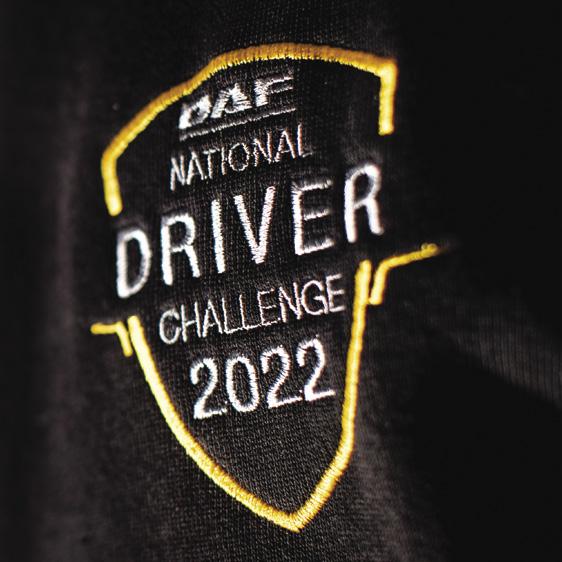
16 minute read
Driver Challenge
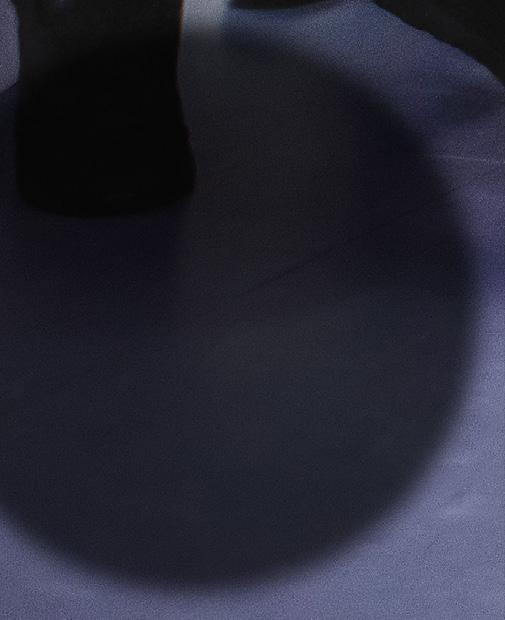

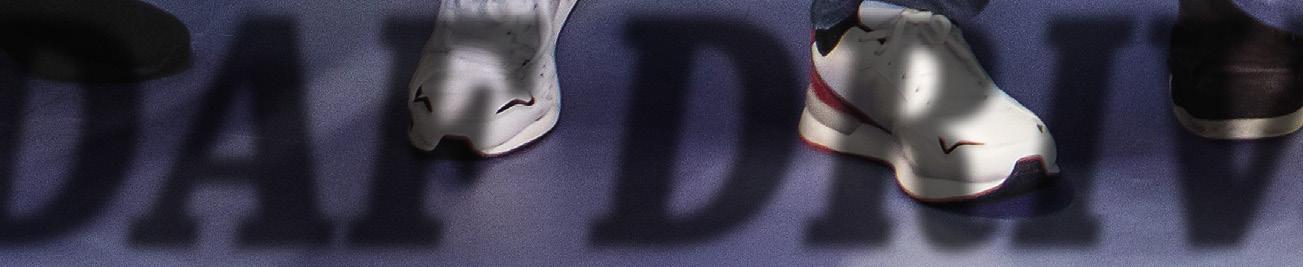

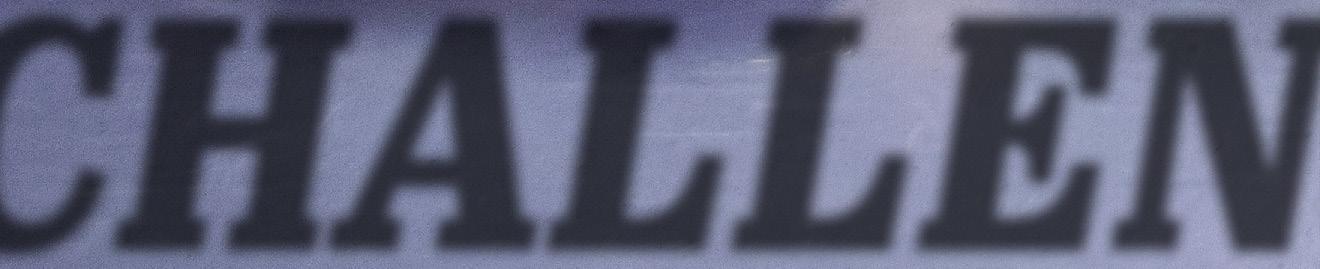
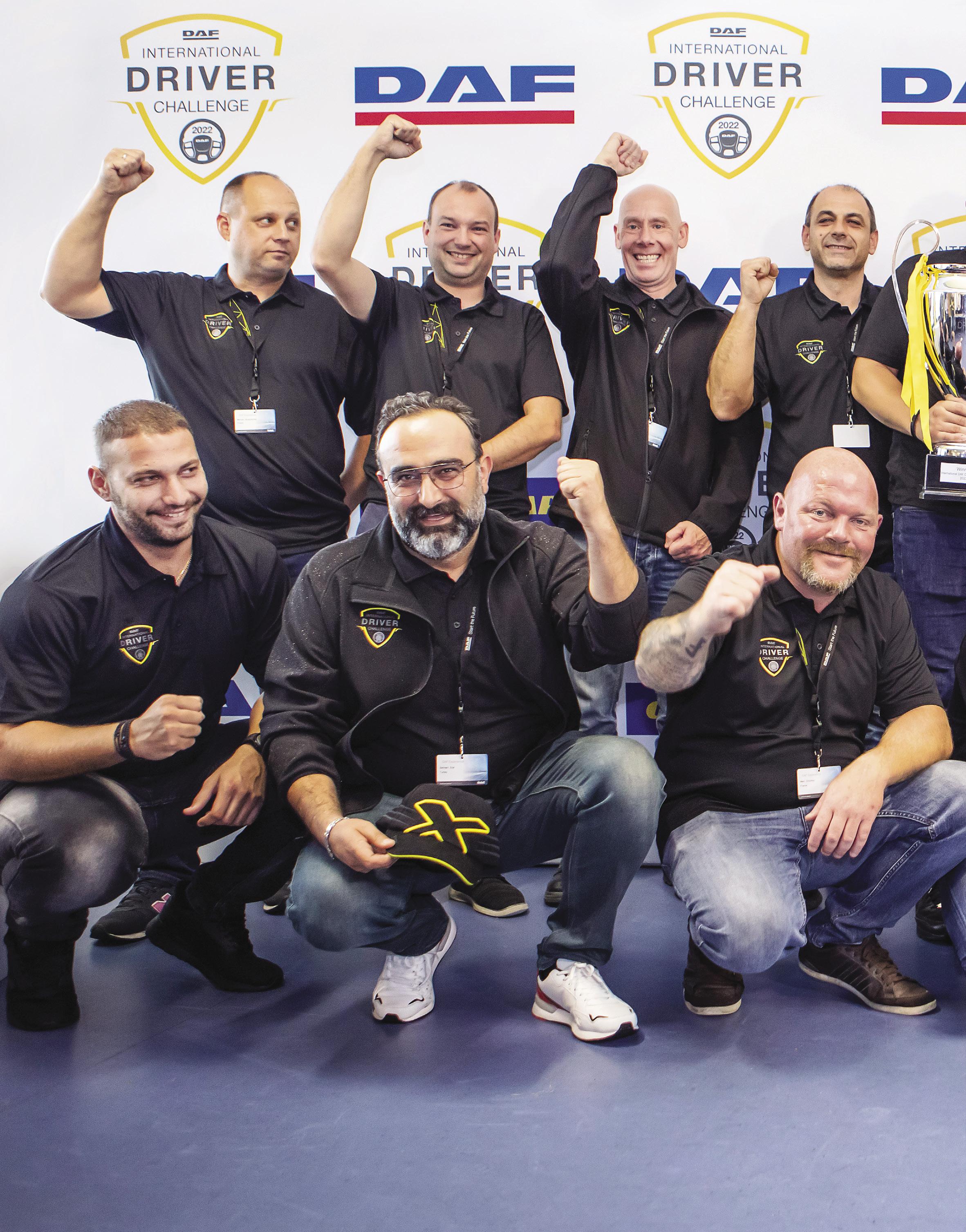
