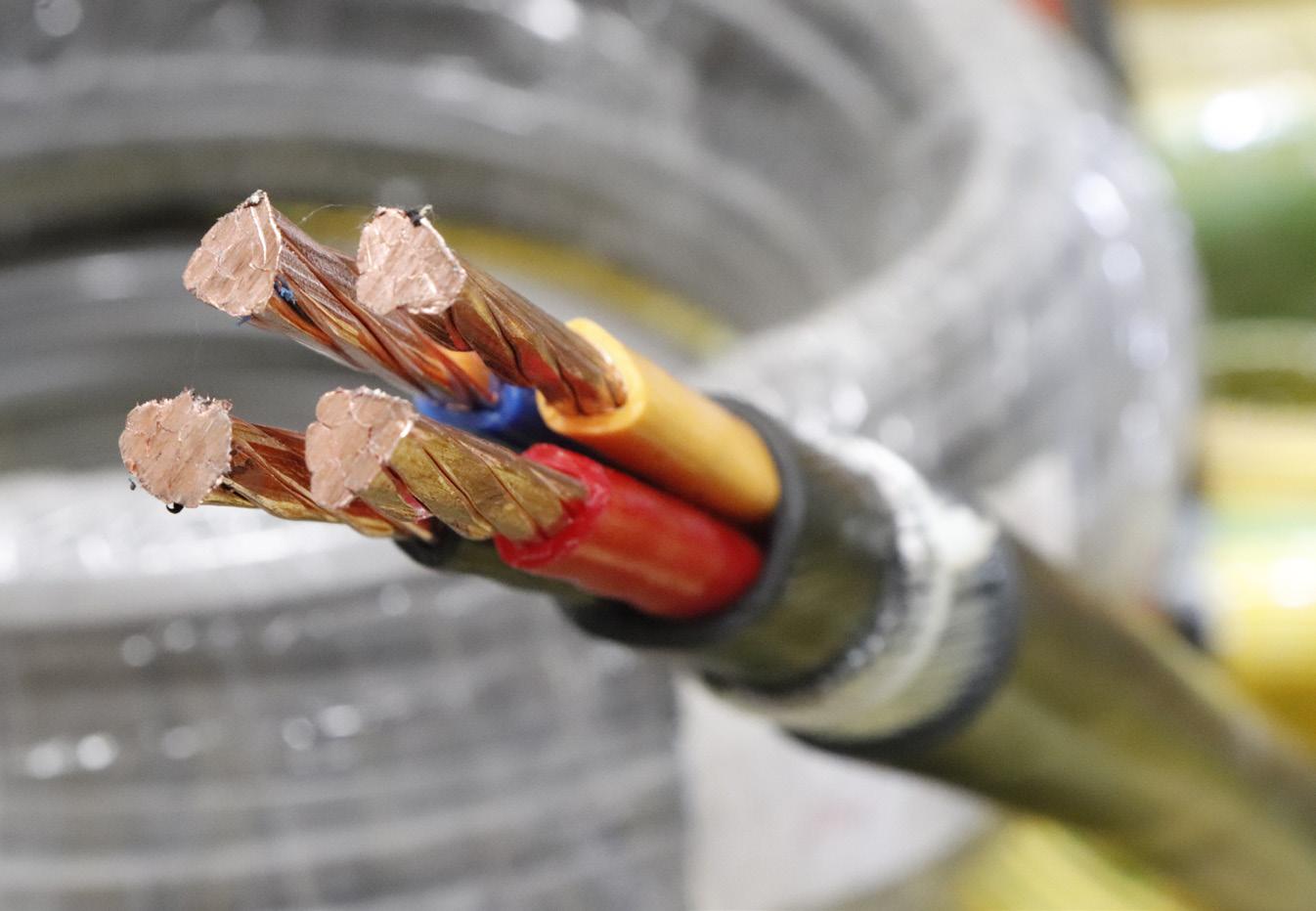
6 minute read
East African Cables Plc - manufacturing cables since 1966
East African Cables Plc
Advertisement
East African Cables Plc has been manufacturing electrical cables and conductors since 1966, that means 5 decades of guaranteed, consistent quality. Our electrical cables are made from 99.98% pure Copper and Aluminium; and insulated with PVC, XLPE, Halogen Free Fire Retardant (HFFR Compound) and rubber depending on the application. All our raw materials are responsibly and sustainably sourced in line with the set international and local standards and manufacturing processes comply to the ISO 9001:2015 Quality Management System guidelines.
