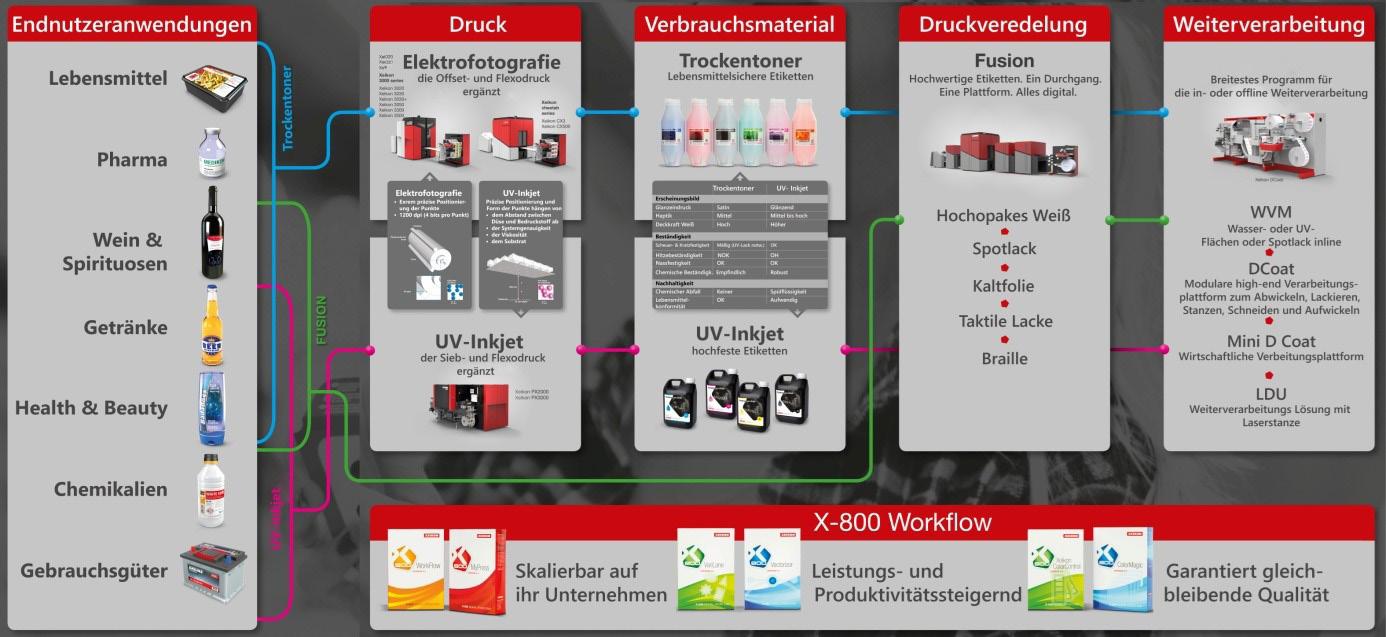
20 minute read
predictions what it will look like ahead News from around Asia and the world
Xeikon white paper on migrationoptimized digital label and packaging printing solutions
The migration behaviour of digital ink systems plays a decisive role in the selection of a digital press and determines to a large extent which application segments the printing system can cover – and to which segments it could be expanded if necessary. These comprehensive aspects of migration-optimised solutions are discussed in Xeikon’s new white paper, in which Lode Deprez, Vice President Technology, provides insight into the criteria that must be taken into account when purchasing a digital printing system.
Advertisement
The white paper initially addresses the question of why there can’t be a “one ink” system that is suitable for all applications in digital packaging printing. It outlines the extremely complex requirements placed on ink systems, which differ in their migration behaviour and whose food safety properties are a very important criteria when selecting a machine system.
In addition, the ink systems used must meet legal requirements. The white paper provides a brief overview of the key regulations issued by legislative bodies, associations and branded goods manufacturers, and provides easy-to-understand information on the current migration limits.
Against this background, it shows the importance of the chemical composition of digital ink systems on migration behaviour. By looking into the different composition of dry and liquid toner and UV inkjet inks, it highlights the advantages of the respective ink systems for different applications.
However, the ink components, with their different molecule sizes, are not the only elements to have an influence on the migration behaviour of digital ink systems. The transfer from printing inks to food depends on other factors such as storage time, storage temperature, barrier properties of the packaging material and, ultimately, the packaged good itself. The white paper also provides clear explanations on this topic.
The result is a clear picture of the user segments in which digital ink systems have their strengths. Divided into the segments of food, pharmaceuticals, wine & spirits, beverages, health & beauty, chemicals and consumer goods, individual recommendations can be derived for each label and packaging printer depending on the composition of their portfolio, which will help them when deciding on a digital printing system. The white paper also goes over the question of how to proceed if the portfolio is to be further developed in a particular direction.
You can download the White Paper here: https://go.xeikon.com/wplowmigration_en
Smurfit Kappa launches additional TopClip packing system designed for smaller brandser
Smurfit Kappa announced the launch of a new packing system for its sustainable TopClip product, a paperbased replacement for plastic shrink wrap that bundles beverage multipacks. This packing system, which is designed for smaller businesses and brands, comes after the launch of their high speed machine with KHS last year. This now completes the portfolio of Smurfit Kappa's end to end solutions for TopClip, ensuring it is suitable for beverage companies of all sizes.