DAF DRIVER CHALLENGE

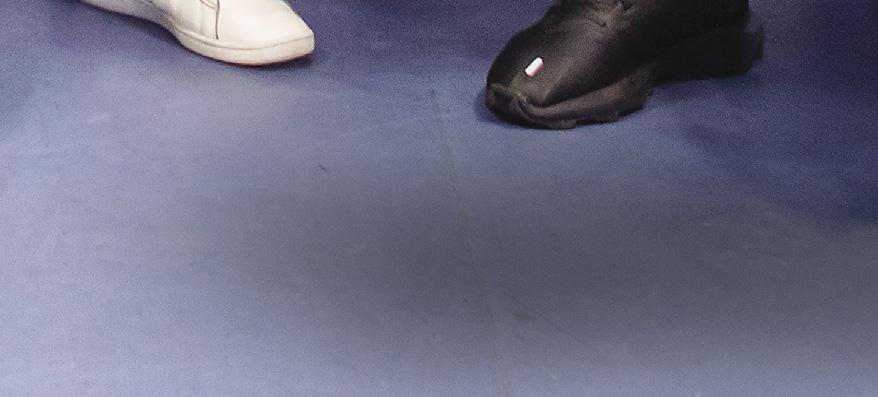
Fourteen drivers tackled seven disciplines to decide who would be the winner of the DAF International Driver Challenge 2022. winner of the DAF International Driver Challenge 2022.
