
12 minute read
DKSH Paves the Way to Packaging Sustainability
With strong industry-leading partners, DKSH is set to be the integrated solutions provider in Asia for companies moving towards sustainable packaging.
Advertisement
DKSH Group is a Swiss company with a global footprint focusing on market expansion services. The group has a wide ranging service portfolio across business units in healthcare, consumer goods, performance materials and technology. DKSH has deep roots in Asia Pacific, having been in the region for 150 years.
In 2019, DKSH established the Business Line, Packaging, Printing and Converting (PPC). The branch now has presence in nine markets in Asia, with key focuses on food and beverage, health, beauty and personal care, and pharmaceutical industries. The company’s main applications are flexible packaging, flexography, rotogravure, laminates and coextruded film.
The packaging market has matured over the years and the Asian packaging industry was projected to exceed USD 26 billion at the end of 2021. Consumer preferences for sustainable packaging continue to grow globally, and this trend is even more prevalent in Asia Pacific.
“The flexible packaging market in Asia has matured over the years and now needs sustainable solutions, given the fact that there is a high focus on banning single-use plastics. This is an area where DKSH Business Line Packaging, Printing and Converting will focus on and align the service and support around it,” said Sulhas Kulkarni, General Manager, Business Developement, DKSH Asia Pacific.
“With the increased focus on eliminating single-use plastic bags, there is also increasing demand for sustainable solutions from the industry,” said Kulkarni. “At DKSH, we want to become the sustainable solution provider that our customers can count on to receive the right support for their business success.” In 2020, DKSH made sustainability one of its key values. In becoming a sustainable partner for its customers, DKSH PPC is focusing on three key areas:
- Providing high quality products and innovative solutions from leading brands to customers in Asia Pacific. - Providing excellent after-sales service from its dedicated teams with deep technical expertise in the printing industry. - Being a reliable trustworthy partner through its 150 years of continuous presence in Asia and track record of financial stability.
An increase in demand for sustainable solutions is not the only key growth factor for packaging in Asia. Other trends that will factor into the growth include increasing demand for food and pharma packaging, manufacturers switching from gravure to flexo technology, as well as a higher demand of print quality.
“Asian customers do not want to sacrifice quality at all when looking for printing solutions. The leading flexo technology offers manufacturers print stability, excellent quality, and registered accuracy in small batches that are on par with the traditional gravure processing method for large columns of printing,” Kulkarni explained.
SOMA – the leader in sustainable flexo technologies
To aid their customers towards sustainability, DKSH specifically partners with companies that aligns with its green values. One of its partners that aligns with its sustainability vision is SOMA, a producer of flexographic printing presses, slitter rewinders, laminators, plate mounters and diecutters. Doing especially well in Asia
Pacific is the SOMA Optima 2, a second generation flexographic printing press. The SOMA Optima 2 dramatically enhances print quality, make-ready times, and running costs – qualities that all contribute to reducing ecological impact. The main focus is to implement sustainable technologies, such as a water-based ink system and technologies to reduce make ready in terms of time & waste.
“This is the second generation of a machine that is already very successful, so customers can be confident that they will receive an exceptional, proven flexo press,” explained Jan Verner, the chief designer of the original Optima 2. “The powerful features that defined our first generation Optima 2 remain: quick job changes for short runs, exceptional print stability for long runs—as well as excellent machine serviceability. In addition, the user will certainly appreciate that the nextgeneration machine can perform many activities automatically and will do so by switching jobs in the most efficient way.”
The new press is focused on increasing efficiency and producing cost-effective print runs with reduced VOCs and material waste through automated job settings. The Intelligent Job Tuning is one of the new functions in the Optima 2 which enables the automatic tuning during job setup. It has specially designed algorithms that can minimise the bouncing effect for each particular design.
“It takes into consideration the dynamic effects of each job—the bridge, the sleeve, the tape and the design itself. This lets each specific piece of artwork achieve its ideal drive setting on the press. It’s quite a revolutionary technology that can bring control of printing press stability to new, exceptional levels of precision,” said Verner.
