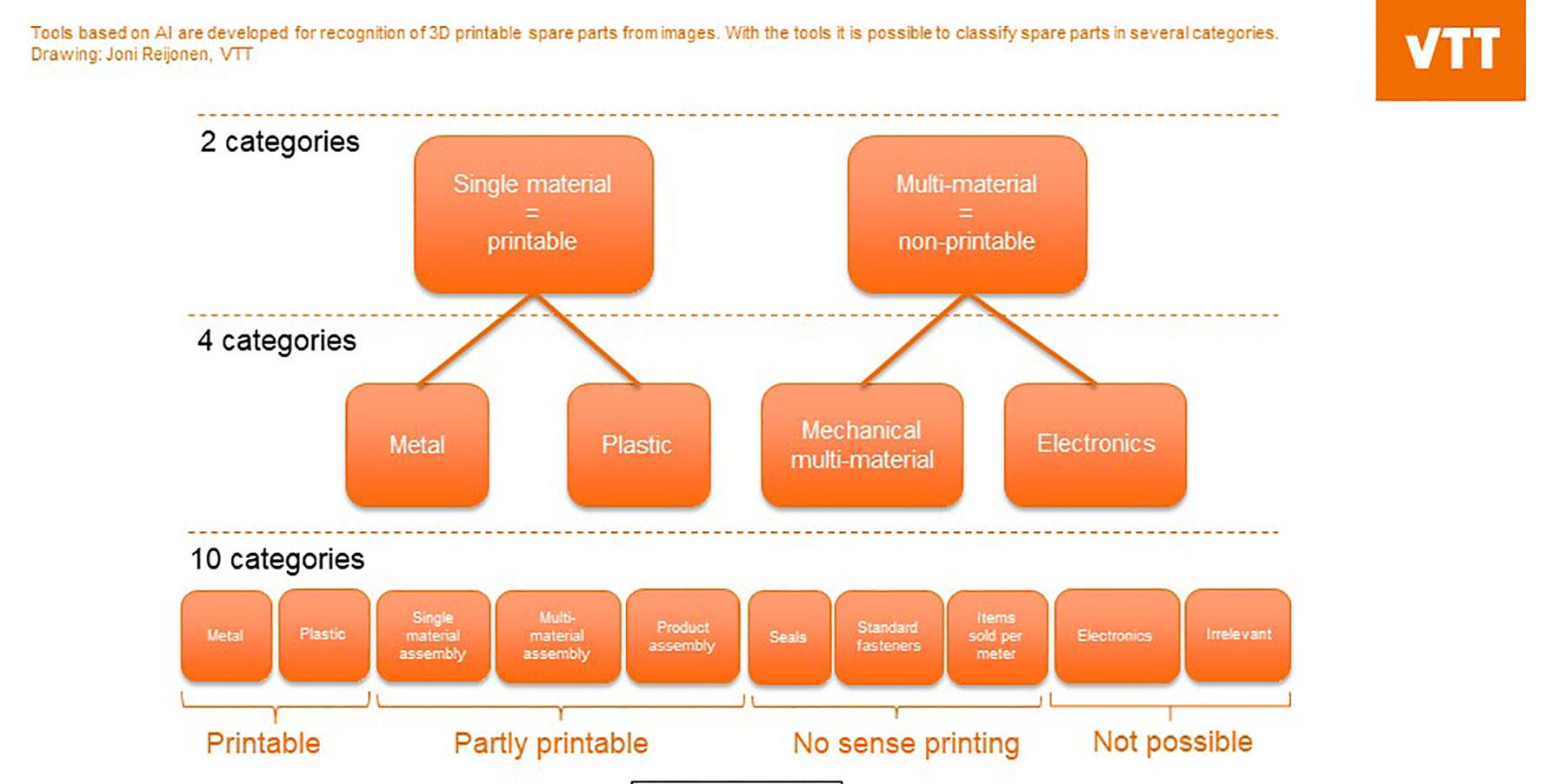
15 minute read
Digitalising and 3D printing spare parts enables
The digitalisation of spare parts is a step towards more sustainable business and reducing the carbon footprint of industry. It also reduces costs and improves the availability of spare parts with quicker access.
Advertisement
VTT and Aalto University have been conducting first-class research for five years now to promote digitalising and 3D printing spare parts.
- We had two extensive research projects where we solved problems related to the introduction of digital spare parts and developed different tools and operating models while working closely with the companies involved in the projects. Many companies have already had successful trials of 3D printing spare parts, and in the next phase, the aim is a wider implementation of digital spare parts, says Senior Scientist Sini Metsä-Kortelainen from VTT.
- The new business from digital spare parts project by VTT and Aalto University is a great example of Finnish research on 3D printing. Companies have huge potential to grow and improve their maintenance business with 3D printing. In the recently completed research project, we identified new ways for industry to make use of additive manufacturing, says Tero Hämeenaho, Department Manager responsible for 3D printing at Etteplan.
Digitalisation of spare parts has significant benefits
Companies that manufacture machinery and equipment are becoming more interested in the digitalisation of spare parts: maintenance services make up a significant part of the business of these companies and spare parts tie up a lot of capital. Companies are particularly facing issues with old equipment that no longer have spare parts available, but repairing them is the sustainable choice both economically and environmentally.
- Since based on digital data, 3D printing makes it possible to produce individual parts or small series quickly and cost-effectively, as there is no need for separate tools such as moulds. Storing digital spare parts does not take up shelf space, and manufacturing can

