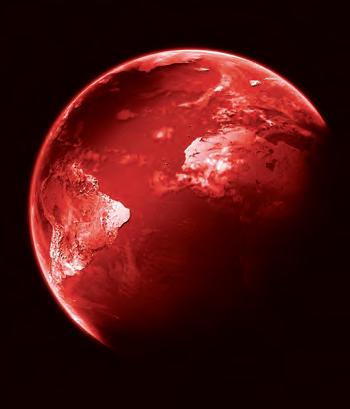
4 minute read
Hero Bennett on carbon reduction
Hero Bennett Max Fordham
Scaling up retrofit for net zero
Advertisement
Now is the moment to create a national market for industrialised retrofit, says Richard McWilliams
Time to declare
MORE CONTRACTORS SHOULD JOIN THE ‘CONSTRUCTION DECLARES’ INITIATIVE ON CARBON REDUCTION, SAYS HERO BENNETT
Industry action can influence global CO2 emissions
The covid crisis has shifted attention from
the biggest risks we face: climate change and biodiversity loss. But the issue hasn’t gone away. Globally we have less than 10 years to halve CO2 emissions. Business as usual is no longer an option.
As an industry the mood is changing, with the Construction Declares movement on the climate and biodiversity emergency launching in 2019 and being supported by architects, building services and structural engineers. Signatories agree to advocate faster change, share knowledge and evaluate all new projects against the aim to contribute positively to mitigate climate and biodiversity breakdown.
After a delay, contractors are now stepping forward to acknowledge the crisis, with BAM, Morgan Sindall, Sir Robert McAlpine, Skanska and Willmott Dixon among the founding members of UK Contractors Declare. But 36 signatories compares poorly with over 1,000 architects.
Personal experience suggests contractors are less knowledgeable about the risks posed by climate change, which include systemic risks to their operations and supply chains. Yet the contractor’s role is significant. The quality of construction on site can be a key component of reducing the ‘energy performance gap’ seen between the designed energy and actual building operational energy consumption.
For example, the quality control process employed on a Passivhaus construction site virtually eliminates unexpected heat loss. Experienced Passivhaus constructors have acknowledged how much they have learned through their Passivhaus projects and that the required processes can reduce a project’s overall risks and associated costs.
Contractors’ influence
Contractors can also significantly influence a building’s embodied carbon, sometimes convincing a client to switch from a low-carbon to a high-carbon product once on board, where cost and construction familiarity is more of a priority than environmental impact. Concrete usually has the most significant embodied carbon impact in a building, though encouragingly, more contractors are becoming comfortable with using low carbon forms of concrete through cement replacements. Contractors can use their close ties with their supply chains to influence behaviour, requiring data on embodied carbon and selecting greener or locally sourced products.
Contractors Declare is a positive movement that I hope will grow and benefit the industry as a whole. We have less than 10 years to make a sizeable dent in the CO2 emissions our industry is responsible for and every one of us has a role to play. ●
Hero Bennett is principal sustainability consultant at Max Fordham and a member of the CIOB sustainability special interest group.
The government’s recent launch of £3bn worth of schemes to help retrofit buildings is a welcome acknowledgment of the climate emergency, the challenge of meeting our net zero targets, and the need to drive economic recovery.
Nonetheless, the focus on job creation, via direct funding for retrofit measures, could undermine the long-term market for industrialised retrofit. Britain has Europe’s oldest housing stock and 80% of buildings that need to achieve net zero have already been built. Retrofit on this scale is not currently within the capacity of the market.
The pandemic provided a unique opportunity to reset the economy and spearhead a green recovery. This will not be achieved under the government’s current policy for residential property, which focuses on loft and wall insulation, new windows or boilers, and one-off heat pumps within ageing buildings. Piecemeal measures like this only scratch the surface.
Instead, we need to create a market for industrialised retrofit that delivers guaranteed performance based on outcomes including warmth, hot water and the wellbeing of occupiers. This can then be packaged up as an investable proposition, creating a longterm funding mechanism with a contractual agreement to deliver homes and buildings that are energy efficient.
This model has already been demonstrated in the UK. In London, Turner & Townsend is the lead delivery partner for the Greater London Authority’s (GLA) Retrofit Accelerator programmes, which have enabled investment in homes and workplaces for over a decade.
The new Innovation Partnership, for wholehouse retrofit, will bring together the GLA, housing providers and suppliers to develop innovative solutions that make an economic price point achievable for performanceassured net zero retrofit. Such a strategy, if rolled out nationwide, requires a local network of contractors and manufacturers. This creates an early-mover advantage for regional authorities looking to build their green economies through long-term jobs that deliver and maintain retrofitted buildings.
This model could give a £400bn-600bn domestic market, with the potential to export the UK’s knowledge and expertise. With national and local government support, there is real scope to create a supply chain for industrial retrofit at scale.
Richard McWilliams is director, sustainability at Turner & Townsend.