EA Cables has heavily invested in technology and does 100% of the cable manufacturing processes locally, this is an advantage to our contractors because we can manufacture cables specific to project requirements. We often get orders from project managers, contractors and utilities that are specific to the project design. As an example, a contractor may import a machine with 27 termination points and requires only 100m of a 27core armoured control cable that has fire retardant capabilities. Importing this short and unique cable would be too costly and would negatively impact project timelines. In this case EA Cables, as a local manufacturer works the with the engineers to design a cable with these specific needs in mind. EA Cables is also part of the technical committee that reviews and develops local cable standards with the Kenya Bureau of Standards (KeBS) to promote the safety of the products in the market. Electrical cables are categorized depending on their final application, current carrying capacity and voltage rating. Cables can have different configurations, always basing their design on national and international regulations. Majority of our cables are Low Voltage cables (up to 1,000 V): (designated (0,6/1 kV). The cables in this class are used for industrial power installations in various fields (general industry, public installations, infrastructures, domestic housing etc.).
Submersible Cables
Submersible Cables is one of our new cabling solutions targeting the agricultural sector and other uses where the cable remains submerged under water for long periods of time, e.g. pumping of drinking and irrigation water from deep wells and boreholes, aquariums, water purification systems, swimming pools etc. Our submersible cables are made from a special skin which is more resistant to corrosion and water ingression/damage as compared to ordinary insulation materials. Submersible pumps are often very expensive and can be rendered useless if a cable with poor qualities of insulation is used.
Welding cables
Another of our new cabling solutions responding to the local market needs is the welding cables. Our welding cables have a special sheath, which is resistant to abrasion and moisture and allows high currents to be transmitted between the welding generator and the electrode. This extended the life of the cable, giving the buyer value for money.
Amoured cables
For industrial applications and for cables that are prone to risk of mechanical aggression, we manufacture armoured cables for places where rodents are present, as well as in installations in premises where there is risk of heavy equipment such as forklifts and trucks driving over the cable. The armouring also protects against possible damage during excavation.
Flexible cables
Other applications call for extra flexible cables for fixed industrial and domestic installations as well as in mobile service. These are cables for machines that move around such as the grinders, lawn mowers and cookers. Flexible cables have very fine strands that make them flexible on all angles without the copper strands breaking. Our flexible cables are reliable, and we use Using modern technology to anneal the copper makes our cables very flexible and malleable thus can be bent and twisted many times without breaking or
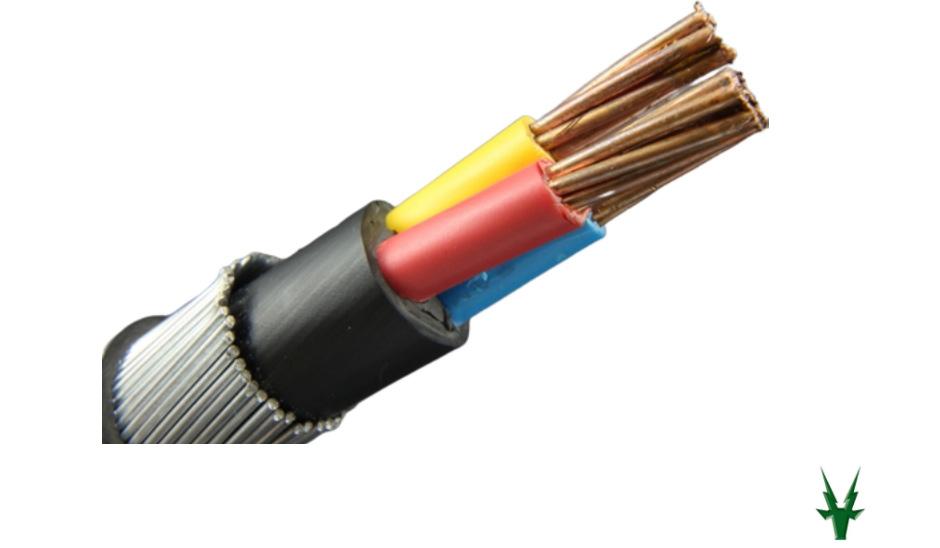
cracking. damage.
