
16 minute read
News from around Asia and the world

CGS ORIS and HanGlobal collaborate to further digital printing in China
Advertisement
CGS ORIS announced its digital printing partnership with China’s HanGlobal Group for the next three years.
In the initial phase of the agreement, CGS ORIS colour management solutions will be applied to the inkjet digital label and book presses.
In a second phase, other digital printing presses of the HanGlory Group – a division of the HanGlobal Group – such as digital corrugated packaging printers, textile printers, large format UV printers and other digital printers will follow.
“Our common aim is to optimize digital printing processes and results and make it even more easier and faster for printing operators to achieve perfect print results. Especially, the handling and reproduction of spot colours play an important role for us,”, said Lilly Xiao, General Sales Manager Greater China at CGS ORIS.
The partnership was cemented in a ceremony between Xiao and HanGlobal General Manager Li Hualin.
In addition, CGS ORIS software will be used to optimize and reduce the total ink volume. That leads to faster drying times and even higher production speed. The customers profit by an increase in productivity and the ability to make full use of their presses while reducing production costs. the development of multi-SKUs, coupled with the Internet of Things, Internet plus as well as one yard, anti-counterfeiting technology, a growing demand for digital products is expected. The strong partnership between the two companies will give answers to that by providing reliable software solutions for the usage of digital inkjet technology with accurate colour in the field of industrial printing.
“We are very glad about the partnership and are very looking forward to bring our colour management solution and experience to the new market to meet the growing number of needs on colour consistence, especially the accurate reproduction of spot colours on high speed inkjet printers,” said Christoph Thommessen, Managing Director Global Sales. HanGlobal is part of the Hanglory Group, a industrial digital printing solution provider that focuses on digital inkjet printing technology and integrates R&D, production, sales and after-sales service. The Hanglory Group owns seven high-tech enterprises, with applications covering advertising, home improvement, clothing, textiles, packaging, books, labels, printed circuit boards, 3C electronics and other industries. HanGlobal focuses on digital inkjet presses for label sand books printing.
Introducing a new business model, consumables, and software
Highcon Systems Ltd., announces the launch of new product enhancements and consumables, and a new pricing model. These new initiatives will enable the customers of Highcon® Euclid and Beam digital converting platforms, to improve their workflow efficiencies to significantly reduce their costs, as well as offering a new level of cutting and creasing performance that will lead to increased product value and job profitability.
These latest Highcon updates have been launched in response to worldwide customer feedback matched to its own R&D roadmap. They have been designed to help customers to better meet the challenges of the pandemic, as well as an increasingly
competitive landscape where margins are tight and product differentiation is key.
“Customers expect us to continually deliver product enhancements and improvements throughout the life cycle of our equipment, and now more than ever, it’s important that we support them. The initiatives launched today, once implemented at each of our customers’ sites, will have an immediate benefit, but they will also secure future success too. For example, our new unified software platform approach will ensure that all Highcon customers continue to benefit from Highcon DART (Digital Adhesive Rule our ongoing R&D investment in Technology) writing head

software tools for years to come,” comments Shlomo Nimrodi, CEO at Highcon.
New pricing model: Highcon is introducing consumables and services at a new bundled price, allowing for consistent pricing of any job. Customers will be afforded the simplicity, predictability, and consistency to make it easier to understand their costs and drive better future business decisions – crucially, making considerable savings in the process.
Austin Meissner, V.P. Operations at Color Ink, Sussex WI, USA said, “We are very excited about the new Highcon business model for consumables and the 5th generation foil & resin.”
New consumables: Highcon is also launching its 5th Generation DART Consumable set (5thGDC), engineered to improve crease quality and reduce setup time by up to 20%. It also features a broader range of supported boards, leading to greatly increased application possibilities and ensuring that Highcon finished jobs meet the quality requirements of major brands.
As the name suggests, this is the fifth generation of consumables since the Highcon Euclid was first introduced, representing years of R&D investment in optimizing specialized proprietary consumables, for dynamic, digitally driven physical creasing.
According to Francois Boussioux of Autajon/Haubtmann “We are very happy with the quality achieved by the Highcon 5thGDC. The crease
Luxury packaging market in Asia Pacific to witness high growth to 2026 - China is a key market driver for growth in luxury goods.
quality of our applications has reached new heights and the crease lines are uniform and without cracks. Setup times have also been reduced and the use of foam strips has significantly dropped. Altogether, we see a terrific improvement.”
Operating System: Highcon is releasing a new and unified software version for both Euclid and Beam platforms, delivering new and upgraded features/capabilities to all our customers. Highcon Euclid customers, some of whom have been running their Highcon solutions for years, will now be able to upgrade their operating system and PC hardware to run the newest version, ensuring optimum production performance, as part of an annual service contract.
