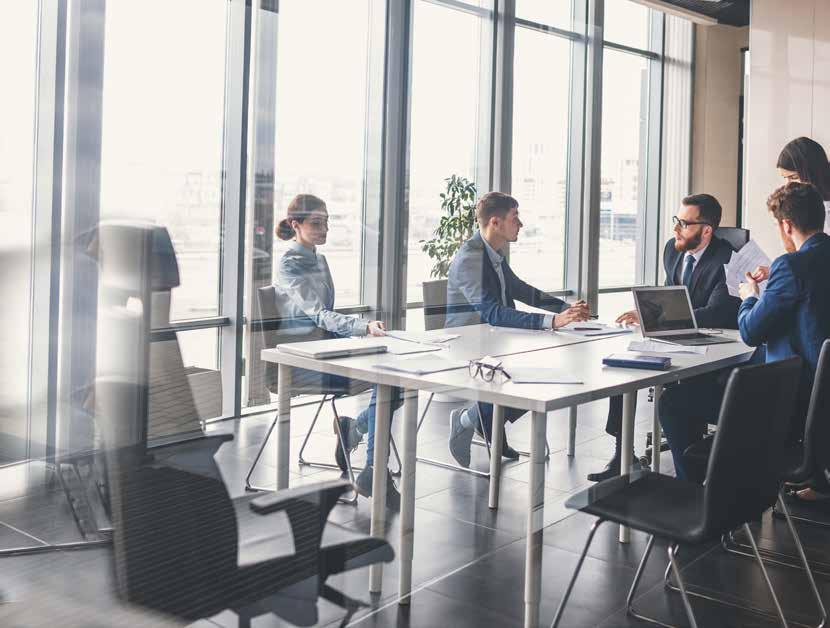
11 minute read
Oh no, not my chillers
from CCME - May 2021
by ccme.news
CONCLUDING PART OF A THREE-PART SERIES ON COMMISSIONING
LIGHT AT THE END OF THE TUNNEL
Advertisement
Today’s market is still suffering from poor commissioning-related competency and general lack of understanding, but it’s not all bad, says Lee Hewitt
he perception and understanding of commissioning and commissioning management in the GCC region is gradually changing, and I am pleased to report, it is for the better. It is a long road, but there is light at the end of the tunnel.
Thanks to the ongoing commitment of our Committee members, the GCC’s Commissioning Specialists Association (CSA) has seen evidence of this with a real desire to implement lessons learnt when speaking to clients, and an increased LinkedIn following, backed by the sharp uptake of applicants to join our education programme; we are seeing a 21% increase in applicants compared to previous years. More project specifications are calling for CSA-certified businesses or candidates, as developers are realising the added value of a quality service carried out by trained and experienced staff.
It appears the market has had time to reassess the negative impact of procuring the most cost-effective vendors to manage or execute the commissioning process. Whilst the fee may appear higher, it pales into insignificance compared to the cost when projects overrun and are repeatedly delivered late.
A great example of this is the current tsunami of work that is occurring in the data centre sector. The potential negative financial consequences if data centres are not finished on time – not to mention the reputational damage to the owner – mean that CAPEX costs, whilst important, are not the ultimate driver. These projects are fast track, technical and require experienced staff to deliver, so their investment is in quality companies to commission the facility on time, the first time around. Not wanting to make the investment would be a counterproductive move. Just think, you wouldn’t want to receive a COVID vaccine from a substandard manufacturer, would you?
Another positive as we all face this pandemic together is that responsible business owners and property managers are genuinely concerned that their buildings have been left inactive or are operating under capacity since the gradual


Lee Hewitt is Managing Partner, Core Emirates, and Chairman of GCC CSA. He may be contacted at
l.hewitt@core-emirates.com
return to the workplace. Noting the World Health Organization has emphasised the importance of having effective ventilation in a building, where airborne transmission is a known risk, the CSA has received many requests asking how best to reopen premises safely, whether that be in full or for partial occupation. The same approach has been taken to ensure the integrity of water systems and the management of risks associated, including Legionella pneumophilia bacteria, noting these are a legal responsibility.
Encouragingly, what the wider CSA community and I are seeing evidence of is the medium-term opportunities for the CSA to add value, taking into account the plethora of government initiatives across the GCC region. These include Dubai’s 2030 Integrated Energy Strategy initiative and 2040 Urban Master Plan, Oman’s 2040 Vision, Qatar’s 2030 National Vision, Saudi’s Vision 2030 and Bahrain’s National Development Strategy, to name a few.
These initiatives will provide the platform for the CSA and registered companies to educate and implement tried-and-tested processes that benefit all parties. One of these targets, in conjunction with the Building Services Research and Information Association (BSRIA), is to work closely with developers and introduce the Soft Landings framework. In essence, Soft Landings is a proven five-stage process to facilitate a unified transition between construction and occupation and, potentially, the remainder of its lifecycle.