be carried out according to need and close to the end user. The availability of spare parts is improved, transport distances are shorter, and natural
resources are not wasted on parts that end up on storage shelves indefinitely, says Mika Salmi, Research Director at Aalto University’s ADD Lab.

Comprehensive data on 3D printing materials
The first bottleneck in the introduction of digital spare parts is the difficulty of automatically identifying the parts whose size and shape make it reasonable and economically viable to manufacture them by 3D printing. It has been estimated that it would be profitable to digitalise roughly 10% of all spare parts.
A recent research report presents methods of identifying parts in spare parts libraries that are suitable for 3D printing. For example, one spare parts library can contain 200,000 parts, and methods for examining this data have been developed using artificial intelligence and machine learning.
Another major challenge is to find the right material for a specific spare part among the 3D printing materials available. There are notably fewer 3D printing materials available than for conventional manufacturing

technologies, and in many cases, the properties of printed materials are different from traditional materials. The manufacturing process must take into account the special features of 3D printing, and proper documentation and quality control as well as property testing of the components.
The research report provides extensive data on 3D printing materials and related heat treatments, differences between processes, and corrosion and UV resistance. The report also includes summarised instructions on the documentation of manufacturing and testing critical parts as well as ways to embed intelligence in 3D printed parts, which opens up routes for more efficient condition monitoring and the traceability of parts.
The new business from digital spare parts follow-up project concluded at the end of September 2020. The final report summarises the results of the project and contains links to other project publications that focus more extensively on each research topic.
The project was funded by Business Finland, Kiwa Inspecta Oy, KONE Oyj, Valmet Technologies Oy and Wärtsilä Services Switzerland Ltd. In addition, 3DTech Oy and Etteplan were involved in the consortium and the steering of the project, and they also received funding from Business Finland for their own projects.
EFI launches two new printers for soft signage
The high volume EFI POWER and COLORS printers create profit opportunities in soft signage. EFI introduced two new printers for the high-end, high productivity soft signage market help display graphics producers reach new heights in productivity and extend their capabilities.
The EFI COLORS 340 printer prints at up to 9,149 square feet per hour (in a four-colour x 4 configuration) while providing unmatched colour capabilities for premium-quality soft signage. For even higher-volume production environments, the EFI POWER 340 prints up to 16,835 square feet per hour.
Leveraging technology from EFI Reggiani’s 70+ year legacy of best-inclass fabric printing, the new offerings have the ability to print with higher quality on a wider range of materials than other soft signage inkjet devices, with 100% penetration on both sides of the material. The printers are able to print either direct to fabric or to transfer paper using the same inkset, eliminating the significant cost and downtime related to switching over inks.
“EFI, through our Reggiani division, has decades of experience bringing to market the highest quality in fabric printing in the industry,” said Scott Schinlever, COO, EFI Inkjet. “These two new printers are specifically designed to meet the most stringent quality and productivity needs in soft signage for companies that want to

