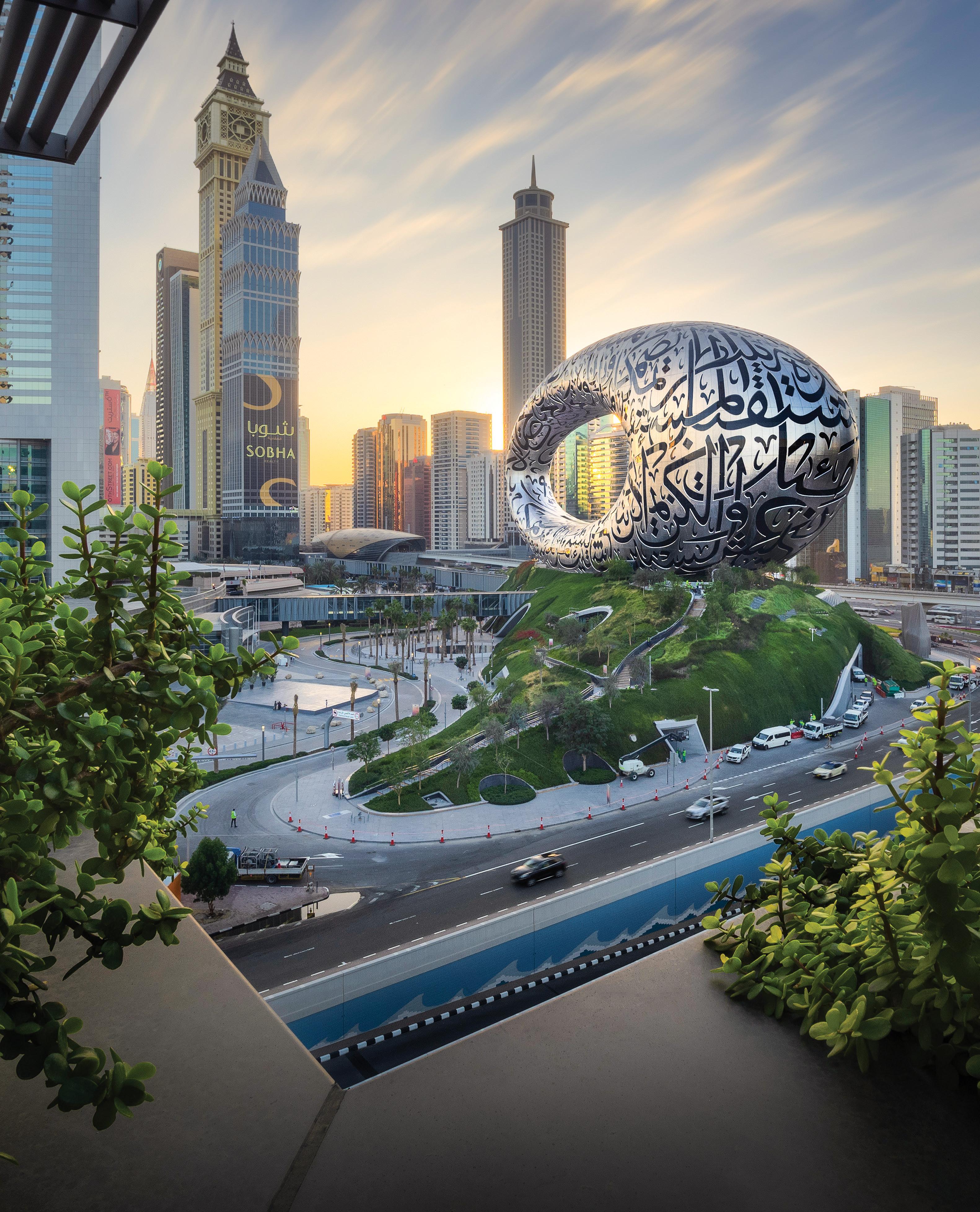
11 minute read
Project Profile
Museum of the Future
PROJECT NAME:
Museum of the Future
CLIENT:
Dubai Government
DESIGNER:
Killa Design
ENGINEERING:
Buro Happold
BIM IMPLEMENTATION AND COORDINATION:
Eversendai
SOFTWARE SOLUTIONS PROVIDER:
Trimble Solutions
Digital Futures
BIG PROJECT ME SPEAKS TO PAUL WALLETT, REGIONAL DIRECTOR OF TRIMBLE SOLUTIONS – MIDDLE EAST AND INDIA, ABOUT HOW THE SOFTWARE SOLUTIONS PROVIDER WORKED WITH THE PROJECT TEAM ON THE MUSEUM OF THE FUTURE TO SUCCESSFULLY DELIVER ONE OF THE WORLD’S MOST COMPLEX AND INNOVATIVE PROJECTS
n February 22, 2022, Dubai’s longawaited Museum of the Future opened to the world in a glittering ceremony that showcased the seven-storey, 77-metre-high structure in all its glory. Located in Dubai’s Financial District, the torus-shaped building is a show-stopping addition to the city’s ever-changing skyline, thanks to its dramatic design and lighting.
Occupying an overall area capacity of 30,548sqm and with a 1,024-piece façade covering a total surface area of 17,600sqm, the Museum of the Future has been called ‘the most beautiful building in the world’ by HH Sheikh Mohammed bin Rashid Al Maktoum, the Vice President and Prime Minister of the UAE, and the Ruler of Dubai.
Designed by Killa Design architects and engineered by Buro Happold, the entire building is symbolic of Dubai’s ambitions – its unique shape a representation of humanity, the green mound on which it sits a symbol of our planet Earth, and the void within it, the limitless future.
Now that the museum has been launched, it is expected to serve as an exhibition space for innovations and new technologies, as well as being home to a research centre, laboratory and auditorium.
However, as impressive as the Museum of the Future might be on the outside, what makes it truly impressive is the engineering and design work that has gone into bringing it into reality.
