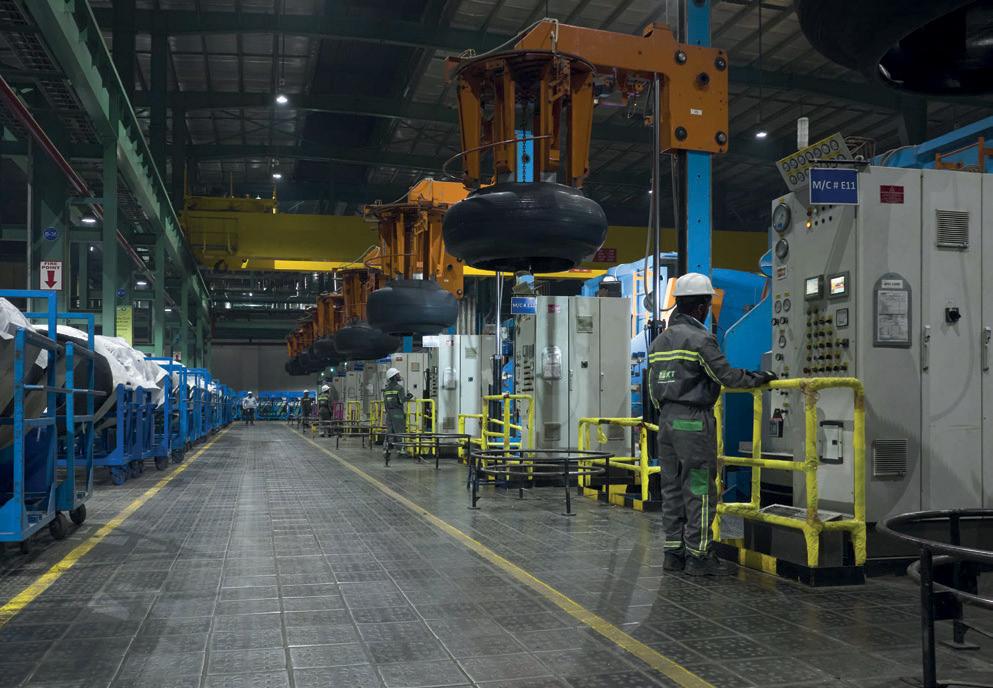
5 minute read
EXPANDING HORIZONS growing
Aline of security guards has formed outside of our bus when we are asked to disembark and form a group close-by. We huddle on a dusty plateau that must have been recently flatten. A few resting machines stand by shallow holes they’ve made in the ground. Arms folded behind his back, the man in charge of the industrial complex behind stands watch. The guards behind, the surly character in front, the bustle of the coach has been replaced with respectful silence.
“I think they are going to use the holes for us,” says a tired voice behind me.
It has been a long day. The sun is setting now but the journey from Mumbai started at 4am to avoid the city’s traffic which streams from our hotel close to the Gateway of India to the airport. Into Gujarat we had a sharp 20-minute turnaround at the Bhuj plant’s surprisingly well-appointed hotel before heading on and into the plant itself.
And what an impressive place that is. Looking past a surreal walk along a narrow route alongside it – where we were joined by acrobats, performers and Bollywood(!) – the six-hour tour of test tracks, vast warehousing and factories, R&D labs, power generation control rooms, reservoirs, was a statement singing that BKT is a serious player. Possibly one with the ambition and facilities of a Bond villain.
“You know how the bad guy is always courteous before he throws you to the sharks,” I warn that voice behind me.
In truth, BKT had been consummate and courteous hosts. Our cordon on the plateau intended to demonstrate the room it has to grow. The plant manager tells us that it will double in size as the company hits fast-forward on its ambitious growth strategy. The Bhuj site, which was inaugurated in 2015 is primed with a well-designed and very significant growth plan and is central to a plan which aims for annual tyre production of 600,000 metric tons (MT) and envisages the achievement of 2 billion dollars in turnover in three years.
When the first tyre rolled off the Bhuj production line in 2012, the plant was located on an area of 123 hectares. At the time it represented a $500 million investment in an area of Gurjarat’s desert-like landscape. Completely arid, there was neither water nor electricity but after the laying of many kilometers of drinking water pipes and power lines, the site grew exponentially: 126 hectares in 2016, 131 in 2019, 137 in 2021, 258 in 2022. By the end of 2023, the forecast is to reach a total surface area of 323 hectares, of which 283 have already been acquired.
More space means more room to install new machines, to accommodate more test areas, to increase volumes and all that goes with it, says BKT. The business has increased by 49% compared to the pre-pandemic period. The company says that this “bears witness to how the Indian multinational is always ready for new opportunities and challenges” and standing in Bhuj, it doesn’t sound like empty words.