Shlomo Nimrodi, concludes: “Our business is growing rapidly, but our vision has remained laser focused - we are dedicated to customer success. And because it answers so many of the big issues faced by our industry and the wider world, we are also committed to making digital finishing a mainstream technology. “From increasing on-shelf appeal to dramatically reducing minimum order quantities and reducing stock and storage, to the recyclability and overall sustainability attributes of product packaging, we believe that digital
The luxury packaging market was valued at USD 16.65 billion in 2020 and is expected to reach USD 22.37 billion by 2026 and grow at a CAGR of 4.8% over the forecast period of 2021-2026, according to a new research by Reportlinker.
The use of luxury packaging for packaging and decorating high-end products is driving the market’s growth. Major packaging vendors are gaining access to numerous high-quality materials and innovative shapes, as these properties improved the consumer experience.
Factors such as changing consumer preferences, growing willingness to spend more, and rising focus of various brands on design, processes, and the overall product development drive the luxury packaging demand.
The report titled "Luxury Packaging Market - Growth, Trends, COVID-19 Impact, and Forecasts (2021 - 2026)", indicated that the Asia-Pacific region is expected to witness the highest growth rate.
Asia-Pacific is expected to grow substantially in the forecast period, due to the increase in disposable income

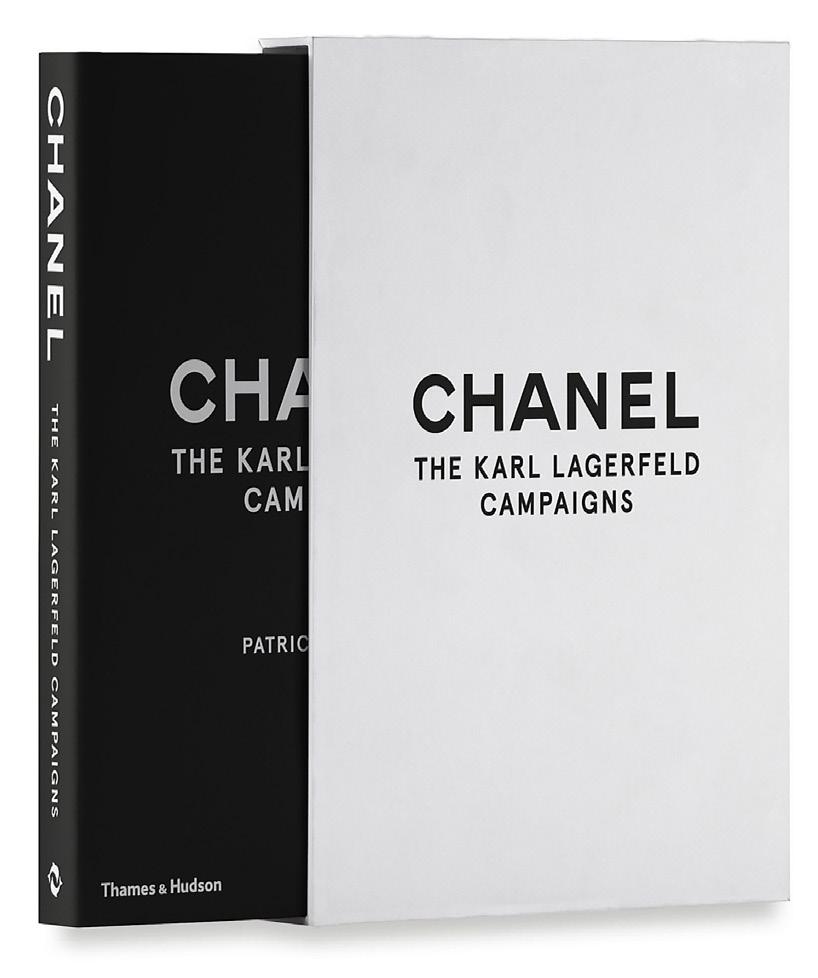
and consumer’s spending on luxury products in the region.
Large population and massive urbanization have led to the rise in the adoption of urban lifestyle, due to the changing consumer patterns and the rising demand for luxurious products. According to the National Bureau of Statistics of China, about 60.16% of the total population lived in cities in 2019.
Sustainable packaging is also driving the market in the Asia-Pacific region. Manufacturers of high-end products are focusing on producing packaging by the help of bio-degradable materials. In addition, major international brands are focusing on eco-friendly luxury packaging solutions to maintain the sustainability goals.