The launch of this new packing solution, and the implementation by Czech beer brewer Pivovar Clock, sees the packaging company selected to supply their innovative and sustainable paper-based TopClip for 500ml cans. A modern and creative brewery, Pivovar Clock are noted within the industry for their early adoption of sustainable technology. The brewer uses the latest steam technology and local ingredients to produce their beer.
Smurfit Kappa has now launched complete solutions, including automation for every shape and size of beverage company, which will be a key characteristic in facilitating the roll out of TopClip with many different brands. Now, with this implementation, Smurfit Kappa has proven their commitment to supplying TopClip, both to the large global brands requiring high-speed machines, and to smaller craft breweries.
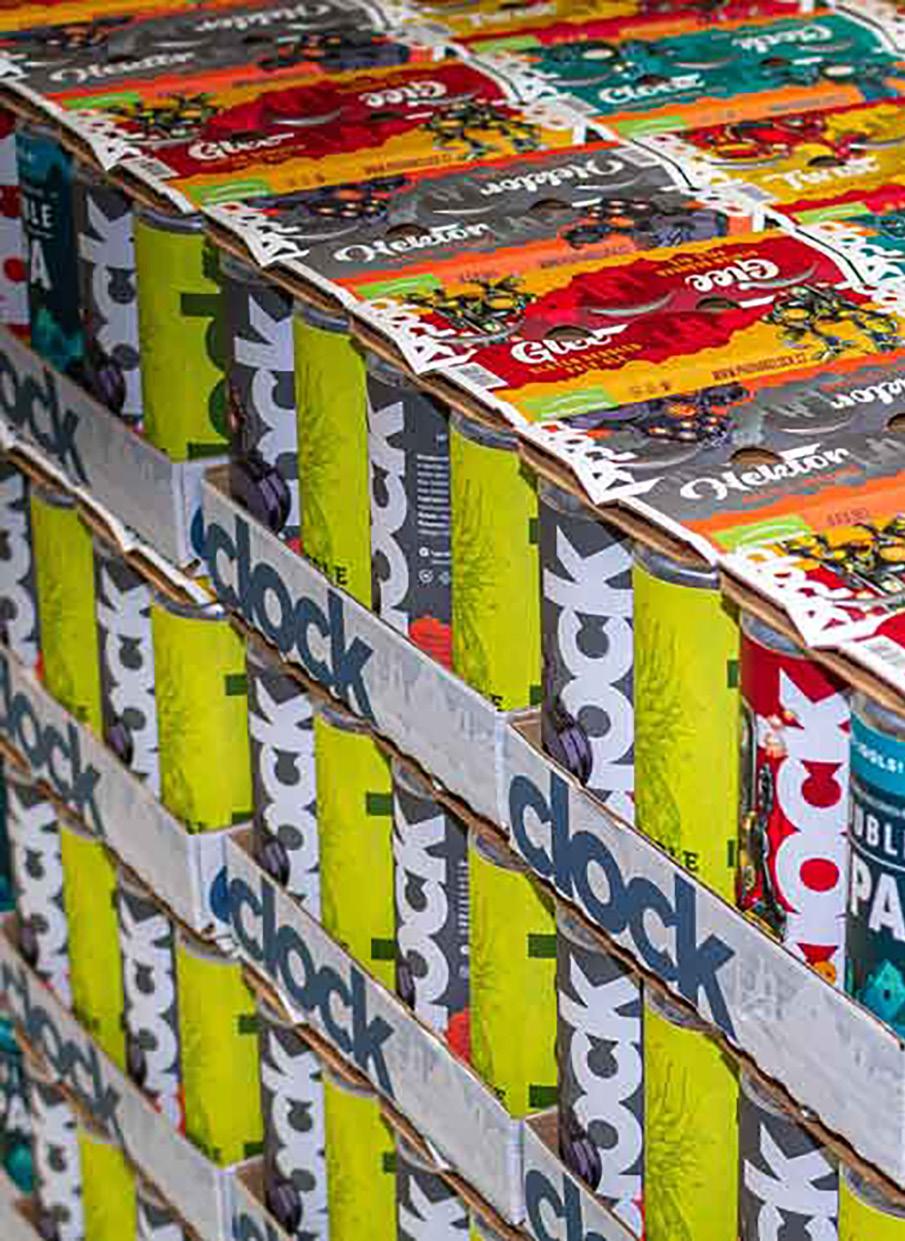
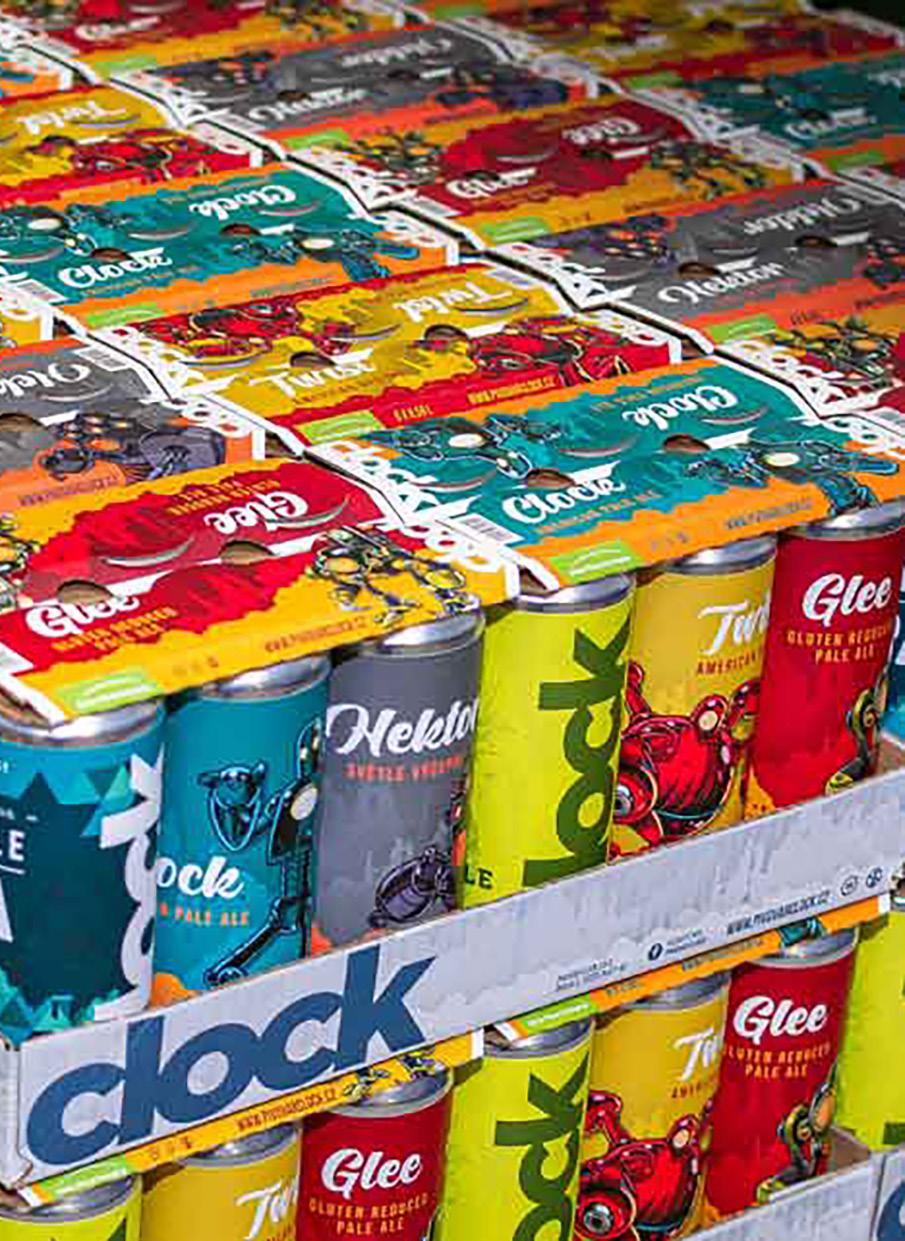
100% renewable, recyclable and biodegradable. As it is made from less material and does not require glue, TopClip is significantly more sustainable than other recently launched same-purpose packaging solutions on the market and offers a premium consumer experience with good branding opportunities.
Welcoming the announcement, Jirí Andrš, CEO at Pivovar Clock said: “As a company, we pride ourselves on only using the highest quality ingredients when making our beers. We want to provide this standard across our business and Smurfit Kappa’s TopClip solution offers us a new sustainable alternative while providing an excellent consumer and branding experience.''
“At Pivovar Clock, we are committed to significantly decreasing our carbon footprint, so by choosing TopClip we are also meeting our environmental obligations by reducing single-use plastics.”
Commenting on the news, Arco Berkenbosch, VP Innovation and Development, at Smurfit Kappa Europe said: “We are delighted to partner with Pivovar Clock by providing their consumers with the latest in innovative and sustainable packaging solutions. Whether you’re a small or large beverage company, there is a version of TopClip to suit your business.”
