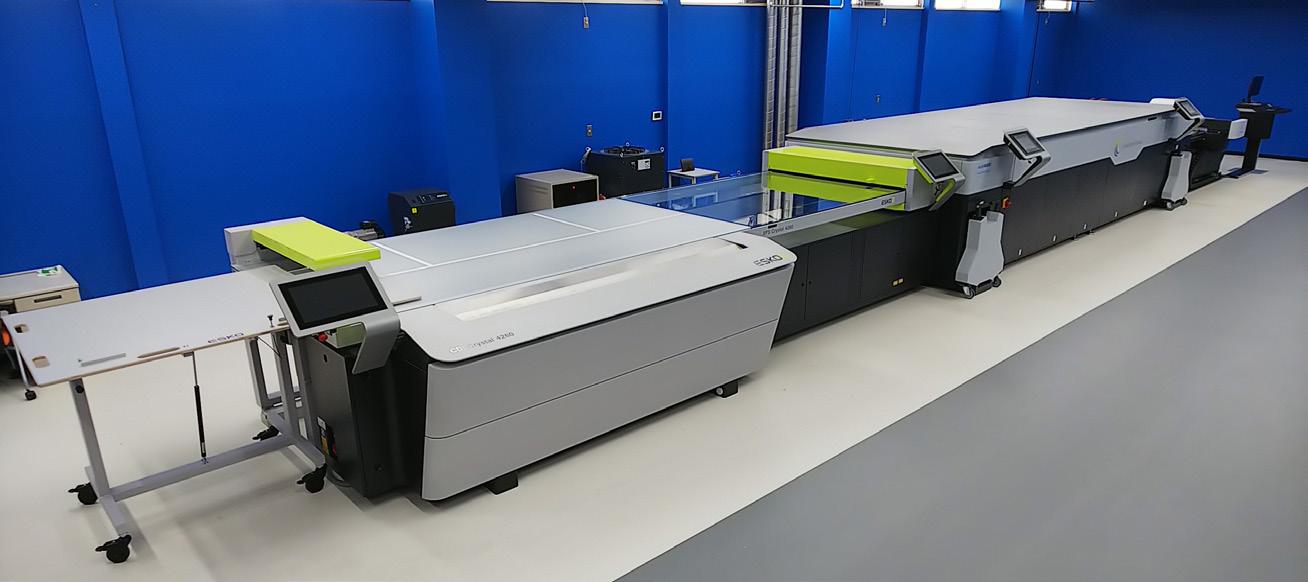
7 minute read
Indusrty news from the region & around the world
Japanese Company Seikodo Adds CrystalCleanConnect to Boost Productivity, Sustainability
Asahi Photoproducts, a pioneer in flexographic photopolymer plate development, today reported that Seikodo Corporation Co., Ltd. is the third company worldwide to install CrystalCleanConnect.
Seikodo Corporation was formed in 1959 and is expert in helping its trade customers create artwork suited for flexographic printing and preparing it for print to achieve the best possible printed quality.
“Prior to implementing CrystalCleanConnect, we were using solvent-wash plates,” explains Mr. Kaneko Osamu, Chief Procurement and Technology Officer. “We were looking for a better solution that would improve our sustainability, contribute to our goal of carbon neutrality, and improve our work environment. We were pleased to learn about CrystalCleanConnect, which met all of those requirements and more.”
Mr. Kaneko Osamu reports that in addition to its initial goals, with CrystalCleanConnect the company was able to transition from solvent-wash plates to Asahi’s AWP™ CleanPrint water-washable plates, while at the same time improving the overall quality of the plates it was producing, introducing improved production efficiency, and reducing both cost and waste. “Moreover,” he adds, “by introducing CrystalCleanConnect, a fully automated system, we are able to find a solution to the less skilled labor market and missing young talent in our industry. CrystalCleanConnect represents, due to its level of automation, an important solution to maintain high-quality platemaking output. All of this adds up to positioning flexography very competitively with offset and gravure for packaging printing.”
About CrystalCleanConnect
As the name implies, CrystalCleanConnect is a clean and sustainable process, an industry first, with no VOC-based washout solvents due to the use of Asahi’s AWPT™ CleanPrint water-washable plates, with never-before-seen levels of automation, generating a cut plate which is ready for mounting. CleanPrint technology ensures a significant OEE improvement, up to 40% in many cases.
And ink usage can be reduced by as much as 20% due to Crystal Screening technologies. Key to the CleanPrint technology is the fact that plates are designed to release ink, resulting in few, if any, press stops for plate cleaning, keeping a consistent print quality from beginning to end of the run. The close nesting of digital files enables precise plate cutting by the Kongsberg table and results in additional 10% plate waste reduction. It is the only automated flexo plate production like that incorporates cutting inline. The name CrystalCleanConnect derives from the ESKO Crystal and Asahi CleanPrint product branding with the philosophy of connecting the printing form making value chain from design to print as one integrated workflow, the first-in-industry platemaking solution that includes this level of automation in balance with the environment including imaging, exposure, washout, drying and post exposure, and plate cutting without the use of any volatile organic compound solvents in the process. .
