
7 minute read
CONSTRUCTION DATA & F IGU R E S
College Graduates are Fleeing Coastal Cities
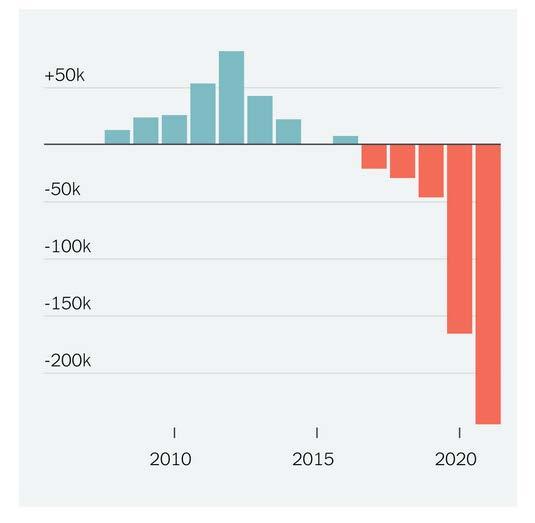
Advertisement
For most of this century, large urban areas — nearly all of them on the East or West Coasts — saw net gains of college graduates, even as they lost large numbers of workers without such degrees. But in a trend that began before the pandemic and has since picked up steam, expensive cities are now shedding educated workers too.
Data analyzed by The New York Times shows that many people leaving cities with high costs of living, like New York and San Francisco, are landing in major metros that are not quite so expensive, including Phoenix, Atlanta, Houston and Tampa, Fla. The pandemic-era rise of remote work has accelerated the shift.
You can look up your metro area to see whether you’re gaining or losing collegeeducated workers.
Net Domestic Migration of Working-Age College Graduates in the 12 most expensive large metro areas (including cities like New York, LA, and Chicago)
Construction Inflation and Prices
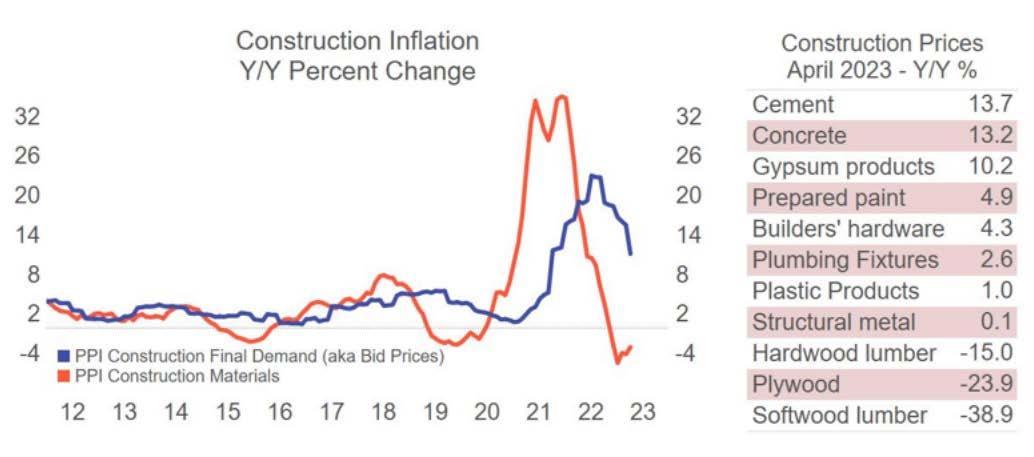
Source: Dodge Data & Analytics - https://www.construction.com/news/April23PPI
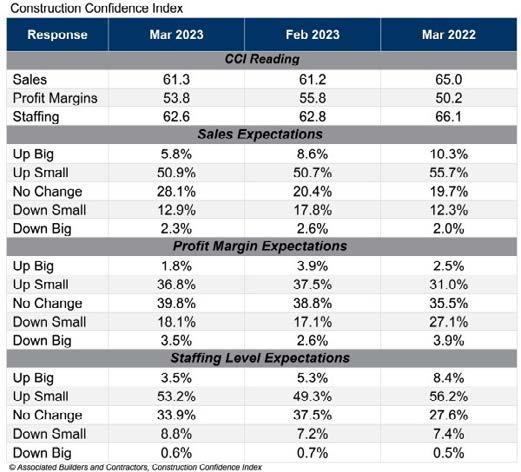
ABC Construction Backlog Indicator increased to
Industry Confidence Index Increases 1 Point
The ENR Construction Industry Confidence Index for the first quarter shows that, of the 305 executives of large construction and design firms responding to the survey, a majority believe the market is growing. The CICI index moved up a point, to a record 78 on a scale of 100, in the first-quarter survey, an indicator of a growth market.
AGC - ConstructorCast: “Contractors Care: An Industry of Support”
Construction has one of the highest suicide rates of any industry. On this episode, we speak with the co-chairs of AGC’s Mental Health & Suicide Prevention Task Force -Mandi Kime of AGC of Washington and Brandon Anderson of AGC of Missouri -- on how they are leading the fight for an industry in crisis. They share why they are so passionate and how they are working to combat construction’s leading mental health difficulties and the stigma that accompanies them. Listen now.
Source: ABC.org
Toxic Job Sites Aren’t Fair…to Anyone
by Lucas Johnson, Vali Homes
“This works sucks. Let the ____ guys do it”. I’ve heard this phrase far too many times after a few decades in the construction industry. It also accurately reflects a general industry attitude: The people with the least power will be assigned the most dangerous tasks.
After years of building in Arizona, we got so tired of seeing this we decided to do something about it. We’ve created Vali’s “5 Factors of Good Building”, which is a design and product specification tool. The 5 Factors include: (1) Comfort & Health, (2) Durability & Resiliency, (3) Efficiency & Renewables, (4) Lifecycle Carbon Impact, and (5) Social Justice.
