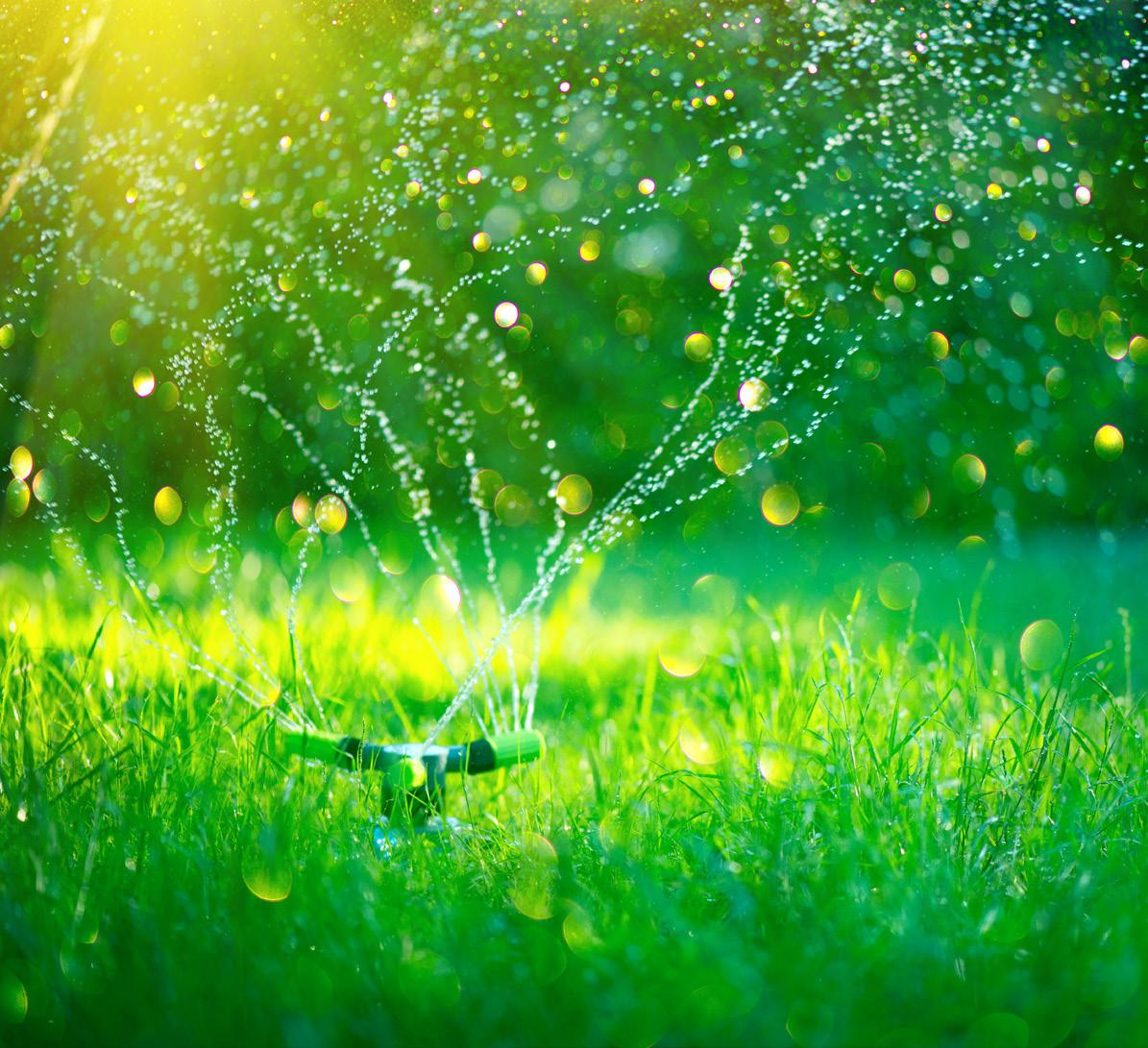
2 minute read
C x IN CHILLED WATER PLANTS
Retro/recommissioning can unlock remarkable savings in CHPs, and the Empire State Building stands testimony to that.
