
19 minute read
to Marketing Vehicle How Digital Inkjet Printing is Creating New Possibilities News from around Asia and the world
Impact Retail becomes world’s first company to invest in Onset X1 HS from Fujifilm
UK retail and shopper marketing agency upgrades from Onset X1 to the automated Onset X1 HS solution to further increase already impressive production speeds
A leader in the production of high quality, luxury retail displays for some of the world’s leading brands, Leicester-based Impact Retail prides itself on a strategically-driven and creative mindset. Its 76-strong team includes designers and project managers who have helped many companies enhance their brands with striking visual displays.
Impact Retail had spent many years outsourcing its digital print work – but in March of last year, they invested in Fujifilm’s Onset X1. Impressed with the results, the company soon became a BETA test site for the new, automated Onset X1 HS solution and following two months of successful testing, Impact Retail has now become the first company in the world to invest in the Onset X1 HS.
“Due to the nature of the brands we work with, the quality of our finished products is critical to everything we do,” says Westley Allen, Print Manager at Impact Retail. “Reducing lead times is also very important, to ensure that we always support our clients to achieve challenging in-store launch dates. Up until mid-2020, we had outsourced the vast majority of our print work, but we decided we wanted to have more control over quality and lead times and looked into options to bring it in-house. We ultimately felt that the first few machines we looked at lacked the set up and print speed levels we needed, and once that became clear, the Onset was really the only option.
“We could immediately see that the Onset X1 could deliver on the print quality front and it certainly ticked the speed box too. We did a site visit to Inca Digital’s Cambridge facility to see the Onset in action for ourselves – from then on, we were sold.
“This was by far the biggest CapEx we’d ever undertaken as a business – so it was not a decision we took lightly, but the speed and quality were of such a high standard that we were confident it was a good strategic long-term investment.”
Covid-19 delayed the installation of the Onset X1 at Impact Retail, which was initially planned for March 2020, with the machine fully installed in July. “We were blown away by the quality it produced and the speed it worked at, and were immediately able to adjust our workflow, reducing lead times and increasing the flexibility of our scheduling,” continues Allen.
With a strong relationship now formed, Impact Retail agreed in October 2020 to be a test site for the more advanced, automated Onset X1 HS. “Given how well things had gone, we were very much open to incorporating robotics onto the X1 to boost speeds still further,” says Allen. “It already ran fast, but we felt that if we could produce the same quality print even faster, we were looking at a game-changer. Seeing it in action, we were immediately impressed.
The automatic unloading of substrates greatly reduces set up times and the versatility in terms of media the robotics can handle is very impressive.”
Impact Retail’s full investment in the Onset X1 HS was finalised in December, and the company is delighted with the results, declaring the machine a huge success. “Combining the technology with a strategic change in working patterns, we have now doubled production capacity. This means we can now work with more clients, more brands and still provide the same exceptional service we pride ourselves on.
“This investment also enables us to venture into more bespoke work, smaller volume production runs and projects that require faster turnaround times that may have been challenging to provide previously.
“Initially, we were printing to display and fluted boards for the temporary display side of the business. We’re now broadening the range of substrates and applications, allowing us to print even more of our premium retail display work in-house.
“Investing in the Onset X1 HS is the single biggest investment this company has ever made and we can safely say it has transformed our business. It’s one of the best things we’ve ever done. We had originally envisaged the Onset taking on around 80% of the digital print jobs we were outsourcing – with the remaining 20% and all our litho work continuing to be outsourced. But it has exceeded our expectations massively. We have, in fact, now brought all of our digital print and litho work in-house – with the exception of a few speciality print jobs – and we’re printing more than double the volume we’d anticipated. When business gets
back up to pre-pandemic levels – we’ll do even more.”
Allen also has high praise for the staff who helped to get the Onset X1 HS up and running: “The teams at Fujifilm and Inca have been great. Everyone we have dealt with has been extremely helpful, very knowledgeable and patient with us throughout the process.”
Heidelberg‘s digital ecosystem given the name “Heidelberg Plus”
Heidelberg is taking the digitization of its customer relationships incorporating useful value-added
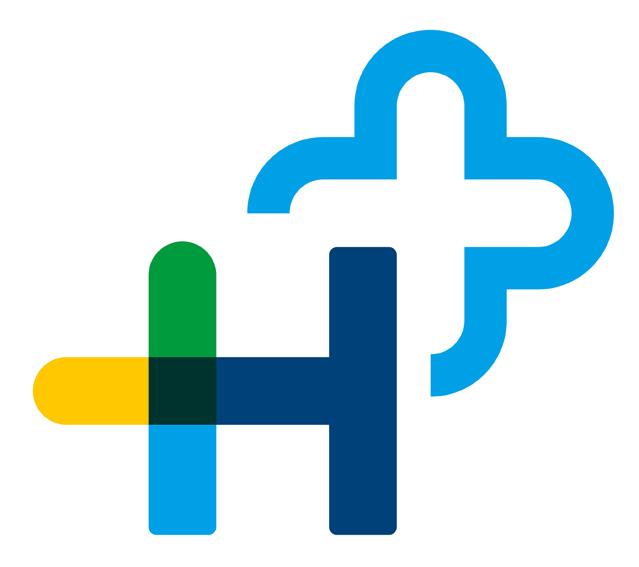
services to the next level.
The company is combining all elements of the Heidelberg ecosystem in its new “Heidelberg Plus” digital customer portal. This includes everything from Internet presence with website and eShop to various performance report, monitoring, and service applications in the production sector and access to instructional videos plus white papers covering technical aspects and applications.
Developments in the areas of cloud technology, IoT, big data, and AI have created new possibilities that Heidelberg will now be systematically harnessing to offer customers further added value. Examples include developing the first AIbased applications to advise them interactively on how they can optimize their own operations, with Heidelberg leveraging and supplying its big data expertise. In the future, customers will be able to access the entire digital world at Heidelberg using a single sign-on.
“Digitized customer relationships coupled with attractive added-value services are the key to establishing collaborative business relationships with customers in our digital world. Our aim is for the Heidelberg Plus ecosystem to simplify the way we work with our customers and offer them more added value,” explains Ludwig Allgoewer, Head of Sales and Marketing at Heidelberg. benefits for our customers,” he adds.
