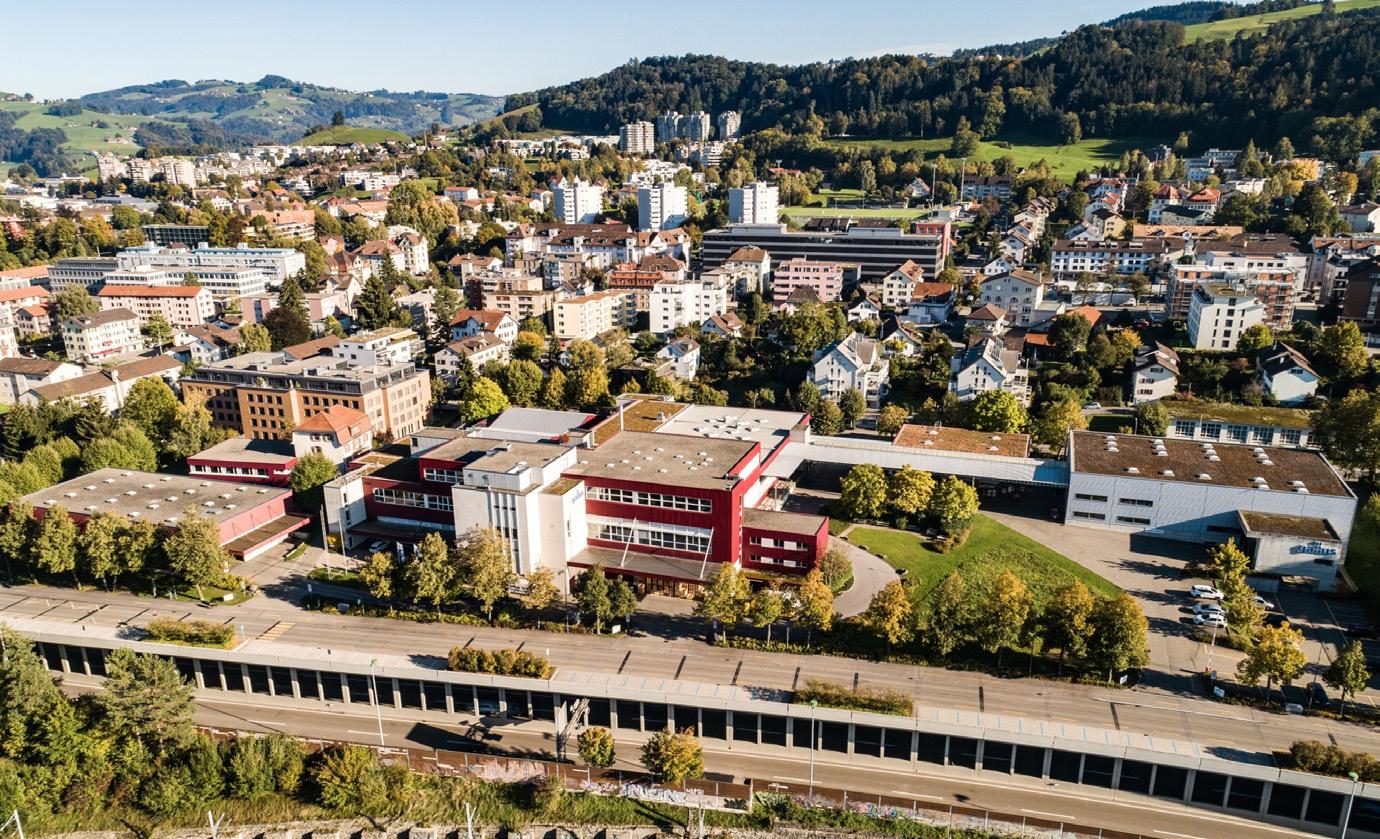
9 minute read
Indusrty news from the region & around the world
Heidelberg focuses on growing label market and strengthens Gallus sites
Heidelberg is further expanding its commitment to the growing label market. As part of this, the Gallus Group sites in Switzerland and Germany have already been strengthened through targeted investments and divided into competence centers.
The next step will be to reorganize the headquarters in St. Gallen, Switzerland, and develop it into a competence center for digital label printing. To this end, the new customer demonstration center is to be opened at the site at the end of the year as the "Gallus Experience Center". The expansion of the digital printing portfolio will be accompanied by comprehensive innovations in equipment, service, software and ink.
