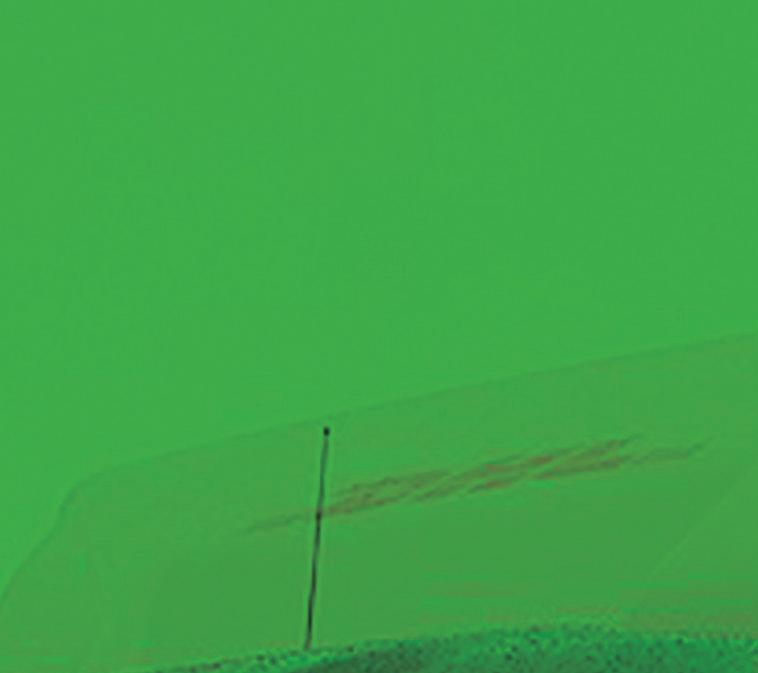
10 minute read
33 PREPARING FOR TRUCKS OF THE FUTURE
Preparing for trucks of the future
Whether they are powered by electricity, hydrogen, gas or something else entirely, transport fleets are going to undergo a transformation over the coming years Words: Steve Banner
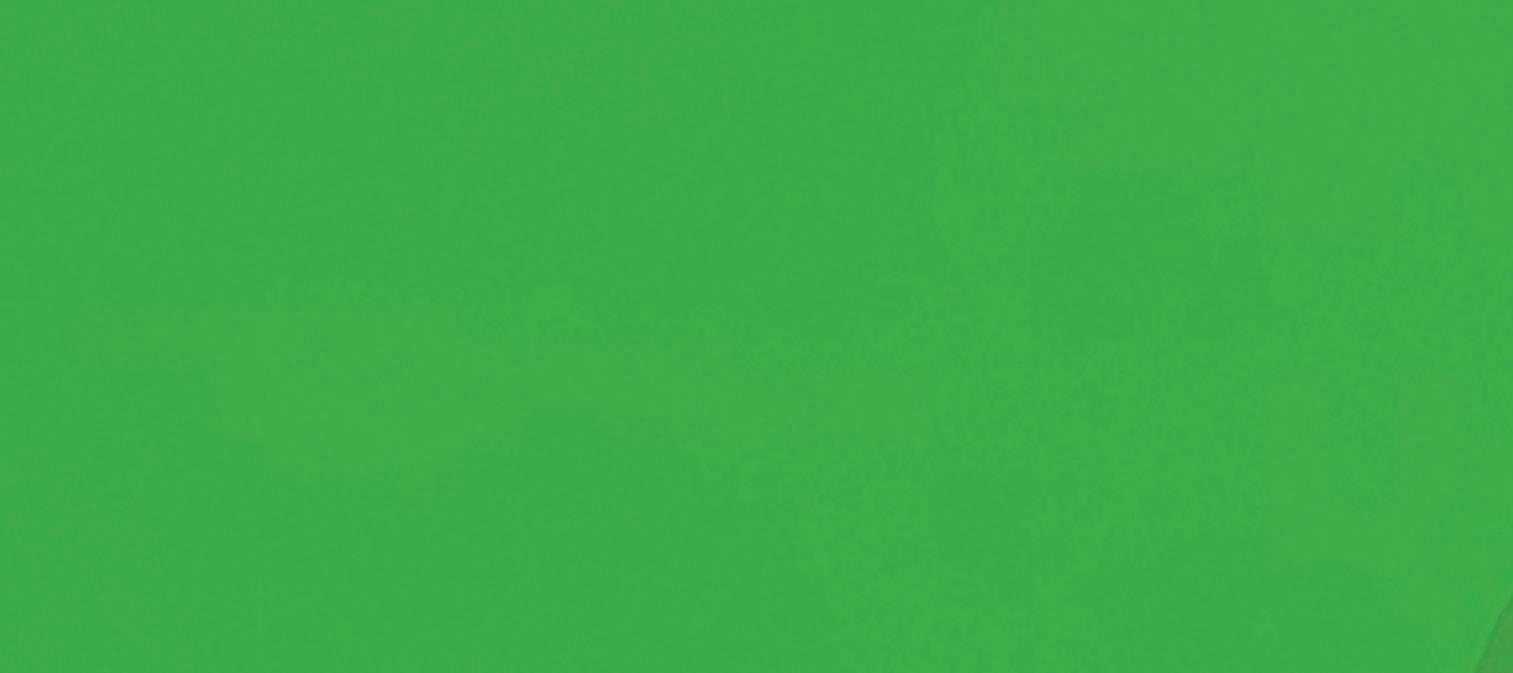
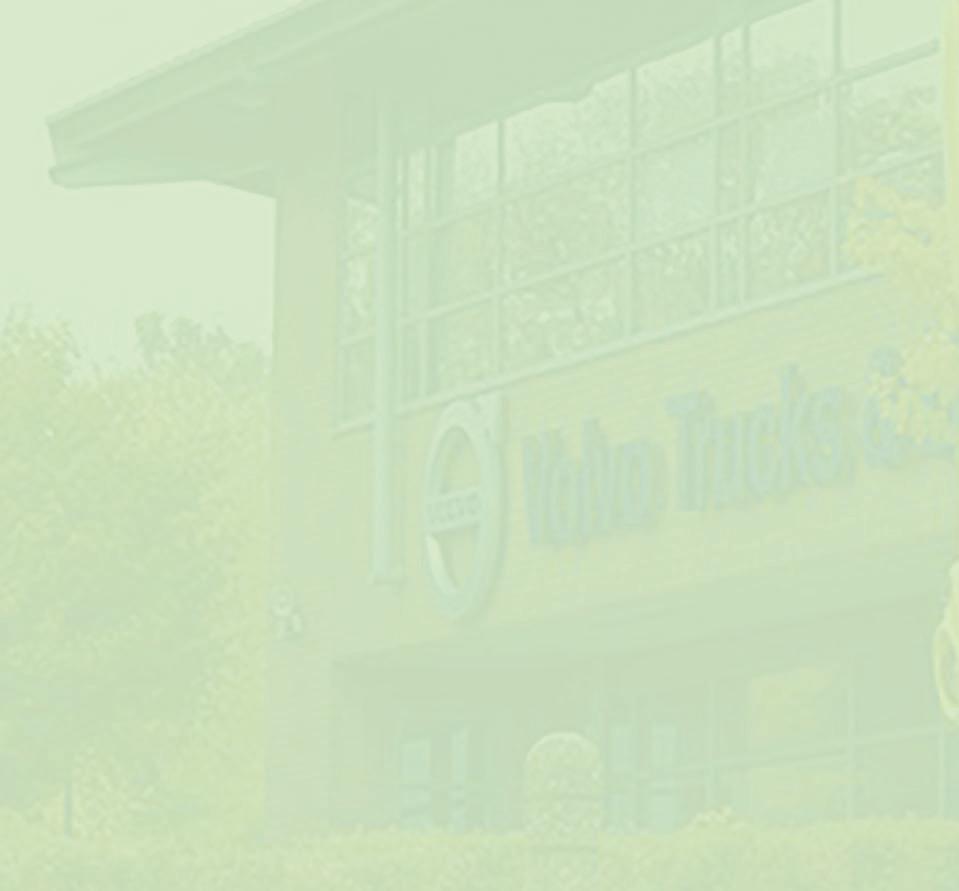
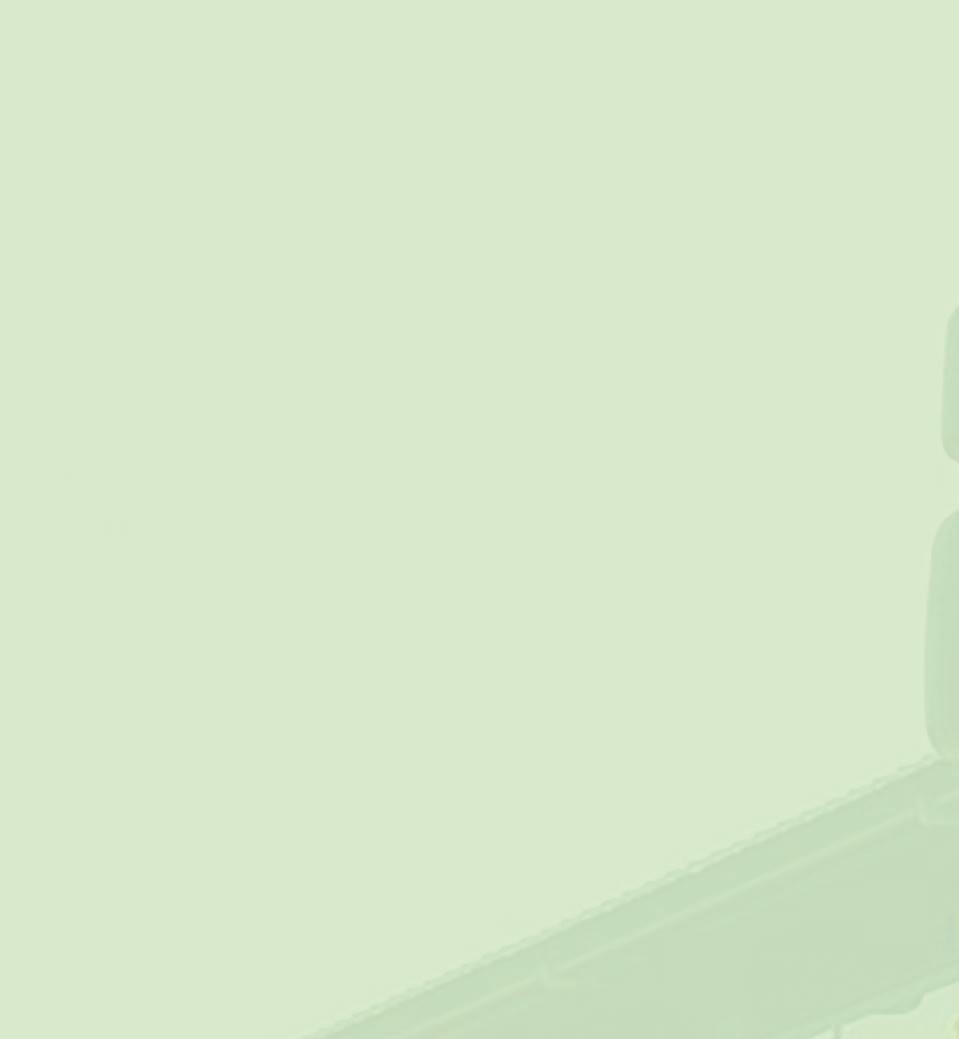
Haulage and distribution centres will change enormously over the next 10 to 15 years as diesel trucks are gradually displaced by electric models. Trucks powered by hydrogen fuel cells may have a role to play too.
One unavoidable consequence for existing centres will be disruption as bulk fuel tanks are torn out and battery charging points – and the electricity cables needed to feed them – are installed. Such upheaval need not plague sites being constructed now, however, if some of the basic infrastructure that will be needed is built in prior to the power shift that is undoubtedly coming.
Think of the needs of the people who work there, including warehouse order pickers and forklift truck drivers, advises Simon Cox, Head of Sustainability at Prologis UK. It constructs major distribution centres which are then occupied by some of the country’s best-known businesses, including Tesco and Sainsbury’s.
