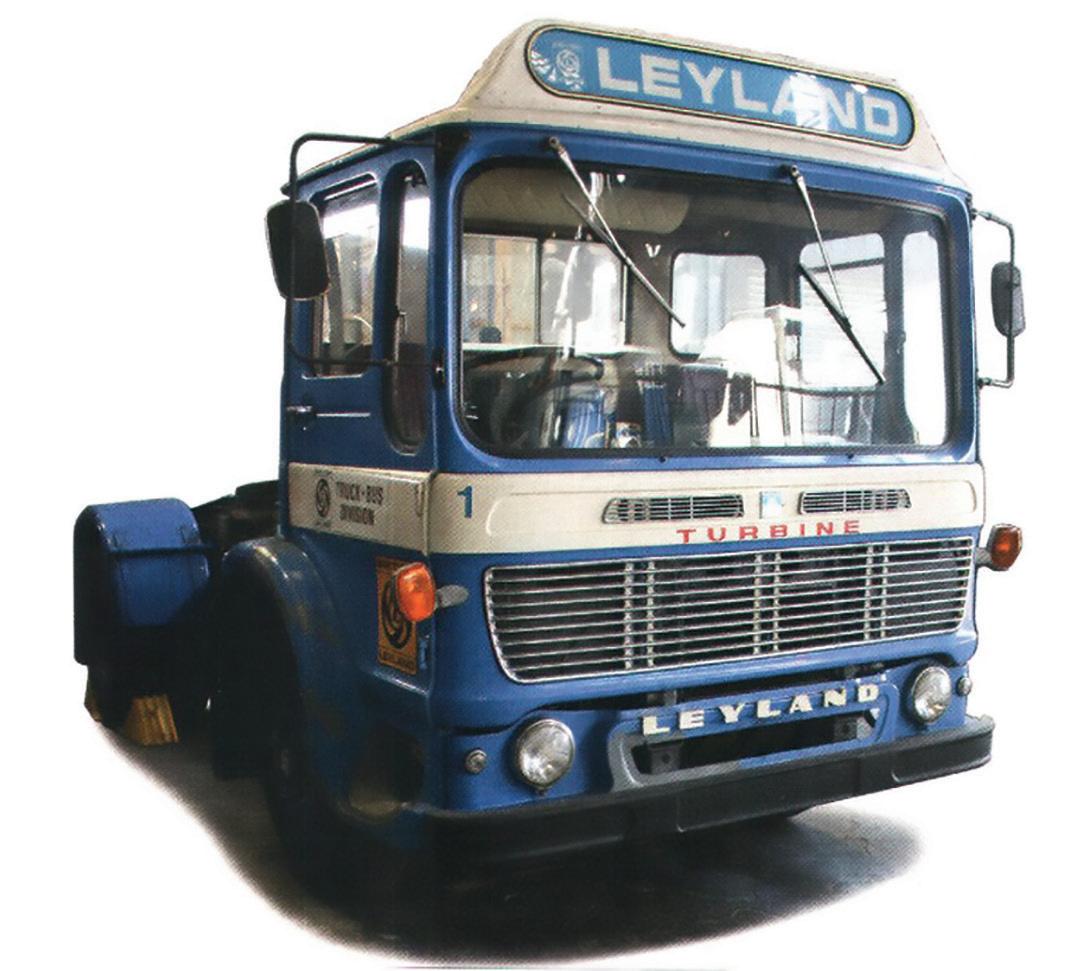
8 minute read
Gas Turbine
BLAST FROM THE PAST
Reproduced Courtesy Of: Commercial Motor
Gas turbines are used for many applications, aircraft, ships, tanks, and stationary generators to name a few, but they’ve never really caught on for road vehicles. That’s not to say they haven’t been tried in trucks, nor that development isn’t ongoing.
