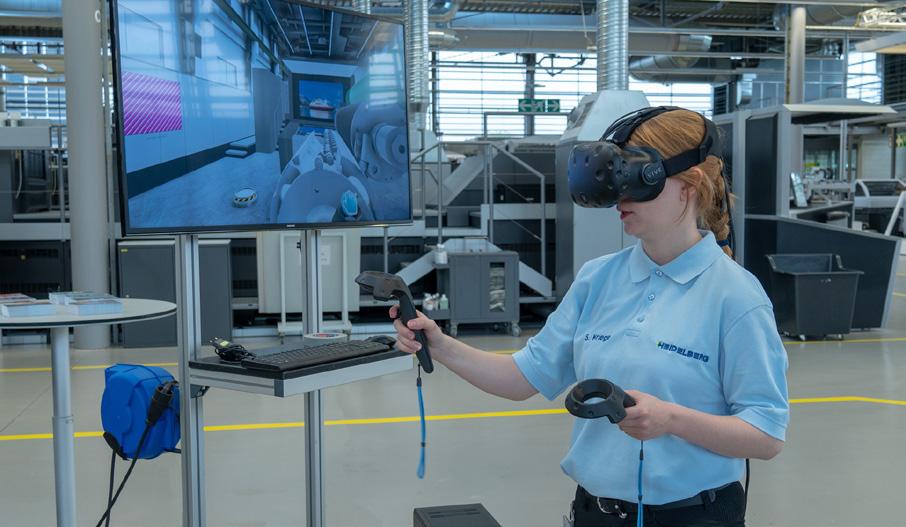
19 minute read
Combination for 3D Printing? News from around Asia and the world
Heidelberg’s 2020 training year kicks off despite Covid-19
The training year at Heidelberg started on 1 September 2020. Despite the ongoing Covid-19 pandemic, another 99 young men and women are embarking on their training or dual study courses at one of the company’s four sites in WieslochWalldorf, Brandenburg, Amstetten, and Ludwigsburg.
The focus is on production-related careers, such as training as a mechanic,
mechatronics engineer, electronics engineer, or logistician. Digital learning content utilizing cutting-edge technologies is becoming increasingly important as digitization spreads throughout all areas of the company and new digital business models come to the fore. Practical examples include the use of augmented reality technology during service and maintenance work on presses, for instance. This trend applies across the board, to commercial specialties and dual study courses in all disciplines, as well as to technical and IT-related careers.
Great interest in dual study courses The popularity of dual study courses is growing ever higher, and not just because they integrate theory and practical projects in the company.
Here, too, digitization is playing a key role. For example, the dual study course in Digital Media/Media Management and Communication covers technical principles for e-commerce and mobile applications, followed by planning media projects, media research, and media automation. The Business IT course teaches key business management and information technology skills. All the dual study courses center on participants developing their own ideas and trying them out in practice at the earliest possible opportunity.
“We invest in up-and-coming talent, and as the world market leader in sheetfed offset presses we offer the best opportunities for highly skilled training, which then generally leads on to a permanent employment contract,” said Prof. Rupert Felder, Head of Human Resources at Heidelberg. “This year, as in previous years, we took on practically all our newly qualified trainees, as we need young people with their ideas and passion – an important investment in the future of Heidelberg.”
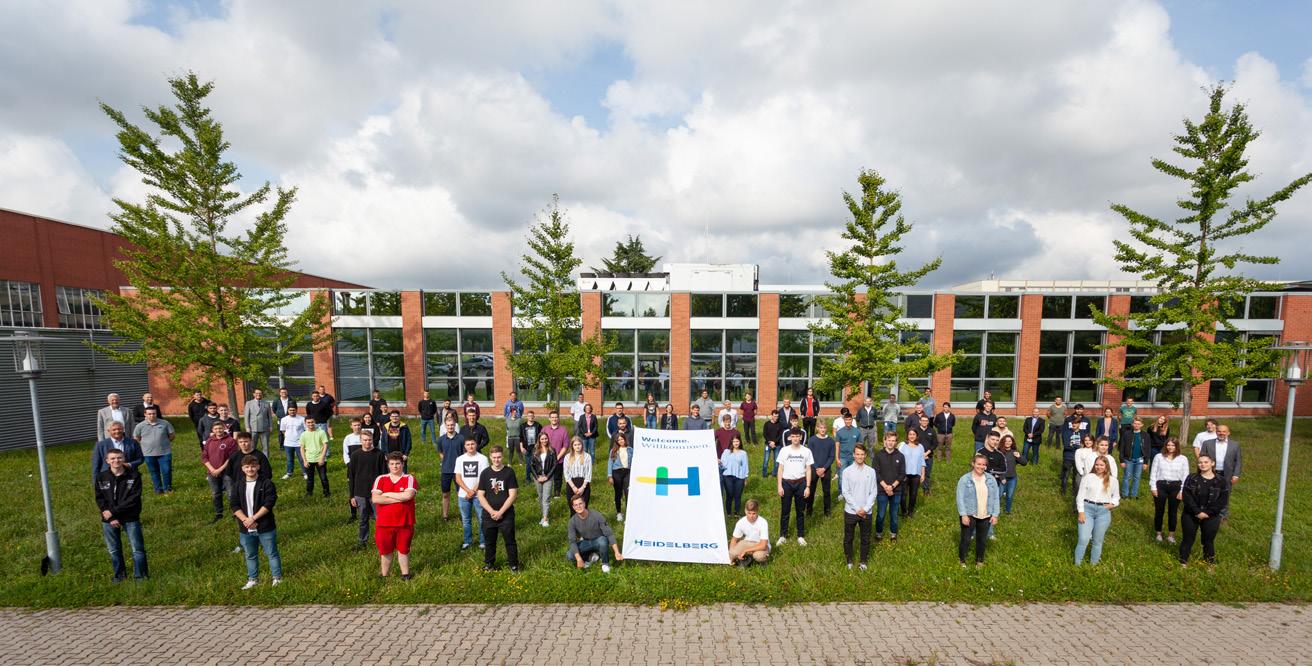
In light of demographic trends and the ongoing digital transformation, the company is planning to progressively increase the number of training places in the years ahead. With primarily older employees retiring in the medium term, Heidelberg will continue to need trainees with an interest in various information technologies and exciting careers in a digital production environment. The company currently employs around 300 trainees at its four sites, approximately 230 of whom are based at the largest site, Wiesloch-Walldorf. in September 2021. School grades are not the only deciding factor when it comes to a training place at Heidelberg. Just as important are applicants’ social skills, personality, and attitude to their career. A full range of information about vocational training at Heidelberg and the application portal can be found on the company’s website.
