific
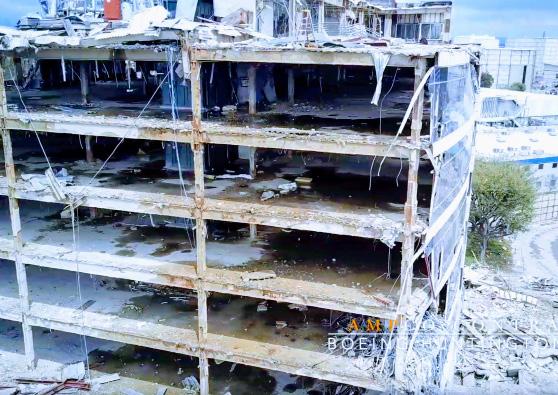
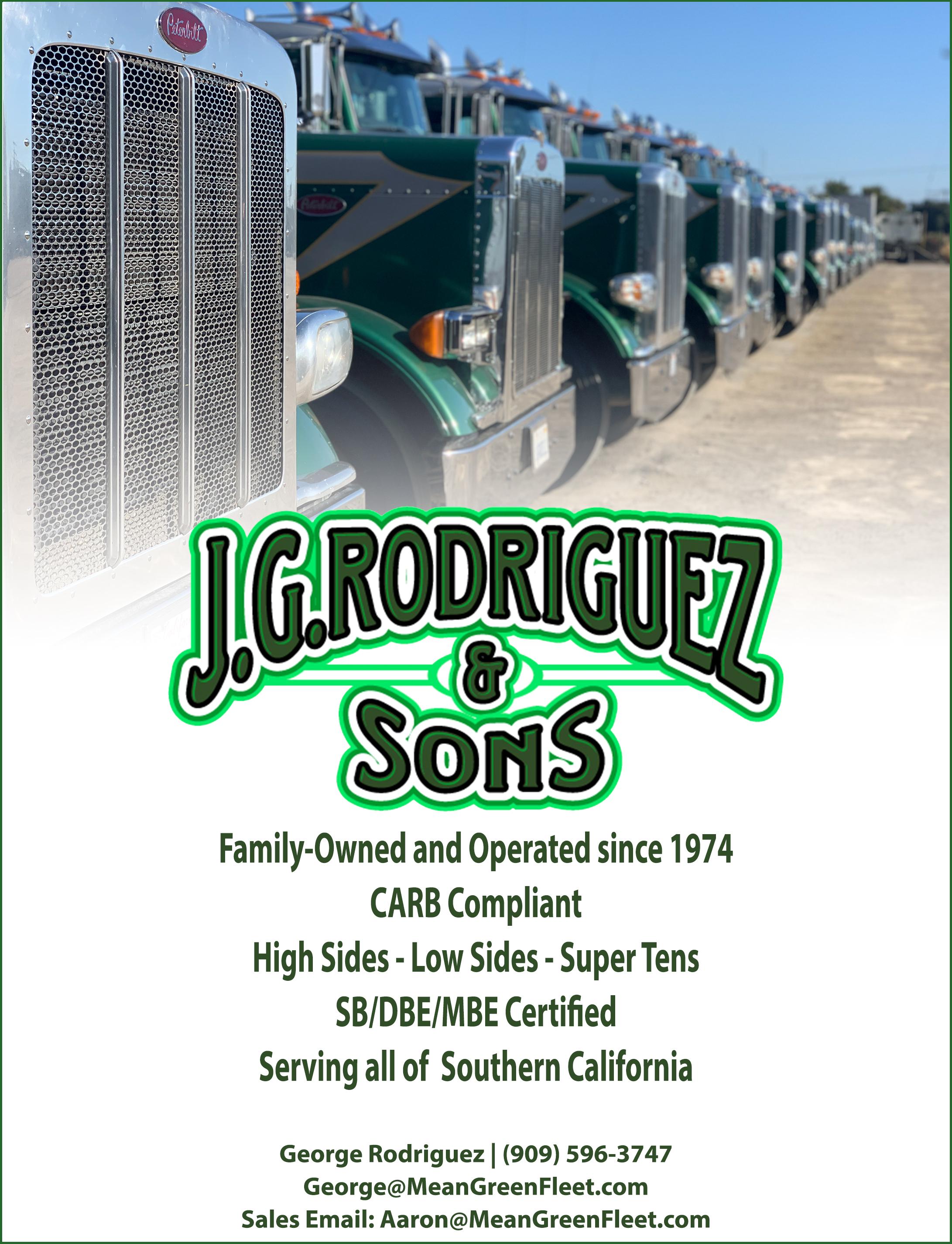
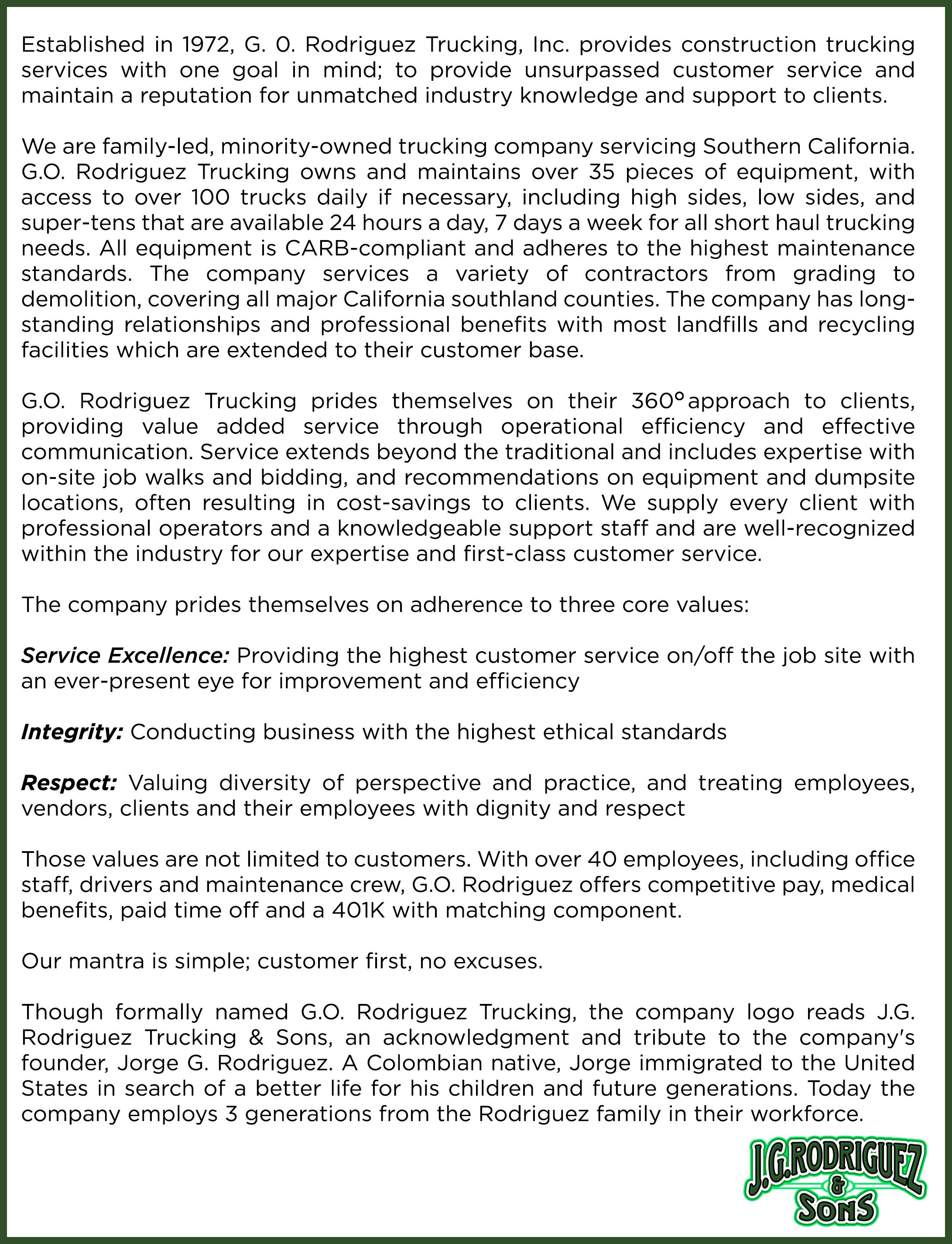
Day To Day
Pennor views himself as a “hands-on” manager. He doesn’t have an office and works side-byside with his team in the cubicles, also known as the AMPCO Bullpen, every day.
“That’s as hands-on as it gets. We meet on Monday mornings to go over what we’re doing for the week, raising potential issues, answering questions, and coming up with solutions. We have a team of 10 Estimators that bid various jobs throughout the state and out of state and we have our own custom CRM (Customer Relationship Management) that we have developed over the last two years,” he says of the technology that is evolving into a CRM and ERP (Enterprise Resource Planning) tool.
The primary challenge facing the industry in California is securing permits in a timely fashion. COVID-19 has slowed the process to a crawl.
“The financing is there but it’s really just a hold-up with the cities – they’re shut down and we’re missing permits. The process in LA was like 30-45 days and now it’s more like three months. It all has to do with COVID because nobody’s working in the office and I don’t think much will change during the next six months,” Pennor observes.
AMPCO worked remotely for approximately the first eight months of the pandemic.
“For a company of our size it’s probably uncommon to have your own IT guy but we have one so Estimating, Project Managing was done from home. But we’ve started to come back into the office and have been able to get some more efficiencies from working together as a team,” Pennor says.
In regards to vendors, Pennor identifies Volvo and Rodriguez Trucking as “our go-to guys.”
