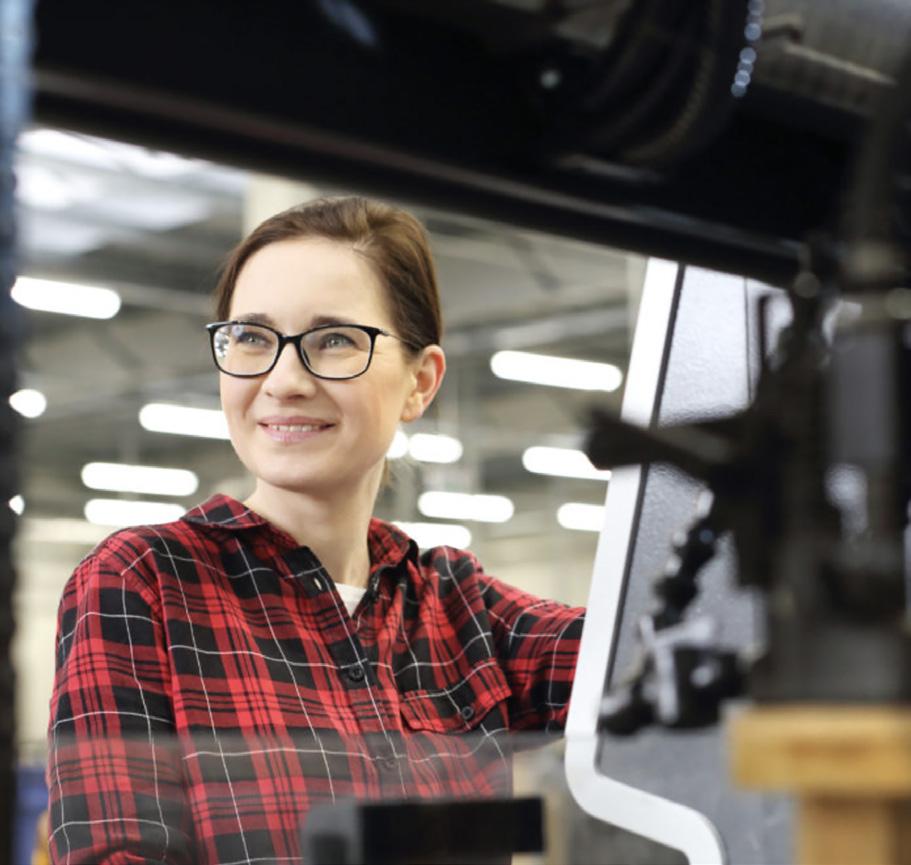
12 minute read
Print vs. Digital - How digital really is the printing industry?
Print and digital solutions: At first this sounds like a contradiction in terms. However, the printing industry has known for a long time that it can only go hand in hand. Anyone who processes data needs a digital infrastructure to offer solutions quickly and efficiently.
1 productivity and collaboration
Advertisement
2 security & compliance
3 analytics & intelligence
4 flexibility, efficiency and sustainability
5 mobility
The easiest way to start is probably to increase productivity by starting to automate processes that make it easier for us. This frees up staff to spend more time on value-adding activities and also on further concept development. Once the start is in place, it also makes it easier for them to collaborate and achieve higher quality results.
In contrast, only 10 per cent have completed automation in accounting. Likewise, 50 per cent of the companies use production data acquisition to identify problems at an early stage.
Decisions are made on a digital basis
A cornerstone of digitalisation is knowledge. Knowledge that is drawn from data. Around 75 per cent of the printing industry already uses this knowledge to make decisions.
Status quo of digitalisation
Already at the last Drupa 2016, digital solutions were presented that make everyday work easier and satisfy customer needs in an automated way. In 2024, digital transformation is even a key topic of the trade fair.
When we asked industry participants on Facebook about digital progress, the most common answers were "we are at the very beginning" and "we don't know where to start yet". This also corresponds perfectly to the studies of the German market. Germany is still to be seen in the midfield of progress. In a survey by the Allensbach Institute for Public Opinion Research, companies from the DACH region in the packaging industry were questioned. 80 percent even completely reject the introduction of artificial intelligence in the work area of transport routes and chains.
Digital transformation in the printing industry - where do you start?
The following areas in particular are considered for digitisation:
A study by Apenberg & Partner clearly shows that this first step has not yet been taken everywhere. Only 6 per cent of the respondents from the German printing industry stated that they had automated their administration as far as possible. Almost half of all respondents are still in the process.
On the other hand, 60 per cent of our colleagues have already completed the preparations by purchasing software and have already put it into operation. Only two percent still check and process data manually, and just under a quarter are still partially involved.
The printing industry focuses on production before administration
During the survey it was clear that the printing industry places its main focus on productive processes. More than half of the participants already map production processes (such as production, makeready and downtimes) in their operating system. Production planning is also automated. Whereby only 6 per cent state that the automation potential in pre-press has been exhausted.
The theory of Print 4.0 - the digitalisation of the printing industry, has one goal: the process from the customer's order to the delivery of the product runs completely digitally and autonomously. The manufacturing and delivery processes are digitally linked and automated. Seamless processes between paper supplier and printer, prepress, printer and material transport: stocks are filled by sensory observations. Human intervention is no longer necessary.
Our industry has already produced many best practice examples from which we can learn. In reality, many industry players have dared to start and have already automated individual workflows. Printing machines behave autonomously. The Corona crisis has once again increased the willingness to digitise. Many companies are switching to digital offerings. Digital providers are entering the market, forcing other entrepreneurs into digitalisation in order to maintain competitiveness.
Now it is time to use this beginning as a competitive advantage and take the next step.