In light of demographic trends and the ongoing digital transformation, the company is planning to progressively increase the number of training places in the years ahead. With primarily older employees retiring in the medium term, Heidelberg will continue to need trainees with an interest in various information technologies and exciting careers in a digital production environment. The company currently employs around 300 trainees at its four sites, approximately 230 of whom are based at the largest site, Wiesloch-Walldorf.
CGS ORIS introduces new software versions
Color management specialist CGS ORIS is introducing its latest software versions. There are lots of changes to discover!
The color server and the proofing software have a completely new look with flat, very clear icons and the user interface has been arranged in an optimized manner for a simplified overview. This is also supported by a new colored status info, additional information can be activated about printers, queues, jobs and other processes to have all important details present at a glance.
In addition, the user is now able to make many adjustments within the programs and it’s now possible to completely customize the software to their own needs and requirements. This makes working within the software even more intuitive - especially for new users its now even easier to get started – and workflows are streamlined enormously.
A nice enhancement is the option to switch between different modes, like light, classic and dark mode (see picture).
But that is not even the half of it: "In addition to graphic-based improvements, it was of great importance for us to implement innovative features that generate added value for our customers and which are, from our point of view, trend-setting", Marcus Brune, Product Manager at CGS ORIS.
The usage, editing, and also prediction of spectral color data and the optimization of spot colors play a central role here. Among others, this was applied in the simulation of overprinting spot colors. More will be announced shortly, the company promises.
Other functions for example relate to the creation of user-defined test charts for all supported measuring devices, the media-relative adjustment of the substrate white point, and scheduled printing.
In addition, new hardware is also supported, including the latest Xrite EyeOne generation and the new Myiro from Konica Minolta. New Canon, Epson, and Mutoh printers have been implemented.
Konica Minolta’s AccurioWide inks achieve Greenguard certification
Konica Minolta announced it has achieved GREENGUARD Gold Certification for its AccurioWide inks in a move that underpins its commitment to sustainability and environmental responsibility.