Designed for short runs, the SOMA Optima 2 is equipped with a newly developed S-Mount automatic plate, which makes plate mounting faster than a manual process. Since it is precisely defined, it can eliminate incorrect plate mounting, reducing press downtime later, during makereadies. Part of this intelligence comes from the system, where plate topography and register are measured, providing the foundation for automatic registration and impressions settings on press. Due to that system, the register and impression on the press is set without operator involvement in a fully automatic mode, with minimal material waste.
The CARTRIDGE system offers printers a means of reducing ink costs on printing jobs where expensive spot colours, special effects, and metallic formulations are required. These high pigment inks are expensive consumables. Reducing ink volumes and residual waste lets printers maintain profit margins while meeting end user price demands.
The built-in ‘Advanced Bounce Control’ system features cutting-edge technology that reduces bouncing at high press speeds to optimize print quality when using HD plates. Bounce reduction results in a sturdier press, and limits the wear of other parts—saving customers even more money in the long run.
The presses can also be supervised remotely, so managers can proactively discover issues before they cause economic problems. Past job history of time and waste can help change future estimates if they have been previously inaccurate.
Web path limitations of a traditional CI press design is removed, because the unwind and rewind systems are located outside of the printing unit modules. This variable design allows the option of choosing any unwind/rewind configuration and in-line upstream or downstream printing and converting units.
One small but outstanding feature is the cooling of the cylinder housings at the motor side, similar to the cooling of the central impression drum. This prevents any temperature-caused expansion, thus preventing dot gain. Another clever feature was developed for the inter-deck dryers. It allows them to swing open by 90 degrees, similar to a door. This makes it easier for cleaning, and provides effortless access to the substrate and CI drum.
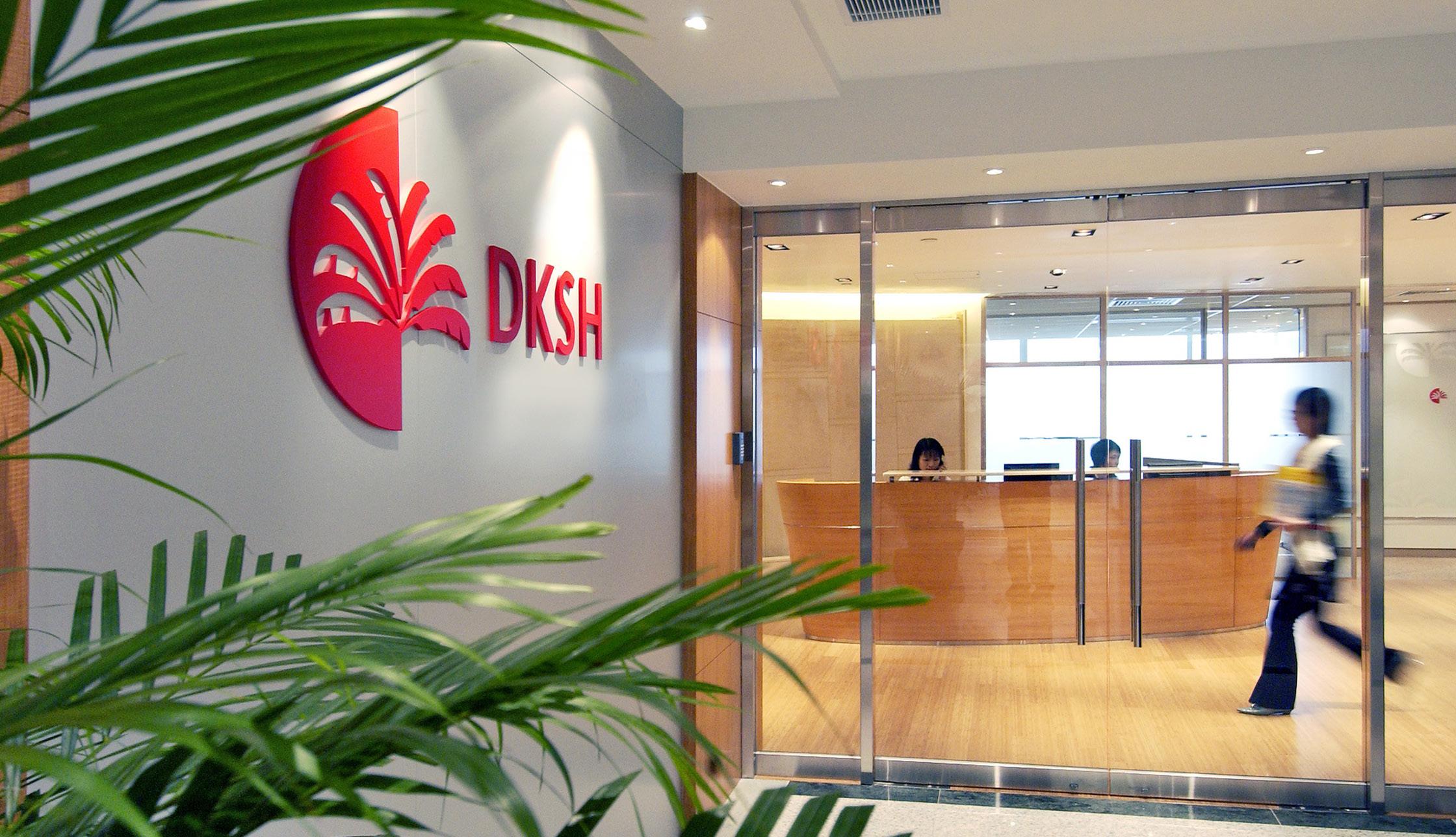
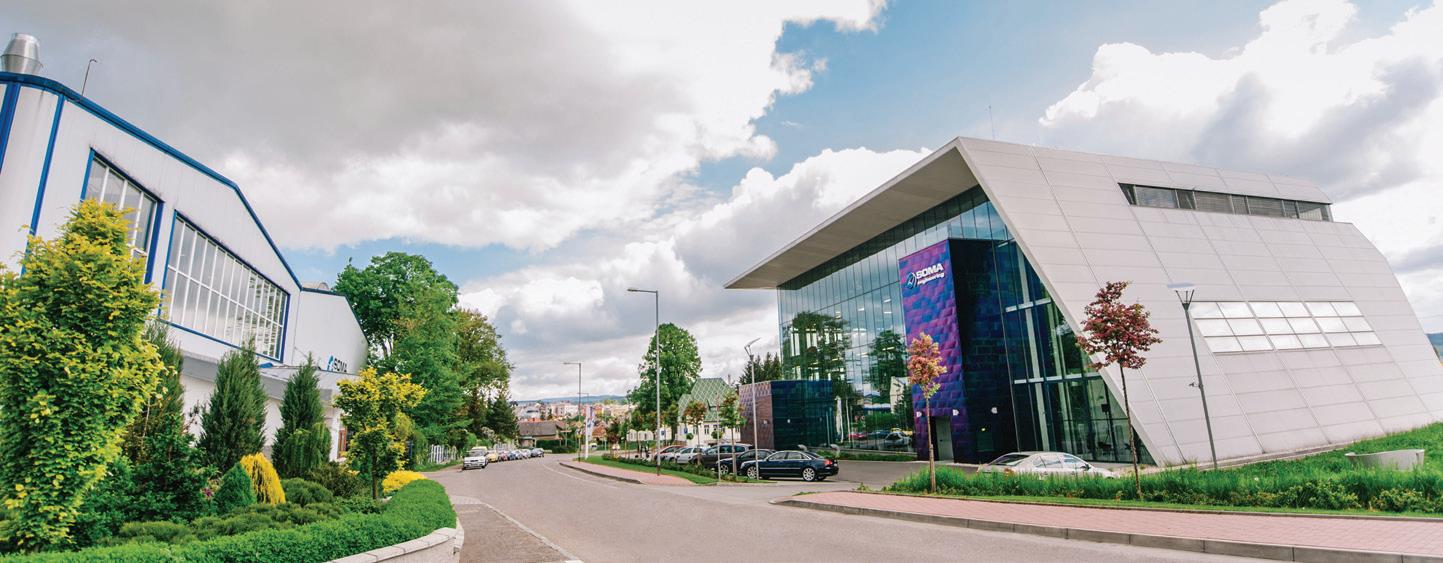
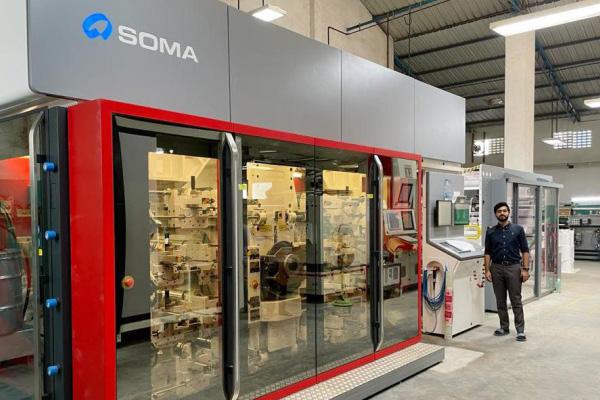
contributes to exceptional quality flexo printing, improved communications, and primarily helps to deliver quick and easy change-overs between jobs, while minimizing operator error. DKSH is the exclusive distributor in Asia for the Optima 2, as well as SOMA’s range of advanced solutions for flexible packaging production.
