
12 minute read
A CASE FOR ROADS
WITH THE INTRODUCTION OF THE 1107EX-D COMPACTOR, CASE OFFERS A FULL-SUITE OF MACHINES FOR EARTHWORKS ON ROAD PROJECTS, WITH DOZERS AND GRADERS THAT OFFER COMBINATIONS OF IDEAL SIZE, FEATURES AND POWER
Travelling down a stretch of smooth tarmac, the last thing that people think about is what went into the building of that road - but ponder a moment and the enormity and complexity of the task can inspire awe.
It all starts with the earthworks, of course, which form the foundation layers of any road. On top of this come several layers of material, and each needs to be spread out, flattened and smoothened to a specific level - or grade – and then compacted together in just the right way to provide firmness and support to the layer on top of it. The final asphalt layer is only the proverbial tip of the iceberg; with so much below it. The trick in getting a road right is to get its foundation and earthworks right. And this is where Case Construction Equipment comes in with its wide model portfolio.
The CNH Industrial brand is among the few construction equipment makers out there to produce the entire range of machines for earthworks in roadmaking - from the powerful excavators and bulldozers to the precision motor graders and the heavy soil compactor. Having one brand supply all the vital equipment for a project through one dealer is always useful for contractors or rental companies, as the single source or one-stop-shop concept allows the fastest and most efficient aftermarket support. And this is part of Case’s USP where roadmaking equipment is concerned.
Zane Barnard, product specialist, Case Middle East and Africa, says: “When you’re doing earthworks on a road project, you can get your complete range of machines from us. Our excavators will dig out and lift the material from the surrounding areas of the proposed road and dump it where our dozers will push the material and spread it in the desired way to give the road its basic shape; our graders will then smoothen, level and contour every layer, and our rollers will do the compaction.
“Starting off with the dozers, Case offers middle or small sized dozers equipped with PAT (Pitch, Angle, Tilt) blades. They do the land preparation, and bulk material moving if needed. The dozers also make light work of base material spreading. As the aggregate materials become smaller, we get a Case motor grader in to spread and cut material and build up our layers. For each layer, the Case compactor will run a pass and ensure good compaction. We then get to the final cut which is highly specialised and the grader is brought back into action,” Barnard explains.
And to do all this, Case offers three dozers – the 1150L, 1650L and 2050M; three graders – the 845B, 865B and 885B, and a soil compactor – the 1107EX-D. Of these, the compactor is among the recent introductions in the Middle East.
“We introduced the 1107EX-D in the region this year. It is a ‘made-in-India’ model, much like our very popular 570T and ST backhoe loaders. It’s a single drum compactor
PLANT VISIT
CASE SHOWCASES INDIAN MANUFACTURING
Case demonstrated the manufacturing capabilities and standards of its plant in Pithampur, India, to key stakeholders from the Middle East and Africa late last year, taking 60 delegates on a seminar and tour of the facility which manufactures the 1107EX-D compactor that is sold in this region.
The aim of the “Made in CNH Industrial India” event was to showcase the Case Pithampur plant, a bronze certified World Class Manufacturing (WCM) site. WCM is a pillar-structured system based on continuous improvement, designed to eliminate waste and loss from the production process by identifying objectives such as zero injuries, zero defects, zero breakdowns and zero waste. To certify improvements, a system of periodic third-party audits evaluates all of the WCM pillars, forming an overall score for each plant.