The “Turbine” badge on an otherwise standard-looking Ergomatic cab is about the only clue to what is under the floor

The roots of the gas turbine go back to 0AD, when Hero of Alexandria invented the aeolipile, a reactive steam turbine that converted heat into rotary movement. But it was seen purely as a toy and it was another 1,500 years before Ottoman scientist Taqi al-Din built a working steam turbine to power a roasting spit, although Leonardo da Vinci had drawn a similar design 50 years previously. The gas turbine, as we know it today, was patented in 1791 by Englishman John Barber.
An automotive application for the gas turbine was first conceived by Rover, in an amazing piece of diversification for what was regarded as the most quintessentially conservative of motor manufacturers. However, it’s not so strange when you realise that Rover was contracted by the Government in 1939 to assist with developing and
BLAST FROM THE PAST
Leyland Turbine Truck
1. Speed sensor drive 2. Power take-off 3. Exhaust stub pipes 4. Compressor 5. Stacks that tilt with the cab 6. Ignition plug 7. Air filter box
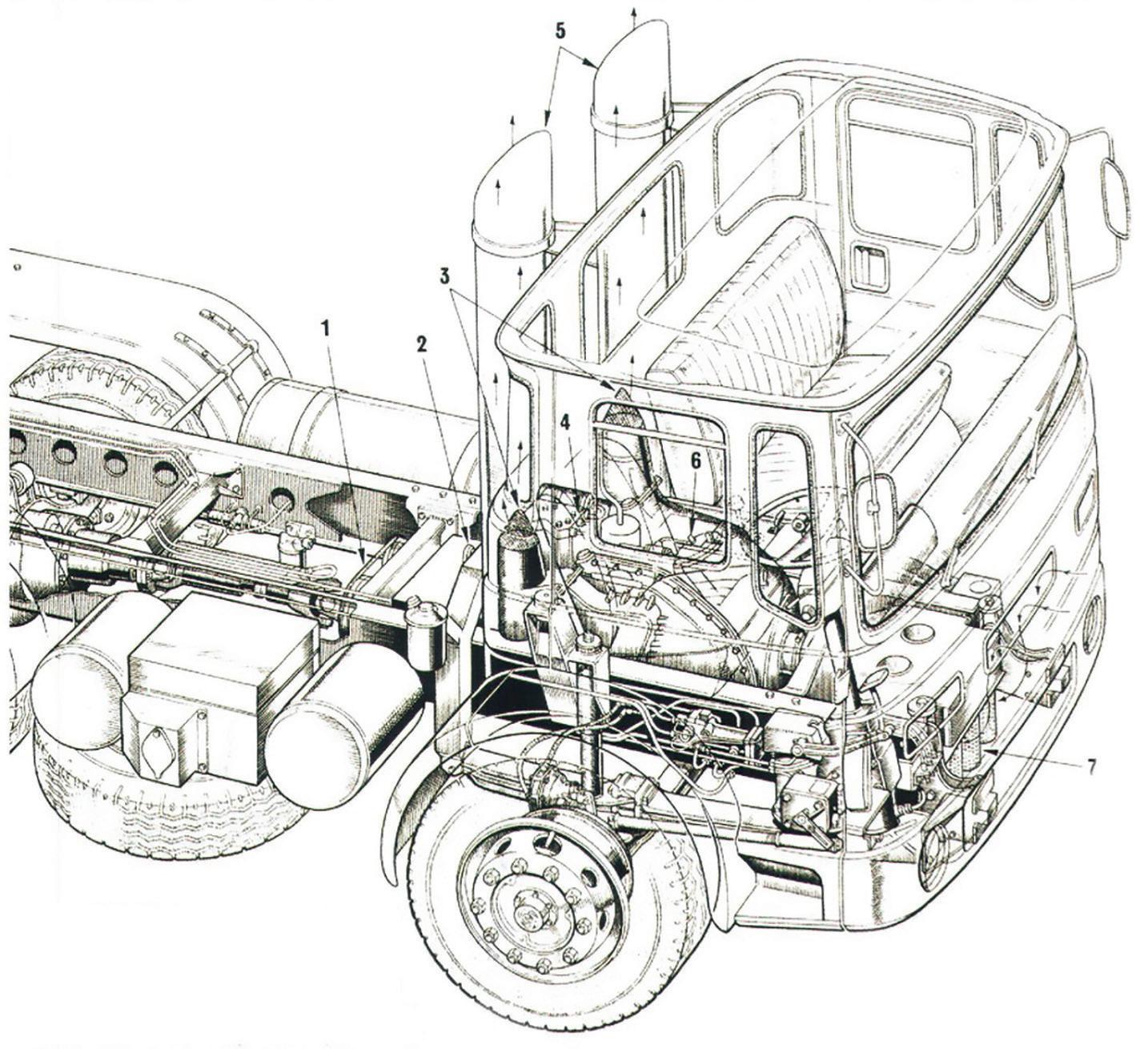
CASE STUDY HOW IT WORKS
