
14 minute read
News from around Asia and the world
Amcor invests in ePac Flexible Packaging
Global packaging company, Amcor, announced its strategic investment in ePac Flexible Packaging. The investment will range between approximately US $10 to $15 million, including a minority ownership interest in ePac Holdings LLC and funding for one or more ePac sites.
Advertisement
ePac specialises in short run digital printing and currently has an all-HP Indigo fleet. In 2020, it expanded into Asia Pacific with two new bases in Singapore and Indonesia. ePac is focused on servicing the needs of small and medium sized consumer goods customers and generates global annual revenues of approximately US $100 million.
"We are incredibly proud of Amcor's innovation and R&D capabilities but with our scale and global footprint we are also uniquely positioned to supplement our internal efforts with investments in complementary technologies and business models. Our investment in ePac is the first corporate venture-type investment for Amcor and provides a great opportunity to learn from a high growth start-up,” said Amcor's CEO Ron Delia.
Amcor's Executive Vice President, Ian Wilson added: "ePac is a truly entrepreneurial technology driven company and has proven its ability to rapidly scale up a flexible packaging business, doubling revenues each year since its formation in 2016.
This is an exciting opportunity for both companies to benefit from the combination of innovative technologies and business models and the deep expertise of the industry leader. We look forward to working with the ePac team and exploring opportunities to further extend this partnership in the future.”
Sharp rise in raw material costs leads to price adjustments at Heidelberg
In order to cushion the disproportionately sharp rise in material, logistics, and other procurement costs, Heidelberg will be moderately increasing the prices for its equipment business with immediate effect. This adjustment is being made in an economic environment of rising demand and costs for raw materials and is a necessary step in order to continue offering customers innovative solutions and first-class service.
"The current price development of raw materials shows an unprecedented upward momentum," said Rainer Hundsdörfer, CEO of the company. "Primarily due to the high demand from China as well as the global megatopic of electromobility, procurement costs have risen significantly in the short term. In recent months we have exhausted all possibilities to avoid an imminent price increase. We want to grow together with our customers and continue to be a reliable partner to them in a changing market environment. The moderate price increase that is now necessary will allow us to further expand our innovation leadership and is therefore also an investment in the future."
The focus is on the customer with his requirements to optimally develop and utilize his business potential through state-of-the-art technologies, innovative solutions and with new business models. With a view to the decisive factors, such as process optimization and intelligent, operatorindependent productivity, Heidelberg offers the smart print shop.
To this end, all Speedmaster models in small, medium, and large formats are equipped with the new Push to Stop functions and a cloud connection as standard. This means that all customer groups can enjoy the steadily growing range of cloud-based software solutions and also benefit from future developments.