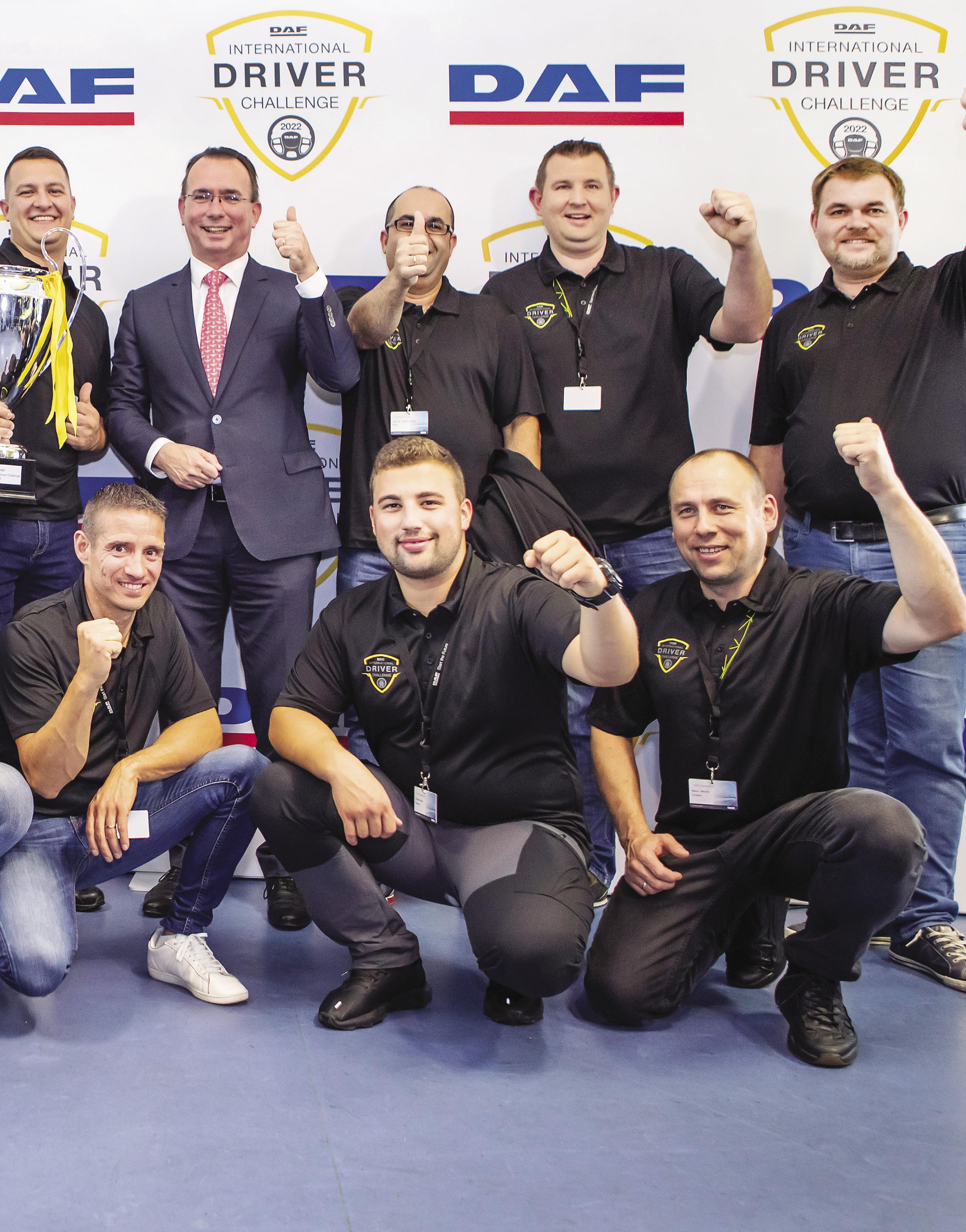

Words: Jack Sunderland Photographs: DAF Trucks
The biennial DAF International Driver Challenge was held at Goodyear’s test and production facility at Colmar-Berg in the small but vitally important country of Luxembourg, which boasts one of the highest GDPs in world.