“In future, more and more employees are likely to come to work in electric cars,” he points out.
What responsible employers should therefore consider doing is putting in below-the-ground channels that can accommodate cabling to support low-speed charge points that can easily be installed as and when required. Workers will be able to plug their vehicles into these points so that they can be trickle-charged while they work their shifts.
Doing the ground work
Put the underground channels and any related subterranean equipment in now and the site will not have to be dug up to install them when they are actually needed.
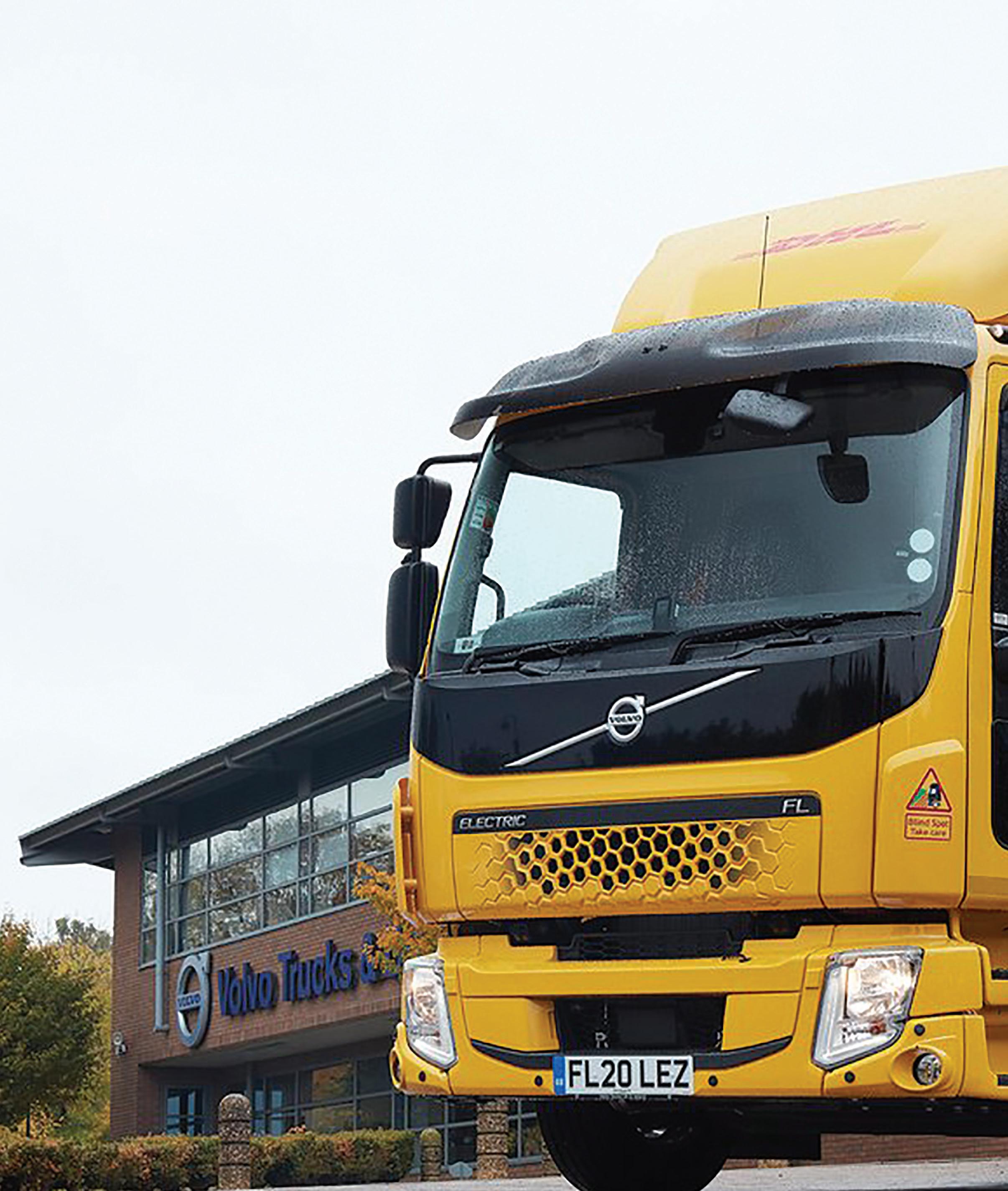

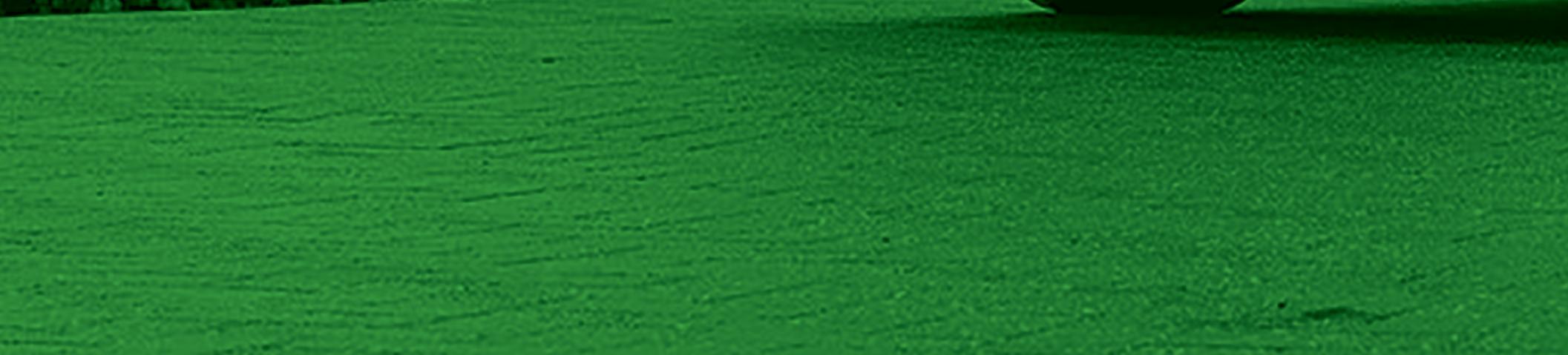
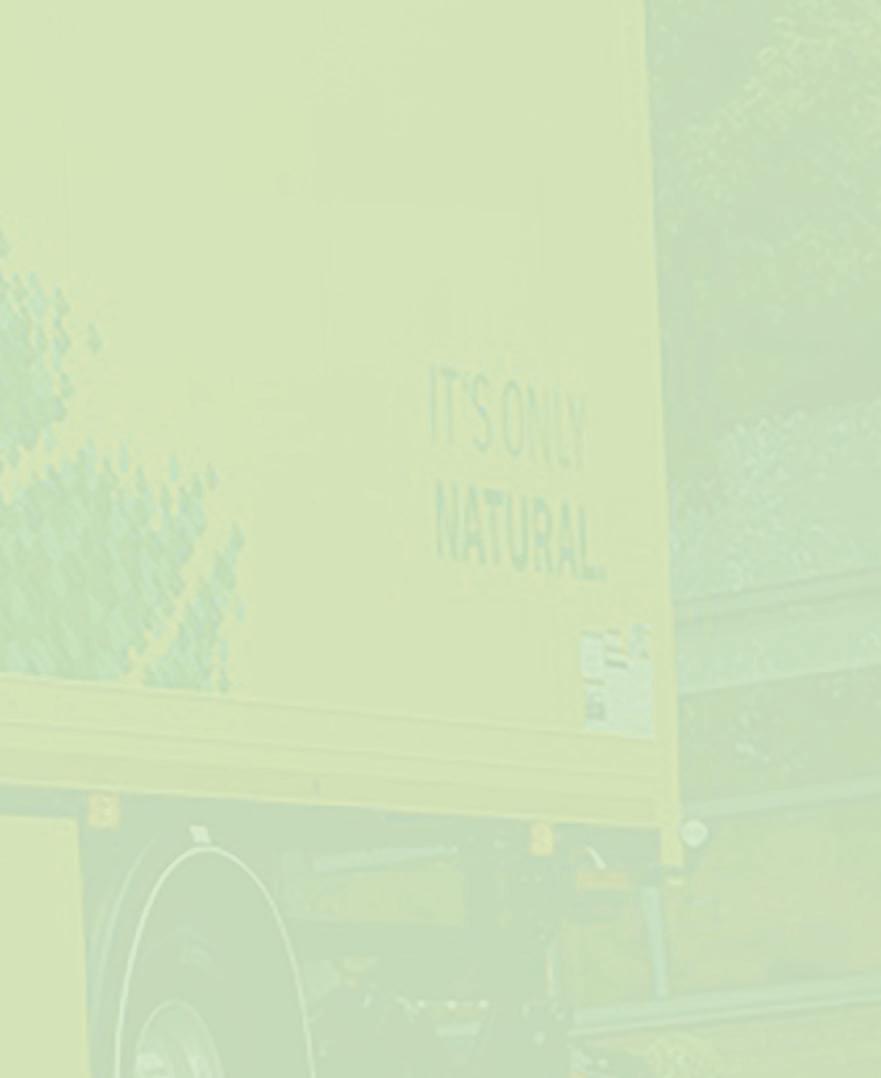

“The ability to recharge their vehicles while at work could be offered to employees free as a benefit, or at a discount subsidised by the company concerned,” Cox suggests.
The same underground network could be used to deliver power to electric vans that businesses will increasingly be using for last-mile delivery.
Individual parking slots may not necessarily require above-the-ground charging posts says Cox. “One option could be to install an inductive charging system,” he suggests – an approach similar to the wireless smartphone charging system now offered in some vehicles.
How about ensuring electric trucks can be recharged? Once again, underground channels will have to be in place to house the cabling – and once again, anybody designing new premises should ensure they are installed in advance.
“Thought needs to go into how the cable runs are planned,” says Adam Boyes, Property and Facilities Manager at Volvo Group Real Estate UK. “It’s highly unlikely that all the trucks will come back at once and go out again at the same time, meaning that charging could be staggered and parking planned accordingly.”
The amount of extra power required at a site to cope with electric trucks is less straightforward to predict. “That will depend entirely on the chargers you are proposing to install,” says Boyes. “A 150kW DC fast charger will obviously require more power than a 22kW AC overnight charger so you may need to have the supply upgraded and a substation may have to be put in.”
Be safe and be smart
The exact details of what needs to be done will depend on how much power is coming into the premises to begin with, and an expensive upgrade may not be required. That is more likely to be the case if a smart grid system is installed that schedules charging overnight, and carefully manages it to ensure that any vehicle required the following morning will have enough juice in it to handle a day’s work.