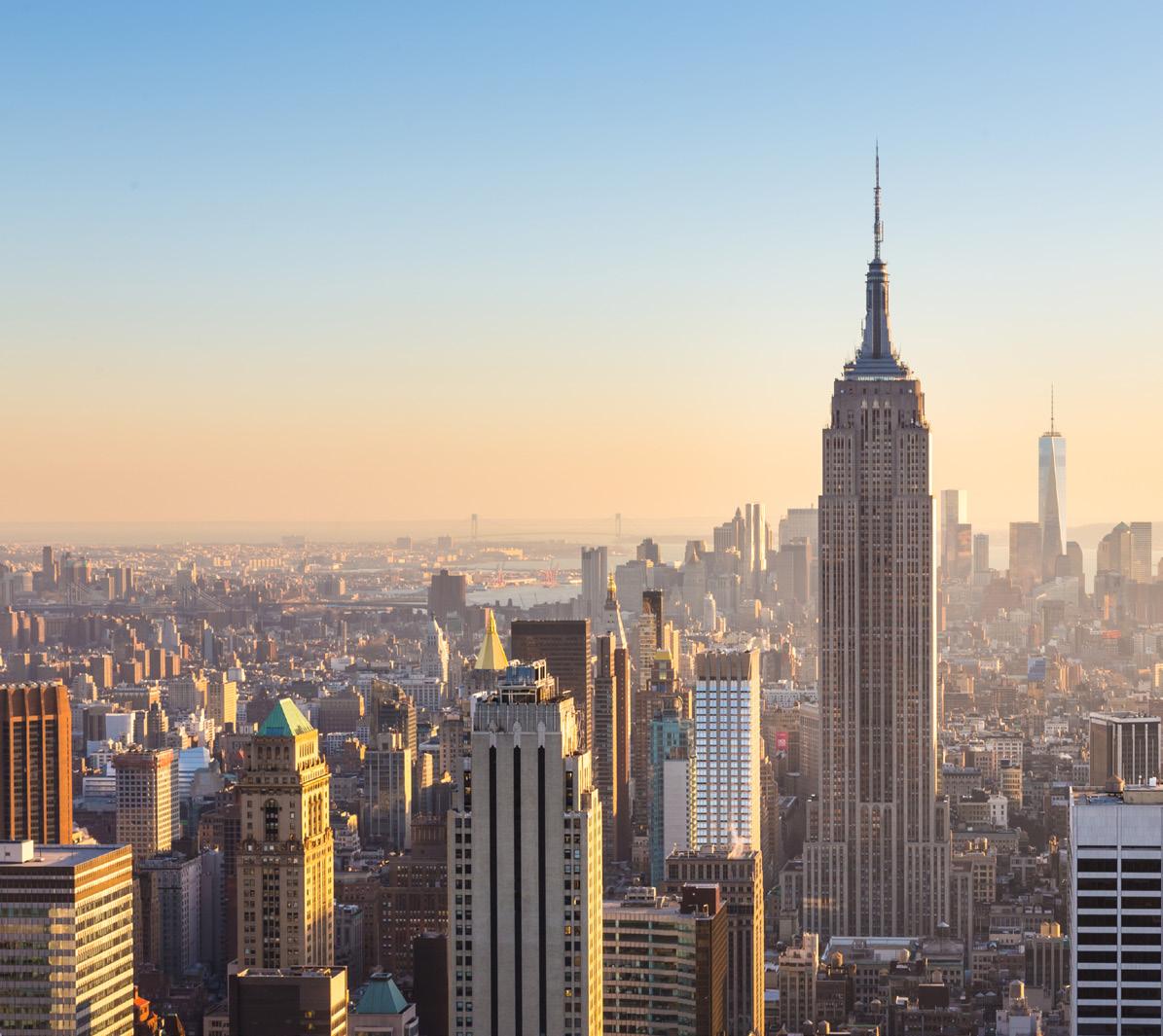
Advertisement
WHAT is energy management with respect to chillers? Currently, the industry standard chiller energy management practice is to provide enough cooling to meet the needs of the facility while minimising chiller run hours. This is either achieved manually by experienced operators or automatically by a building automation system or chiller plant manager automation system with operator oversight. Neither of these methods addresses the enormous energy savings of increasing chiller performance and operating efficiency, though.
The Empire State Building, in New York City, is an American cultural icon. Built in 1931, it remains the fourth tallest building in the United States. It is designed in the distinctive Art Deco style and has been named one of the Seven Wonders of the Modern World by the American Society of Civil Engineers. It is ranked number one on the AIA’s List of America’s Favorite Architecture.
