
5 minute read
Sustainable Packaging Innovations in Asia
When it comes to addressing the plastic pollution issue in packaging, paper and bioplastics are two materials that often gets discussed. We scope out some of the latest sustainable packaging materials to have come out of Asia’s world of packaging in recent times.
Toppan develops paper-based tube-pouch
Advertisement
Paper-based material for body of easy to squeeze tube-shaped pouch further reduces plastic volume.
Toppan Printing (Toppan), has developed the paper tube-pouch, a new paper-based version of the existing tube-pouch, which is shaped like a tube and easy to squeeze like a pouch. The paper tube-pouch is ideal for use in the food, toiletry, and pharmaceutical sectors, and full-scale sales are scheduled to be launched in Japan in fiscal 2020.
Due to the use of thinner film material, the conventional tube-pouch is easier to squeeze and uses 30% less plastic than the type of laminated tube widely used for toothpaste. The new paper tube-pouch maintains the tube-pouch’s functionality while demonstrating even better environmental performance by employing a paper-based material for the body, making possible a 50% reduction in plastic volume according to Toppan. Coupled with a redesign of the plastic parts of the head section, this enables plastic to be reduced by a total of 65%. Although plastic has been replaced with paper, the tube-pouch still maintains its shape even when the volume of content inside decreases, and the use of Toppan’s proprietary GL BARRIER film on the inner surface ensures the world-class and complete barrier performance required for such items as food and cosmetics.
Pinyapel – the sustainable pineapple paper from the Philippines
Made from discarded pineapple leaves, Pinyapel is food-safe, naturally waterresistant and 100% biodegradable, making it a viable packaging option. Developed by the Design Center of the Philippines, Pinyapel is a specialty paper that is processed and manufactured from the locally sourced pineapple leaves. The Philippines is the second largest pineapple producer in the world, and Pinyapel is made from the discarded leaves of its plants.
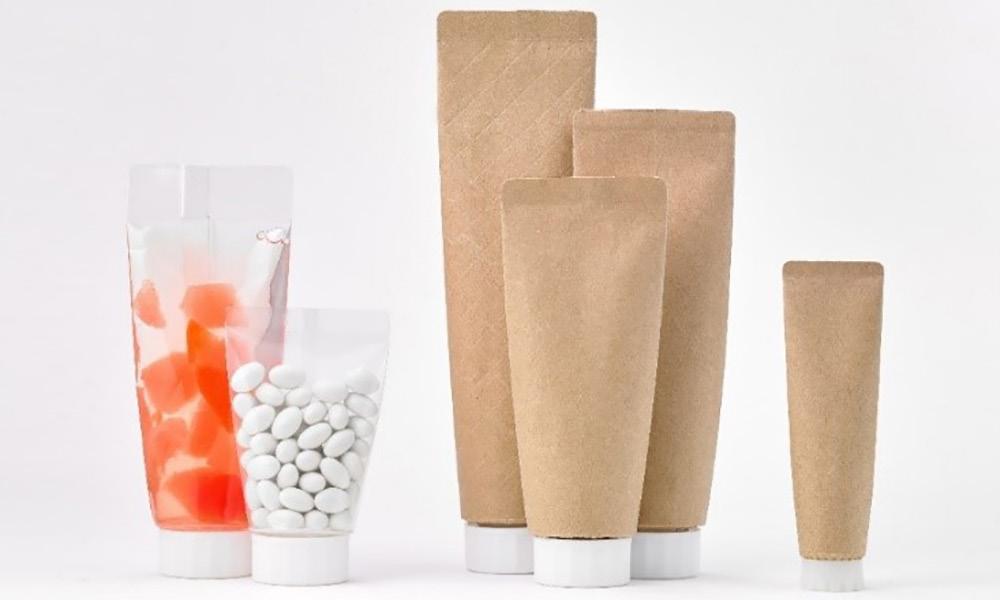
Pinyapel is reinforced and print-ready for packaging applications.
