
3 minute read
Kimberley Ports Authority: Wharf Extension Underdeck Access
Involving the conceptual development, detail design and installation of an access system for the routine inspection and maintenance of underdeck assets, including piles, headstocks and services along the full length of the Broome Port Wharf in the northwest of WA, the wharf consists of the original portion, constructed in the 1960's, and the later extension constructed in 2007. A simple access system is installed to the soffit of the original wharf deck but not to the wharf extension.
Wave International was commissioned to perform the detailed structural and mechanical engineering design for the wharf extension access system and develop solutions to numerous challenges arising from the client’s design brief, the operational environment, existing constraints, and the contractor’s execution methodology.
Advertisement
Significant for numerous stakeholders, in addition to the extension of asset life for the client, further economic, safety and environmental benefits were to be realised. For example, prior to the new installation, all inspection and maintenance works under the wharf extension had to be completed using cantilevered / hanging scaffolding, top-side mobile cranes, boats and barges, attracting additional overhead costs and increasing the risks to maintenance crews. The new access system sought to mitigate these risks and the design requirement for full encapsulation, further enhanced safety and ensured any negative environmental impacts, particularly from blasting and painting operations, were minimal.
The design portion of the project, though small in scale and dollar value as far as engineering projects are concerned, was big on innovation combined with solid, firstprinciples engineering. The final design of the access system (shown in Figures 1 to 3), is, put simply, a travelling personnel basket. It allows for complete access to all areas of the headstocks and piles within the tidal zone for up to four people and tools, under various combinations of dead, live, wind and wave loading conditions. It consists of an upper steel frame to house the main driving components, wheel bogies and slewing frame, with aluminium framing for the walking deck, driving cabin and extending boom arms to help reduce the overall weight.