Sandon Global – on the forefront of sustainability in Anilox
In 2020, DKSH inked an agreement with Sandon Global to promote solutions for anilox and coating rollers in key regions of Asia. Headquartered in the United Kingdom, Sandon Global is committed to minimising environmental impact with its solutions.
“Even the smallest change in the manufacturing process, materials or logistics can collectively contribute to the drive for operating a sustainable business, quite literally. As an anilox manufacturer our accountability varies from material changes such as the imminent introduction of recyclable packaging and shipping containers to more complex process and equipment investments,” said Global Marketing Manager Stephen Lloyd.
Anilox manufacturers typically produce both chromium oxide and aluminium oxide waste materials as a by-product of the coating process. Sandon Global have a closed loop system in place that takes this waste and re-melts it to produce fused materials for application in other industries.
Furthermore, their unique Enhanced Densification Treatment (EDT) has been developed to provide a preventative barrier to substrate corrosion and oxidisation. It is applied prior to laser engraving making the chromium oxide ‘ceramic’ coating totally impervious to any liquid or chemical ingress.
As a result, EDT delivers a more efficient and consistent ink evacuation from the engraved cells leading to a more consistent ink film thickness. In short what this means for printers is both a reduction in cell “plugging” of dried ink and therefore less time required to deep clean their anilox inventory. Ultimately contributing to printer’s sustainability and environmental objectives as set out in a variety of government policies around the world.
“We spend significant time on R&D which benefits our customers in the long run. One of our points of differentiation is durability, printers need to rely on their anilox inventory to perform consistently at high speed. Our laboratory team constantly conduct tab samples testing the porosity levels within a tolerance of 1%, that the minimum hardness value of 1350 Vickers is achieved, and the bond strength of our coatings are robust,” Lloyd continued.
“Why does this matter in the context of reducing operational impact on the environment? The integrity and performance of an anilox roll or sleeve is vital to reducing downtime and the impact that has on energy usage and waste materials or consumables such as inks,” said Lloyd.
It is reported that several other initiatives under the sustainability banner have been introduced. Such as a Hydrogen-Argon–Nitrogen mix coating system which replaces the need for Helium, a mined gas which is the only element on the planet that is a completely non-renewable resource so needs to be used sparingly.
Sandon Global have also developed lightweight narrow-web anilox rolls using recyclable aluminium and steel bases, which delivers health and safety benefits for the operators. New engraving formats have been designed to reduce ink usage through improved release and transfer characteristics.
Not only have Sandon Global walked the walk in terms of sustainable product development but their brand new facility has been designed using BREEAM (Building Research Establishment Environmental Assessment Method) the world’s leading sustainability assessment method. The purpose built factory has been assessed for environmental, social and economic sustainability performance. This means BREEAM rated developments are more sustainable environments that enhance the well-being of the people who live and work in them. The impressive building includes a solar panel roof and multiple energy saving technologies which is due to complete for the end of the year.