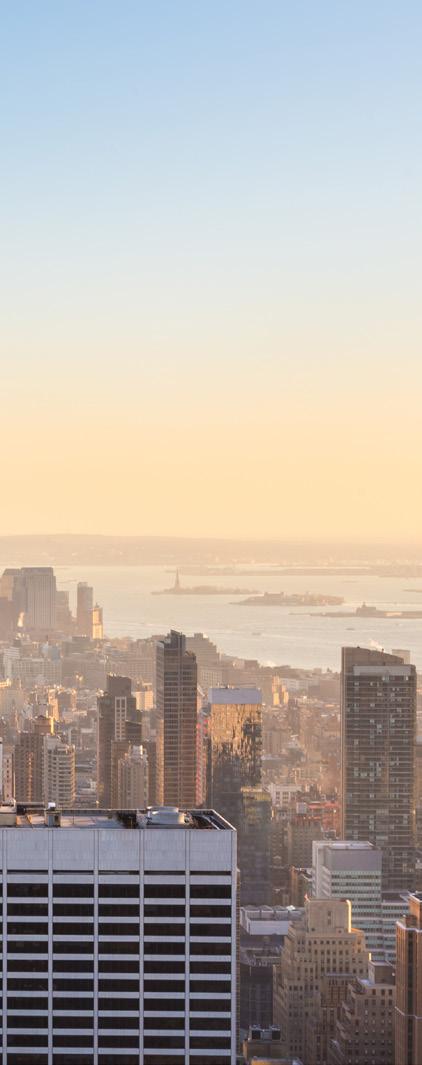
The building’s 10,000 RT plant includes electric- and steam-driven centrifugal chillers and is located three storeys below ground. The plant supplies chilled water to three zones: Low, medium and high. Each zone is a primary flow parallel chiller arrangement. Cooling towers are located on the ground floor in the open-loading dock area. Tim Dailey, the Director of Engineering at the Empire State Building, was looking for a way to save more energy in his facility. The Empire State Building had already been recognised as a LEEDcertified building and had incorporated almost every ECM (Energy Conservation Measure) available in the industry. The chilled water plant had VFDs on all its condenser and chilled water pumps, on its cooling towers and on all its electric-driven centrifugal chillers. Additionally, it had a stateof-the-art BMS/CMS operating and controlling the building and optimising the chilled water plant, so it seemed not much was available to further save power at the building’s 10,000 RT plant. Dailey still felt that his plant could save additional energy, and that’s when he contacted US Chiller Services to have a look at his plant to see if we could do something more.
After a brief inspection of the plant, we realised we could save at minimum 15% of the plant’s energy; and with the plant maintenance being put out for bid, we thought this would be an ideal opportunity to implement retrocommissioning of the plant, should we win the bid, which we did.
The year 2017 was used as the baseline, as all ECMs were fully installed and operational in 2017 and the savings achieved were already confirmed and proven. This was the perfect baseline for us to prove the additional savings we would achieve with our retro/commissioning services, which were all performed as part of our service agreement for the plant. The sweetener was that the iconic building did not require any additional investment for any savings achieved.
In 2018, we completely retro/ recommissioned the plant, paying particular attention to the electricdriven York YK centrifugal chillers. We utilised two parameters for savings verification: the chiller’s kW/ton performance and the 2017 vs 2018 utility bills, which were weather and occupancy normalised.
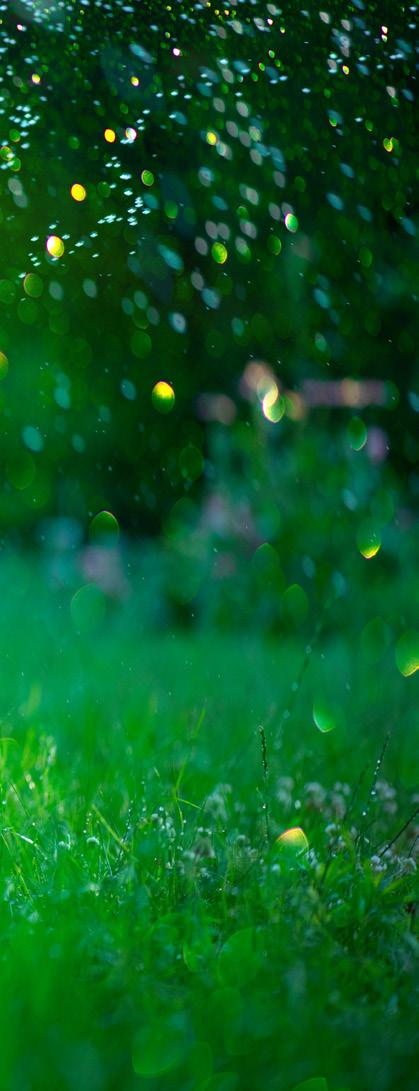