truly differentiate themselves in a highly competitive marketplace.
With their extreme speed and reliability, the EFI POWER and COLORS printers can often replace multiple soft signage printers, producing more premium signage work with a single footprint.” The new printers follow the market successes with VUTEk FabriVU® soft signage dye sublimation printers. There are more than 250 FabriVU printers installed worldwide.
A new level of quality in premium soft signage The EFI COLORS 340 printer is ideal for many applications, from table throws and pop-up promotional tents to SEG backlits, flags and retail fixtures.
At 11 feet wide with the ability to handle different fabrics up to 450 gr/m2, the printer uses genuine EFI water-based CMYK dispersed dye inks. The printer gives users entrée into an ultra-premium point-ofpurchase category for soft signage, producing smoother colour transitions and ultra-realistic skin tones.
Available with up to 24 printheads, the COLORS 340 offers greater versatility in colour capabilities to print in four-colour x 2, four-colour x 4 or six-colour x 4 configurations, as well as an eight-colour configuration featuring standard CMYK and light CMK colour inks, plus a penetrating agent. The EFI COLORS 340 produces high quality prints at speeds up to 9,149 square feet per hour.
The printer’s 2,400 dots per inch (dpi) resolution with four level grayscale printing and drop sizes from 4 to 18 picoliters can deliver 100% penetration on both sides of the material, making it ideal for the production of national flags. Its precision sticky belt feeding mechanism ensures near-perfect, continuous tone image quality at high speeds with no wrinkle artifacts on a wide range of materials. EFI’s unique continuous ink recirculation system for textile printing improves ink yield, reducing the need to purge while eliminating downtime associated with printhead maintenance.
Extreme POWER meets maximum productivity needs The EFI POWER 340 digital soft signage printer has most of the capabilities of the COLORS 340 but at a faster speed of up to 16,835 square feet per hour.
The POWER 340 is also capable of printing direct-to-fabric or onto transfer paper using genuine EFI water-based CMYK dispersed dye inks. Like the COLORS 340 model, it employs the proven, reliable sticky belt feeding mechanism.
The POWER 340 features up to four colours, in either four-colour x 4 or four-colour x 8 configurations. With its remarkable speeds, users can profit from producing the appropriate quality at the highest speed with a lower total cost of ownership for high-volume demands.
Reduce your footprint, increase your output With these two new solutions, soft signage producers can reduce their production footprint while also increasing their output by replacing multiple, slower devices with a single high-volume, premium-quality production powerhouse.
Both printers employ a powerful EFI Fiery® proServer Premium digital front end, which means operators can take advantage of the ultimate in colour management, job management, and powerful tools for nesting, step and repeat, scaling, cropping, barcode creation and tiling.
Durst launches air disinfection system
Durst announced it is introducing a solution for reducing the viral load in indoor environments, the Durst UVCR Air Disinfection System.
In response to the Covid-19 pandemic, the digital print manufacturer first started production of community masks as a first preventive measure in April. The Durst UVC-R Air Disinfection System is a solution for reducing the viral load in indoor environments.
Over the last few months, Durst has put its expertise in production and UV technology to come up with the Durst UVC-R Air Disinfection System.
In the Durst Labs, the main transmission paths and descent rates of droplets and aerosols that transport virus-containing liquid particles were analyzed, as well as the effectiveness of countermeasures with continuous air exchange and UV irradiation. The solution is the Durst UVC-R, which combines both air exchange and UV irradiation in one system, effectively reducing infectious aerosols, viruses and germs in indoor environments. Through an antiviral membrane, the room air is led into a closed system and irradiated with UV-C light.
The disinfected air is continuously released back into the room through an air outlet.
“We checked the efficiency of the UV-C sources in our laboratories and analyzed the ideal exposure time and volumetric flow," said Christoph Gam-

per, CEO and co-owner of the Durst Group. “An external laboratory for medical technology and disinfectants in Germany is currently in the process of verifying our results. At the same time, the efficiency of the Durst UVCR is tested in real mode with "pseudoviruses" or so-called bacteriophages.