Neil Woodfin, VP, Construction and head of Global Alliance at CNH Industrial, said: “India is a manufacturing hub and a strategically important market in CNH Industrial’s global growth plan. The ‘Made in CNH Industrial India’ initiative is a reflection of our excellence. The state-of-the-art facility in Pithampur is amongst the best in the country and the adoption of global manufacturing standards has further increased the plant’s role in our overall construction equipment business plan.” CNH Industrial has a significant presence in India with three manufacturing plants of which Pithampur caters to construction equipment needs. The plant is the fastest growing bronze level WCM certified plant. A full range of construction equipment is built there, supported by research and development. Apart from the 1107EX-D vibratory compactor, it also produces Case backhoe loader models that are popular in the Middle East.
weighing in at 11,030kg and is packed with features. Kicking off with an air-conditioned closed cab option, it has a two-speed hydrostatic transmission with drum drive for outstanding gradeability. The compaction drum up front boasts a drum wall thickens of 32mm, ensuring longevity and reliability. The industry standard for an 11t compactor is a 22mm drum. We went upsize on it and this extra drum thickness enables it to carry a little more weight, which transfers into the compacting effort on the ground and complements the vibration system.
“A vibrating compactor has two key features: frequency and amplitude. Frequency is the speed at which we move the compacting drum from a vertical Top Dead Centre (TDC) point to a Bottom Dead Centre (BDC) point. This is measured in time as Hertz. Amplitude is the distance the drum will move in millimetres between TDC and BDC. The rule of thumb is the longer the travel distance (amplitude), the higher the impact. The 1107EX-D delivers a massive 32t of compaction force at 31Hz and an amplitude of 1.8mm.”
Coming to other features, Barnard elaborates: “The cab is one of the highlights in this machine. Before we launched it over here, we listened to our customers, who said they wanted an airconditioned, closed cab with full ROPS/FOPS design. So that’s the way we designed it. We put the cab on the machine and tested it rigorously and it turned out to be very suitable. This was because of the extra weight of the cab, which gave it an added ability to compact the soil. So now we have an 11t machine, which produces the compaction of 32t. This is quite remarkable and a class-leading figure putting the Case soil
The three bulldozers Case offers in the region come with PAT blades and tracks desgned for better floatation on sand. The hydrostatically driven mediumsized units are ideal for roadworks. compactor right up there with the big boys and very hard to compete against.”
The 1107EX-D is available in two versions. With the cab it is a 110hp machine while power for the canopy version is 100hp. Both use the robust 3.9-litre made-in-India FPT S8000 diesel engine, which is tuned for a higher output in the cab version because the air-conditioning system draws more power and, as Barnard explains, “you don’t want that coming at the cost of performance”.
“The 1107EX-D has been accepted very well by our customers from the very beginning. Its build quality and performance are both top-notch. And it is also equipped with some leading-edge machine control systems and telematics,” he states.
“On big projects you’ll see several compactors lined up behind each other with a radar measuring the front compaction. The telematics units then tell the machines and operators where to run and the radar up front measures the ground compaction in real time. They can tell you how many passes you need to do, so there will typically be one low pass with one unit, followed closely by a second machine to which the information is relayed to tell him how fast to drive, how much compaction pressure needs to be sent down, and then a third machine might also be following on, also guided by the telematics information relay.”
Case’s technology partner for telematics and machine control is Leica Geosystems, Barnard informs us, and the company can offer these technology aids on its compactors, as well as graders and dozers - all of which “come out from our factories ‘play ready’ for Leica systems to be installed”.
Providing more details of the 1107EX-D, he adds: “Our compactor comes with a drum drive, which means that along with the tyres on the rear axle, the steel drum of the machine is also driven by the engine. This helps when working up a slope, achieving an awesome 20° gradeability.