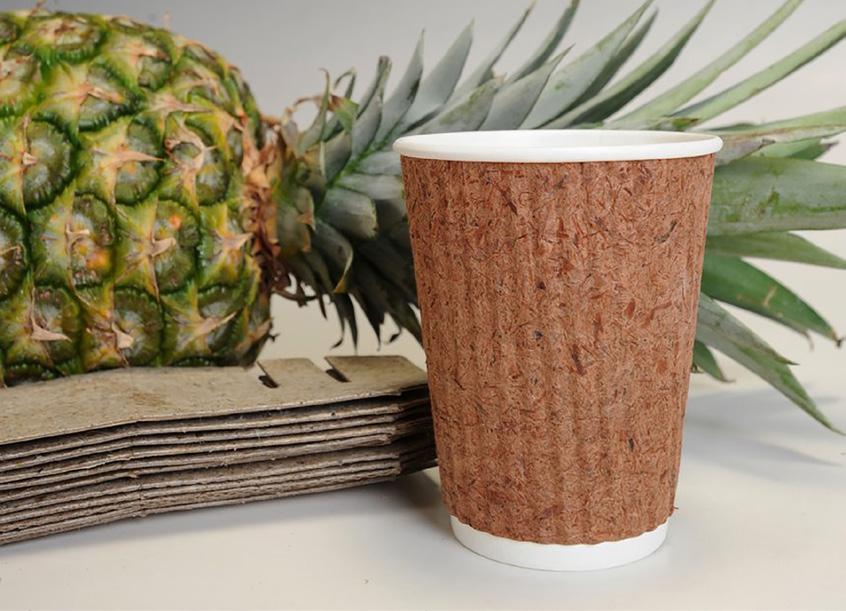
The specialty paper can be used to make a number of products from paper shopping bags to coffee cups, most of which in the market are lined with plastic to make them water resistant. Pinyapel requires no extra plastic film layer, as pineapple leaves are naturally water-resistant. Pinyapel-made packaging can be in direct contact with food, making them a feasible alternative for food packaging.
Pinyapel is 100% biodegradable. It can also decompose faster than other paper products. According to tests by the Design Center of the Philippines, Pinyapel reached about 55% mass loss in four weeks, much higher than the 21% mass loss in commercial paper bags. The innovation won the 2019 Wood Pencil award by the UK-based charity D&AD Future Impact for sustainability. It is also the Philippines’ first award for the category.
