
6 minute read
Made in Vidalia
VIDALIA MILLS LEADS THE WAY IN SUSTAINABLE AMERICAN TEXTILE PRODUCTION
By Christina Leo
China, Bangladesh, Vietnam—all places most familiar to us Americans from the labels on our clothes, our tools, our home decor. These nations have long dominated the international manufacturing industries, exporting products halfway across the world to us—and though the price tags on these products tend to be lower, the environmental and socioeconomic costs have grown, especially in recent years, to be astronomical. Producing enough material at a fast enough rate to make packing and shipping clothing across thousands of miles profitable, it turns out, largely depends on poor quality of life for overseas workers and wasteful energy expenditure. This says nothing of the effects of the lost local industry in communities across our own country.
But things don’t have to be that way. What if the future did, in fact, look a little brighter? And what if part of the solution lay, of all places, in a refurbished Fruit of the Loom factory in Vidalia, Louisiana?
Vidalia Mills, the cotton textile manufacturer located just across the border from Natchez, Mississippi, has recently made a more visible name for itself during the present COVID-19 pandemic, when it converted much of its production to face masks for civilians and health care workers. Founded in 2014, the mill specializes in performance yarns and premium textiles— particularly top-quality selvedge denim jeans—with a focus on sustainable, home-grown production that still competes with overseas countries’ lower labor costs. Under the leadership of Managing Director Daniel Feibus and Senior Advisor Robert Antoshak, the mill has provided more than one hundred new jobs to the Vidalia area, along with industry prestige, and draws clients from high-end denim brands like Imogene + Willie and Raleigh Denim.
Even the selvedge looms themselves come with more than a bit of a reputation, many of them Draper X3s salvaged from North Carolina’s now-shuttered Cone Denim White Oak facility. Rare finds, the looms are responsible for the fine quality threads and jeans produced in Vidalia, and, according to Antoshak, made a touring group of designers tear up a bit upon first sighting them.
The little town of Vidalia also has some history of its own. Perhaps you’re familiar with its founder, the colonial Spanish nobleman Don José Vidal. Or perhaps you’ve heard something of “The Great Sandbar Fight” of 1827, which involved none other than famed—if contemporaneously less admired— Louisiana resident Jim Bowie, who was seriously injured when he stepped into the duel between Alexandria natives Samuel L. Wells III and Dr. Thomas H. Maddox’s supporters (Bowie was a supporter of Wells). The town’s most recent claim to fame is its status as the home of Louisiana’s first hydroelectric power plant and the largest prefabricated power plant in the world, the Sidney A. Murray, J. Hydroelectric Station, established in 1990. In recent decades, however, the town, like so many small enclaves in rural America, has lost much of its identity as a center of industry. Much like the formerly industrialized suburbs of Detroit, Pittsburgh, or Cleveland, rural cities across the U.S. have seen drastic population decline in the wake of job loss, with centers of manufacturing moving into larger cities, or else overseas, where products can be produced more cheaply at the expense of workers. This is exactly what Feibus hopes to change.
“It isn’t even this noble goal of altruism, necessarily,” said Feibus. “We just genuinely have a terrific work force in Vidalia. We see talent dying in general across the South and rural America, and I think that over the last thirty years there’s been a blind tradeoff there.”
The mill itself is a standout in American manufacturing, the only mill in the world which consumes one hundred percent sustainably certified cotton. It also partners with BASF CropScience’s e3 cotton, a program, which traces cotton from the seed to the farmer to the gin, all the way through to the merchant, mills, and retailers who sell the final product, whether it be t-shirts, masks, or denim jeans.
“A cotton mill in India will use significantly more water, around 2.5 times the traditional American process,” said Feibus. “In areas like that, where there’s already a surface fresh water shortage, globalization has taken over the industry so that people have to source water from father and farther away, leaving a lot of developing countries with a lot of environmental and social bills to pay.”

In Vidalia, cotton can be produced not only using the natural resources of the area—from the water of a hydroelectric dam to the employees to the cotton—but with unprecedented quality control.
For Antoshak, a philosophy major and a consultant for the fiber, textile, and apparel industry website, just-style. com, good business means that the ethics of quality and aesthetic are just as important as the finished product.
“It’s about understanding slow fashion versus fast fashion,” he said. “Older generations like mine are so used to overstuffing our closest with tons of cheap things we don’t need and creating waste, but I’ve noticed that younger generations are taking into account where their clothes come from and what they’re made out of. Buying fewer, highquality, classic items that last for years is much more efficient, and we like to showcase that every step of the way, even in the brands’ final packaging of the jeans.”