Halogen-free fire-retardant cables Halogen-free fire-retardant cables (HFFR) are a special class of cables that do not emit hazardous fumes when heated (the main cause of fatalities in a fire outbreak) and have fire retardant capabilities to prevent progression of fire. They are suitable for use in wiring of electric panels and installation in public places where many people are like to be present, e.g. malls, hotels, hospitals, office blocks etc. The fire-retardant cables are also preferred for use in emergency systems i.e. circuits and equipment that supply illumination, power, or both after interruption of the normal electrical supply. This product range of cables is gaining popularity especially in new developments in hospitals, airports, and high-rise buildings with many occupants.
Industrial Process Control Cables
Control cables for fixed or mobile installations are mainly designed for the interconnection of machine parts used for manufacturing, for signaling and control systems, for the connection of motors or Variable Frequency Drives (VFDs), for signal transmission where the voltage induced by an external electromagnetic field may affect the transmitted signal or for power supply connections to avoid generating electromagnetic fields. These cables are often uniquely configured and may have upwards of 40 cores bunched together. suitable for connecting photovoltaic (PV) panels, and the panels to the AC inverter. Thanks to the design of their materials and their skin, which is especially resistant to solar radiation and high temperatures due to carbon black compound used in the insulation, they can be installed outdoors. We also custom make battery cables for the solar battery storage systems.
Aside from the cables mentioned above EA Cables manufactures aluminum cables for power transmission and for ‘dropping’ power to the house or building. These include our Arial Bundled Cables (ABC), Concentric Neutral Cables (CNC) and the bare overhead lines which we manufacture for utilities in Kenya and in the Eastern Africa Region.
Last, but certainly not least is the most famous and most commonly available cables in the market, the domestic house wires. These are the cables used in wiring lights, sockets, and miniature circuit boards for power distribution in buildings. In response to the market requirements, EA Cables has also partnered with a reputable original equipment manufacturer to bring on board some of the accessories such as sockets, switches, and miniature circuit breakers (MCBs).
Causes of power cable failure
The short answer here is the quality of insulation material, the quality of conducting material and the process used and the dimension of the cable as compared to the standard. If a cable is properly sized to match the power requirements and voltage rating of the application, cables will last for decades. Therefore, when a homeowner decides on the cable, it should be a cable that will power the home for years to come. The engineer should always use a derating factor and calculate future additional load requirements when recommending a cable.
We are however living in times when there are unscrupulous people who risk the lives of millions by supplying substandard cables that are prone to failure. In a case where the engineer recommends use of a cable of 2.5mmsq cross-sectional area and the supplied cable when measured is 1.0mmsq crosssectional area (irrespective of the labeling), that cable will heat up and may even result in a fire sometimes causing extensive damage. The reason is because the cross-sectional area of a copper conductor is inversely proportional to cable resistance. High cable resistance will heat the insulation no matter how thick and result in eventual cable failure.
The type of insulation is key for each application. PVC is a good insulator but, may not be the best for use in specialized applications e.g., areas with oils, chemicals, water, abrasive environments etc. For these applications, a special skin, though slightly more expensive would be the better option and give value for money. If the quality of insulation is unsuitable for the cable application, there will be cable failure.
The workmanship and correct sizing of cables is also a major root cause of power cable failure. It is our strong recommendation that a developer needs to select the right quality of cables and to hire a qualified, licensed installer to guarantee total peace of mind.
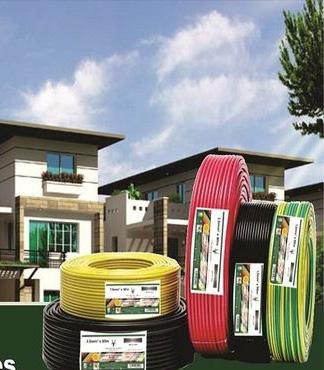