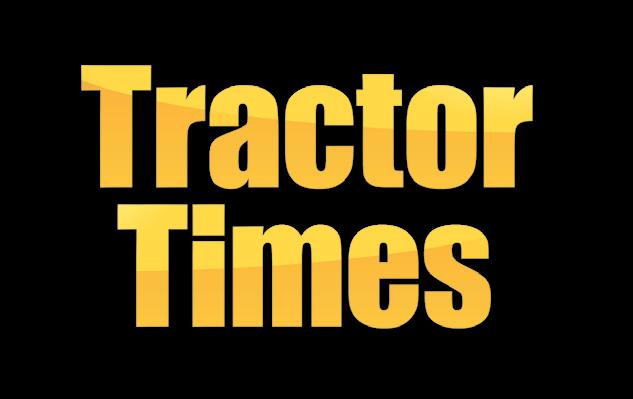


Stay aware of service
Dear Valued Customer:
I hope your year is going well. As you move further into the busy construction season, it can be easy to focus on production and lose sight of maintaining your machines. TEC’s Planned Maintenance Department is here to help support those efforts.
Your newer Komatsu machines are covered for scheduled services for 2,000 hours or three years with Komatsu Care. Our skilled technicians will perform the services on-site, at your convenience. We can also service your older machines and nearly all of your non-Komatsu products. Reach out to your local service department, product support representative, territory manager or branch to learn more about the service plans that we offer and to schedule a service.
One way you can ensure you are keeping up with scheduled services is by utilizing your My Komatsu account. Komatsu’s digital hub lets you monitor your entire fleet — even non-Komatsu machinery that is registered in My Komatsu — from the convenience of your office, home or other locations. Read more about this efficient fleet management system inside this issue. If you don’t have a My Komatsu account, contact us for information about setting one up.
This issue also highlights the many industries that Komatsu serves. Check out the valuable articles on equipment for forestry, demolition and construction. Do you need to log on steep and soft ground? The 951XC is a good choice. Do you want to efficiently do more high-reach demolition? The PC490HRD-11 with a K100 boom change system lets you do boom changes quickly from the cab and reach up to 105 feet.
Do you want a productive fleet of construction machinery? Komatsu showcased several great machines during its recent Demo Days event, including the highly efficient HB365LC-3 hybrid excavator.
If you’re looking for parts, consider Komatsu Reman. Its parts and components deliver like-new performance with a great warranty, provide significant cost savings and contribute to sustainability.
As always, if there is anything we can do for you, please feel free to call or stop by one of our 20 locations.
Sincerely,
Chad Stracener CEO
Gordy Construction Company Inc. pg. 4
Meet Schley Gordy, whose business serves the Columbus, Ga., area.
Guntersville Marine Inc. pg. 8
Discover which machines are crucial to the company’s operations.
Technician Training pg. 13
Read about TEC’s Apprentice Program.
Improved Fleet Management pg. 15
Learn about My Komatsu.
Open House pg. 17
See TEC’s new full-service facility in Huntsville, Ala.
Hands-on Happening pg. 18
Explore Komatsu’s Demo Days.
Demolition Demonstration pg. 20
Find out what equipment was displayed at the NDA showcase.
Reaching Higher pg. 23
Look at Komatsu’s PC490HRD-11 high-reach demolition excavator.
New Milling Machine pg. 24
View the new WIRTGEN W 150 Fi compact milling machine.
Life Cycle Solutions pg. 27
Promote profitability and sustainability with remanufactured parts.
Guest Opinion pg. 28
Follow the advice of Safety Director Ronnie Freeman.
OnTrack pg. 29
Get a glimpse of Komatsu’s partnership with Williams Racing.
Birmingham, AL (205) 591-2131
Tuscaloosa, AL (205) 752-0621 (800) 582-4625
Anniston, AL (256) 831-2440
Alabaster, AL (205) 621-2489
Dothan, AL (334) 678-1832
Huntsville, AL (256) 851-2222
Chad Stracener, Chairman/CEO
DeVaughn Pettit, President
Jeremy Tolbert, Executive V.P./General Manager – Product Support
Brett Bussman, Senior V.P./General Manager – AL
Jamie Steele, V.P./CFO
Joe Patton, V.P./Regional Sales Manager – AL
Autrey McMillan, V.P./Regional Sales Manager – AL & FL
Tony Daughtry, V.P./Regional Sales Manager – GA
Andrew Pettit, V.P./Regional Sales Manager – GA
Mike Burkes, V.P., Service – AL & FL
Brian Holder, V.P., Service – GA
Greg Carroll, V.P., Sales-Major Accounts – GA
Chris Lucas, V.P., Information Technology
Chris Kohlenberg, Director of Parts Operations
Copeland Bush, Director of Product Support – AL & FL
Russ Lane, Director of Product Support – GA
Ben Osborn, Director of Product Support-Major Accounts – AL
Jim Hensley, Director of Product Support-Major Accounts – GA
Travis Howell, Director of Wirtgen Group Products
Mark Shoults, Manager of Used Parts
Tim Thomas, Used Equipment Manager
John Pierce, New Equipment Rental Manager
Birmingham
Shay Holliday, Branch Manager
Bert Suttle, Service Manager
Tim Woods, Parts Manager
Tuscaloosa
Jody Thomason, Branch Manager
Keith Watkins, Service Manager
Matt Tolbert, Parts Manager
Anniston
Alan Preston, Branch Manager
Will Hurst, Service Manager
Buck Brown, Parts Manager
Decatur
Zach Thomas, Branch Manager
T.J. Smith, Service Manager
Shawn Pewitt, Parts Manager
Huntsville
Daniel Kent, Service Manager
Jann Patterson, Parts Manager
Panama
Dothan
Chuck Tibbets, V.P./Branch Manager
Christopher Simer, Service Supervisor
Drew Bronson, Parts Manager
Alabaster
Randy Hawkins, Branch Manager
