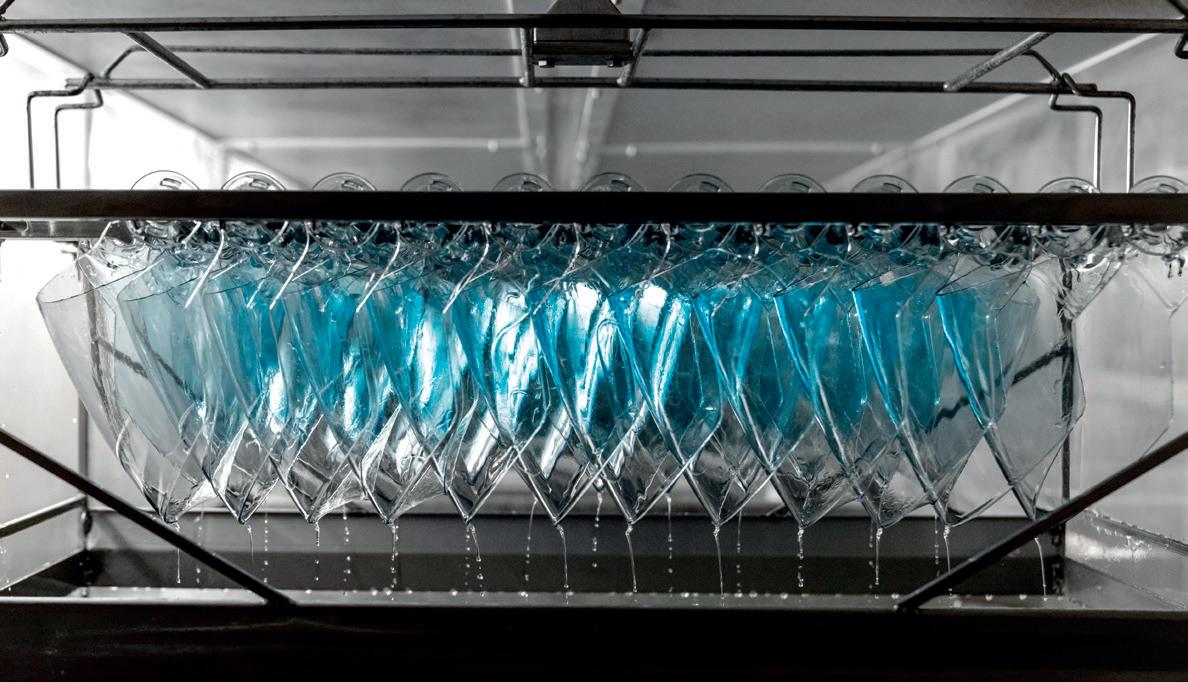
1 minute read
INTEGRATED MANUFACTURING PROCESS
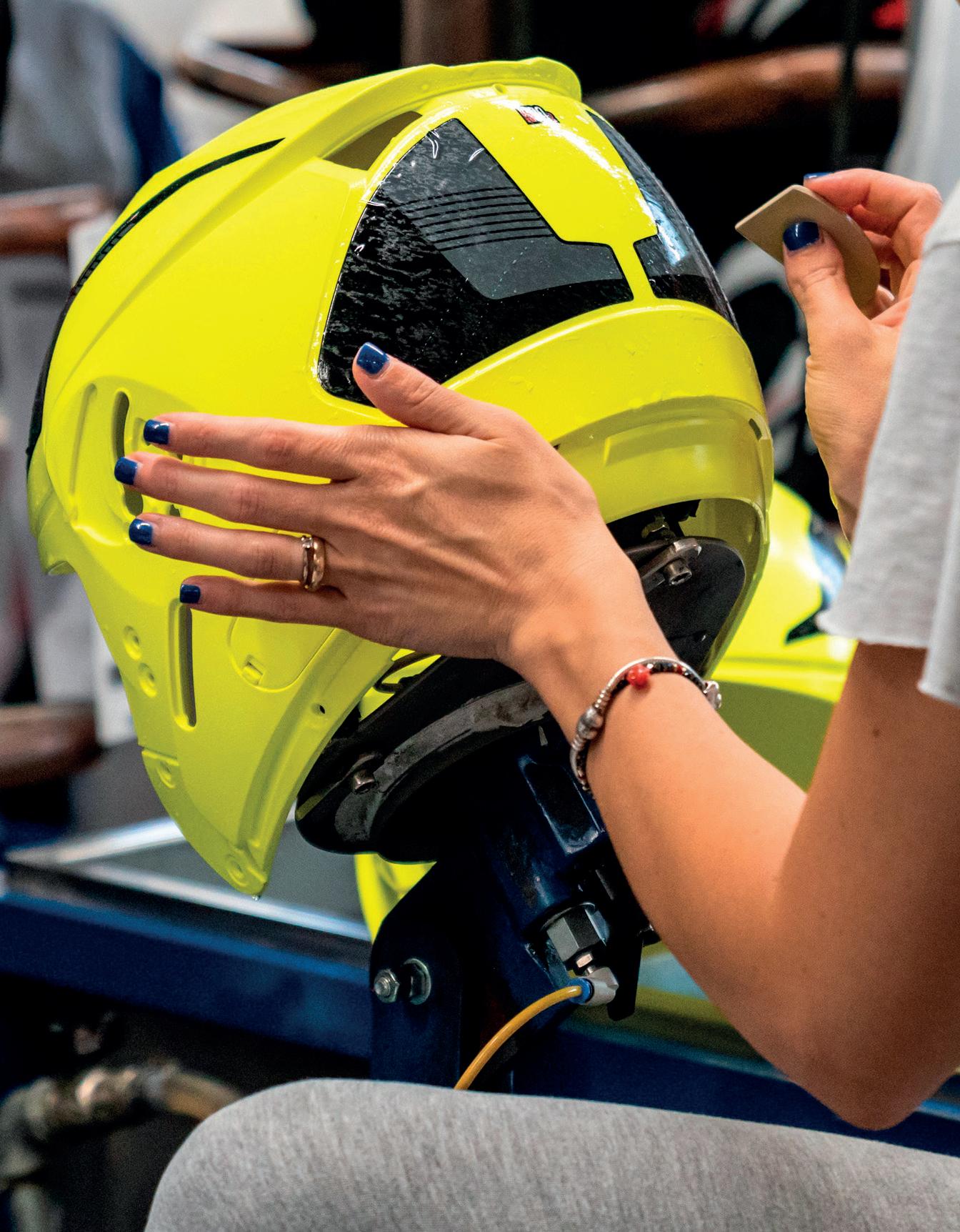
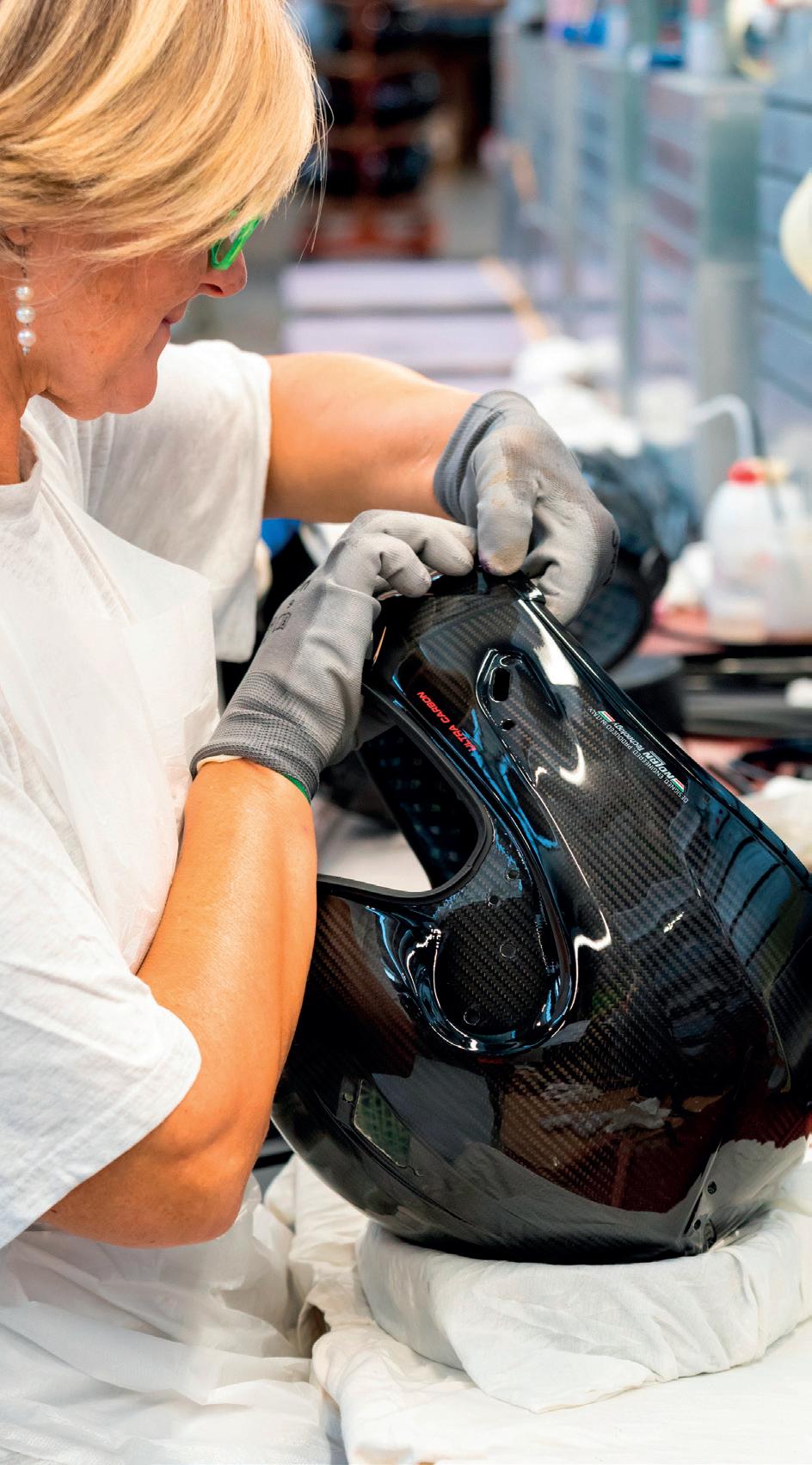
/ The production of the outer shell for Nolan brand helmets occurs trough LEXAN™* polycarbonate injection moulding