EFI Announces Best in Ground (BIG) as New Distributor in Thailand for Display Graphics and Cubik Solutions
Electronics for Imaging, Inc. has named Best In Ground (BIG) as a new inkjet distribution partner in Thailand. The new partnership will focus on the distribution of EFITM printers for the signage and display graphics space, as well as EFI Cubik single-pass UV LED printers for the decoration of wood and other building materials. In addition to serving as an EFI distributor, the BIG staff will be trained to provide complete servicing for customers in the region, enhancing the existing EFI services infrastructure.
Headquartered in Nonthaburi Province, BIG is a graphics service provider dedicated to offering a high level of customer satisfaction with first-rate solutions and experience. The team provides local customers in the printing and packaging industry with profound expertise and technical aftersales services.
“We are thrilled about this opportunity to partner with EFI,” said BIG
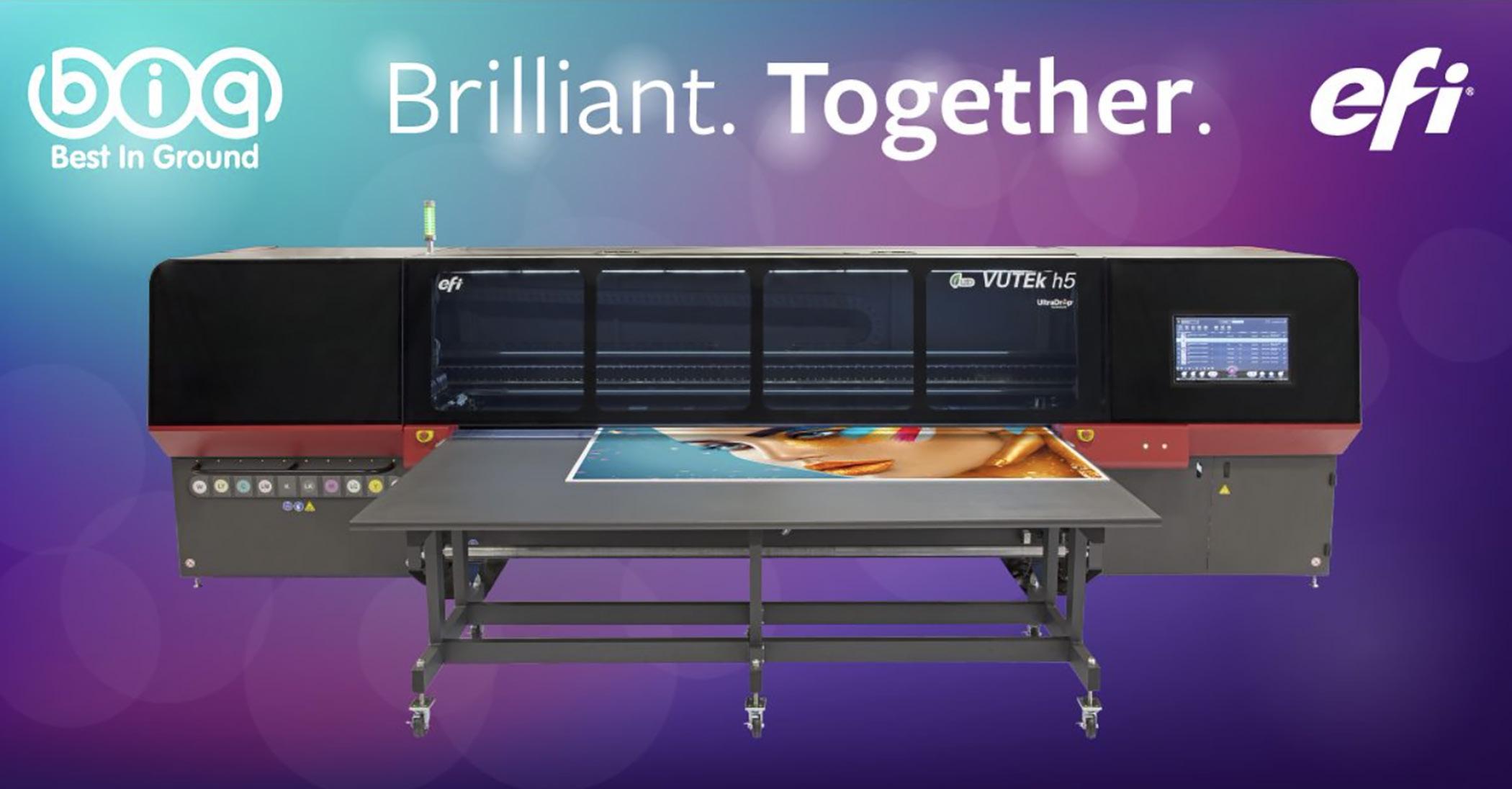
Managing Director Kornphob Panprasong. “The foundation of our business is to meet and exceed our customers’ expectations and to support them in the growth of their businesses. Efficiency and speed in addressing market demands are our customers’ biggest needs, and we are confident that EFI solutions will empower them to thrive in the face of these challenges.”