“The machine is fully hydrostatic and so the power is transferred to the drum for both the travel and vibration motors hydrostatically, which is apparent when you see the two sides of the drum and the hoses connecting the
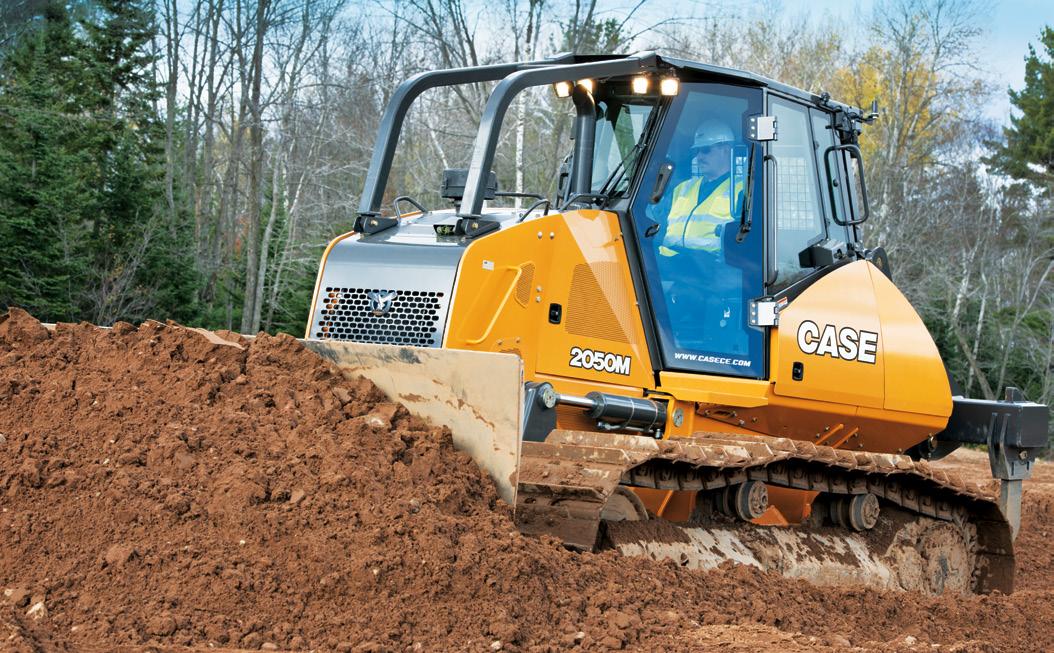
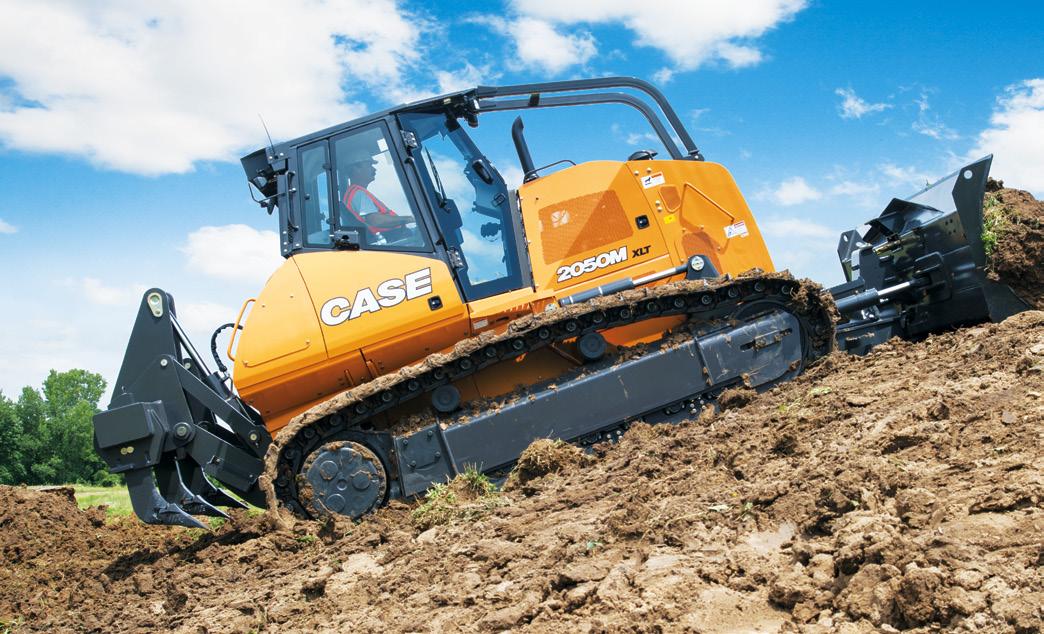
machine’s hydraulic heart to the drum. The pump drives both the front and rear in this machine, so the engine basically only works the hydraulic motor, which does the rest.