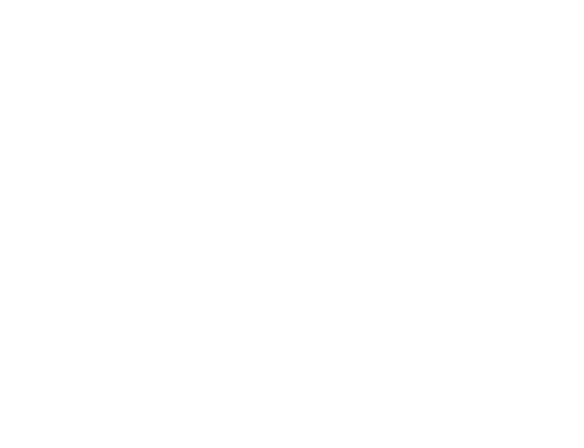
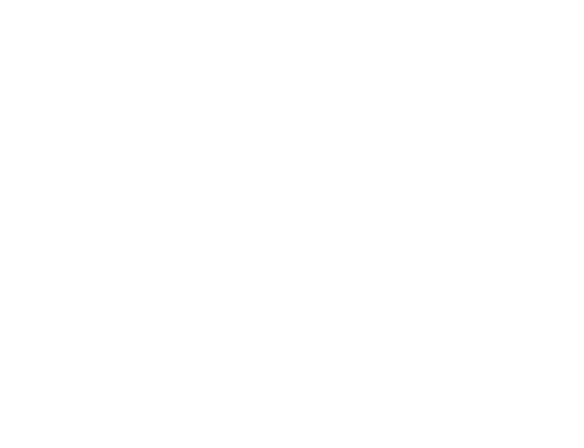
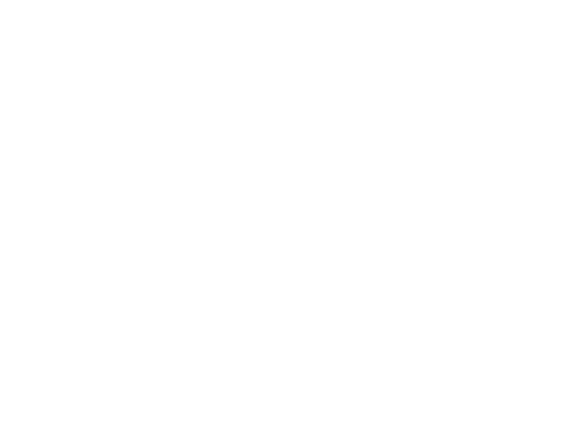
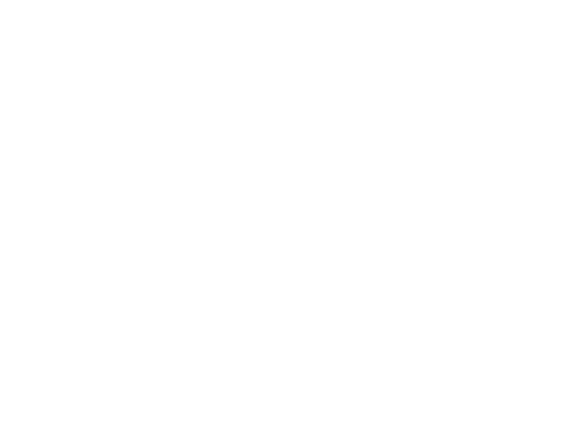

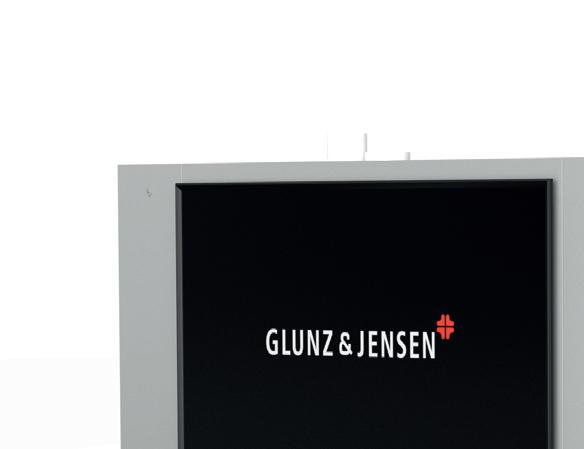
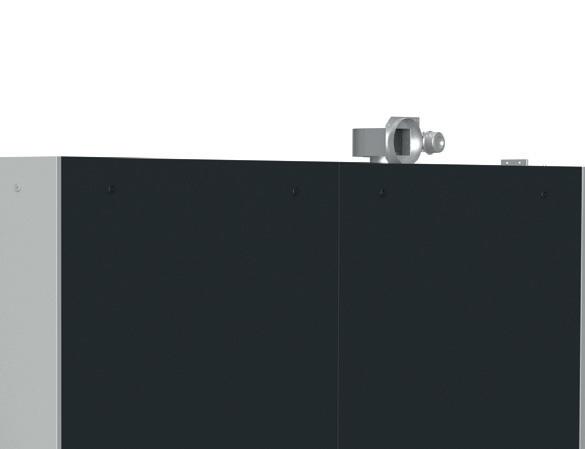
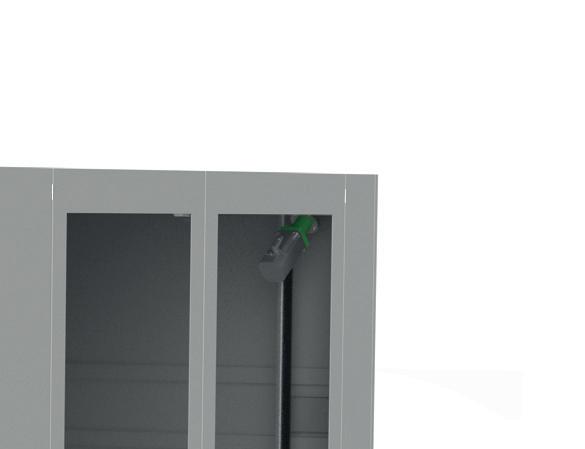
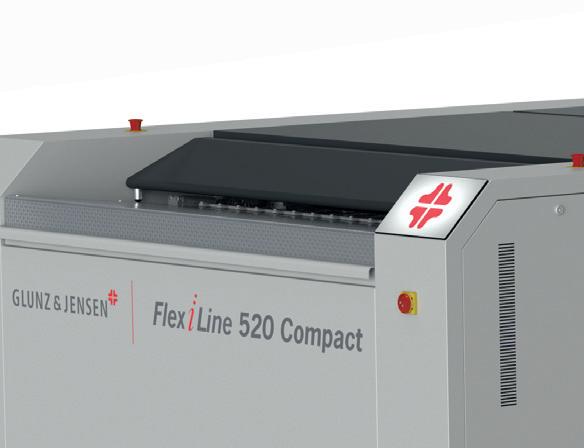

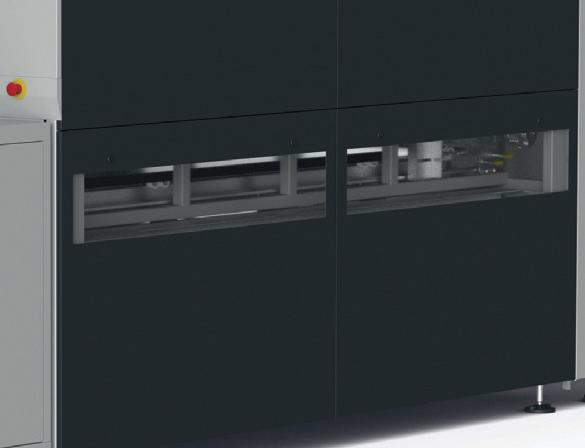
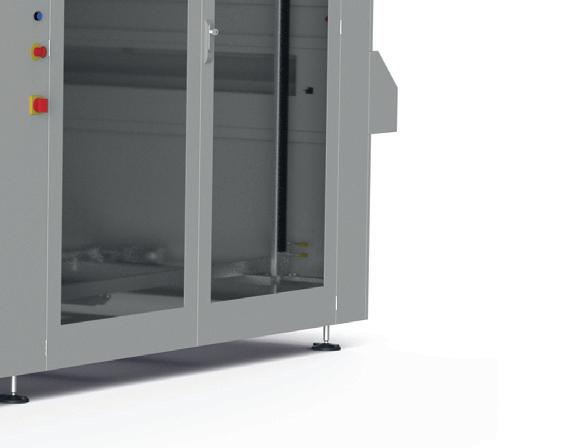
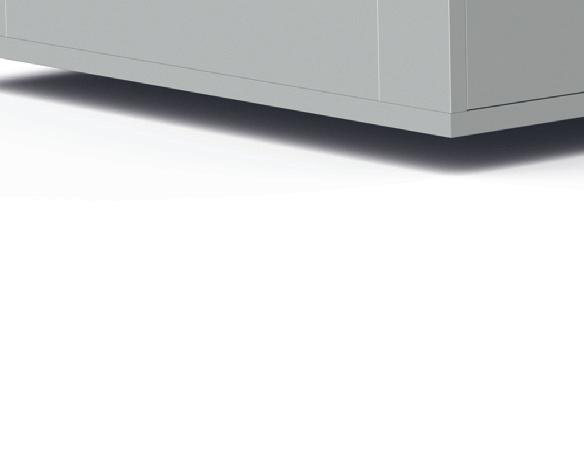
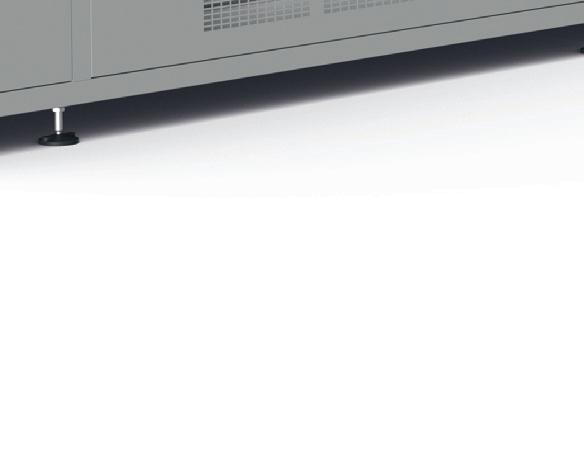
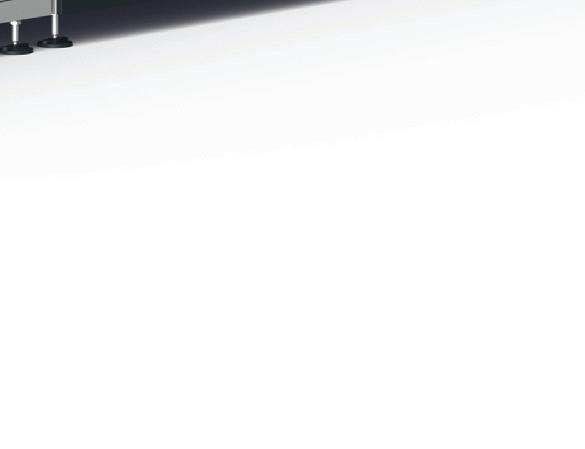

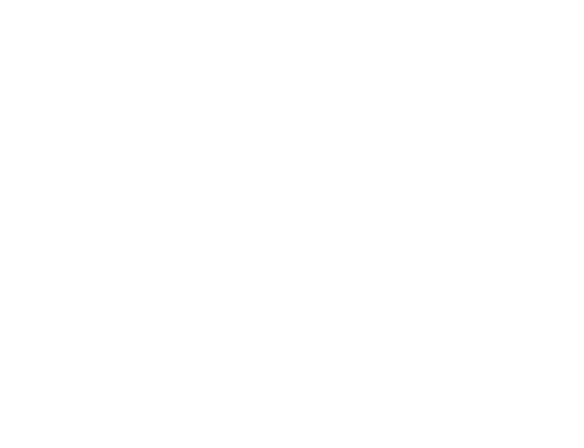
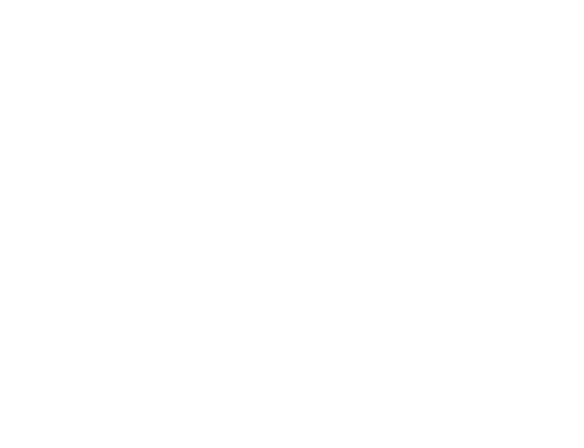