“The legacy that BIG has built in the Thailand market will help EFI to extend our customer reach even further to customers in the Asia Pacific region,” said EFI Inkjet Regional VP of Sales Rodd Harrison. “We are excited to be partnering with BIG to grow our presence in this rising market.” around them and provides the information. Based on this structure, individual complete solutions can be realized for every need.
Previous Process Today, the procurement of secondary packaging materials is mostly carried out analogue: a manufacturer of pharmaceutical products plans sales and the resources and capacities needed for production at the beginning of a business year.
However, the packaging supplier is not involved in this planning from the very beginning, but only when the manufacturer places a concrete order. Of course, the supplier can not react and manufacture the ordered packaging until an order has been received.
Pharma Packaging of Tomorrow: Why Digital Supply Chains are Necessary Digital supply chains are on the rise – for good reason. The advantages are obvious: better overview, fast delivery through predictability and easier quality assurance. The pharmaceutical industry and packaging manufacturers would also benefit from this and thus make their cooperation more efficient.
The printing and packaging sector is also involved in the growing pharmaceutical industry: Due to the increasing demand for drugs and healthcare products and the pressure to bring new developments to market quickly, it is also important that packaging can be produced flexibly and in a timely manner. The solution to this might lie in a digital supply chain.
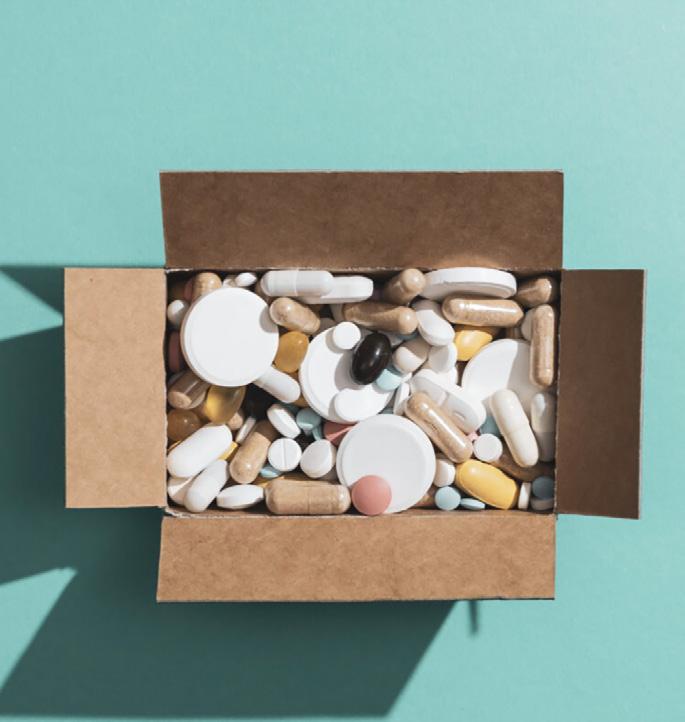
Structure of a Pharmaceutical Packaging We encounter packaging in many areas of our lives – including when we have to take medication. They protect the contents and convey important and legally required information to doctors, pharmacists and patients. Labels and package inserts also contribute to the necessary information of the purchaser. Here, too, a distinction is made between primary and secondary packaging. The primary packaging is, for example, cans or blisters that protect the medication. The secondary packaging (usually made of cardboard)is wrapped In order to do this, he in turn has to calculate raw materials and capacities, which is becoming an increasing challenge due to the ever shorter lead times in the pharmaceutical industry. These two supply chains run completely independently of each other. An exchange only takes place at the moment of order transmission and when the ordered goods are delivered.
Advantage of Digital Supply Chains To counteract this, digital supply chains offer many advantages: by analyzing the shared data in advance, future requirements can be better predicted and thus served more quickly. Detailed information opens up new opportunities for customized products. The transparent exchange between companies, suppliers and customers makes the entire value creation process more accurate and reliable. Accordingly, a digital supply chain promotes sustainability and cost savings. In addition, quality assurance is also easier to design. In addition, automated processes also reduce analogue efforts.
Faller Packaging provides a detailed white paper on the topic of digital supply chains (German only) here.
“Digitization of the value chain is no longer a dream of the future, but already offers the pharmaceutical industry very concrete added value today.” Nils Höpker, Head of Logistic and Demand Management Operations EU, Faller Packaging Building Digital Supply Chains
Essential to digital supply chains are cloud-based platforms for data exchange and analysis. This is because, unlike the linear supply chain, it is a multidimensional network that extends far beyond site and country boundaries. This is made possible by the end-to-end networking of all people, machines, processes and goods involved via the Internet of Things, by automation and, above all, by the comprehensive collection and analysis of all data generated in the supply chain.
Collecting, sharing and analyzing information makes it possible to digitize individual work steps, implement new technologies and concepts, and thereby generate significant benefits for both pharmaceutical companies and their suppliers.
Relevant information includes: Forecast data - Historical order data - Order change data - Batch records - Inventory quantities - Actual line requirements
The best way to exchange data between companies is via interfaces between the respective Enterprise Resource Planning (ERP) systems. These can be defined and created individually for each company and each system. In most cases, SAP is used as the ERP system. This speeds up the flow of information and at the same time makes it more comprehensive, secure and transparent.
