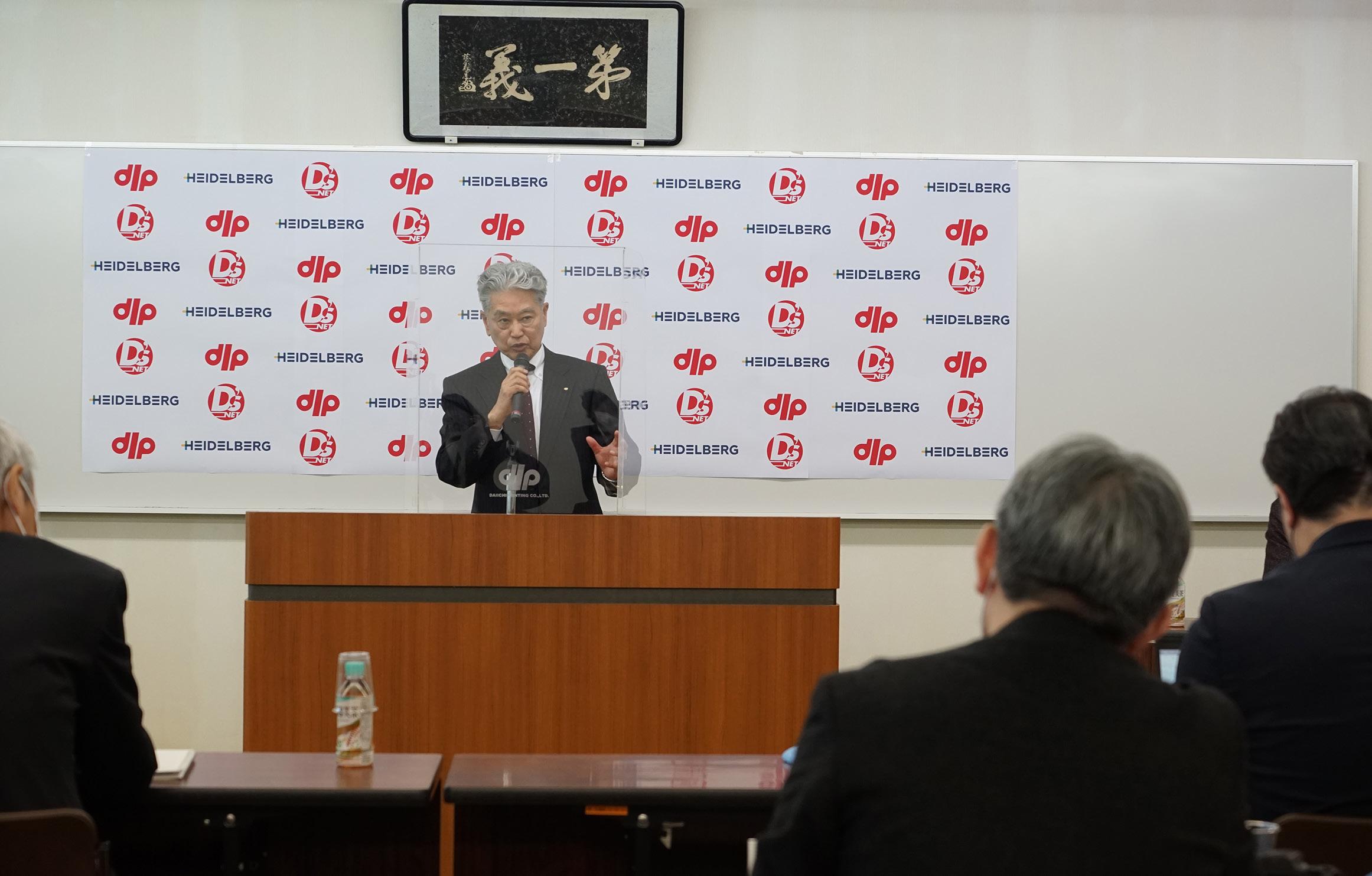
4 minute read
Realizing high-quality service and contributing to the community.
Daiichi Printing Co., Ltd.,(Daiichi) with 240 employees, is a comprehensive printing company headquartered in Niigata City, Japan.