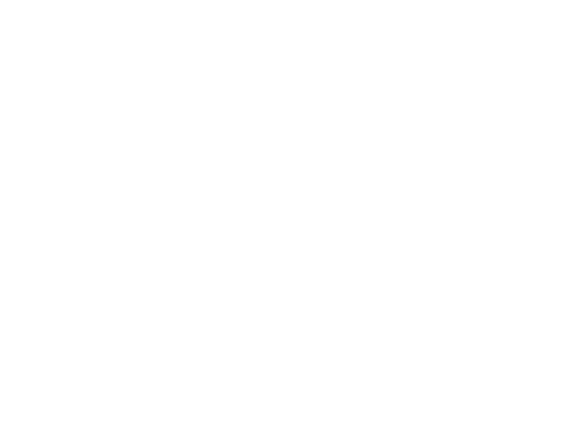
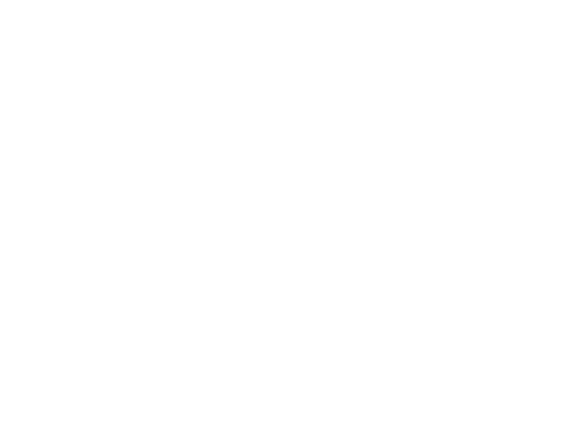
Swiss leading-edge technology in the Far East
High-performance mailroom for South Korea's most modern newspaper printing plant
The South Korean Hankyung Media Group, publisher of the business newspaper "The Korea Economic Daily," is investing in a complete new newspaper printing plant. The longestablished media company wants to ensure not only top quality but also the highest possible production speed and process automation. For the equipment of the mailroom, the company has therefore opted for cutting-edge Swiss technology from Ferag.