Of the competing countries, each held regional finals, with the winner qualifying for the national final. From there, the national winner qualified for the grand final in Luxembourg. Unfortunately, due to flight cancellations, the Italian finalist was unable to attend. The U.K finalist, Colin Court won his place at the UK’s national final which was held at Motus DAF in Gloucester during summer 2022. Age: 51 Home: Guisborough Married to: Hamida Career: Senior Driver Employer: Heidelberg Materials, formerly Hanson Cement Experience: 25 years with Heidelberg/Hanson. Six years with Preston’s. Passed C+E (class 1): 1992 Hobbies & Interests: Country walking. Anything to do with trucks and transport Job likes: Being his own boss as soon as he leaves the yard. Massive improvements in safety right across the industry. Totally loves driving. Job dislikes: The level of traffic. DAF likes: The New Generation DAF. In particular safety and driver comforts – a real game changer. Vehicle: DAF XF 450 FTP
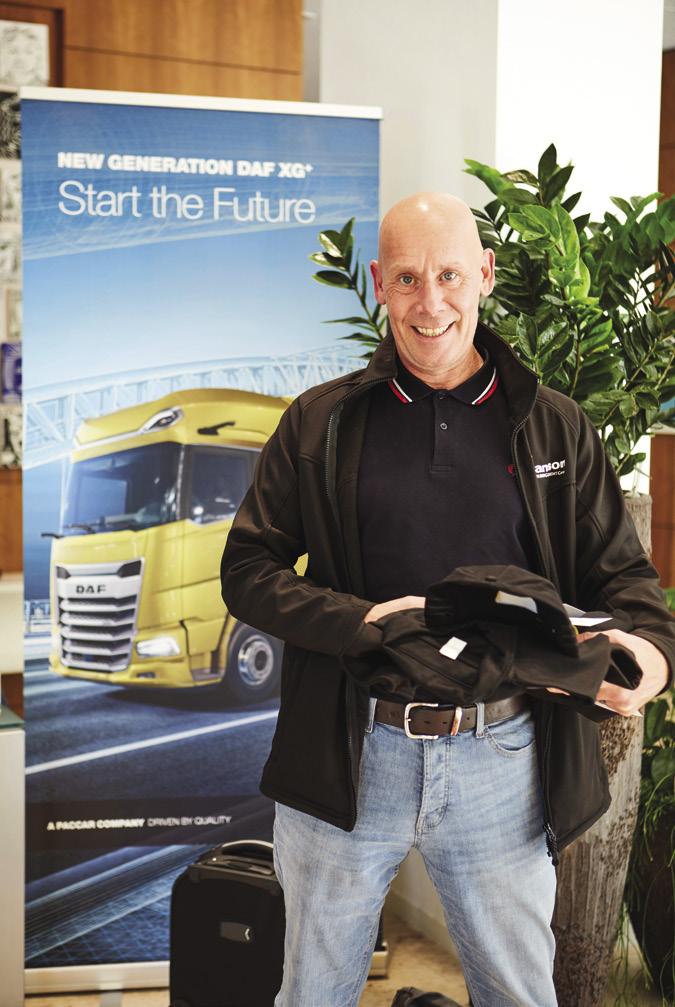
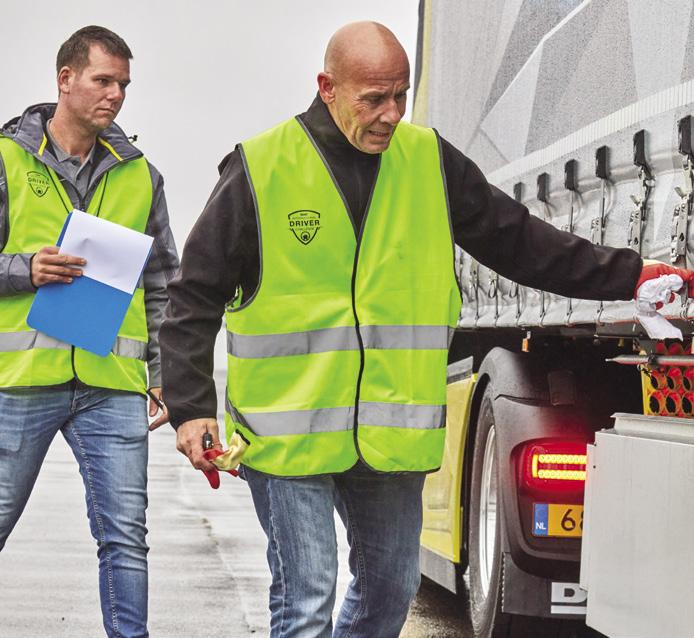
1. DAILY CHECKS
This involved a visual walk round but with a very strict brief. The scenario was that the vehicle was being driven from the Netherlands to Spain so needed to be prepared for the route, including both the correct paperwork and technical checks.
The vehicle under scrutiny was the ‘all new’ DAF XF complete with DDVS (DAF Digital Vision System) with Corner View. The XF was coupled to a tri-axle curtain side trailer with the curtain open, showing a load made up of steel stillages filled with concrete blocks. The stillages were strapped to the trailer. There was also a spare wheel. It was all designed to give opportunities for the driver to check and question. The walk round checks needed to be carried out as very much a ‘show and tell’ with the finalist explaining any faults or issues as they carried out a perfectly planned systematic circular route around the vehicle. The finalists were also free to ask questions.
The exercise had a limit of 20 minutes, giving enough time to carry out a systematic appraisal.
How did it go for Colin? Colin felt reasonably confident, comparing it to a normal day at work. “How’s the route planning going from the Netherlands to Spain?”, we asked. Colin immediately realised that a road consignment (CMR) form would be necessary as well as spare bulbs, warning triangles and other safety related equipment. The first implemented defect that Colin noted was a damaged electrical suzie that had been repaired with insulating tape.
2. ECO DRIVE
Getting the best from the vehicle was of paramount importance. Fuel efficiency was the main consideration but being able to put the onboard driving and performance technology to good use was imperative. A list was needed to explain what the competitor was doing in preparation and setting up the vehicle before they started, as well as explaining what they would be doing with the technology to enhance the vehicle performance once out on the road.