“It’s about the people and I think we’ve done pretty well bringing the right people on board. People make the “ company, not the equipment, even in this day and age of how well-connected we are with Social Media.” - Andrew Pennor, President
“It comes down to price and service. Volvo isn’t the lowest but they provide all the equipment, the attachments and the specific requirements we need to run machines for our trade. Rodriguez Trucking is a very good vendor. They provide high-side and low-side service for C&D disposal of concrete, asphalt and other materials,” Pennor says.
Looking Ahead
Despite the looming specter of COVID, Pennor still likes the company’s overall position.
“I’m hoping we can come out of this and still have a couple of years with a good economy. It’s about the people and I think we’ve done pretty well bringing the right people on board. People make the company, not the equipment. Even in this day and age of how well-connected we are with Social Media, it’s still about the people,” Pennor concludes. “And speeding up the permits would help a lot.”
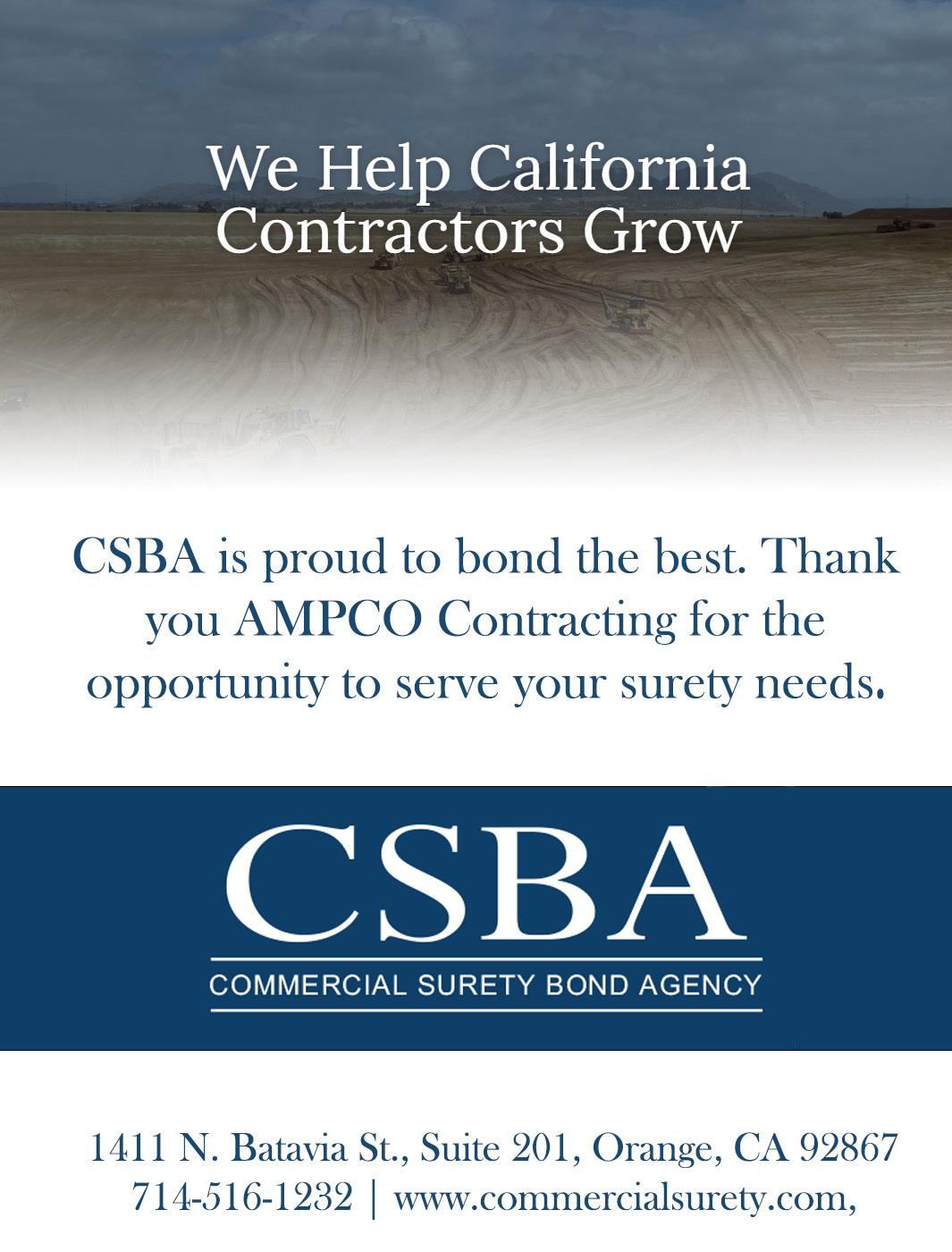
COMPANY INFORMATION
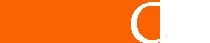
Company Name:
AMPCO Contracting
Country: United States
Industry: Construction
Est: 2004
Premier Services: Provider of
pre-construction services such as
site demolition, abatement and
earthwork.
President: Andrew Pennor
Website:
www.ampcocontracting.com