“With our portfolio of machine solutions, Smurfit Kappa can provide a holistic offering to reduce your carbon footprint and ultimately help grow sales,” concluded Mr. Berkenbosch.
The announcement means that TopClip, which has already been available in the UK and the Netherlands with other brands, will be now additionally be available to consumers in the Czech, Polish and Slovakian markets.
TopClip is part of Smurfit Kappa’s Better Planet Packaging, a portfolio of innovative packaging solutions designed to be more sustainable and always made from a renewable and recyclable raw material.
SOLitrack 2.4 delivers web-based job control, proof and approval, and JDF finishing control for an efficient PDF-centric production print workflow
Solimar Systems, provider of leading workflow solutions for print production and digital communications, today announces the release of SOLitrack™ version 2.4. This version includes many new features including web-based job control, proof and approval capabilities, and JDF finishing for PDF files — all to maximize the effectiveness and efficiency of a remote print production workflow.
Key to the ease-of-use and overall visibility that SOLitrack 2.4 provides is a central dashboard, now available worldwide as a web-based platform with SOLitrack Mobile. The dashboard displays event notifications and tracks Solimar’s Chemistry™ platform components in detail providing users in-depth views of their production workflow processes.
SOLitrack 2.4 keeps a continuous record of processing activity which provides a history of the entire workflow that can be viewed and reported on in real-time. The platform constantly monitors the production workflow for errors, notifying appropriate users on issues or events needing attention.
“Many print businesses need their operational staff to remotely oversee and manage processes in their factories. As such, company managers need visibility, live access, and control to ensure production processes run smoothly,” states Jonathan Malone-McGrew, Senior Director of Engagement, Solimar Systems. “SOLitrack provides a comprehensive, reliable production print workflow solution to do just that. It enables companies to track and report on workflow processes from the shop floor or remote locations.”