Interesting innovations in the field of intelligent assistance systems and AI impressively demonstrate what is already possible today and where developments will go in the coming years.
Customers will be contacted directly by the Heidelberg sales team.
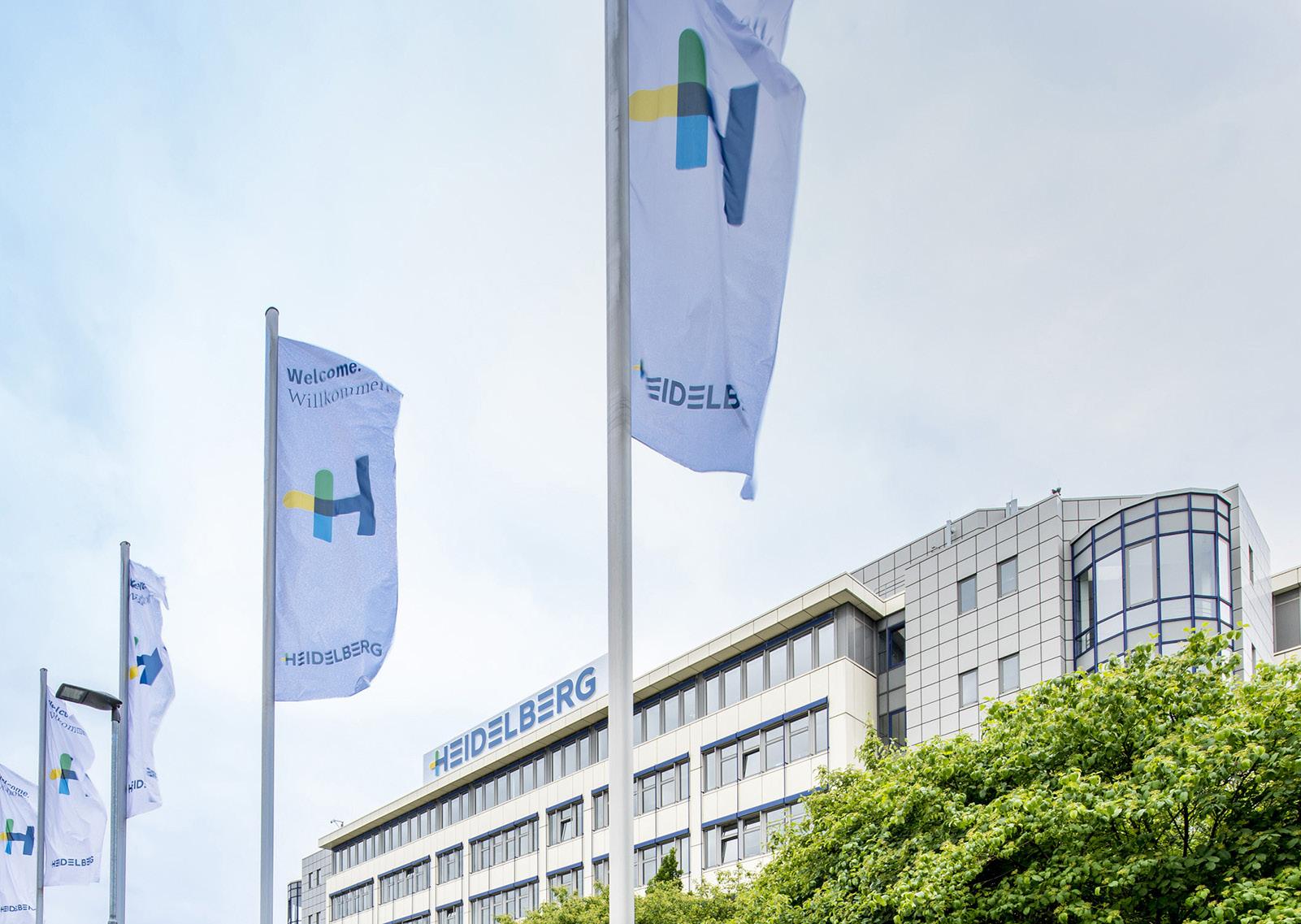
Miraclon launches KODAK TIFF Assembler Plus (TAP) Flexo Edition Version 5.0
Miraclon announces the launch of the new KODAK TIFF Assembler Plus (TAP) Flexo Edition Version 5.0 software, further enabling KODAK FLEXCEL NX System users to simplify their operations and ensure continuous production.
TAP 5.0, available in 11 languages – including Chinese and Japanese, has specifically been designed to allow more configurations and robust usage, and supports the latest operating systems that includes Windows 10, Windows Server 2019, as well as macOS Big Sur (11.2) and macOS Catalina (10.15). New cutting table enhancements boost the quality, speed, and reliability of the process across a wide range of cutting tables, while its Invert Trim Waste feature, which automatically inverts the nonimaged areas of the plate, will reduce plate processing costs through fewer photopolymer wash outs, less chance of re-deposits, and lower solvent spend.
Building on its already strong reliability, TAP 5.0 also features improvements to customers’ connected support experience, enabling a more accurate scheduling of preventative maintenance and effective on-site and remote support or training. Meanwhile, back-ups of TAP 5.0 will now occur automatically in the background to minimize disruption if any problem arises.
Joerg Kullwitz, Commercial Director for Miraclon’s Asia Pacific Region, comments: “Our R&D Team with their rich heritage in innovation are continuously looking at ways that will enable customers to streamline their daily operations. Tap 5.0 will enhance the efficiency, reliability and ease of use of our KODAK FLEXCEL NX Solutions to allow our customers to concentrate on the effective management and growth of their businesses.”
Tap 5.0 is available to current FLEXCEL Solutions customers to download, at no cost, immediately.
KODAK FLEXCEL NX Ultra Solution moves to its new home at the W&H Technology Center
Renovations at the Windmöller & Hölscher (W&H) Technology Center in Lengerich, Germany, have been completed, and included moving their in-house prepress technology – a KODAK FLEXCEL NX Ultra Solution from Miraclon – to a brandnew plate room for quicker and easier accessibility. Providing a fast and solvent-free and VOC-free option to predictable, consistent and top-quality flexographic plates, the FLEXCEL NX Ultra Solution is used at W&H for a broad range of applications, including platemaking for press demonstrations and printing tests, as well as customer events.
“We really value our partnership with the team at W&H, who shares a similar vision about where the flexo industry is moving to”, says Grant Blewett, Chief Commercial Officer at Miraclon. “Since the equipment has been installed in 2019, it has worked virtually uninterrupted for demonstrations and application development tests.
We look forward to seeing more customers face-to-face again in the near future to showcase the capabilities of FLEXCEL NX Solutions on W&H’s state-of-the-art flexo presses.”
Ulrich Harte, W&H Product Management, adds: “Our 10,000 square-meter Technology Center is the largest of its kind anywhere in the world and it’s equipped with cutting-edge technologies. We can demonstrate the entire packaging printing value chain including prepress here in one place to existing and potential customers in a live atmosphere that is closely aligned to practical needs.