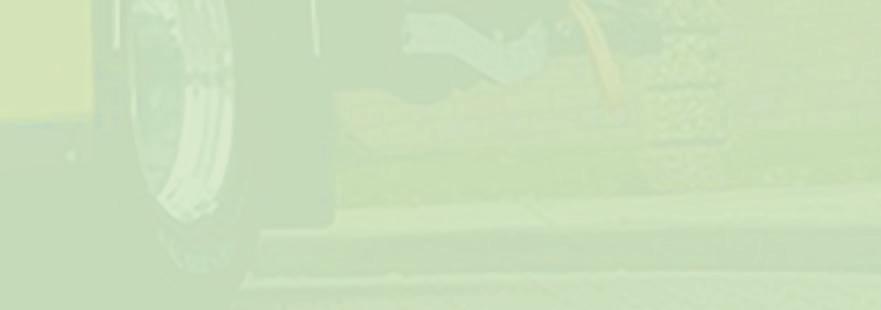
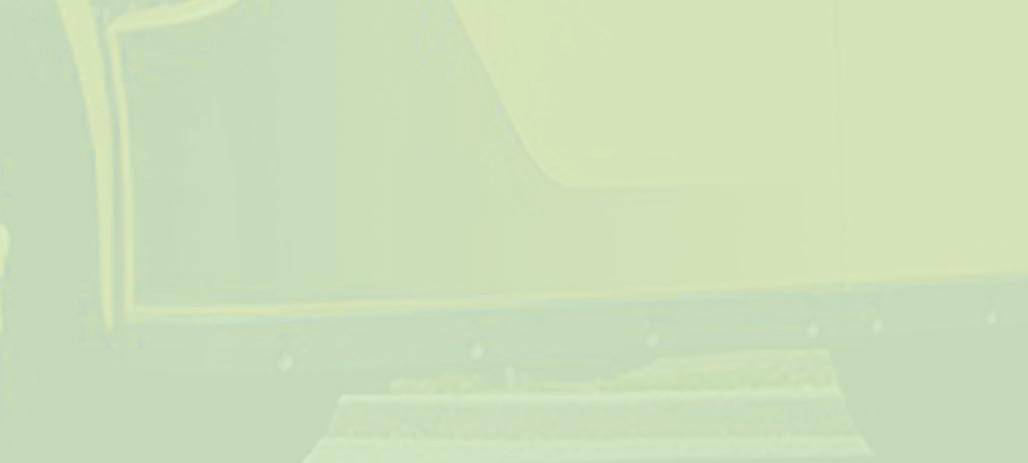
cont.
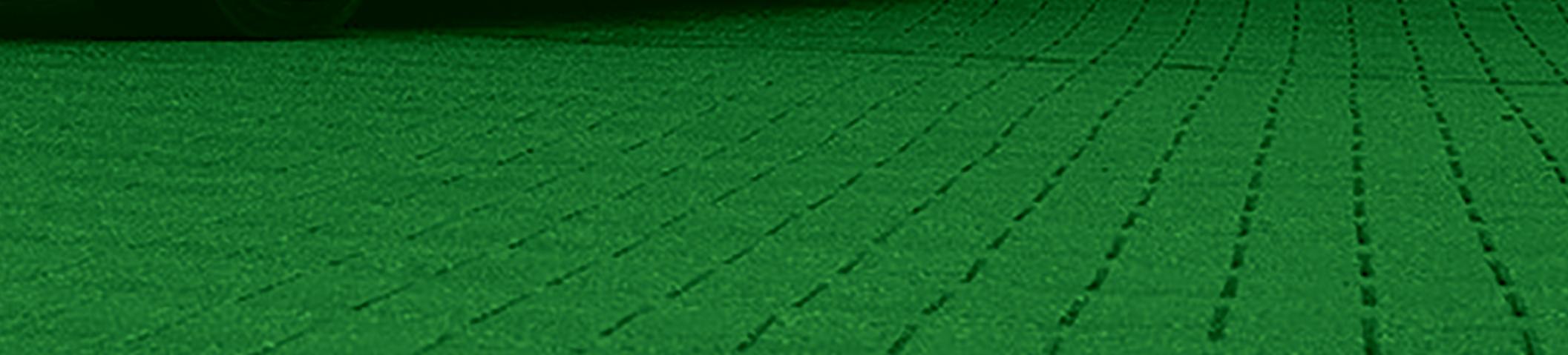

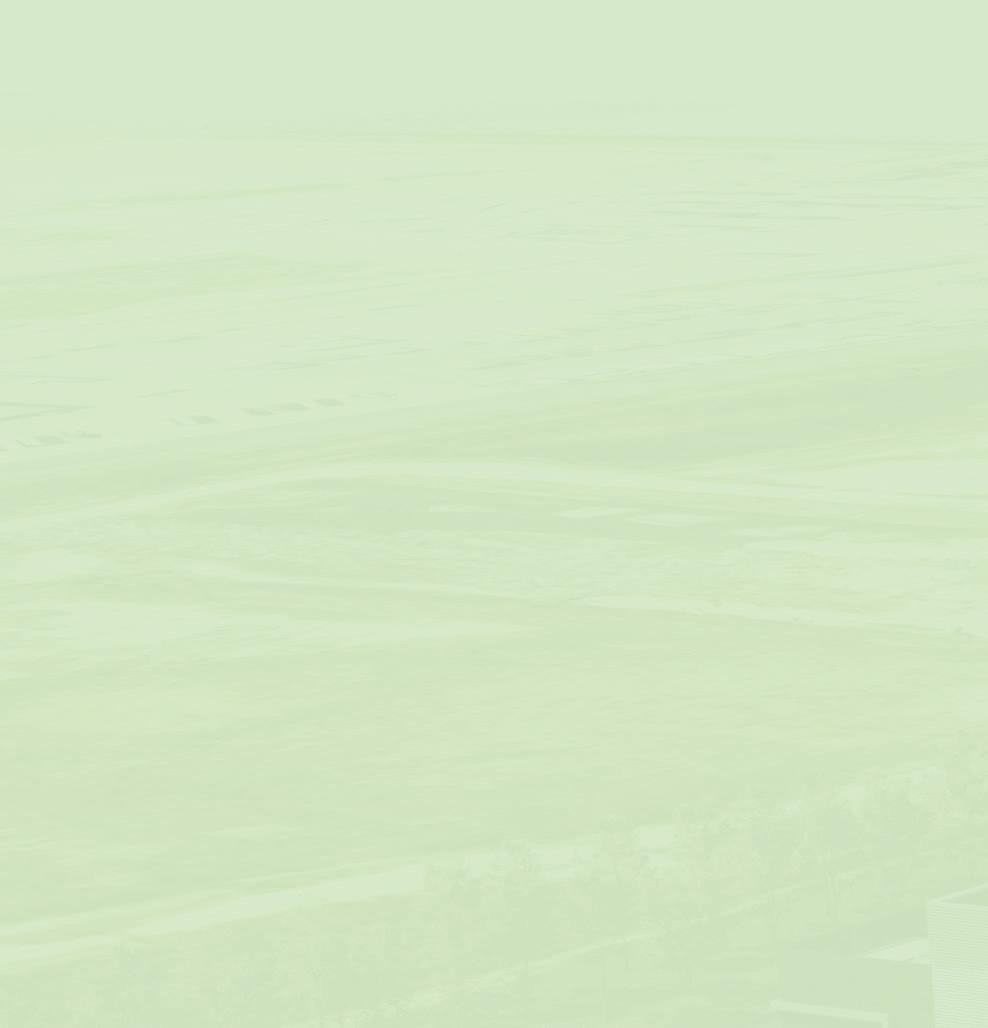
It can be accompanied by an energy storage system potentially created out of batteries no longer suitable for use in vehicles. They can hold lowtariff electricity which can be called on as and when required.
Cox suggests that a different approach may be required to charging trucks than the one that it is typically advocated by truck makers. It is one that is regularly used to keep electric forklifts running.
In this scenario, warehouses hold racks of batteries that are fully charged.
When a forklift’s battery is on the verge of running out of power, it is removed and swapped for one that is charged up. It then goes back onto the battery rack to be replenished.
“Swap the batteries on electric trucks and it will help to keep the charging load on the site constant,” Cox says. “If you keep your load flat, then your power will cost you less.”
Site designers will need to ensure that sufficient space is allocated for battery banks, he says. Bigger substations and transformers may also still be needed at some locations. However, the impact of the additional power draw may not be quite as great as is supposed, Cox contends.
“In the past, lighting used to account for 90 per cent of a distribution warehouse’s electricity requirements,” he says.
“That percentage has reduced dramatically in recent times thanks to the introduction of motion and daylight sensors and LEDs, but the electricity capacity remains in place.
“That gives the site’s occupant some headroom when it comes to charging vehicles,” adds Cox.
Battery swap shop
Replacing a 26-tonner’s electric battery pack would be far more problematic than swapping a forklift’s, given its size. It would also require the truck to be designed in such a way that it could be done quickly and safely by workers who are unlikely to be fully-trained workshop technicians.