In addition, the Proof and Approval feature in SOLitrack 2.4 empowers In-Plants and Print Service Providers (PSPs) to automate the approval process of jobs and work orders.
From the secure, web-based SOLitrack client, everyone in the approval chain can easily review, approve or reject jobs. Individual components of jobs can be managed with the Piece Level Tracking (PLT) feature. This Proof and Approval process also supports multi-step approvals, including rules for the overall review process, notifications and auto-approvals based on schedules and events.
With SOLitrack’s support for Job Definition Format (JDF) finishing controls, operators can direct jobs to JDF-enabled printers to dynamically apply the appropriate tray calls, stapling, binding, or other finishing. The benefit for PSPs is time savings, a simplified print production workflow and overall reduced operational costs.
“We’re excited to deliver this new functionality and grateful to our Customer Advisory Council members who provided helpful insights to help boost their productivity and empower remote working,” adds Mary Ann Rowan, Chief Experience Officer, Solimar Systems. “We’re working hard to make 2021 a stellar year full of valuable enhancements as well as a celebration of our 30th anniversary.”
Certified drivers for HP’s new portfolio of versatile Latex printers
SA International (SAi), the leading provider of software solutions for professional signmaking, wide-format digital printing and CAD/CAM machining industries, has announced that they now offer certified drivers for the new HP Latex 700 and 800 Latex Printers.
SAi’s Flexi RIP design and print software enables you to fully utilize the advanced new features of the HP printers, including multi-layer printing. SAi Flexi will also separate layered PDF files into separate pages for printing. With an integrated HP online media library, users can view and download the latest media and print modes directly to their printer, which auto-synchronizes with Flexi creating a seamless workflow.
In addition to advanced workflow features, SAi Flexi supports white ink layered printing, a versatile and powerful tool. Flexi can generate white ink on the fly or from the white layer from the predefined design. Users can control how white ink is printed in both the Flexi Design and Flexi RIP Production Manager functions. With the ability to preview the white channel beforehand, users save RIP and print time and avoid wasted materials.
SAi also provides drivers for:
HP DesignJet Printer Series HP Scitex Printer Series HP Stitch Printer Series All HP Latex Printers SAi Flexi is the industry leader for creating a variety of applications such as vehicle wraps, banners, signs, soft signage and much more. With a low monthly operating cost, SAi Flexi subscription includes free software upgrades, e-mail and phone support and all of the design and production features SAi Flexi has always been known for.

Thailand-Based NR Instant Produce PCL Leverages V-Shapes Unique Sachet Packaging for Continued Growth
V-Shapes, an innovative supplier of vertically integrated products and services for convenient, hygienic and sustainable single-dose packaging, today reported that Thailand-based NR Instant Produce PCL, a leading global manufacturer of sustainability produced ethnic, plant-based and functional foods, has installed four V-Shapes ALPHA packaging lines to support manufacture of its non-food consumer products for domestic and international distribution, including its Sustainable
Development Brand (SDB) clean shots hand sanitizer as well as co-packing of third-party products. The company, which was founded in 1991 and had annual sales of approximately € 31 million in 2019, was recently listed on the Stock Exchange of Thailand (SET) with the distinction of being the first purpose-led listed Thai company in the field of plant-based food, its primary business.
The company has manufacturing facilities in Nakhon Pathom and Ratchaburi provinces in Thailand and plans to invest in plant-based manufacturing plants in the UK and United States. The IPO will also provide funding to reach a total of five (5) V-Shapes manufacturing lines for the production of sanitization products for sale in Canada, the United States and the Middle East.

NR Instant Produce PCL is building a global platform focused on producing the future of food, building state-ofthe-art facilities in key geographies around the world to enable the production of food that will support a world of 10 billion people by 2050. “We decided to partner with V-Shapes in December 2019,” said NR Instant Produce PCL CEO Dan Pathomvanich. “We saw it as a super-cool solution that has provided us with a packaging solution that is very different and unique from what everyone else is offering.”
NR Instant Produce PCL is another example also of V-Shapes’ ability to adapt to pandemic conditions by providing virtual installation support using smart glasses. Pathomvanich added, “The experience of virtual/ online commissioning is perfect to help a company and not commit any error during the installation while keeping everyone safe.”
In addition, with V-Shapes lines in place, NR Instant Produce PCL was able to assist with pandemic mitigation by providing 10 million of its SDB clean shot hand sanitizer sachets, produced with V-Shapes technology, for use in the Southeast Asian region. “Prior to implementing V-Shapes,” Pathomvanich said, “we would have been unable to provide this critical service.” V-Shapes technology in the Southeast Asian region, and the availability of this unique packaging approach is also generating new business for the company. “We are very happy with the configurations we have in place today,” he concludes, “but we are also looking forward to continued innovation from V-Shapes, including in-line printing, that will make us more productive and enable us to provide faster cycle times and more variations in the products we provide to our customers.
Another reason we chose V-Shapes is their consistent work towards a circular economy and the continuous development of sustainable materials with a 360-degree approach to using compostable, biodegradable, and/ or recyclable materials, laminates and substrates.”