The simple gas turbine engine can be likened to a four stroke piston unit, with the familiar four stages; inlet, compression, combustion and exhaust. The difference is that there is just one moving part, a shaft carrying a series of vanes or blades, which is located in a tubular housing. Vanes at the inlet end of the shaft, which like a piston engine has to be initially rotated by an external starter motor, draw air into the housing. The compression stage is achieved by an effective reduction in the housing diameter, and as the air passes through this, its temperature increases. By the time the air reaches the combustion chamber, it is hot enough to ignite a continuous spray of fuel, normally kerosene. As the now even hotter gas expands, it applies thrust to another set of blades, which converts the energy to the rotating shaft. Once combustion is underway, the process becomes self-sustaining. There are numerous refinements to the basic principle, according to the application. The latest prototype runs on hydrogen with plasma ignition.
manufacturing Frank Whittle’s nascent jet engine. Three years later, having become the leading developer of jet engines, Rover decided to leave the world of aero engines and effectively did a swap with Rolls-Royce for the V12 Meteor tank engine, developed from the legendary Merlin.
Move into cars
Shortly after the war ended, Rover began to develop the gas turbine as a car engine, with financial backing from Leyland Motors. The story of the road cars from JET 1 in 1950 to the T4 Le Mans contender in 1965 is enough for a book of its own, but it eventually became one of high performance allied to high fuel consumption, and the concept quietly faded away from the car scene.
Although Ford and Volvo made abortive attempts to create gas turbine trucks, probably the best known are the Leylands built in the late 1960s and
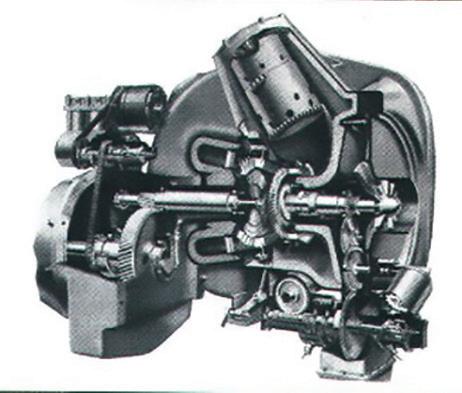
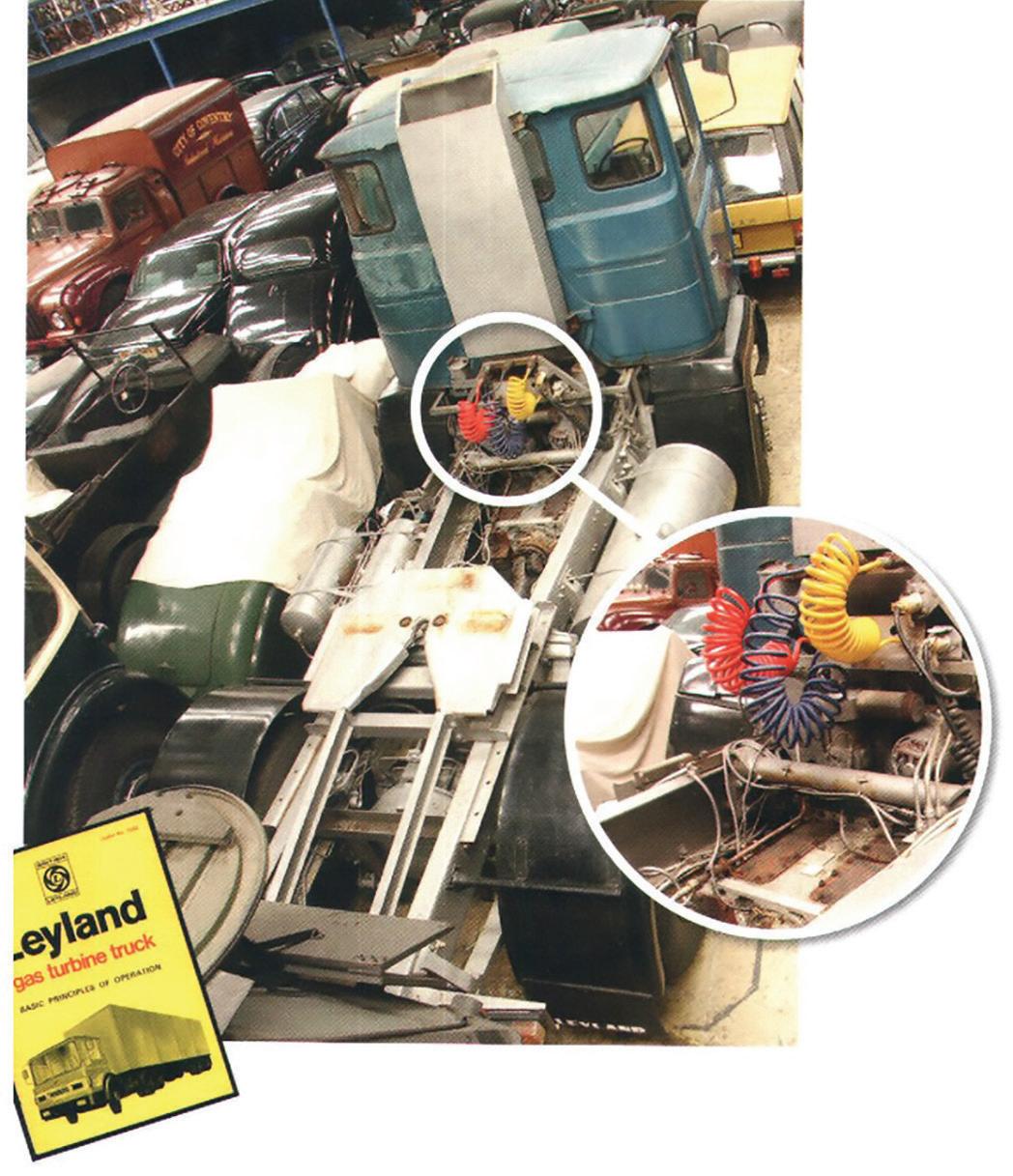
Left: Marathon version is now parked up at Coventry Museum
Right: Secondgeneration engine is on show at the Leyland Museum
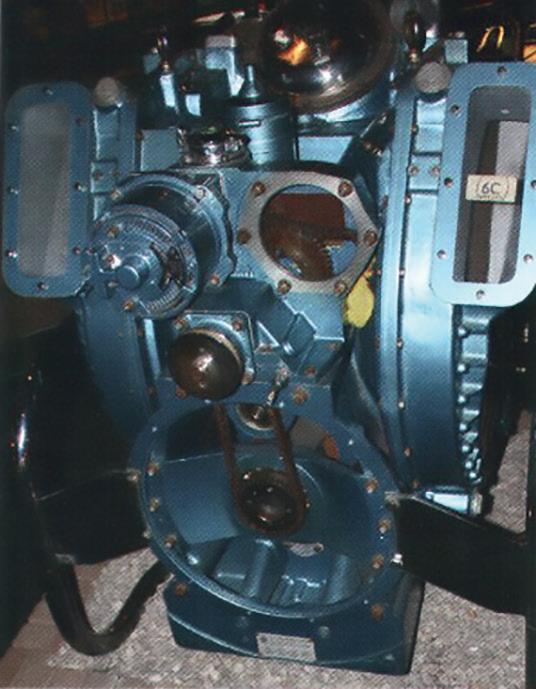
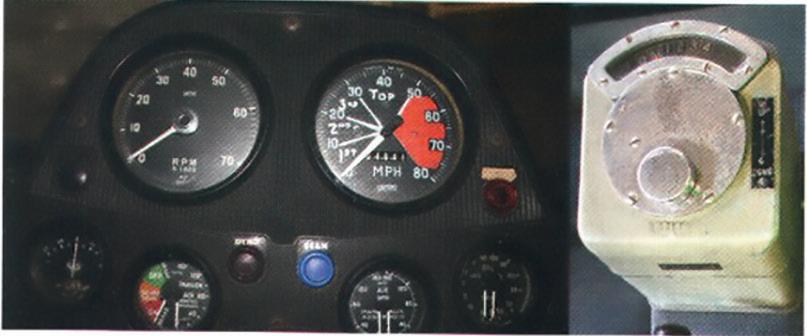
Higher than usual rev-counter, and that’s after 10:1 reduction in turbine speed
early ‘70s. The first example was revealed at the 1968 Commercial Motor Show at Earls Court, London.