The vehicle selected for the eco drive task was the XG FT loaded to 37-tonnes. The route was a mix of A-roads and motorways which best represents the environment the XG? will be best at home in.
How did it go for Colin? From Colin’s perspective, he felt he couldn’t have done any more to improve his eco driving. He felt he put both the PCC (Predictive Cruise Control) and the DSC (Downhill Speed Control) to as good a use as he possibly could by setting parameters up properly to get the maximum from Eco Roll on the undulating road route.


3. THEORY
This consisted of a 45-minute classroom session set in an examination situation. The finalist worked alone on a multiple-choice paper made up from a mixture of DAF product and their operating systems, with the benefits they bring. There was also a smattering of operational questions based around EU regulations.
How did it go for Colin? He felt reasonably happy with his answers on the multiple-choice paper. In his own words “The questions regarding the tachograph, Working Time Directive and general EU rules and regulations were things we should know.” This involved a series of three manoeuvring challenges all of which were timed, with the whole exercise lasting 30 minutes.
1. The first exercise was a time trial, which involved driving the loaded XD 450 rigid through a series of slalom curves marked by cones. The exercise was finished with a controlled stop in a box, with the wheels lined up between the two clearly marked control cones. To score maximum points, the driver needs a clear run and a quick time. Importantly, the front wheels need to be positioned perfectly between the marker cones when the vehicle comes to a complete stop. Points were deducted for clipping the cones, as well as poor positioning of the vehicle.
2. Part two of the challenge involved manoeuvring and reversing the XG+ 480 and trailer. The course initially ran straight ahead, with the driver bringing the vehicle to a halt at a designated stop position. This was followed with a right-hand blind side reverse into a box marked with cones. The driver then pulled away and entered a left hand turn before heading into another parking box. The exercise finished with a righthand blind side reverse into a box, which was very similar to the C+E reversing test exercise. Again, this exercise was against the clock with a maximum of 10 minutes allowed. Points are given for speed and penalties awarded for hitting cones. How did it go for Colin? “I really enjoyed that and in particular the controlled stop”. Both of the blind side reversing exercises were very testing, especially with the CF Electric and the city trailer. Being left-handdrive really made him work hard but he found it very enjoyable never-the-less.
5. INTERVIEW
Each finalist took part in a 25-minute interview. The format was informal - more of a ‘getting to know you’ chat with the newly appointed Director of Marketing, Rik van Aken. Importantly DAF wanted to find out what finalists thought they had brought to the industry, how they got involved in transport and how they viewed DAF and its products. The big question was what each finalist could potentially bring to DAF as a brand ambassador.
How did it go for Colin? “The interview was more of a chat. Rik wanted to know my perspective of DAF and how I could pass my knowledge on.”
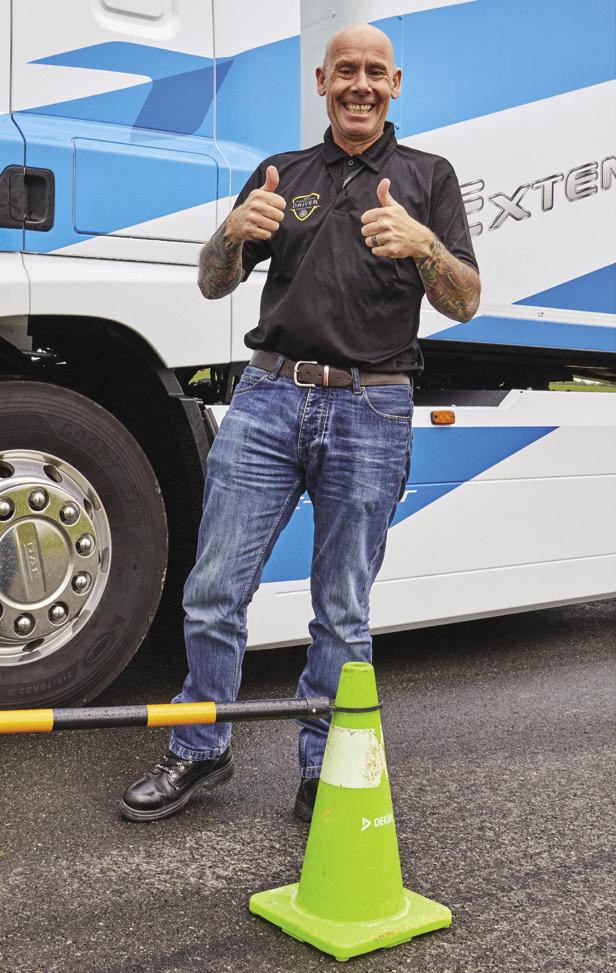
6, COUPLING AND UNCOUPLING
Potentially a more difficult element of the challenge was to complete a two-part exercise, adhering to the rules of coupling and uncoupling. The first task involved a 6x2 XG 480 drawbar combination, with VBG coupling equipment. The second task, more in line with UK procedures involved a 4x2 XG+ tractor and tri-axle trailer with a Jost fixed fifth wheel.