Due to its size and complex design, the Museum of the Future involved massive amounts of data generated during its design phase. In order to manage this, Eversendai, the company tasked with
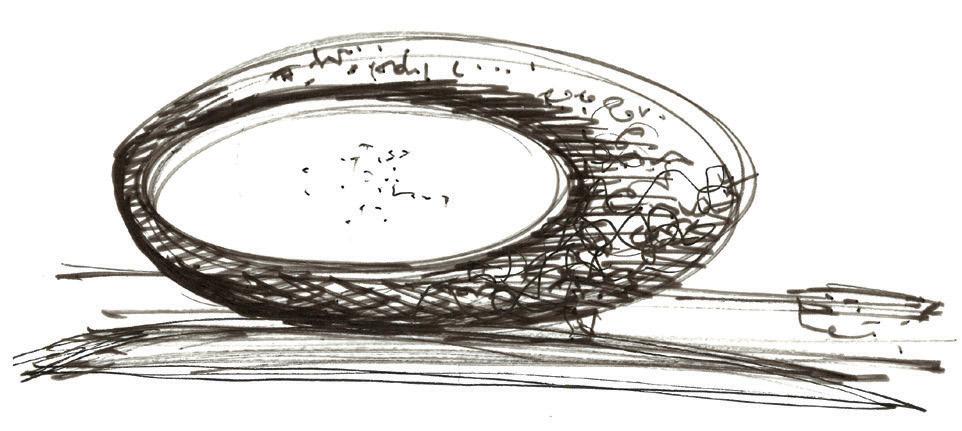
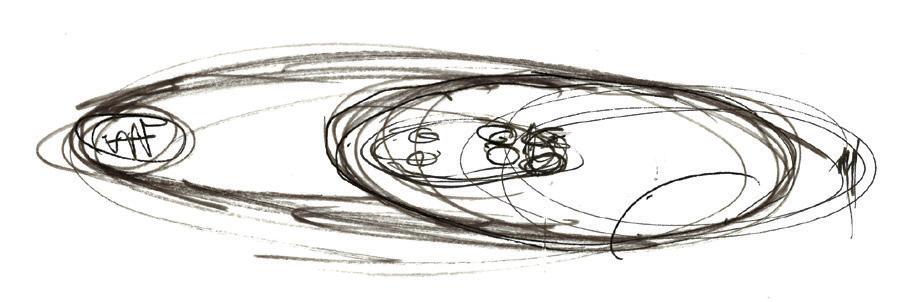
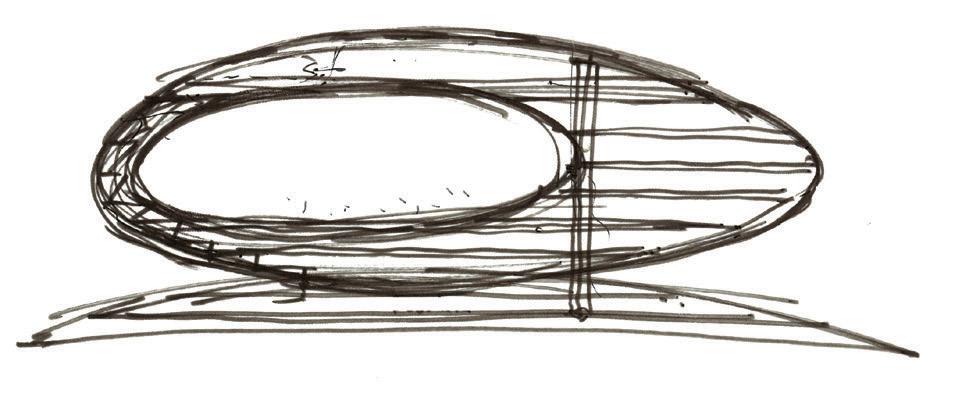
Complex designs
The size and complexity of the Museum of the Future’s design meant that advanced construction technologies were necessary to build it.
High level of detail
Tekla Structures was utilised on the project because of its ability to include high level of details required for construction. overseeing the BIM implementation and coordination for the project, brought on board Trimble, the global construction solution provider, and its suite of products to help manage the process.
Therefore, in this interview, we speak to Paul Wallett, regional director, Trimble Solutions – Middle East and India, to learn how the company’s advanced construction technologies and software solutions were used to enhance and simplify the details and workflow in the design, fabrication, and coordination phases of this landmark project.