The major key factors driving the growth of the market include a massive increase in the number of product launches in the fashion and cosmetic sector. The major international brands are eyeing on the emerging economies, such as China and India, to set up their stores in these countries, as these countries pose various growth prospects.
The rise in penetration of online retail and travel retail, increasing innovations in technologies in luxury packaging, and others are among various other factors, driving the growth of the market in the region. leading luxury brands, as the country is fast turning into the world’s largest consumer of luxury goods. Chinese consumers are also looking for easyto-use and quality food products. A surge in online retailing in China is expected to drive the demand for luxury packaging solutions.
Paperboard is Witnessing an Increased Adoption Paperboard is one of the most popularly used materials in packaging. Some of the other used materials include metal, glass, plastic, and wood, among others. Most of these materials used are easily sourceable and, at the same time, help to establish a sense of premium quality in the minds of customers.
Paper and paperboards have maintained a strong position in luxury and premium packaging, with their ability to serve as the canvas for flawless graphics and eye-catching decoration. The features, such as laminations, unique coatings, super embossing, and debossing effects, make papers much more attractive in the packaging of luxury items. These packagings also provide superior strength and smoothness.
In the high-end wine and spirits segments, papers have always been popular label materials. The craft-beer brands use paper-labels to describe or advertise the products’ premium or handcrafted values.
Due to the wordlwide lockdown because of COVID-19, the supply chain of the luxury packaging market was disrupted. But the market is recovering and is not supposed to create any significant effect in the long run.
Xeikon adds brand new CX50 press to its wall decoration suite
Xeikon announces an eco-friendly, cost-effective digital answer to today’s wallpaper production challenges. As a key part of Xeikon’s Wall Deco Suite and with Xeikon’s bespoke and environmentally friendly dry toner technology with extended colour gamut, the new Xeikon CX50 is introduced.
The Xeikon Wall Deco Suite is an allin-one streamlined solution including inline finishing – all developed to cost effectively produce creative wall decorations including custom illustrations and photomurals in short runs. Meeting today’s consumer demand for individualised home interiors, the Xeikon CX50 digital press offers unlimited creative freedom across a wide range of substrates where every printed product can be unique.
Dimitri Van Gaever, Market Segment Director for Graphic Arts, states, “Xeikon has once again led the way in bringing to market a complete endto-end solution for wall decoration production. What we have put together is a complete automated Wall Deco factory coming together to produce a quality finished coreless roll.
The Xeikon CX50 digital press fits perfectly into our portfolio for wallcovering applications, midway between the Xeikon 3050 REX entry level option and our high-end Xeikon CX500 digital press. For higher speeds the Xeikon CX50 can be upgraded from 20mpm (65ft/min) to 30mpm (98ft/min). With Xeikon’s dry toner technology and advanced
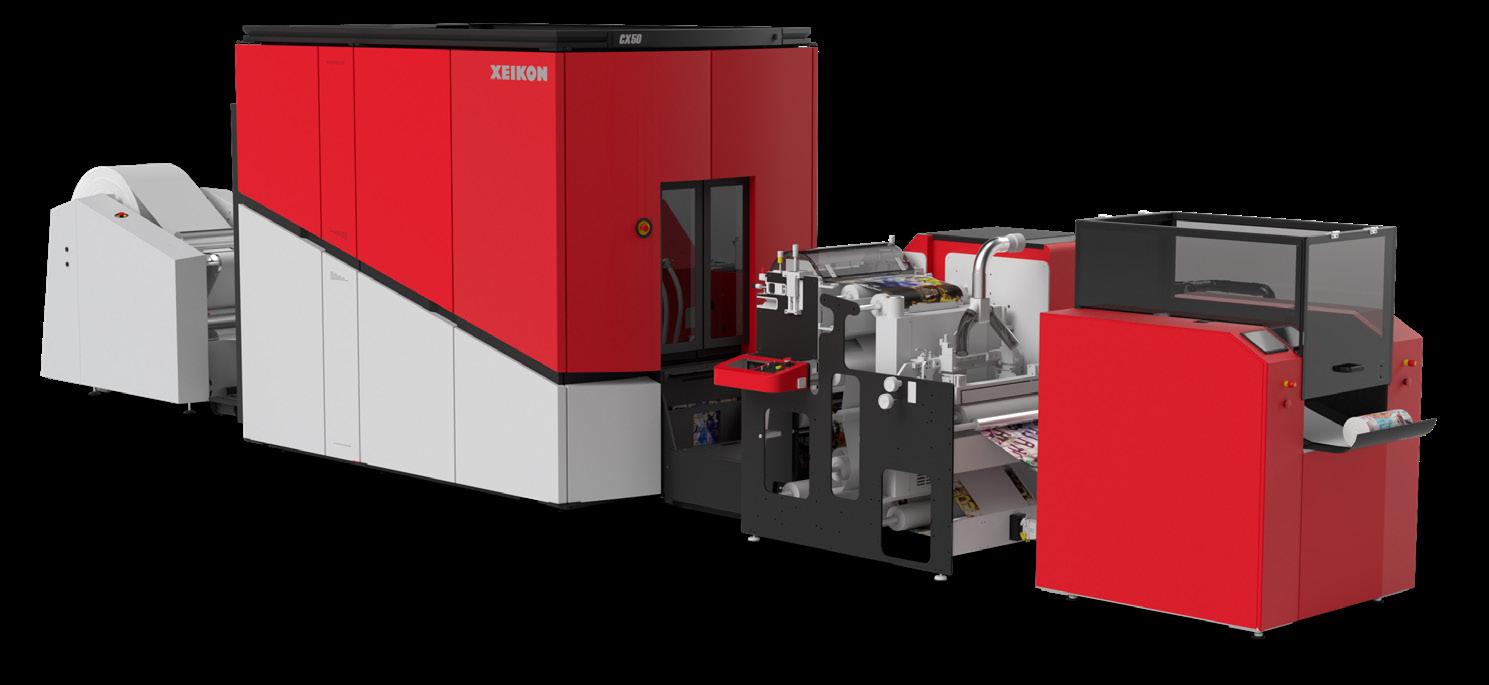
colour management capability with new generation interfaces and cloud connection, the Xeikon CX50 simplex digital press is designed to offer maximum OEE and TCO.”
