
4 minute read
Challenges and Opportunities for Mono-Material Packaging Businesses in Asia
The present global demand for mono-material flexible polymer packaging is estimated at 21.5 million tons per annum with a value of nearly USD 59 billion. According to the Smithers report, The Future of Mono-Material Plastic Packaging Film to 2025, the demand for more sustainable solutions will continue to accelerate and exceed USD 71 billion by 2025 with a total of over 26 million tons consumed each year.
What is this mono-material that is generating so much interest? It is a product that is composed of a single type of material or a product with components that are made of a single type of material. Mono-materials can ease the maintenance, re-use, and provide effective disassembly and recycling of products.
Advertisement
Common Applications
At present, polyethylene (PE) is the most widely used polymer for monomaterial film packaging, accounting for over half of the global consumption.
By Karen PRAGER Senior Manager, Business Development, Packaging, Printing and Converting, Technology - DKSH
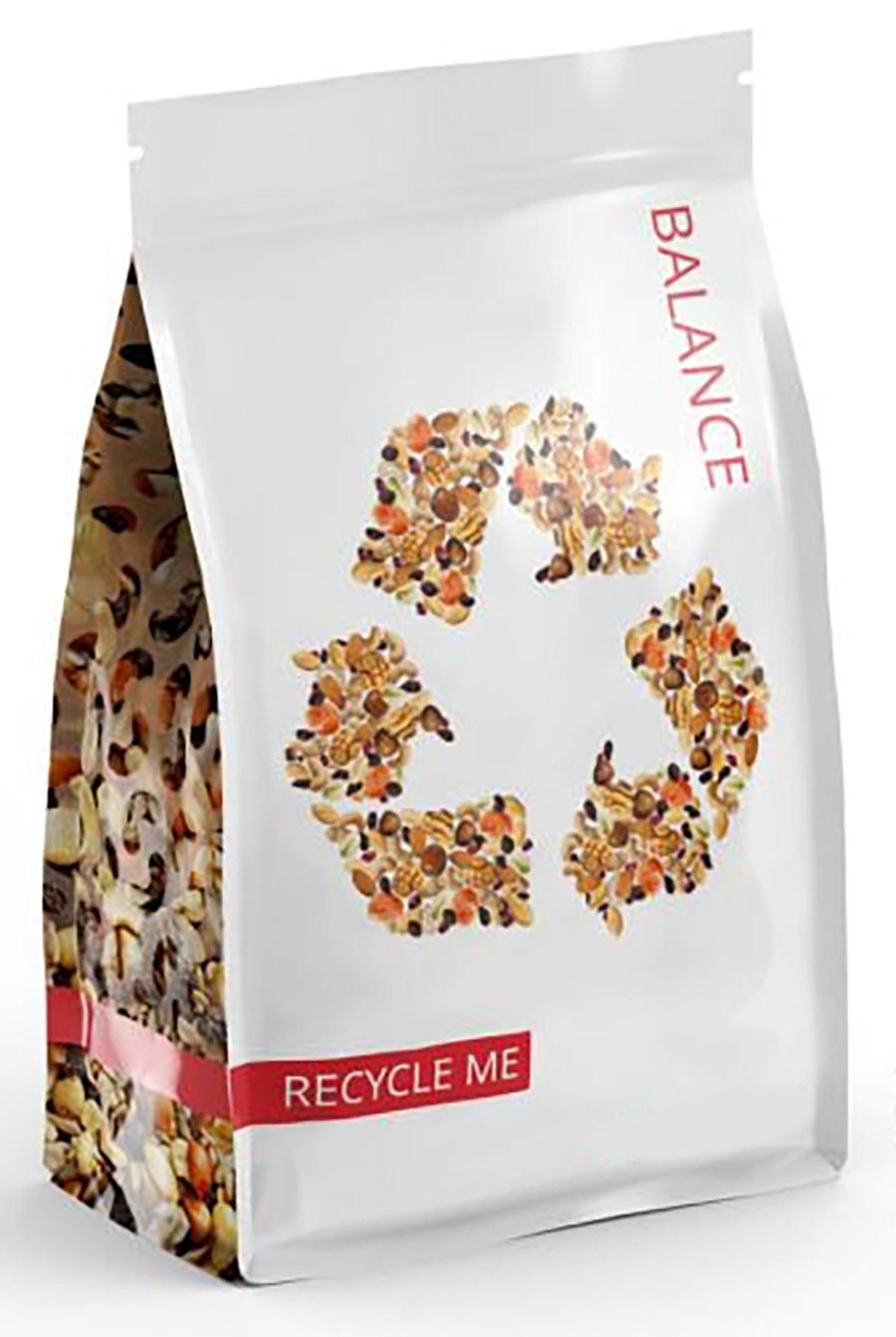
Although PE continues to grow, the demand for polypropylene (PP) grades is rapidly growing. Another alternative material seeing increased interest is the use of regenerated cellulose fiber.