Some distribution sites may elect to offset any increase in the power they need by producing their own. Solar panels mounted on what may be acres of unused roof space could represent one possibility, as could a wind turbine if the location is suitable and there is sufficient room. They could help premises become carbon neutral or even carbon negative.
Trucks fitted with fuel cells could be employed on long-haul work in the future, so thought may have to be given to allocating space to dispensing and storing – or even producing – hydrogen. As far as
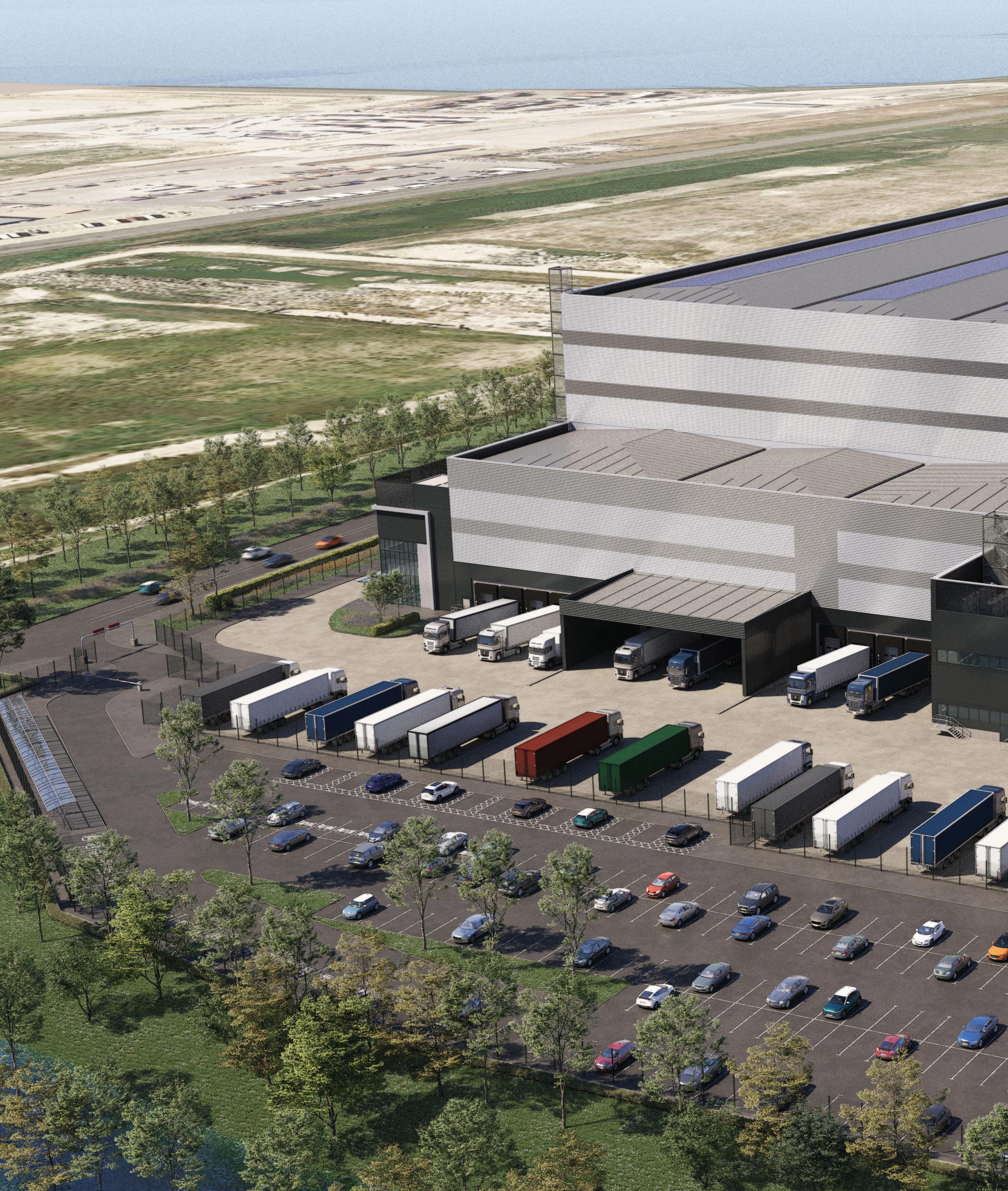
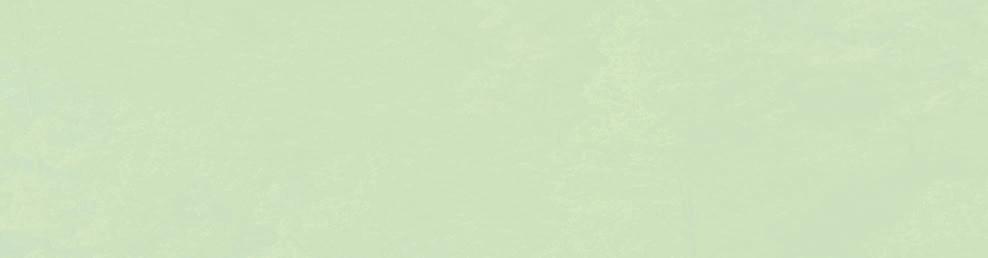

industrial parks are concerned, one option could be to create a centralised hydrogen production and refuelling hub that can serve a number of clients.
Such a hub is being created in Holyhead in North Wales backed by the Isle of Anglesey County Council and the Welsh Government’s Local Transport Fund and supported by clean energy solutions provider Logan Energy. It should be in service by 2023.
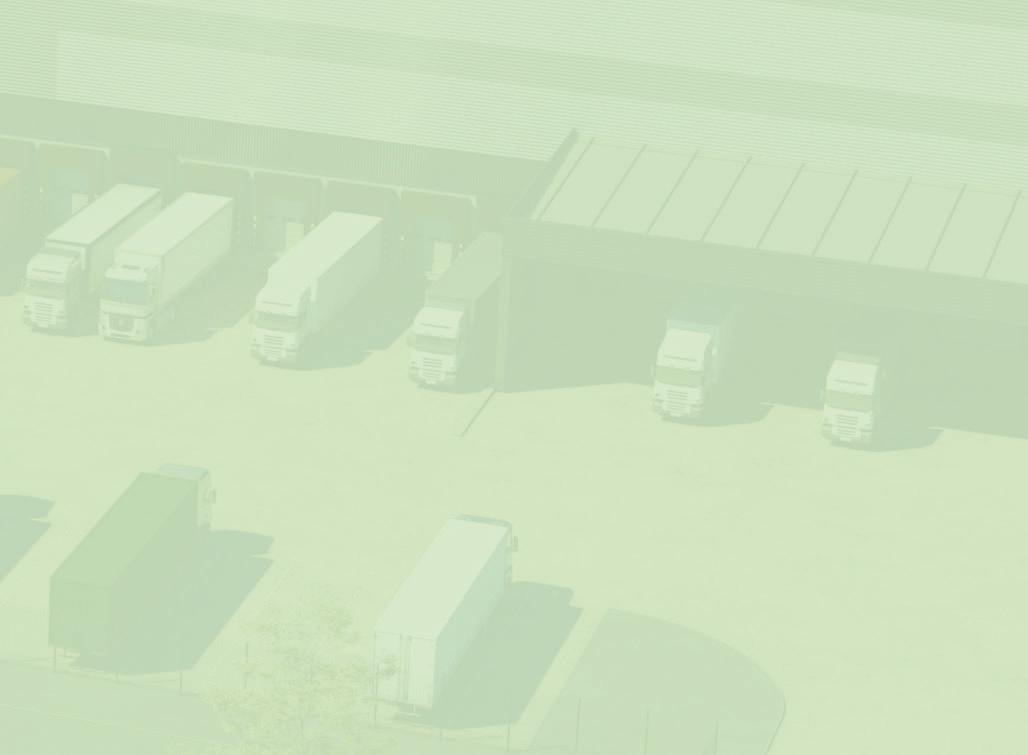
Is hydrogen the new hope?