At the new production site in the Bupyeong National Industrial Complex in Incheon, west of the capital Seoul, a state-of-the-art printing plant is currently being built on a plot of land measuring around 3,700 square meters. As early as September 2022, the Hankyung Media Group had ordered from Manroland Goss Web Systems the printing presses, which will form the core of the newly built printing plant.
The scope of supply of the Augsburgbased machine manufacturer has now been expanded to include the mailroom technology. The Hankyung Media Group has opted for a solution from Ferag (Hinwil/Switzerland). "The Swiss cutting-edge technology ideally complements our COLORMAN e:line presses," says Hyun Seung-Yoon, Executive Director at Hankyung Media Group. The South Korean company is also convinced that the partnership between Manroland Goss and Ferag is a guarantee for the success of the project.
Clear commitment to printed products
According to Seung-Yoon, the aim is to offer the best print quality of all Korean newspapers for the company's 60th anniversary in 2024. The director said this directly after signing the contract with Manroland Goss Websystems in September 2022.
"In this context, the production system also offers many attractive advantages for contract printing orders from the Korean newspaper market." The goal of becoming the largest newspaper contract printing company in Korea in the next few years is understood as a clear commitment to the future of printed daily newspapers in South Korea.
The Manroland Goss printing systems allow a total production volume of 190,000 copies per hour. This corresponds to the production of up to one million newspapers per night. Thanks to the high level of automation, it is possible to achieve the stated goal of profitability with reduced unit costs for both long runs and shorter contract print runs. Highly automated production with maximum availability
To ensure that this performance can also be realized in the mailroom, the presses are equipped with four Ferag UTR conveyor chains for up to 100,000 copies per hour each. These convey the newspaper copies to the bundling lines with four Ferag MTS3 MultiStack high-performance compensating stackers.
The Hankyung Media Group deliberately opted for cutting-edge technology from the Swiss company, which already has excellent references worldwide as well as in South Korea itself. "The selected high-performance mailroom guarantees an optimal workflow through the Ferag Navigator software as well as highly automated production with the highest availability and maximum service life," adds Hyun Seung-Yoon.
Since the bundling lines are located one building level higher than the loading ramps, Ferag also supplies a PKT plate chain conveyor with a spiral to connect floors. By means of this, it is possible for the newspapers bundles to reliably overcome the height difference and be allocated to the loading ramps according to the cover sheet data.

The plate chain conveyor system is based on a chain, supported by lowfriction rollers. Due to the low rolling friction, very long conveying distances can be achieved with only a few drives and without any transfers. The Ferag mailroom equipment is scheduled for delivery to South Korea in early 2024 to enable Hankyung Media Group to have the project operational in time for the company's anniversary.
Introducing UVbiz's Cutting-Edge BOBST M6 Label Press
UVbiz, the packaging division of major food company, MB Industries, has proudly announced the successful installation of one of the first BOBST M6 label presses in India.
The BOBST M6 is a cutting-edge label press that represents the pinnacle of technological innovation in the packaging industry. As a leading manufacturer of printing and packaging equipment, BOBST designed the M6 press to provide
SPEED UP YOUR PROCESSES with optical systems for UV curing and drying

exceptional flexibility and versatility. It enables high-quality printing of labels, shrink-sleeves, flexible packaging, and offers advanced automation features for rapid production and efficient workflow as well as enhanced decorative options. In addition, its oneECG feature for Extended Colour Gamut printing guarantees less ink and substrate consumption, and more time-saving operations.
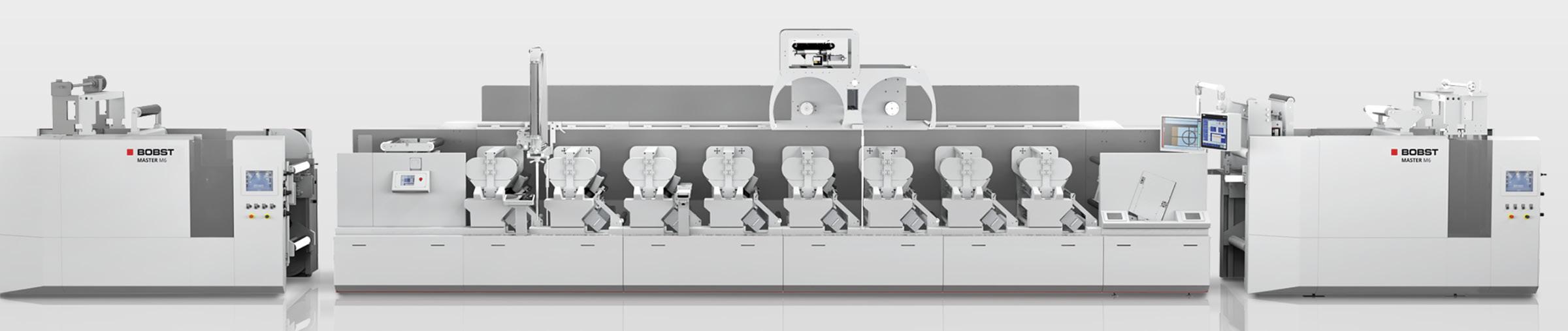
With a strong foothold in the flexible packaging market, UVbiz has quickly established itself as a leading provider of innovative packaging solutions. Specialising in short-run flexible packaging, the company offers a wide range of products, including inmould labels, shrink sleeves, wet glue and wraparound labels, catering to various industries such as beverage, confectionery, home and personal care, pet care, agro products, and frozen food segments.