A total of around 160 people work in St. Gallen, including business and R&D management as well as finance, sales, service, marketing and purchasing. The new office infrastructure and the Experience Center will be reorganized in the main building of the site.
"With targeted investments in the Gallus Group, we want to gain further momentum in the growing label market," said Dr. Ludwin Monz, CEO of Heidelberg. "The reorientation of our site in St. Gallen into a competence center for digital label printing underlines the high strategic importance for Heidelberg in the packaging sector. We welcome, that the commitment of entrepreneurs Marcel and Roger Baumer will create an innovative environment in St. Gallen from which we can also benefit."
Baumer entrepreneurs from St. Gallen develop property into open industrial and technology campus with Gallus as anchor tenant As part of the reorganization of the site, St. Gallen entrepreneurs Marcel and Roger Baumer will take over the entire area in St. Gallen with around 20,000 sqm on April 1, 2022. The brothers are the fourth-generation owners of the Hälg Group and have acquired the site privately. Gallus will continue to use the required space as the main tenant in this area in the future. A corresponding purchase and long-term lease agreement has been signed. Heidelberg expects the transaction to be completed in the first quarter of the 2022/23 financial year. The parties have agreed not to disclose the purchase price.
"The Gallus area is set to develop into an open campus for companies and institutions that are helping to shape the future and strengthen St. Gallen as a workplace. We are delighted that the Gallus Group, with its headquarters and Digital Campus, is the anchor tenant of the site," says Roger Baumer.
Folding cartons digitally printed and embellished in one pass
Packaging is an attractive market that has recorded continuous growth for some years now. This tendency has been further reinforced by the Covid-19 pandemic. In addition, especially in food packaging, the trend is towards smaller packaging units – reflecting the steady rise in the number of small and one-person households – as well as a wider variety of packaging due to more differentiated consumer demand. This diversity is also encouraged by the fact that brand owners want to differentiate their multiple SKUs and increase the frequency of marketing campaigns to secure consumer attention.
At the same time, the growing importance of sustainability is a driver for the use of more environmentally sound materials. Wherever possible, brand owners and retailers are opting for plastic-free packaging and ecofriendly packaging materials that can be easily and completely recycled.
All these trends benefit folding cartons as high-quality packaging, being valued by consumers as a sustainable and environmentally conscious alternative. Digital printing represents a motivating option for small-batch production of folding cartons. In general, digital permits very short-term production following the approval of packaging designs, meeting demands for a short time to market.
Furthermore, digital printing enables customization or versioning of folding boxes in any form. The technology makes it simple to add security features such as serialized codes for supply chain tracking or regional regulatory content. Similarly, variable design and marketing elements – such as variable codes for lottery or gaming campaigns and connected or smart packaging applications linking the analog with the digital world – can be integrated into folding carton designs.
When it comes to packaging applications like these, the new KODAK ASCEND Digital Press is in its element. The sheetfed electrophotographic press is based on an extremely robust platform from Kodak that is capable of reliable, superior quality production of millions of impressions per month.
ASCEND Digital Press is an ideal cost-effective solution for folding carton printing, not least because it can print sheets up to 1,219

mm long. Equally important for packaging applications is ASCEND’s compatibility with a very wide range of substrates. The press is suited for printing on uncoated as well as matte and glossy coated board stock and papers – including recycled materials – and a whole range of special substrates. The substrates can be up to 762 microns thick or have a weight of up to 687 g/m2.
The strengths of combined highquality printing and in-line print embellishment Another remarkable feature of the ASCEND Digital Press is its fifth imaging unit. It enhances ASCEND’s ability to effectively convey the brand identity on packaging, supporting the decisive impulse at the point of sale. This unit enables the press to print one of a total of 13 available eco- friendly specialty inks in one pass, in addition to the new KODACHROME Dry Inks for CMYK process colors. This allows special color or finishing effects to be achieved, producing vibrant and eye-catching packaging.
The specialty inks include Orange, Gold, White, Clear, Dimensional Clear and Foil Dry Inks to name just a few. Not only does KODACHROME Foil Dry Ink enable a multitude of true cold foil print enhancement effects, it also greatly reduces costs with foil used only where it is required, instead of covering expensive foil board with costly white ink.