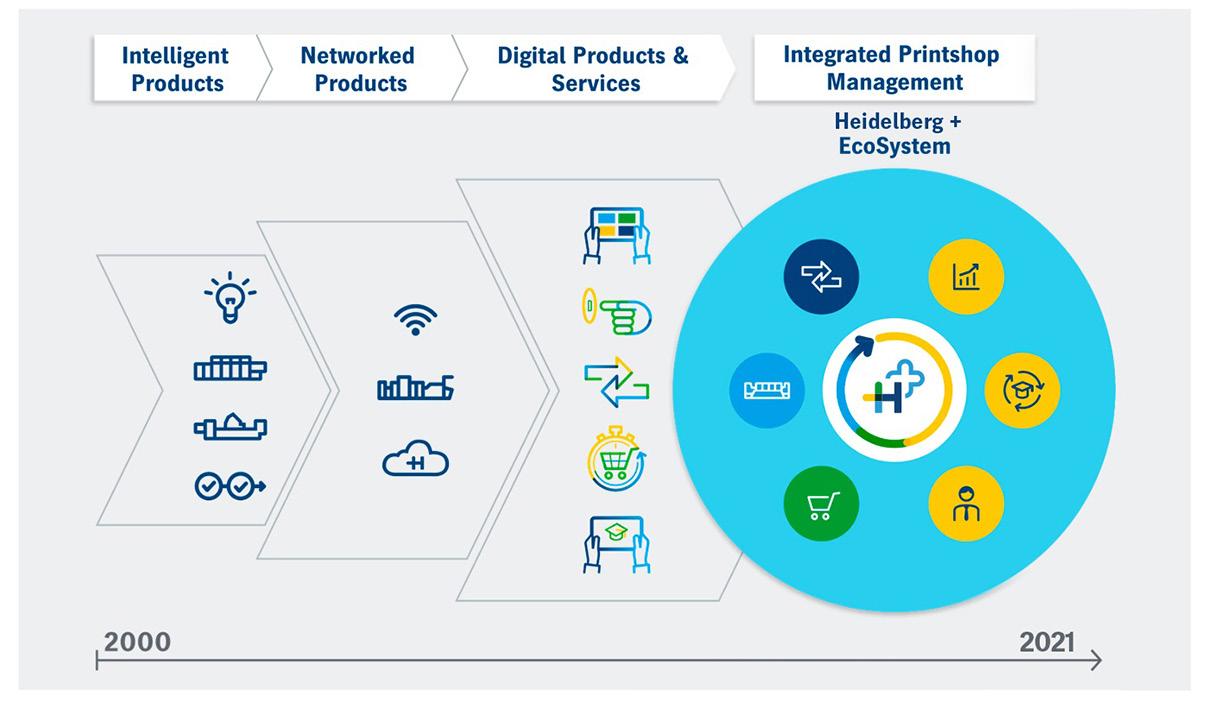
The company will soon be unveiling the new Heidelberg Plus ecosystem to the public – at the China Print trade show this summer. In the fall, it will then be showcased at the Print Media Centers in Germany, the United States, Japan, and Brazil.
Heidelberg is thus combining existing applications with new services for customers. In the future, a single point of access is all users will need for a complete overview of all information and tools, networked functions, and the entire Heidelberg service portfolio. This will make it quick and easy to obtain information, purchase items (eShop), and monitor operations.
Fully recyclable plastic films approved for HP Indigo presses
The new digitally printed packaging solution allows brands to personalize their environmentally friendly packaging with HP Indigo’s printing capabilities
Over 1,600 print shops already use Heidelberg Assistant (HDA) to access their production data. To obtain the relevant services, they need to be registered or have purchased specific services (e.g. Maintenance Manager) as a contract customer.
“What is already impressing users more than anything is the option of using mobile devices to monitor machine operation, purchase consumables, or create service tickets. Regular HDA users range from large businesses with sites located in dozens of different countries to SMEs with just one site,” says Allgoewer, summarizing the customer benefits. “Key elements of the ecosystem such as HDA and the eShop have already developed very encouragingly. By merging these and other existing applications, and also integrating new ones, we will further enhance the In collaboration with HP Indigo, Polysack has validated its packaging films for printing on HP Indigo digital presses.
Polysack is a green-tech manufacturer of plastic film products for flexible packaging and high-shrink labels. According to the company, its Pack’N’Cycle plastic film is 100% recyclable. The company added that some 9% of all plastic is recycled and that “most “recyclable” plastic is not actually recycled or fully recyclable”.
“The ability to combine our 100-percent recyclable film with HP Indigo’s printing capabilities allows businesses to create packaging that fits their brand while remaining environmentally conscious,” said Yanir Aharonson, CEO of Polysack. “Plastic waste is a major environmental problem, and we’re glad to help make the world a bit more green.”
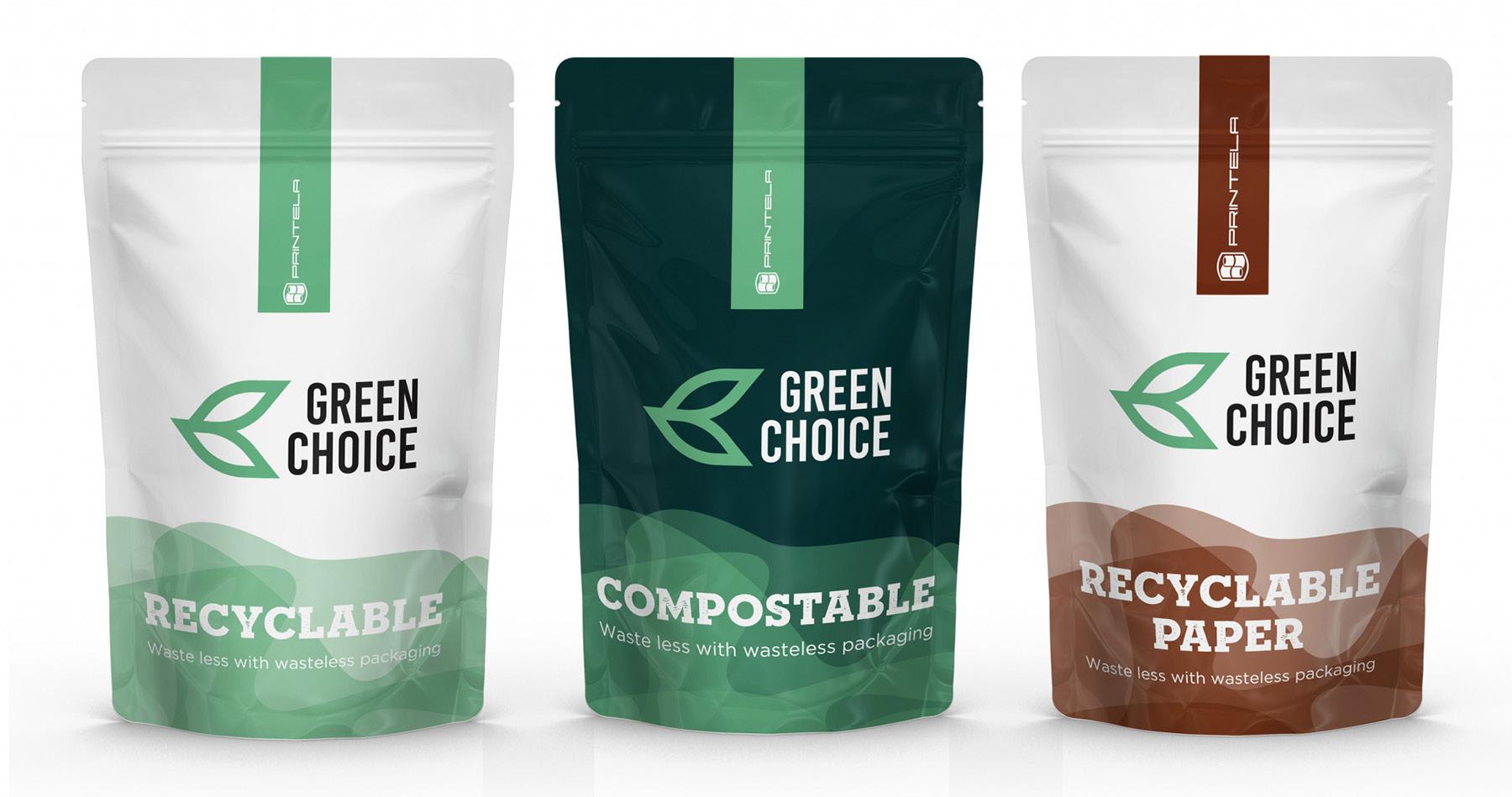
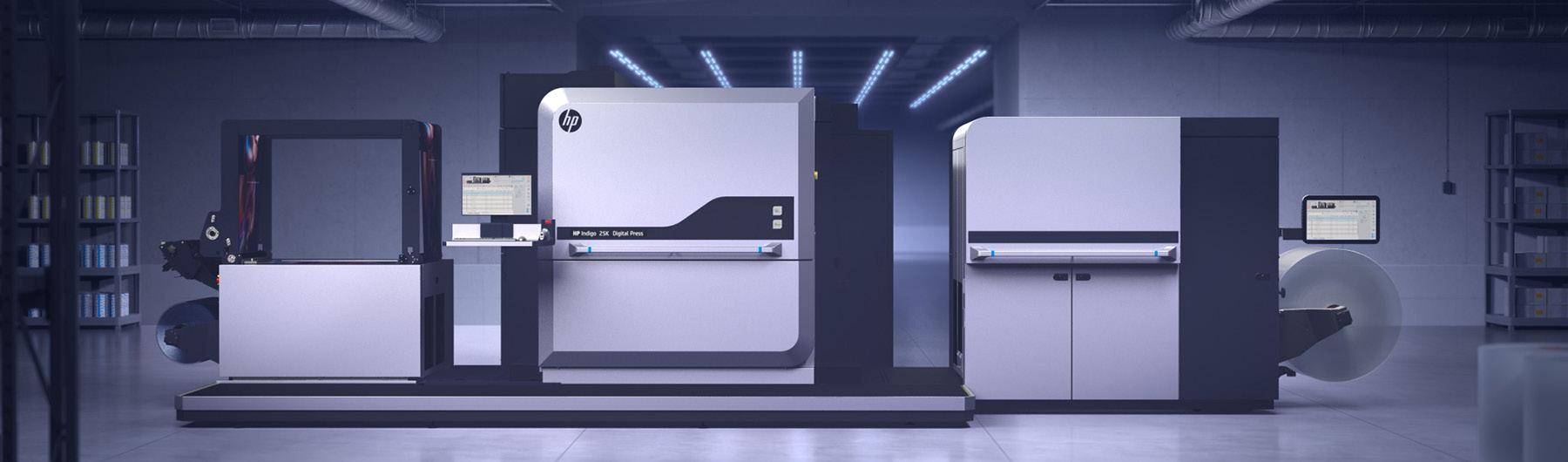
Polysack’s film can replace 70 to 80% of unrecyclable plastic to fully recyclable packaging without increasing costs, modifying people’s usage habits, or needing to rebuild the infrastructure for the package production.