“Using a hydrostatic system enables the 1107EX-D to put more power on the ground, because we’re not transferring through a differential or a torque convertor, in which a lot of power is lost. This is why with a hydrostatic drive we can use a smaller motor to power the unit and still deliver the same power onto the wheels because there is no loss.”
There is also a padded drum option on the 1107EX-D, Barnard adds. This is useful when the material being compacted is wet. It helps dry the material quicker and increases the compaction surface area.
The compactor aside, Case also, of course, offers the other tools of the roadmaking trade – the dozer and grader, along with other earthmovers necessary at various stages of roadbuilding, such as excavators and wheeled loaders.
“Normally, before the process kicks off, excavators and wheeled loaders are brought in along with the dozers to either remove or add material where needed. On the dozer side this is where our 2050M XLT comes into play, moving material with the aid of a Semi-U production blade. The next step is contouring and landscaping the soon-to-be roadway. All three dozers we offer are useful in this process, each fitted with a PAT blade, making grading, contouring and landscaping quick and easy. Our dozers are packed with essential features for the region and all are hydrostatic, meaning we put more power to the ground and deliver better traction and movability. Another important feature is
Case motor graders come with a three-radius involute patent blade. The 885B model is popular in the region and was recently revamped, adding bigger tyres for better floatation on sandy terrain. our V-shaped cooling system that increases surface area and improves cooling efficacy. Our dozers are also fitted with extra-long tracked undercarriages for greater floatation in demanding conditions,” Barnard says.
“There’s a misconception that laying a road down is initially about moving massive amounts of material. But you’re better served if you’re using a PAT blade, because the job is more about contouring than about moving a lot of material. Case dozers offer just the ideal size and performance package for road building, with fuel economy and productivity, and minimal wastage in terms of power.
“We also offer three motor grader models in the region, which come in a range of weight and power: the 845B, 865B and the popular 885B. With this last model, all the tweaks that Case has done is paying off for us now in terms of sales and market share, which are quite good for the machine. For example, we increased the tyre sizes for the 885B since its launch here around three years ago and now it sports bigger tyres so that we get better floatation on soft sand.
“Our graders also have a three-radius involute patent blade, which rolls the material instead of pushing it, reducing the load on the blade and consequently on the engine as we reduce friction caused by pushing material. By rolling it over, you use less power, making the grader more efficient, return better fuel economy and also move the material faster.
“Moreover, our fully automatic transmission prevents machine stall at low speeds and operators like feature as it allows them to just concentrate on driving the machine – with the option to shift manually if required to hold a gear for a particular operation.”
Though the years, Case has refined its machines to tackle every aspect of earthworks for roadbuilding, Barnard says, with the result that now with the mix of its dozers, graders, soil compactor and other earthmovers, the brand offers one of the best packages for roadbuilding contractors with advanced and robust machines, packed with innovative tech and solutions. “In the final analysis, all these innovative solutions from Case add up to incredibly versatile and efficient machines for roadbuilding,” Barnard signs off.

