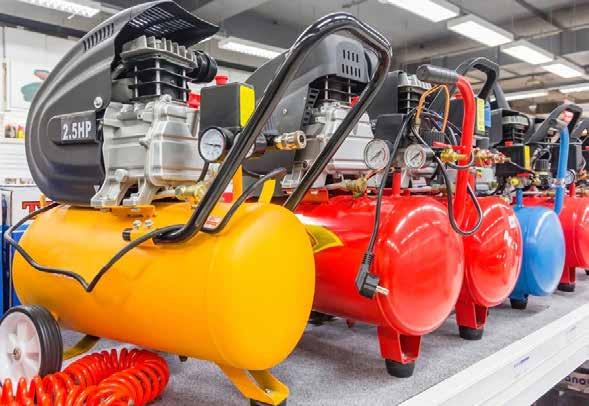
4 minute read
4 Types of Air Compressors: Which is Right for Your Project?
Air compressors are some of the most necessary appliances found at construction sites, as they can be used as a power source for electric tools. There are many different types of air compressors, each with its own unique capabilities and drawbacks.
Air compressors are categorized as either positive displacement or dynamic displacement, based on their internal mechanisms. The four most common types of air compressors are:
Advertisement
1. Rotary Screw Compressors
2. Reciprocating Air Compressors
3. Axial Compressors
4. Centrifugal Compressors
To help you make an informed decision for your project, we’ll cover the key features of each type and explain how each one works below.
Positive Displacement Compressors
Positive displacement compressors encompass a variety of different air compressors that generate power via air displacement. Air compressors in this category work with different internal mechanisms, but the principle for each is the same. A cavity inside the machine stores the air brought from outside, then slowly compresses the cavity to increase the air pressure and potential energy.
Rotary Screw Compressors
A common type of displacement compressor, rotary screws are some of the easiest types of air compressors to take care of, as they are equipped with an internal cooling system that doesn’t require much maintenance. They are typically large industrial-sized machines that can be either lubricated with oil or run oil-free. Rotary screw air compressors generate energy via two internal rotors that turn in opposite directions. The air gets trapped between the two opposing rotors and builds up pressure within the housing. Because of the internal cooling system, these air compressors are designed for continuous use, and range in power from 5 horsepower up to 350 horsepower.
Best For: Large-scale jobs and industrial settings that require continuous airflow
Reciprocating Compressors
Reciprocating compressors are another popular type of displacement compressor. They are typically found at smaller work sites such as garages and home construction projects. Unlike the rotary screw compressor, the reciprocating compressor is not designed for continuous use. A reciprocating air compressor also has more moving parts, which are lubricated with oil for smoother movement.
Reciprocating compressors work via a piston inside a cylinder, which compresses and displaces the air to build pressure. Reciprocating compressors can come in single- or multi-stage variations, which affects the pressure ranges they can achieve.
When you need more power, the multi-stage compressor is the way to go. While single-stage compressors will get the job done for smaller projects such as woodworking and metalworking, multi-stage compressors provide the power needed for intense construction, such as automobile assembly and maintenance.
Best For: Home and small-scale construction projects
Dynamic Compressors
Dynamic air compressors generate horsepower by bringing in air with rapidly rotating blades and restricting it to create pressure. The kinetic energy is then stored as static within the compressor. Axial and centrifugal compressors are the two most common types of dynamic compressors.
Axial Compressors
Axial air compressors are not typically used in construction projects. Instead, they are commonly found in high-speed engines on ships and planes. Axial compressors have a high efficiency rate but are much more expensive than other types of air compressors, making them best suited for aerospace applications requiring high horsepower.
Best For: Aerospace applications and high-speed engines for ships
Centrifugal Compressors
Centrifugal air compressors slow and cool incoming air through a diffuser in order to build up potential energy. Because of their multi-phase compression process, centrifugal compressors are able to produce a high amount of energy in a relatively small machine.
These compressors require less maintenance than rotary screw or reciprocating compressors, and some types can produce oil-free air. Because they can reach around 1,000 horsepower, centrifugal compressors are typically used for more demanding construction sites like chemical plants and steel manufacturing centers.
Best For: Large-scale steel and chemical manufacturing plants
How Do I Choose the Right Type of Air Compressor?
In addition to the power-generating mechanisms and energy output levels discussed above, there are several other factors to consider when choosing the air compressor that is best for your job.
Consider Air Quality
In clean manufacturing environments, using oil-powered air compressors can create a problem. Most air compressors rely on oil to lubricate the inside mechanisms, and the fumes may contaminate the air, resulting in damage to products or manufacturing processes. With an oil-free air compressor, this risk is greatly reduced.
Though oil-free compressors are generally more expensive, they are the only option for facilities that guarantee clean manufacturing. Oil may still be necessary to lubricate the machine, but the inner workings of oilfree compressors contain a different sealing mechanism to ensure that no oil gets into the actual compressor.
In addition to clean air, oil-free compressors often have lower running costs, as parts do not need to be changed as frequently.
Prioritize Energy Efficiency
If you’re working on a long construction project, getting a high-efficiency air compressor can be worth the extra cost in the long run. If you’re looking for an energy-efficient air compressor, consider one of the following options:
•Variable speed: Variable speed-driven (VSD) compressors save energy and money by allowing you to increase or decrease output on demand. In comparison, the motors in fixed-speed compressors are constantly churning at the same rate and require a cool-down period that uses extra energy.
•Natural gas: Natural gas air compressors run on natural gas instead of diesel or electricity. They often operate more efficiently than other options and have better heat recovery capabilities than electric compressors. If efficiency and energy savings are your main goals, a natural gas unit may be a good fit.
Consider Portability Limitations
If you transport your air compressor between sites, a portable unit is a good option. Small, lightweight units can still deliver energy, but in a compact package. Though they won’t be as powerful as larger units, portable compressors can be ideal for smaller construction projects. Certain units can even be plugged into a car’s power adapter to fuel small airbrush painting or tire inflation tools!
Determine the Need for Additional Features
There are a variety of add-ons and additional features you can use with different types of air compressors. For example, couplers or air hose splitters allow you to hook up multiple tools to your air compressor so you don’t have to disconnect when you’re changing tasks. Air compressors with thermal protection add-ons keep track of internal heating and stop motor damage if the machine is overloaded.
Some air compressors have belt drive systems rather than direct drives, which allow for quieter operation. If you think you will need any of these additional features, you’ll want to make sure that the type of air compressor you choose is compatible.
If you don’t want the commitment of purchasing an air compressor for your construction job, BigRentz has several types of air compressors for you to rent for your next job. From small and portable to industrial-scale, you have all the information you need to make the best choice for you.