The wall decoration business has huge potential, however online ordering, stricter environmental controls and consumer demand for unique products is presenting a number of challenges for conventional wallpaper companies. Xeikon is dedicated to helping its customers improve business profitability and drive growth through our creative solutions. Xeikon has designed and developed its Wall Deco Suite to give businesses an allin-one cost-effective solution which can give them every advantage in the marketplace.
Like all of its presses, the Xeikon CX50 is driven by Xeikon’s powerful and intelligent X-800 digital front end for full automation and integration. Xeikon’s Digital Front End (DFE) workflow is a true differentiator and enabler and can be integrated with common ERP and MIS systems. The X-800 workflow, which is the same across all Xeikon dry toner solutions, features a ‘poster layout’ function for murals and wallcoverings to ensure spot-on registration for seamless installation.
Accuracy of colour reproduction is guaranteed by an integrated on-press inline spectrometer and an optional registration camera. The Xeikon CX50 press provides superior colour consistency and an extended colour gamut. Xeikon’s developed dry toner is available in CMYK, Red, Blue, Green, Orange and Magenta, plus additional colours such as one-pass opaque white and colours produced on customer request. Inline finishing equipment has been specifically designed to work within Xeikon’s Wall Deco Production Suite and includes inline water-based varnishing, slitting, waste removal and coreless rewinding, providing a fully finished wallpaper roll, ready-to ship, in one operation.
Van Gaever concludes, “Part of Xeikon’s ongoing value proposition is to offer the market choices to help customers drive business growth. We believe a successful and costeffective investment in a digital production solution works best when it is based on expected and realistic print volumes. The Xeikon CX50 press is ideal for those working in wall decoration production with flexible orders and shorter runs.
With its capability to upgrade to higher speeds, an investment in this press ensures and secures future business growth. With Xeikon’s long standing expertise, we can help our customers make relevant and appropriate choices. We are recognised as a ‘go to’ trusted advisor and solutions provider. With the introduction of our Xeikon CX50 digital press for Wall Decoration, we strengthen our comprehensive portfolio so that our customers can find everything they need from Xeikon.”
Fujifilm invests in new US $19m ink production plant
FUJIFILM Imaging Colorants, Inc. (FFIC), will construct a new production plant for pigment dispersions, which is a colorant for water-based pigment inkjet inks, in order to accelerate the growth of the global inkjet business.
Construction will start in April 2021 and is scheduled for completion by 2022. The investment for this construction is approximately US $19 million.
Inkjet technology has the capability to deliver fast, versatile, print production at short or long run-lengths with variable data. Applications for inkjet are expanding into industrial fields such as packaging printing in addition to commercial and publishing printing. In particular, there is a growing need to use water-based pigment inkjet inks, which have low environmental impact and potential to meet requirements for food packaging safety compliance.
Currently, FFIC Inc. in the U.S. is a water-based inkjet ink manufacturing facility. By adding the new production plant for pigment dispersions (the main colorant in water-based pigment inkjet inks), it will be able to produce consistent, fully-featured water-based pigment inkjet inks built with Fujifilm's own core dispersion technology.
