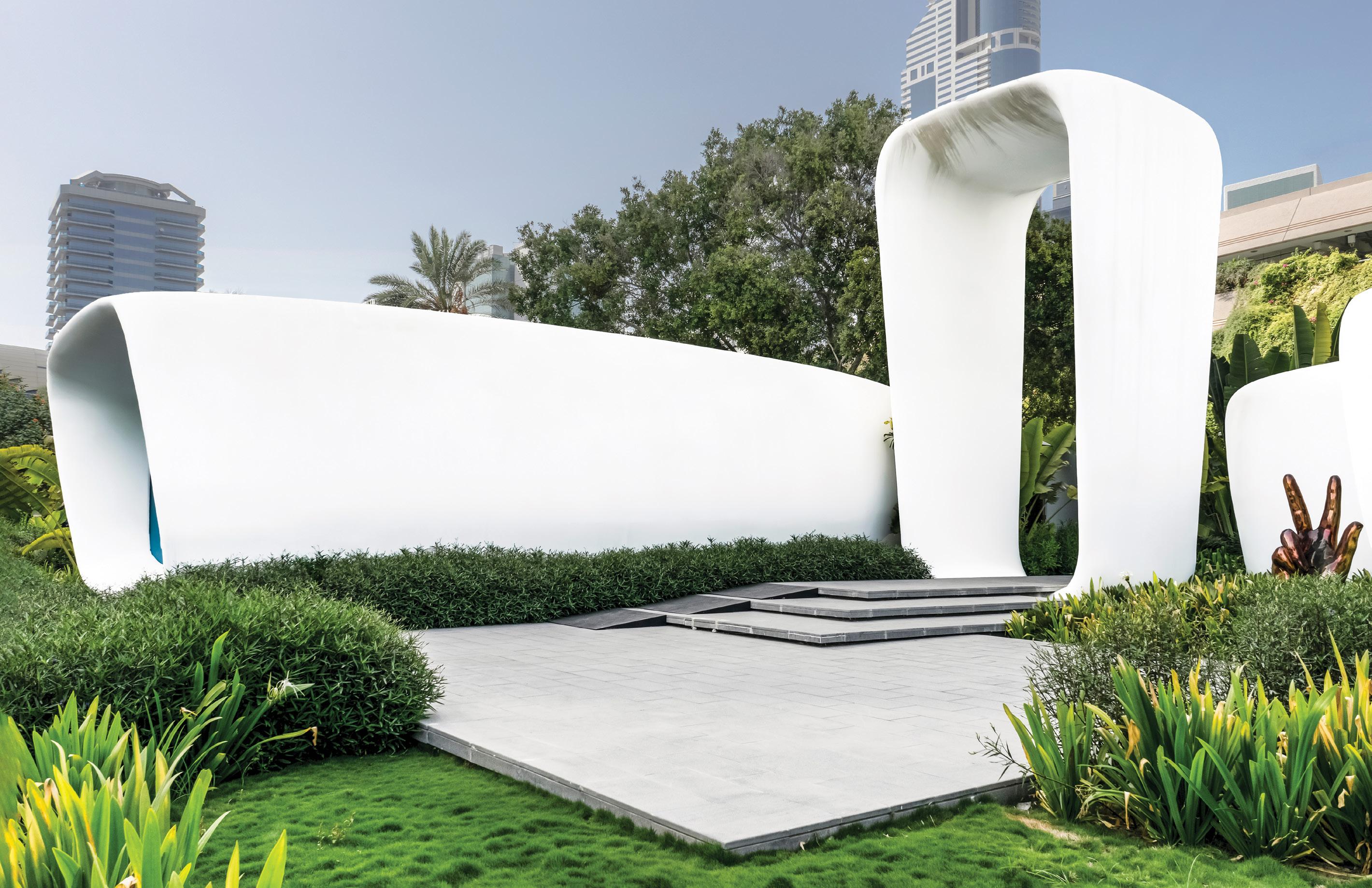
5 minute read
PRINTING THE FUTURE
DR. MUSTAFA BATIKHA, ASSOCIATE DIRECTOR OF RESEARCH AT THE HERIOT-WATT UNIVERSITY DUBAI’S SCHOOL OF ENERGY, GEOSCIENCE, INFRASTRUCTURE AND SOCIETY, DISCUSSES THE PROS AND CONS OF 3D CONCRETE PRINTING AND THE WAY AHEAD
Arapidly growing population is one of our biggest challenges in the 21st century. Recent data from the United Nations confirms that the world’s population will reach 9.7 billion in 2050 with an average yearly increase rate of 0.84% between 2010 and 2050. With this population growth, it is predicted that the global construction industry will record a compounded annual growth rate (CAGR) of 5.7% to reach about $12tr trillion by 2024.