The Integrated Solutions Provider in Asia
In addition, DKSH has strong partnerships with other industry leading solution providers such as TEG Technologies, sei Laser and Koenig &
SOMA Optima 2 in operation
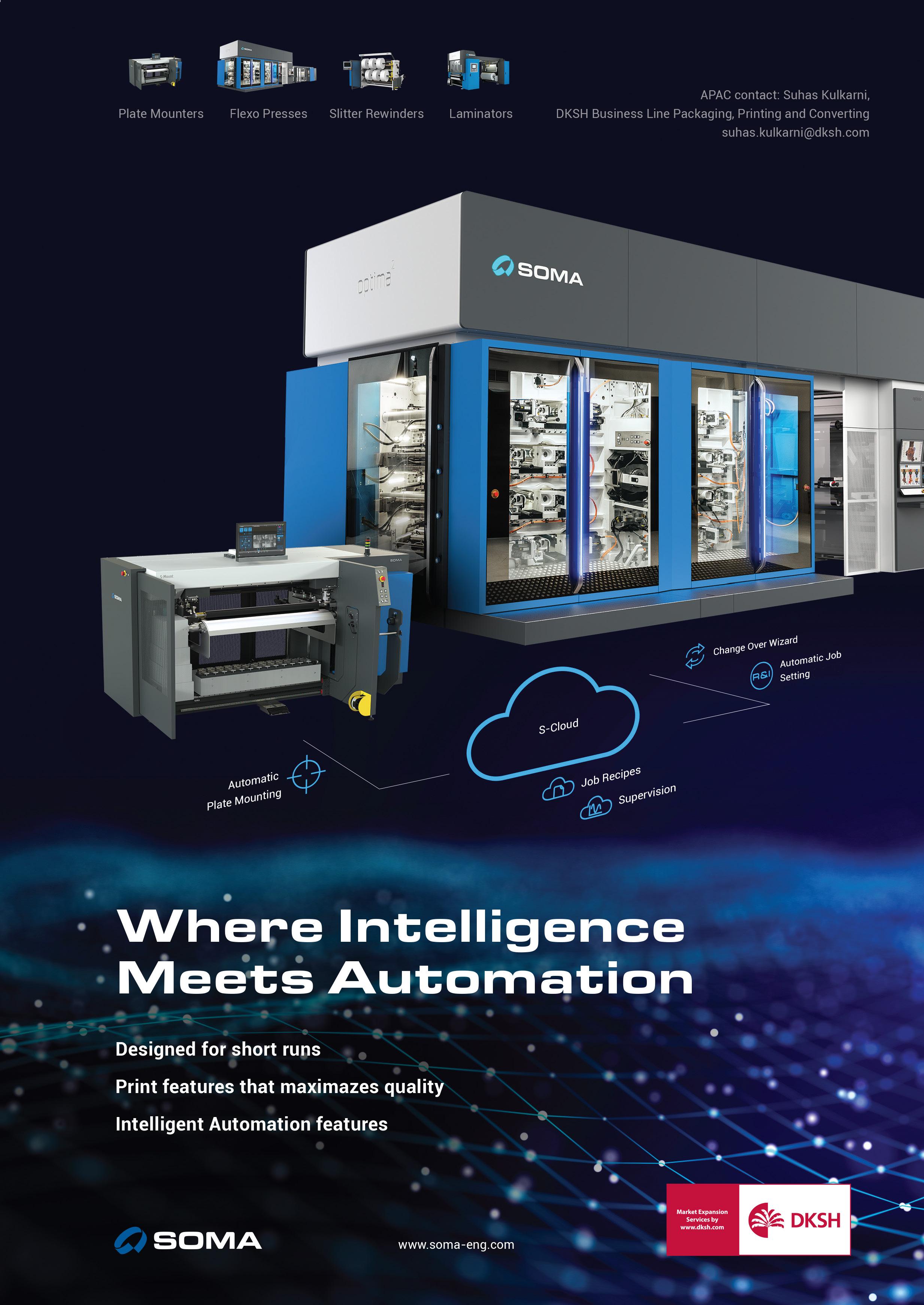
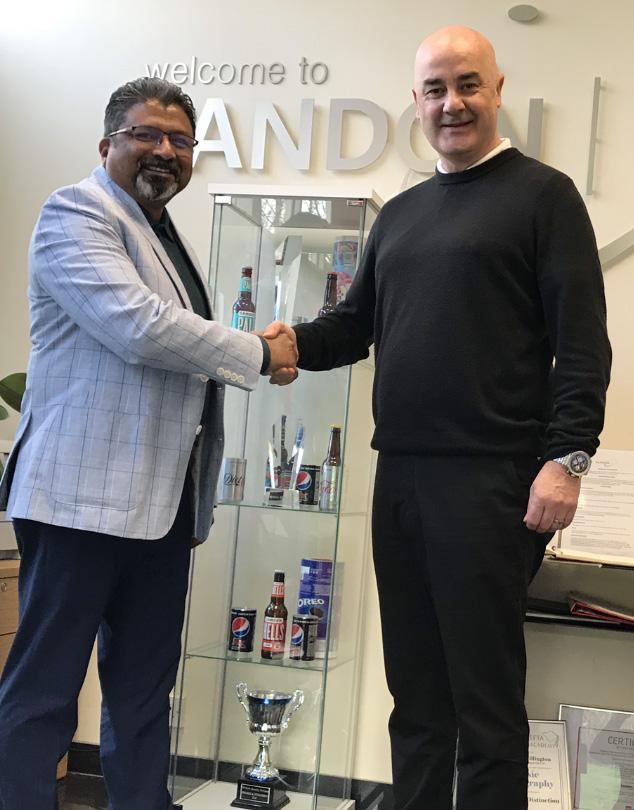
Sulhas Kulkarni, General Manager, Business Developement, DKSH Asia Pacific and Stuart Mitchell, Sales Director at SANDON Global
Bauer Coding.
“We would like to become a Turnkey Solution Provider that offers a consultative approach for flexographic printing. Led by our professional team, DKSH will provide step by step guidance to our customers from engagement, analysis, execution, handover, education to optimization,” Kulkarni emphasized.
Adopting a consultative approach for flexographic printing will benefit Asian customers such as ‘greenfield sites’, which would need a 360-printing solution from scratch.
“This will be beneficial to customers who are currently using gravure but would like to cross over to flexo through professional services. Customers who are already using flexo could also benefit from our service & knowledge to improve productivity, efficiency, and sustainability,” Kulkarni added.
Customers can also expect digital print solutions coming up in DKSH’s product offerings: “We would like to continue expanding our portfolio of leading technologies to the Asian customers. We are now looking to expand into digital print solutions, blown film extrusion lines as well as consumables such as mounting tapes and photopolymer plates,” said Kulkarni.
The first key geographical markets that DKSH will be focusing on are India, Indonesia, Thailand, Japan, South Korea, Malaysia and the Philippines.
“We believe that growth opportunities will continue to differ by market. At DKSH, we will customize the approach for market expansion based on our market intelligence,” said Kulkarni.