Fujifilm's pigment dispersions are based on its unique “RxD (Reactive Dispersant)” technology, which crosslinks polymer dispersants adsorbed on the pigment particles. The dispersant prevents desorption from the pigment, creating a very stable dispersion. This technology makes RxD dispersions suitable for multiple applications as they enable the design of stable ink formulations that meet demanding performance requirements.

Fujifilm uses RxD dispersions not only for its own inks, but also supplies to ink manufacturers around the world, and they are used in many water-based pigment inkjet inks.
Currently, the development and manufacture of pigment dispersions using RxD technology is limited to FUJIFILM Imaging Colorants Ltd. (Grangemouth, Scotland) in the U.K. In the establishment of a new dispersion plant at FFIC Inc, in the U.S., Fujifilm will continue to ensure the production of the highest quality products and strengthen global supply capacity to meet the future needs of the growing industrial inkjet market.
“RxD is a key technology for current and next-generation water-based inkjet inks,” said Ian Wilkinson, President & Chief Operating Officer of FFIC Inc. “Expansion of our manufacturing capacity is part of a commitment to ensure we can meet increasing demand to support our global customer base. We are already manufacturing a very high-quality, high-purity product in the U.K. In this venture we are using the design and project management expertise of our U.K. team to execute this project in the U.S. This, alongside expert knowledge, technology and processes will ensure that we manufacture RxD dispersions to the same exceptional standard across both sites.”

Unilever making progress tackling plastic packaging in Asia
In 2019, Unilever announced its commitment to halve the use of virgin plastic in its packaging, and to help collect and process more plastic packaging that it sells. The organisation hopes to achieve this by 2025.
Unilever announced that around 11% of its total plastic packaging worldwide consists of recycled plastic, a progress towards its 25% recycled plastic use by 2025.
Unilever has updated on its progress in Asia Pacific through partnerships, collaborations and initiatives. Using Technology In China, Unilever teamed up with the Alibaba Group to create an Al-enabled recycling system for plastic bottles. Through the Waste-Free World initiative, Unilever installed 20 recycling machines in offices and community spaces in two of China’s largest cities, Shanghai and Hangzhou. The machines automatically identify the plastic the bottle is made of, sort and store it, so it can be collected and returned to recycling centres and fast-tracked for reuse. Consumers earn Unilever coupons and green energy points on the Alipay ‘Ant Forest’ for each bottle they deposit.
In Indonesia, Unilever utilised ‘Google My Business’, a platform that enables consumers to find the location of nearby waste banks directly on Google Maps. At the moment, almost 800 waste banks are searchable on the digital tool in 18 cities. Unilever aims is to make 2,000 available.
Investing in waste management systems in Asia Together with other large consumer goods companies such as PepsiCo, P&G and Coca-Cola, Unilever has collectively pledged a total of US$100 million to the Circulate Capital Ocean Fund – the world’s first investment fund dedicated to preventing ocean plastic.
By demonstrating the investibility of the waste management and recycling sectors, Circulate Capital’s aim is to attract the billions of dollars of institutional investment needed to scale companies and infrastructure across South and Southeast Asia. These regions contribute disproportionately to ocean plastic pollution, primarily because they lack the infrastructure to manage the problem.
The fund provides financing to waste management, recycling and circular economy start-ups and SMEs in India, Indonesia, Thailand, Vietnam and the Philippines, helping solutions to scale and replicate by connecting them to supply chains, including those of the world’s leading companies.
One such investment is Recyckal, India’s first waste-commerce company. Recyckal provides end-to-end digital solutions that connect waste generators, processors, recyclers and brand owners. It also facilitates material flows and transactions across the waste management and recycling value chain. Developing Holistic Solutions Four years ahead of plan for India, Unilever will collect and process more than 100% of the plastic packaging it sells.
Since 2018, Hindustan Unilever has facilitated the safe disposal of more than 120,000 tonnes of post-consumer-use waste. In Mumbai, Unilever partnered with the United Nations Development Programme (UNDP) and consulting firm Xynteo to create material recovery facilities. The aim here is to demonstrate the feasibility of inclusive end-to-end waste management solutions.
In a separate collaboration, Unilever Pakistan has partnered with UNDP to make Rahim Yar Khan a zero plastic waste city. The initiative will test solutions to reduce plastic waste and turn it into a resource. The ultimate aim is to create a circular economy system for plastics waste management that can be replicated across the country.
iDurst Group. “With the predictive maintenance developed in the project Framework and the machine learning techniques used will in future trigger the maintenance of the printing systems independently in order to guarantee predictable and trouble-free operation.