“We are excited to help brands find new packaging options for their products to continue to improve their sustainability profile,” said Yair Gellis, head of Flexible Packaging development at HP Indigo, “The HP Indigo digital printing solution for flexible packaging offers brands sustainability advantages including lower waste.”
XSYS announces the launch of nyloflex® FTM Digital flexo plate for printing with water-based inks
• Suitable for printing on paper substrates to meet sustainability demands • Enables printers to switch from solvent to water-based inks • Offers superior ink laydown and reduced costs
The new nyloflex® FTM Digital plate with inherent flat top dots has been developed specifically for flexographic printing with water-based inks on different grades of paper substrates.
The trigger for the development of this new plate solution is the acceleration in the demand for more environmentally friendly packaging production. As the market moves towards more sustainable substrates in response to those demands, XSYS is introducing the nyloflex® FTM Digital plate which enables printers to use water-based inks on coated and uncoated paper for aseptic food packaging and corrugated preprint liner.
“This latest addition to the nyloflex® plate portfolio will have a broad appeal for printers serving different segments of the packaging production wishing to move to a more sustainable operation, but still retain the ability to produce the highest quality products,” said Simon Top, Product Manager at XSYS. “The nyloflex® FTM Digital will help to fulfil the brand owners’ sustainability requirements by allowing printers to switch from printing on plastic film materials to printing on paper substrates with water-based inks.”
The nyloflex® FTM Digital is a medium hard plate with a smooth surface, bringing a good ink transfer and ink laydown out of the box and capable of reproducing sophisticated surface screenings in case this is required. With no need for additional equipment or auxiliaries, the plate can be exposed in existing systems with standard tube lights or LED UV-A light exposure, before solvent processing.
XSYS innovative inherent flat top dot technology ensures minimum dot wear and significantly less dot gain compared to round top dot plates, thereby also greatly improving press uptimes to reduce costs and start-up waste in the press room. Featuring advanced dot sharpening, the nyloflex® FTM Digital presents fine highlights and a high solid ink density in print, increasing the shelf appeal of the final product.