1) Inception and Briefing – An opportunity for designer, constructor and developer to come together for initial discussions. 2) Design Development – Where the entire project team gains insights and learns lessons from similar projects and really starts to understand how the building will work once in operation. 3) Pre-Handover – A chance for operators to really spend some time getting to know the interfaces and systems before occupation. 4) Initial Aftercare – Where systems are fine-tuned, initial issues “ironed out” and post-occupant evaluation surveys (POEs) take place. 5) Extended Aftercare – Resolution of any issues from the POEs and recording of lessons learnt for future projects.
Currently, the absence of the above is negatively impacting energy efficiency, reliability and Indoor Air Quality during building operation. Problems such as mould growth, leaking ducts and general poor performance could have all been avoided if correct building commissioning and processes, such as Soft Landings, had been implemented.
In conclusion, today’s market is still suffering from poor competency and general lack of understanding, but it’s not all bad; moreover, it remains our mission to collectively raise the bar through education and professional delivery.
CPI Industry accepts no liability for the views or opinions expressed in this column, or for the consequences of any actions taken on the basis of the information provided here.
Dan Mizesko is Managing Partner/ President, U.S. Chiller Services International. He may be contacted at
dmizesko@uscsny.com
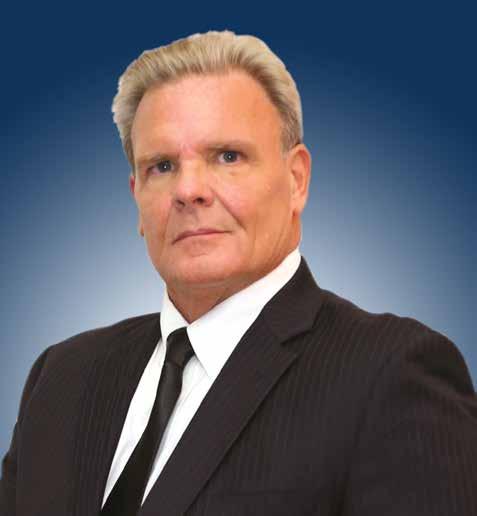
OH NO, NOT MY CHILLERS!
Equipment operators and plant owners are in denial or just plain unaware that most chillers are operating above their design efficiency, says Dan Mizesko
he evidence is clear, the majority of chillers and chilled water plants operate above their intended design efficiency (kW per ton). Most chillers operate above efficiency design, and I’m not talking about one per cent or two per cent here. I’m talking about 20%, 25%, 30% and even higher. I have seen chillers operating 60% above their kW per ton design.
What’s most frustrating is that the equipment operators and owners do not even realise their equipment is operating inefficiently and consuming excessive power or are in denial. Now, I know some of you reading this are saying, “Oh no, not my chillers!” or “Not my plant”. You are saying, “We have the most efficient chillers, and we have a CMS system and a SCADA system, we do all the maintenance as per the OEM manual, we have VFDs on all our pumps, towers and chillers.” Unfortunately, the bad news is that just because you have purchased the most efficient chiller in the world does not mean it's operating efficiently. Just because you are performing the maintenance as per the OEM manual does not mean your chiller is running efficiently. It takes substantially more than the recommended maintenance procedures to ensure your chillers operate as efficiently as possible. Isn’t that the goal to operate chillers and chilled water plants as efficiently and reliably as possible? Now, let me explain how I can state why most chillers do not operate as efficiently as designed.
OUR FINDINGS
U.S. Chiller Services from 2003 to 2012 analysed extensive data from operating chillers and plants in the Gulf region, from the newly constructed and commissioned plants to five-year-old plants. All were electric-driven centrifugal plants. What we determined was that the operating range of these chillers was from 0.98 to 1.8 kW per ton. Water-cooled electric centrifugal chillers in the Gulf region are generally selected and designed to operate in the range starting from 0.687 to 0.760 kW per ton. So, it was clear these chillers were operating 30% above design efficiency at minimum. Again, some of these chillers were just commissioned and put into beneficial service by the OEM field service department.
WE ARE NOT ALONE IN OUR FINDINGS
A survey report by the U.S. Department of Energy found more than 120,000 chillers in the United States are expending more than 30% in additional energy through operational inefficiencies. This is not a misprint – 120,000 chillers operating more than 30% above design!
A survey report by San Diego State University Energy Engineering Institute on 31 chiller plant sites across the United States found chillers that should be operating in a range starting from 0.65 to 1.00 kW per ton, according to the OEM specifications, were often actually operating in a range starting from 1.5 to 3.0 kW per ton and that most chiller plant operators had no idea how well their chiller plants were performing.
A report on 14 chiller plants by the Northwest Energy Efficiency Alliance found a substantial variation in plant energy efficiency ranging from 0.55 to 1.80 kW per ton.
