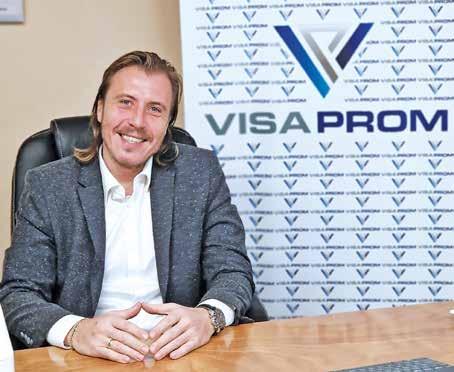
6 minute read
VLADIMIR MITIĆ, CEO, VISA PROM D.O.O. (LTD
VLADIMIR MITIĆ, CEO, VISA PROM D.O.O. (LTD.)
Respecting Nature, Nurturing Quality
Advertisement
Visa-Prom, one of the largest primary wood processors in the Republic of Serbia, which has been operating successfully since 1992, this year marks the 30th anniversary of its existence. The capital of this enterprise, which has more than 250 employees, is under complete domestic ownership
In every segment of its operations – from cutting and transporting wood, via processing and production, but also to trade – this Kanjiža-based company consistently respects all environmental protection and circular economy principles, thus providing a huge contribution to ensuring an environmentally friendly future.
You’ve been operating in Serbia for a full three decades, while since 2011 you’ve also been engaged in the production and processing of wood. How did you diversify your operations and what does your portfolio comprise? - Apart from trade, since 2011 our composition has also included a primary wood processing plant, which was opened with a desire to renew the production of packaging and create new jobs for residents of the municipality of Kanjiža. Our company is one of the largest primary wood processors operating in the Republic of Serbia, with annual processing that exceeds 50,000m3. We are simultaneously one of the largest producers of pallets, with annual production exceeding 600,000 units that are sold on the domestic market, as well as over 12,000m3 of poplar veneers and plywood that are sold exclusively on the markets of the EU.
Does the fact that you source raw wood material exclusively from forests that are managed sustainably represent your contribution to Serbia’s eco-friendly future? - We have the FSC [Forest Stewardship Council] certificate, which represents a guarantee that our wood reaches the end user via a chain that’s strictly monitored: from certified forests, through processing to final production. The FSC certificate represents a reliable link that can be traced back from the product in the hands of the end user through responsible production and the rational use of wood, to the felling of forests under strict expert supervision.
What do you mean precisely when you say that your factory is free of waste? - We like to say that there is no waste in the wood industry, only leftover wood. In the production process, during the processing and treatment of wood, a large amount of leftover wood remains, which accounts for approximately 40% of the total raw material processed. We use leftover wood as an energy source for our furnace plants. In order for us to round off the production process and maximise the use of raw materials, we invested in a new plant for the processing of leftover wood, with the aim of creating added value usage and a new product: compressed wood blocks, which serve as an integral element in the production of pallets. Creating the new plant and equipment to produce compressed blocks included an investment of considerable funds, exceeding 1.5 million euros.
Your operations consistently respect all environmental protection and circular economy principles. One could say that you place a great emphasis on this aspect in all stages of production, even more than you’re obliged to do so according to laws and regulations? - Visa-Prom is the only company on the Serbian
market that produces compressed blocks. As one of Serbia’s largest producers of EPAL pallets, we have licensed our compressed blocks according to the EPAL standard, with which the use of these blocks in the production of EPAL pallets is enabled. We also possess a thermal treatment certificate, while production is harmonised with the European standard ISPM 15 [International Standards For Phytosanitary Measures] and we have implemented ISO standard 9001 on management quality. As a responsible player in both the economic and social life of Serbia, we endeavour to organise our production process with respect for all legally stipulated environmental protection procedures and processes. We are planning to invest in a new furnace plant, with which we would reduce emissions of harmful gases and therefore also reduce environmental pollution. If we were to implement this investment with some form of subsidy and state assistance, we would create conditions for the creation of new jobs, in addition to improving energy efficiency.
For what do you use the green energy that you produce from excess materials in your own furnace? How far have you progressed with your ambitious plans to instal solar panels? - As I mentioned, our furnace plants use leftover wood from the production process as an energy source. The heating energy released is used to launch operations at the plant for drying veneers and pressing plywood and LVL [Laminated Veneer Lumber] boards, as well as to heat the plant and thaw logs during the winter months. We thus ensure the self-sustainability of production.
Ash is left behind as the remains of the burning of leftover wood in furnaces, which unfortunately represents waste. When considering how we can turn this waste into a viable product, we discovered that there are furnace plants that produce bio-coal instead of ash. Bio-coal has broad applications in agriculture, due to the fact that adding it to farmland significantly increases the fertility of the soil and helps restore degraded land successfully.
Given that electricity is becoming a scarce product, with a serious price growth tendency, we decided to instal solar panels on the premises of the factory. The first phase of the investment is already being implemented, with the installation of solar panels to produce 140kWp of electricity, and will be completed and made operational before the end of November. The implementation of the second phase, which implies the installing of additional solar panels with a capacity to produce 80kWp, is planned for the first quarter of 2023.
We are also currently in the phase of conducting a feasibility study for the implementation of an investment in a large solar power plant up to 10mWp. The realisation of this investment wouldn’t only cater fully to the factory’s electricity needs, but would also enable us to make the excess energy produced available to the Serbian power grid.

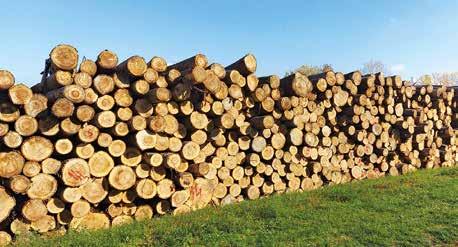
There is no waste in the wood industry, only leftover wood… and it accounts for approximately 40% of the total raw material processed. We use leftover wood as an energy source for our furnace plants
We shouldn’t overlook the fact that your company also engages in trade and that you take care to protect the environment and adhere to circular economy principles in this segment of your operations. You also adhere, among other things, to very stringent regulations with regard to packaging… - Our retail outlets sell dyes, varnishes, paints for interior and exterior walls, electrical materials, façades and thermal insulation materials. Our dyes, varnishes and paints are packaged in metal or plastic containers. We encourage customers to return the packaging to us after they’ve used the product, which we dispose of in an appropriate way and subsequently submit to recycling companies. Our desire is to collect as much of this type of waste as possible, in cooperation with companies that handle the recycling of this type of waste, and we are prepared to offer storage facilities to cater for its disposal, with the possibility of jointly investing in a major recycling centre.