“The nyloflex® FTM Digital can be considered as the flat top dot counterpart of our well known nyloflex® ACT Digital plate,” explained Top. “The plate enables printers to easily tackle both coated and uncoated papers without the need to use two different plate types. In the past, a hard plate like the nyloflex® ACE UP and medium hard plate like nyloflex® ACT were often combined to achieve the optimum result. At one customer case, we were able to reduce
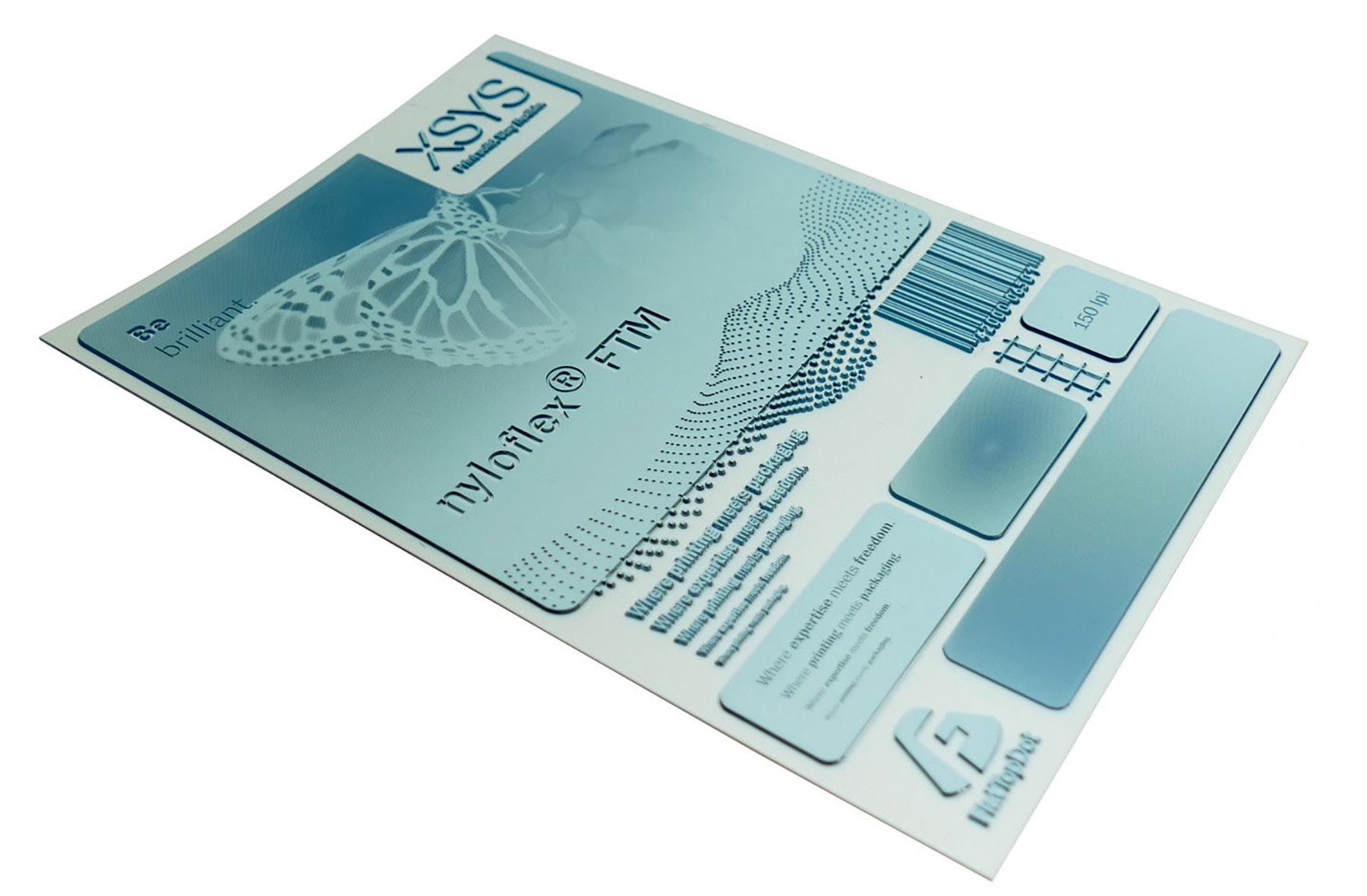
this complexity for up to 60% of the print jobs by using the nyloflex® FTM Digital.” An additional benefit is the better plate filling that could be achieved and thereby reducing the plate waste and total plate cost in the plate making process.
nyloflex® FTM Digital plates are commercially available in 1.14 mm (0.045 in) to 2.84 mm (0.112 in) thicknesses and in varying plate sizes. The nyloflex® FTM Digital plate material will be available for shipment as of May 31, 2021.
“As the optimum choice for long highquality print runs on more sustainable substrates, the nyloflex® FTM Digital is the perfect response to the pressure from the market to find solutions that are better for the environment, but also cost efficient,” Simon Top concluded.
Brand-New Premium Packaging Plant in Gdansk, Poland, Has SWEDBRAND Well-Positioned to Address Luxury Brand Requirements
SWEDBRAND Group, the packaging partner to some of the world’s most iconic brands, today announced the opening of its brand-new converting plant in Poland, Swedbrand Poland Sp z o.o., for premium customized rigid boxes for luxury products. Supported by a global production network of owned and partner-run facilities, the state-of-the-art Gdansk plant is operated by experienced staff and is able to deliver significantly reduced cost and time for intra-Europe delivery. The facility is managed by Bogdan Putko, who has 35 years of experience in the Polish packaging market and has worked with many global brands.
“The company has well-established packaging capabilities in China and Viet Nam and began looking for opportunities to initiate production in Europe as well about two years ago,” said Zaid Bunni, co-founder of the SWEDBRAND Group. “This seems prescient today in light of the disruptions brought on by the pandemic and the instability in Asian markets. We are especially pleased to have Bogdan join our team and bring his extensive knowledge of both packaging and the Polish printing/ converting environment as we built out our new factory.”
Bunni points out that the Gdansk factory, which is a highly automated state-of-the-art converting operation for premium rigid boxes, brings a number of benefits to brands requirement rigid box production for use in Europe.
Plant manager Bogdan Putko adds, “We’ve seen dramatic increases in both time and cost for shipping from China to Europe. While manufacturing time and labor costs are somewhat higher in Poland, it can take four to five weeks just to secure a 40-foot container in China, and then five to seven weeks to ship it to Europe. In addition, just in the last few months shipping costs have increased by a factor of four or five, from US$2,000 for a 40-foot container to as much as US$10,000. Our shipping costs per truckload from Poland to Germany, for example, are between €850 and €1,300. This way the delivery can be accomplished in as little as three days.”
These reduced shipping fees lead to a more competitive overall cost structure for the premium rigid boxes. With regards to brands, these premium boxes are important for communicating the respective brand image and increasing their luxury product’s shelf appeal, while protecting often fragile contents at the same time. In addition, being able to get products to the shelves up to a month earlier than previously possible results in a significant revenue opportunity for brands and retailers.