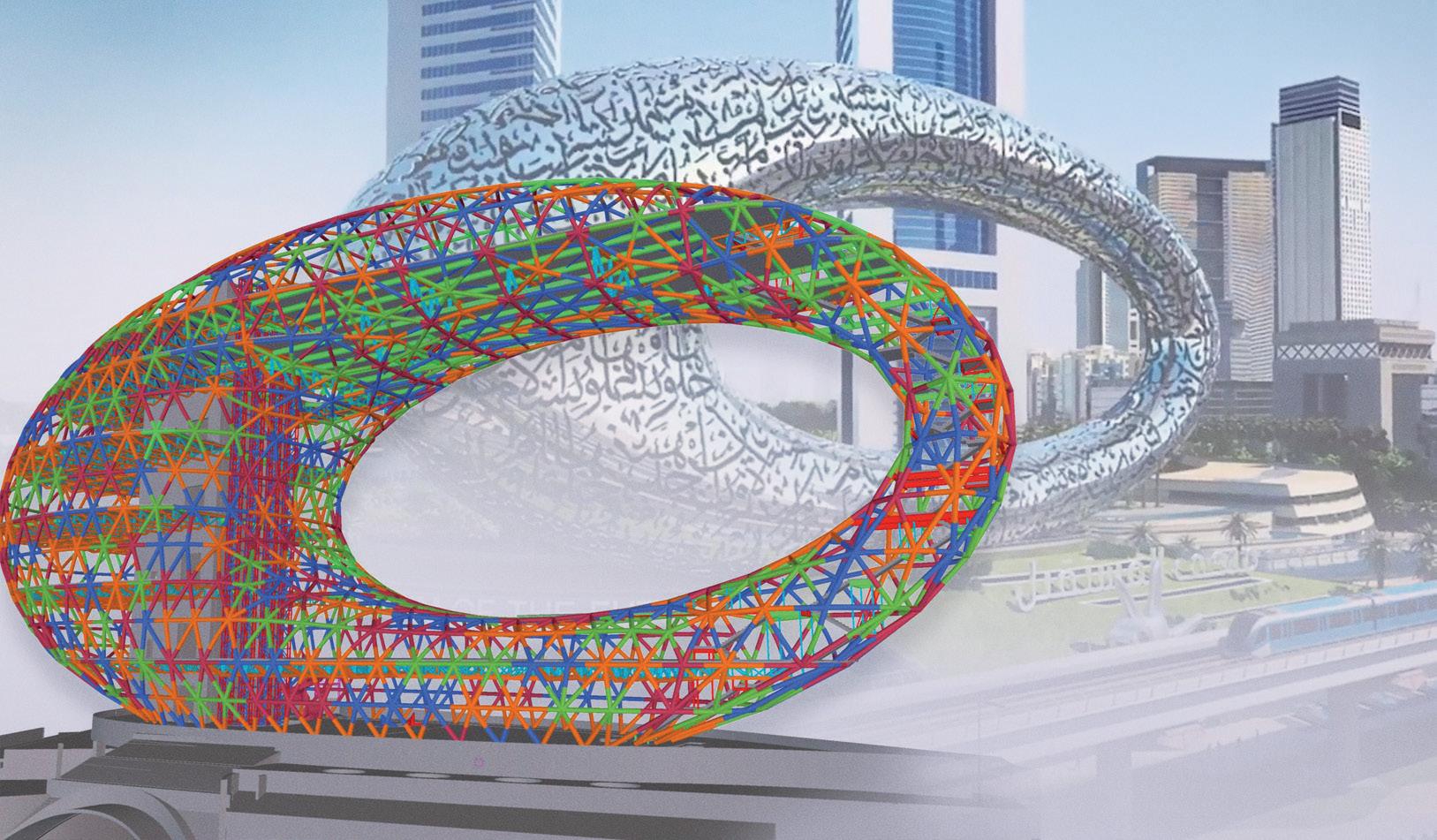
How did Trimble get involved with the Museum of the Future project? We have been here in the region for more than two decades with a proven track record of offering the best-in-class construction technology solutions. Our flagship product Tekla Structures is the solution of choice for most fabricators in handling unique and complex projects. Leading industry players in the region such as Eversendai has implemented it to achieve Complex Geometry structures modelling, generation of detailed Fabrication and Erection Drags, electronic data such as NC /DXF and profile cut Xml data as well, in an easy manner.
Eversendai used Tekla Structures for its ability to include high level of details required for construction, and on many projects across the region. Some of the projects they have delivered include: the KAFD Iconic Station in KSA, One ZA’BEEL Tower and One Za’beel Canopy in Dubai.
The Museum of the Future is one of the world’s most complex construction projects. It comprises of a concrete basement and core tower, with a highly reinforced concrete ring beam supporting the main steel diagrid structure up to Level 7, with composite concrete floor slabs. This design approach allows a columnfree interior space but requires a number of different and uniquely challenging elements within the building’s steelwork.
There were several contractors and subcontractors involved in the construction process of the Museum of the Future. Eversendai oversaw the project’s Building Information Modelling (BIM) implementation and coordination, connection design, shop drawings, erection engineering study
and stage analysis, workshop fabrication drawings, supply, fabrication, and erection of structural steel works. In order to achieve all this, they turned to Trimble’s various solutions to streamline and simplify the entire project execution.
What were the requirements from Eversendai when it came to choosing the right software solutions? For a project as complex as the iconic Museum of the Future, Eversendai needed complete collaboration, coordination, and precise data for the project lifecycle. Our advanced structural BIM software is known for these functions and best suited their needs. The software emerged as the potent tool behind the success of the Eversendai’s project team due to its powerful 3D modelling capabilities and flexibility to open API options that gave the executing team a large scope to explore and develop routines to do modelling and detailing accurately in a relatively short time with a high degree of precision.
Considering the complex geometry as well as the intricate shape of the structure and also provision of multistaged construction pre-set requirements of CMES Analysis, Tekla Structures had played a vital role in concluding the Engineering and Detailing activities within the project deadlines.