For decades, Konica Minolta has been committed to sustainability across its global operations. Its environmental action plan, Eco Vision 2050, sets ambitious goals to reduce its carbon
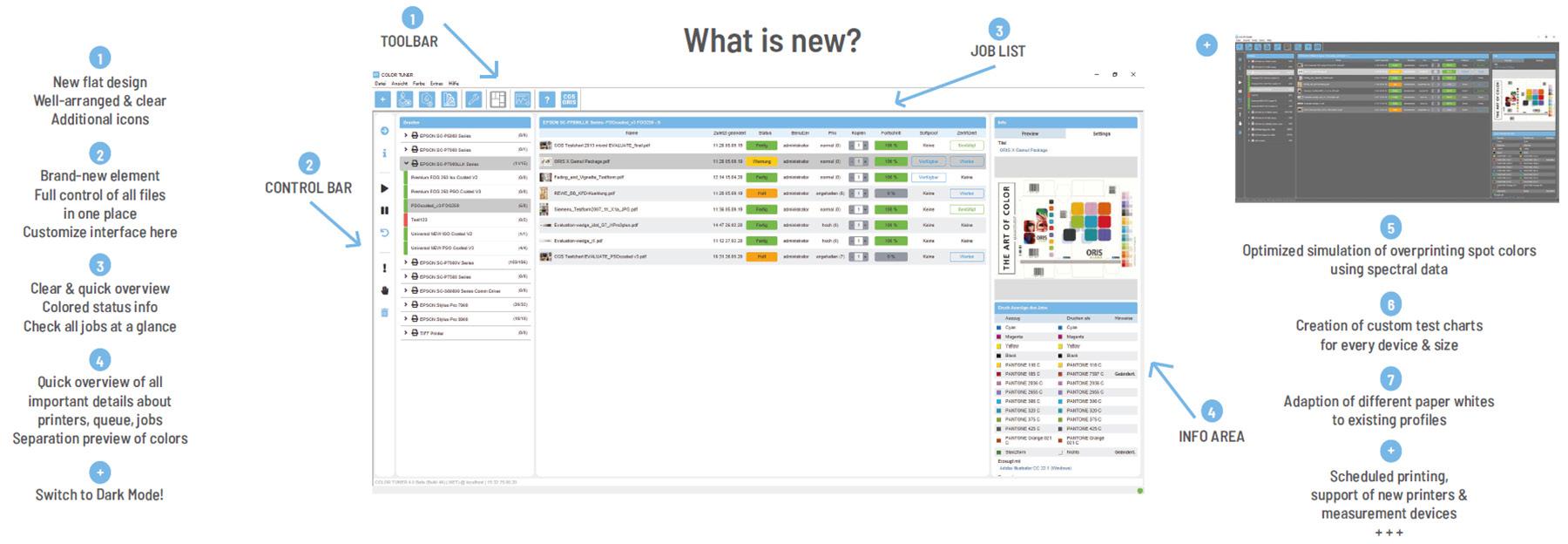
footprint and preserve the planet, while enabling customers to do the same. Products receiving the GREENGUARD certifications are scientifically proven to meet some of the world’s most rigorous third-party emissions standards, helping to reduce indoor air pollution and the risk of chemical exposure.
In addition to maintaining low indoor emissions, Konica Minolta’s AccurioWide UV LED inkjet inks for sign and display printing offer the following benefits: • Wide colour gamut and high colour vibrancy for dynamic results that impress and inspire • Versatility to print on rigid or flexible media with accuracy and excellent adhesion to broaden the scope of possible applications • Lowest ink consumption per square foot – the lowest on the market GREENGUARD certification is provided by UL, a global safety science company that promotes safe, secure and sustainable living and working environments for people by the application of science, hazard-based safety engineering and data acumen.
Miraclon announces judging panel for Global Flexo Innovation Awards
The judges for this year’s Global Flexo Innovation Awards, hosted by Miraclon, have been announced. The panel comprises eight flexo industry influencers and technical experts who bring vast experience from every segment of the flexographic value chain. Each judge’s area of expertise offers a unique take on the judging criteria, which will mark each entrant against their show-stopping creativity, transition to flexo from another print process, print production workflow efficiency and commitment to sustainable print.
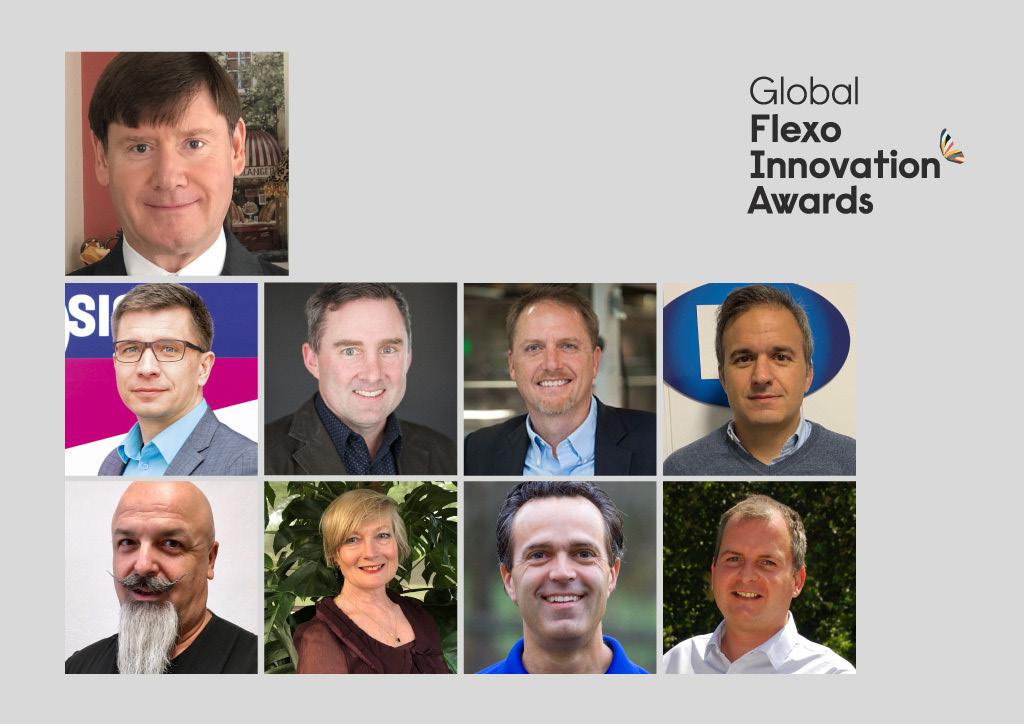
Joining this year’s independent judging panel are: Laurel Brunner (UK), Consultant and Journalist for Digital Dots, Verdigris & Spindrift; Matthew Daniels (UK), Artwork Excellence Innovation Manager at Unilever; Stefano d’Andrea (Italy), Industrial Graphic Expert; Kai Lankinen (Finland), Executive Partner & Co-Owner of Marvaco Ltd; Sebastian Longo (Argentina), President and Managing Director of Fotograbados Longo S.A; Ken McGuire (US), Research Fellow at Procter & Gamble; Jason Goode (Australia), Packaging Manager at Reece Group; and Dr. Chip Tonkin (US), Chair – Department of Graphic Communications at Sonoco Institute of Packaging Design & Graphics.
Chairing the judging panel, after being a judge for the first awards in 2018, will be Christopher Horton, former Senior Vice President of Southern Graphics Systems (SGS) who has had a distinguished career in graphic services, having founded Advance Printing Products, Inc. (APP) in 1988.
He then became a senior executive within Southern Graphic Systems, Inc. when the two businesses merged in early 2001. Christopher was instrumental in the company’s growth to become a global graphic services provider before he retired from SGS in 2015. He still remains active in graphics services and provides business optimization and exit planning consulting services.