“We have just completed putting the finishing touches on our factory and are now entering full production phase,” Putko added. “We also offer brands a unique opportunity for a virtual factory tour in light of pandemic conditions that are still restricting travel. The virtual tour is designed to showcase all aspects of the factory and provide brands with the confidence that we can provide reliable and timely service. In addition, the Gdansk factory addresses the need of many of the world’s most well-known brands to diversify risk by moving all or some of their packaging converting from Asia to Europe.”
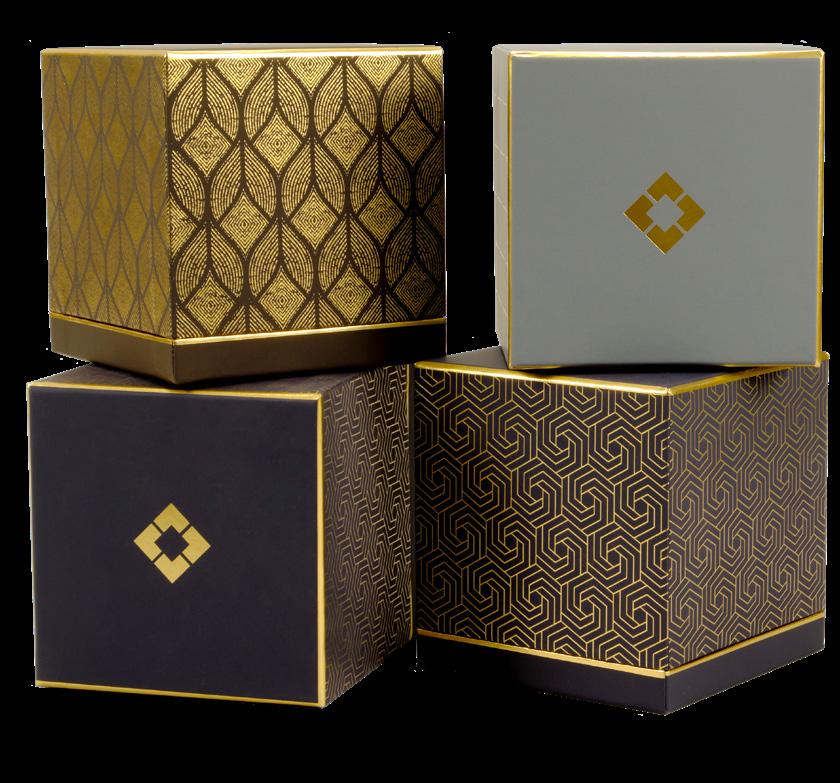
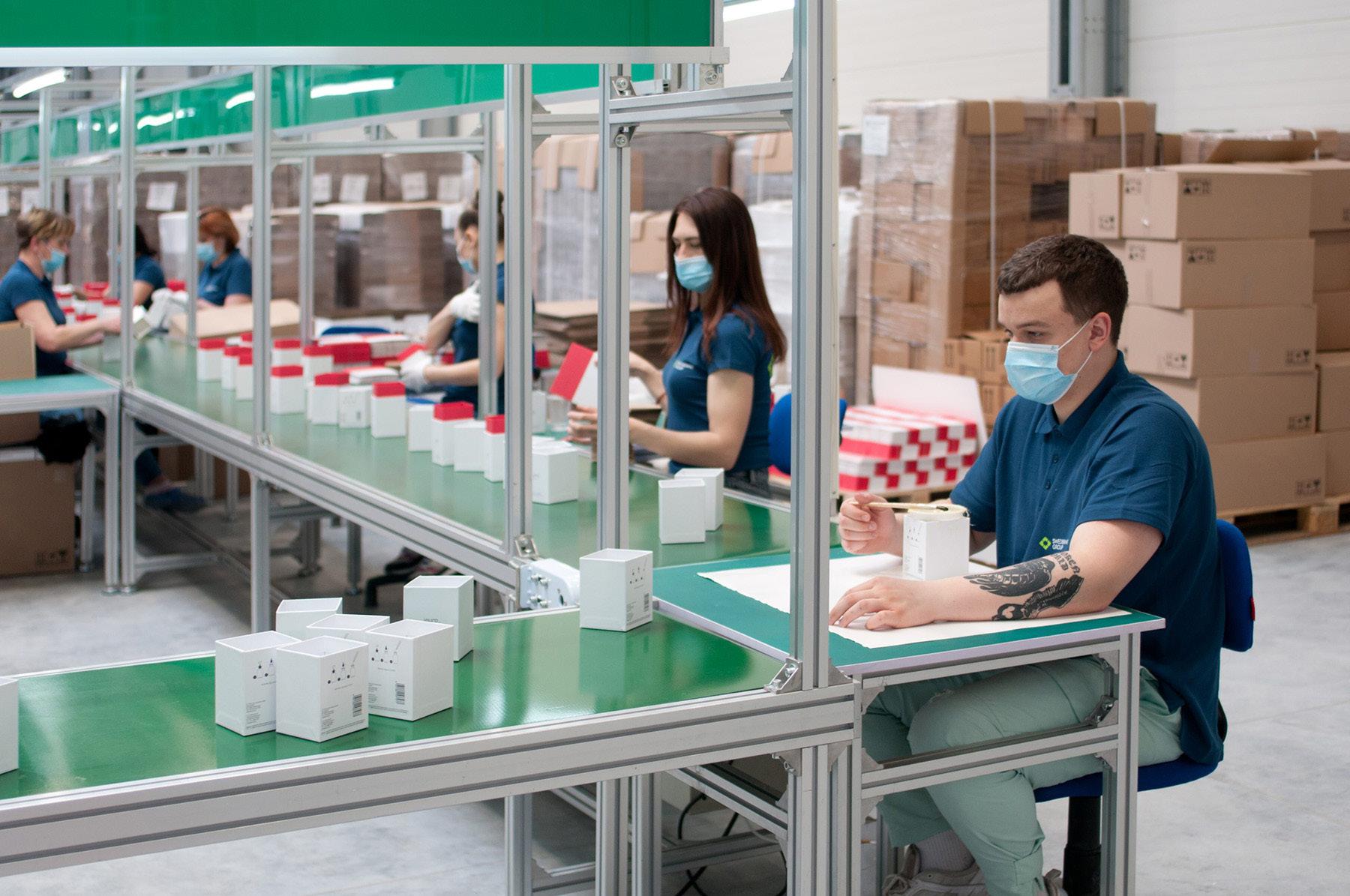
successfully completed the beta program for its revolutionary, sustainable and cost-effective metallization technology
ACTEGA Metal Print GmbH today announces that the German print specialist, Kolbe-Coloco Spezialdruck GmbH, has successfully completed the beta program for its revolutionary, sustainable and cost-effective metallization technology, EcoLeaf™. The new ACTEGA technology is enabling Kolbe-Coloco to meet its customers’ sustainability targets for reduced waste, while increasing operating efficiencies and opening the door to new profitable business.