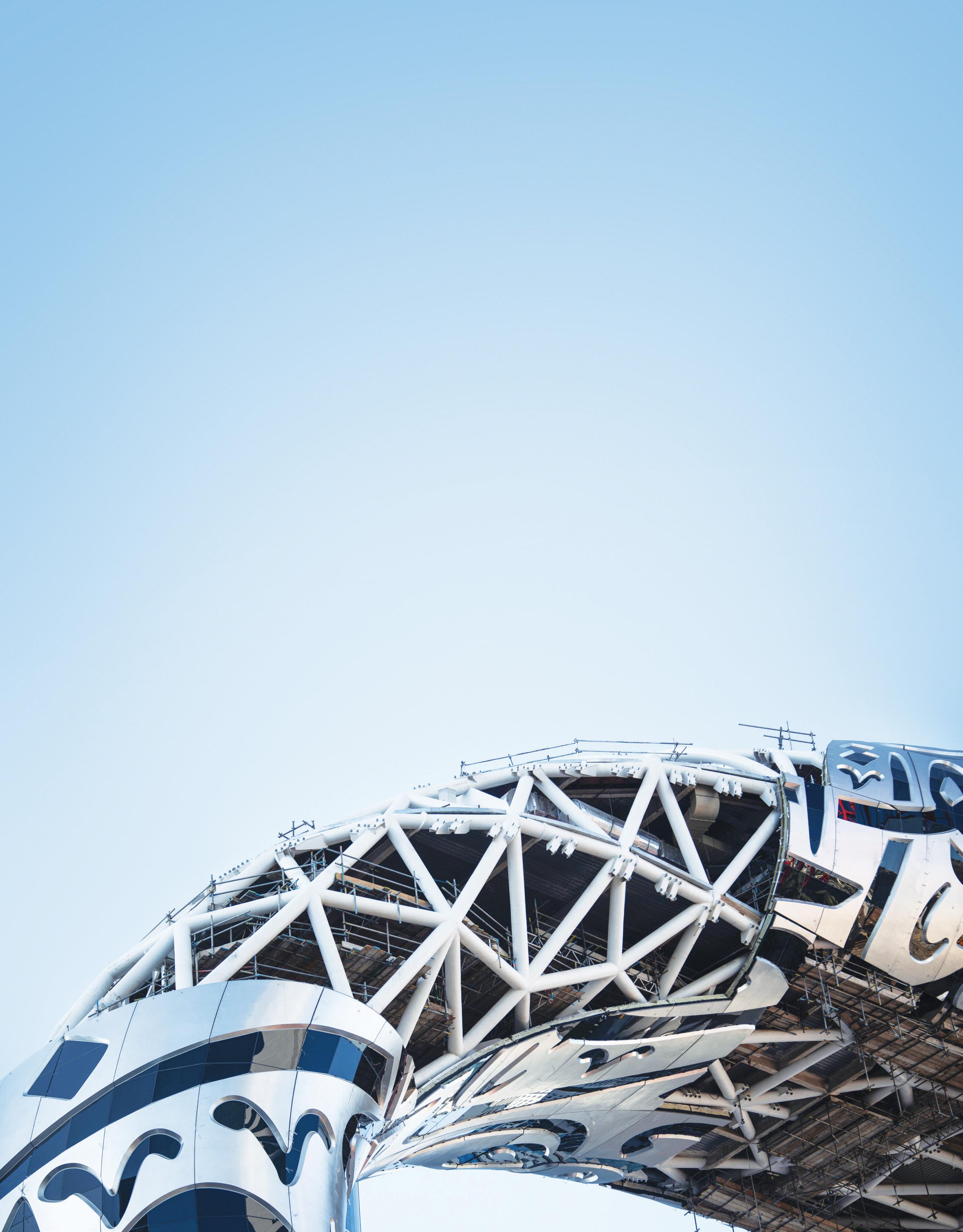
Eversendai has mentioned that the software enhanced and simplified details and streamlined workflows – can you explain in more detail what that means? One of the most interesting aspects every steel building has is thousands of unique parts and earlier the logs of these parts were maintained manually. However manual implementation for structures like the Museum of the future is extremely difficult. That’s why Eversendai detailed in 3D using Tekla Structures. The software has an outstanding level of detailing capacity, especially with the complexity of calculating the setting out of the curves etc.
The software does the math required to produce the 2D piece drawings that the fabricator can use and then assemble all the pieces on the ground into the complex 3D shape it needs to be for the erection and for transportation to site. That’s where it’s complex and very difficult.
Further, the executing team used Trimble Connect, an open collaboration tool as the Common Data Environment (CDE) that connects the right people to the right data at the right time. This enables informed decision making and enhancing project efficiency. It allowed the team to identify clashes with other trades, such as roofing, facade, MEP and RCC contractors and were able to resolve the clashes in the design phase itself. This streamlined the workflow by bringing people, technology and information together to deliver the project efficiency on time with ease.
1,024
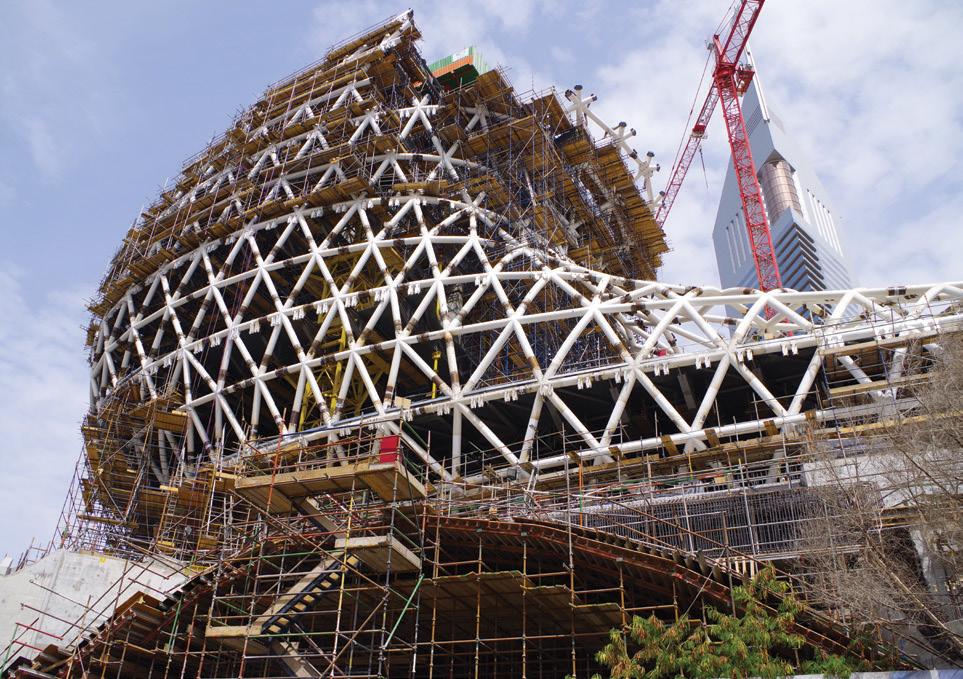

Number of panels on the Museum of the Future facade
Can you outline how the massive amounts of data that were generated during the design phase were integrated and correctly utilised? Given the size and complexity of the design, the Museum of the Future entailed huge amounts of data. Our software solutions provided stakeholders with the luxury of having information of intricate
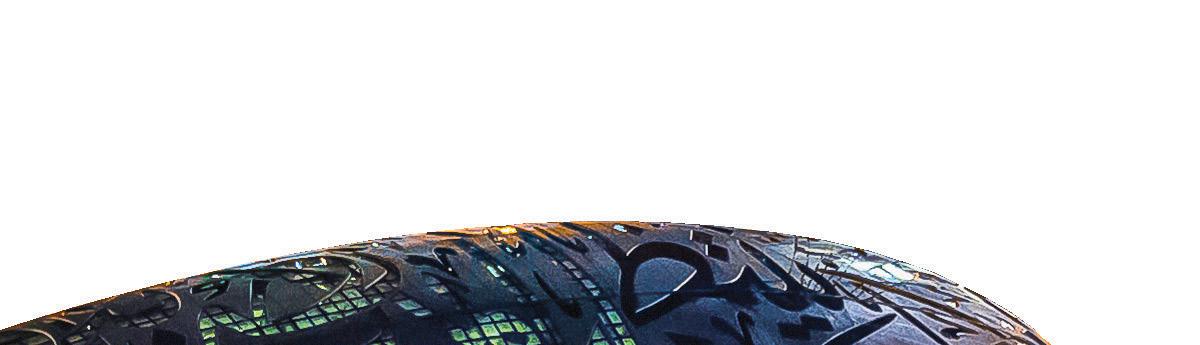
details involved in the construction of the Museum. Earlier the construction industry did not have this facility, but through the use of BIM, the industry is advancing.