Hydrogen production requires green credentials in order to be viewed as truly environmentallyfriendly. Irish gas and electricity supplier Energia has managed to achieve this goal.
The company makes hydrogen using an electrolyser at a wind farm it operates in County Antrim. The fuel is then delivered to bus operator Translink in Belfast in specially-designed trailers supplied through Logan Energy for use in its fuelcell-powered double-deckers.
“There is no upper limit to how much hydrogen you can store,” says Bill Ireland, Logan Energy’s Chief Executive Officer. “By following industry guidelines and regulations hydrogen can be safely stored at transport depots.
“Rules include integrating stand-off distances between stored hydrogen and any potential sources of ignition – and keeping storage facilities at least 8m away from buildings,” he adds. “Planning consent is needed and, if you are storing more than five tonnes of hydrogen, there are additional regulations to follow. But depots can be designed with these in mind to support the rollout of renewable fleets.”
Operator experience of electrics
While views on the energy strategy that should be adopted may differ, businesses that fail to plan ahead and embrace the changes that are coming over the horizon will undoubtedly suffer. That is something FORS operator DHL has already recognised – and it is responding accordingly.
Last autumn the company began trialling an electric Volvo FL 16-tonner in London.

“We’re encouraged by the results and we’re committed to the widespread adoption of alternative fuels to achieve our target of zeroemission logistics by 2050,” says Ian Clough, Managing Director, Network Logistics and Transport, UK and Ireland, DHL Supply Chain.
“To support this goal, electric charging facilities are being incorporated into all our new sites, with the supporting ducting future-proofed,” he says. DHL is also calculating how much more power its sites will need, with self-generation one of the options.
Solar and wind power are undoubtedly environmentally-friendly, and have a further advantage so far as accountants are concerned. Once the necessary technology to make use of them is installed, the sun and the wind come free.

No transport company will complain about that. end

• Simon Cox • London Gateway • Volvo electric truck
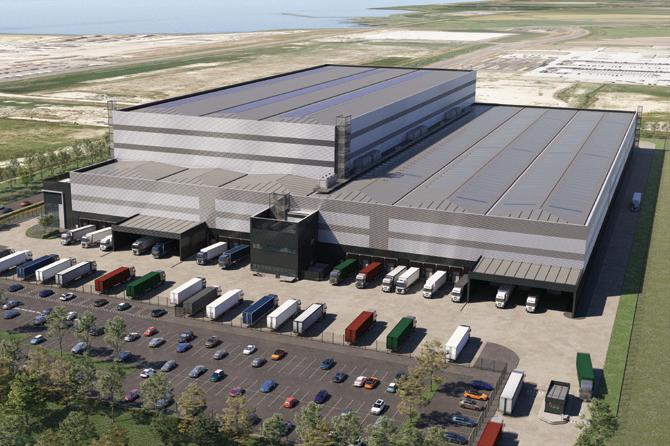


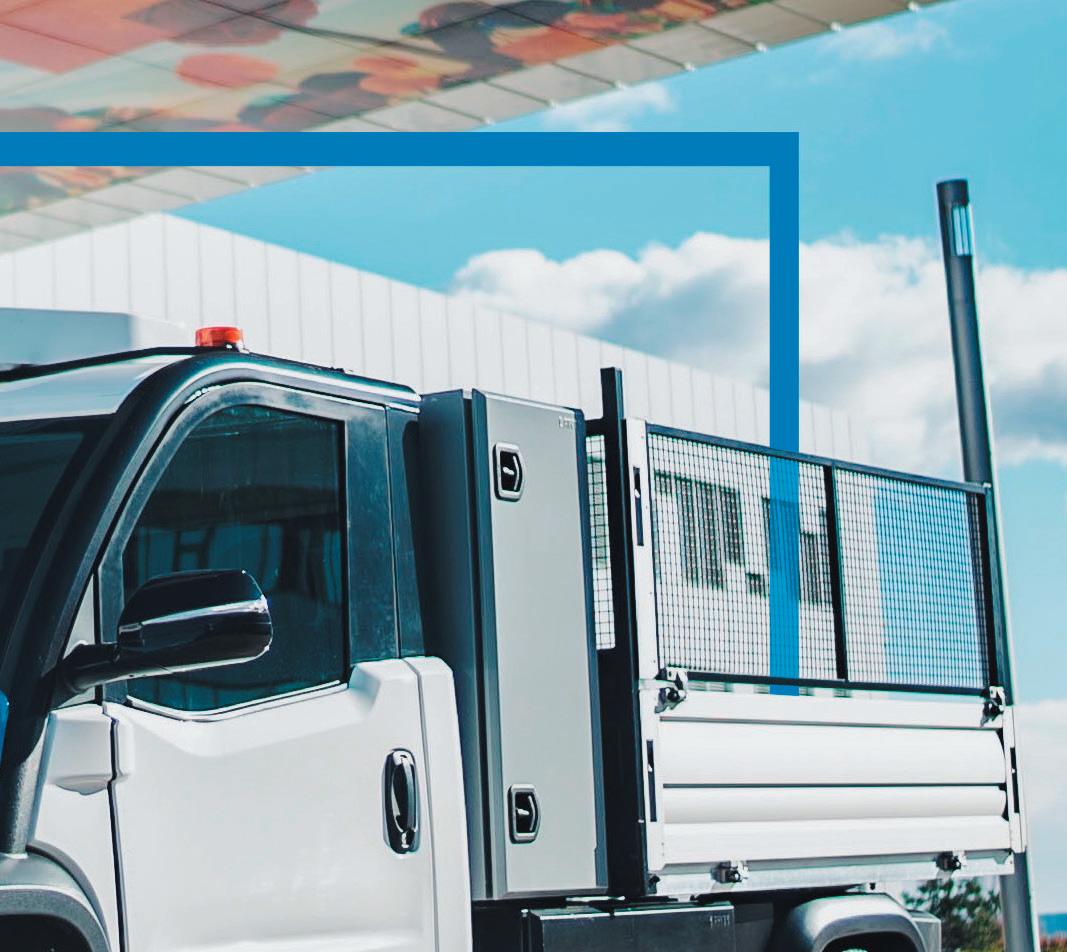
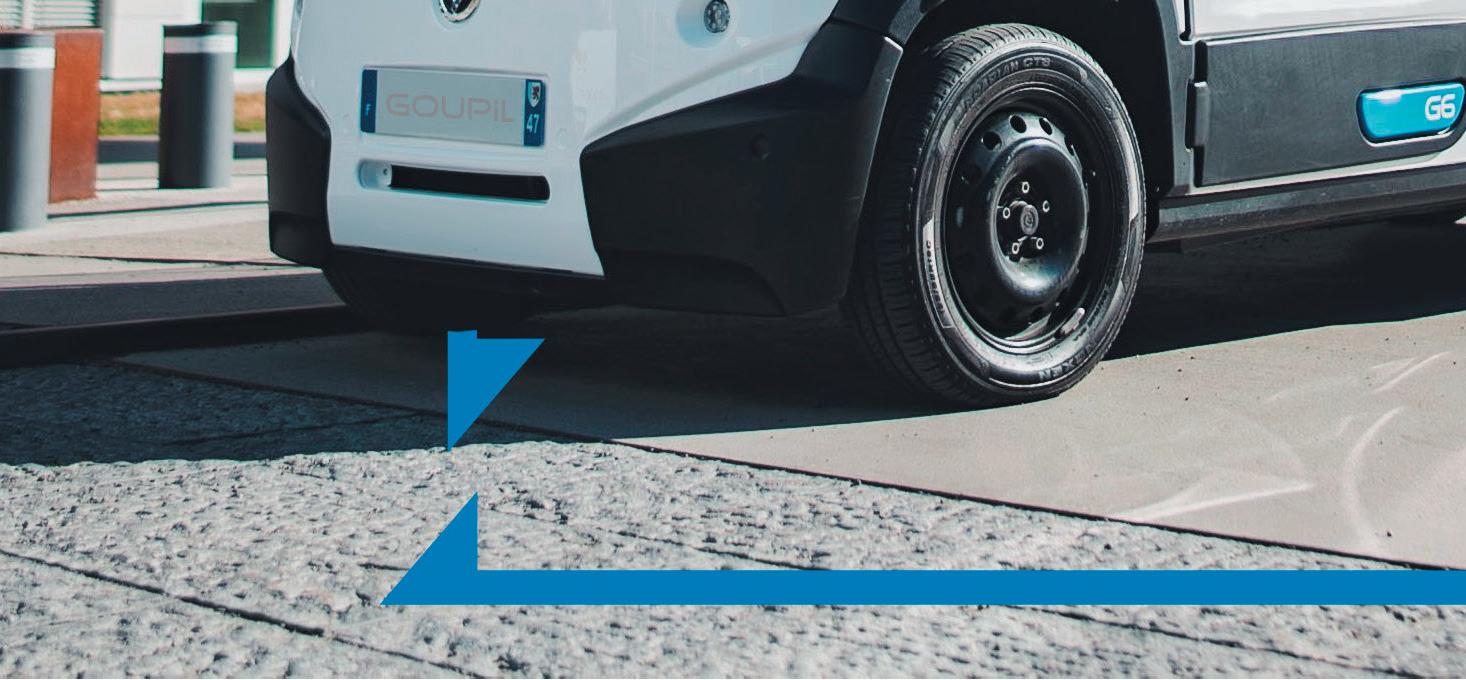
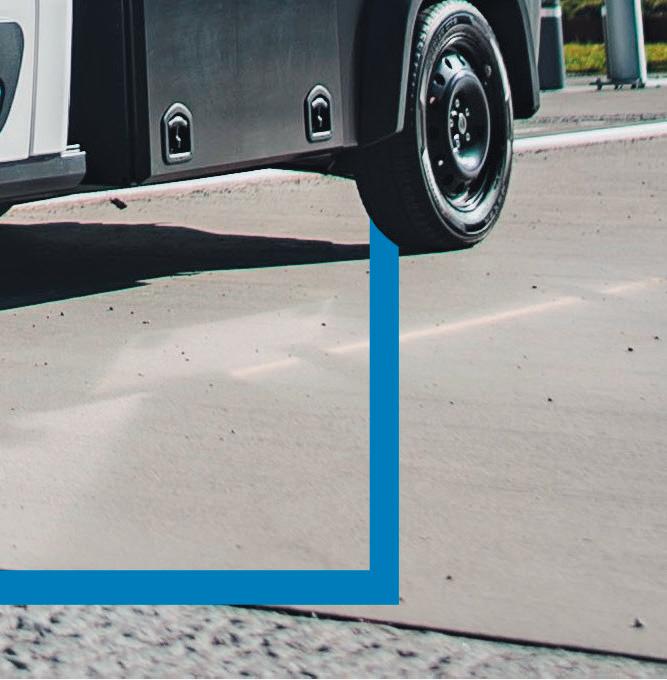