Announced as the world’s first EcoLeaf customer in March 2020, KolbeColoco concluded the ACTEGA beta program in less than 11 months. Installed on the company’s Gallus RCS 430 modular inline labels press, the business is now using the breakthrough EcoLeaf technology for paid commercial jobs. Representing 20% of all label jobs it produces, and as part of a phased transition, the business is now gradually moving all its foil-based work to its new EcoLeaf solution.
Stefan Klinksiek, Kolbe-Coloco’s CEO, comments: ‘EcoLeaf is already enabling us to enjoy resource savings and significantly less waste. What’s more, the ACTEGA technology has also become a real catalyst for new business too – brands truly engage with its benefits and see it as a premium service. There’s no doubt that EcoLeaf has provided us with a competitive edge.”
As part of the Hamburg-based printing group, H.O.PERSIEHL, Kolbe- Coloco employs 170 people and is based in Versmold, Germany. The company is renowned for providing superior performance “multi-sensory print finishing”, which delivers selfadhesive labels that better engage the consumer and leads to increased sales. In addition, and as part of its drive towards sustainability best practice, Kolbe-Coloco is now ISO 9001 certified – critical in serving its portfolio of food and beverage and pharmaceutical blue-chip customers.
“Despite the pandemic, the installation of EcoLeaf went very well. After initial alignment of software and hardware, we started the first tests in June and were delighted with the results,” concludes Stefan Klinksiek. “Now that we’ve moved into commercial sales, we predict ROI from Ecoleaf by 2022, with the anticipated need of a second unit in the not-too-distant future.”
In addition to processing all the learnings from its beta program, the team at ACTEGA Metal Print have also redesigned and launched a new outer skin for the EcoLeaf unit. As a result, all new EcoLeaf systems now feature a cover that offers user friendly functionality, superior durability and a style that reflects the cutting-edge nature of the technology. Jan Franz Allerkamp, Managing Director of ACTEGA Metal Print, comments: “We are obviously delighted that Kolbe-Coloco has successfully completed the beta program and that EcoLeaf is making such a positive contribution to their business.”
“While the last 16 months have been a huge global challenge, some trends such as sustainability, smart logistics and local production have further intensified. Brands are actively seeking new processes and new technologies, such as EcoLeaf, to better meet their ambitions – we are proud and excited to support our customers in delivering this for metalized printed labels,” concludes Jan Franz Allerkamp.
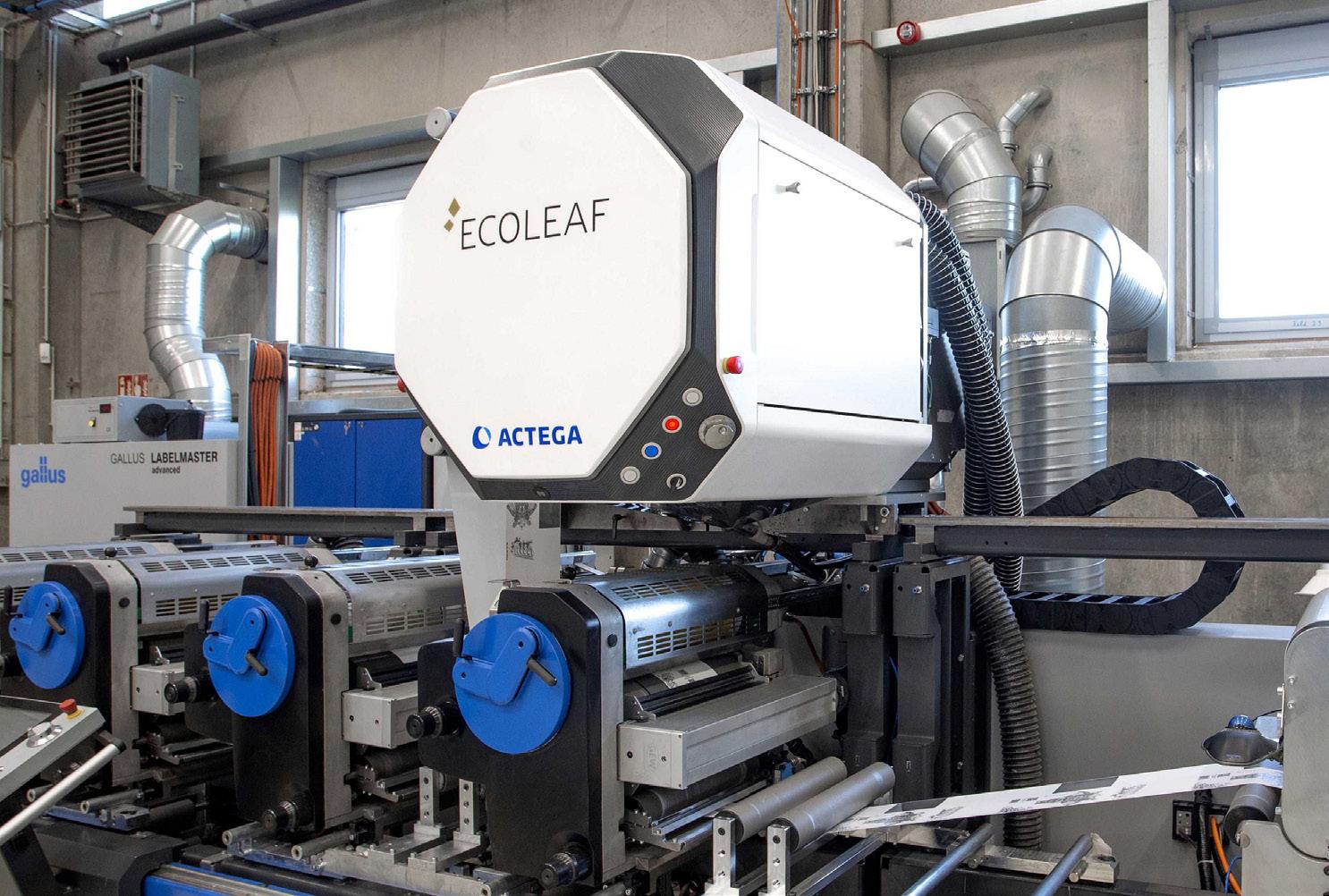
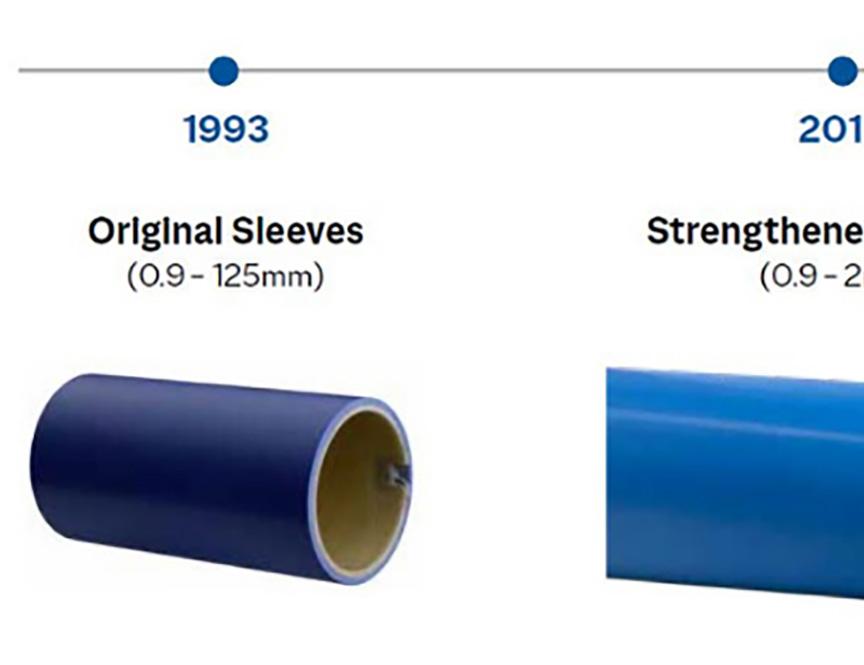
Novotecno enjoys major benefits from next generation rotec® sleeves
By deploying the latest rotec® Blue Light Sleeves from XSYS on its wide web flexo presses, the Spanish fresh produce packaging specialist has been able to reduce downtime and running costs. The next-generation, thinwalled sleeve features a longer-lasting construction that improves efficiencies and productivity in flexo printing production.
