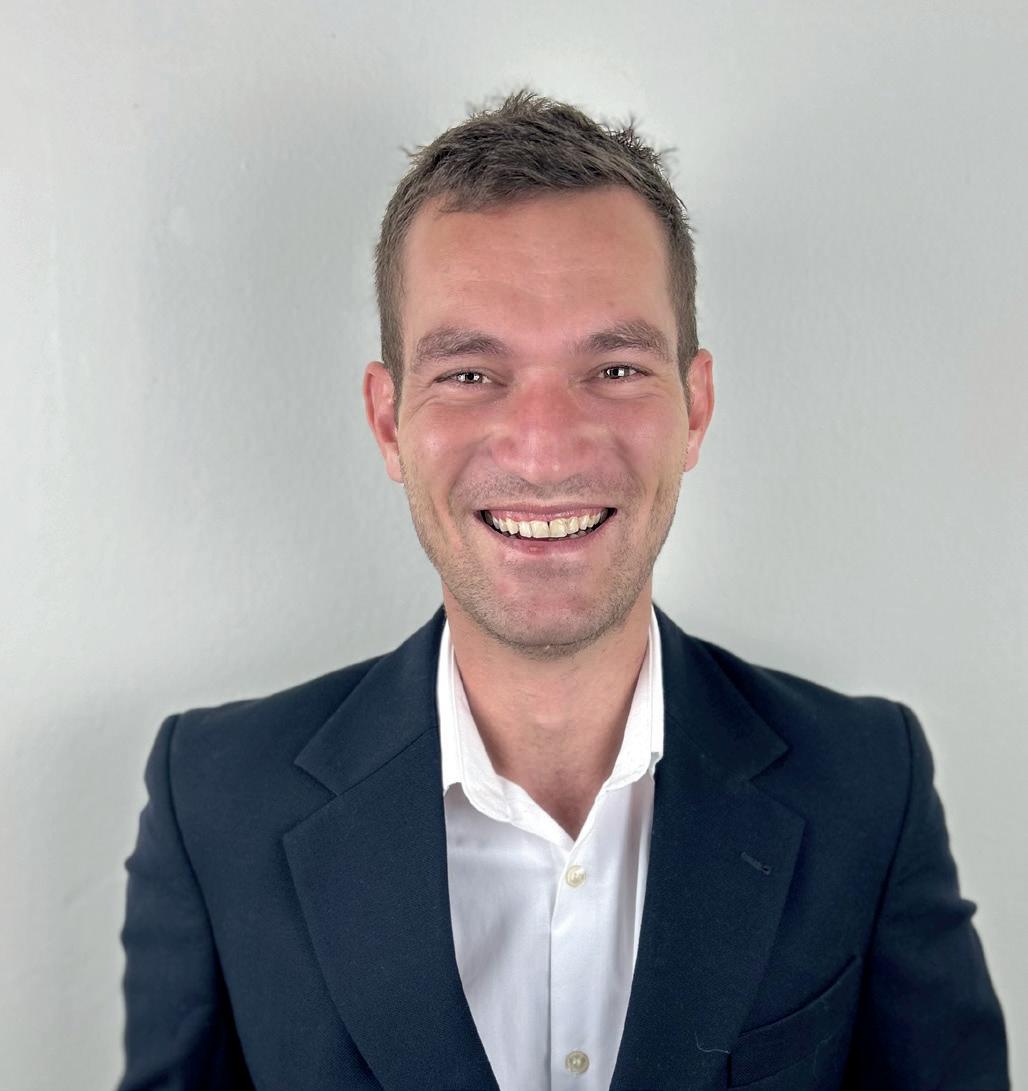
12 minute read
IGNUS STORM
Chief Operating Officer at Hall
Core Drilling
Advertisement
Ignus Storm dreamt of studying medicine, yet circumstances led him into the world of geology.
Ignus holds a Bachelor’s degree in Geology, followed by a Honors degree in Soil Chemistry & Mining Rehabilitation both from the University of Pretoria. After finishing his Honors degree in 2014, he started working at RHC Mining. He was a part of the first teams to successfully employ drones for commercial surveying.