Jake Osborn, Parts Manager
Montgomery
Andy Huggins, Branch Manager
Steven Blake, Service Manager
Brad Hubbard, Parts Manager
Mobile
Chris Howard, Branch Manager
Robert Bush, Service Manager
Jacob Packard, Parts Manager
Renew Center
Gerald Blakey, Service Manager
Chuck Tibbets, V.P./Branch Manager
Montgomery, AL (334) 288-6580 (800) 832-9563
Decatur, AL (256) 355-0305
Mobile, AL (251) 457-8991 (800) 233-7213
Panama City, FL (850) 763-4654 (800) 342-2055
Pensacola, FL (850) 505-0550
Forest Park, GA
(Atlanta)
(404) 366-0693 (800) 488-0693
Calhoun, GA (706) 879-6200 (800) 827-3072
Macon, GA (478) 745-6891 (800) 786-3120
Columbus, GA (706) 562-1801
Hoschton, GA (706) 654-9850 (888) 334-9850
Kennesaw, GA (678) 354-5533
Augusta, GA (706) 798-7777 (800) 659-3090
Savannah, GA (912) 330-7500 (800) 827-1405
Albany, GA (229) 435-0982 (800) 733-0982
FFor over a century, one construction company has provided consistent services for Columbus, Ga., and the surrounding area.
Gordy Construction Company Inc., founded in 1923 by Schley Gordy’s great-grandfather and namesake, has been a cornerstone in the community, specializing in pipeline, water and sewer projects. This fourth-generation family business has thrived by providing consistent, reliable services for its customers.
Schley Gordy, the current president, started working at the company after graduating college.
“At first, I wasn’t sure about my path, but once I joined, I dove headfirst into the work,” Gordy recalled. “Starting as a laborer in 1998, I quickly found my passion in this field and worked my way up to where I am today.”
Over the years, Gordy Construction Company has kept a consistent workforce size of approximately 30 employees, focusing on quality over quantity.
“The company hasn’t grown much in size, but we’ve maintained a steady pace, focusing
on our capacity to manage multiple projects efficiently,” Gordy commented.
Gordy Construction Company’s operational scope covers a 150-mile radius around Columbus. Annually, the firm manages between 15 to 20 projects split between three to four crews. This strategic limitation allows for a concentrated focus on each project, ensuring high-quality results and maintaining strong community ties.
“We handle a mixture of municipal and private sector projects,” Gordy elaborated. “Recently, we’ve been involved in a lot of road projects, relocating utilities for road widenings, running sewer outfall lines through forests, and installing sewer and water systems for new subdivisions.”
Gordy Construction Company’s choice of equipment plays a pivotal role, with the firm relying heavily on a fleet of specialized machinery tailored to its typical job site needs.
“We operate seven or eight excavators, from owning larger excavators like the Komatsu PC490 down to owning more compact machines like the PC45 tight tail swing excavator,” explained Gordy. “They are crucial for our trenching work, which involves laying down water lines, sewer lines and storm sewers.”
In addition to the PC45MR, Gordy Construction Company utilizes several other Komatsu tight tail swing excavators, including PC138USLC, PC238USLC and PC308USLC models.
“The tight tail swing excavators are essential for our work, especially when we’re operating next to utility poles, fences or traffic lanes,” declared Gordy. “These excavators allow us to maneuver in limited spaces without the risk of damaging surrounding structures.”
To further enhance its operational efficiency, Gordy Construction Company has embraced advanced technology and recently acquired a Komatsu PC390LCi Intelligent Machine Control (IMC) 2.0 excavator.
“The machine displays construction plans over real-time location and depth data directly on
the machine’s monitor,” stated Gordy. “This has been instrumental in improving precision, reducing over-digging, and minimizing the need for laborers in the trench.”
Gordy Construction Company’s fleet also includes five Komatsu wheel loaders, ranging in size from the WA270 to the WA320, which are essential for material transportation on-site.
“Our wheel loaders are primarily used for hauling gravel and pipes,” noted Gordy. “Their versatility, reliability and minimal maintenance issues have significantly contributed to maintaining our project schedules.”
This integration of traditional business operations with IMC technology reflects Gordy Construction Company’s commitment to maintaining a balance between proven methods and innovative solutions, ensuring that the firm remains at the forefront of the construction industry for another 100 years.
Gordy Construction Company’s strategic integration of innovative solutions is due in large part to the relationship with its equipment distributor, Tractor & Equipment Company (TEC). This partnership, which has helped Gordy Construction Company find the right equipment for its projects over the years, has grown beyond the traditional support from a dealership.