Seaweed is the new Plastic Based in Jakarta, Indonesian company Evoware uses seaweed as an alternative material to plastic. Their seaweed
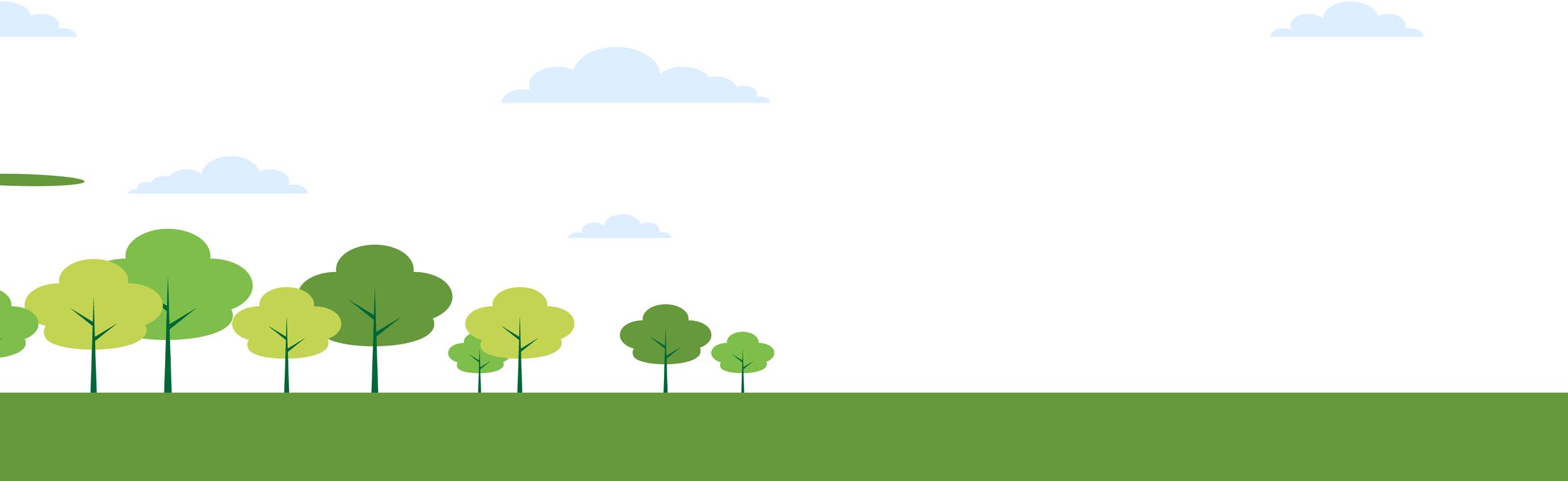
Sustainable Packaging Innovations in Asia
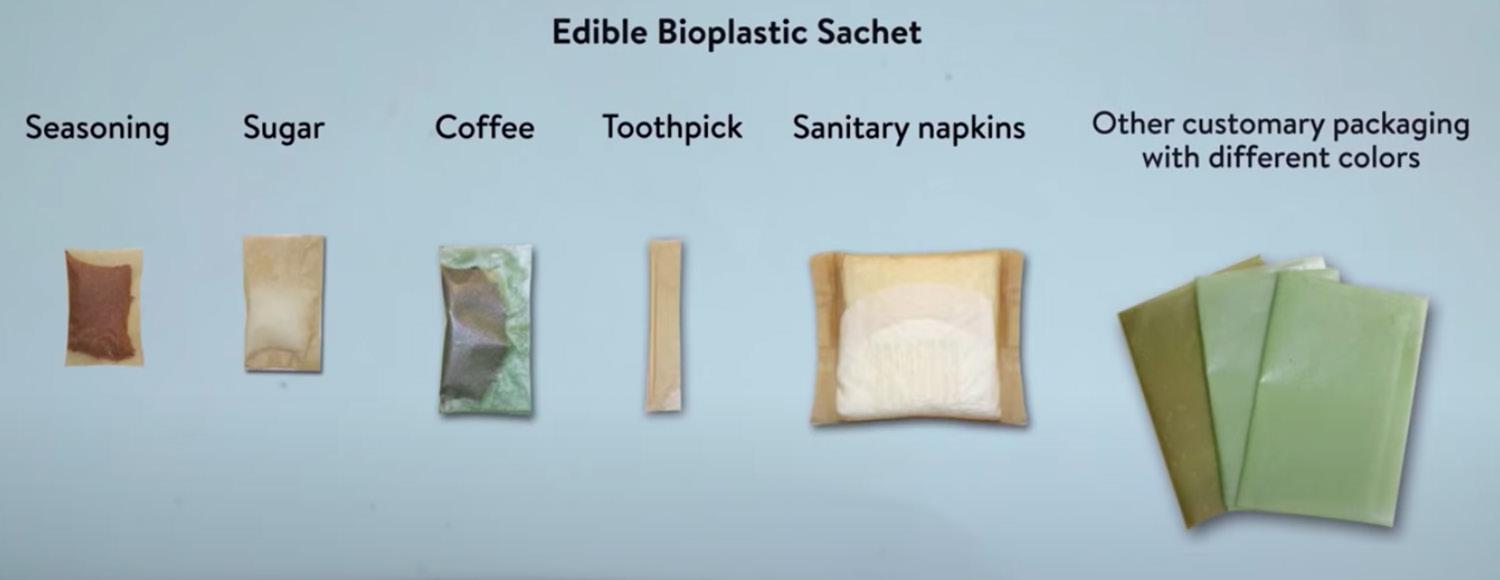
based packaging is biodegradable and chemical-free. It can be dissolved in warm water, and has a two-year shelf life without preservatives.
The company first launched Elle Jello, edible seaweed cups that come in a variety of colours and flavours. Evoware also produces edible food wrapping such as burger wrappers and single-use sachets, typically used for instant coffee or food condiments.