Emma Schlotthauer, Chief Marketing Officer at Miraclon, commented: “Across the flexo printing marketplace, there are a host of innovative companies who are driving technological enhancements throughout the production process, even in unprecedented times like these. At Miraclon, we want more than ever to honor the talent and innovation in the industry that is driving flexo forward.
That’s why we’re returning this year with the second Global Flexo Innovations Awards to place a spotlight on companies using flexo to expand their business horizons. Through the awards, we’re not only celebrating these companies and sharing their inspirational stories, but we’re also connecting like-minded individuals to create a valuable global network. We’re excited to be strengthening that network with this year’s awards program.”
“Without our independent judging panel, our Global Flexo Innovation Awards are not possible. We are thrilled to be welcoming nine judges to our panel this year, each who have a vast experience and unique perspective of the flexo print industry. Collectively, they are ideally qualified to recognize the entries that have made the most significant impact across the packaging value chain and we look forward to hearing their choices and revealing the winners,” Schlotthauer concluded.
Launched in 2018, the Global Flexo Innovation Awards were introduced to recognize companies at the forefront of the transformation of the flexographic printing industry. Looking beyond print quality and technical execution, which is expected to be of the highest caliber, entrants are challenged to demonstrate how flexo printing and KODAK FLEXCEL NX technology, with their own innovative approach, has been used to achieve outstanding results throughout the whole production process, from design, to production efficiency and commitment to sustainability.
The Global Flexo Innovation Awards will be open for entries in September 2020. For more information on the Global Flexo Innovation Awards program, 2020 judging panel and 2018 winners visit www.transformingflexo. com.
Integration of AI into On Demand Workflow
Kodak and PerfectPattern GmbH, a specialist in innovative artificial intelligence (AI) solutions for manufacturing industries, announced a new agreement by which Kodak will take a license for the source code of PerfectPattern’s sPrint One software. This will allow Kodak to further develop the version of sPrint One used in the KODAK PRINERGY On Demand Workflow. The latest agreement extends the successful partnership which began between the two companies four years ago with an official announcement at drupa 2016.
The special licensing arrangement will enable Kodak to integrate sPrint One’s AI based functionality more closely with the innovative, cloud based PRINERGY On Demand Workflow for an even more streamlined print job preparation. sPrint One is already the engine for the optional KODAK
Dynamic Print Planning Service for automatic, optimized job ganging and press planning in a single processing step, taking account of numerous printer-specific parameters. The tighter integration of sPrint One into PRINERGY On Demand will help printers achieve even more highly automated workflow processes, greater production efficiency, even lower production and material costs and hence improved profitability.