“Our decision to consistently choose Komatsu is largely due to our sales rep at TEC, Jon Lake,” stated Gordy. “He ensures top-notch service, whether it’s routine maintenance or urgent needs, and I know I can rely on him and the team at TEC’s shop to promptly answer the call and any questions.”
‘We’re
Gordy Construction Company also utilizes Komtrax and My Komatsu, which are digital tools provided by TEC and Komatsu that offer crucial real-time data on machinery.
“These systems are invaluable to us,” Gordy declared. “They allow us to track machine hours, idle time and locations efficiently and in real time. We’ve even managed to recover stolen equipment using this technology, which shows just how critical it is to our day-to-day operations.”
As Gordy Construction Company looks to the future, it is setting its sights on maintaining a balance between embracing technological advancements and preserving its operational scale. Gordy Construction Company has articulated a clear vision of weaving emerging technologies into the fabric of its business operations without expanding the company size beyond its current efficient structure.
“We want to keep up with emerging technology, whatever that may be in the future,” commented Gordy. “Maintaining our current size while integrating new tech is key to staying efficient. This strategy will allow us to continue tackling our projects head-on, ensuring we not only meet but exceed our goals. We’re here to help anyone who needs us.” ■
*The opinions expressed here are from the end user as quoted. The results described herein are those of these end users under certain conditions. Individual results may vary.
SSituated along a pivotal juncture of the Tennessee River, Guntersville Marine Inc. has added to the growth and development of inland waterway commerce in the United States since its inception in 1985. Over the last four decades, the port has evolved into a crucial node in the supply chain, particularly for the agricultural and energy sectors.
President Mike Lueken shared, “Guntersville Marine has been a strategic part of our operations under General Marine Holdings since 1989. With facilities that cater to a range of needs from stevedoring to full-service terminal operations, we’re more than just a point in the supply chain; we’re a critical facilitator of commerce and logistics.”
Located at mile 358 on the Tennessee River in Guntersville, Ala., Guntersville Marine operates as a comprehensive harbor terminal. The facility’s strategic location allows for the efficient handling of a variety of goods, especially agricultural commodities like corn and soybeans, which are pivotal to the region’s economy.
Facilities Manager Lance Joyner elaborated, “We’re positioned at the southernmost navigable part of the Tennessee River, which is essential for the poultry industry in North Alabama. This position allows us to serve as a vital link, supporting local industries with necessary commodities. In addition to agricultural products, we handle coal coke for steel mills and other bulk commodities such as phosphate and salt. We have the capability to unload up to five barges simultaneously at our docks.”
Through the years, Guntersville Marine has adapted to the shifting demands of the market. From handling wood flooring in the ‘80s to focusing on the poultry industry today, the facility continues to support and grow alongside the industries it serves, proving to be an indispensable part of the regional economy.
As Guntersville Marine continues to grow, the addition of advanced equipment such as Sennebogen 860 E and 870 E hybrid material handlers has become crucial to its operations. These machines, heralded for their efficiency and environmental benefits, underscore the facility’s commitment to innovation and sustainability.
“The integration of Sennebogen machines into our operations has been a game-changer,” Joyner noted. “Specifically, the Sennebogen 860 E — the first hybrid of its kind in the United States — and the more recent Sennebogen 870 E have significantly enhanced our handling capabilities and reduced our environmental footprint. These machines not only deliver exceptional performance but also align perfectly with our sustainability objectives.”
Guntersville Marine’s Sennebogen hybrid material handlers are each equipped with a 5-yard bucket and are primarily used to transfer grain and aggregates from barges directly to trucks. This method minimizes spillage and loss, proving essential for operational efficiency. Additional attachments, such as a C-hook and a 60-inch magnet, broaden the range of materials that
can be handled, from rail ties to pig iron and various alloys.
“Their reach and strength enable them to handle heavy loads efficiently, which is crucial for our diverse cargo needs,” Joyner explained. “These hybrid machines are designed to withstand the demands of heavy lifting without the usual wear on hydraulic systems. This design not only extends the life of the machines but also cuts down on fuel consumption, which is a significant cost-saver for us.”
Joyner added, “These machines will also track up and down the dock, so we can do multiple barges with one machine.”
Purchasing and Safety Officer Cody Burgess appreciates that the hybrid material handlers are easy to maintain and have top-notch safety features.
“Transitioning from older models to these modern Sennebogens has elevated our safety standards,” Burgess stated. “They’re not just powerful — they’re also cleaner and easier to maintain, which is crucial for both safety and environmental responsibility.”
In addition to the Sennebogen machines, the firm relies on several Komatsu wheel loaders,
including a WA320 that is used to handle a variety of tasks around the dock. Its quick coupler system allows for fast attachment changes, increasing the flexibility and speed of operations.
“The Komatsu WA320 is indispensable for day-to-day operations, providing the agility and reliability we need to maintain a seamless workflow,” said Joyner. “Once the machine came onto our facility, it never left. We also have four WA500 models that are used for moving mass amounts of material, and our two WA200 models typically move about 250 tons a day loading trucks and moving material.”
Strategic partnership
Guntersville Marine’s relationship with its distributor, Tractor & Equipment Company (TEC), plays a pivotal role in its operations. The partnership extends beyond simple purchasing transactions to integral support essential for Guntersville Marine’s success. The firm has built close ties with sales representative Conner Bussman and Decatur Branch Manager Don Burgreen.