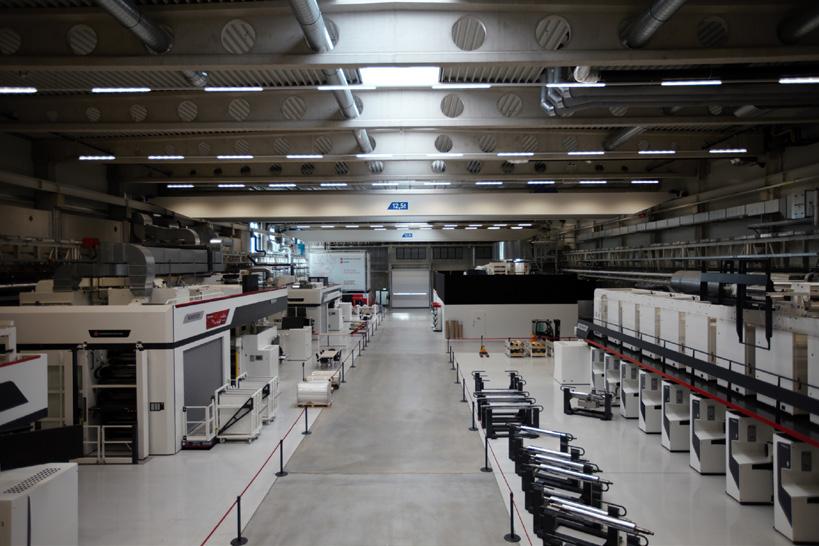
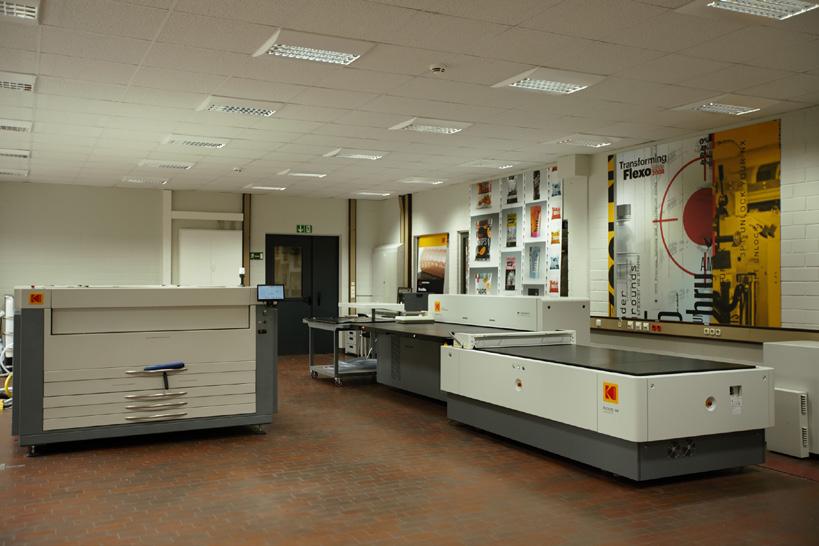
The availability of innovative technologies like Miraclon’s FLEXCEL NX Ultra Solution is crucial to our ability to present high quality flexo packaging printing as an efficient end-to-end process.”
New Beam 2 For Folding Carton Installed At Van Nuys Site≠
Following the successful installation of a Highcon® Euclid IIIC digital cutting and creasing machine at their Brook Park, OH site at the end of 2019, Digital Room has now increased production with a newly installed Beam 2 machine at their site in Van Nuys CA.
For over 25 years, Digital Room has been a trusted leader in online printing. As an industry innovator, they offer a vast range of print and packaging products for dozens of branded online sites. By leveraging the latest manufacturing and e-commerce technologies Digital Room can provide high value products in whatever quantity their customers need in a delivery turnaround time as short as 24 hours.
According to Chase Cairncross, COO, Digital Room: “With the constant increase in e-commerce, customers want to be able to decide the shape, size, color and quantity of the items they need – they do not want to be limited to what they are told they can have. By using digital finishing technology, we eliminate the need for physical dies, we dramatically shorten the cycle time from order to delivery and we offer our customers unlimited design creativity, all benefits that are extremely challenging or practically impossible using conventional finishing equipment. That is how we started using the Highcon Euclid IIIC machine for corrugated. As our business grew, we realized the potential of extending the digital finishing revolution would allow us to expand the range of products for other categories we are able to offer our customers.”
Cairncross added, “the experience we had with the Highcon team was outstanding. We were up and running, delivering customer jobs within 4 days of the equipment arriving at our facility. In less than four months we are already operating three shifts per day. Highcon’s consultative approach is making a significant difference in our ability to maximize the value of their digital finishing technology and accelerate our return on investment while increasing our customer satisfaction”.
Mike Ciaramella, VP Sales & GM Highcon Americas added:” Digital Room has built their business around the concept of offering customers creative products combined with ultra-fast delivery, while ensuring a high level of customer satisfaction. Today’s consumers require the flexibility, customization, and variety that Highcon systems deliver. We are proud of the confidence Digital Room has in our technology and are committed to helping them grow and succeed.”
FUJIFILM and FUJIFILM Business Innovation jointly open virtual event “FUJIFILM Virtual Exhibition 2021”
FUJIFILM and Fujifilm Business Innovation hereby announce that the graphic communication division of the two companies will hold an online event “FUJIFILM Virtual Exhibition 2021” from June 24th to July 9th. The new products will include a new print on demand system renewed under the Fujifilm brand, a new digital press in the packaging segment where high market growth is expected, and a new line up of wide format inkjet printers.
The event will also feature a range of seminars from independent graphics industry experts covering a wide range of subjects, with the focus during the exhibition period on creating new value, with various topics covered including updates on industry trends and tips for overcoming the COVID-19 disaster.
Overview of FUJIFILM Virtual Exhibition 2021
1) Concept Under the title of “BELIEVING IN PRINT”, Fujifilm’s “Virtual Exhibition 2021” will open as a place for printers to experience multiple solutions all designed to help create new value. Fujifilm will exhibit the latest solutions across a broad range of sectors such as commercial, package and sign & display printing in a 3D space built to reflect a “printing factory of the near future”. On show will be a variety of high quality videos of webinars and demonstrations that support the formation of growth strategies for developing new business and process reforms aimed at further efficiency.