“This step will enable PRINERGY On Demand to utilize innovative AI technology more easily and more directly than ever by providing an integrated platform with Industry 4.0 and automation features unmatched throughout the printing industry,” commented Todd Bigger, Vice President, Software, Kodak Print Division. “At the same time, it will strengthen Kodak’s portfolio of high performance, cloud-based workflow solutions, which printers can tailor precisely to their unique needs.”

New software release for automated print file preparation: prepress suite expanded with powerful features
• Reduce file sizes significantly through image referencing • Automated creation of hemstitches • Use of file properties for dynamic workflow routing and Variable Data Printing
The last few months have made one thing quite obvious: in order to emerge stronger from crisis situations, it is essential to be able to rely on automated processes in unforeseeable situations and to intervene flexibly and quickly in print production.
OneVision, the specialist for automation solutions in print data preparation, has considered these aspects, among others, when further developing its prepress software Asura over the past months and has equipped it with three new, powerful functionalities.
Shorter processing times by reducing file sizes through image referencing
In the field of direct mailing or dialog marketing, but also in the production of books, brochures and other print products, images are often repeated in files. This causes unnecessarily large file volumes. With the new "Embed recurring images only once" function, identical images are embedded only once. For all other occurrences, "Reference XObject" elements are being created that reference the embedded image. This allows file sizes to be significantly reduced and processing times of subsequent systems to be accelerated.

Automated creation of hemstitches makes large format printers and sign manufacturers work more efficiently
Hemstitches are mainly important in wide format and textile production. The new module "Add Hemstitches" adds hemstitches to supplied print data. The print image can be flipped on all sides or white space can be added. The required sizes can be set individually. For double-sided printing, the motif can be chosen between front and back. Print data are therefore perfectly optimized for production requirements.
Workflow routing and Variable Data Printing (VDP) through file properties
Print service providers send their customers proof sheets of prepared print files for print approval. This is intended to avoid costly and time-consuming reprints. With the improved functionality of the VDP module, colors and fonts contained in the print file can be used as properties. This information can be used in many different ways including for the
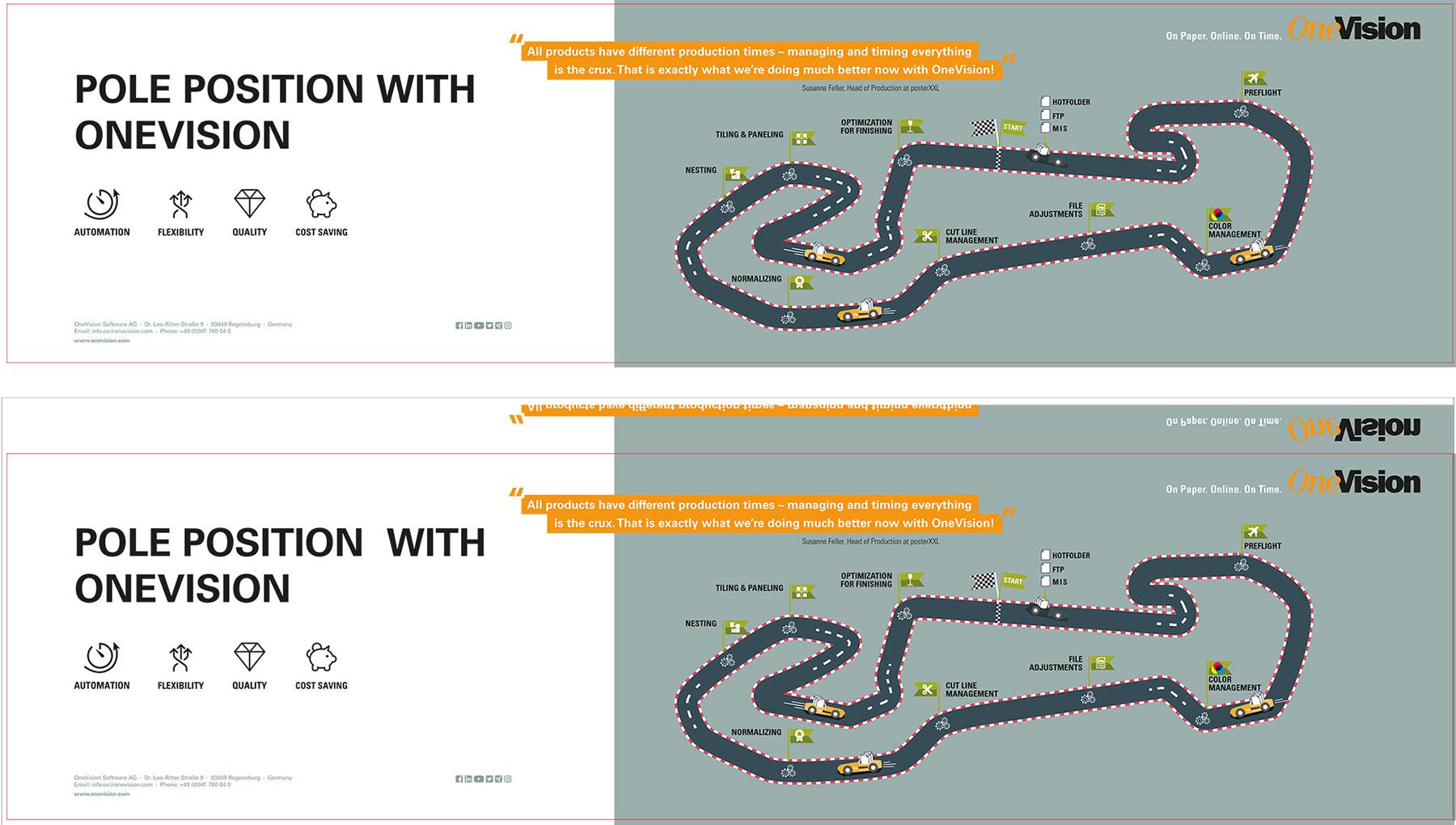
dynamic generation of proof sheets. In addition, the file properties enable routing within the workflow and hence ensure a dynamic, smooth file preparation.