Indonesia is the second biggest source of ocean plastic waste. With the use of seaweed, the company hopes to help the country cut down on plastic use, as well as providing income to local seaweed farmers.
ndonesia produces some 10 million tonnes of seaweed each year, and targets 19 million tonnes by 2020. Seaweed do not take up land space and does not pose a risk to deforestation. Seaweed is also free from chemicals as it does not require fertilizers.
No thorny issue: durian-based packaging
Malaysian researchers developed biodegradable packaging from durian skin.
A research team from Malaysia has created biodegradable food packaging made from the skin of the durian fruit. skin fibres of the durian with epoxidized palm oil, transforming it into a biodegradable polymer that can be moulded into food packaging containers.
The team found that after three months of being buried in soil, about 83% of the packaging has degraded. In comparison, consumer plastic packaging reportedly take hundreds of years to degrade.
The polymer is also found to be antimicrobial. The material can also be used as filament for 3D printing.
Alibaba-funded Green Packaging Ecoinno is a Hong Kong-based green material company focused on providing alternatives to single-use plastics. It recently announced the closing of a US$6 million funding from Alibaba. The company plans to use the funds to begin industrial-scale production of its proprietary Green Composite Material (GCM) and to strengthen its material research and engineering platform to help meet pressing consumer packaging needs.
Ecoinno has developed a patented Green Composite Material (GCM) and related processes, based 100% purely on natural plant fibres, an abundant, renewable, and naturally occurring polymer on earth. By repositioning nature's plant fibres, GCM harnesses the natural attributes of plant fibres. Notably it is 100% biodegradable in the natural environment within 75 days and has extreme temperature tolerance (allowing freezing and oven reheating).

GCM is also three times stronger than plastic and bioplastic in tensile strength. It is impermeable to oxygen, with an extremely low transmission rate, on par with even metal. The material is water and oil-resistance, and most importantly, has passed FDA tests to be toxic free.
With its breakthrough GCM technology, Ecoinno aims to provide the global consumer and industry with an attractive and viable 'Third Option' that is a break-out from the traditional choice between petroleum-derived plastic and bio-plastic (consisting of mostly non-naturally occurring polymers) in a significant step towards creating a sustainable, circular economy.
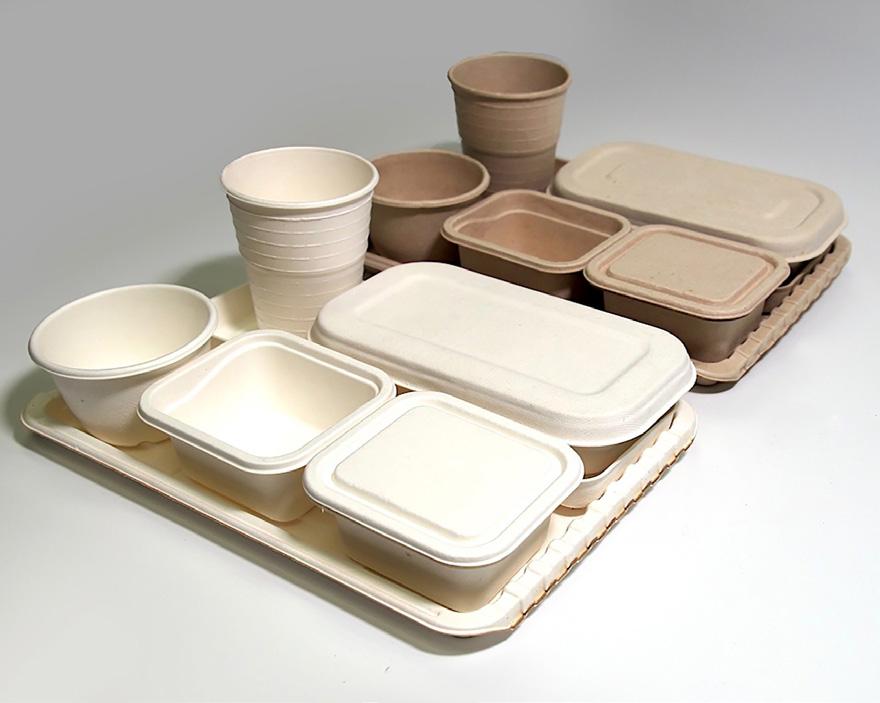