Manufacturers of fresh foods, snacks, and confectionery are the largest users of mono-material film in recent years. The Smithers report also showed that fresh foods will see the highest increase in demand over the next five years. Other fast-growing applications for mono-material film packaging include chilled foods, frozen foods, pharmaceutical, and medical-related products.
Benefits of Mono-materials
1. Recyclable. There is a rising demand for easier to recycle polymer formats across the packaging value chain

to help reduce pollution associated with plastic. Conventional multi-layer composite films are difficult to recycle because of the need to separate the different film layers and many markets lack the necessary recycling systems and processes to do so. Mono-material films on the other hand are fully recyclable.
2. High-barrier properties. Full PP laminated with high-barrier properties is a better alternative for packaging purposes as compared to using aluminum foil. As aluminum foil uses an inseparable barrier layer, it is often tedious for the recycling process.
3. Enhances value chain to customers. As the industry becomes more challenging, adopting mono-materials can offer a significant impact on packaging converters and their value chain. Leveraging on these innovations and technology capabilities could lead to new partnership opportunities to support customers in enhancing their packaging and service portfolios. Examples of these applications include sustainability areas and regulatory requirements.
Challenges in Adopting Mono-material While flexible mono-material packaging is leaning towards eco-friendly and sustainable features, not everyone involved in the industry can keep up with the pace. As it stands, the final link in the chain appears to be the weakest: if there is no optimal sorting or proper retrieval, the initiative will collapse before the crucial circular phase.
There are currently limited opportunities for re-utilization due to the lack of facilities that can process new high-value materials. As such, compromises are made on functionality and the overall quality of the final product.
To create effective packaging, coatings formulators and packaging manufacturers must prevent materials from migrating into food packaging. They also need to ensure adhesion and cohesion in multi-layer laminate systems. At the same time, to remain competitive, they need to create original sensory brand experiences.
Finding the right solution that achieves all this responsibly and sustainably without adding matting agents and toxic compounds, will be the biggest challenge. Here are some potential solutions to consider:
• Blown film lines capable of manufacturing mono layer are required with higher barrier properties to replace laminate structures. Achieving the barrier properties, for example, liquids with higher performance requirements, remains a challenge, however, manufacturers of resins and packaging materials are investing heavily in R&D to overcome this challenge
• Ultrasonic sealing solutions for mono-materials to improve the sealing capabilities are recommended
• Efficient waste extraction systems for packaging machines, slitters, rewinders, and extrusion lines
• Flexographic printing machines with an innovative UV LED drying system which are suitable for fully recyclable mono materials due to their excellent external print properties
The printing and packaging industries in Asia are progressing ahead with the advancement of technologies, and it is not easy to keep up with the continuous innovation and advanced industrial solutions. Here is where a proven partner like DKSH can come in to help businesses with the right solutions to achieve higher efficiency and performance reliability.