Headquartered in Badalona, in Spain, Novotecno S.A. – Grupo Giró is an international innovation leader in packaging systems and products for the fresh fruit and vegetable industry. The company produces tubular nets, labels and films, as well as manufacturing specialised weighing and bagging machinery for the horticultural sector.
The Giró brand is known worldwide for the excellent quality, high reliability and great modularity of its machinery, which allows packers to achieve the best productivity in the market and to respond quickly to new demands from customers.
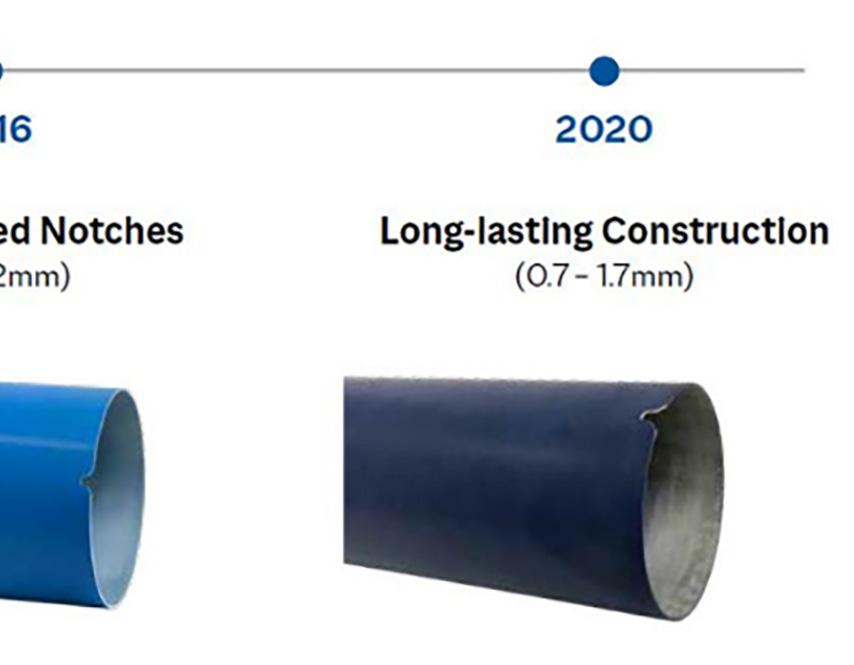
Working with XSYS regional agent LR Flexo, Novotecno has been relying on rotec® Blue Light plate-mounting sleeves for all flexographic printing at the factory in Badalona for more than 10 years. It was the first converter to upgrade to the new long-lasting construction, thin-walled sleeves, and the improvement has been impressive.
“On average, we were ordering approximately 50 rotec® Blue Light Sleeves of this size each year, because they became damaged so quickly. Since switching to the new construction in July 2019, lifetime has doubled, so that amounts to a substantial saving for us,” said Daniel Moreno, Production Manager at Novotecno.
Continuous innovation from XSYS The long-lasting construction rotec® Blue Light Sleeves is the third generation of this thin-walled, plate carrier technology from XSYS Sleeves. Introduced to the market in 2020, the new sleeve offers improved overall stability compared to the original Blue Light Sleeve from the early 1990s. The development builds on the thin-wall technology of the second-generation sleeve from 2016, but is less likely to crack and more cut resistant. It also has a smoother surface than competitive products.
Available in lengths between 250 and 2600mm, the new thin-walled sleeve is offered in a thickness of 0.9 – 1.7mm. It can be combined with various adapters for plate-mounting off press and offers easy and reliable handling of all flexo plate types.
“With the new construction of the thin Blue Lights, the product is more robust. Soon after we started using them, it became clear that the surface is much more resistant and doesn’t crack after a few cuts.” commented Daniel Moreno.
Preferred partner for sleeves The XSYS rotec® product development team is constantly driving innovation to meet the needs of customers and stay ahead of trends. The evolution of the sleeve technology goes hand in hand with the partnerships that have been created over many years.
“Having represented rotec® Sleeves & Adapters for more than 20 years, I am impressed by how easily the rotec® team understood the situation and proposed a new solution for our common customer,” said Lluis Rebled, owner of LR Flexo. “Our partnership with Novotecno is a real success story and it is a clear example of how we work together with customers to help them succeed.”
Commenting on why Novotecno chooses XSYS Sleeves as their supplier, Moreno concluded, “The product quality is excellent, and we know we can rely on XSYS if there are any issues. When we had a specific problem, XSYS and the agent LR Flexo took it seriously and solved it for us quickly. This is the relationship and cooperation we expect with our partners, therefore rotec® is our preferred brand for sleeves.”