A report by the California Energy Commission addressed the problem that buildings and chilled water central plants do not perform as well in practice as is anticipated during design.
The reasons cited were: • Improper equipment selection and installation • Lack of rigorous commissioning and proper maintenance • Poor feedback on operational performance and energy performance
FACTORY WITNESS PERFORMANCE TEST
Many companies who purchase centrifugal chillers for their facilities demand a Factory Witness Test of the chillers they are buying before accepting delivery and payment. The OEM Sales Engineer will select the chiller with a software selection program to predict the chiller’s performance. The buyer agrees to purchase the chiller based on the software selection program’s predictions of the chiller performance, including capacity part load and full load and also kW per ton, to name just a few of the parameter performance predictions. The Factory Witness Test confirms that the actual chiller performance matches the predicted performance, and the results serve as a benchmark.
AHRI STANDARD 550/590
The witness testing standard requires specific types of instrumentation and specifies chiller testing procedures and tolerances. It also requires that accurate measurement is an integral part of Witness Performance Testing. All of the following instrumentation must be calibrated and traceable to NIST, the National Institute of Standards and Technology: Power meters, temperature sensors, flow meters and pressure transmitters. This ensures the instrumentation meets the accuracy requirements of AHRI Standard 550/590. A copy of the latest calibration report is made available to the attendees of the Witness Test. As per industry standards, the factory test loop must have redundant measurement devices designed into test loops to verify test data. Redundant sensors are used to measure evaporator water flow, evaporator water temperatures, condenser water flow, condenser water temperatures and chiller power consumption. Agreement between the calibrated sensors confirms that the data taken is accurate.
Some companies even require a ZeroTolerance Witness Test to be performed. In other words, the chiller MUST perform at its predicted design performance and, if not, the buyer can cancel the sale. I have been involved in many Factory Witness Tests over the years, and I can tell you it takes the factory days to prepare the chiller for the test, with the objective of getting everything right, so that the chiller performs as designed. Even with the days of preparation, the chiller will often not perform to design kW per ton. More days of adjustments must be done to finally achieve design performance, sometimes including changes to the chiller’s design. As and when the chiller is certified and meets design, a printout is given to the buyer to benchmark that the chiller performs as predicted.
Take a look at an OEM field start-up and commissioning sheet…
DESIGN CONDITIONS
TONS BRINE FLOW RATE TEMPERATURE IN TEMPERATURE OUT PRESSURE DROP PASS SUCTION TEMPERATURE
COOLER
CONDENSER
RECORD PRESSURE DROPS: Cooler Condenser
CONDENSER TEMPERATURE
CHILLER START-UP AND COMMISSIONING IN THE FIELD
Does anyone reading this think that when a chiller is started and commissioned in the field, it receives the same amount of attention, care and diligence as during a Factory Witness Test? Are the proper and precise tools and equipment utilised in the field, as during the Factory Witness Test? Is the same data looked at during the field startup as during the Factory Witness Test? Is the chiller kW per ton even checked during a field startup as it is during a Factory Witness Test? Finally, is the Field Startup Technician as trained and aware of how the chiller should perform as the Factory Witness Test personnel? Of course, the answer to all the above questions is NO.
After answering all the above questions with a “NO”, how could chillers ever operate as efficiently as designed? As the data shows, chillers do not operate as efficiently as designed. The primary reason is ineffective start-up and commissioning from day one of beneficial usage.
The above is a small section taken from an OEM commissioning manual. I want the reader to understand the design condition that the startup technician is to record. Does it mention kW per ton? No. Also, what’s interesting is that the flows are to be determined by pressure drop readings. The Factory Witness Test is performed with a calibrated flow meter; however, the startup technician sets design flow with an instrument that is not nearly as accurate as a flow meter. My point is that energy efficiency is not a priority or even checked during the initial startup and commissioning of the chillers.
With that being the case, if the chiller is not started and commissioned in the field with the same level of expertise, tools, equipment and data with an emphasis on efficiency, how can you expect the chiller to operate as efficiently as designed? The fact is that the chiller operated at design efficiency at the factory, and that was the last time it did.
Next month, I will explore chiller diagnostics tools that identify chiller inefficacies, restorative opportunities and optimisation to restore proper chiller operation and overcome the lack of rigorous start-up and commissioning.
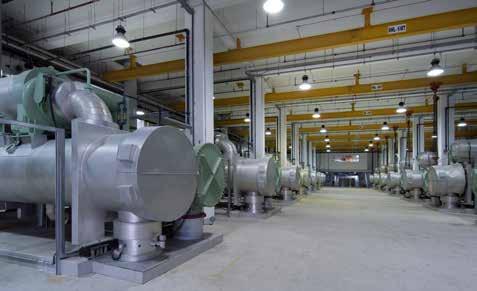