Governments around the world are under enormous pressure due to a shortage of affordable housing. For example, the UAE government has taken the initiative of launching The Emirates Development Bank (EDB) with $2.7bn aimed at financing affordable residential projects for UAE citizens by 2021.
On the other hand, there is a demand for addressing important issues in the construction sector, such as sustainability and health and safety, in the backdrop of rapid and cost-effective construction. Thus, the construction industry is in need of new innovative construction technologies such as 3D Concrete Printing (3DCP), which is paving the way for meeting future requirements.
Understanding the technique 3DCP was developed to build a structure upwards through a series of layers, one on top of another through a robotic arm or a gantry girder system. The concrete material in this technology is the printer’s ink, while a nozzle attached to the printing system plays the printing mechanism’s role. The final output is a layer of concrete of the desired shape and thickness.
Printer selection plays a vital role in terms of cost and printing quality. For example, the robotic arm offers better flexibility since it has six degrees of freedom. It also allows superior quality in printing for precise, complex printed shapes. Its limitation is the limited arm length. Also, the operation and maintenance of the robotic arm make printing cost higher than the gantry girder by about three times.
The robotic arm’s biggest disadvantage is that the printer has an unstoppable process until the element is fully printed. Therefore, design errors will produce material wastage. However, the selection of the printer is defined based on the printed structure’s type.
Advantages of 3DCP 3DCP in construction avoids the disadvantages of in-situ reinforced concrete (RC), such as excessive construction waste, formwork cost (which comprises more than 60% of the overall cost), formwork preparation time (which takes up 50% to 70% of the total construction duration), and the lack of worker health and safety (where workers’ injuries in in-situ RC construction are double the accidents registered by other industries). WinSun, a pioneer of 3D printing technology in construction, claimed that the labour cost of their ‘Office of the Future’ project in Dubai was reduced by more than 50% when compared to conventional buildings of similar sizes.
The world’s largest 3D printed building is a two-storey, 640 square metre, one completed in 500 hours by Apis Cor for Dubai Municipality. The city wants 25% of new buildings 3D printed by 2025.
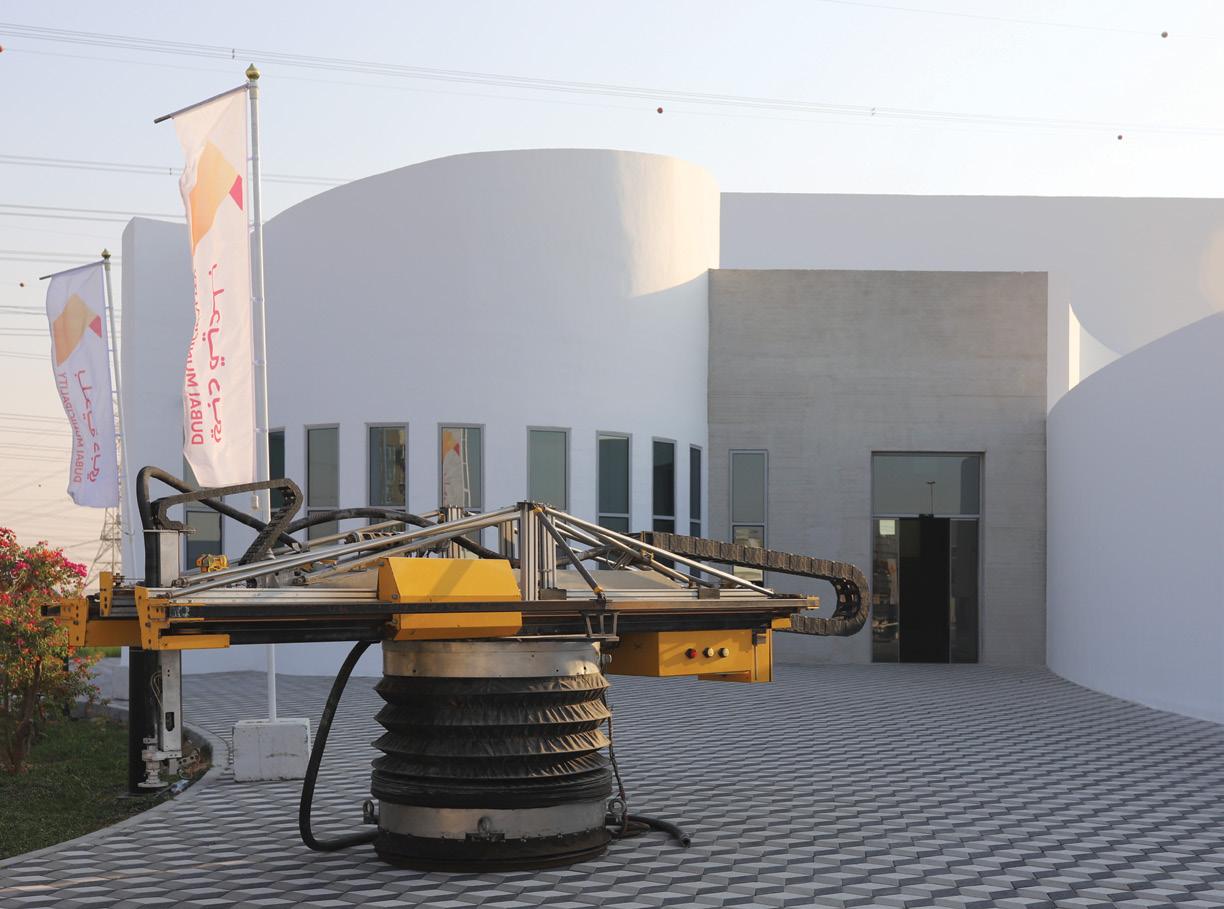
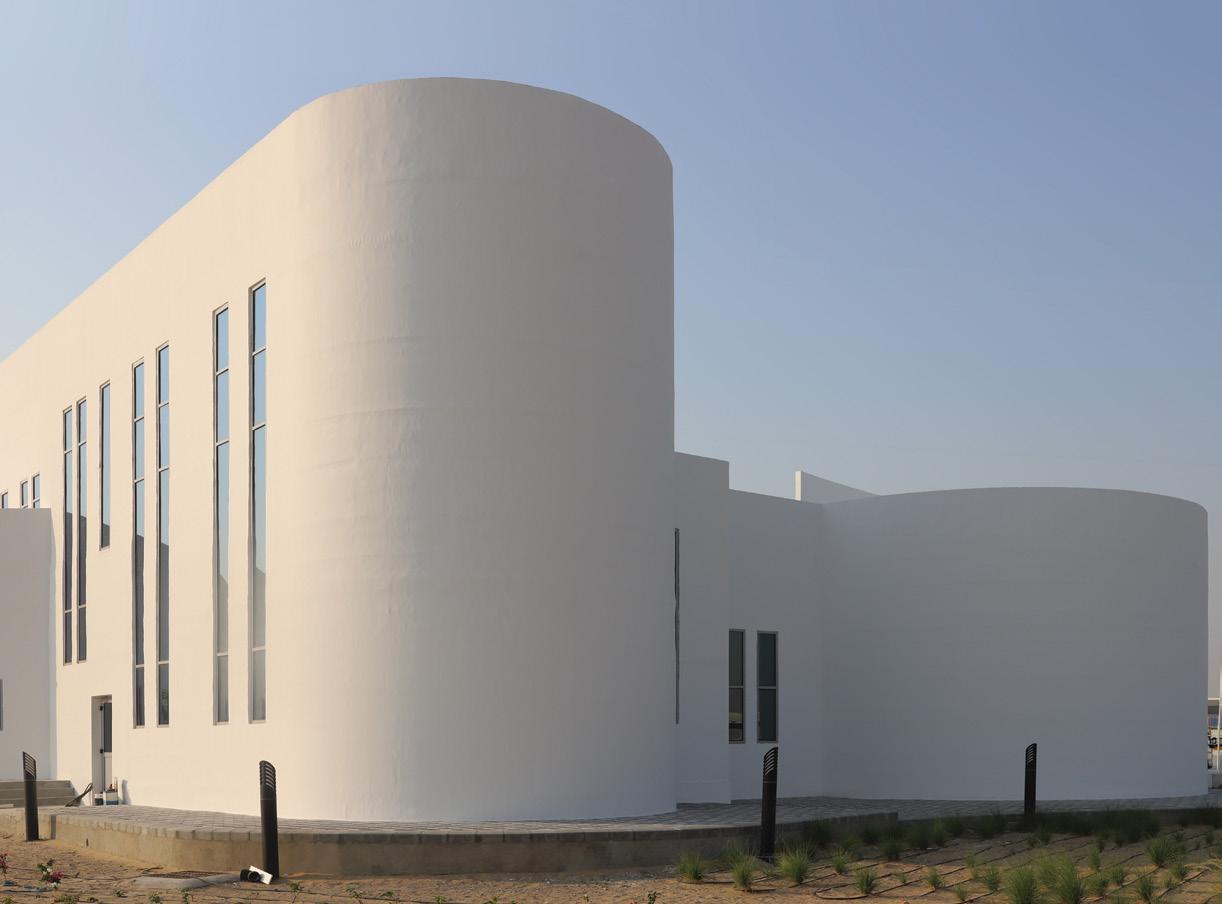
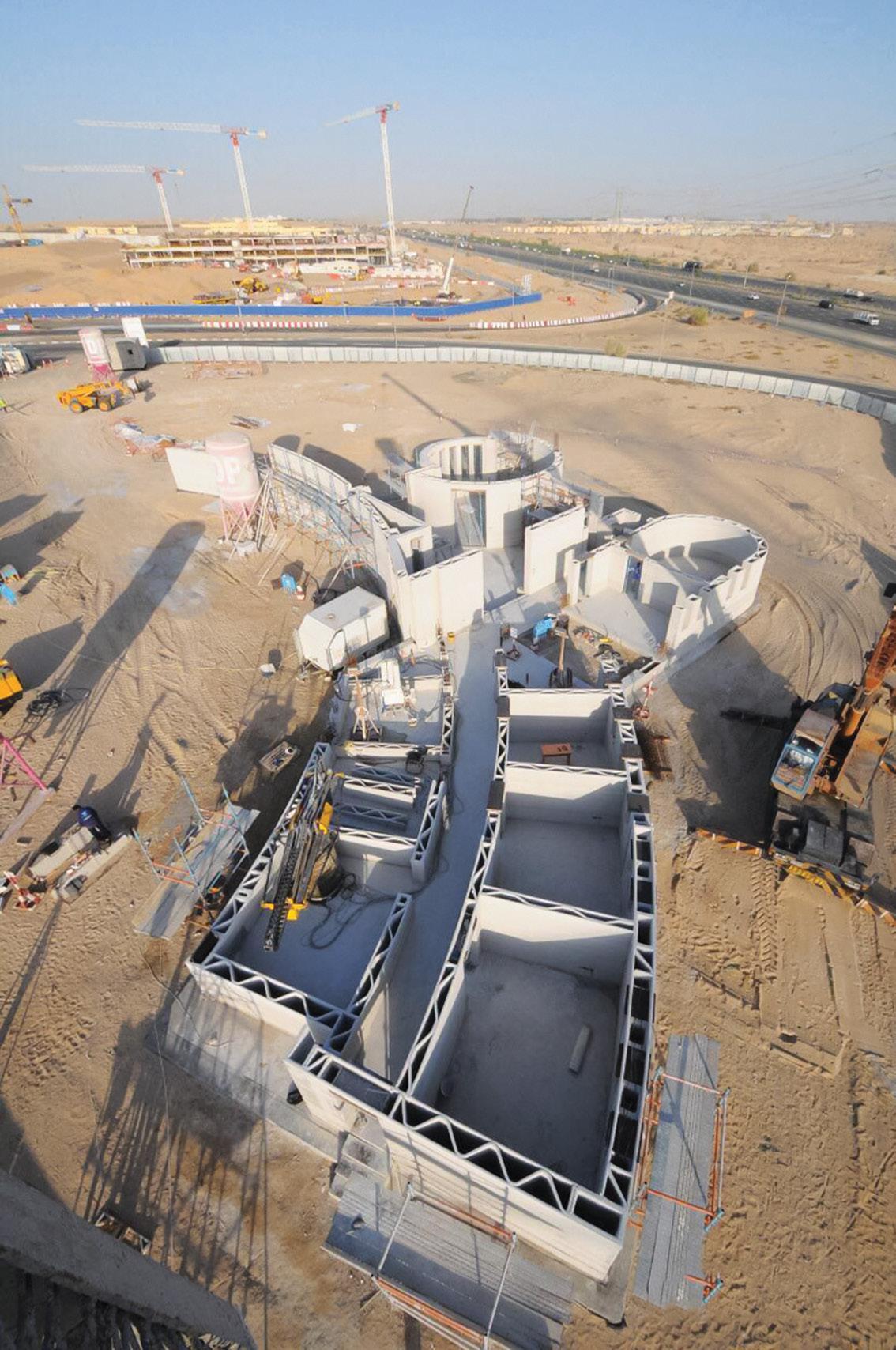
Compared to Precast Concrete (PC) construction, 3DCP is more economical and sustainable, although PC is faster in terms of construction duration. A recent study by Heriot-Watt University also confirms that 3DCP reduces cost by 39% and CO2 emissions by 48% compared to PC.