For more information about the new XSYS division of the Flint Group, please visit www.xsysglobal.com or contact info@xsysglobal.com.
successfully completed the beta program for its revolutionary, sustainable and cost-effective metallization technology
ACTEGA Metal Print GmbH today announces that the German print specialist, Kolbe-Coloco Spezialdruck GmbH, has successfully completed the beta program for its revolutionary, sustainable and cost-effective
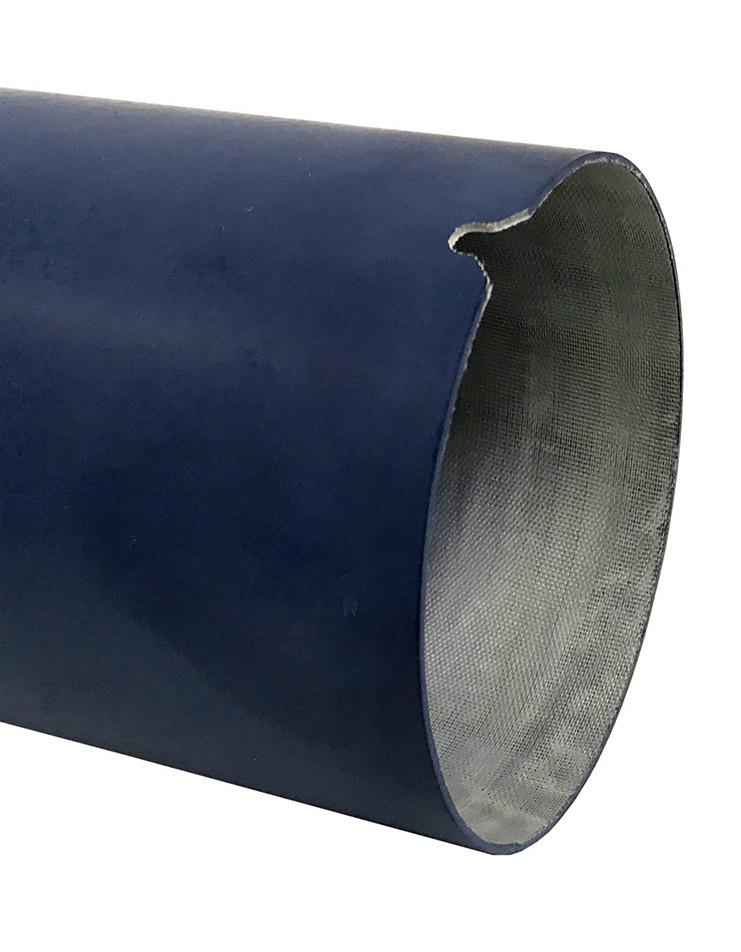


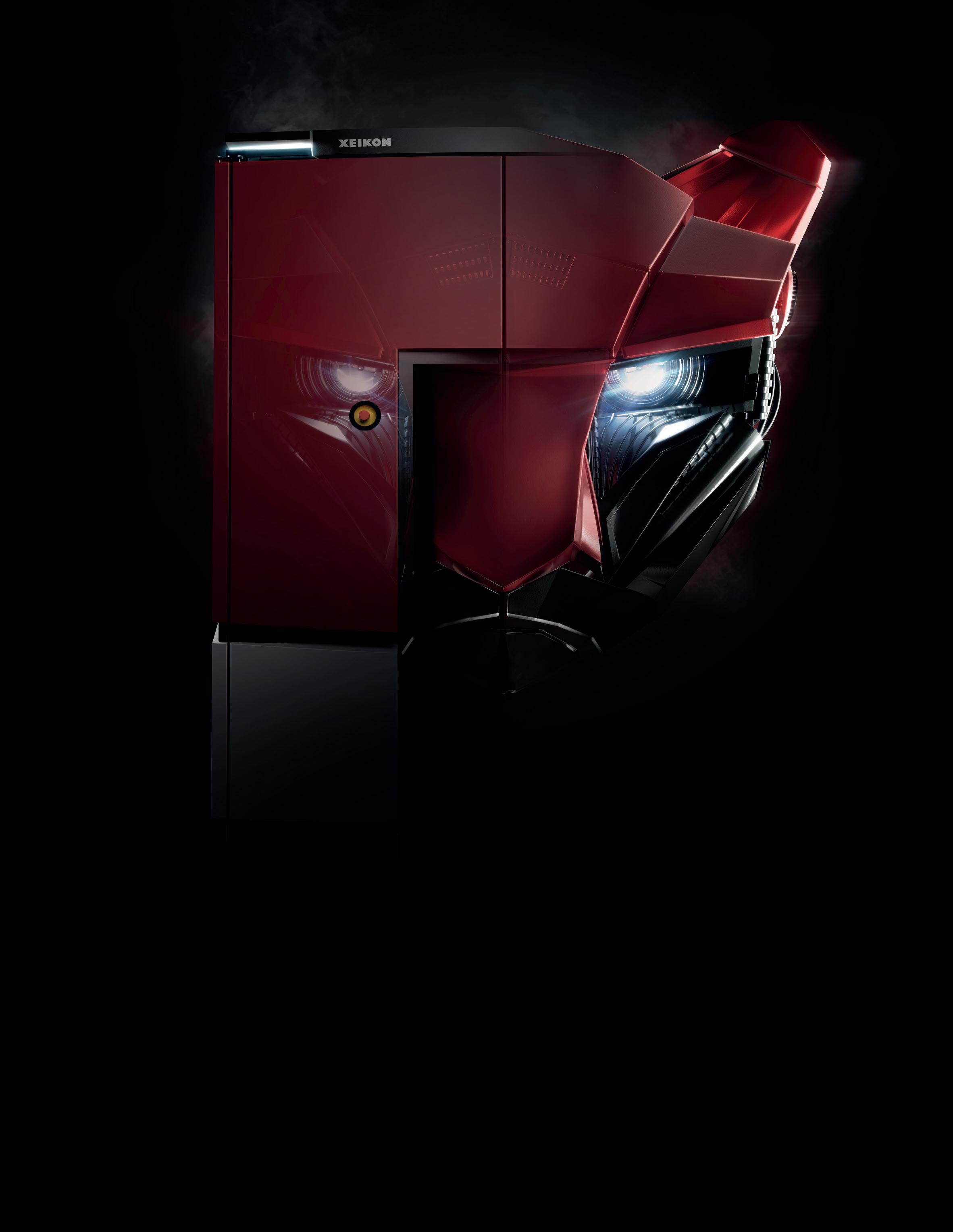