“Our partnership with TEC began in 1999, sparked by a crisis when one of our wheel loaders failed,” reflected Joyner. “We acquired a WA320 from TEC, and it became a turning
‘Our relationship with TEC is absolutely amazing’
point in our relationship and business. Since then, our partnership has only strengthened and shapes the current operational capabilities of Guntersville Marine.”
Joyner elaborated, “Machine reliability has been phenomenal, largely due to TEC’s lube services, which significantly reduce our downtime. The support we receive is not just technical but also personal — we truly feel like part of their family. This camaraderie extends beyond work, enhancing our professional interactions and support experience. Our relationship with TEC is absolutely amazing.”
Burgess commented on the logistical benefits of partnering with TEC, stating, “Working with TEC means having access to rapid response and maintenance expertise across several branches. This is crucial because downtime here directly impacts our bottom line. Whether it’s parts from Huntsville or maintenance from Birmingham, help is just a phone call away, and that’s invaluable.”
Through strategic partnerships with distributors like TEC, Guntersville Marine can leverage strong support networks to maintain high operational standards, maximize uptime, and continue growing its business. As the company eyes future expansions, integrating operations across multiple states remains a key strategy.
“We’re actively integrating our operations from Washington Park, Illinois, to Tampa, Florida, and enhancing our services in Guntersville,” Lueken explained. “By aligning similar bulk commodity handling and adding value through customized packaging, we’re setting up northern Alabama as a strategic distribution hub. This positions us well to capitalize on growth opportunities and support regional industrial expansion.”
With a robust growth rate over the past four years, Guntersville Marine looks to further its positive trajectory with versatile equipment like the Sennebogen 870 E, which promises broader applications and improved operational efficiency. This forward-thinking approach emphasizes the company’s commitment to not only meet current demands but also adapt to future market needs, ensuring sustained growth and regional economic contributions. ■
*The opinions expressed here are from the end user as quoted. The results described herein are those of these end users under certain conditions. Individual results may vary.
You trust SENNEBOGEN for the best in productivity, safety, and efficiency. Now think “beyond the machine” with life-long SENNEBOGEN service.
•Expert application support
•Local in-stock parts
•Factory-trained technicians
•Free technical training
•Prepackaged service kits
•Lease-by-the-Hour® financing
Maximize productivity on your job sites with advanced automation technology. Komatsu’s Intelligent Machine Control (IMC) can help you get the most from your machines, crew and carefully designed plans.
•Get new operators up to speed quickly
• Go from mass excavating to finished grading faster than ever
•Helps eliminate potential damage to design surface
• Empower operators to work efficiently, pass after pass
TTractor & Equipment Company's Apprentice Program provides specialized training to build upon the foundational skills gained by working in TEC's service department. The program focuses on accelerating the understanding and troubleshooting of hydraulic, electrical and A/C systems, thereby maximizing the technicians’ knowledge and efficiency within TEC’s operations. While gaining hands-on experience at one of TEC's 20 locations, participants will attend the Apprentice Program at TEC's Training & Education Center in Birmingham, Ala., one week per month over 12 months.
After completing the Apprentice Program, the technicians will continue their professional development with ongoing Manufacturer Training throughout their careers. This comprehensive approach ensures that TEC's technicians remain highly skilled and up to date with industry advancements. ■
Have you seen what’s new in My Komatsu?
We’ve made some exciting changes! An all-new mobile app, simplified ordering through the Online Parts Store, Komatsu Care Program (KCP) integration and more have been added to enhance the My Komatsu user experience.
Log in to your My Komatsu account to see the full range of new features. Don’t have a My Komatsu account? Go to mykomatsu.komatsu to sign up.
fleet? No problem. My Komatsu gives you the ability to manage it in one
Do you want an easy way to track telematics data from your mixed fleet? My Komatsu, Komatsu’s comprehensive digital hub, gives you an efficient way to monitor all of your assets in one complimentary fleet management tool that gives users machine-specific views for utilization and health and production information without the need for multiple user IDs and passwords.
With ISO 15143-3 API integration, My Komatsu can pull data from Komtrax and ISO API 15143-3 (AEMP 2.0) information from other original equipment manufacturers (OEMs), using the ISO feed to import numerous key data points defined by the Association of Equipment Management Professionals. You can quickly view and manage information on one dashboard, receive alerts and order parts, troubleshoot to help minimize downtime, monitor machine location, benchmark performance, track fuel consumption, and manage fuel efficiency.
“It’s a huge benefit in time and cost savings that you can monitor an entire fleet on a single platform, regardless of OEM,” said Tommy Hergenreder, North American Manager, Digital Product, Komatsu. “Another is that Komatsu
doesn’t charge for connecting other APIs, which some OEMs do. Currently, there is a long list of other manufacturers that you can get API credentials for, and it’s growing all the time.”