Durst offers the 1st series of the UVC-R as a Limited Edition for preorder. Within the next weeks the entire UVC-R portfolio will be available in a webshop. Start of delivery of the 1st series is planned for early December.
HP and Shutterfly Announce Record HP Indigo Digital Press Rollout to Accelerate Personalized Gift and Photo Printing Markets
HP Inc. (NYSE: HPQ) and Shutterfly, the world’s leading online retailer of personalized products, today announced a landmark expansion of their strategic relationship to deliver next-level productivity to supply the growing ecommerce market of photo gifts and photo products. Shutterfly is investing in more than 60 new high-performance HP Indigo Digital Presses to drive higher productivity for its range of highquality, photo-based and personalized products including photo gifts, photo books, school portraits, holiday cards, and home decor.
The agreement with Shutterfly, the leading US supplier of HP Indigo digital print, is the largest single customer order to date for the HP Graphics business. Now underway, the rollout includes next-generation, high-productivity B2 sized HP Indigo 100K digital presses, high versatility HP Indigo 12000 digital presses, as well as significant investment in web-fed photo presses to transform photo portrait printing to digital.
“Over our 20+ year legacy, Shutterfly has committed to investing in the best and most innovative technology to fuel our business, delivering high-quality products to our customers, hosts and partners,” said Shutterfly Inc.’s chief operating officer Dwayne Black. “This latest upgrade of our HP Indigo fleet continues that investment in quality, productivity and innovation, with significant advancements in speed and automation that help us deliver even higher quality products to our customers, even faster at a time when sharing tangible memories is more important than ever.”
The annual global photo printing and merchandise market is expected to reach a value of $3.117 billion by the end of 2026, with a CAGR of 8.1% during 2021-2026, compared with USD 1.7960 billion in 2019.1
“Today more than ever before, tangible, personalized experiences are becoming more precious. Consumers are looking for quick turnaround, alongside real-to-life photo quality. We at HP Indigo are proud to be Shutterfly’s provider of choice in making this a reality,” said Haim Levit, general manager, HP Indigo.

In this latest wave of installations, Shutterfly is investing across three HP Indigo press generations and formats. Shutterfly was one of the first customer beta sites for the new 29-inch format HP Indigo 100K, engineered for high productivity and nonstop printing while delivering Indigo’s renowned digital offset look and feel. Shutterfly’s new HP Indigo 12000 presses loaded with a value pack deliver higher end prints using a wider

range of inks and materials up to 24 pt, including synthetic, metalized and canvas applications.
The presses will be installed across four manufacturing facilities in Shakopee, Minnesota; Fort Mill, South Carolina; Tempe, Arizona; and Plano, Texas over the next 18 months.
To keep production at the highest level, Shutterfly takes advantage of HP PrintOS, the cloud-based PSP management solution, to monitor productivity of presses in real-time to keep press uptime to a maximum.
NiceLabel launches new version of labeling management portfolio to streamline production of supply chain documents
NiceLabel, a leading global developer of label design software and label management systems, has launched a new version of its label management solutions portfolio: version, 2019.3. The new software update will enable organizations to use just a single platform for designing and printing their labels and supply chain documents (something many struggled with before), thereby saving them time and costs and streamlining their whole production process. The NiceLabel software previously offered out-of-the-box label design, allowing business users to quickly and easily design and print labels. The new version builds on this capability, enabling users, especially those working in factories or warehouses, to seamlessly design and print related supply chain documents, including delivery notes, pick lists, packing slips and invoices, from a single platform.
“As always, we are strongly focused on listening closely to customers and adapting our labeling solutions to meet their needs,” said Ken Moir, VP of Marketing NiceLabel. “We know it has been possible to design and print these documents before, but it has been complex requiring people with the highest levels of technical skills. With the latest version, we have made it easy for users to design these documents.”
“The result is something that we believe is a real differentiator in the marketplace,” added Moir, “a userfriendly way for businesses to design and print their labels and supply chain documents all in one label management system.”
The 2019.3 release of the NiceLabel software also features a connector to cloud-based software from Workday. This is an example of a cloud-to-cloud integration that also supports cloud connected printers (IoT printing). Businesses that adopt this functionality can print driverless, completely eliminate their on-premise labeling footprint and save costs as a result. Their existing Workday process remains the same, but they gain the benefits of streamlined label printing through NiceLabel Label Cloud.
“With any cloud-based system, there is an expectation of ease of integration with other cloud-based applications,” continued Moir. “Users anticipate that Label Cloud will be able to interact seamlessly with other cloud-based applications. That’s exactly what this new release delivers through its connectors and cloud-to-cloud integration capability.”
The release also includes enhancements to NiceLabel’s SAP advanced business application programming


