
9 minute read
News from around the world and around the region
Catena+ wins Chinese flexo award
ThermoFlexX’s Catena+ inline plate making system won the CI Flexo Tech Technology Innovation Award. The new award programme was established in 2019, and is the first such award to cover the entire flexo industry in China.
Advertisement
Canmaker demonstrates the power of personalised print on a tin
Personalisation and customisation are far from novel concepts in the graphics market – but in the stubbornly analogue world of print for metal packaging, they still very much are.
In a sign of how this is beginning to change though, William Say & Co., a company with a proud heritage dating back nearly a hundred years, chose to demonstrate the new potential for customisation and personalisation of printed cans by commissioning and forming a run of 100 unique individual tins to give away as Christmas gifts to valued customers. directly with Fujifilm to produce a short run of hot chocolate tins for a special Fortnum and Mason in-store display early last year. Since then, things have moved on even further.”
In 2020 Fujifilm entered into a technology partnership with Tinmasters – one of Europe’s biggest
The aim is “to discover, promote, encourage and commend innovative technologies in the flexo printing industry”. A committee consisting of 46 flexo experts including leading printers, brand-owners, universities, trade magazines and technology suppliers, judged the finalists in the 2020 CI Flexo Tech Technology Innovation Award.
ThermoFlexX imagers and Catena units are designed and built by Xeikon Prepress, Ypres, Belgium. Catena is a modular concept of individual units that can build up to a fully in-line solvent-chemistry flexo plate making system.
Christophe Lievens, Sales & Marketing Director said: “We’re very proud to win this award courtesy of so many peers in our field. We’re fully aware of the demand for the highest quality of flexo print in China. This is a very exciting time for us as Catena systems are our first project 100% combining our equipment design knowledge with Flint Flexographic plate making and flexo print expertise. Development has been a total partnership and we believe the result is a product portfolio of ThermoFlexX and Catena equipment with flexo plates that exactly fits the market-place.” “We’ve been watching developments in digital print technology in our industry for a while,” says Stuart Wilkinson, Marketing and Sales Director at William Say & Co. “We actually had the privilege of working metal packaging printers. As part of this relationship, Tinmasters bought and installed an Acuity B1 inkjet printer at their site in Swansea.

“We’ve worked with Tinmasters for many years,” says Wilkinson. “And now they have this partnership with Fujifilm, and the ability to print extremely high quality short-run work, they were perfectly placed to help us. We’re really excited about the growth potential inkjet offers our business and our industry and we wanted a way to clearly demonstrate this to our own customers.
“We printed a run of 100 tins, in full colour, each with a unique series number. It was a simple exercise that would have been extremely complex and costly using traditional offset print.

“There used to be a lot of canmakers in London. Now we’re the only ones left. And in large part, it’s because of our willingness to seize opportunities like this that we’re still here, and thriving, and will be for many years to come.”
Kevin Jenner, Business Manager, Fujifilm Wide Format Inkjet Systems says: “Inkjet is going to transform the print for metal packaging industry in the same way it has every other print sector from labels, to commercial print to sign and display. It’s happening later and more slowly than it has in other sectors – but it is happening. We’re proud to be driving that change and all the possibilities it brings, and we’re delighted to be working with companies like William Say and Tinmasters to make it a reality.”
The latest static control monitoring solution for modern automated industries
Meech has formally unveiled its newest remote monitoring solution, SmartControl Touch. An advancement of Meech’s SmartControl device – the new unit allows users to monitor, control and adjust the performance of multiple connected Hyperion ionising bars and sensors via an integrated touchscreen; or remotely via a mobile phone, tablet, or desktop.
“SmartControl Touch has been designed in line with the growth of Industry 4.0 technology, which is helping businesses maximise productivity and quality of output,” says Adam Battrick, Sales Director at Meech International. “It’s an advanced monitoring and controlling device that includes a 10” integrated touch screen and data logging, as well as being compatible with Meech voltage and distance sensors – so monitoring the performance of our Hyperion static control bars is easier than ever before.”
SmartControl Touch has the capacity to connect up to six devices, with an additional 12 per expansion unit. In total, SmartControl Touch can monitor and control up to 30 devices. Battrick continues: “Our customers use a variety of our static control bars from our Hyperion range, so giving them maximum visibility and control of their performance via a single device allows for increased productivity and quality output on production lines.”
Fast and easy installation means SmartControl Touch can fit in seamlessly with operations. It is simple to use for operators, offering a userfriendly interface that requires minimal training. Changes can be made quickly and easily, and with voltage and distance sensor compatibility, SmartControl Touch offers more accurate neutralisation of all charges on materials. Data logging also provides graphic representation of performance, which can be exported for additional analysis.