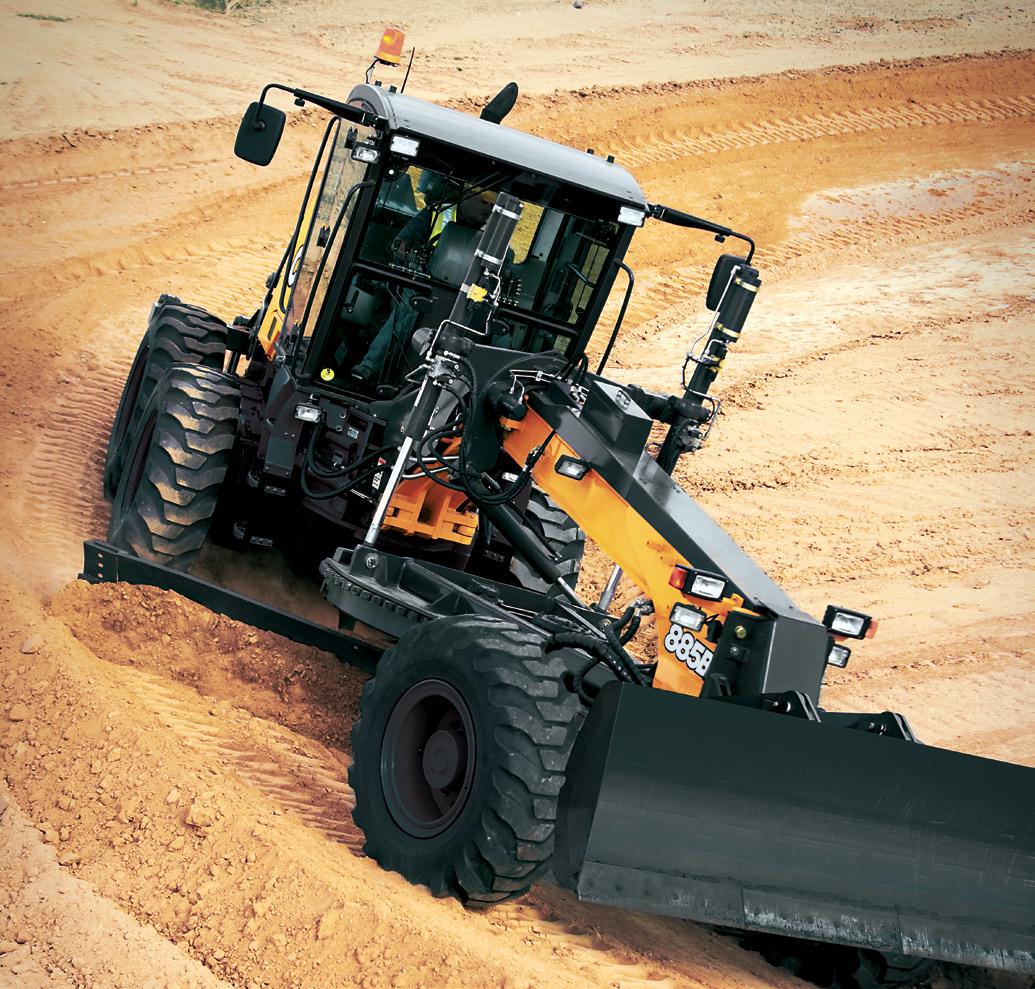
POPULAR IN THE ROUGH
CASE DELIVERS 125 UNITS IN ANGOLA
In what was one of its largest deliveries for 2020, Case announced earlier this year the delivery of an order comprising 125 units of earthmoving machines to the Angolan government.
Announcing the delivery to the Angolan Ministry of Transport, Case Middle East and Africa regional headquarters in Dubai said the order consists of 35 units each of Case’s 2050M bulldozers and 885B motor grader. The 570ST backhoe loader and CX220C crawler excavator make up the rest of the order.
Case said the order is a sign that the global and regional construction equipment sector is beginning to see an uptake in activity amidst the Covid-19 pandemic, “as governments of countries with downward trends in contagion enter into their respective next phases, reinstating select construction activities”. The “substantial” delivery in Angola is the result of a tender won by Redondo y Garcia SA, a key Case partner. Aftermarket services tied to this delivery are being supported by Case dealer Ivecar SA. Despite the logistical slowdown related to
Covis-19, the delivery was successfully concluded. “Throughout the pandemic crisis, Case has continued to support its global dealer network and to maintain aftermarket services,” said Case MEA. “With Angola being one of the highest spenders on roads in Africa, infrastructure development is crucial to the country. Case machines will be used to support the construction and maintenance of the country’s roads.”