process. LEXAN™* is a material ensuring, for the same shape, thickness and process, higher performance compared to ABS, the raw material used for the moulding of almost all motorbike helmets on the market.
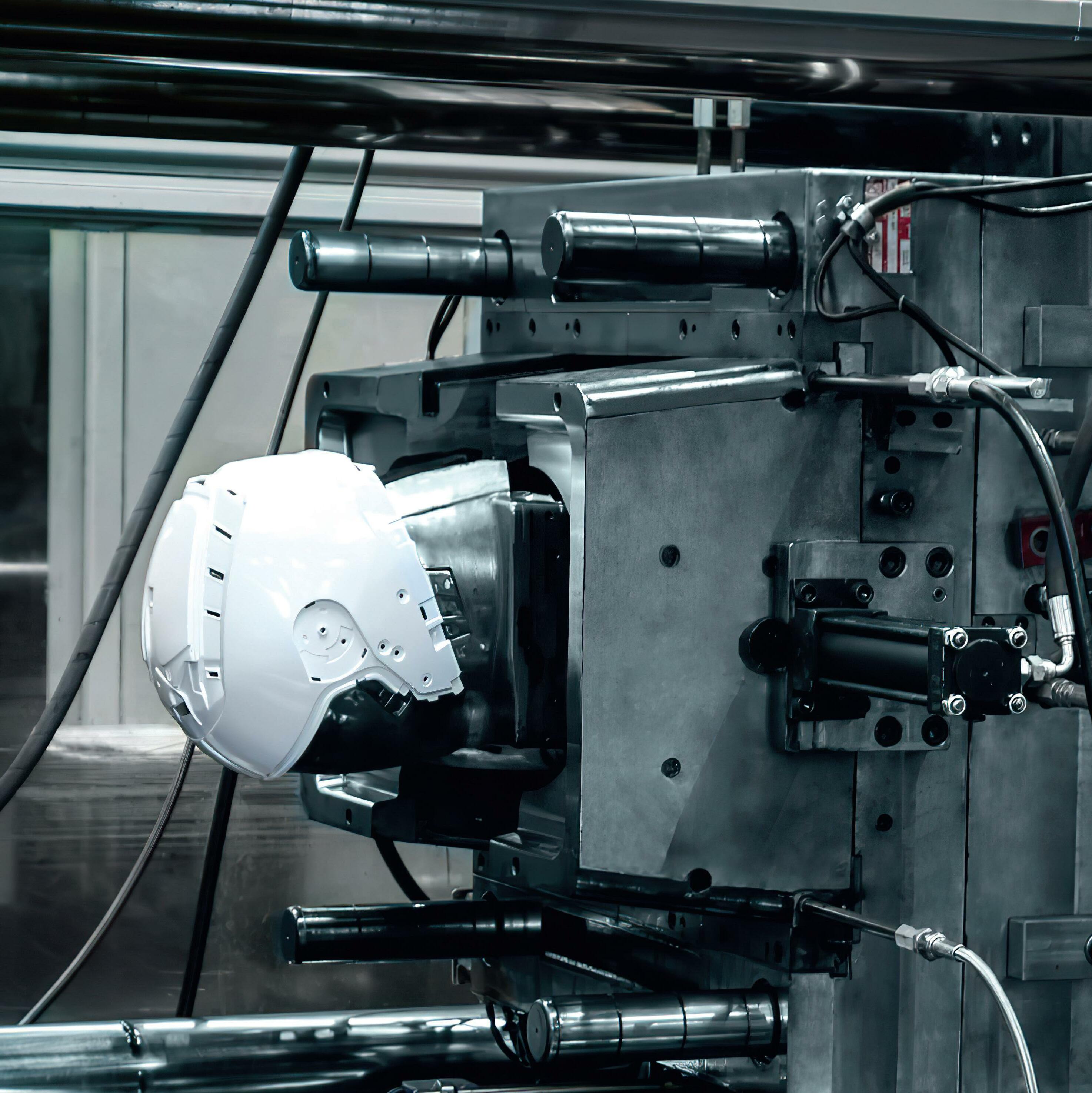