Pathomvanich also notes that V-Shapes brings a high level of quality and state-of-the-art technology to the market, including the fact that there are a number of patents in place on the process, as well as the unique single-dose packaging it enables. These were also contributing factors to choosing to partner with V-Shapes.
MPS Systems extends production floorspace
MPS Systems extends their floorspace with a 1.600 m2 building across the street from their headquarters based in Arnhem, Netherlands. The additional space will be used to extend production capacity, warehouse logistics, and secure space for future growth.
Following a move in 2015 from MPS’ previous headquarters in Didam to a more conveniently located and modern building in Arnhem, MPS experienced rapid growth. As the new assembly hall in Arnhem became too restrictive in size to accommodate the increasing demand of MPS machines sold, MPS invested considerable time searching for an alternate location in close proximity.
More space and new possibilities The new MPS facility with 1.600 m2 floorspace will be used initially to extend the warehouse and MPS assembly lines. “Having a beautiful, spacious building just across the street from our headquarters doesn’t just give us more space and new energy, but also plenty of new possibilities to consider,” said Anton Spierenburg, MPS Supply Chain & Operations Manager.
“With our ambitious global plans, MPS is planning for more growth in the future. We’re planning to use this space for the build of our press lines, but it also gives us the opportunity to redesign our main building to maximize space and efficiencies in both locations.”
MPS’ address remains the same at Delta 100 in Arnhem, the Netherlands. The new location is Delta 134.
Sensors Finding Their Way Into Various Areas
If a single image can show what a business is all about, the cat on the gin box is the one that does just that for Victory Graphics. The attention-grabbing combination of dark black tones, a fine image and bright reverse-outs are exceptional enough, but when you
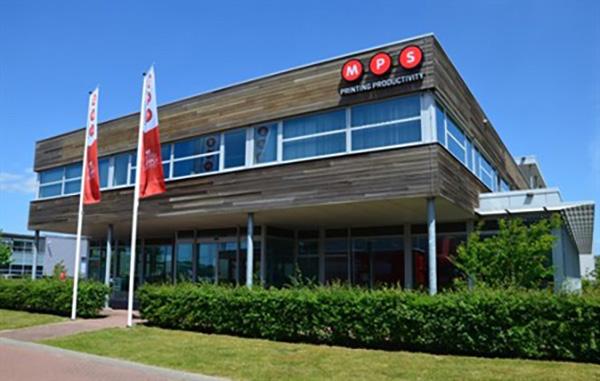
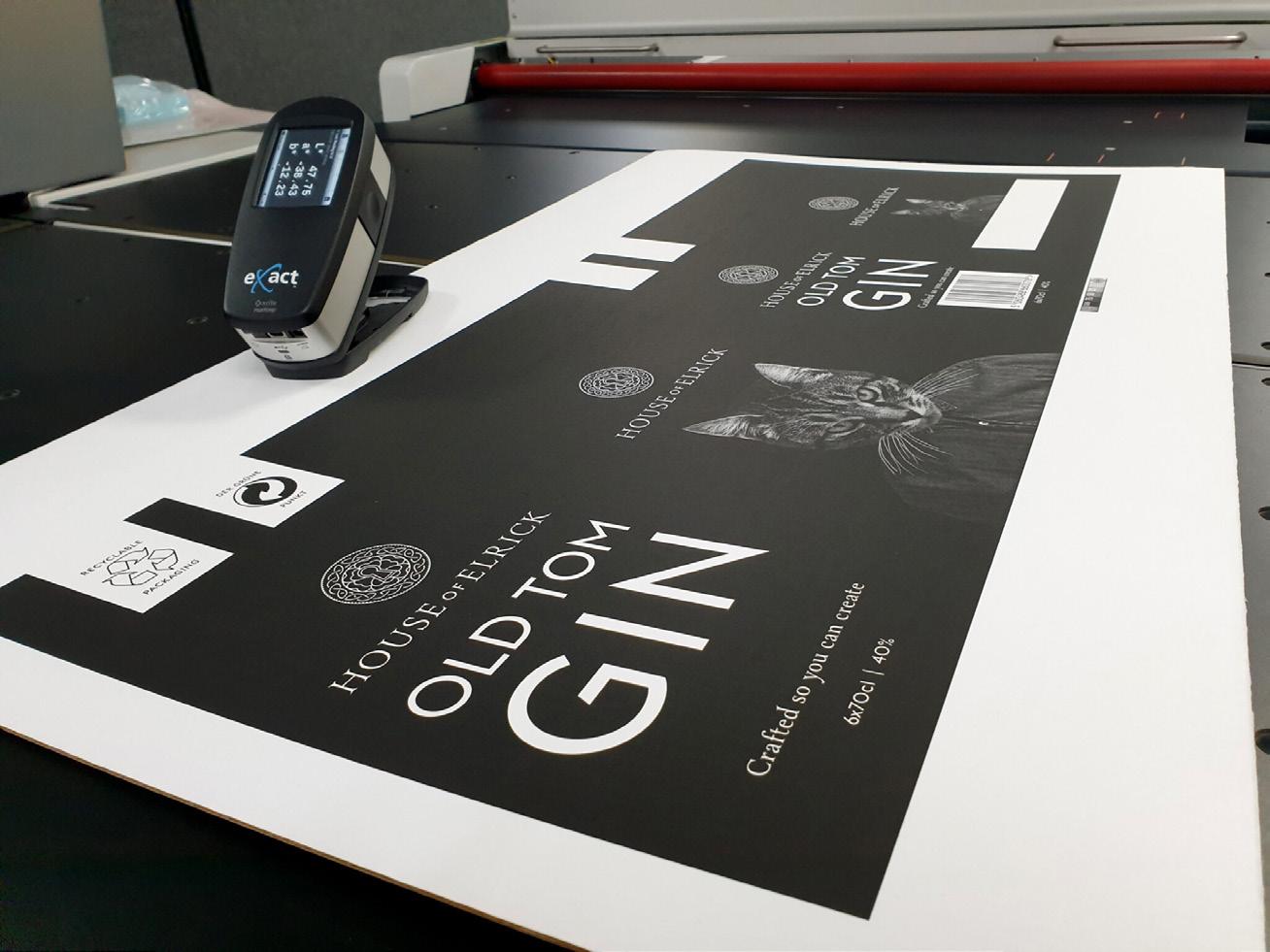
consider it was produced on a 20-yearold press using a single KODAK FLEXCEL NX plate, thus eliminating register issues and reducing cost, it becomes truly extraordinary.