Both combinations were uncoupled. The driver had to successfully couple both vehicles, following the correct procedures. They also had to describe each process and explain what they were doing and why. Each element was assigned 10 minutes and points were awarded for successfully completing each task in line with the correct process. How did it go for Colin? “I’ve never had to couple up a wagon and drag before and haven’t used a palm coupling for over 20 years”. He used the same process for the semi-trailer which worked fine.
Colin said that the tractor and trailer was far more straight forward to couple and although he was working from the left-hand side, he just worked around in the correct order and explained what he was doing, which seemed to go well for him.
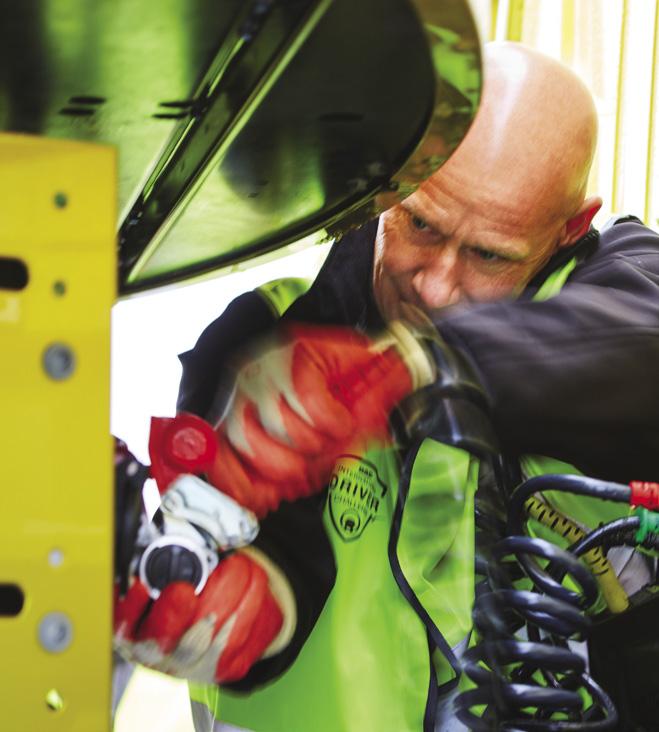
7. THE SPRINT.
This was a little bit of fun that could potentially be used as a tie breaker. Each finalist had to guess the elapsed time of a sprint race. Hosts Goodyear had set up a drag style sprint race, using an unladen DAF XG 450 4x2 running on worn Goodyear tyres with just 2mm of tread depth. This was coupled using a straight bar to a fully laden XG 480 6x2 rigid. The driver needed to pull the heavy truck over a 100m track. The twist was that the track was absolutely soaking wet. Each finalist submitted an estimated time on a piece of paper. The one coming up with the closest time was the winner. Goodyear was very keen to demonstrate the impressive performance of its tyres, even with minimal tread depth and in such poor working conditions. Interestingly, the estimated times ranged from 2 min 30 seconds to under 10 seconds. The winner submitted a time of 20.6 seconds. 3. Part three was possibly the hardest reversing exercise of all. With a DAF CF electric tractor unit coupled to a rear-steer city trailer, the exercise had to be carried out in reverse only. The course Involved a series of long sweeping bends on the Goodyear test track with a series of slaloms over approximately 350 metres, finishing with a bay park, before a sprint finish and controlled stop lining the front wheels up with designated marker cones. The exercise needed to be completed within 10 minutes with points awarded for speed and deducted for clipping the cones.

THE WINNERS

With all competitions closed, the finalists and guests had to wait for the results for what seemed like an eternity. The senior management teams from both DAF Trucks and Goodyear Tyres assembled to present the results of the two-day competition. Lifting the DAF International Driver Challenge 2022 Trophy was the Hungarian finalist Gábor Szabados, who achieved excellent scores in all the disciplines. Second and third places went respectively to Pierre Emmanuel Huet from France and Emanuel Mezi from Romania.
Commenting on his win, Gábor said, “I can hardly describe how happy I am right now”. 32-year-old Gábor, is a truck driver for Gogolak Gabor. “The competition was fierce. We all had to really push ourselves to the limits.” All driving tests were performed behind the wheel of the New Generation DAF truck series, including the brand-new DAF XD for vocational and distribution applications – revealed just two weeks before and recently awarded ‘International Truck of the Year 2023’. “The challenges, which included practical driving tests with trucks and trailers, were extremely tough and the exams that we had to take covering technology, legislation and regulations tested us to the limit,” said Gábor. “Driving an electric truck was completely new to me – and I have to admit, I loved it!” The ever-smiling UK entrant Colin Court picked up a very respectable sixth place. A sterling effort bearing in mind all the vehicles featured left-hand-drive. Colin said, “I was really pleased to be part of the whole competition and do my best for Britain.”