Afterward, Ignus began working for Basil Read Mining and their client Anglo American, developing his managerial skills further. During the same time, he also completed a Master’s degree in Engineering from the University of Witwatersrand.
In 2018, he joined Hall Core Drilling (Hall Core) and quickly ascended through the ranks. First, he was a Head of Production, then a General Manager and Operating Manager. As such, he helped turn the company into one of the biggest contractors in Africa.
In March 2023, Ignus became the COO of Hall Core Drilling and, in his words, aims to bridge the gap between the technical and commercial sectors of mining operations through the development of systems for analysis.
Questions
Grigor Topev: Hi Ignus, thanks for taking the time to do this interview. Let’s start at the beginning: why did you choose Geology for your university degree?
Ignus Storm: Despite my lifelong dream of studying medicine, circumstances led me down a different path, and I ended up studying Geology instead. However, my passion for physical science never wavered, and I found myself intrigued by the subject matter from the very beginning.
Interestingly, my father’s hobby of collecting rocks also played a role in fueling my fascination with geology. As I delved deeper into the subject, I found myself drawn to the practical applications of geology in the field of mining engineering. The operations aspect of mining in particular captivated me, and I ultimately decided to pursue a Master’s degree in mining engineering to further explore this interest. Although my career path ended up being quite different from what I initially envisioned, my love of science and the natural world remains at the core of everything I do.
GT: How did you start working at Hall Core Drilling?
IS: I joined Hall Core Drilling after being recruited from Basil Read Mining, where I served as a Technical Manager. Hall Core was searching for someone with experience in mining operations, specifically drilling, and they needed a candidate who could better understand and manage their drilling activities. They were looking for someone with experience working at a larger mining company and with a strong technical background.
My skills and experience matched their requirements, and I was offered the role. Since starting at Hall Core Drilling, I have been able to apply my technical knowledge and experience to oversee drilling operations and ensure we execute the highest quality of work. My time at Basil Read Mining prepared me well for this role, and I have been able to use my expertise to make valuable contributions to the Hall Core team.
GT: What’s the Hall Core’s story? When was it founded? How has it developed over the years? What were the biggest projects ever completed?
IS: Hall Core was started by Kobus Halliday with a single drill rig in the early 2000s in the small South African town Brits. The current owners bought the business from Kobus in 2007 and set out to build a sustainable exploration business by establishing a solid track record and offering unique value-added services to their clients. The business has evolved over the years and today Hall Core makes use of some of the most advanced technology in our industry to enable the team to supply safe and relevant information to our clients in their drive to deliver services that reach ‘Beyond the Core’.
GT: One of the highlights of your time as Head of Production is a program for increasing drill bit life. Many have tried achieving an improvement, though few have succeded. Tell us more about the program. Was it related to R&D or to the selection of the most efficient drill bit (price to performance)? Also, could you give some tips and tricks to our readers?
IS: We improved the average bit life by about 20% from 2019. This was achieved purely by selecting the correct bits, which we accomplished through infield testing and desktop studies. Our research has led to understanding of the geology and most importantly drilling muds management. It is incredibly important that the correct chemicals are used, and drill cuttings need to be separated from drilling fluids before being pumped back down the hole. A large portion of the success in increasing bit life was incentivizing exceptional operational performance. We further embarked on a campaign to teach operators and drill crews about the benefit of increased bit life and increasing time on the face; drilling. We have also implemented spot incentives for drill crews that get exceptional life out of drill bits.
GT: You worked closely on a project with Anglo American in 2019. Please tell us more about their operations at that time.
IS: In 2019, this project was started with only 14 drill rigs at a platinum mine in Limpopo, challenges and negative aspects are you facing?
South Africa. This project is now by far the biggest Hall Core has been involved in. We currently operate 35 core drilling drill rigs with a team of about 250 people. Since the start of the project, four years ago, we have drilled more than 300 000 m (984 250 ft), of which 150 000 m (492 126 ft) were drilled in 2022 alone.
GT: I absolutely must ask: did you try to do some drilling while in the field?
IS: Yes, we are incredibly excited about this innovation, a first in our industry. We are busy replacing the mechanical over hydraulic valves of the controls on our machines in the fleet with electric over hydraulic solenoid valves. The machine is then operated from a distance via a wireless remote. We have completely removed the operator from the line of fire. We initially converted one machine as a trial and after a year of testing, we have now started to convert the rest of our fleet. One machine a month at the premises of our development partners, who are experts in the field.