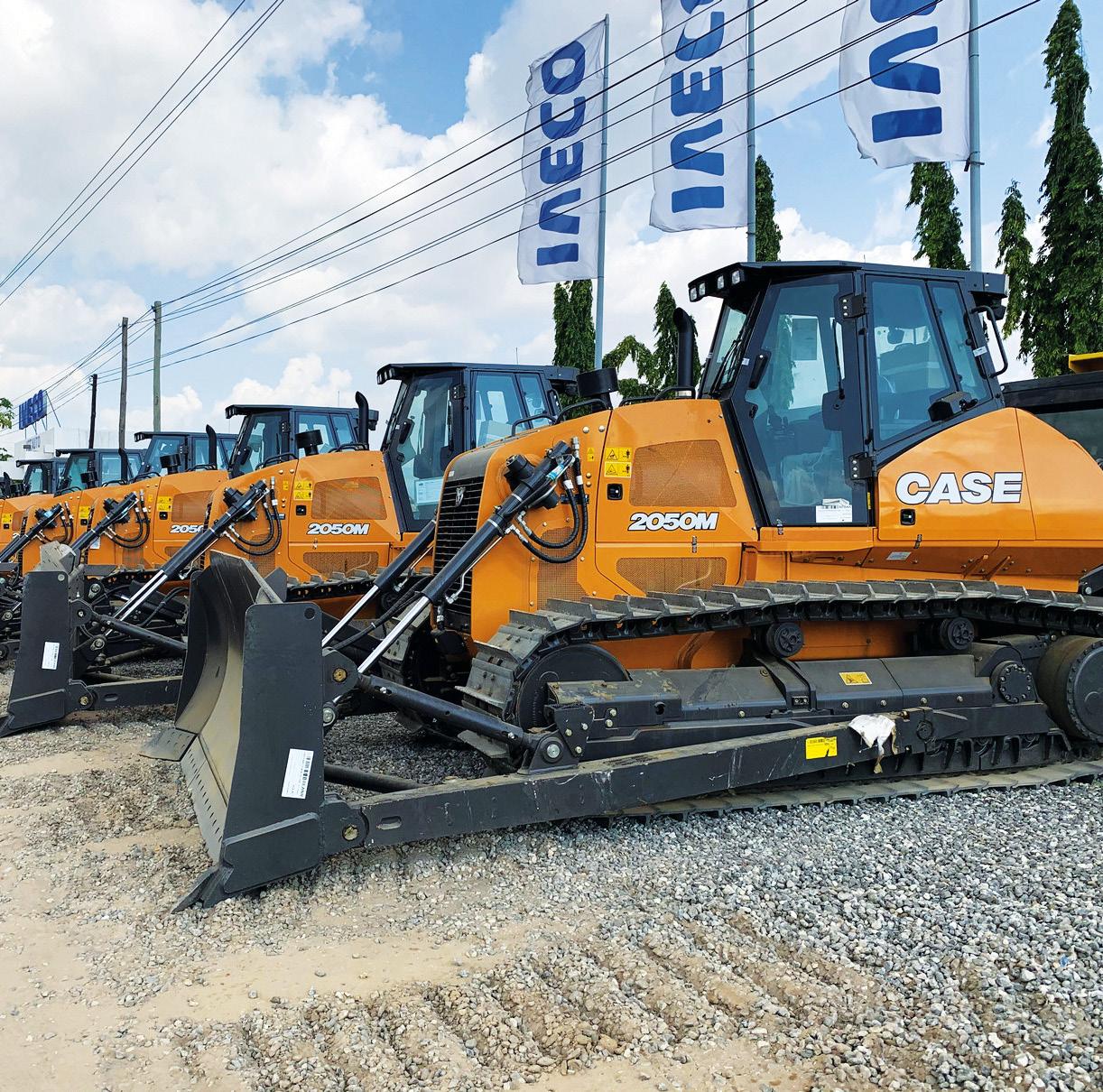
“Most job-sites in both construction and internal landscaping...almost always involve light compaction equipment.So our aim was to be a one-stop-shop solution provider for our customers and give them all the equipment they might need“