/ The production of the outer shell for X-lite helmets is based on the use of multi-axial hybrid fabrics (carbon-glass and aramid-glass) which are cut, in order to produce over 100 reinforcement pieces forming the base of the layers of the shell. Pre-established “recipes” differing in relation to the homologation required, the model and the size of the product. During the moulding phase of the shell, a thermosetting resin is poured into the layered mould and, via pressure from a counter-mould, is hardened, absorbing and binding the fabrics.
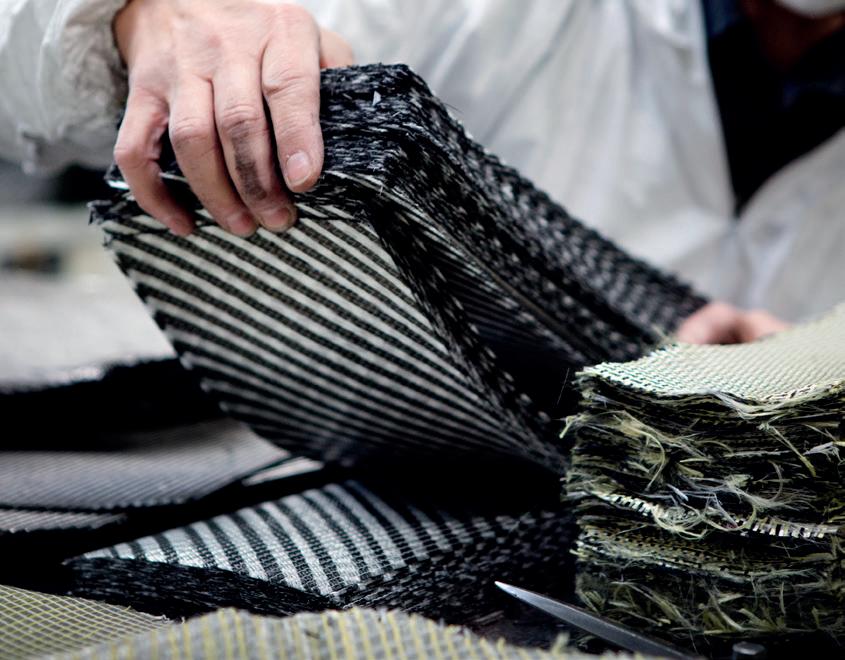