There is a high percentage of steel reinforcement in precast concrete, which results in high CO2 emission in the manufacturing process of the steel reinforcement produces. Besides, the formwork manufacturing process in precast consumes energy, although the formwork can be reused 75 times.
The globality of 3DCP Globally, projects implemented using 3DCP include the Rain Collector of 2.15x2.20x2.6 m3 completed within nine hours by XTreeE; the Icon House of 33m2 within 47 hours by Austin Texas; a 38m2 villa within 24 hours by Apis Cor company; a two-storey structure of 400m2 by HuaShang Tengda within 45 days; Dubai’s 250m2 Office of The Future completed within 17 days by WinSun Global; and a two-storey office of 640m2 – the world’s largest 3D-printed building – completed for Dubai municipality within 500 hours by Apis Cor. 3DCP will make further progress, thanks to Dubai’s ambitious plan to 3D-print 25% of the city’s new buildings by 2025.
Challenges facing 3DCP Looking at the current and future challenges facing 3DCP, various solutions might need to be adopted. To date, no official codes and standards for 3DCP design have been outlined by the authorities. Therefore, research is critical into supporting the issuing of a design standard for 3D printing.
The concrete material used in printing has a relatively high cement quantity, making it costly and not sustainable. Developing this material by using recycled substances will reduce the cost and significantly improve sustainability.
The structural configurations of the printed elements need to be studied and confirmed for economic design and energy savings. Additionally, printing roofs and elements under bending with a low steel reinforcement percentage needs further research as well.
Currently, printed buildings are capable of only rising to one or two storeys with steel reinforcement addition. The challenge of the future is to make 3DCP more suitable for multistorey buildings under different action scenarios.
The use of 3DCP for segmental precast construction requires more intensive research in order to be used in large structures. The connections among segments need to be studied to confirm high performance and low maintenance during their life cycle. More research and development is required to make the 3DCP printer more flexible and efficient.
At Heriot-Watt University, the Centre of Excellence in Smart Construction (CESC) researches subjects such as ‘Productivity and Performance’, focusing on technologies that improve the construction industry’s efficiency. The CESC established a special team in 2019 for research in the area of 3DCP and many research dissertations at Heriot-Watt University are currently focused on finding solutions to the problems of 3DCP.