Tekla Structures allowed easy and fast-tracking of the construction process, with access to studying each phase of the project. The stored data can now be utilised for future references or future projects.
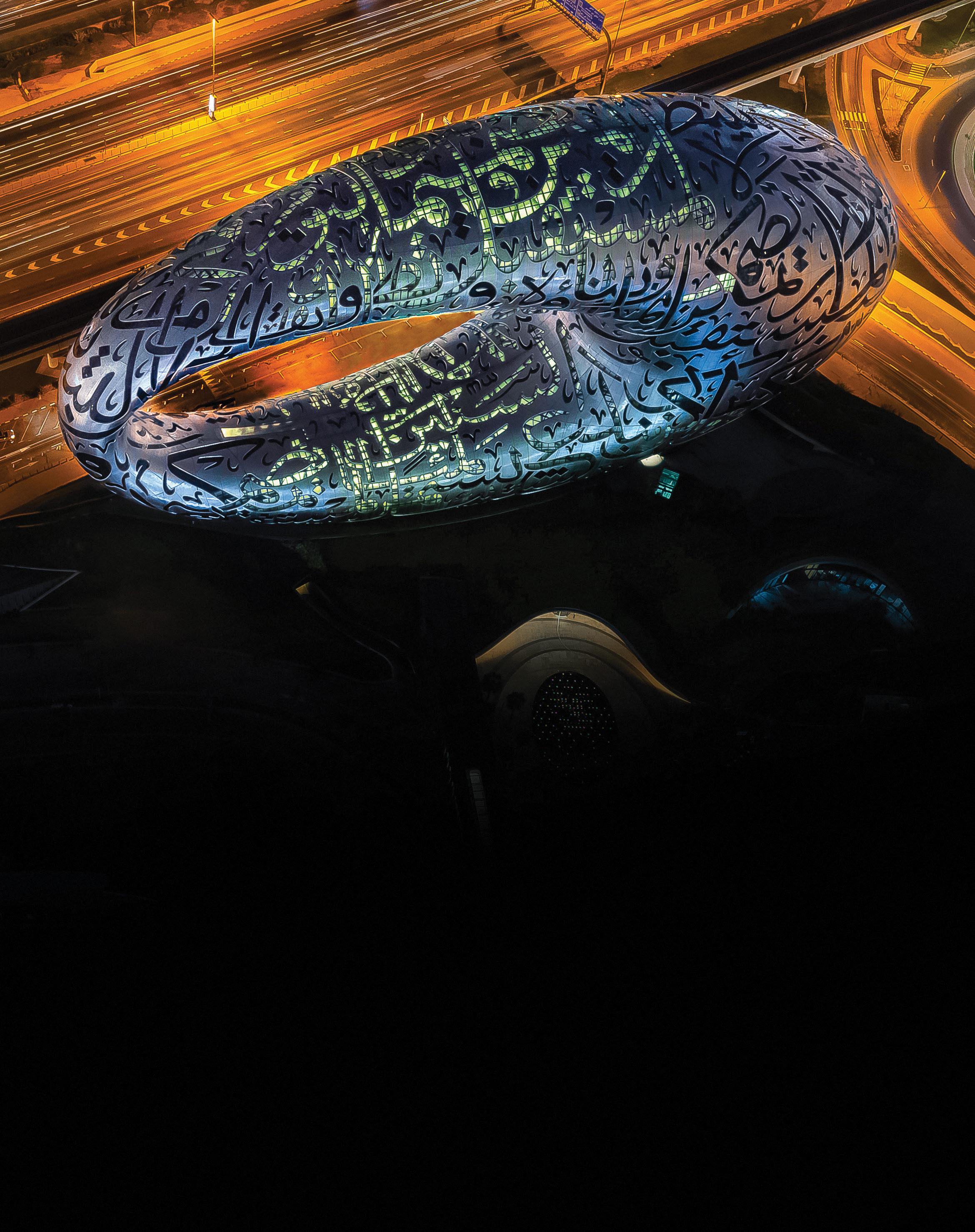
Can you put a figure on the improvement in efficiencies and performance that came from using Trimble’s software and provide more detail about that? The software’s interoperability helped ensure that the modelling of the Museum of the Future was quicker and accurate in comparison to traditional modelling methods. Further the BIM model generated on Tekla helped with clash detection in the early stage of modelling with other disciplines through data sharing. Tube NC files helped with accurate profile cutting of the pipes. Fabrication layout coordinates helped to verify the accuracy of fabricated assembly versus fabrication drawing.