2) Registration Registration is required to enter the Virtual Exhibition, which can be carried out at https://believinginprint. fujifilm.com/eu/en/
4) Webinar Fujifilm will offer eight sessions by
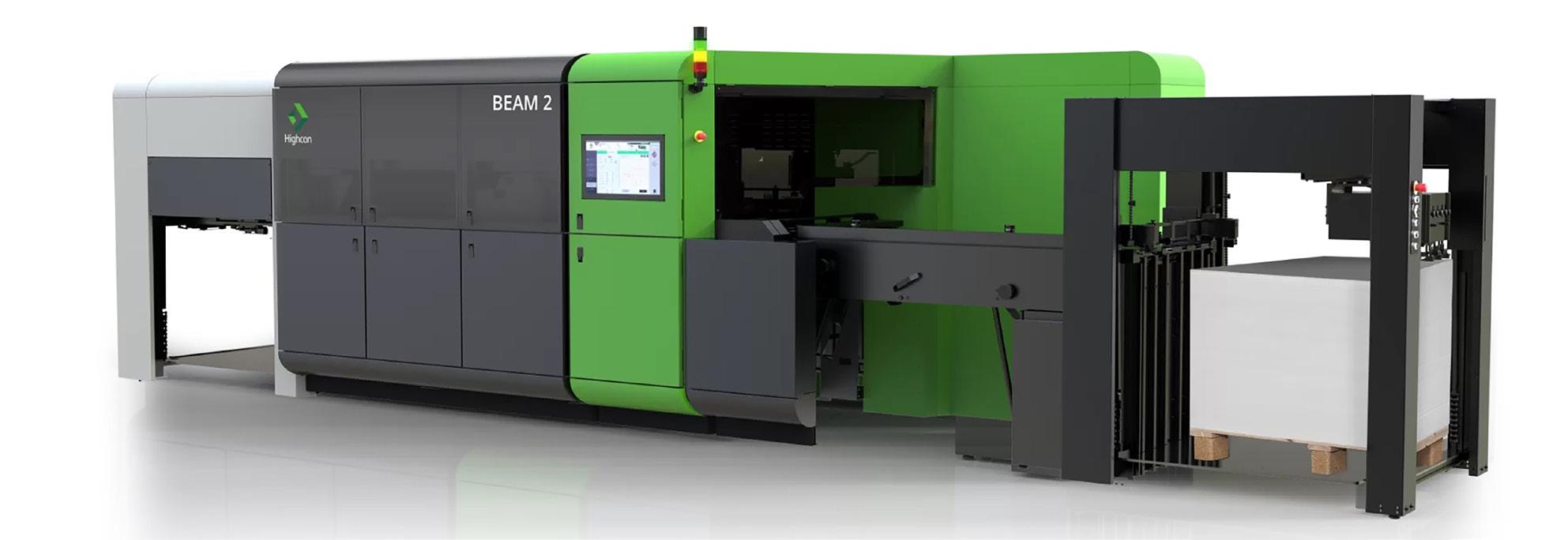

experts from a wide range of fields in the industry which can be used to develop ideas about new printing possibilities, such as developing new businesses and growth strategies, and ideas that lead to process reforms for further efficiency.
1. Keynote Session “The Graphic Arts Industry and the New Fujifilm” (24/6 14:30@CET, LIVE Jim Hamilton Industry Analyst, Keypoint Intelligence Hiroaki Shimosaka General manager of Graphic Systems Business Division, Fujifilm Corporation
2.“Technology driving change for variable data on direct mail and transaction print” (25/6, on demand) Ryan McAbee Director Production Workflow Consulting Service, Keypoint Intelligence 3.“Future of Digital Labels and Flexible Packaging” (25/6 16:00@CET, LIVE Sean Smyth Printing &Packaging Technologist, Smithers analyst &consultant, SMITHERS
4. “Technology driving change for variable data on direct mail and transaction print” (25/6, on demand) Greg Balch Vice President and General manager in charge of FUJIFILM Integrated Inkjet Solutions Shane Tansey Business Development Manager for FUJIFILM Integrated Inkjet Solutions Ankur Mour Mechanical Engineer III for FUJIFILM Integrated Inkjet Solutions 5. “Digital Printing Value & How to Sell it” (28/6, on demand) German Sacristan Director Production Print & Media Group, Keypoint Intelligence 6. “Challenges and opportunities for commercial printers post-COVID” (28/6 16:00@CET, LIVE Marco Boer Vice President, IT Strategies
7. “The State of Wide Format Printing 2021 – Roadmap to Recovery” (29/6, on demand) Eric Zimmerman Director of Wide Format Printing, Keypoint Intelligence
8. “A digital imprinting strategy for packaging” Greg Balch Vice President and General manager in charge of FUJIFILM Integrated Inkjet Solutions
Shane Tansey Business Development Manager for FUJIFILM Integrated Inkjet Solutions Jamie Walsh North American Sales Manager for FUJIFILM Integrated Inkjet Solutions
Revolutionary technology to unlock a profitable and sustainable label future
ACTEGA, manufacturer of specialty coatings, inks, adhesives and sealing compounds for the print and packaging industry, today officially launches Signite™ – a revolutionary, ACTEGA patented, premium quality decorating solution, designed to significantly reduce, and one day eliminate, waste in label production.