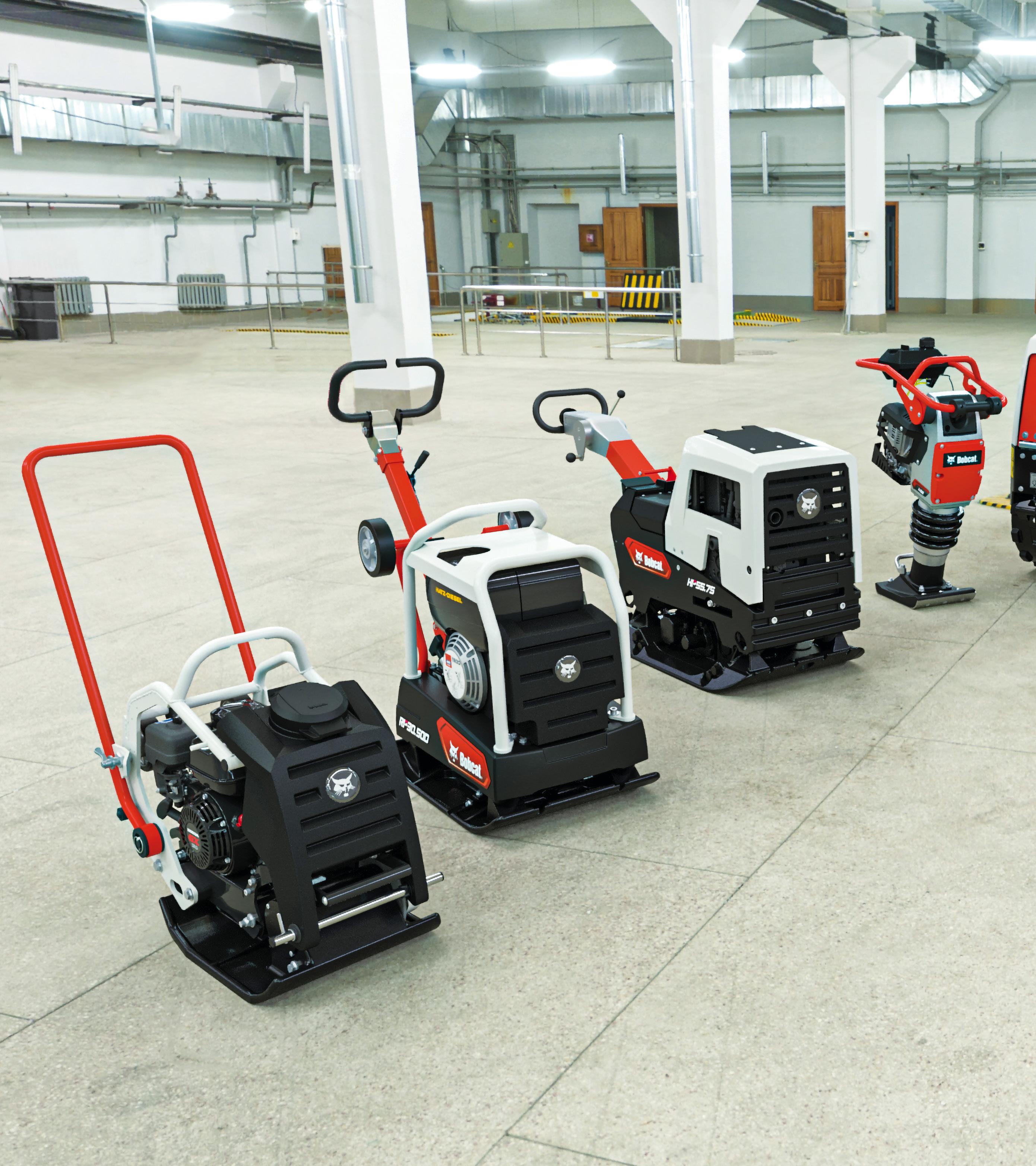
Bobcat’s new light compaction range has seven families: vibratory rammers, vibratory forward plates, reversible vibratory plates, hydrostatic plates, walk behind rollers, trench rollers and tandem rollers.