Kulkarni asserted on the importance of DKSH being a long term and trusted partner with a strong collaborative mindset: “We understand Asian customers build their trust around a partner who knows the specific needs of their business and is empathetic and respectful of their expectations. They also appreciate a partner with total honesty and is transparent with them on implementation planning.”
“Asian markets are transforming from being product-centric to a servicedriven focus. Along with this shift, the Asian customers also have higher expectations from service providers including support for equipment,” Kulkarni continued.
This service-provider stance became more crucial than ever in current pandemic times. During the pandemic, DKSH digitised its support system to its customers by leveraging omnichannel approaches. One of the ways was to collaborate with its business partners and provide online webinars to share new technologies and solutions in different local languages.
“In 2020, we see that many countries have struggled to maintain previous levels of growth particularly due to lockdowns. For example, flexible packaging demand growth was at 5.5%, down from 7.4% in 2019. We also see that food packaging continues to be the main flexible packaging application in the region, totalling 21% of overall demand. And yes, there are delayed investments, but we still see high engagement of our customers in the markets especially through webinars in learning leading technologies and solutions for their future growth,” said Kulkarni.
“Despite the challenging environment, we have been keeping our employees safe, serving our customers and clients in the markets to continue growing their business. We are facing the same challenges as everyone. However, leveraging our strong structure and local set up, we are able to continue providing services and support to our customers,” said Kulkarni.