The specialty inks can be placed in the first, second or fifth imaging unit of the press. This allows ASCEND Press to meet production requirements for different ink sequences. This is helpful, for example, when printing on colored or natural brown board stock. First, a background can be created with Opaque White, onto which the CMY colors are then printed. Whether it's folding carton boxes, blister cards, paperboard food boxes or belly bands – in packaging applications, it's essential to render brand colors accurately. ASCEND’s high gamut KODACHROME Dry Inks are capable of achieving more than 90% of the PANTONE library with just CMYK, allowing the extra imaging unit to focus on embellishments and special effects.
And if that shouldn’t suffice, one of the specific KODACHROME Custom PMS Colors can be used as the fifth color. With regard to sustainability, it is also important that KODACHROME Dry Inks are manufactured using environmentally sustainable materials and are fully recyclable. They are also rated for indirect food contact.
There's another plus that makes ASCEND a perfect choice for folding carton printing: It is the first digital press that can control gloss levels during the electrophotographic process. With the KODACHROME Dry Inks, the operator can adjust gloss levels without compromising on speed, accuracy or quality.
This allows specific requirements of brand owners to be met. In addition, this feature helps to match the look and feel of folding cartons printed digitally in short runs even better to long runs printed in traditional sheetfed offset.
KODACHROME Dry Inks also surpass the Sutherland Ink Rub test. This means the printed image has maximum durability and a high resistance to abrasion that package handling, shipping or storage can cause. Furthermore, these inks were designed to support additional lamination and coating/varnishing of the printed sheets as well as glues for the packaging industry without the need for dedicated “digital” formulations which usually are more costly and have fewer varieties.
Additional applications beyond shortrun folding carton printing In addition to packaging, ASCEND Digital Press can also handle commercial jobs at high throughput and in stunning quality. As the press has four standard feeders for different paper types and sheet sizes in addition to the long sheet feeder for the thick folding carton substrates, such applications can be run in quick succession with packaging production.