Even getting to the final as a competitor in the DAF International Driver Challenge 2022 was a massive achievement. The competition, right from the regional events to both the national and ultimately the international final was probably the most difficult challenge any professional truck driver would ever face and ultimately really tested the mettle of even the most experienced driver. At the final, the sense of camaraderie between the competitors was very apparent. All were very eager to win, but with the shared belief that they were all truck drivers and damned good ones at that. As technology develops, correct and proper use will bring a heightened understanding of the onboard technologies. The only variable in vehicle performance is the driver and the need for correct and proper training to ensure efficiency is now a fundamental part of truck use. A good driver properly trained with the correct level of understanding of the new generation of truck technology will ensure better performance of the asset and will undoubtedly save money. the DAF International Driver Challenge 2022 offered a clear demonstration that training matters.
DDM
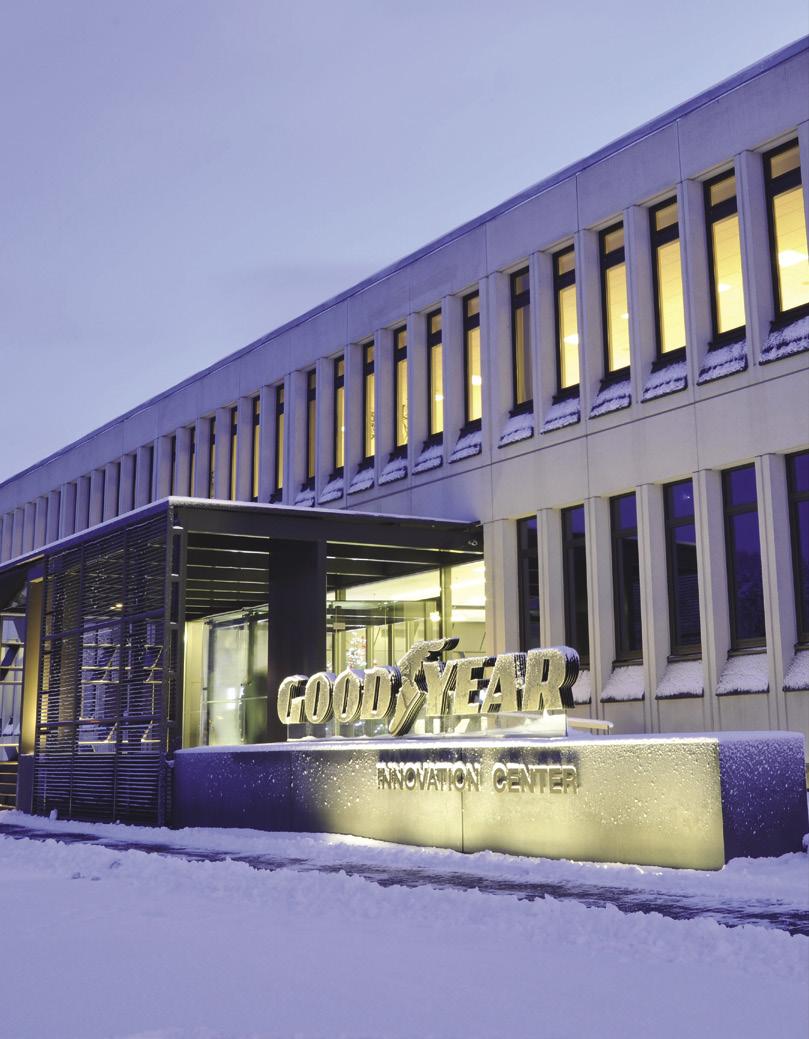
GOODYEAR
Goodyear operates two innovation centres in Akron, Ohio, and Colmar-Berg, Luxembourg, both of which strive to develop stateof-the-art products and services that set the technology and performance standard for the industry.
Established in Luxembourg since the 1950’s for its central position in Europe and location next to the tyre plant, which includes the production of prototypes, this research and development and industrial complex is the most diversified complex outside the United States.
Today, approximately 3,500 associates from over 80 nationalities are working across Goodyear facilities in Colmar-Berg, Bissen, and Dudelange. More than 1,000 associates are based at the Colmar-Berg site, consisting of engineers, technicians, PhDs, data scientists, designers, researchers, tech scouts, and business strategists, who support EMEA and Asia Pacific regions directly with consumer, commercial, and motorcycle tyre development. In addition, this facility also supports Goodyear globally with new technologies and beyond tyre innovations.