Figure 1 – Elevations of new underdeck access trolley – boom arms extended
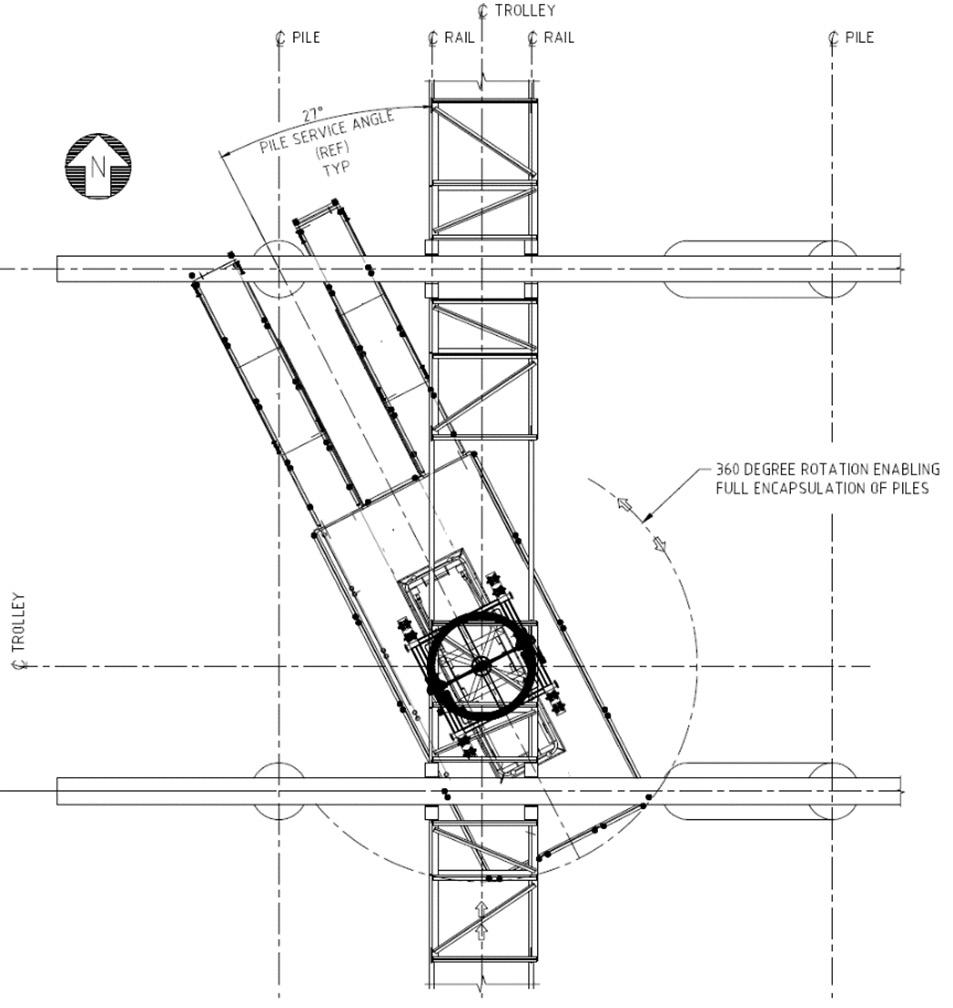
Figure 2 – Plan view of new underdeck access trolley
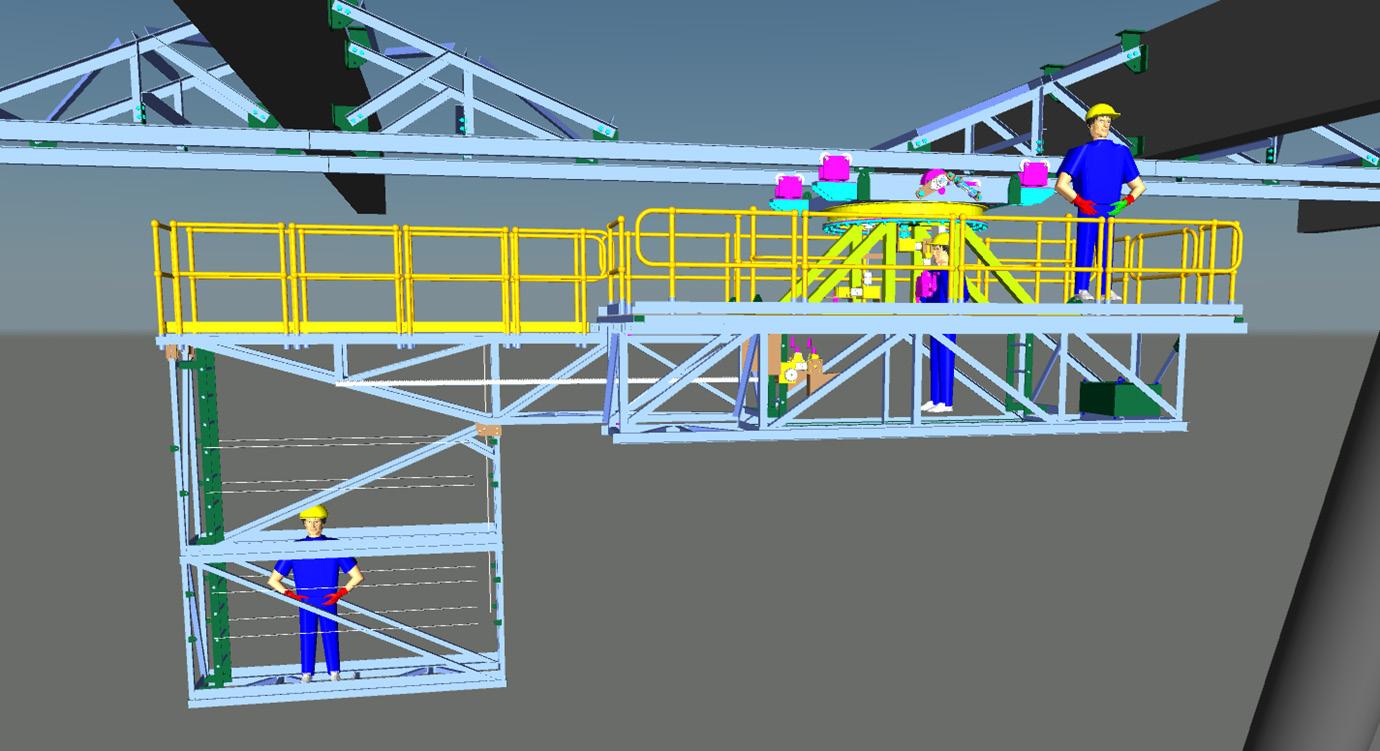
Figure 3 – 3D model of new underdeck access trolley Figure 5 – Photograph of new underdeck access trolley during rail installation works
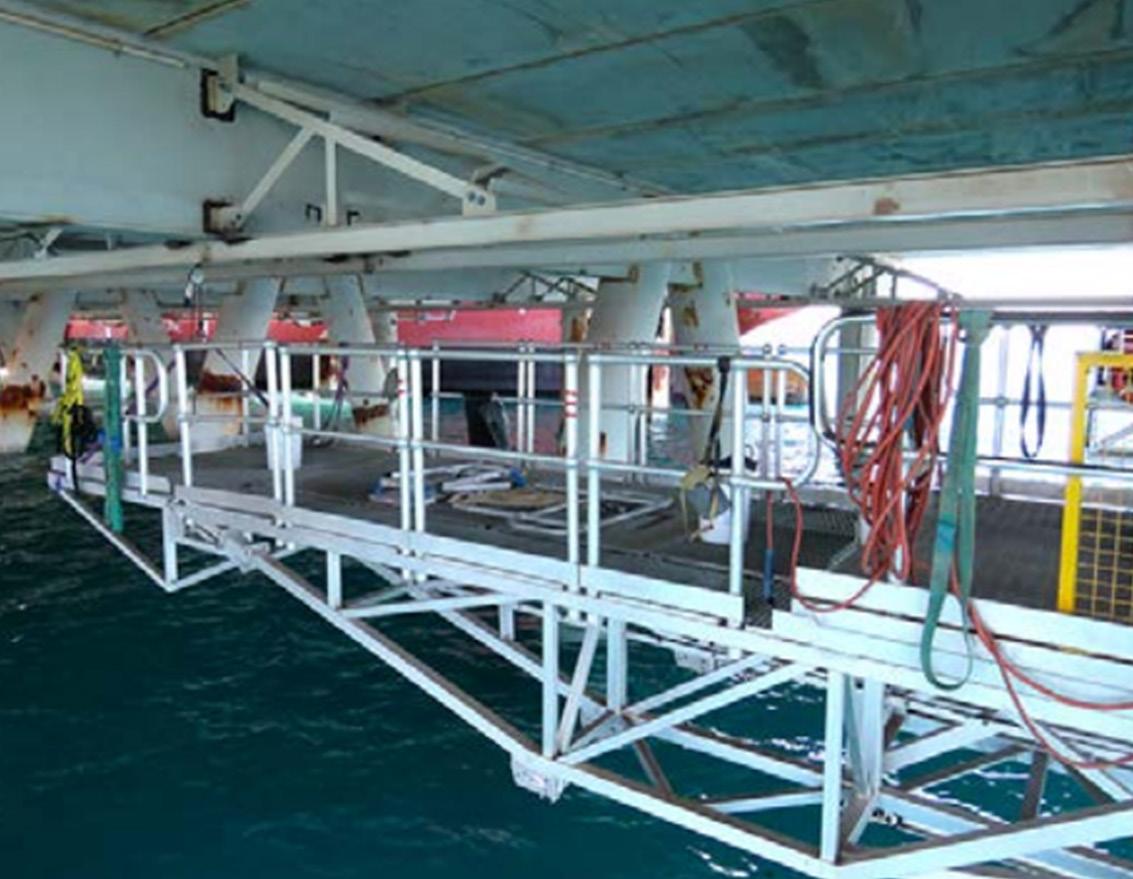
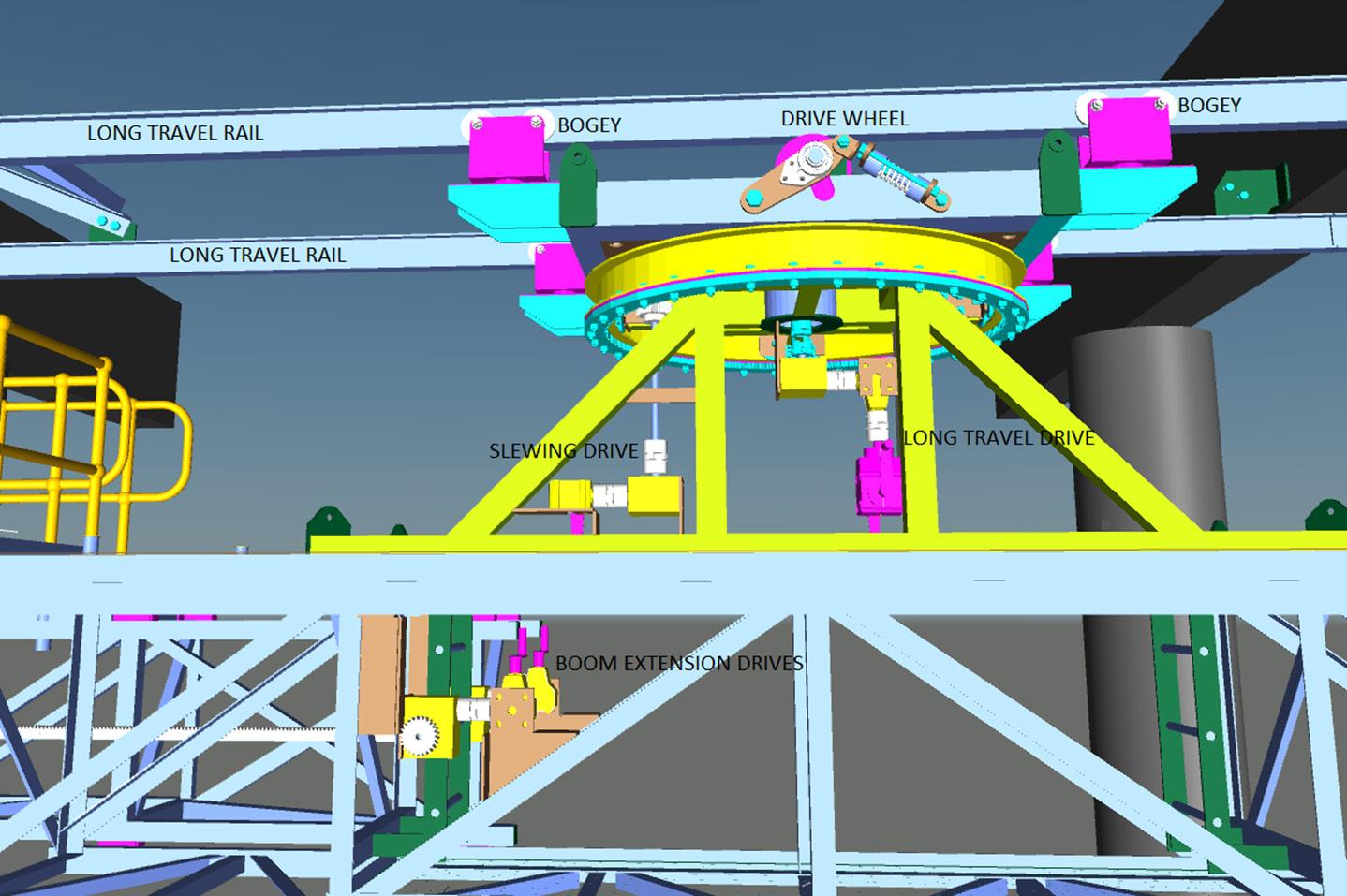
Figure 4 – Drive mechanisms of new underdeck access trolley
The driving mechanisms are shown in Figure 4. The main drive can be operated by hand or small battery powered motor. Each drive wheel has a pair of adjustable compression springs for setting the necessary frictional resistance while maintaining reasonable manual effort to generate linear motion. The slewing mechanism allows for 3600 rotation and consists of a hand driven gear box and shaft turning an internal ring gear. The boom arms are extended via a manually driven rack and pinion system. All materials for gears, drive and slewing wheels were carefully selected for their durability against chorides, hardness and bearing strength.
The contractor’s work methodology required the trolley to be utilised for the installation of its own travelling rails. To this end, a boom extension piece was designed to increase the total working area from the backside of one headstock to the next. Each new section of rail was loaded onto the trolley and hoisted from temporary attachments before being welded in place. This process was repeated until all rails were installed. Figure 5 shows the trolley during the rail installation phase.
The project utilised a 3D modelling environment, overlayed on point cloud scans of the existing wharf. This ensured all dimensional issues, clashes, and how well the rail bends would be negotiated could all be confirmed prior to fabrication. This 3D design environment, innovative thinking and good engineering all contributed to the success of the project which achieved its design goals while solving the numerous competing constraints.