Various project teams used multiple solutions: Trimble Connect was used as the Common Data Environment (CDE); Trimble’s SysQue was used for the intricate MEP design; while
Seamless workflow
Designers and contractors on the project utilised Trimble’s digital solutions to create a seamless, integrated workflow. Tekla Structures also proved helpful in designing the building’s highly complex structure and finally, our highly accurate Robotic Total Stations were used for the automated on-site layout, providing a true construction BIM workflow, digitally transferring the as office designed details to as positioned and constructed site placement.
The use of modern Trimble solutions helped reduce the rework by up to 65%, while we noted a 50% productivity boost and a 25% total reduction in energy consumption.
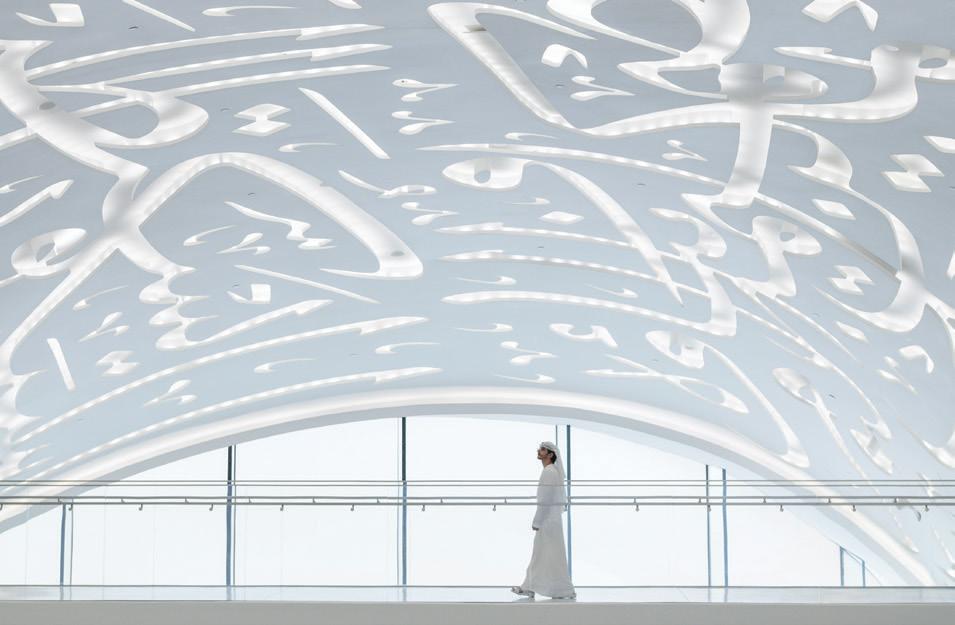

How were the other software solutions and products integrated together to give the project teams the best outcomes? Trimble’s SysQue is a solution that was integrated for the intricate MEP design of the structure. MEP designers and contractors used it for a seamless workflow from design to fabrication to construction phase. The solution improved the accuracy and consistency of the models. Robotic Total Stations were used for the automated on-site layout besides our structural design software, which proved helpful in designing the building’s highly complex structure.
Meanwhile, Trimble’s Hololens was also used to provide updated information and data, which was constantly transferred into Trimble Connect to be tested with the Trimble safety helmet that integrated the Microsoft HoloLens. It is the only device that is compatible with an industry-standard hardhat and certified for use in safety-controlled environments. The device integrated a
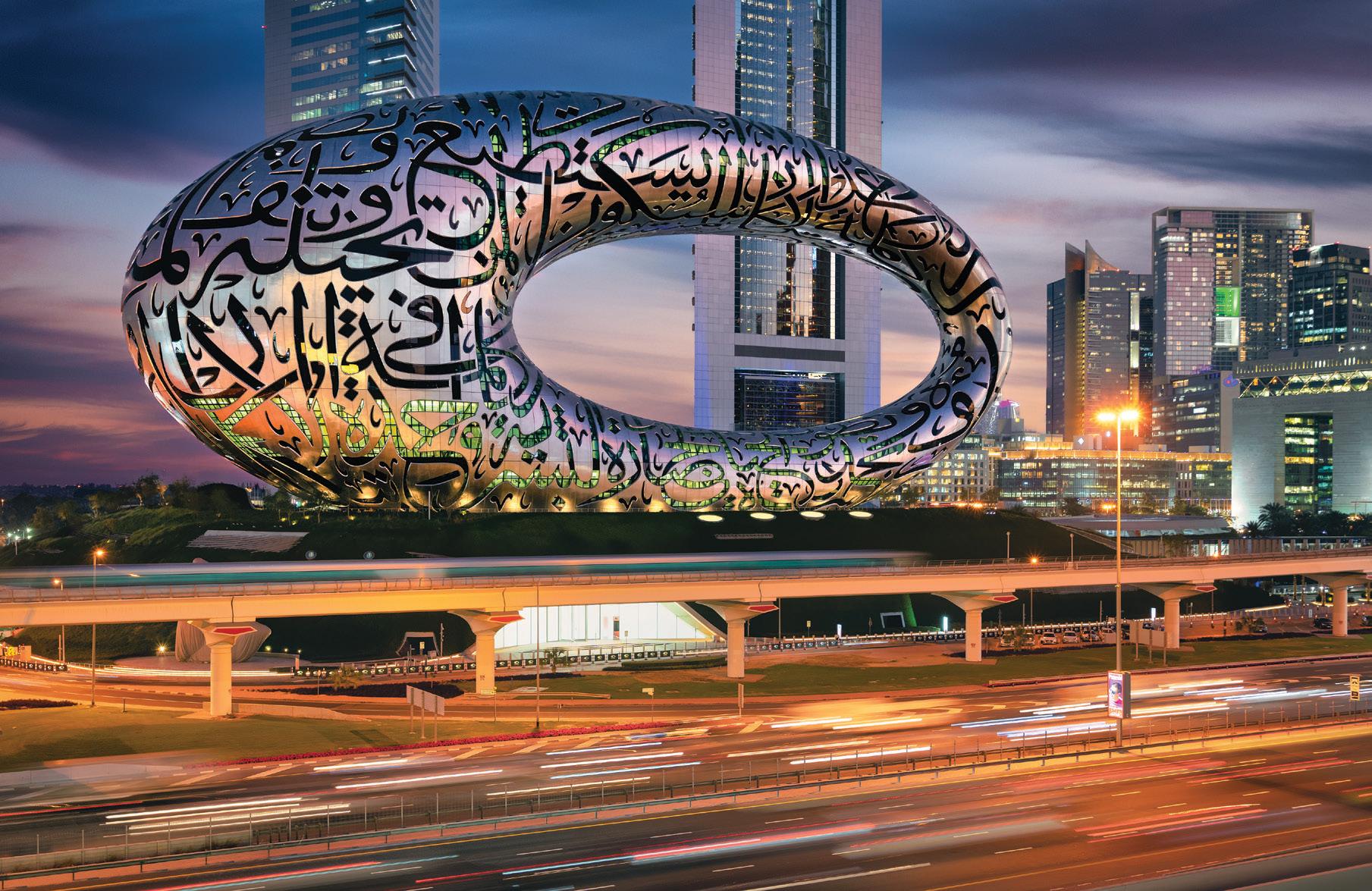
The Museum of the Future stretches structural engineering to its limits and showcases the creativity of what is possible using innovative modelling technology. We are proud to have contributed to its construction”
HoloLens 2 into a hardhat to produce safety-first mixed reality solution.
What were some of the challenges encountered on the project and how did Trimble help overcome them? The calligraphy and the building’s unconventional shape made it one of the most complex construction projects ever attempted. And there were quite a few challenges along the way. The Museum’s foundation, basements and main ring beam are in concrete. And given the complexity and heavy congestion of the rebar in the ring beam, TEKLA CIP was used to design all the reinforcement. Everything above the ring beam is made up of steel apart from the central lift tower core. The steel diagrid structures reach level seven with composite concrete floor slabs. The interior space is columnfree, and its steelwork comprises various elements, each presenting its complexities.