With the new release, OneVision Software demonstrates again that its now more than 3,000 customers worldwide receive major new features regularly – at least twice a year – that enable printers, publishers and other print service providers to automatically produce error-free, high-quality print files and ultimately increase their job profitability.
Flint Group unveils Sustainable Supply Model
Sustainable Supply Model for a Transparent & Ethical Supply Chain Revealed by Flint Group Packaging Inks in New White Paper A commitment to demonstrating robust ethical management is at the heart of an innovative Sustainable Supply Model implemented by Flint Group Packaging Inks.
In a new white paper unveiled by the company, an ambition to achieve transparent and sustainable supply conditions for the print and packaging supply chain is outlined.
Arno de Groot, Vice President of Procurement for Flint Group Packaging, said: “We have a strong sustainability vision embedded in everything we do at Flint Group Packaging Inks. However, this can only be truly realised if we extend our commitments to our stakeholders


and suppliers located around the world. The rigorous standards we set ourselves should also be applicable to those with whom we partner, so that our supply chain is transparent and aligned in achieving sustainable business practices and processes.
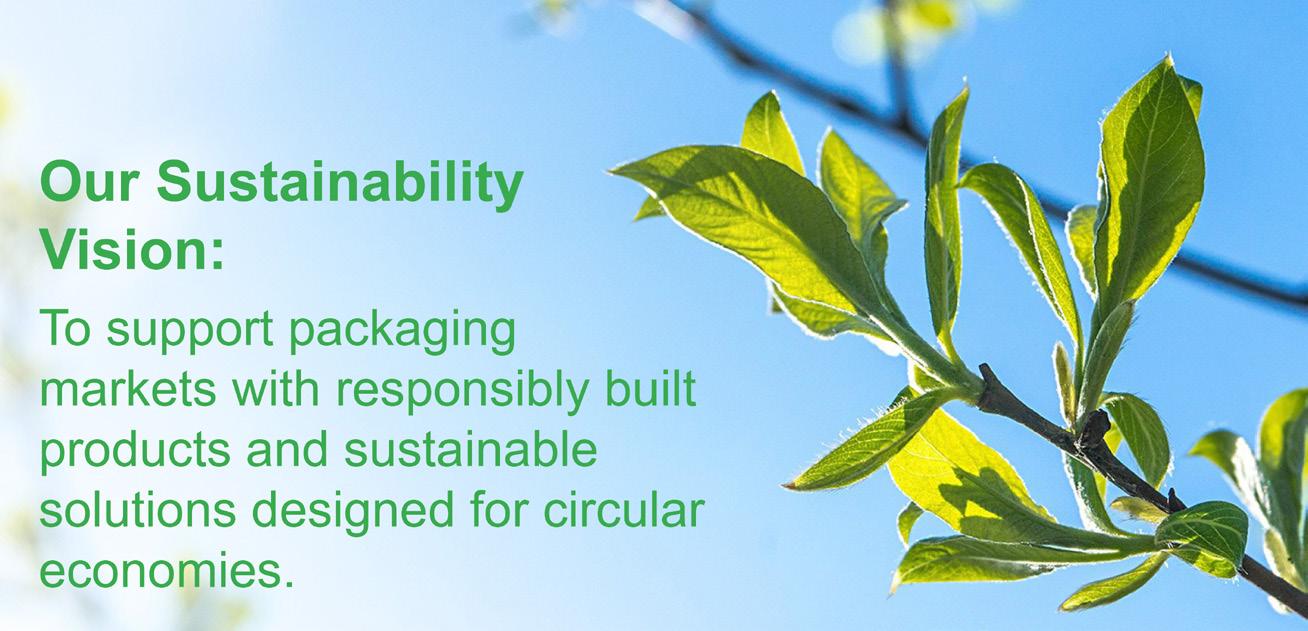
“Our Sustainable Supply Model is built on the principles of strong ethical management and, within our Packaging Inks business, we have aligned our strategies and operations to that of the United Nations (UN) Global Compact in relation to management of human rights, labour, the environment and anti-corruption.