If you are considering the best approach to leverage sustainable flexible packaging solutions or simply to learn more about the benefits of mono-materials packaging, start by talking to us to learn more about what is readily available to you. https://www.dksh.com/ppc
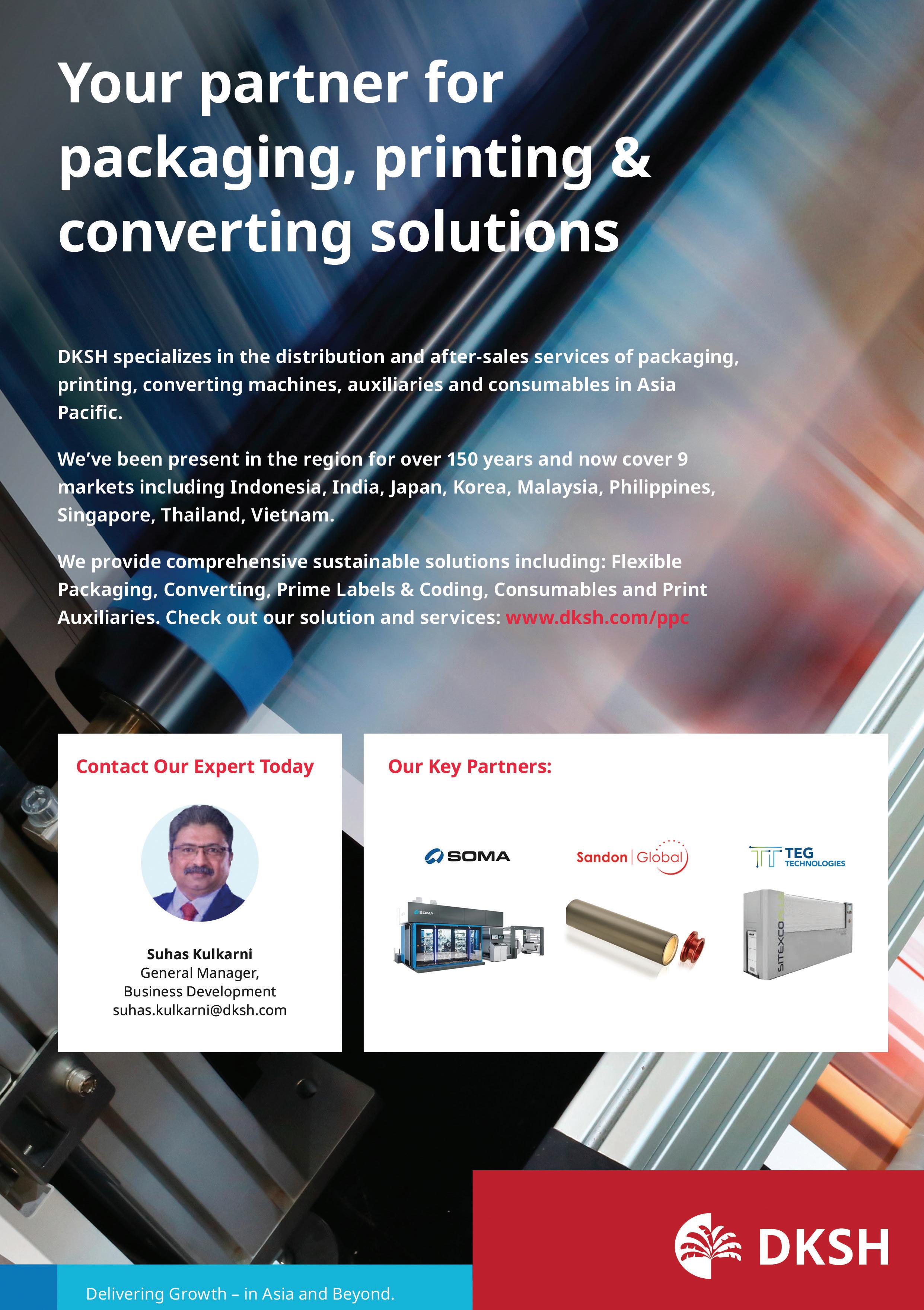