The first step to adding non-Komatsu machines is obtaining API credentials from your OEM representative. Once you have those, log into your My Komatsu account and follow these steps:
• Click on the My Fleet page
• Navigate to the Other OEM Configuration screen and click the +Add OEM Configuration button
• Enter your credential information
• Test the connection
• Save your API (a green confirmation text box will indicate that you saved successfully)
“One API credential from the OEM covers all of the manufacturers’ machines that you may have and want to input into your My Fleet page on My Komatsu,” said Andrew Casey, Digital Solutions Analyst, Komatsu. “This is a very cost-effective, convenient solution to managing a mixed fleet without any additional cost to implement My Komatsu.” ■
My Komatsu lets you access telematics data from non-Komatsu OEMs with an ISO 15143-3 API integration. You can import numerous key data points and quickly view and manage your mixed fleet on one dashboard.
TTractor & Equipment Company (TEC) recently opened a new full-service facility in Huntsville, Ala., that customers and vendors were able to explore during an open house event.
TEC has operated a full-service operation in Decatur, Ala., and maintained a parts-only location in Huntsville for several years. The decision to upgrade the Huntsville location to a full-service branch was driven by the area’s growth and the increasing needs of its customer base.
Chris Kohlenberg, Director of Parts Operations at TEC, highlighted the importance of this expansion.
"TEC is a product support-focused company,” said Kohlenberg. “Taking care of our customers is our number one priority, and in order to be able to serve our customers to the highest potential, it was imperative to have a full-service facility.”
The upgraded Huntsville location boasts a 10-bay shop capable of performing any necessary repairs and services on equipment. The facility also has sales desks, a service desk, a parts warehouse, and a storefront with a range of basic shop supplies. This expansion aims to transform the location into a one-stop shop for customers.
“Our inventory is diverse, and we are excited to highlight our state-of-the-art hose shop, where we are able to build hydraulic hoses for any make or model of machine,” commented Kohlenberg. “We are stocking numerous products in our lobby
and warehouse that are vital to our customers' operations, including DEF, batteries, rubber tracks, teeth, blades, and much more.”
The open house provided an opportunity for clients to tour the new facility and see the capabilities of the enhanced Huntsville branch. More than 400 customers attended the event, which was a testament to the strong community and relationships TEC has built.
“We are proud to host this event and welcome our customers to the new full-service facility,” said Kohlenberg. “The turnout was incredible, and we appreciate all of those who were able to take time out of their day to join us in celebrating the grand opening.” ■
LLearning about what equipment can do provides valuable insights into how it can help your operations. The ability to experience a machine for yourself from the operator’s seat takes it to another level. Komatsu gave attendees opportunities to do both during its recent Demo Days event at its Cartersville Customer Center in Georgia.
More than 30 products were available for customers to see up close and operate, ranging from compact excavators to large construction, demolition, forestry and mining machines. Representatives from Komatsu and Komatsu affiliates Montabert, Lehnhoff and Hensley Industries provided insight on how to effectively implement the equipment and attachments into attendees’ operations.
Komatsu Smart Construction and Smart Quarry representatives had display areas set up to provide information on solutions available for job site management such as Smart Construction Remote, Office, Field and Drone, as well as Smart Quarry Site and Smart Quarry Study. My Komatsu representatives provided information about Komatsu’s central hub for fleet management.
“What we’re hoping our customers take away is our dedication to them and their business,” said Andrew Earing, Director of Operator and Technical Training at Komatsu’s Cartersville Customer Center. “We have more than 100 Komatsu employees here, ranging from service engineers to product management, to answer questions and listen to customers in an effort to learn more about their needs and how Komatsu can help them improve their job site efficiencies.”
Each day began with informative presentations about equipment, Smart Construction solutions and Smart Quarry solutions that Komatsu offers to increase productivity, efficiency and sustainability. Hands-on operation followed, letting customers operate a mix of standard and Intelligent Machine Control (IMC) equipment in working environments on the 38-acre site.
“It’s neat to see all the yellow iron together, from motor graders to dozers to excavators, loaders and the intelligent machines,” said Eli McDonald, Equipment Coordinator for Reece Albert Inc. and CSA Materials Inc. in San Angelo, Texas. “It’s rare to see this many assets in one spot. I hope to take away the knowledge to go back and reassess our fleet and improve our operations.”
IMC 2.0 dozers ranging from the D39EXi-24 to the D71PXi-24 and IMC 2.0 excavators ranging from the PC210LCi-11 to the PC490LCi-11 — all of which are equipped with factory-integrated GPS machine control — were highly popular during the event. Customers could also operate a PC138USLC-11 with 3D Machine Guidance, a Smart Construction solution that brings 3D to most conventional excavators and gives operators in the field and managers in the office access to 3D design and topography data that helps drive accuracy.
“Our big excavators are 90% Komatsu, including IMC machines, and we also have IMC dozers,” said Dan Earley, a co-owner of LEi in Rapid City, S.D., noting that his company also uses Komatsu’s Smart Construction Office and Dashboard. “It makes my operators way more efficient. There’s so much data in there we can collect and see where production is on a daily basis. Now, with Office and Dashboard, we can see in real time what was done that day. Did we get enough moved? The information is invaluable. I appreciate coming down here and getting to run what we want. I hope to keep coming back. This is a great event.”
Hybrid highlight
Komatsu also featured its HB365LC-3 hybrid excavator that delivers eco-conscious performance as energy is captured during swing and stored in the ultracapacitor. When swinging, all available hydraulic power is sent to the boom,
arm and bucket for improved cycle time, reduced fuel consumption and increased production.