The Sustainable Supply Model complements the objectives set within the Compact and is intended to extend our approach to sustainability and ethical responsibility across our supply chain.”
The recently published white paper explores four key initiatives that have been developed as part of the Sustainable Supply Model. These include: a Supplier Selection Process, which sees potential new suppliers undergo checks and financial assessment to ensure appropriate trading capability is in place; a Sustainability Performance Assessment to compare supplier performance against 10 UN Global Compact principles.
And some of its sustainable development goals; a Health Safety & Environment Review to assess delivery processes and compliance to local and international packaging and labelling legislation; and a Quality and Regulatory Assessment, which considers compliance with regulatory requirements according to product, service, market and geography.
Potential suppliers are provided with a score and if all parts of the Sustainable Supply Model have been effectively addressed, can begin working with Flint Group Packaging Inks.
To find out more about Flint Group Packaging Inks’ sustainability strategy, the new white paper can be downloaded from the company’s website here: https://flintgrp.com/ en/divisions/packaging-narrow-web/ sustainability/
Toyochem launches Biodegradable Polyurethane Adhesive
Toyochem Co., Ltd., a member of the Toyo Ink Group of Japan, has developed a new series of biodegradable pressure-sensitive adhesives (PSAs). Marketed under the Cyabine series of polyurethane PSAs, the newly developed product is suitable for materials for the packaging industry. It can also be used in construction, agriculture and other industries where the use of biodegradable or recoverable materials are preferred.
In recent years, there has been growing interest in reducing plastic waste, in particular with regard to the development of biodegradable materials that reduce the use of petroleum and its negative impact on the environment. In many countries, industrial waste generated from fields such as civil engineering, forestry and agriculture need to be recovered or decomposed naturally without imposing a burden on the environment. While the base paper or film substrates used in recovered products are biodegradable, the additives such as adhesives traditionally used to coat or treat them are not, resulting in disposal issues. In response to this issue, Toyochem researchers in Japan developed a high performance biodegradable PSA based on an innovative biodegradable polymer design.
In addition, by using plant-derived raw materials, the new Cyabine adhesive achieves a biomass content on a dry weight basis of up to 45%. This means the product can reduce CO2 emissions throughout the lifecycle of the newly developed product, without compromising on adhesive performance.
According to Toyochem, after use, the adhesive waste can be digested by soil microorganisms and converted over time into substances, such as carbon dioxide, water, nitrogen and methane gas, thus helping to reduce landfilling and further close the circular loop on plastic waste.
Moreover, the new PSA system demonstrates biodegradation rates of 60% or higher after 60 days. When combined with other biodegradable materials used in a wide range of products, it helps to improve the overall biodegradability of these products (see illustration).
The biodegradability of the new Cyabine PSAs has been confirmed under controlled composting conditions as prescribed by the Japanese Standards Association’s JIS K 6953-1, the equivalent of the international standard ISO 14855-1. It is currently available in Japan with a worldwide release to follow in the next few years.

16 th

FREE ENTRY FORM DEADLINE 5PM NOVEMBER 3RD 2020 3 Windy Hill Drive, Mulgrave,3170 Victoria, Australia
SINGAPORE - THAILAND - INDIA - MALAYSIA - JAPAN - HONG KONG - CHINA - KOREA - TAIWAN - VIETNAM - INDONESIA - SRI LANKA - PHILIPPINES - CAMBODIA - MYNAMAR
The annual Asian Print Awards was founded to recognise outstanding achievement in the print and packaging industries across Asia. With more than half the world’s population represented in this fast growing area, communication in the form of printed matter links Asia’s diverse cultures. It is imperative that such print achievements do not go unrecognised, especially among the population base that Asia enjoys.
The Awards are judged on a wholly quality-oriented set of criteria to ensure that fair play is enacted at all times.
The Independent Judging Panel comprises highly qualified personnel from within Asia and around the world. The independent judging panel has no knowledge of the actual entrants details. ALL ENTRIES ARE NUMBER-CODED. Entries must be commercially produced work.
The Asian Print Awards is the only regional print quality competition of its kind in Asia. Supported by leading industry-supply companies, any progressive quality print house should enter and prove that they are the best - by winning the Gold, Silver or Bronze award. Proving pride in quality awareness is what customers love to see. It’s not just empty words, you can prove it.