Recognising the need for cutting-edge technology to meet the demands of short-run production, Rohit Badlani, Managing Director of UVbiz, explains the company's decision to invest in the BOBST M6 press and add to its existing Brotech inspection system, DuPont Cyrel fast plate processors and Esko CDI Spark flexo imager capabilities:
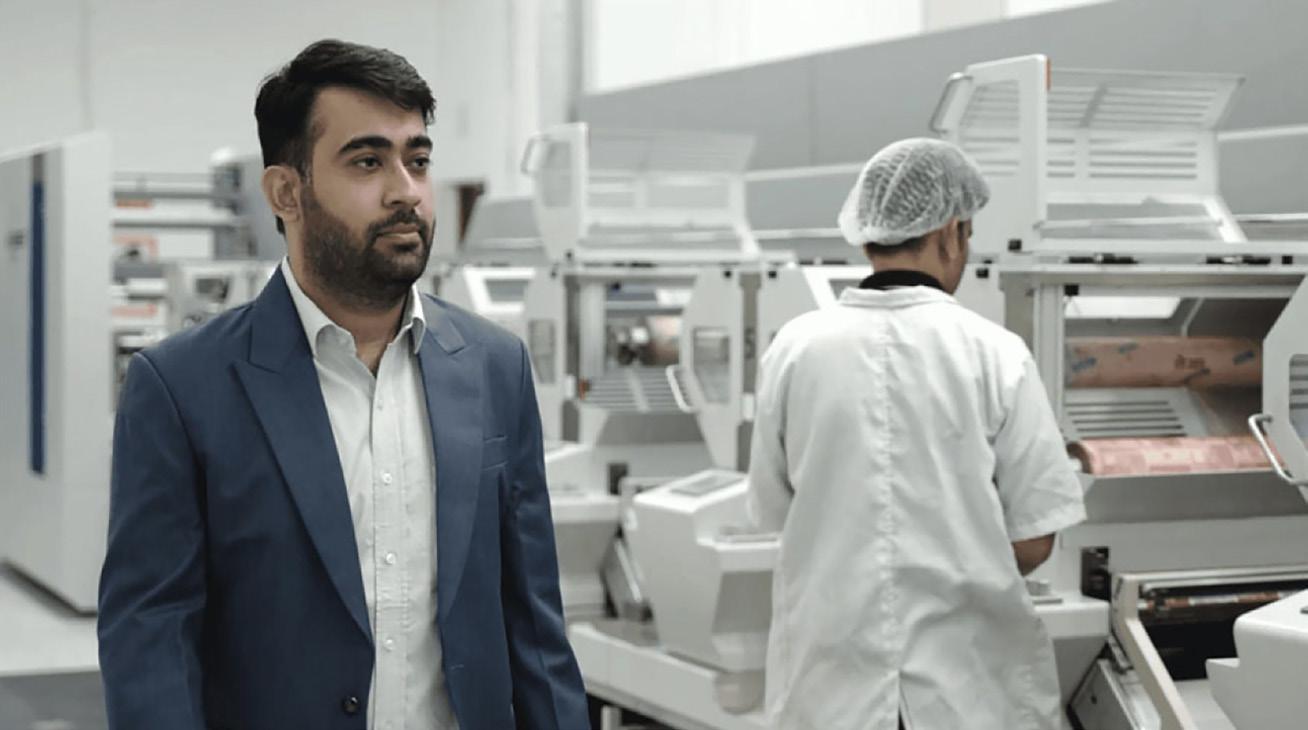
"We felt that other available technologies were not doing enough [for short runs], and lots of startups were cropping up at that time. Luckily, BOBST was also, at the time, publicizing the idea of going for short-run flexible packaging technology. So, we decided to go for it.”
Badlani also highlights the potential for decorative shrink sleeves in the Indian market, which has primarily relied on gravure printing, “Since we are in more of gravure driven area, printing has mainly taken place through gravure but there is scope for machines like BOBST to create décor and innovative sleeving options for customers.”
BOBST’s unwavering support and expertise have been invaluable to UVbiz, whose background is not primarily in the packaging industry. Badlani commends BOBST for its continual dedication and assistance, stating: “BOBST has been one of those fantastic partners, which has been with us from day one from the first trial job to executing in India and going through the process of multiple jobs every day. It has been fantastic. It is always a message away from us; whenever we are stuck in materials, understanding of the business, BOBST is right there.”
One of the key reasons behind UVbiz's selection of the BOBST M6 press is its exceptional flexibility. Initially purchased for short-run flexible packaging, the company quickly realised its potential to print also supported labels and shrink sleeves. "The flexibility of having multiple substrates on the same system was the main idea that drew us towards it," notes Badlani. "When you enter a new industry, it is important to have a backup plan where if one thing doesn’t work, the other should. That gave us the confidence to go with a big investment for BOBST.”

Thanks to its partnership with BOBST and the state-of-the-art capabilities of the M6 press, UVbiz is attracting interest from prominent players in the industry. “We partner with them for all kinds of new product development and new decorative materials in the market. BOBST brings that brand value to our organization for which people want to partner with us.”
The impressive automation of the BOBST machine, with its remarkable 10-second changeover, has left a lasting impression on clients. Badlani shares: "We do it every day, 20 times a day. Most brands are just blown away by the idea of it. They visit just to see it. It has been a fantastic journey. We have had multiple brand owners pitching in their ideas and getting them executed quickly. We have had brand owners coming in at 9am and returning with printed sleeves by 4pm. That is the speed we go by.”

UVbiz is particularly impressed with the OneECG feature of the BOBST press. Although customer awareness for Extended Colour Gamut (ECG) in shrink sleeves remains relatively low in the market, discussions surrounding this innovative technique are gradually gaining momentum.
“Brand owners are discussing it, and it is not far when they will start asking for it. We have understood the idea. People have been attempting OneECG for quite some time, but we have been doing it successfully for the last two years. We don’t have any other ink in our facility apart from the seven fixed colours. We will continue to follow this system whatever new machine we buy with BOBST.”
Badlani concluded by praising the level of service support received from BOBST and recognised its steadfast packaging partnership. He said: “BOBST has been connected with us in a manner that it takes direct feedback from my machine operators to find out more about challenging jobs and asks for feedback on the machine for improvements. It has been a fantastic three-year journey. We will be a loyal BOBST customer for many decades to come.”
drupa next age: Platform for networking and new business
The Special Area drupa next age (dna) sets the scene for newcomers and young talents from the print and packaging sector in a targeted manner. In Deborah Corn and Frank Tueckmantel drupa has enlisted two strong partners with longstanding industry expertise for organising and designing this show-in-show for crosssectional technologies.