(ABAP) package including the ability to print supply chain documents more easily; and exporting data sources for streamlined design.
The new 2019.3 release additionally features a web-based manager for the NiceLabel integration system that allows users to centrally manage all integrations.
In parallel with the 2019.3 launch, NiceLabel is also introducing a brandnew edition of Label Cloud. Label Cloud Compliance is vertically aimed at regulated companies including medical device manufacturers, pharmaceuticals
businesses and chemicals companies which require a compliant labeling process to meet evolving US Food and Drug Administration (FDA) and European Union (EU) regulatory requirements.
Next generation direct to garment technology available
heightened productivity, best-in-class operation and ease of use with the launch of the Ricoh Ri 2000 Direct to Garment (DTG) printer. The next generation system supports the production of promotional and personalised goods locally.

The Ricoh Ri 2000 prints 1200 x 1200 dpi resolution on a wide range of garments, from traditional t-shirts or tote bags to an extended application range of canvas shoes, baseball caps or long sleeve shirts. It also supports the production of textile face masks and safety vests via the flexibility of the quick-change magnetic platen mechanism and the automatic table height adjustment that easily switches between garment types.
"The new generation of DTG printer represents Ricoh's continued commitment to deliver industry leading inkjet solutions, empowering

our customers to grow their business," said GrahamKennedy, Director Industrial Printing, Ricoh Europe. "Working closely with early adopters in the continuously growing DTG market during product development, Ricoh customers can now enjoy the benefits of a DTG turnkey solution. The Ri 2000 meets the needs of innovative digital print providers, custom apparel online retailers, as well as traditional businesses offering added value by printing on garments. It joins Ricoh’s DTG portfolio that already includes the Ri 100 and Ri 1000 devices as the production flagship.”
The Ri 2000 sets a new benchmark in terms of productivity and efficiency in its class. This is achieved by integrating hardware and advanced software endto-end.
Enabling colour consistency, automation of production workflows and creation of white layers for printing on dark garments with ColorGATE’s Textile Productionserver.
Continuously monitoring ink supply, temperature and humidity levels, reducing human interaction whenever required.
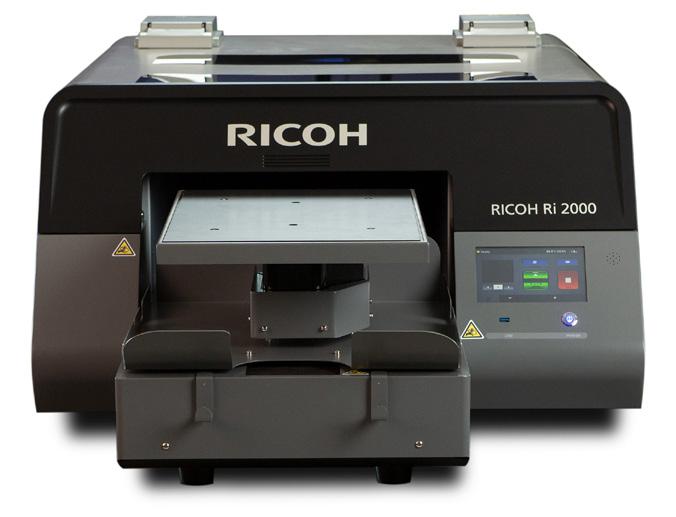
Intuitively guiding the operator with a 7-inch colour touchscreen display providing maintenance alerts, for all tasks that are not automated. Simplifying maintenance with automated cleaning and an innovative head cleaning jig that eliminates the need to manually maintain print head nozzles.‘Genko-Itchi’, Fuji Xerox Singapore believes in a bespoke approach in empowering their customers’ digital journey.
The company’s dedication is also reinforced as it launched 19 new models from its digital multifunction printer ApeosPort and DocuPrint series recently, to support customers in accelerating efficiency while enhancing security, document management and remote working capabilities.