‘We improved the average bit life by about 20% from 2019. This was achieved purely by selecting the correct bits, which we accomplished through infield testing and desktop studies. Our research has led to understanding of the geology and most importantly drilling muds management. It is incredibly important that the correct chemicals are used, and drill cuttings need to be separated from drilling fluids before being pumped back down the hole.’
IS: Unfortunately, I did not. The mine operations have very strict rules regarding the operation of machinery if you are not qualified and permitted. I have operated machines outside these operations but limited to the most basic of functions.
GT: Another thing I noted is that you are currently implementing remote-controlled drilling operations. How’s that going, what rigs are you using, and what
GT: Please share with our readers more about the drilling industry/market in South Africa and Hall Core’s place in it.
IS: The current position of the mining industry in South Africa is heavily influenced by commodity price volatility due to a weak currency, which has a major impact on the funds available to the sub-industry. The industry’s instability is further exacerbated by social and community-related obligations. Increasing work stoppages, corruption, policy and regulatory uncertainty and the lack of investment incentives are further eroding the potential profitability of mining operations, which further influences exploration expenditure and new project development. With the substantial mineral endowment of South Africa, it is concerning that exploration expenditure is at the lowest levels observed in decades.
Hall Core Drilling finds itself in a very privileged position to be involved in projects on the scale at which we are currently operating.
GT: What are the most common challenges that drillers face when drilling in South Africa? What solutions does your crew come up with?
IS: I believe that drilling crews find it difficult to adapt to new technologies. Most of the drilling crews, and especially operators, are old guard and rather set in their ways. Introducing new technologies and ensuring that they are utilized correctly has been one of our biggest challenges. The first step is to get the buy-in from the direct supervisors and production managers and then rely on them to teach the crews on not only the use, but the inherent benefits these technologies could have for both the crew and their output. The on-boarding process takes time and patience, but if you persevere it can be done.
GT: Whenever we can, we ask about the record-breaking deep holes over 3500 m (11 483 ft) deep in Africa. Since you are from the younger generation, have you heard any stories about them? What is their role nowadays… are they part of the mostly forgotten industry lore, or do they serve as examples/teachings for the drillers?