While it’s important to consider all Five Factors in every decision, this article will focus on the factor that is listed last, though it is certainly not least: social justice. This can be a confusing and politically fraught subject, but at the most basic level it seems beyond debate that people should have a right to fair compensation and a healthy environment. Yet the lived experience of workers is often unfair and unhealthy. Injustice plays out when people with less power are assigned the dirty work. Of course, construction will always require digging in the dirt, but ironically enough, dirty work isn’t typically referring to literal dirt. Dirty work typically means interfacing with toxic materials.
Product Lifecycles of Embodied Injustice
There are three primary stages where workers are forced to interface with toxic materials. These include material extraction sites, manufacturing facilities, and construction sites. In each of these stages, the workers are rarely compensated fairly for the risks they are taking. As construction professionals the key action we can take is specifying healthy materials with socially just lifecycles.

In terms of the materials we use to build, we must expand our thinking beyond what occurs at construction sites. The lifecycle impact of a material begins much sooner before you buy it at the store. Pro tip: when there is a low price on the shelf it typically means there were low standards of care for the people who created it.
Unfortunately, with pressure to build as cheaply as possible, a lot of products are made with what could be called lifecycles of embodied injustice. While the goal of creating affordable housing is good, it isn’t okay to create toxic environments for future occupants and the workers who build their living spaces. How can we expect people to escape cycles of poverty when they are living in uncomfortable and toxic environments?
When the Foam Hits the Wall
Let’s explore spray foam insulation as an example of lifecycles of embodied injustice. We will look at one of the simplest applications, which would be installing it around a window to seal between the frame and the rough opening. Let’s start by considering the ingredients used to make spray foam.
Spray foam is effectively a mix of fossil fuels and concerning chemicals on the Red List, which is a comprehensive list of chemicals known to have negative human health impacts. It is therefore inextricably tied to the large chemical and fossil fuel companies who have caused some massive problems, including climate change. These include war-for-oil and incredibly poor working conditions at extraction sites. These also include factory workers being exposed to toxic materials in their work while the same factories dump these chemicals into the local environment. For a powerful example, please check out the documentary called “The Devil We Know.”
Then we get to the job site where workers, often without sufficient protection, are installing spray foam. Insufficient protection typically occurs due to workers not having the resources to afford the proper equipment and/or due to not being made aware of what they need to be safe. This is a perfect example of what anthropologists and other social scientists call structural violence.
To do a reasonable job installing spray foam, it requires being close to the application. Workers are exposed to concerning chemicals. Maybe these chemicals all off-gas during construction, but maybe the chemicals continue offgassing long enough to harm the future occupants as well. Either way there has been a deep history of toxicity from raw material onwards.
So how do we solve this problem and create social justice in construction? It starts by caring about the people who do the actual work. This is the moment to give a big shout-out to all the subcontractors and trades. Thank you from the bottom of our hearts for the work that you do. We understand it isn’t easy and it is our job as a developer to have your back.
The Vali Way
The Vali approach to social justice in construction begins with specifying nontoxic materials. It continues by taking a deep look into the product lifecycle of materials before we specify them. Circling back to the window integration example: instead of spray foam, we stuff the shim space gap with sheep wool insulation and use non-toxic (aka certified Red List Free) tapes to seal from the frame to the rough opening. We also occasionally use non-toxic caulking when zero reveal details require it. Of course, the rough opening has also been prepared with non-toxic airtightness and waterproofing materials, which can include membranes, tapes, and/or liquid applied.
The product lifecycle of wool insulation can be one to celebrate. It is worth emphasizing that all wool insulation is not created equal. Some wool can come from poorly treated sheep handled by poorly compensated workers and then enter a toxic manufacturing process. That being said, we are lucky to have Havelock Wool located in Reno, NV who provide a truly good and socially just product.
The Havelock Wool product lifecycle begins in New Zealand with extremely high standards of care for the sheep and the people who raise them. The insulation product comes from a former waste product, which is the early season shearing of the belly wool. This is removed so it doesn’t drag on the ground, which can cause illness and comfort issues. The additional revenue stream of selling a former waste product helps the shepherds immensely. This is clearly much better than the raw material extraction process behind chemicals and fossil fuels.
The raw wool is shipped in densely packed containers to Reno, NV. Each container of raw wool can create roughly 50 containers of finished product. Their factory in Reno is a happy and healthy environment where people are well compensated for their work. Fire code requires adding the minimal amount of boric acid, but otherwise there are no toxic chemicals, such as glues or binders, added. This is also clearly a much better manufacturing process than you find with conventional materials.
The non-toxic approach is not only fairer to workers, but it also provides much better performance with much less maintenance for the occupants of the building.
The next time you are specifying a product, please consider the entire lifecycle of the product and how it has affected people throughout the process. We must demand products that are good for the people who make them, install them, and live with them.
Beyond specifying truly good nontoxic materials, it is critical to engage the contractor community with respect for their trade. At our most recent project in Phoenix called Vali Mews, we put the effort into finding craftsmen who run small local businesses. We worked with them from the design stage through construction to properly price their services so they would be fairly compensated. We also made sure they would have a safe and enjoyable working environment installing healthy products. It cost a little more upfront, but it prevented many mistakes, avoided reiterative work, and created a truly spectacular result. Creating good buildings requires creating good working environments for the people who do the work.
About the Author
Lucas Johnson is Chief Building Nerd at Vali Homes and a board member at the EcoBuilding Guild who has contributed to over 10,000 high performance building projects ranging from deep energy retrofits of large commercial buildings to Net Zero Passive Houses.