Dominating the site are the pipes and steel chimneys of its Carbon Black plant. The plant came into operation in 2017, when the first 65,000 MT/PA of Hard grade carbon black was produced, the type of carbon black used specifically in the tyre tread. In the following year, production increased from 65,000 to 110,000 MT and saw the addition of production of soft grade carbon black, which is used in the casing compound to improve its strength and durability, generating less heat. In 2021, total production of the two types of carbon black reached 138,000 MT per annum, while last year it rose to 165,600 MT per annum.

The goal for 2023 is 198,600 MT, in addition to this, the Research and Development department plans to add a third type of carbon black, the “Specialty carbon black”. It is a type of carbon black with unique properties compared to that used in rubber compounds, such as high resistance to coloring, a high level of purity, a low ash level and very low level of PAHs, which make it suitable for use in specific applications such as paints, plastics and inks.
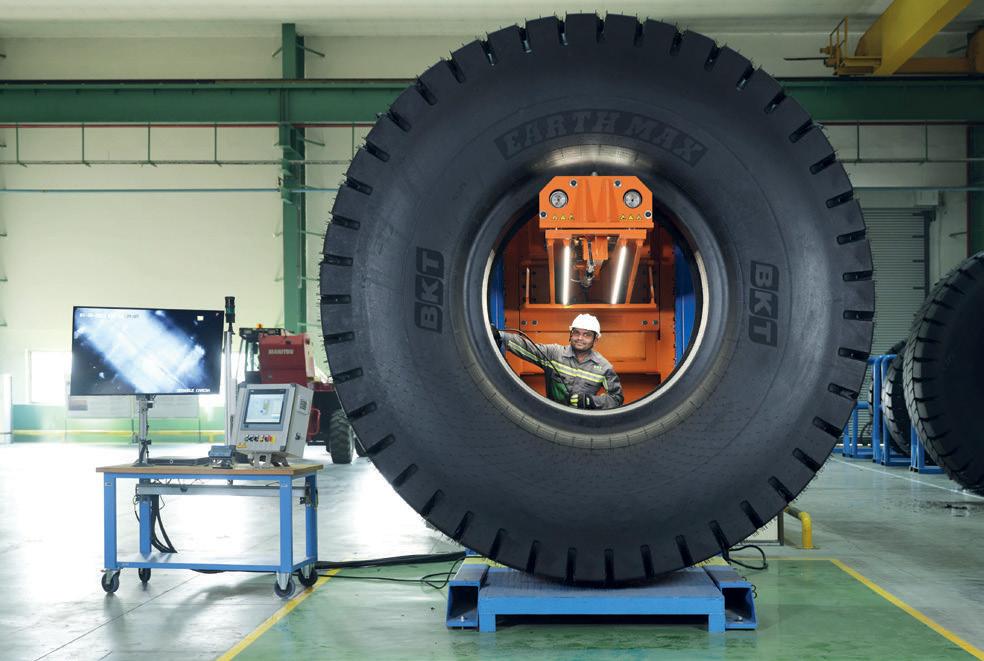
The expansion of the plant means an increase in production capacity, but operational logistics have also improved significantly, which has allowed the introduction of new specialist workers, as well as providing greater flexibility in production and storage flows.
Speaking of work, the construction of new facilities also marked an improvement in employees’ safety conditions, an aspect which BKT takes very seriously; the community that operates on the Bhuj site today is very large, at the end of December 2022 the number of people working there was 4,776.
BKT dedicates significant investment to the wellbeing of its community every year, through for example the expansion of the area housing the families of employees (now almost 1,000 people live there), in the care of their health, in the education of their children. In short, a true all-round “community factory” which remains a virtuous model among the first in the world in the manufacturing sector.In 2013 an internal power plant was created to have a reliable and controlled source of electricity. Today, both solar panels and the cogeneration plant make it possible to self-produce energy; in 2022 the cogeneration plant was expanded, from 20 MW to 40 MW, and projects are still underway to
FOUR-FOLD INCREASE IN PRODUCTION – SO FAR
The plant has increased from 92 MT production per day in 2015, Bhuj ended 2022 with its best result ever, 436 MT daily. Much of this increase has come from the investment in more efficient machinery.
using. For example, BKT has introduced a new approach to the carbon black production where the tyre production plant feeds the carbon plant with the aid of mobile silos with material transported pneumatically to storage. This will make BKT save on packaging, i.e. 100,000 bulk bags in the next few years. And not only that, but the whole transportation system is also designed to reduce energy usage, consumption and quality, too. Every transfer system is controlled by weight and by energy used. And the future goal is challenging: reducing energy consumption up to 70%. This translates in saving more than two million kilograms CO2 emissions per year, which are comparable to 5,000 apartments of 100 square meters each.
increase the power of self-produced renewable resources.Water is also at the heart of BKT’s virtuous path towards Sustainability. Since 2019, the Zero Liquid Discharge (ZLD) principle has been adopted, which means that no liquid waste is released outside the plant. All water used in the plant is treated, purified and reused. The objective of the ZLD principle is to conserve water resources, reduce the environmental impact of wastewater discharge and improve the overall efficiency and sustainability of the plant.