“KODAK ASCEND Digital Press is a uniquely versatile production platform that supports efficient and profitable small batch production of folding carton packaging,” said Jeff Zellmer, Vice President, Global Sales and Strategy, Kodak. “The combination of high-quality CMYK printing and a wide range of print embellishment options in a super-reliable, easy-touse machine makes ASCEND an extremely attractive investment.”
Fujifilm announces the launch of the Activ Hybrid LED UV curing system
Fujifilm today announces the launch of the Activ Hybrid LED UV curing system, which can be installed on new presses or retrofit to existing equipment by label and packaging converters. The system combines the latest, high power, low heat LED UV curing technologies with Fujifilm’s ink expertise to improve label production on narrow web presses. It enables traditional UV or water-based flexo presses to be seamlessly converted to LED UV curing, resulting in significant environmental savings, cost and material savings and increased productivity and quality.

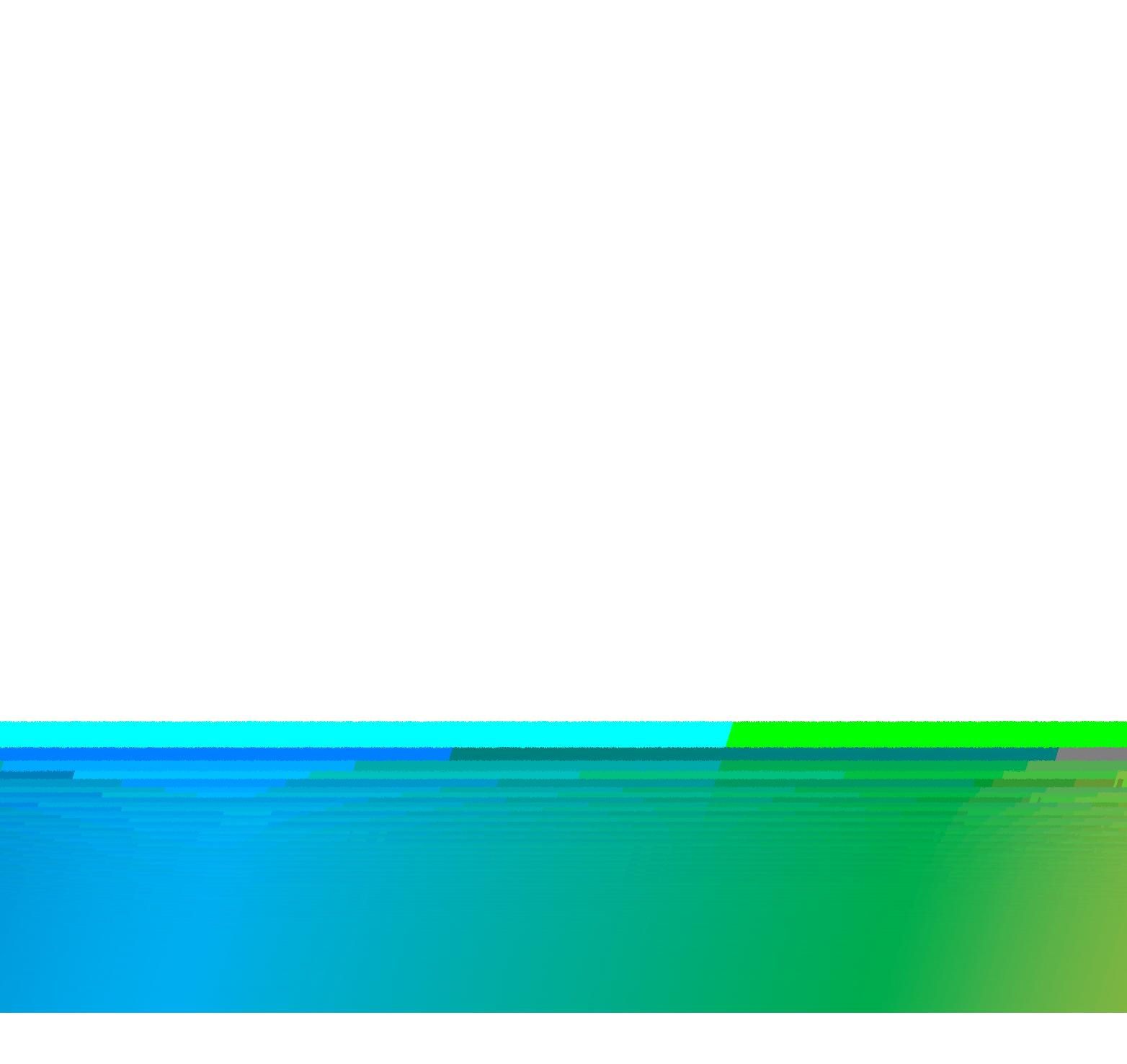
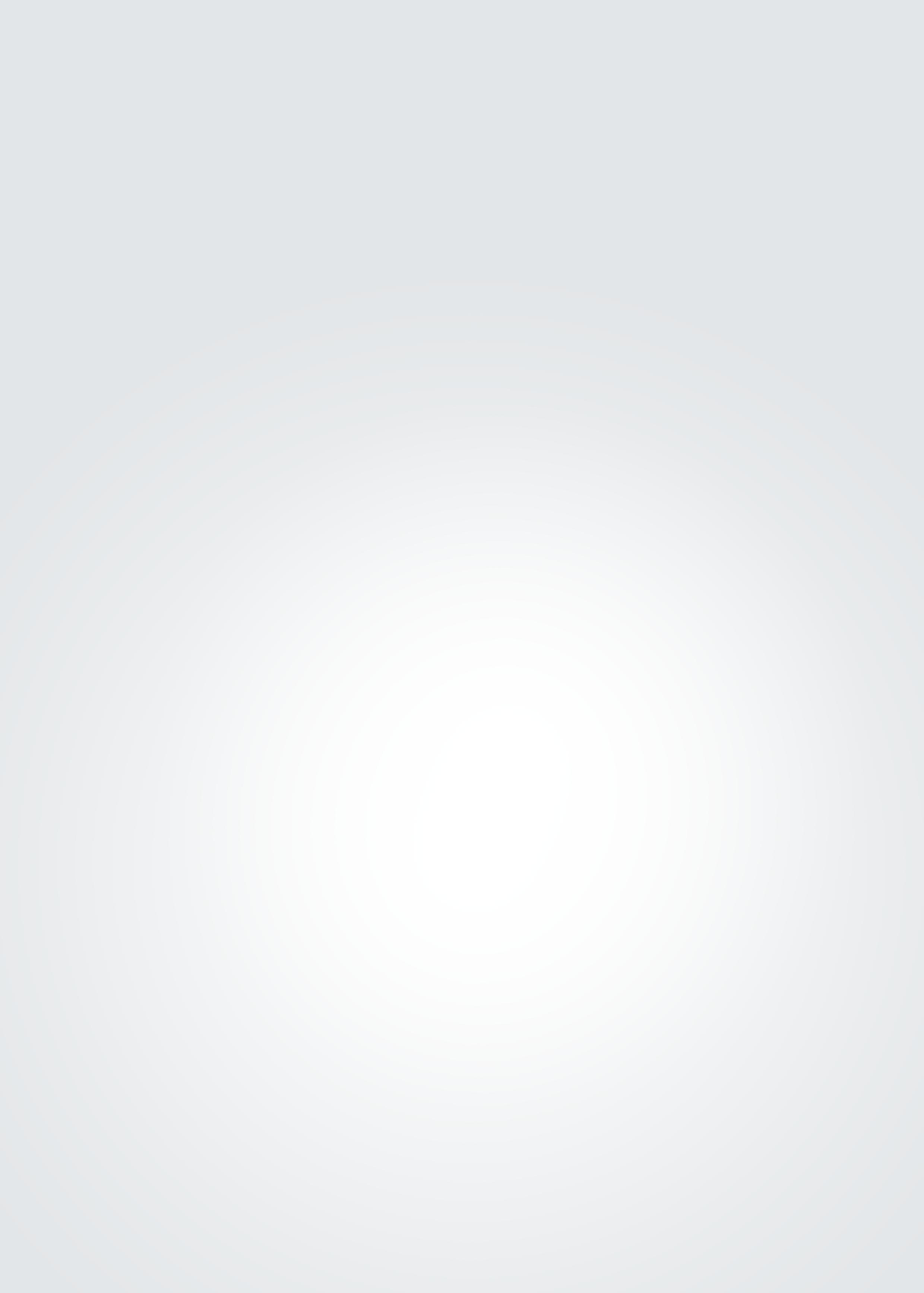
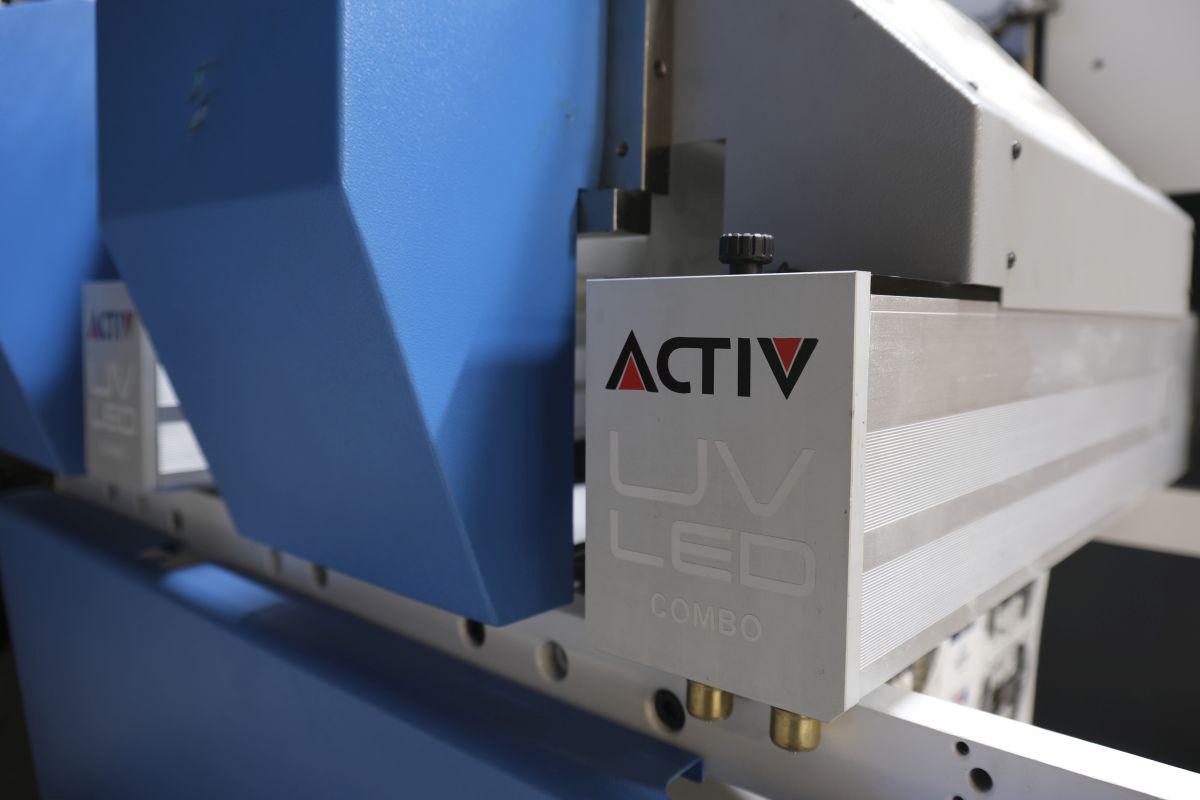
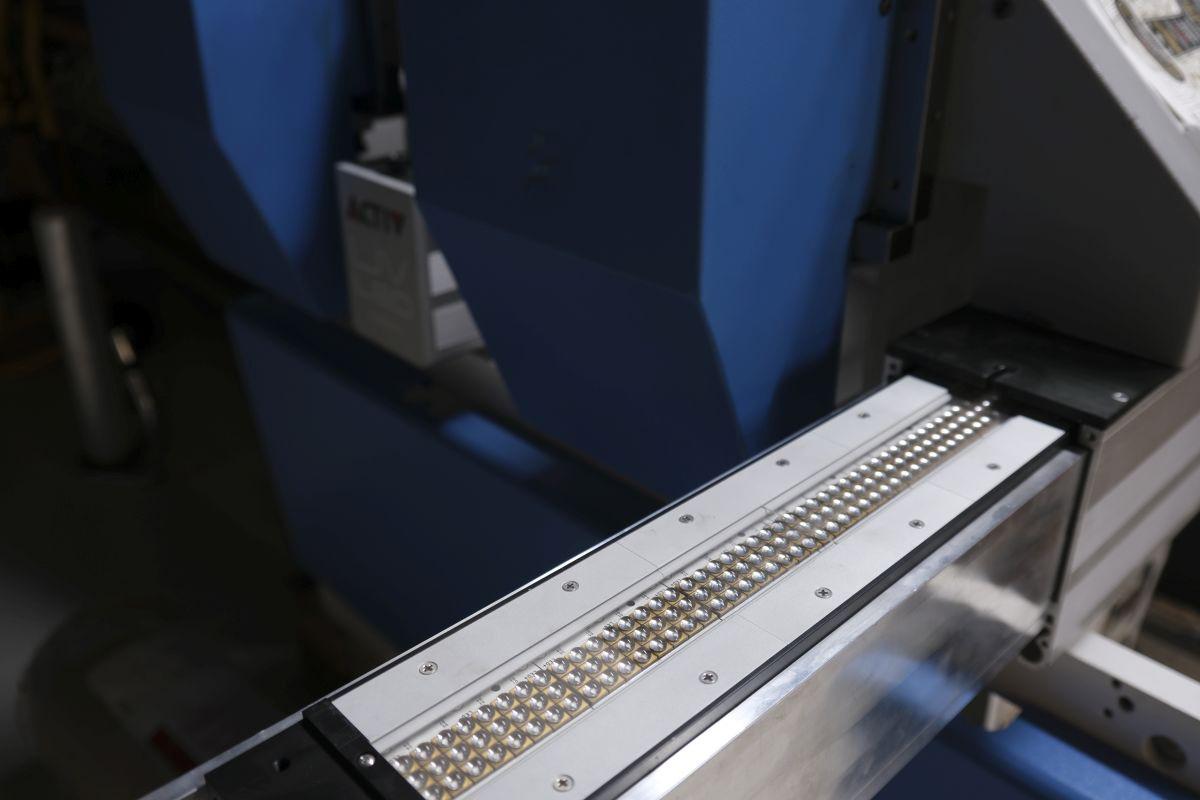
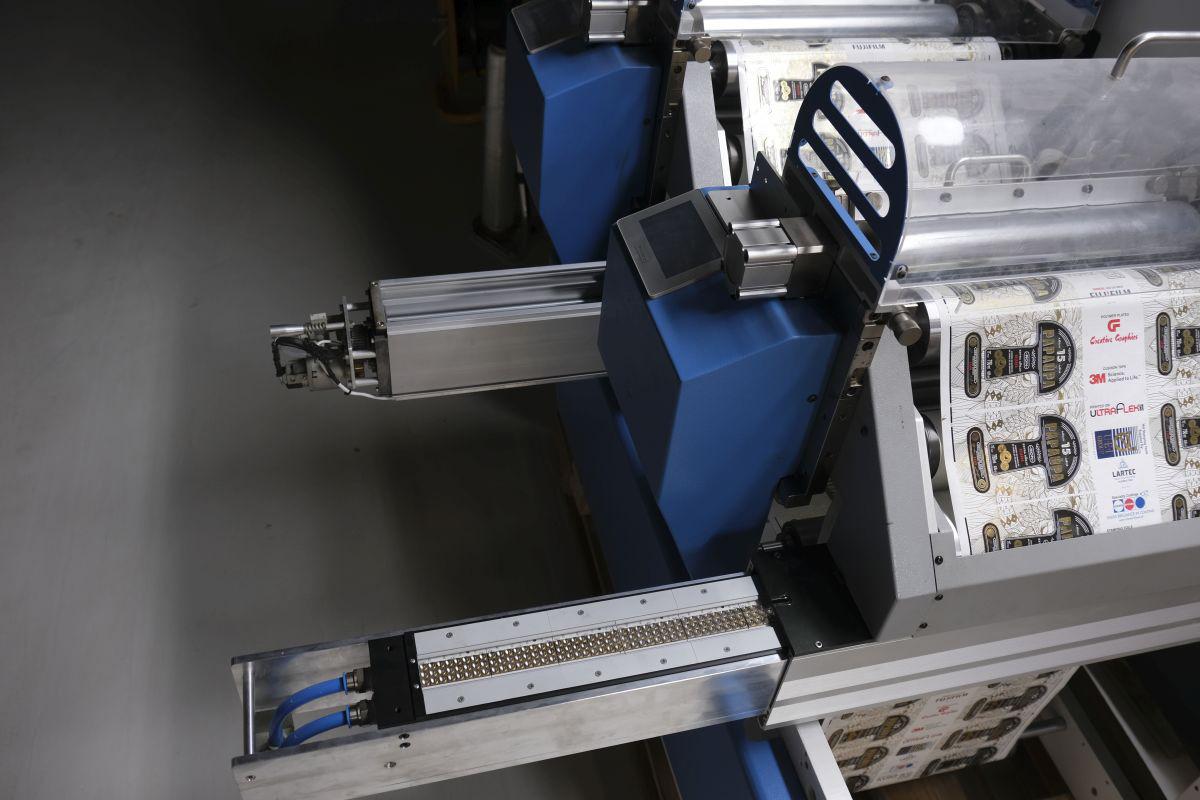
The LED lamp system and Sericol Flexo JJ ink range have been developed in harmony to ensure optimal performance. The system’s hybrid design has the added benefit of conventional UV Arc capability, arming printers with the option to also print with specifically developed and unique conventional UV inks.
The Activ Hybrid LED UV curing system offers significant environmental benefits over conventional UV systems. Energy use is drastically reduced, VOCs are eliminated, and less waste is produced. The working environment for operators is also improved, with many undesirable factors eliminated, including heat from the conventional UV lamps, noise and even the smell. Material usage is also reduced, and the system requires less maintenance and labour.