The background to Leyland’s gas turbine project is not dissimilar to today’s engineers, looking for ways to provide adequate cooling for the next generation of Euro-6 engines. In the ‘60s, demand was growing for more power, but existing cab dimensions were hampering progress. The bright idea was to try the now neglected Rover engine, in which Leyland Motors still had a stake, in an Ergomaticcabbed 4x2 Super Comet. Part of the thinking was that the gas turbine’s characteristic of producing maximum torque at stall better suited a truck application. The installation was matched to an epicyclic gearbox from the company’s bus range. This is the example still in its Leyland Motors livery, which is currently in storage at the British Commercial Vehicle Museum, in Leyland, awaiting a full restoration hack to running order.
Although a bit short of power, it was considered a partial success and encouraged development work on a larger engine more suitable for truck use.
When this unit appeared, it was in the 6x4 Lynx/Bison chassis, newly developed for the Leyland 500 engine. As well as being physically larger than the car-derived unit, it included the heat exchangers essential to improve the gas turbine’s thermal efficiency Power output was 350hp, with scope to develop to 400hp. Transmission was again a bus-derived epicyclic, but with extra electronic fully-automatic control. The AEC Mandator V8’s walk-through Ergomatic cab was used, with external modifications by Range Rover and Rover SD1 stylist David Bache.
Weight penalty
Although the engine now produced adequate power, with the addition of the heat exchangers, its weight was nearer 900kg than the target
450kg, rather too close to the 1,000kg of the conventional 680 engine. Five examples of this model were built. The first one, shown at Earls Court in 1970, and a second development truck, were kept in-house. After development support from Shell, Esso and Burmah Castrol, the oil companies had the final three. The final chapter was a mocked-up version on the 1972 Marathon chassis, which is now owned by the Coventry Transport Museum.
So what went wrong? Well, for a start, it was a bit late. By the time it was ready, the turbocharger was making its presence felt on diesel engines, vastly increasing their power/ weight ratio and thermal efficiency. With the gas turbine engine ending up heavier than expected, the difference was too small.
But most of all, it was too thirsty. At the end of the day, fuel economy depends on thermal efficiency. Heat lost is heat that isn’t converted to power. The amount of heat that could he exchanged within the Leyland gas turbine was limited by the materials available on the day. While components made of unobtainium were theoretically available, their prohibitively high cost and dramatically short service life made them impractical for production purposes. The fact that the oil companies baulked at the consumption tells it all, really.
And so ends the story of gas turbine engines in trucks... or does it?