IS: The deepest we have drilled since I have been involved was just over 1400 m (4593 ft). Not a lot of stories are shared, and I am not aware of any other contractors drilling that deep currently. Our biggest achievement thus far has been the drilling of over 150 km (93.2 mi) in just 12 months on our current project.
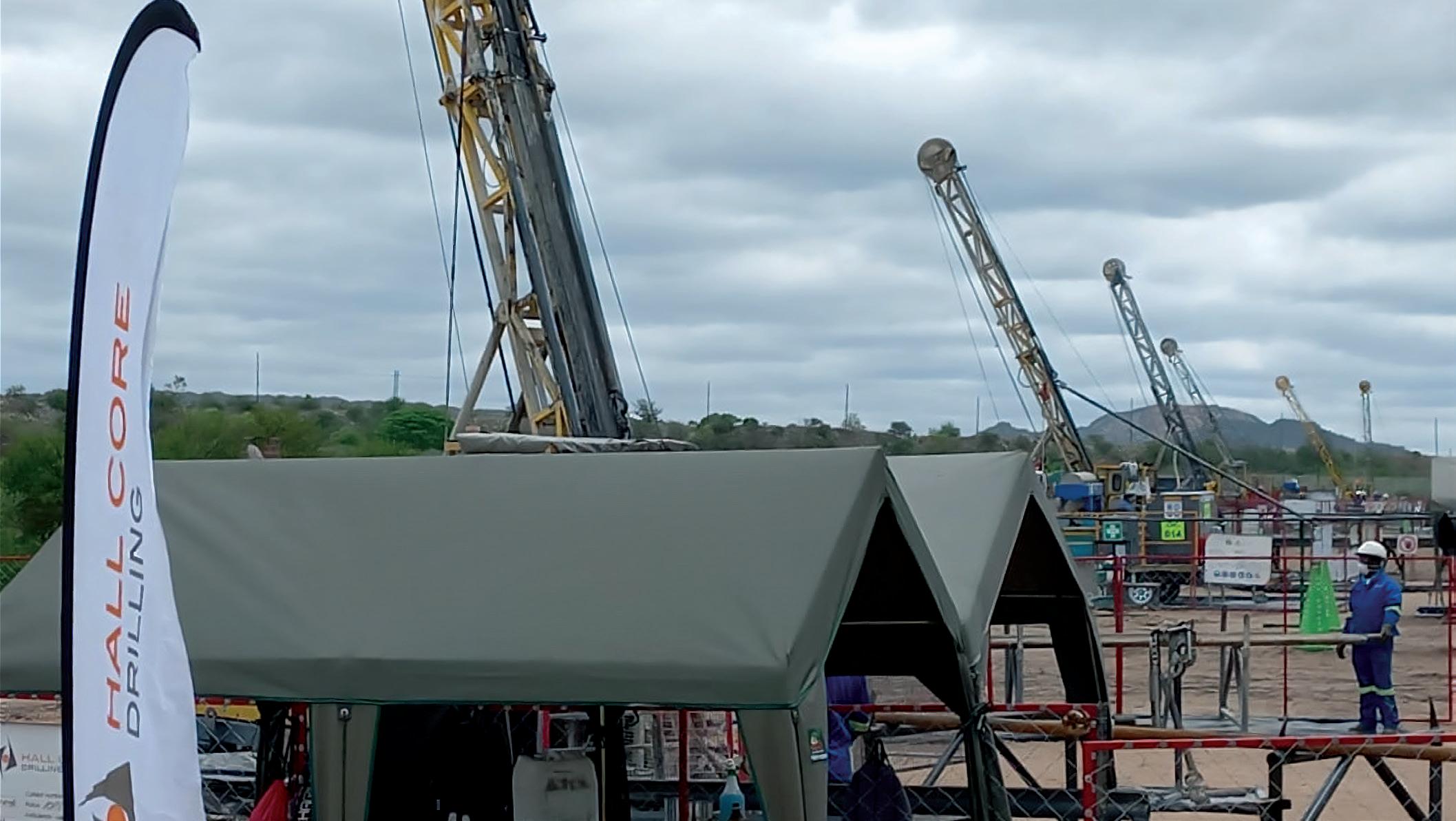
GT: Which are the leading core drilling companies in South Africa?
IS: I would say that Hall Core is currently the leading core drilling company in South Africa.
GT: What are the hot spots for drilling in South Africa?
IS: I would say that there is currently a lot of drilling taking place in the following areas:
• Limpopo on the Bushveld Complex primarily for PGMs;
• Northern Cape for Iron ore. There are talks of drilling for gas in the Northern Cape, as well as offshore, but to my knowledge, this is not so far advanced yet. Other than the big projects in these two provinces, other projects would likely be very small in scale and scattered across South Africa.
GT: Which directional drilling methods are being employed in South Africa? What is your opinion of this drilling technique? What makes it practical?
IS: Hall Core currently only uses directional wedges. We have not really used downhole steering motors for our current projects.
GT: What is your definition of a good driller?
IS: A driller that consistently drills the scheduled meters. Consistency, day after day after day. One that shows no massive spikes in production days and then very poor days thereafter. They take care of the bits, manage their drilling fluids, maintain good housekeeping, and have their paperwork in order. Most importantly, a crew that makes safety their priority almost always proves that the production output naturally follows.
GT: How do you approach training Hall Core’s staff? What problems have you identified and resolved during staff training?
IS: There is a lot of cross-pollination between employees, and we tend to train each other internally. Where OEM training or legal training is required, we utilize accredited training providers and our employees are trained and certified by them. We then have internal assessments to verify knowledge. Furthermore, the mine assesses the employees, too. There are quite a lot of checks before employees are certified to grab the controls of machinery.
GT: In the process of doing this interview, you became the COO of Hall Core. Congratulations! What is your vision for the company? What are your first tasks?
IS: As the newly appointed COO, my vision for Hall Core Drilling is to continue to build on our success and steer the company towards becoming the preferred diamond drilling contractor on the African continent, if not the world. Our aim is to grow in stature and change people’s lives for the better wherever we work.