Increased productivity is another significant benefit. Press running speeds are 30-50% faster than a conventional UV system. Shorter job setups and make-ready times are also possible, thanks to improved substrate stability and the elimination of material distortion, and lower press down-time results in additional significant productivity gains.
The system offers more consistent quality as the impact of the heat from the UV lamps is removed, resulting in better registration and less substrate stretching. In addition, colours are vibrant and easy to achieve with Fujifilm’s high performance LED UV inks, and the dramatic reduction in power required for the LED UV lamps, means substantial cost savings can also be made.
Manuel Schrutt, Head of Packaging, Fujifilm Europe comments “We are delighted to be bringing such an innovative product to market. Fujifilm is proud to be the only supplier able to offer both a state of-the-art LED curing system and a high performance LED ink range to the label and packaging industry.
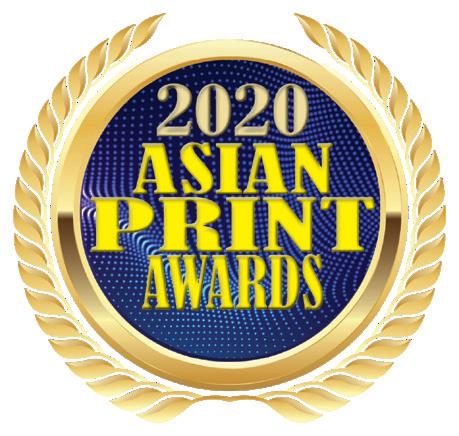
The Activ system takes advantage of the very latest LED UV curing technologies, along with Fujifilm’s ink expertise, to deliver a reliable industrial curing system with none of the disadvantages of higher power and higher temperature conventional UV lamps.”