Vidalia Mills is the only mill in the world which consumes one hundred percent sustainably certified cotton, produced using resources—water, labor, and cotton—from the immediately surrounding area.
Photo courtesy of Vidalia Mills
Jennifer Crumpler, director of the e3 sustainable cotton program, knows that the more we progress into an age of awareness and technological advancement, the more important it is that we share the stories of the people who produce our goods, and ensure the ethics and quality of what we consume.
“No one is telling these farmers’ stories or connecting these players in the grand scheme,” she said. “I can’t think of anyone more sustainably-minded than a farmer. They work the land. They constantly have to do more with less. They’re so humble about what they do, so I’m excited to have this platform and advocate for them.”
Many people in the garment industry, she said, might have never set foot in a real cotton field before. That’s why she’s organized trips to bring brands and designers to places like Concordia Parish, to see the farms at work, help break down stereotypes, and bridge the gap between knowledge and experience.
“For us at e3, we work with our growers and their information,” she said. “Our three main goals are to be socially equitable, economically viable, and environmentally responsible. We watch the data and see how we can continue to be better, and to tell the story better to others who don’t know it.”
For Jennifer, even the cotton plant itself has an aesthetic mission.
“If you look at it closely, it tells its life story from beginning to end,” she said. “You can see the finger lengths of growth between branches, see where it may not have gotten a lot of rain one week, and plenty of rain in another.”
Like the narrative jointed in the stem of the cotton plant, or the recycling of one mill to produce another, or the revitalization of a town once prided on working hand-in-hand with rivers, the rural spaces of America may, in the end, be the new starters on the world of manufacturing’s more beautiful, ethical, and equitable playing field.
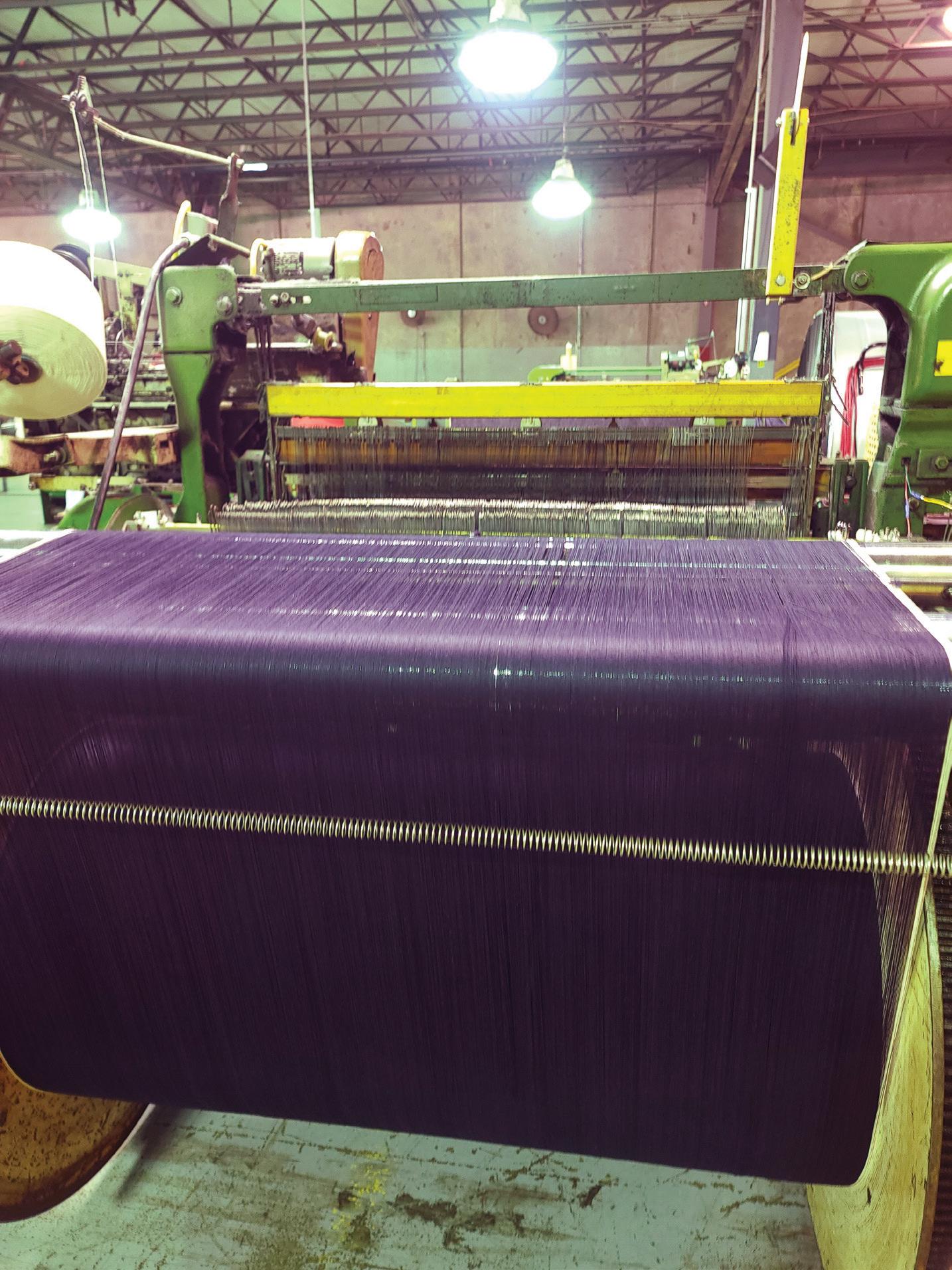
Vidalia Mills, once a Fruit of the Loom plant, now uses rare Draper X3 selvedge looms, which were salvaged from North Carolina’s now-shuttered Cone Denim White Oak facility to produce high quality American-made denim for comapnies such as Imogene+Willie and Raleigh Denim. The comapny has brought over one hundred jobs, as well as industry prestige, to the little town of Vidalia. Photos courtesy of Vidalia Mills.
Photos courtesy of Vidalia Mills

vidaliamills.com