Advertisement
The company is constantly aiming to exceed the value and expectations of their clients. With a one-stop service that integrates everything from planning to prin-ting and delivery, as well as digital, video, promotion, and outsourcing. whilst at the same time contributing to the local community.
In April 2018, Daiichi installed their first Speedmaster XL106-8-P with DryStar LED. This peak performance Heidelberg XL Press was installed to meet the increa-sing demand as well as to meet the changing environmental expectations within the printing industry.
Since its introduction, the company has achieved and deployed fully autonomous printing using their productivity and reliability for their customers. The latest 2020 Generation Speedmaster is the core printing press for the company. We are able to produce high-level printed products, with “high-quality service“ which was our ultimate goal. We also wanted to contribute to and revitalize the local community.”
Heidelberg‘s Push to Stop philosophy, achieving the world‘s highest level of print quality in 2020. Achieving a global OEE average of 20, while it was said to be in the desired percentage range, we actually managed to achieve a figure of 37.7%, which far exceeds the target OEE of 31%.
In February 2021, Daiichi invested in a second press, the latest 2020 Generation Speedmaster XL106-8-P DryStar LED, which was customized to suit the high levels of productivity and quality that Daiichi had established and wanted to continue achieving. The company‘s president, Mr. Hajime Hori, noted that although Japan was being disrupted by the Corona di-saster, they took the decision to purchase the machine to strengthen Three points improving the company’s production model Hironobu Koide, managing director identified three points as the aim of this new press. “The first is the realization of a oneman operation. A similar machine usually requires two operators, but this a more intel-ligent and automated machine and can be operated

Accelerate production innovation with the Speedmaster XL106-8-P DryStar LED 2020 Generation
"The latest 2020 Generation Speedmaster is the core printing press for the company. We are able to produce high-level printed products, with “high-quality service“ which was our ultimate goal."
Mr Hajime Hori President of Daiichi Printing Co., Ltd.
by one person. The additional manpower can be then allocated to other processes so that the productivity of the entire group can be increased.
The second is efficiency by moving to a common prin-ting plate size reducing the complexity of plate sizes and automating the plate making process. We now have choices to share the workload between machines and streamline the post press processes. size printing presses from six to four. By reusing the factory space created by this, we have optimized the workflow within the factory and improved the efficien-cy of our production control.”
Heidelberg Assistant software is used for the collection of vast amounts of data from internet-connected machines with software for production analysis as well as for predictive maintenance.

Heidelberg eShop. It is a convenient IoT tool that you can use.
Heidelberg Assistant, according to Mr. Kiyoto Minami, General Manager of Product D‘s NET Promotion Office, Manufacturing Headquarters, who introduced Heidel-berg Assistant is an indispensable tool for daily work, I use it every day to see the performance of the machine and turn the PDCA cycle to improve our production efficiency as well as checking the condition of the machine, schedule service calls, order status of parts and maintenance. I use it in various situations such as checking the contract status of the company.
Haruo Nakata, general manager manufacturing, said that Prinect analyze point is indispensable for the business. „The first thing I see after coming to work every day is Prinect’ s analyze point, I see the operating status data over time, not just the fixed numbers such as operating time and average number of revolutions.
The operators are working hard whilst looking at the OEE on the wall screen of the machine, which is a great motivation. I think this also leads to an improvement in the productivity of the entire factory. One month after the introduction of the 2020 Genera-tion Speedmaster XL106-8-P DryStar LED it has printed more than 2 million impressions, and the production record is about 1.4 times that of the previous year. “In the future, we will aim for 1.5 times more productivity with the two Speedmaster XL106s, which means that we will have three productions from two machines, and another invisible XL106.” Mr. Koide said with a smi-le his willingness to further improve productivity.
The latest 2020 Generation Speedmaster XL106-8-P DryStar LED features include:
• The most highly automated and most intelligent Speedmaster delivering operator-independent high performance.
•The in-line color / register measurement control system „Prinect Inpress Control 3“ accurately measures and controls the color and register during printing even at the highest speed.
• Variable air transfer system with dynamic sheet space control provides non-contact paper transfer based on characteristic profiles for excellent print quality for single-sided and double-sided printing.
• Robust mechanical design delivering smooth operation at speeds of up to 18,000 sheets per hour.