Big ideas, small budgets – many young companies find it hard to make the right contacts and establish their exciting and forward-looking solutions on the market. For this target group drupa has created a special platform: drupa next age (dna).
Here newcomers, young talents, startups and long-established enterprises can network on a level playing field, find matching cooperation partners and swap innovative business ideas.
For some participants this is the opportunity to present themselves to an international professional audience for the first time ever.
“In today’s digital age, there is one thing technology can’t replace: personal communication,” explains Frank Tueckmantel, who with Deborah Corn is responsible for shaping the dna programme. “Here’s why Face-to-Face marketing matters: no Tweet, Snap, or chat can ever replace a real human connection. Faceto-face marketing is all about visibility and trust. Moreover, in-person interaction fosters engagement.
For this reason I’m honoured and excited to work together with drupa on the 2024 drupa dna program, hopefully engaging with many of the attendees that will participate in the largest get together our industry has to offer.”
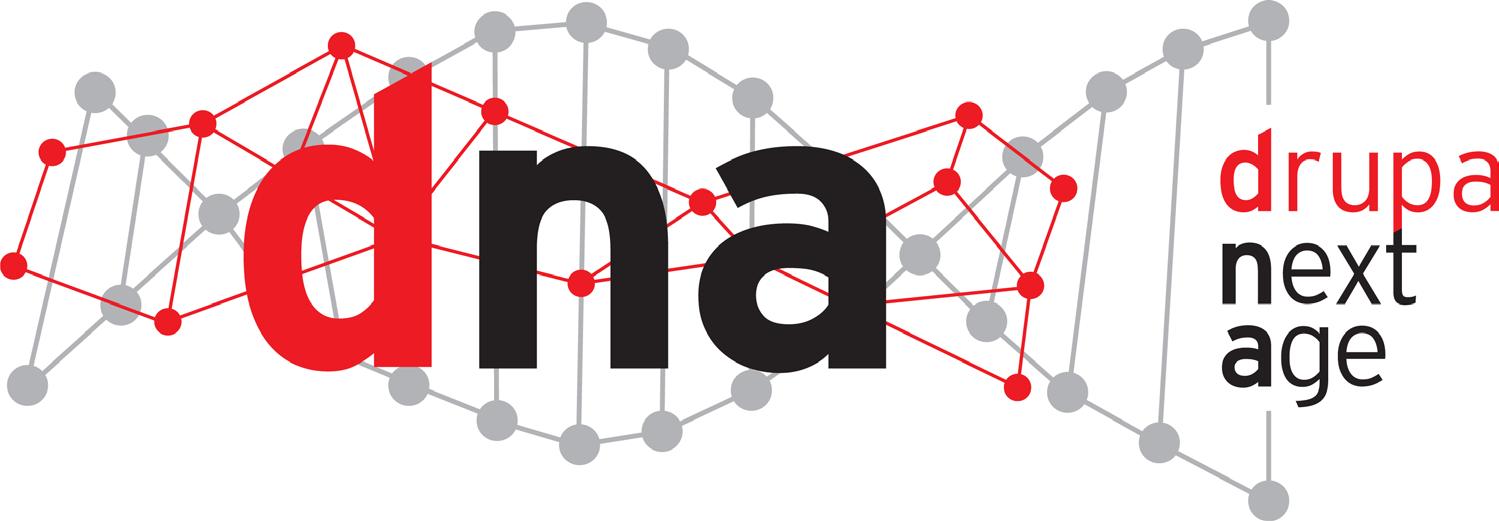
Participation made easy thanks to Plug-and-Play
To keep the hurdles for participation low, drupa for dna focuses on a transparent stand concept with flexible modules and Plug-and-Play. Presentations, panel discussions and interviews on the dna Stage complement the exhibition area in Hall 7.0 providing the ideal forum to win over investors with new business models, product solutions and technologies.
The focal themes at dna will include among others: Additive Manufacturing, Artificial Intelligence, Business Intelligence, New Materials, Platform Economy, Predictive Maintenance, Printed Electronics, Remote Services, New Business Models and Process Design.
At present, interested companies can still register for participation at the dna
Forum – and there are even several ways to get involved: as an exhibitor, sponsor or speaker.
“drupa dna is the ‘Big Bang’ for new companies, new ideas and fresh perspectives that will form and define the future of print,” confirms Deborah Corn. “Our curated program is designed to provide a global stage for global conversations focused on the technology, tools and people who are pushing the industry forward and enabling unique business opportunities for the graphic communication value chain. I encourage everyone to stop by Hall 7.0 during their time at drupa and get a head start on creating a profitable future.”
Companies that exhibit or would like to take part as sponsors at the trend forum dna will be assisted by Benedikt Salmen from the drupa Team (SalmenB@messe-duesseldorf.de). Companies interested in appearing as speakers can obtain more information from Deborah Corn (deborah@ printmediacentr.com) and Frank Tueckmantel (tuecki@mac.com).
About drupa:
Under the umbrella of the megatrends sustainability and digitalisation the international print and packaging sector will meet at drupa from 28 May to 7 June 2024. The world’s leading trade fair for print technologies is synonymous with inspiration, innovations, high-calibre knowledge transfer and intense networking.
This is where the international top decision-makers of the industry meet and exchange on current technology trends and ground-breaking developments. For more information please visit: http://www.drupa.com/
Cut complexity and costs with FLEXCEL NX Solutions.
Simply consistent Decrease waste and setup with predictable plates
Simply efficient Increase on-press performance with a robust plate
Simply sustainable Support sustainable inks and substrates all with the same plate

Simply better Address your most demanding brand and quality requirements
From prepress to on-press, deliver the efficiencies and productivity needed from your plates to maximize your bottom line.
For SALE
Polar Mohr 115X paper guillotine

Year of Manufacture 2005
Price GBP 21,000
The machine is in very good condition, ready for production, after a review.
• Mileage of only 50,000 cuts
• The set includes documentation & a set of tools a tapping block a spare knife and one in the machine
If you have any questions or would like more information, please don't hesitate to contact us.