All of this is unverifiable by T&FME, but, anecdotally, the complex at least ‘feels’ clean and throughout there are touches where the firm is clearly determined to be recycling and re-
At the same time, the gas used to manufacture carbon black is now ending up in a co-generation plant able to reuse 75,000 cubic meters of gas per year. This means saving 215,000 MT of coal per year. Looking for the right solution means testing it and in 2017, a special Test Track was inaugurated. Thanks to a wide variety of tests, many important characteristics such as traction, handling, comfort, soil compaction and much more can be measured here, thanks to high-precision devices and instruments.
“People have asked me if all this was really necessary, so much in such a short time,” says Rajiv Poddar, Joint Managing Director at BKT. “The goals we set ourselves when we decided to open the Bhuj site were proportional to the financial solidity of the time, but above all to a vision which is as great as it is concrete.”
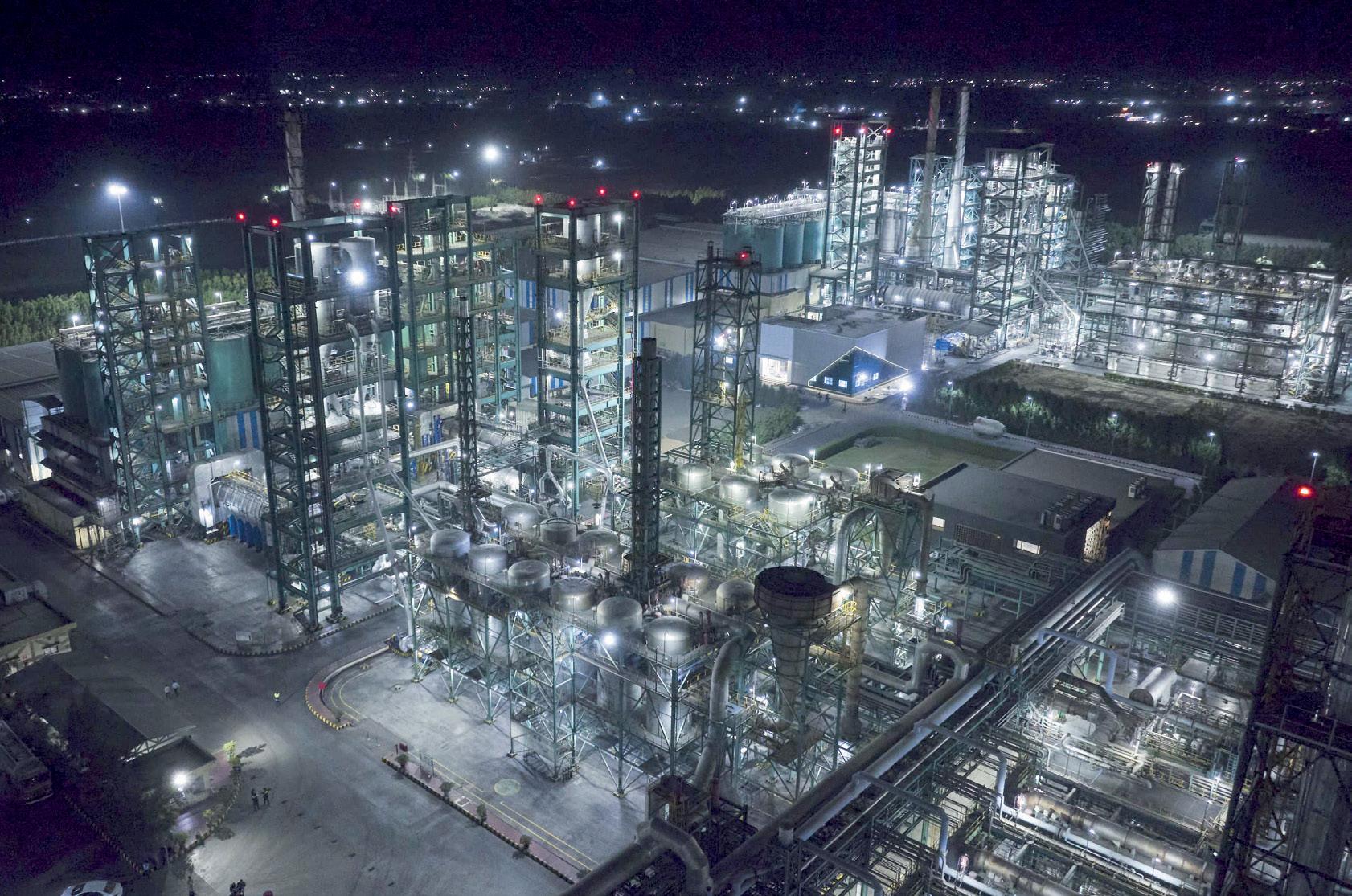