Helping printers produce flexo packaging that combines such high quality and remarkable on-press efficiency is all in a day’s work for specialist flexo prepress business Victory Graphics, based in Portsmouth, UK. In the case of the cat image, the impressive print was produced by Newmarket-based Caps Cases, where print manager Wayne Booker, supported by Victory Graphics, is continuously driving print quality on such challenging jobs using FLEXCEL NX plates.
Diversification Victory’s website describes the company’s mission rather modestly: “Our aim is to help our clients grow by improving quality and reducing the cost of flexographic print”. Behind the strapline is an impressive story. It started in 2014, when the company entered the flexo prepress market, diversifying away from its previous concentration on coating plates (“a niche business”, in the words of owner and managing director Karl Pampus) and towards a broader base in packaging — flexible and corrugated — and labels.
Today coating plates account for around one-third of sales, says operations director Dean Darby, who adds that “offering a wider range of services helped us maintain growth even during the Covid-19 pandemic. Any fall-off in, say, label demand has been compensated by growth in corrugated.”
In 2016 Victory installed a KODAK FLEXCEL NX System, featuring a large-format 50” x 80” imaging unit capable of producing any size of plate. Looking back, Pampus credits the FLEXCEL NX System from Miraclon with setting the company on the path to the reputation it now enjoys in the corrugated market. “With FLEXCEL NX we can provide clients with a plate technology that’s far superior to anything else available — one that delivers not only consistently high quality, but also really significant production efficiencies and cost savings.”
1-to-1 reproduction for true print consistency Pampus goes on to describe the majority of Victory’s clients as “independent corrugated sheetfed plants that are striving for quality despite often having older, lower-specification presses. With FLEXCEL NX plates, the press can produce work that combines excellent coverage in solid areas with crisp reverse-outs and fine tones. In turn, this means we can reproduce both line and tone using just the one plate, instead of one plate for each. Essentially, we lift the quality these plants produce from standard to premium, giving them the ability to compete for work they previously thought was beyond their capabilities.”
The FLEXCEL NX System’s combination of flat-top dot technology and advanced plate surface patterning makes this possible. Flat-top dots deliver true print consistency through true 1-to-1 reproduction between the digital file and the physical plate structure, while KODAK DIGICAP NX Patterning enables surface structuring to be applied to all print areas on the plate, including very small dots, aiding precise metering of ink for each print element. The plate surface can therefore be tailored to specific print requirements and press specifications.
Pampus continues: “Avoiding pinholes and areas where there’s too much ink not only produces brighter colors with reduced ink usage, it also allows the press to run faster. The even spread of ink on the plate gives homogeneous coverage, while the lower pressure results in consistently good transfer. In addition, lower-volume aniloxes can be used with associated savings on ink.”
There are significant operational benefits for the printers, adds Dean Darby. “Customers regularly tell us how much faster they get to color, which reduces make-ready waste. And with FLEXCEL NX plates they don’t have to clean as frequently on long runs; we’ve had customers reduce cleaning by over 50%.

Conversions In common with many FLEXCEL NX plate users, Victory sees considerable scope to transition litholamination jobs to flexo post-print and gravure jobs to flexo. One such opportunity currently under discussion with a leading brewery — the outer case for a premium-label beer — could yield five-figure cost savings with a switch to flexo. Says Pampus:
“What helps us in these discussions is FLEXCEL NX’s consistent ability to match proofs and samples produced by the incumbent technology — that consistency in delivering print results makes the difference. Sure, with other plate technologies it’s possible to get good results by tweaking parameters on the press, but with FLEXCEL NX it’s the certainty of getting results so quickly that makes press passes a routine task — almost a non-event!”
Looking to the future for corrugated, Pampus expects the visual appearance of outer packaging to become even more important to brands, influenced in part by the acceleration in e-commerce in the wake of Covid-19 and the growing ‘unboxing’ phenomenon, whereby social media users share videos of product unpacking. “These developments will in turn put pressure on corrugated to achieve higher quality.”
He acknowledges that there are pressures on printers too — the perennial ones on prices and margin. “These trickle down to suppliers like us, of course, and our response is to become more efficient, more productive. We’ve invested just over £500,000 in the last year on measures to achieve this, including the recent installation of a new MIS.” Darby adds that last year the company also more than doubled the production area with the addition of a mezzanine floor — a sure sign of confidence in the future.