COUNTRY : Europe
For SALE
CONTACT : Michael Fisher • EMAIL: cpisuffolk@cpi-print.eu
Wanted
Komori S440 4 Colour Printing Operator
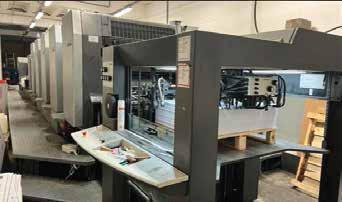
• 2-3 years practical experience (in printing industry )

• Singapore Citizen / PR
• Able to work independently
• Able to work overtime if needed
• Working Hours Mon to Fri: 9am to 6pm, Sat : 9am to 1pm
COUNTRY
Heidelberg Speedmaster CD 102-5+L
CP2000, Auto Plate, Diagonal Register, Preset, Auto
Impression Cylinder Wash, Auto Blanket Wash, Auto Ink roller wash, I/R Dryer + Hot air, Extended delivery, Powder Spray, Technotrans refrigeration, Ink Temperature Control, Dedicated
Coater
Type: Offset Printing
Year: 2004
Impressions: -
Colours: 5
Perfect: -
Sheet size H: 1020
Sheet size Y: 720
Position Vacant
Senior Printing Technician
• Responsible for setting up and operating high-end automated printing machine for quality output and timely delivery
• Ensure machine output is according to specifications required by the job run
• Examines printed results for ink density, accuracy of design and registration conforming to required artwork
• Perform first level analysis and optimize the set-up between the printed sheets
• Constantly monitors the output and take the necessary corrective actions to minimise rejects
• Perform quality control and troubleshoot during job run
• Prepares and updates all production documents required
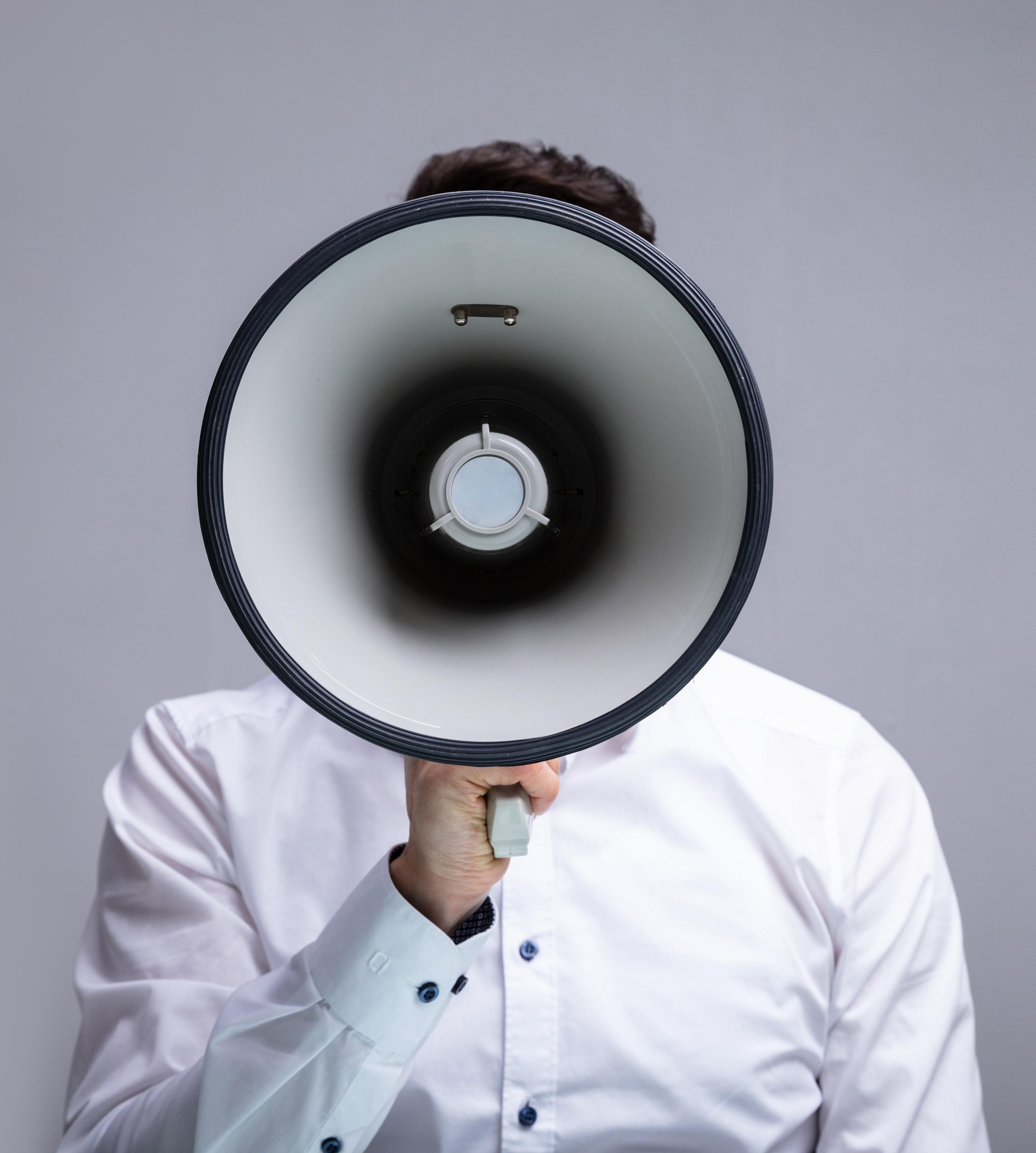

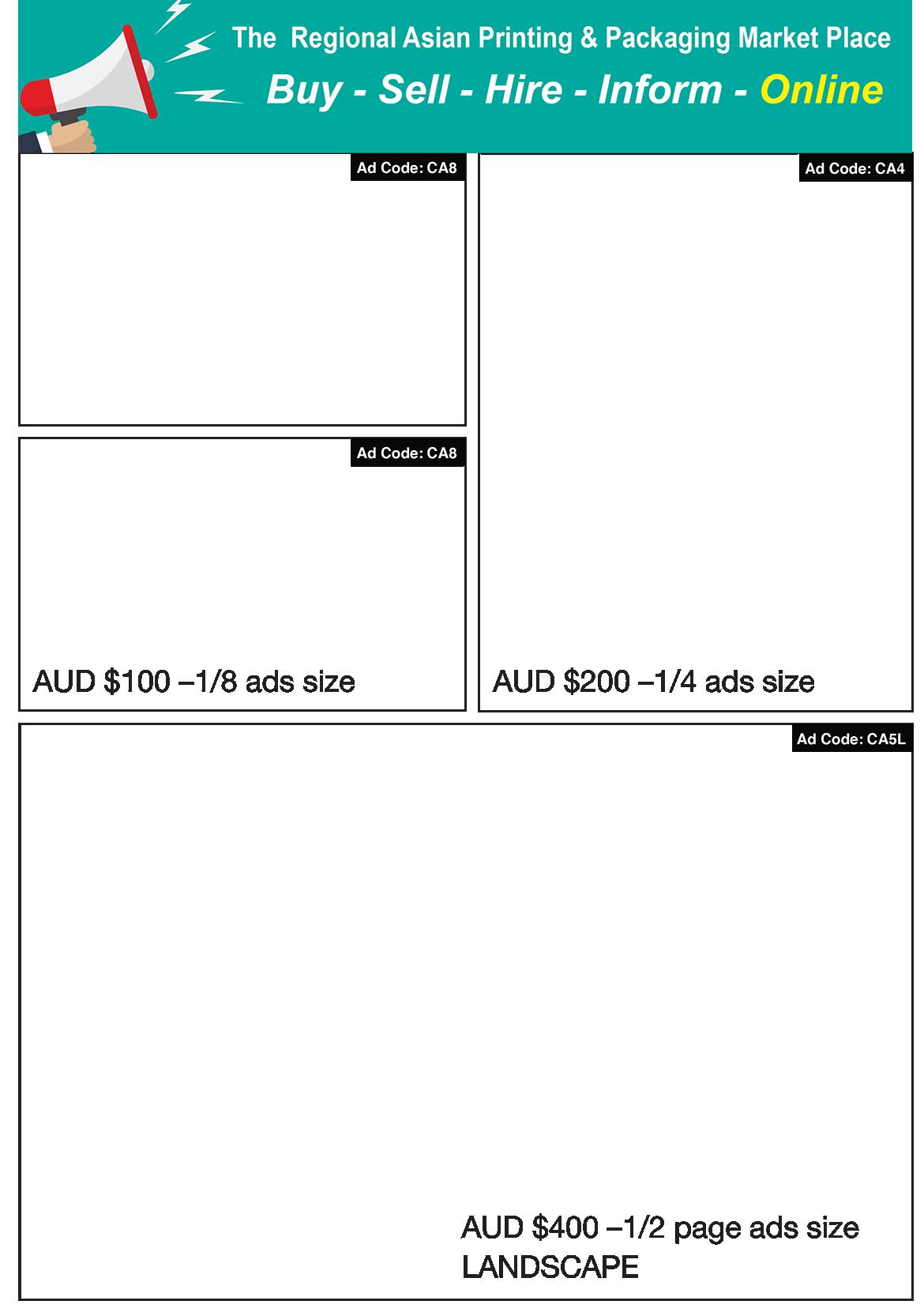
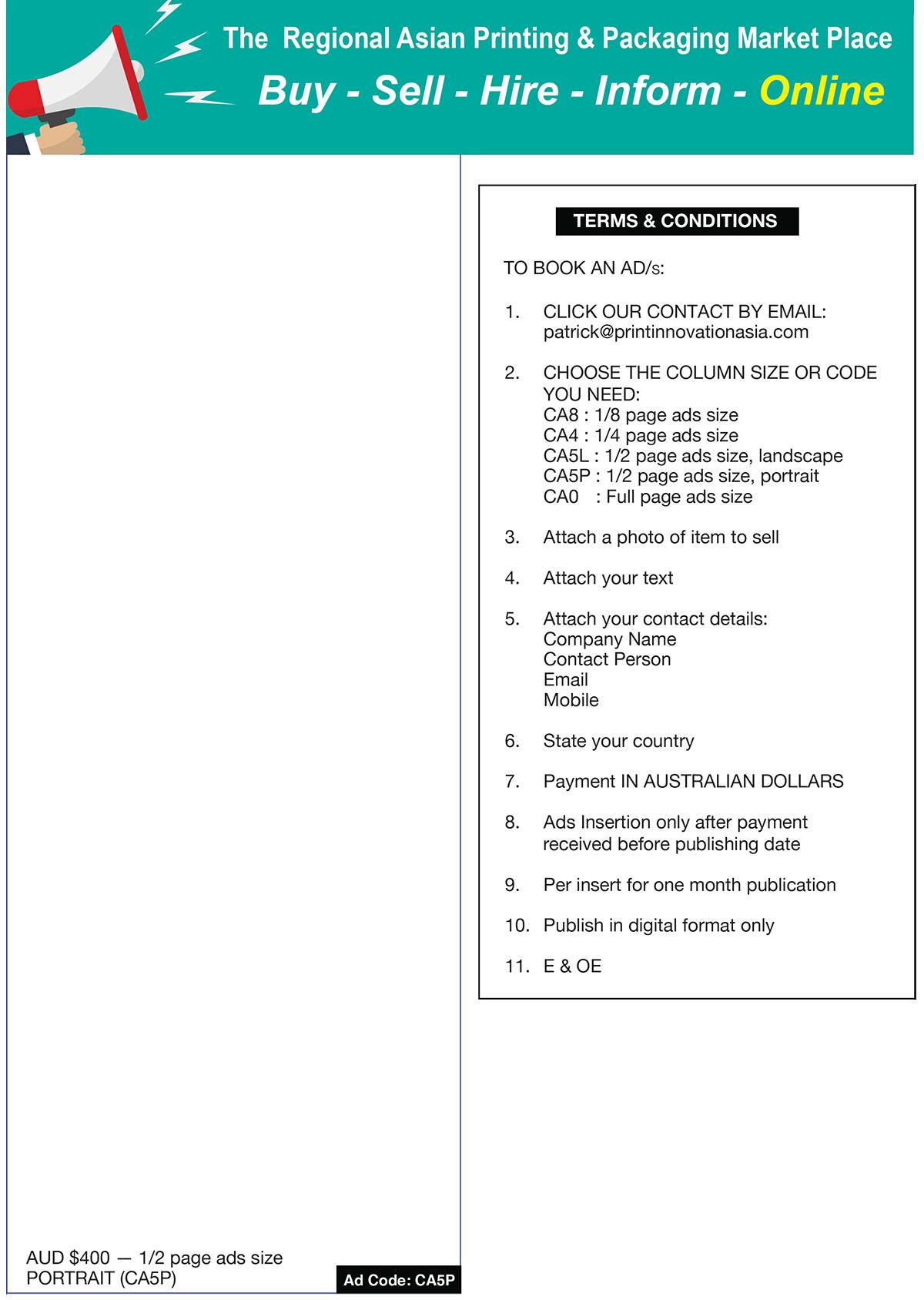