“Like all Meech products, SmartControl Touch has been designed in response to feedback from the industry,” concludes Battrick. “We work closely with our customers to understand their needs and how we can better help them to improve their quality control and productivity. Static charges have always been a threat to productivity for many manufacturing and converting sectors and SmartControl Touch is yet another innovation from Meech designed to keep unwanted static under control and ensure smooth-running and safe production lines.”
The latest static control monitoring solution for modern automated industries
Whilst most of us were glad to see the end of 2020 with all the disruption and distress caused by Covid-19, many label and packaging printers experienced a healthy growth due to growing trends in e-commerce and with brand owners using more variable data printing (VDP) and personalisation to communicate with consumers during this time of uncertainty.
Jim Orford, K600i Product Manager from Domino Digital Printing Solutions, says: “Covid-19 has really accelerated the growth in e-commerce, a trend which is likely to remain after lockdown restrictions are lifted. Brand owners are also placing more emphasis on personalisation to engage with consumers through loyalty and promotional programmes, and to track their products through the supply chain. This has resulted in some of our label and packaging converter customers reporting a 40-50% increase in the demand for variable data printed labels during the pandemic.”
The Domino K600i is all about high quality and high speed digital printing of variable data. This ranges from simple alpha-numeric text and sequential numbering, to a wide range of industry standard machine-readable barcodes and 2D codes, including QR and Data Matrix codes. These are used for logistics and reverse logistics in e-
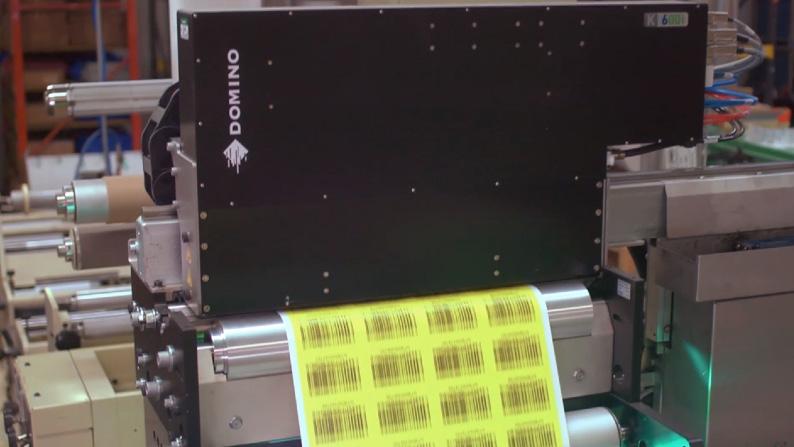

commerce and online retail, for ‘track and trace’ applications in the food and beverage sectors, and for security applications including brand protection, in the pharmaceutical and tobacco sectors. the benefits of Domino’s unique iTech intelligent Technology features, which together result in reduced setup time and maintenance costs, high reliability and uptime, and improved profitability.
Watch Philip Easton, Director of Domino Digital Printing Solutions, walk you through this high speed digital printing demonstration of Domino’s dual bar K600i inkjet printer integrated on an AB Graphic International Omega SRI high speed inspection and slitting line. This was shown in action for the first time at Labelexpo Europe 2019.
This versatile, monochrome UV inkjet printer is available in seven different print width formats, ranging from 108mm to 782mm, in either a standard single print bar or the high speed dual bar configuration. It can be retrofitted onto most conventional printing presses and finishing lines. The K600i can be used with Domino’s UVcurable, LED-curable and aqueous pigmented ink sets, with a high opacity white ink, a fluorescent ink and a clear varnish also available.
The single print bar prints 75 metres per minute at 600 x 600dpi resolution with optimum print density, but can print at up to 150 metres per minute. The dual bar unit demonstrated in this video prints 150 metres per minute at optimum print density, and can still print at 600 x 600dpi at up to 200 metres per minute. Philip concludes, “We recognise converters have a choice from the various inkjet printing equipment suppliers in the marketplace. We are delighted that so many have chosen Domino for high speed digital printing – we now have approaching 1000 global installations based on this 6th generation inkjet technology. Our customers recognise that the K600i digital inkjet printer is simple to run and maintain, offering exceptional productivity and efficiency, enabling them to react to this VDP opportunity and providing profitable, efficient, on-time delivery to their brand owner customers.”
Avery Dennison acquires label material company
ACPO Ltd. producing pressuresensitive overlaminate products for the label and flexible packaging markets. Avery Dennison announced that it has acquired ACPO Ltd. for the purchase price of $87.6 million, subject to certain post-closing adjustments. ACPO is a US company producing pressuresensitive overlaminate products for the label and flexible packaging markets and has approximately 170 employees.
Avery Dennison has acquired the majority of ACPO’s assets, including coating, finishing and distribution operations at its Ohio headquarters, as well as three finishing and distribution sites all over the US. ACPO employees will transition to the Avery Dennison Label and Graphic Materials team. “Our acquisition of ACPO will further strengthen our leadership in core label materials segments,” said Mitch Butier, Avery Dennison’s chairman, president and CEO. “By adding ACPO’s wellregarded and complementary overlaminate product, we are increasing our product portfolio and adding even more value for our customers.”
“We are delighted to have ACPO become part of Avery Dennison,” said Missy Larick, chief operating officer of Esperia Holdings LLC, the holding company of ACPO Ltd. “As anyone in our industry knows, Avery Dennison is a strong, sophisticated global organization and a brand known and respected worldwide, which will help accelerate the commercialization of ACPO products around the globe. We know that tapping into the know-how of Avery Dennison’s materials scientists, with their expertise in adhesives, base labels, and surface chemistry, will dramatically accelerate innovation of ACPO products.”
Jeroen Diderich, vice president and general manager, Avery Dennison Label and Graphic Materials North America, noted that ACPO’s reputation for quality and service, its entrepreneurial spirit and its agile, customer-focused way of working—from quick turnaround to low minimumorder quantities—makes it a good fit for Avery Dennison’s culture and the current state of the market.
“Our top priority is to ensure industryleading service, quality and unmatched customer responsiveness for customers of both businesses,” said Diderich. “We look forward to leveraging ACPO’s strengths, learning from their people, and welcoming them as valued members of the Avery Dennison family.”
With over 42 years’ heritage of developing and manufacturing digital inkjet printing equipment, Domino has created a flexible system with superior performance and reliability. In the video, Philip highlights and explains