Depending on the decoration design, the technology can currently reduce label waste by over 50% compared to a similar footprint pressure sensitive label by elimination the label matrix, reducing the decoration thickness to about a third of that of a typical clear pressure sensitive label and eliminating label media plastic in non-print areas.
Furthermore, with Signite decorations comprising substantially less material mass than alternative modalities such as pressure sensitive labeling and shrink sleeves, this novel alternative is much more accommodating to current recycling processes and the expanding brand led container re-use programs beginning to dominate single-use glass packaging throughout the world.
The ground-breaking Signite decorations represent a true alternative to “no-label look” labels, bringing the look and feel of direct to container screen or digital printing with the efficiency of pressure sensitive labeling.
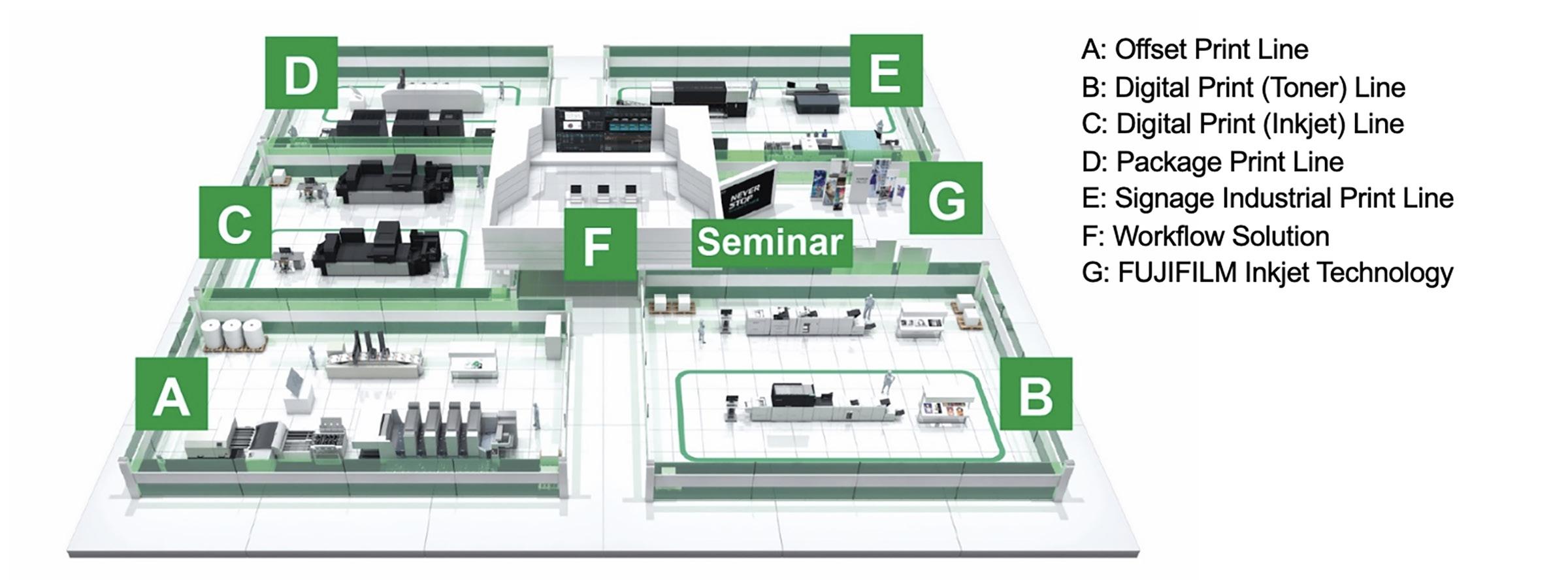

Today, the decorations are produced using slightly reconfigured narrow web flexo or hybrid digital printing processes running at standard narrow web printing speeds. Small to mid-sized brands have the potential to utilize these new or modified variations of their printing assets immediately, therefore allowing for relatively seamless scaling of their decoration production as the Signite technology continues to commercialize.
Transfer of the Signite decorations to containers requires designed-for-purpose variations of pressure sensitive labeling equipment. The first Signite in-line applicators launched into the market address rigid cylindrical containers at lower throughput speeds. Subsequent system designs, that are in different stages of prototype development, will address aluminum and asymmetrical containers along with thin-walled container types requiring inflation for decoration transfer.
High speed Signite applicator machines and corresponding decoration media are planned as an inherent part of the technology roadmap and are anticipated to move into prototyping in 2022.
“Brands are taking a leadership position on sustainable packaging solutions, with ambitious waste reduction goals and a drive to increase the efficiency and scale of container recyclability,” explains Anthony Carignano, Technical Director Marketing – Signite, ACTEGA. “At the same time, these companies are seeking ways to unlock new high-quality label aesthetics and tactile experiences for premium products.
“Signite offers these brands the best possible chance to meet all of these objectives. The solution is truly gamechanging with no other technology delivering plastic waste reduction on this scale. Plus, as the solution advances and becomes compatible with other production processes, such as digital inkjet, the impact on the industry and ultimately, the environment, will only become more significant.”