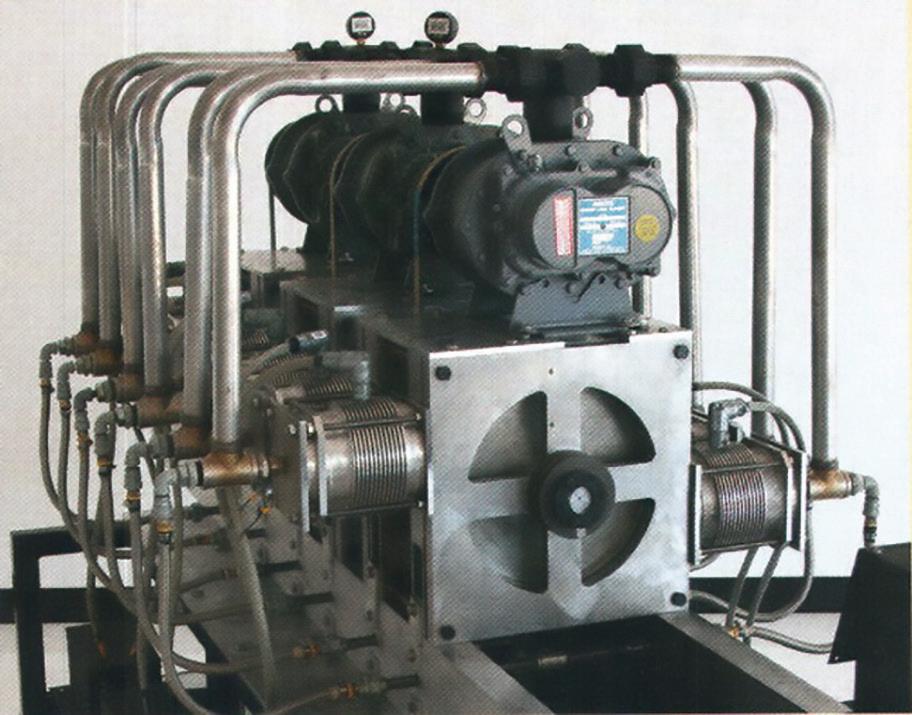
THE FUTURE
Gas turbine engines may seem to be no more than an interesting footnote in history, but at least one American company sees them as part of tomorrow’s road scene. Turbine Truck Engines (TIE) of Daytona Beach, Florida, is now on the fifth generation of its prototype Detonaton Cycle Gas Turbine engine (DCGT).
The engine is a scalable and modular unit, capable of powering anything from a lawnmower to an ocean-going ship. Each module looks a little like a BMW boxer motorcycle engine, although with one high pot and a lower one on the other side. What look like cylinders are actually the combustion chambers, and they work in opposing pairs. Air is pumped by a crank-driven blower into the combustion chamber where fuel is injected, the mixture is ignited and expands. The expanding gas acts against the main engine’s only moving part, which is a water-wheel type turbine attached to the equivalent of the crank shaft, creating rotary motion.
As the ignition process occurs, it creates back pressure down the intake manifold, which effectively causes a pressure blockage and diverts the incoming charge to the opposing side of the engine, which has a slightly longer manifold. This is vital to provide the staggering of the firing events. The process then repeats, giving rise to the “Cycle” part of the engine’s name. That’s basically it for the single module unit; the truck-sized prototype consists of three modules. The advantages of the DCGT engine are that the lack of moving parts and low-pressure, low-stress combustion process will make it cheaper to build and maintain than a conventional engine. TIE claims this to be half the cost and twice the life of a diesel.
The explosive nature of the combustion process is said to result in a near 100% burn of fuel, giving reduced fuel consumption and emission levels. Again, TTE’s claim is 30% better economy than for a comparatively powered diesel. The DCGT is also truly multi-fuel, capable of running on any fuel that is gaseous or can be gasified, from coal dust to hydrogen.
TIE makes no secret that it has no interest in becoming an engine manufacturer, preferring to license the concept. It has spent some time trying to persuade the US truck manufacturers to get on-board, but with little success, so far.
While still actively pursuing finance in the West, TIE is now placing most of its eggs in the Chinese basket. The first step is likely to involve production of 150hp car and 400hp bus engines.
However, TIE has identified 33 industry sectors in 100 countries that it sees as potential markets, so there’s a fair chance we are likely to see more of the DCGT in the future.