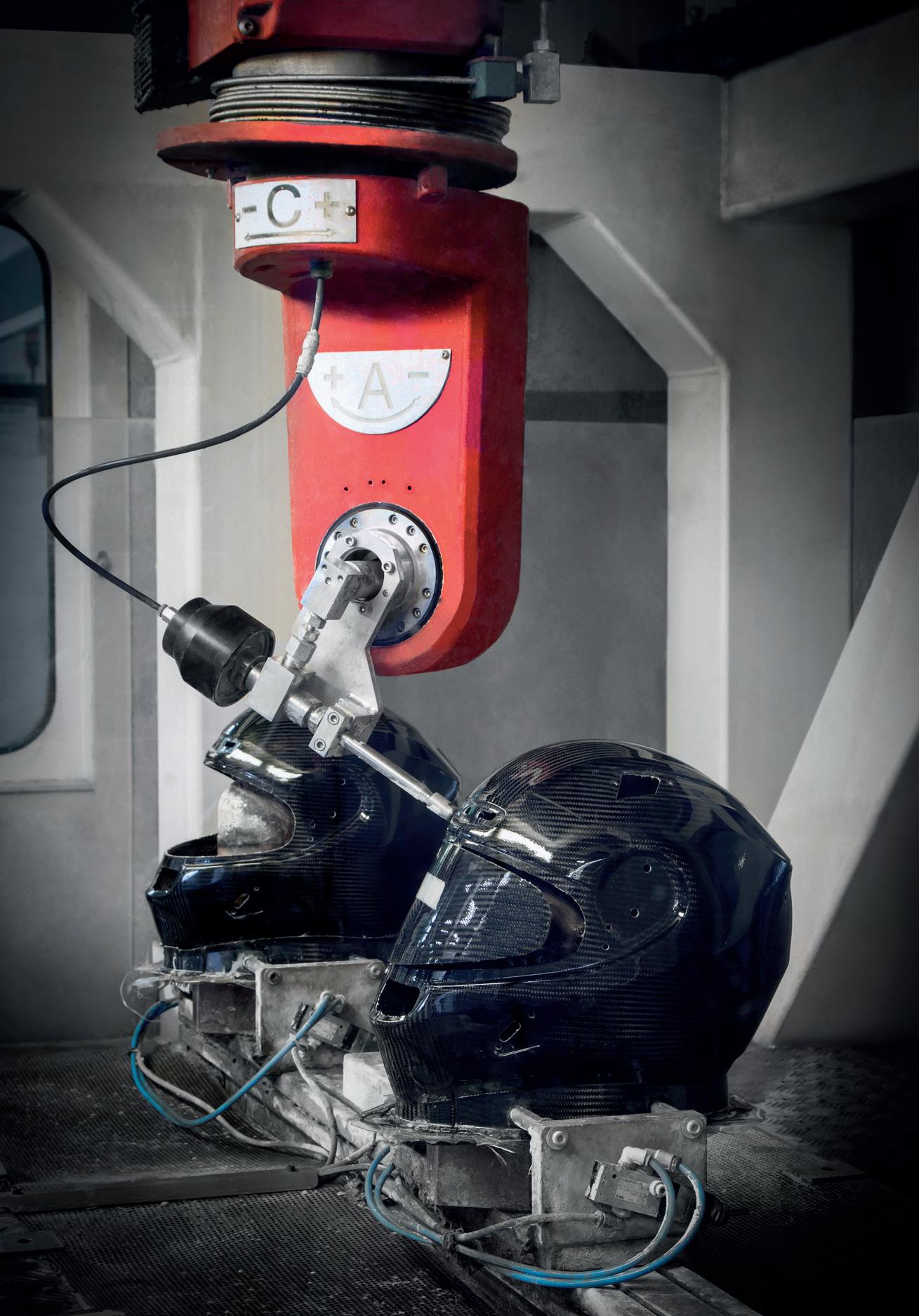
A numerically-controlled water jet machine cuts the shell: at high pressure, approximately 4,000 bar, visor windows and air intakes are cut.
The cycle ends with the automatic sanding of the shell by robot, visual checks and manual finishing for painting.