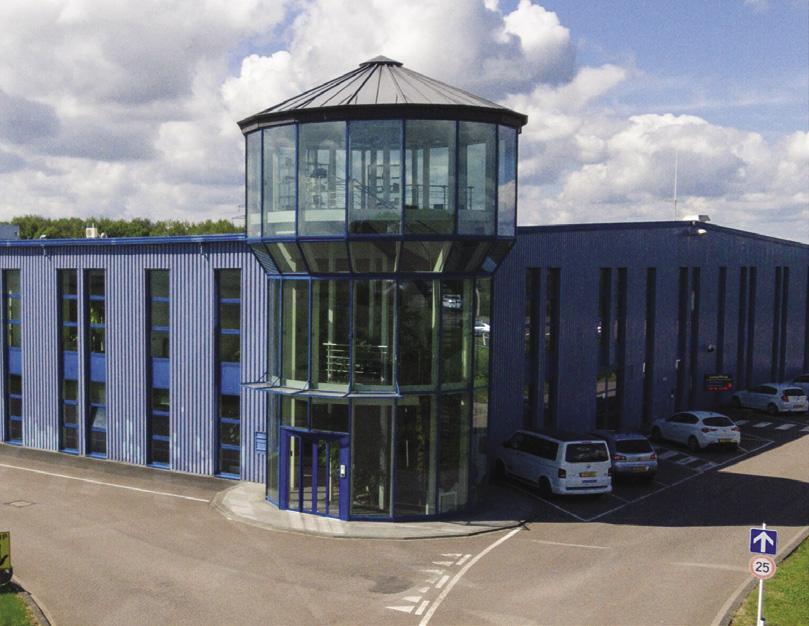
Q&A WITH BRIGADE ELECTRONICS
Answered by Emily Hardy • Job role UK Marketing Manager • Length of Service 15 Years
Q: How long has Brigade been in business and operating within the ‘Commercial Vehicle Industry’?
A: Brigade Electronics has been pioneering the cause of commercial vehicle and plant safety since it was first established over 46 years ago. Over this time, we have gained extensive knowledge and understanding of the problems our customers face, which now enables us to work alongside governing bodies to act as an industry voice and use our experience often in an advisory capacity, sitting on both legislative and international committees.
Q: What was the first product you introduced?
A: Our founder, Chris Hanson-Abbott, introduced the very first tonal reversing alarm to Europe in 1976 – at a time when vehicle safety systems were unheard of. The company went on to pioneer and introduce many of the safety systems we use today, including the first rear-view camera monitor system in the UK and the first white sound reversing alarm in the world. Brigade’s extensive portfolio includes 360 camera monitor systems, digital recorders, ultrasonic detection sensor systems, radar systems and of course reversing and speaking alarms. We are introducing more AI technologies such as Sidescan® Predict that can differentiate moving and stationary objects and can predict collisions. This reduces false alerts and significantly reduces driver overload.
Q: Are you solely UK based or international and if so, do you have chosen distributors?
A: We have nine subsidiaries working across the globe, and we also have a strong network of approved distributors, all chosen for their high level of service and expertise. Together we cover seven continents, distributing in over 80 countries worldwide.
Q: What is your main aim as a company and what is the primary focus of your products?
A: Preventing collisions and saving lives. Brigade is committed to making roads and worksites safer for all. Our products are designed to assist drivers whilst also protecting workers, pedestrians and cyclists. We strongly believe in a complementary range of passive and active systems to alert both the driver and the vulnerable road user of a potential collision.
Q: What are your best-selling products and why are they popular at present?
A: We find most operators choose to fit camera monitor systems, sensors and alarms as best practise, realising the importance of active and passive systems in aiding both drivers and the vulnerable road users. Direct Vision Standard legislation and industry standards, such as FORS, have encouraged operators to fit a basic level of safety equipment. Over recent years we have also seen demand increase for digital recording systems, which act as an accurate witness and provide irrefutable evidence in the case of an incident. In addition, many operators are also seeing costsaving benefits of fitting recording equipment, such as reduced insurance premiums.
Q: Do you offer aftercare/after service?
A: Yes! Our Onsite Service Warranty package helps keep Brigade products in working order. In the unlikely event of product failure, we will send a local Approved Fitter or Brigade Service Partner (BSP) to your vehicle within the UK to repair or replace the faulty part and get you back on the road as quickly as possible. The Onsite Service Warranty is in addition to our standard and extended warranties and provides peace of mind, especially for larger fleet operators or vehicles working on sites throughout the UK. We also have a comprehensive product support area on our website and a technical helpline manned by a team of engineers.
Q: You have a network of ‘Approved Fitters’, do they undergo special training or tests to be part of the wider Brigade team?
A: Brigade Approved Fitters are a nationwide network of carefully chosen partners who supply product, installation service and support to Brigade customers. The fitter network enables us to provide installation services across the country to large fleets or businesses operating vehicles at multiple sites throughout the UK. Approved Fitters receive ongoing training from Brigade’s own product managers and applications engineers, and are required to provide evidence of compliance to work in partnership with us. Quality product is only effective if fitted correctly.
Q: You offer numerous warranty cover and in some cases ‘Lifetime Warranty’, you must be very confident in your products?
A: Brigade safety products are managed from concept to production and tested to beyond industry standard to achieve quality and reliability. They are pushed to their maximum capabilities and tested to beyond relevant international standards and environmental safety. Products are only released once we are confident that they are fit for purpose. Whatever the product or technology, it must pass rigorous and comprehensive testing before we consider it suitable to be included in our portfolio. A closely controlled design and manufacturing process, plus in-house research and development, is all managed by a proficient engineering team that sets us apart from the competition. They ensure our products are, and remain, at a consistently high standard.