Signite promises to be a pioneering solution for numerous market sectors and aims in the future to support the high-volume production required by high-profile brands. Today, the solution is ideal for small volume contract decorators and specialty brand owners looking for a substantial differentiator that strengthens their competitive edge.
“In this first phase of the technology’s launch, we have a strong and clear focus on advancing this solution for the glass packaging sector. The end customers initially benefitting from this solution will therefore include producers of craft distilled spirits, micro- or mid-sized winery products, specialty food and non-alcoholic beverages, natural and nutraceutical pharma products, and home glassware, such as candles. With several beta customers already in operation working with glass containers, and additional versions of the technology targeted for rigid PET containers and aluminum beverage cans anticipated over the next few months, we expect the demand for this solution to accelerate its success and rollout across the industry.” says Carignano.
Thorsten Kröller, President Division ACTEGA, concludes, “This is an exciting time for ACTEGA and the industry in general. We are developing and bringing to market a solution that helps brand owners achieve their sustainability targets as well as achieve unique aesthetics for premium labeling. Although it is still in its infancy, Signite represents a huge milestone for the industry and on ACTEGA’s sustainability roadmap.”
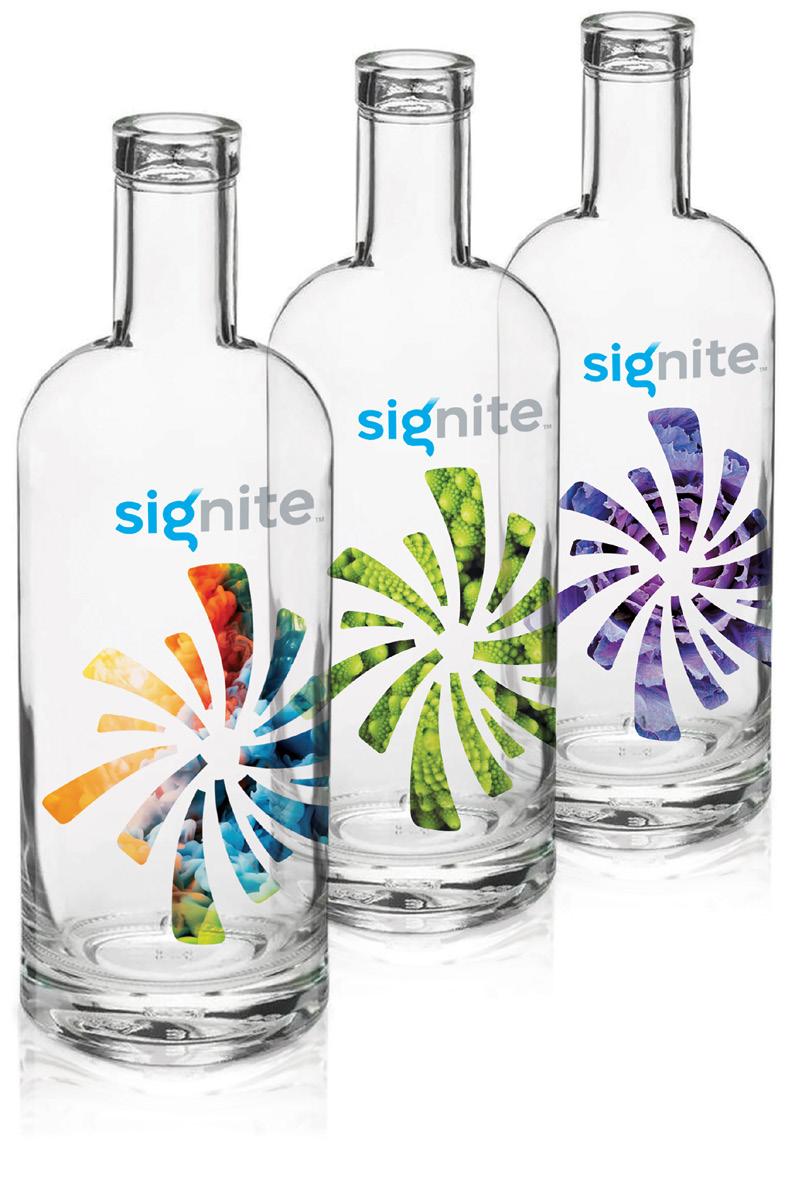
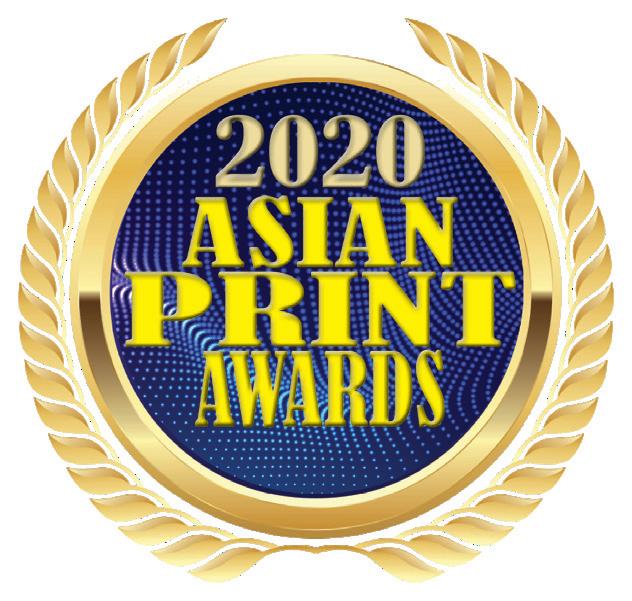
Winners Announced Next Issue
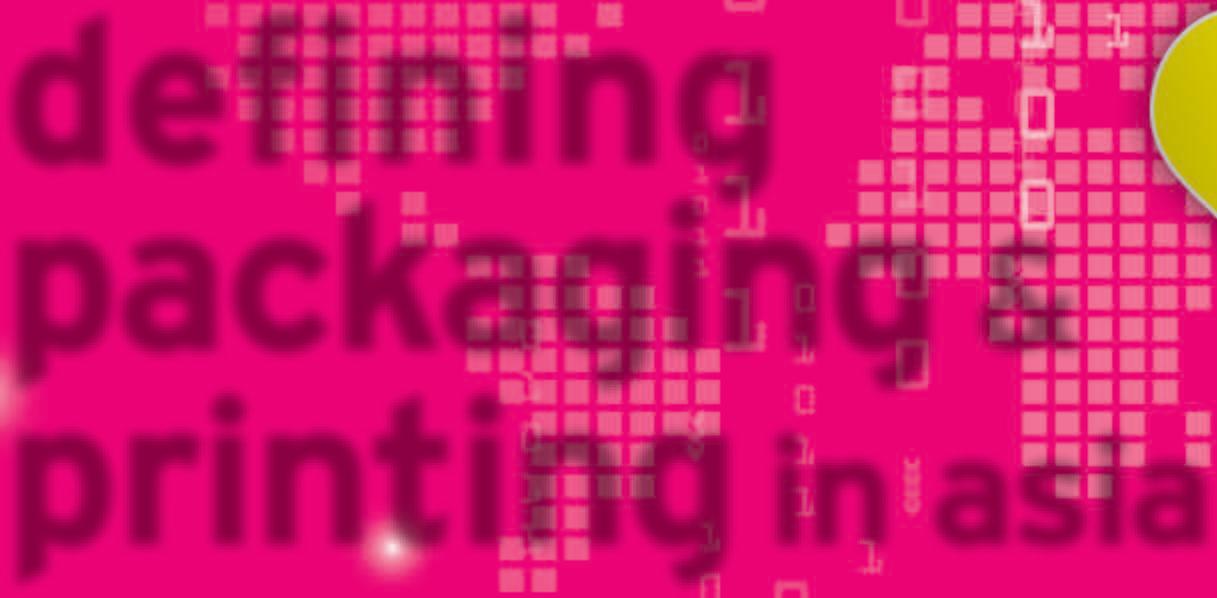
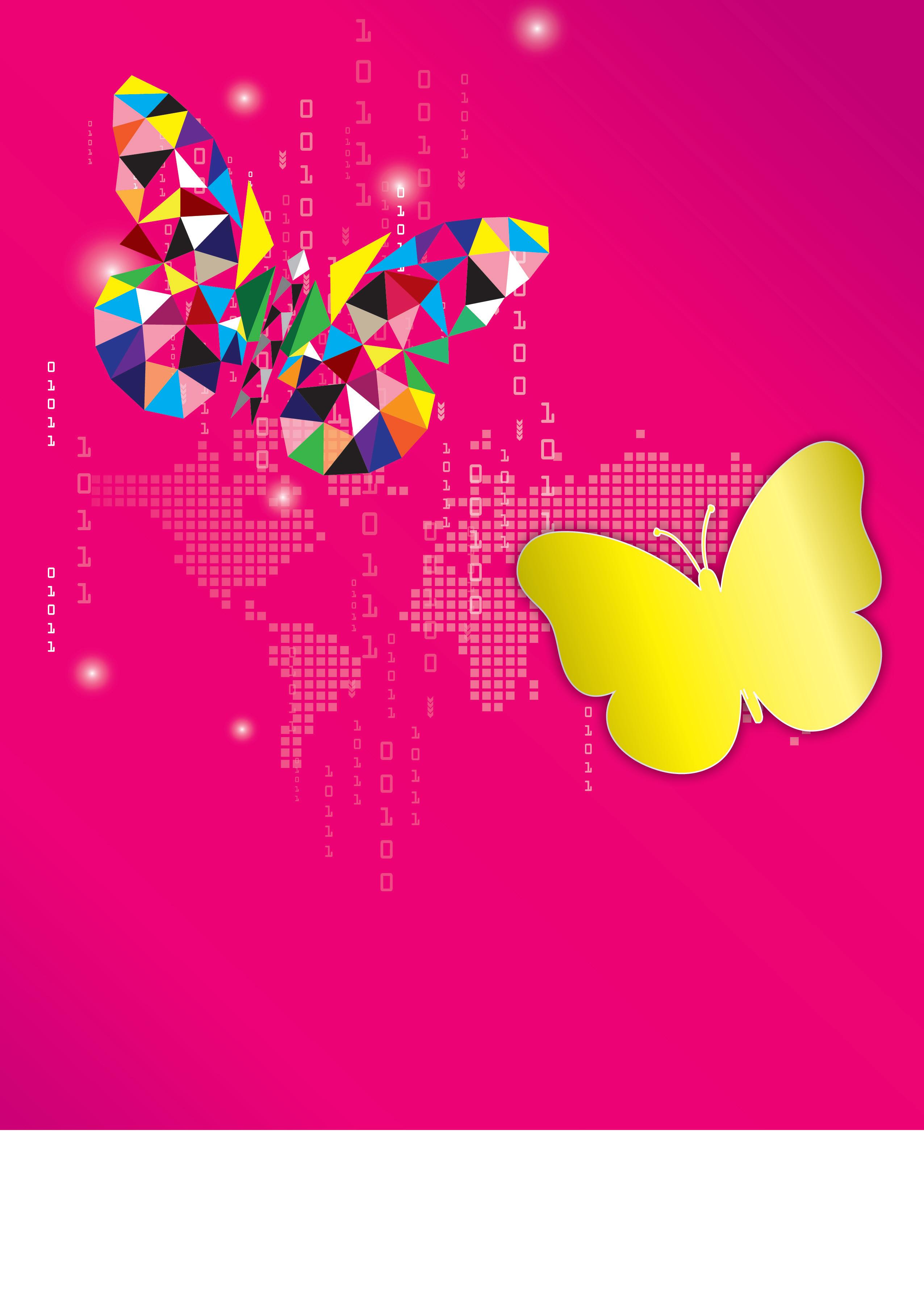
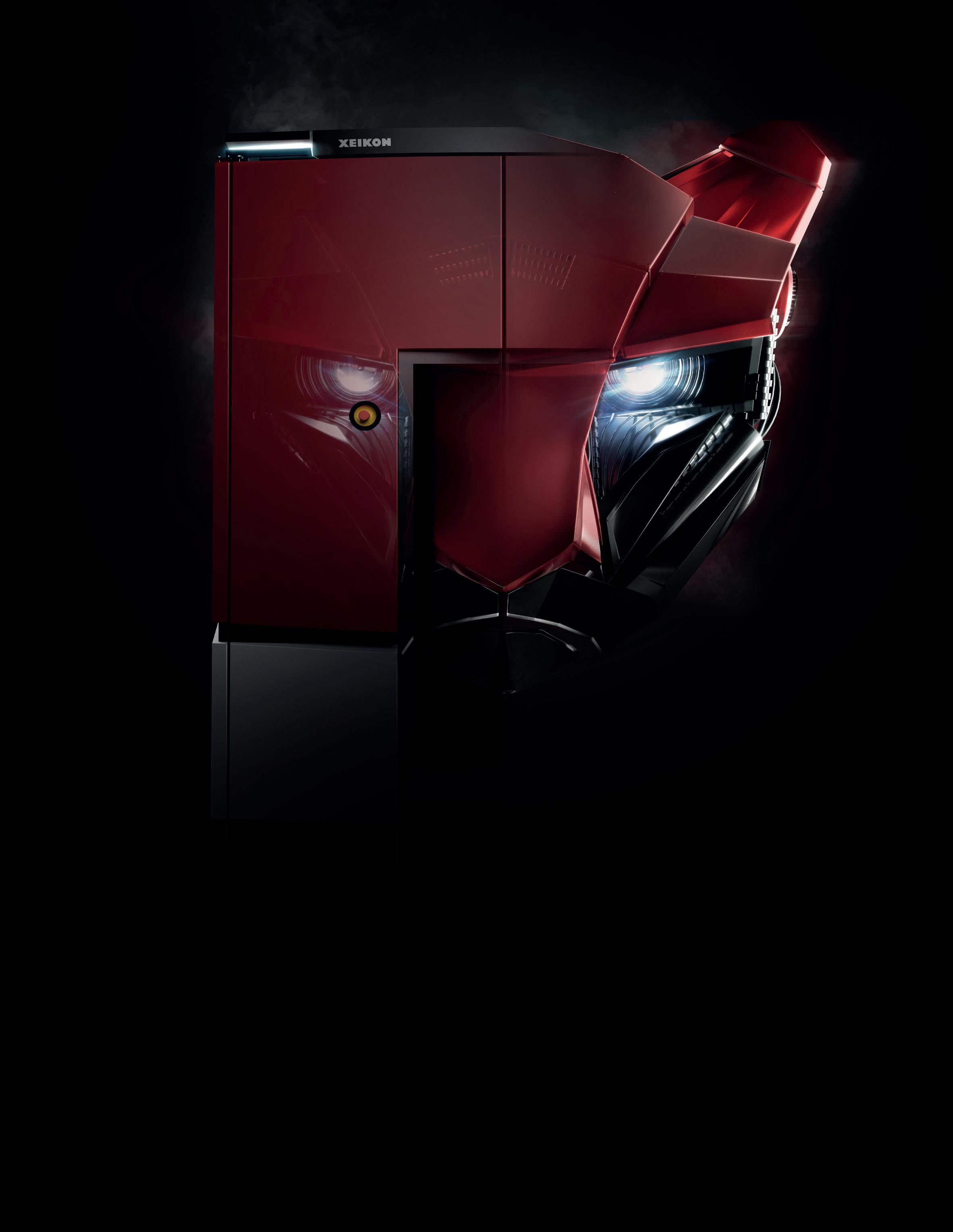