“It seemed like it was stronger on the swing and something that I think we would really like in our company,” said Troy Henderson, a part owner of KTA Construction in San Diego. “Being in California with the emissions that we have to deal with, the hybrid is a great choice to improve our fleet and reduce emissions.”
Harry Olsen, the chief operating officer and a co-owner of Hugo Tree, a company that does land clearing, sitework and demolition in Hugo, Minn., commented, “With the hybrid specifically, I really like that the fuel consumption has dropped down. I think one of the things Komatsu’s always done really well is made a very efficient, smooth machine, and I think the hybrid is the next evolution. We do a lot of stacking and material handling, so being able to have that very finite swing is nice. It’s efficient.”
Additionally, there were demonstrations of Komatsu’s new PC490HRD-11 high-reach demolition excavator equipped with a K100 boom change system that allows for hands-free boom changes from the cab of the machine, as well as a soon-to-be-available Komatsu PC360LC-11 straight boom demolition machine. Attendees could also check out demonstrations of Komatsu’s Smart Construction Drone and Komatsu’s RF-5 reclaim feeder.
“One of things we are proud of here is we let customers get in the equipment, touch the quality, feel the performance and get the full experience of our product, but Demo Days
is about more than that,” stated Earing. “It’s an opportunity for both us and our customers to learn more about each other. It’s a great platform and venue to connect with our customers and truly understand their needs.” ■
*The opinions expressed here are from the end user as quoted. The results described herein are those of these end users under certain conditions. Individual results may vary.
AAt the annual National Demolition Association (NDA) show, attendees could test out Lehnhoff and Montabert products during the event’s live demonstration, as well as talk to their manufacturing representatives. Both Lehnhoff and Montabert are Komatsu-owned companies.
Lehnhoff’s new SQ80V fully automatic symmetric quick coupler was popular at the show. It connects an attachment to an
An attendee operates a Komatsu PC360LC-11 excavator with a straight boom that is equipped with a Lehnhoff SQ80V fully automatic symmetric quick coupler and a Montabert HCP 1000-R pulverizer.
excavator in the same way as a hydraulic line — without the need to disconnect and reconnect a hose. Operators can make the connection from the cab of an 8-ton to a 70-ton machine.
“Time savings and increased productivity are big advantages with the SQ80V,” stated Simon Maurath, a sales representative for Lehnhoff.
“It’s a matter of seconds compared to minutes or hours because there are no hoses or pins to connect. It is a great match for a demolition machine that comes plumbed for a coupler. With the proper kit, it can also be added to a standard excavator to increase its versatility.”
Lehnhoff also displayed an HTL35 HD-1500 heavy-duty backhoe bucket, which features a double-conical design to enhance digging performance for efficient loading and dumping tasks.
During the event, the SQ80V was mounted on a Komatsu PC360LC-11 excavator with a straight boom, so attendees were able to quickly switch out and test the various Montabert attachments that were on-site, including a V46 hydraulic breaker with automatic variable speed technology that senses changes in material hardness and adjusts the impact energy and the striking rate; an HCP 1000-R pulverizer with a heavy-duty steel body designed to enhance durability; an HCM 750-C multiprocessor with interlocking jaws that break and crush material rather than compress it; and an HCG 32-1200 grapple with 360-degree continuous rotation for enhanced positioning.
“One of the highlights of the Lehnhoff and Montabert products is that they are suited for all types of machines and all brands,” commented Montabert Sales Engineer Michelle Wilson.
In addition to the attachments that were available for attendees to operate, Montabert displayed its HCM-C 700 multiprocessor with 360-degree rotation and an HCG 23-700 demolition and sorting grapple.
“We want attendees of the demolition show to see what Montabert and Lehnhoff can offer to help their teams work more efficiently,” said Wilson. “We’re a small part of the Komatsu family, which offers us phenomenal resources to research and develop cutting-edge tools.” ■
FFrom hammering to processing to loading, demolition often involves quickly changing tasks. With easy attachment switches and the ability to work at heights of up to 105 feet, Komatsu’s new PC490HRD-11 high-reach demolition excavator helps achieve greater efficiency, according to Matt Buerstetta, North American Product Manager for Demolition Machines, Komatsu.
“The PC490HRD-11 is a highly versatile machine that’s easily reconfigurable for changing work demands and can run a wide variety of attachments, including grapples, hammers, processors and buckets,” said Buerstetta. “One of the biggest advantages is our K100 boom change system that lets operators quickly switch out booms. What would normally have taken up to a day in the past can now be done in a mere fraction of the time.”
The in-house K100 boom change system uses oversized quick connectors for the hydraulic lines that minimize back pressure and oil heating without restricting oil flow. The system also features hydraulically powered pins mounted inside the main boom structure to help reduce the risk of damage to the equipment during reconfiguration. With the K100 system, operators can easily reconfigure the machine from the cab, improving safety, productivity and efficiency.
The PC490HRD-11 has a base weight of 128,199 pounds and a weight of 161,500 pounds with the extended high-reach boom. At full extension,
it can handle a maximum attachment weight of 5,512 pounds. A 360-degree Working Range Indicator system with side stability provides a pre-alert function.