Our software was instrumental in arriving at the optimal arrangement for the diagrid from endless possible permutations.
What support, training and collaboration did Trimble provide to Eversendai and other project stakeholders? Tekla Structures is an intuitive and easy-to-learn software, yet we offer a selection of customised training courses for beginners and advanced users. We also assist the self-learners through e-learning materials such as product guides, support articles and tutorials.
We emphasise on customising the training content, and its delivery to suit user requirements and aligned with the projects that they are involved in. In addition, customer care is available for all new subscribers of Tekla Structures as well, which assists them in a smooth transition to digital workflows.
The Trimble Middle East technical service team also got engaged in the very early stages. Apart from day-today technical support and software consultation, the team conducted up-skill training sessions for Eversendai’s team.

Setting new limits
Paul Wallett says that The Museum of the Future has shown what can be achieved by using innovative modelling technology that stakeholders trust.
77m
Total height of the Museum of the Future
Further, the team got involved at the micro-level to suggest best modelling practices in the software. In addition, the service team enhanced an existing dedicated weight calculation tool developed for Eversendai in the past to suit new project needs. Software defects and feature development requests reported by the team were addressed on priority and more efficiently Moreover, regular review meetings with the senior team were arranged.
Finally, how has this project impacted future developments and projects? The Museum of the Future was able to demonstrate that BIM to Construction process really works throughout the lifecycle of construction. The stakeholders initially wanted to use some other solution for the rebar, trying something more traditional and what was seen as ‘trusted methods.’ However, they took a leap of faith and modelled the Rebar in 3D as well, while also adopting other integrated digital solutions as earlier mentioned. The project team moved from traditional stake out to using mobile solutions to coordinate with the office and onsite teams. All stakeholders involved trusted the BIM process from start through to completion.
The Museum of the Future stretches structural engineering to its limits and showcases the creativity of what is possible using innovative modelling technology.