THE NEW GOUPIL G6 100% ELECTRIC ZERO EMISSIONS
Building electric utility vehicles for 25 years, the latest and the largest model in the range offers a generous payload of up to 1,050kg for the pick-up and an impressive 9m3 for the cage body. With a vast array of body options, the Goupil G6 is suitable for various business needs and applications whilst delivering environmental and sustainable operations. Designed to fulfil everyday tasks, the 100% electric G6 comes with a 28.8kWh lithium battery providing a 93-mile range.*
SALES@BRADSHAWEV.COM | 01780 782 621 WWW.BRADSHAWEV.COM/GOUPIL-ROAD-VEHICLES
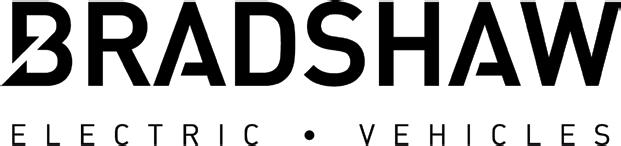

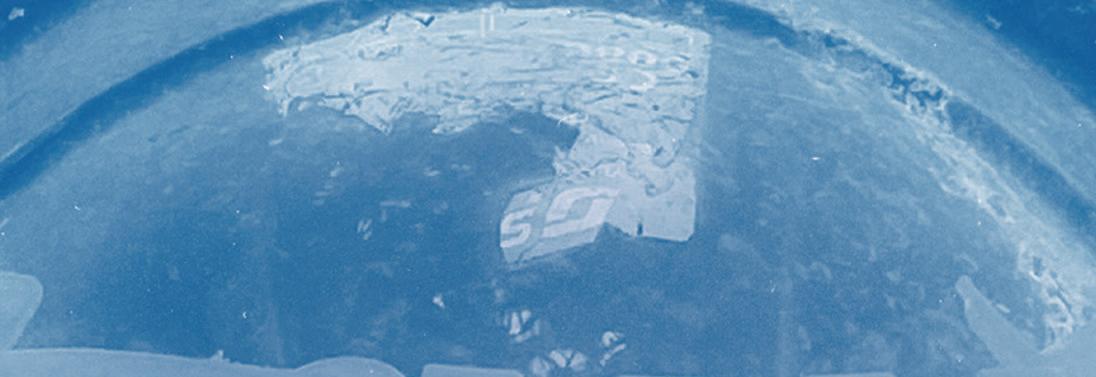
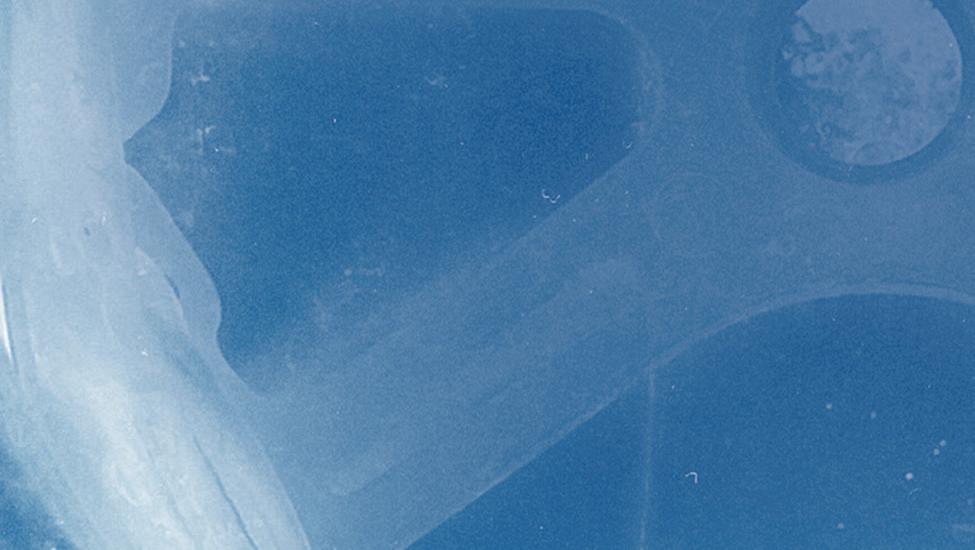
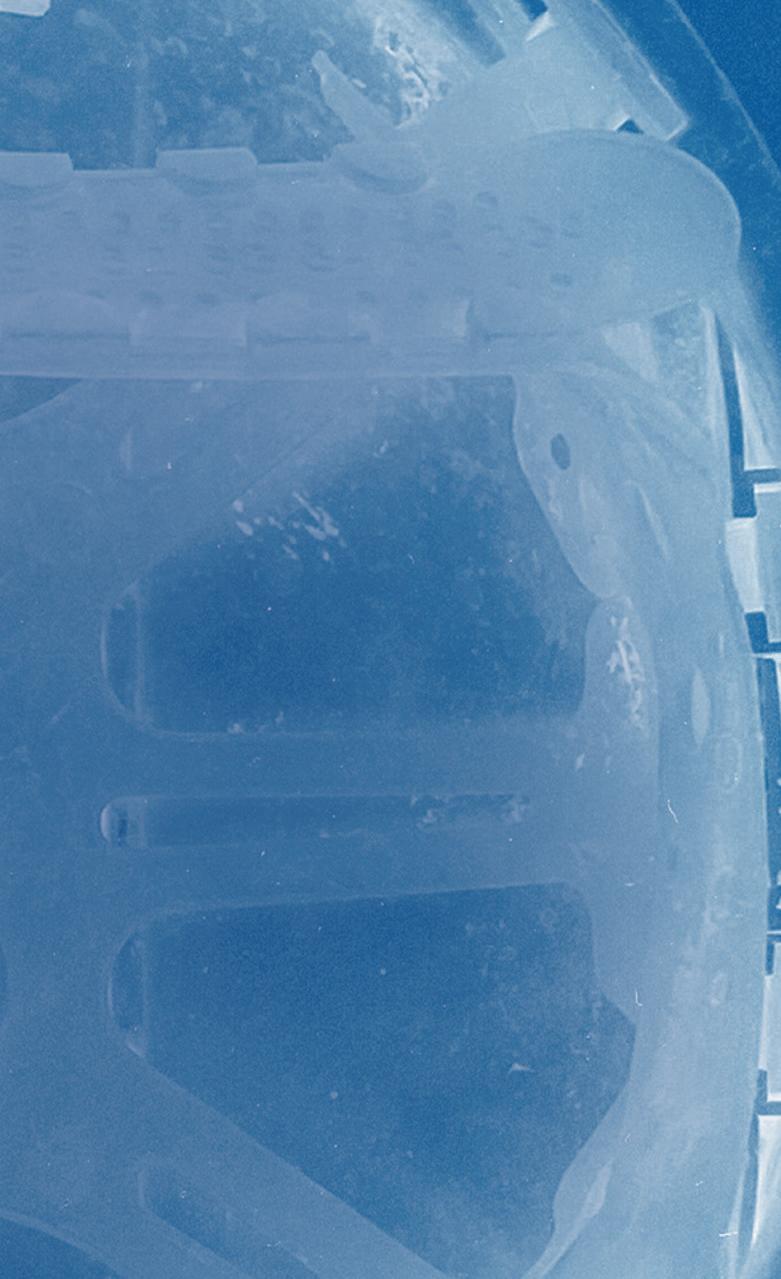

He was our big mouth - he’d always have an answer for everything, except for why he should still be here.
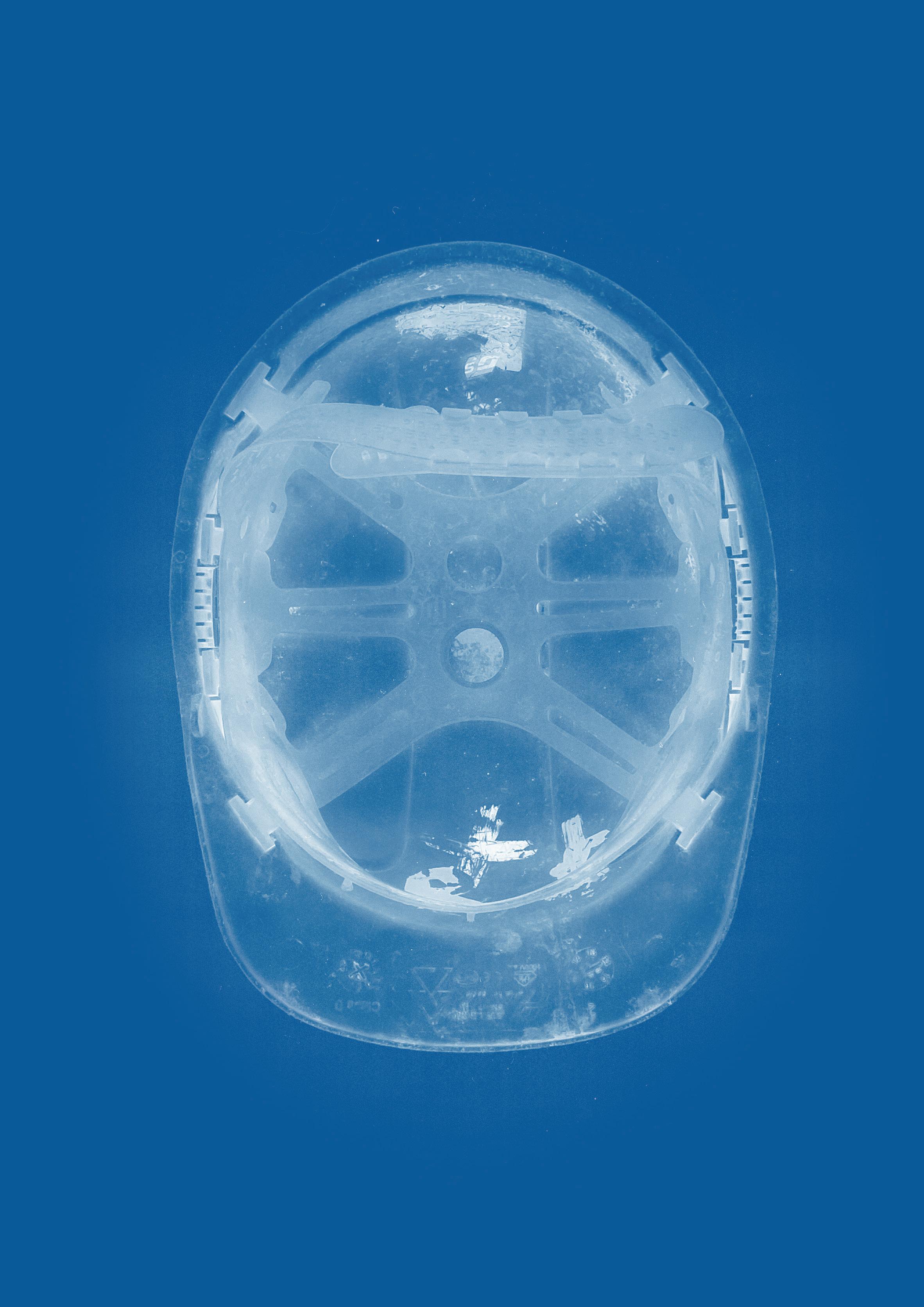
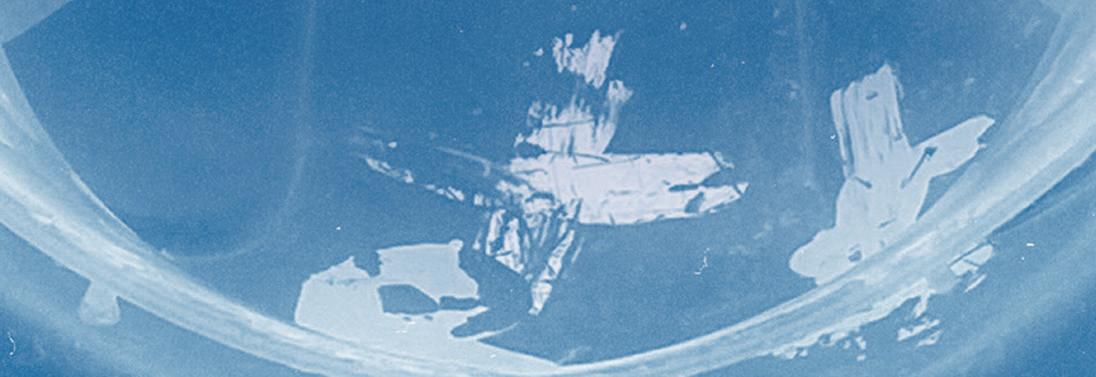

Our industry can be physically and mentally tough. Together with our partners and supporters, the Lighthouse Construction Industry Charity are working night and day to ensure that no construction worker or their family feels alone in a crisis. So if you or a workmate need support, we are always here to help.