A hydraulically expandable undercarriage enables the tracks to be narrowed for transportation and expanded for working. The tilting demolition cab can be tilted up to 45 degrees and allows the operator to use joysticks to position the cab for an optimal view.
Full demolition guarding helps protect components and keep the PC490HRD-11 running in harsh conditions. It has guards on the revolving frame and undercover, as well as level two window guards for the front and top glass. A dust protection system minimizes dust and debris in the engine and cab.
“The PC490HRD-11 has a heavier counterweight, coming in at about 18 tons, which is bigger than our standard PC490 excavator,” said Buerstetta. “It has been a proven winner in Europe for several years already. We’re excited to bring it to the North American market, and we encourage anyone who has large demolition work and wants a versatile machine that will handle a wide variety of tasks to contact their local distributor.” ■
Model PC490HRD-11
Quick Specs Horsepower 362 hp
Operating Weight 128,199-161,500 lbs.
Maximum Reach 105 ft.
Komatsu’s PC490HRD-11 is a proven demolition machine that can quickly and easily be reconfigured with the K100 boom change system to tackle a wide variety of projects and applications. It offers six working arrangements, with a boom extension for higher reach or extended digging.
WWIRTGEN rounded out the top end of its compact milling machine class with the new high-performance W 150 Fi, which is an ideal choice for use on major construction sites with restricted space such as in inner city locations. Its size — in combination with an intuitive design, digital assistance systems, and the LEVEL PRO ACTIVE leveling system — allow for efficient one-person operation.
The agile front loader has a standard working width of 5 feet and features the latest and currently most eco-friendly engine technology to meet Tier 4 Final standards. The engine offers a maximum rated output of 426 horsepower and has been specially adapted to meet the needs of cold milling applications. Its high torque and simultaneously low noise emissions under all load conditions are impressive. Fuel consumption is low, even when delivering the highest milling performance and at the maximum working depth of 1 foot, 1 inch.
These systems are proven in other F-series cold milling machines, giving users the benefits of higher performance, and thanks to an automatically generated construction site report, clearly structured documentation of all site-relevant data.
In automatic mode, Mill Assist selects the operating strategy with the most favorable balance between milling performance and operating costs, reducing fuel and water consumption, pick wear, and CO2 emissions. Mill Assist controls engine speed automatically according to the needs of the operator. The wide range of possible engine speeds means that the machine’s uses are equally broad. The lower speed range enables a significant reduction of diesel fuel consumption and pick wear. In the upper speed range, an optimum milling pattern can be achieved at higher performance rates.
The WIRTGEN W 150 Fi compact milling machine unites high productivity with the advantages of compact dimensions. It has a standard working width of 5 feet and a working depth of 1 foot, 1 inch.
Operators can select one of three performance strategies: ECO, performance optimized, and milling pattern quality. This makes it possible to predefine the required milling pattern quality incrementally from coarse to very fine at the press of a button.
Mill Assist, WIRTGEN PERFORMANCE TRACKER, and LEVEL PRO ACTIVE assist operating personnel and increase milling efficiency.
The LEVEL PRO ACTIVE leveling system is installed as a standard feature. It has an intuitive operating design and ensures precise milling results. The machine has an improved basic configuration for the integration of 3D and laser leveling systems and a revised Multiplex system with three-fold scanning. All sensors and measurement values are displayed in an easy-to-read format on the control panel in order to maximize process efficiency. Important machine functions are directly interconnected, allowing for a high degree of automation. ■
DDo you want to save money without sacrificing quality and reduce your carbon footprint at the same time? Using remanufactured parts and components could be the answer.
“Fewer raw materials are used in remanufacturing than new parts manufacturing,” said Matt Beinlich, Senior Director, Remanufacturing Business, Komatsu. “According to a paper from the Rochester Institute of Technology titled ‘Capturing Energy and Resources through Remanufacturing,’ the rule of thumb is that 80% of the mass of a component is reused through the remanufacturing process, reducing the need to extract new materials from the earth. Remanufacturing is necessary and good for the industry and the environment because it contributes to sustainability.”
It can also contribute to profitability, Beinlich added.
“Remanufactured components are a much more cost-competitive option compared to new ones because fewer raw materials are required,” Beinlich emphasized. “The quality of genuine Komatsu remanufactured parts and components is better than will-fit items. That’s why we back them with a one-year, unlimited-hours warranty and a quality assurance program of up to 10,000 hours on major components.”
Enhancing availability
Beinlich leads a new team of Komatsu remanufacturing personnel that is committed to increasing customer utilization of reman parts and components. It includes longtime remanufacturing specialists such as Senior Product Manager Goran Zeravica, as well as Remanufacturing General Manager Isamu Hamai, Parts Sales and Marketing Manager Eric Uehara, Reman Procurement Manager Krutarth Desai, Senior Quality Engineer Cody Clark, and Quality Assurance Specialist Bryan Davis.
“When customers buy a Komatsu machine, they expect that those machines will have readily available, reasonably priced, high-quality parts and components necessary to keep them running throughout the machine’s life cycle,” said Zeravica. “Genuine Komatsu remanufactured components can play a significant role in meeting that expectation. Our goals include improving availability and
utilization so that our customers have a better total cost of ownership.”