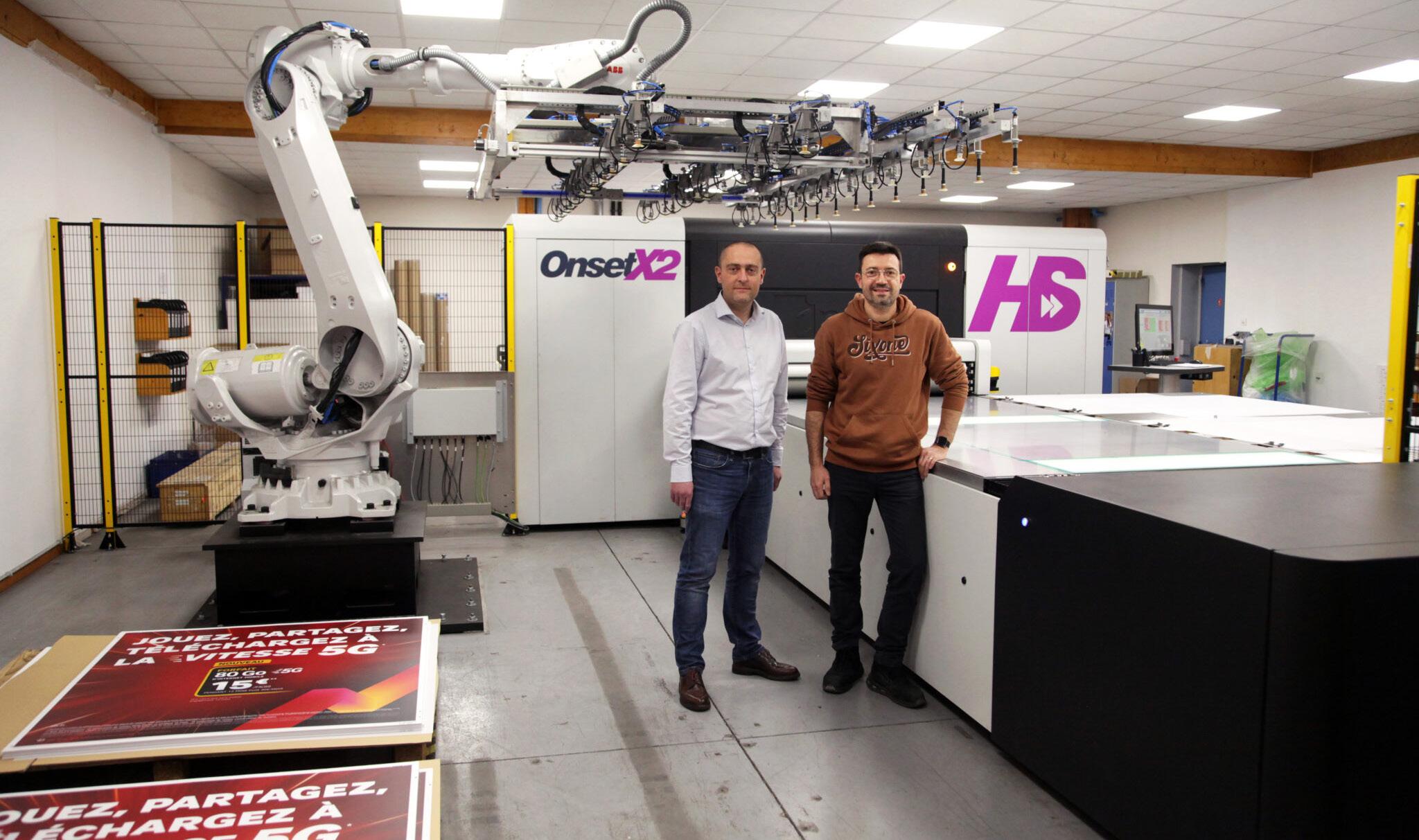
Victory is also responding by continuing to do what it has done so successfully to date: exploiting all the advanced features that set FLEXCEL NX plates apart from the competition, constantly seeking further improvement. Says Karl Pampus: “At the heart of the business are innovation and continuous improvement across our complete offering, all with the ultimate aim of giving printers the print quality improvement and cost reductions that will help them succeed as well.”
They are highly productive – the best on the market
Based in Saint-Denis-sur-Sarthon, Normandy, SDPS is a leading supplier of high quality wide format print to the French POP and POS market. The company installed its first Onset X2 in 2016 and followed that with a second installation the following year. Three years on, in the summer of 2020, they decided to take the opportunity to upgrade to the Onset X2 HS, which was launched by Fujifilm and Inca Digital in 2019.
“We were very happy with the two X2 machines,” says Richard Charrier, Technical Director at SDPS. “They are highly productive – the best on the market – but we saw an opportunity to boost our production speeds even further if we invested in an HS model.”
The Onset X2 HS was installed in August, with the accompanying robotic arm system having to follow later due to COVID restrictions. Neither Charrier, nor company CEO Regis Broussin have been disappointed. “Job set-up times are much faster now,” says Broussin. “We’re saving five to ten minutes in set-up time with every job, and with anywhere from two to ten jobs in a typical shift, that time saving quickly adds up.”