To achieve this vision, we will maintain the utmost regard for safety as a top priority, and we will continue to prioritize innovation at our core. Our goal is for Hall Core Drilling to be recognized as the most innovative, productive, and safe drilling contractor in the industry.
We will work tirelessly to stay at the forefront of the industry by embracing emerging technologies and techniques that can enhance our capabilities and allow us to provide better solutions for our clients. We will also invest in our people and provide them with the tools, training, and resources they need to excel in their roles and deliver exceptional results.
In short, my vision for Hall Core Drilling is to build on our strengths, prioritize safety and innovation, and become the contractor of choice for diamond drilling projects around the world.
GT: Now being COO, how does your dayto-day work change? Are there things that you need to learn/skills to develop?
IS: As the COO, my day-to-day work will largely remain focused on ensuring that our day-to-day operations are managed safely and efficiently. I will be responsible for overseeing various aspects of our business, including production, logistics, and quality control, among others. I will also work closely with other senior leaders within the company to develop and implement strategies that will help us achieve our goals and grow our business.
While I have extensive experience in the industry, there will undoubtedly be things that I need to learn and skills I need to develop in order to excel in this new role. However, I am excited about the new opportunities that this role presents, and I am eager to learn and grow in my new position.
One of the biggest challenges that I anticipate will be learning to delegate effectively. As the COO, I will need to rely on my team to help me manage various aspects of our business. This will require me to trust in their abilities and provide them with the support and resources they need to succeed. I am confident that with time and practice, I will develop the skills I need to delegate effectively and lead our team to success.
GT: I noted on LinkedIn that you’ve stated that you aim to bridge the gap between the technical and commercial sectors of mining operations through the development of systems for analysis. What does this mean and how can companies turn this into reality?
IS: Bridging the gap between the technical and commercial sectors of mining operations means creating a more cohesive and integrated approach to mining. Often, the technical and commercial sectors of a mining operation work in silos, which can lead to inefficiencies, communication breakdowns, and missed opportunities. By developing systems for analysis, companies can bring these two sectors together and create a more holistic approach to mining operations. These systems for analysis could include tools and techniques for data collection, analysis, and reporting that allow technical and commercial teams to work together more effectively. For example, companies could develop software platforms that integrate data from various sources, such as geological models, production data, and financial data. This could allow technical and commercial teams to analyze this data together and make more informed decisions about mining operations.
To turn this vision into reality, companies will need to invest in technology, talent, and training. They will need to develop or acquire software platforms and data analysis tools that can integrate data from various sources. They will also need to hire or train personnel with the skills to work with these tools and analyze the data effectively. Additionally, companies will need to foster a culture of collaboration and communication between technical and commercial teams, encouraging them to work together and share information.
GT: Is there anything you’d like to see changed in the relationship between a drilling company and the Client?
IS: A few years ago, my first answer would have been more transparent communication and an increasing sense of collaboration. In recent years, there has been a significant drive from our clients to promote a collaborative and partnership-based relationship, which has changed the way we communicate. This has had considerable net positive impacts on our operations.
GT: What would you like to see improved or fixed, within the drilling industry in South Africa and the world in the next ten years?
IS: I believe the exploration sub-industry outside South Africa is quite healthy and an increase in expenditure can be observed over the past few years. The South African focus remains on social and economic development, but a clear method to achieve this is often not discussed. Globally, the relationships between tax incentives, economic development, capital, policy, and regulation are prominent. Research suggests that those countries realizing significant growth in the sub-industry understand what mechanisms are required to ensure the sustainability of the sub-industry. A clearly defined program to stimulate growth needs to be formulated. The government needs to work closely with the private sector to determine if the current proposed mechanisms will be sufficient to ensure the growth of the industry. Reform cannot be formulated in isolation from the government. Without the support of the private sector, the programs will not be successful. The exploration sub-industry is vital in ensuring the sustainability of the mining industry. South Africa should look to the countries where exploration is healthy and thriving to determine which mechanisms these countries rely on and then develop and focus on similar programs in South Africa. The development of policies and regulations that encourage investment must be ensured and implemented. C