Zeravica added, “To promote our customers’ success with remanufacturing, we have brought a lot of people together from various parts of the Komatsu family including suppliers, our parts depots and distributors. Ordering reman parts and components will be easier too, as we bring that into the digital age by making them available through My Komatsu.” ■
II’m sure you’ve heard the phrase, “There is no such thing as a stupid question, except the one that didn’t get asked.”
About the Author:
Ronnie Freeman is the safety director for Mount Pleasant (South Carolina) Waterworks and Safety Committee chair for the Water Environmental Association of South Carolina.
Some people have trouble raising their hand and asking the question that’s important to them. Perhaps it’s the possible embarrassment of being the only one who doesn’t know the answer, or it could be that you missed an important point during a discussion and are afraid of looking like you weren’t paying attention. Sometimes other employees may show some frustrations when you ask questions and that can also discourage you from asking. Whatever the reason, we can sometimes talk ourselves out of asking a very important question that could very well be important to our safety.
In our industry many employees face different kinds of hazards on a daily basis — risks such as entering a confined space, operating heavy equipment, digging and working in trenches, handling chemicals, and fall hazards. Part of mitigating those hazards is preplanning and implementing safeguards to protect us from those hazards. Sometimes though, things change, conditions around us change, a new piece of equipment is brought on-site. If employees are afraid to ask questions, they could be putting themselves at risk of injury or even death. When it comes to safety, it’s critical that you ask questions
Encouraging questions can help employees stay safe on the job. The willingness to ask the necessary questions about tasks, risks, hazards and worst-case scenarios helps maintain a good safety culture.
like what could go wrong, how can you prevent it from happening, how do you protect yourself, and what do you do if something does go wrong. By being willing to ask these and other important questions you might be helping your coworkers who may have similar questions.
Also, asking the right questions begins with the willingness to admit you aren’t trained in working certain types of equipment or projects. Sometimes our ego can get in the way of asking questions as we don’t want to be considered the weak link on a work crew. So, we just begin working, putting ourselves at risk. Don’t let this be you. Ask the questions you need to ask.
Don’t let complacency creep in Complacency can creep in when we do the same work tasks over and over again. Workers with experience can easily become complacent and not even recognize the hazards, or they feel like there is less risk because they’ve seen it before. These employees are less likely to ask the questions that can get hazards addressed. If the work environment discourages questions, that just adds to the hazard.
Also, an employee’s lack of knowledge can be a danger too as they might not recognize the hazards that are present. This can come from a lack of training or the employee being too new to the task at hand. They probably will not ask the necessary questions because they simply don’t know what to ask.
Don’t let the responsibility of knowing all the answers fall to them. Encouraging questions can help employees stay safe on the job. The willingness to ask the necessary questions about tasks, risks, hazards and worst-case scenarios helps maintain a good safety culture while on the job.
If you are a supervisor, encourage questions. This is just one simple step, but it can make a difference in improving the overall safety culture at your workplace. ■
Editor’s Note: This article originally appeared as an online exclusive on DigDifferent.com (https:// www.digdifferent.com/online_exclusives/2024/01/ speak-up-and-stay-safe-your-question-couldsave-a-life) and has been reused with its and the author’s permission.
KKomatsu is back in the racing game after signing a multiyear deal with Williams Racing to become the British team’s principal partner for the start of the 2024 FIA Formula One World Championship (F1) season. Komatsu’s logo and branding will feature prominently on the 2024 Williams Racing livery, as well as the team’s overalls and kit, during the F1 season.
Komatsu was a key F1 partner of Williams Racing during the 1980s and 1990s, a period of abundant success for the team. The most notable achievements were in 1996 and 1997, when Komatsu supported Williams Racing to Constructors’ and Drivers’ Championships with Damon Hill and Jacques Villeneuve, respectively. With an eye to the future, both brands are excited to build on their shared history as they embark on a new era.
Komatsu’s official designations with Williams Racing reflect the companies’ shared focus on the long-term development of engineering, technology and new generations of talent: Official STEM and Early Careers Partner, Official Esports Partner, and Official Construction Machinery Partner. These areas will overlap and combine within the partnership, as Komatsu endeavors to engage and bring focus to the next generation of innovators through STEM events enriched by the Williams Racing esports platform.
“Komatsu and Williams Racing have shared values around innovation and the development
of our people,” said Hiroyuki Ogawa, President and CEO of Komatsu Ltd. “Through our partnership, we look forward to creating value together, both on and off the track. Our partnership with Williams Racing is aligned with Komatsu’s mission to create value through manufacturing and technology innovations to empower a sustainable future where people, businesses and our planet can thrive together.”
Foundation for cross collaboration
One of the driving forces behind the partnership was the alignment of vision that the two brands share. The characteristics embedded in Komatsu’s DNA and values, such as cutting-edge technology, outstanding quality and unwavering reliability, are all demonstrated by Williams Racing at the highest level of motorsports. This new partnership creates a foundation for cross collaboration between the companies into the future.
“Williams Racing is delighted to be rekindling our relationship with Komatsu,” said James Vowles, Team Principal of Williams Racing. “We have enjoyed huge success together in the past and reuniting is a significant step in Williams Racing’s long-term mission to return to the front of the grid. Both Williams Racing and Komatsu are committed to attracting and developing the best young talent in pursuit of our goals, and we look forward to working together again.” ■