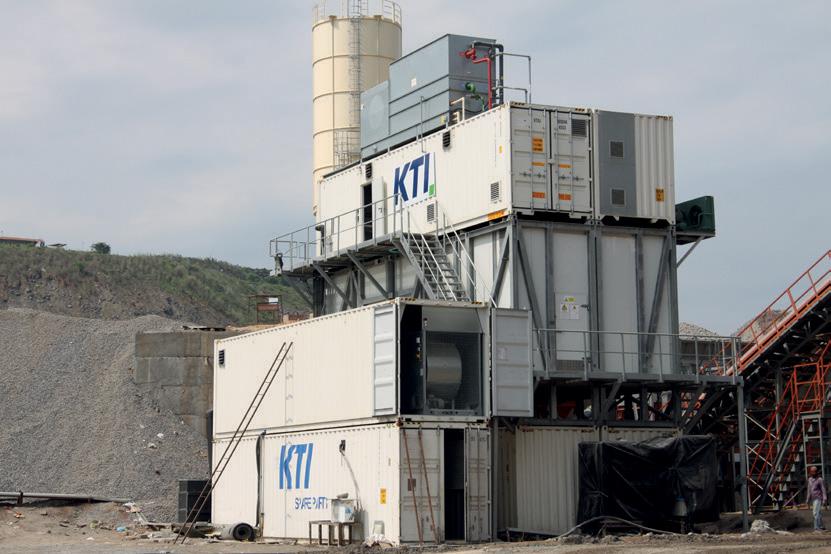
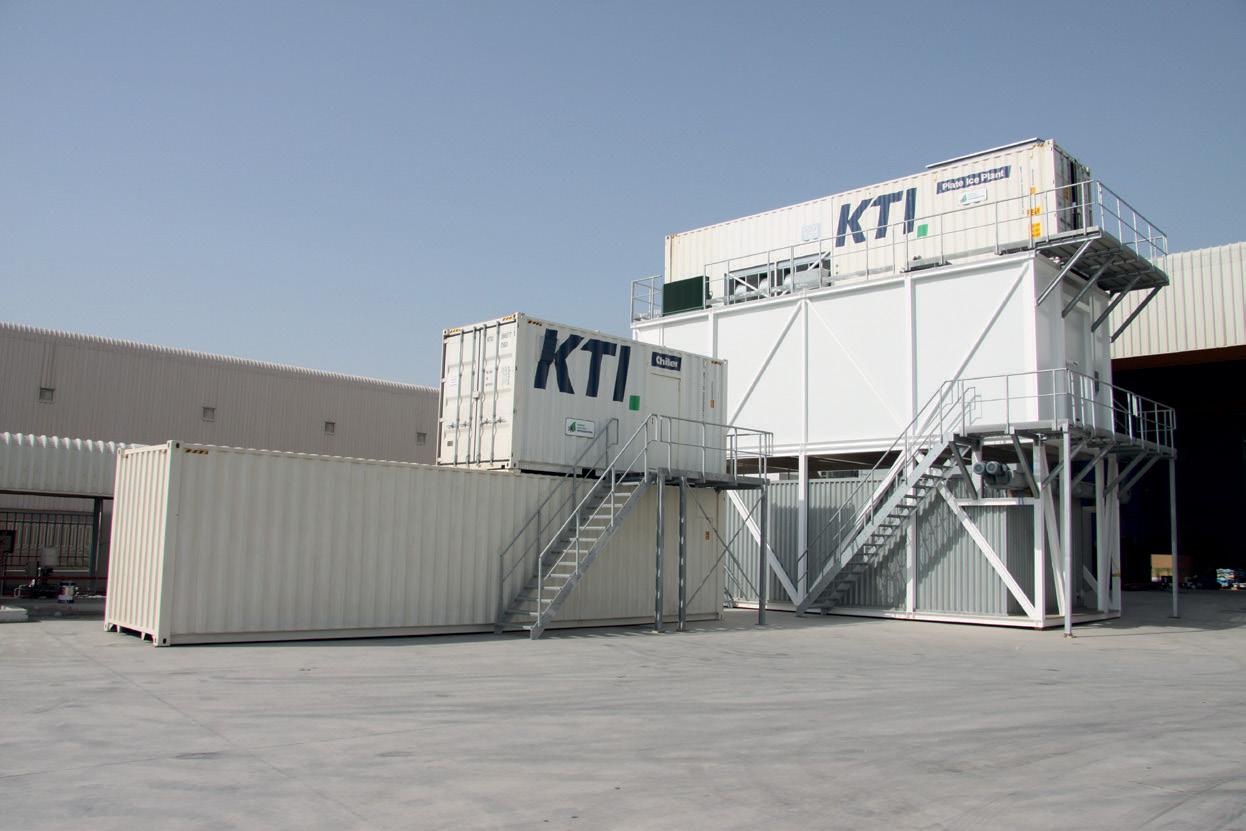
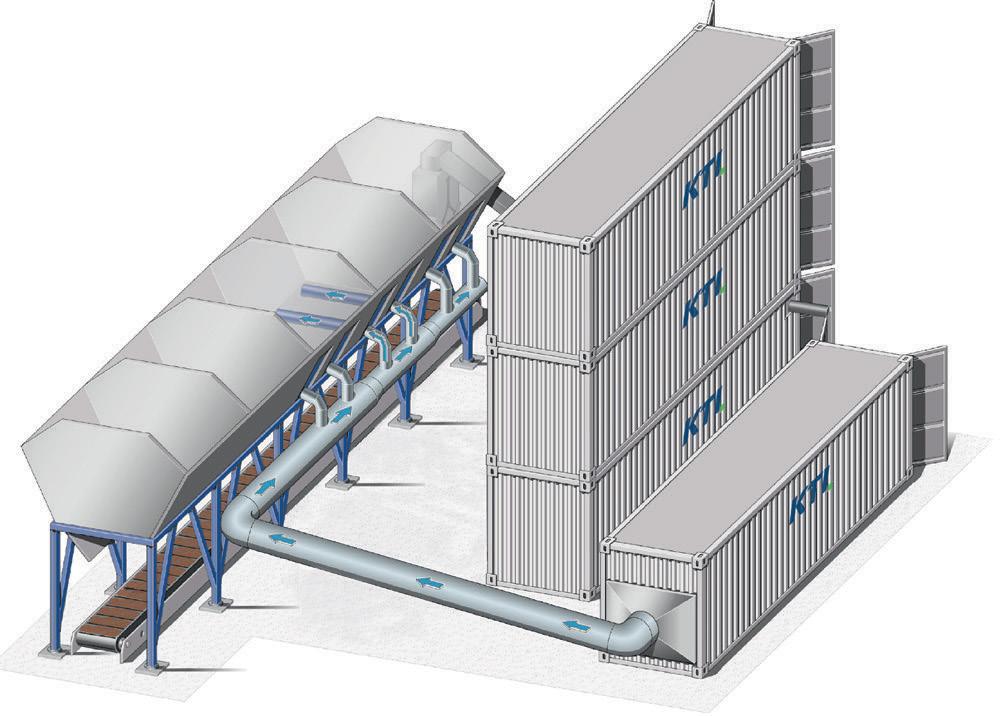