Categories 1-8 : Offset Printing Only
1. Calendars – any format
Sheetfed Magazines
Book printing – less than 4 colours
Book printing – 4 or more colours
5. Limited Editions & Artwork Reproductions (under 1000 print run)
6. Web Offset – Coated stock 70gsm and above
7. Web Offset –LWC (light weight coated) 65gsm or less
8. Offset Packaging products
Categories 9 - 21 : Digital Printing Only
9. Book Printing
10. Calendars
11. Personalised photo books – any format.
12. Posters
13. Showcards & Point-of-Sale material
14. Digital Magazines
15. Gold, Silver and Special colours 20. Digital Labels
21 Digital - Outdoor Billboard
Categories 22-26 : Specialty Categories
22. Multi–Piece Productions and Campaigns
Any substrate or print process: Multi–piece Production must be 3 or more items such as folder, leaflets, ring binders, inserts, envelopes including their contents.
Campaigns must be 3 or more items with a consistent theme produced during the year by the same printer for the same client.
23. Embellishment
Any substrate – any combination - for example: embossing – diecutting – foil stamping –laminating - coating.
24. Innovation / Specialty Printing
The entry must exhibit any innovative and/ special application of machinery, process, substrate or finishing.
A short description must be provided for the judges, detailing reasons for entry into this category.
25. Company Self Promotion Any item printed to promote a product or company involved in the graphic arts industry. Self promotion cannot be entered into any other Category.
26. Judges Special Award (A job that catches all the Judges’ attention)
16. Restaurant Menus
17. Limited Editions & Artwork reproductions (under 500 print run)
18. Digital Proofing (must supply the digital proof and the prinnted product)
19. Digital Packaging Best in Digital Award
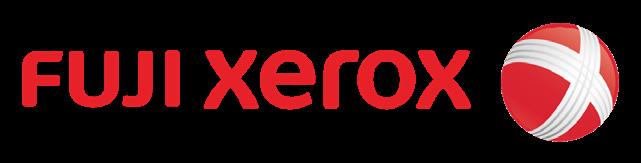
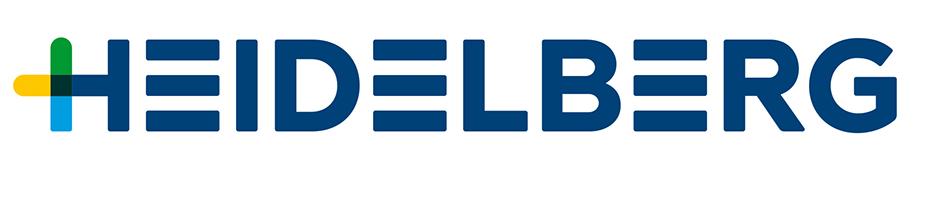
Best in Offset Award
Best Use of Colour Award
SECTION A (This will not be shown to judges). Please fill the form in capital letters.
Entered by (company name): ______________________________________________________________________________________
Contact Person: ________________________________________________ Email______________________________________________
Address: ___________________________________________________________________________________________________________
Telephone: __________________________________ Country________________________________
Category entered __________________________
Title of entry (ie: " Paul's Ice Cream" ): ____________________________________________________________
Printed by (Printers name): ________________________________________________________________________________________
Client name: ________________________________________________________
Designer Pre Press House: ___________________________________________________________________________________________
Brand of Printing Machine used: _____________________________________________________________________________________
Stock supplied by (Merchant’s name): ______________________________________________________________________________
Brand name of stocks Coated Uncoated: ____________________________________________________________________________
By signing here you accept the rules and conditions of the Asian Print Awards
Signature over printed name_____________________________ Name_____________________________________________________
SECTION B Production information to be shown to judges ( tape this securely to the back of your entries)
Category entered (Same as above): __________ Entry number (Administrative use only] ____________
Title of entry (ie: " Paul's Ice Cream" )__________________________________________Print method: _______________________
Number of ink colours (4-6-8 etc) ________ Any Embellishment (foil stamping etc) __________________________________
Quantity produced (Print run copies): ___________ Other technical details (finishing processes etc) ________________________ This Year due to COVID-19 the Judging will be done in Australia ____________________________________________________________________________________________________________________ The Awards will be held in December in Asia
16th Asian Print Awards 2020 ENTRIES SUBMISSION CLOSES 3rd NOVEMBER 2020, 5pm Send all entries to: APAM Pte Ltd, 3 Windy Hill Drive, Mulgrave,3170 Victoria, Australia Email: paul@printinnovationasia.com Additional entry forms can be downloaded at www.printinnovationasia.com Please note that entries are non-returnable unless a self addressed courier pack is supplied.