Due to the strong set up, DKSH was able to complete a recent installation of a SOMA 880 Optima CI Flexo press, at the main plant of Multiflex Polybags (P) Ltd. in Chennai, India during the pandemic.
“At DKSH, we are dedicated to providing a comprehensive omnichannel solution and deliver the best service experience to customers; embedding a service culture and mindset of our employees; obtaining and maintaining top-notch service expertise. We believe excellence in customer satisfaction is the only way to sustainable business growth,” Kulkarni concluded.
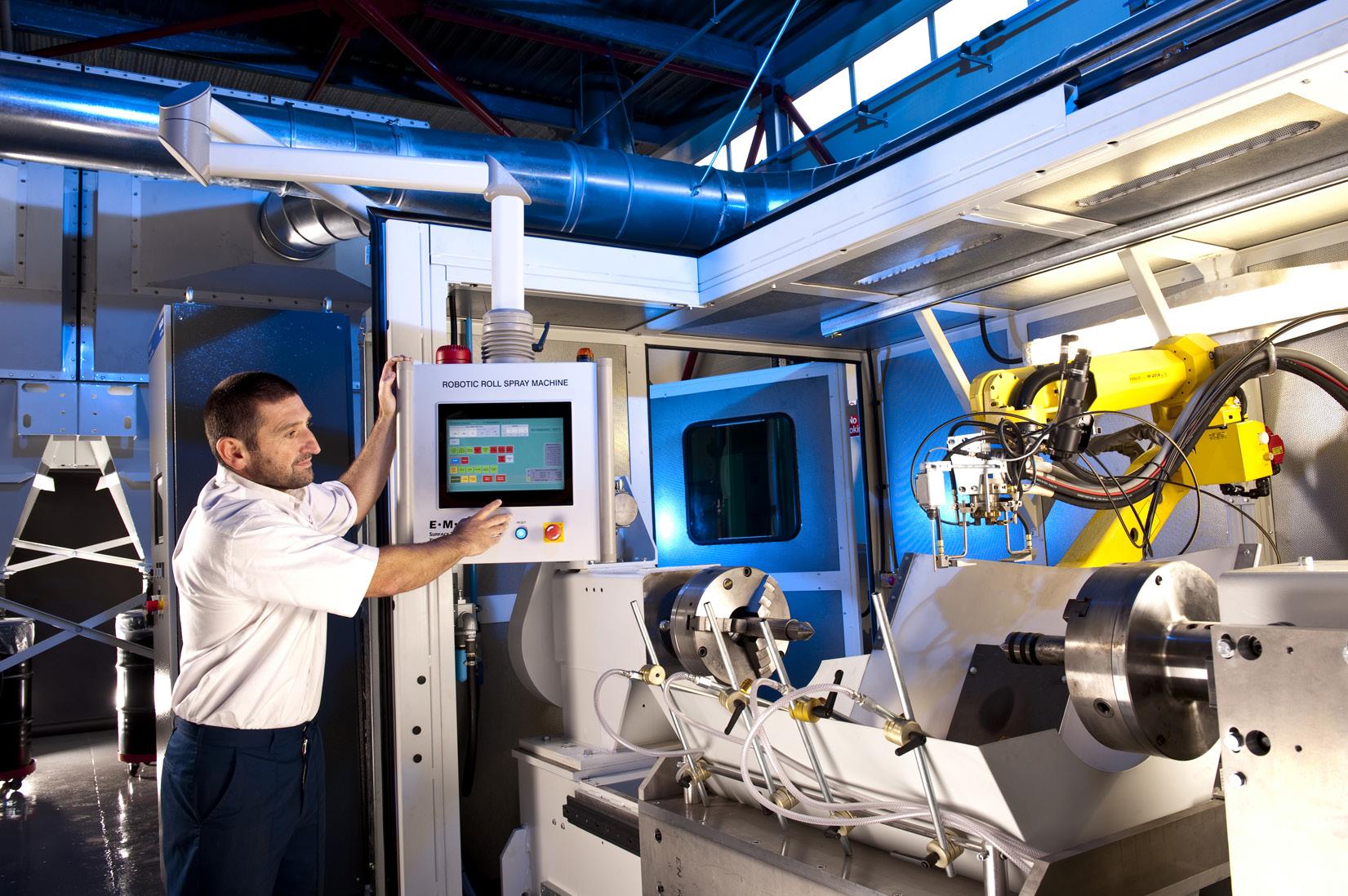
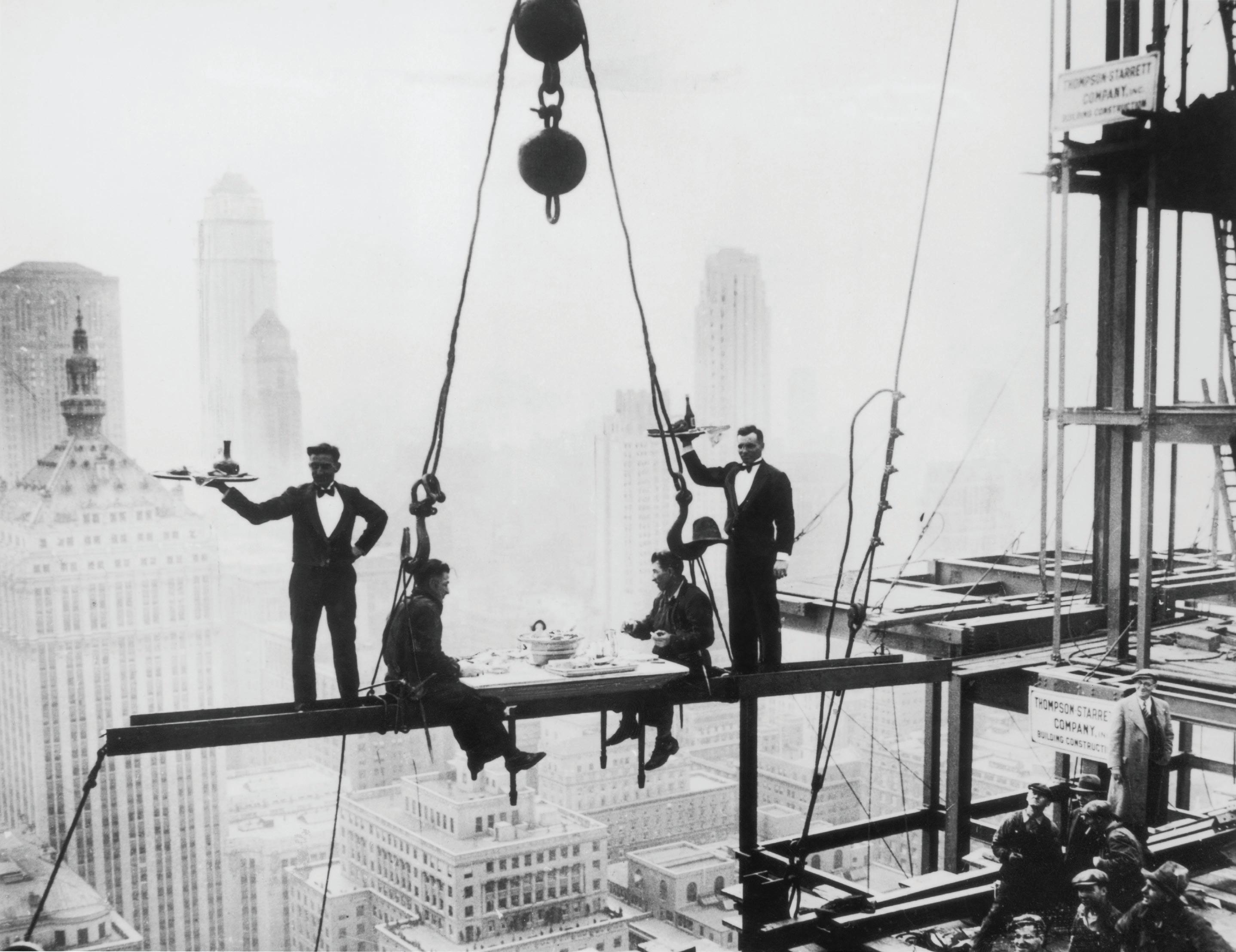
Email: suhas.kulkarni@dksh.com