2022 ASIAN PRINT AWARDS
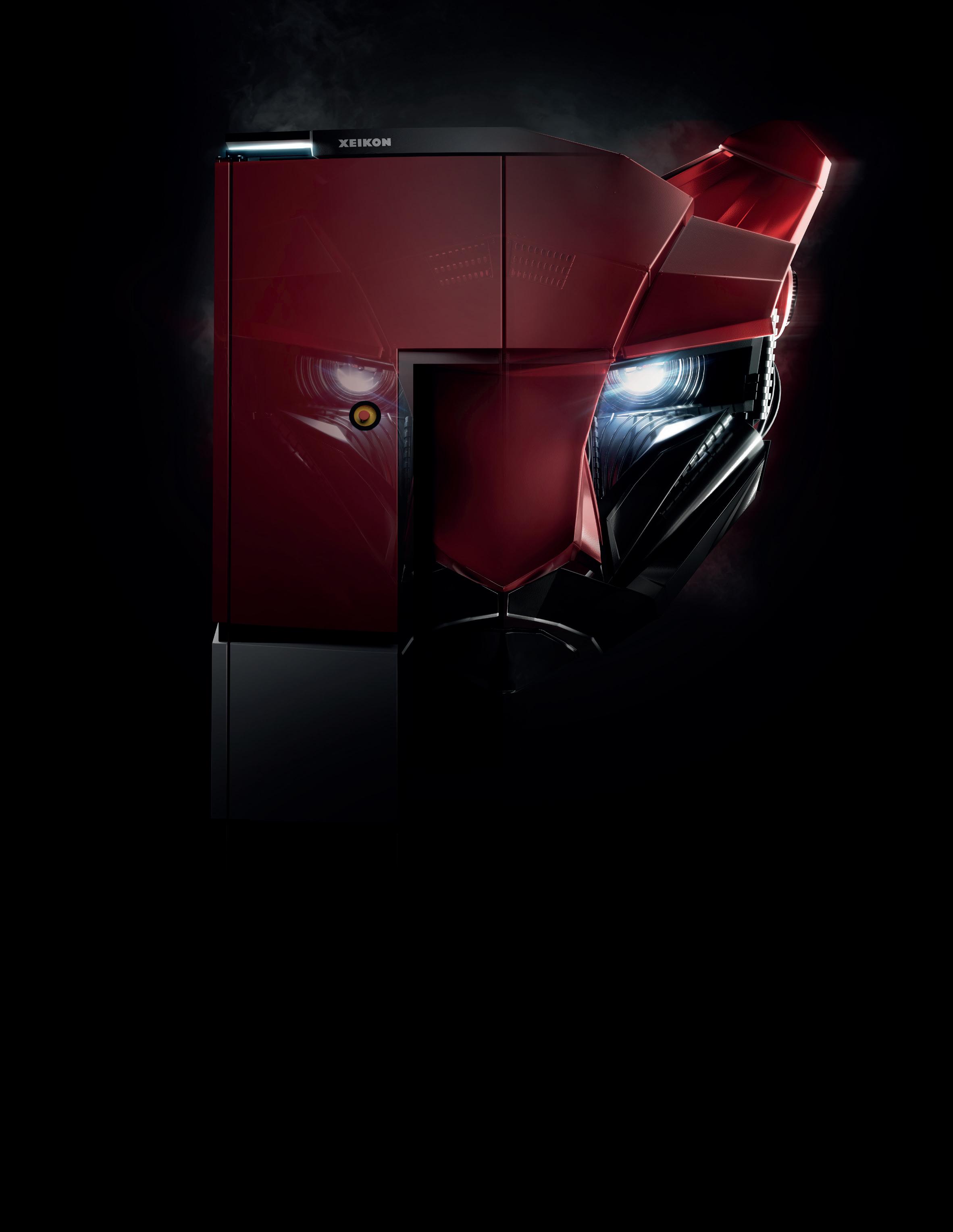