Nor is it just with the job set-up that time savings are being made. “The printing speed is faster as well,” Broussin adds. “The heads adjust more quickly and the loading and unloading is much smoother. All together we’re saving one-and-a-half to two hours of production time every shift. What that has meant is that we’ve moved from a pattern of three eight hour shifts per day to three seven hour shifts per day. We’ve also now been able to start closing the factory on Saturday mornings and giving everyone a welcome break. And we’ve been able to do all of that while maintaining the same levels of production as before.”
Charrier notes that the quality the Onset range is known for is still very much there. “The extra speed hasn’t affected the quality at all,” he comments. “It’s still every bit as good and our customers are delighted with it.”
Like all print businesses in Europe, SDPS faced significant challenges in 2020 as a result of the pandemic. “A lot of our usual work dropped off during the first lockdown in the spring,” says Broussin. “It picked up rapidly in July and August – we were much busier then than we normally would be – but overall it’s certainly been a very tough year.
“Looking ahead, the print production market is very competitive and I expect to see a bit of a price war next year among us and our competitors. Having an exceptionally reliable, high quality and high productivity machine like the Onset is certainly an advantage for us in that scenario.”
Jerome Delplanque, Commercial Director, Wide Format, Fujifilm Graphic Systems France says: “SDPS has been a valued customer of Fujifilm’s for a number of years now. Having been with them for so many new steps on their journey, we’re delighted to have been able to give their production yet another boost with our latest high speed Onset model. In what has been a very tough year for all of us, SDPS has performed admirably well and we’re proud to be working with them.”
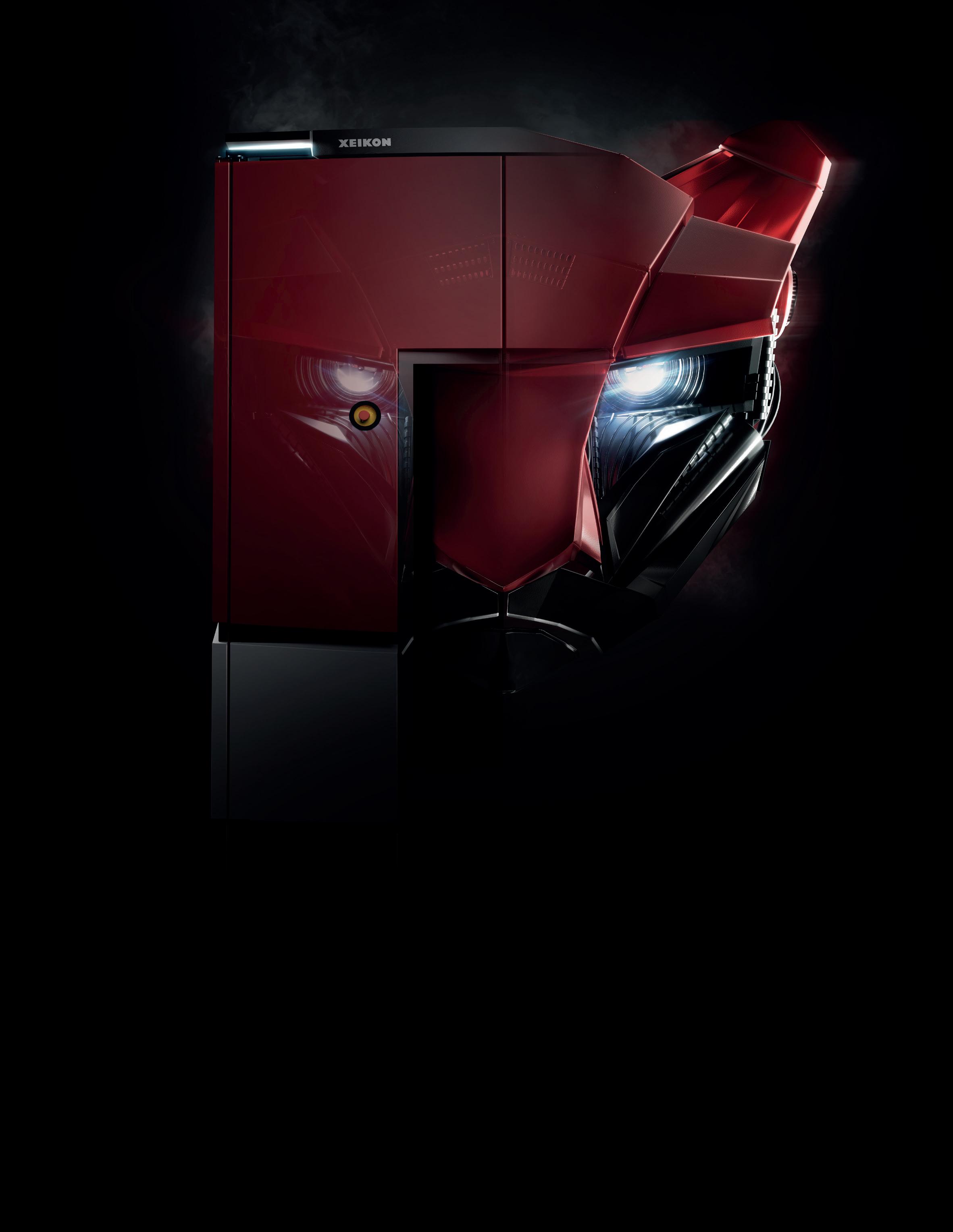