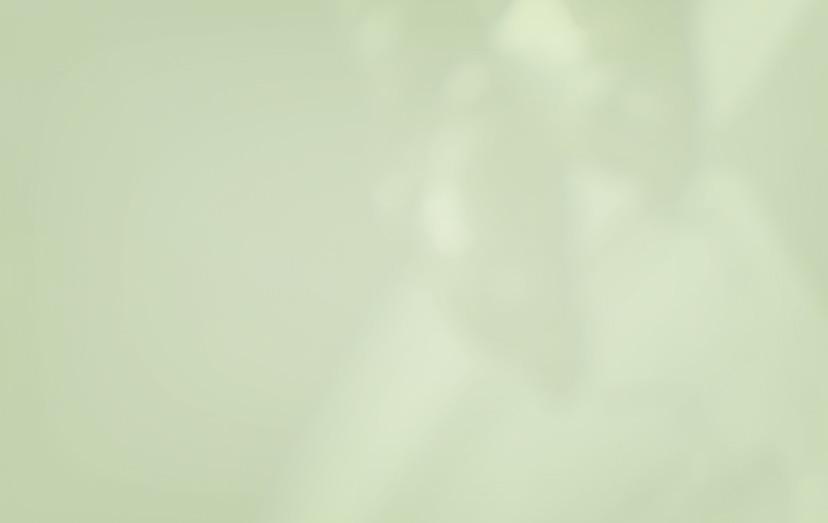
3 minute read
TREADING THE RIGHT PATH
Extending the life of premium tyres.
The Michelin name
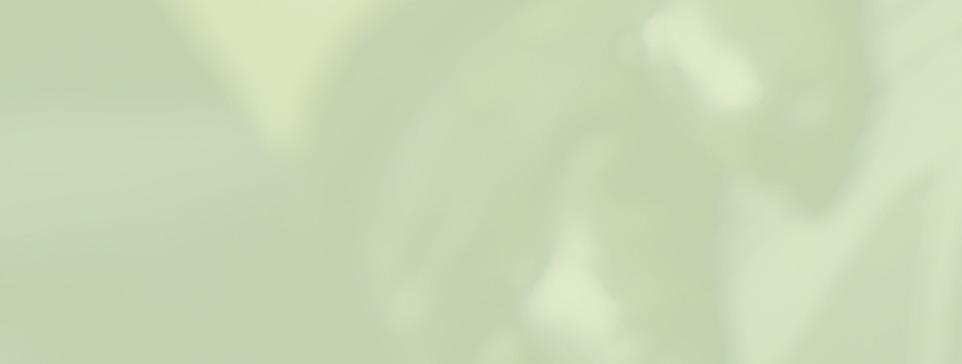
thas long been synonymous with Stoke-on-Trent, but few probably realise that sitting just outside the city centre is one of the most advanced truck and bus tyre retreading facilities in the world, with the capacity to manufacture up to 300,000 retread tyres annually.

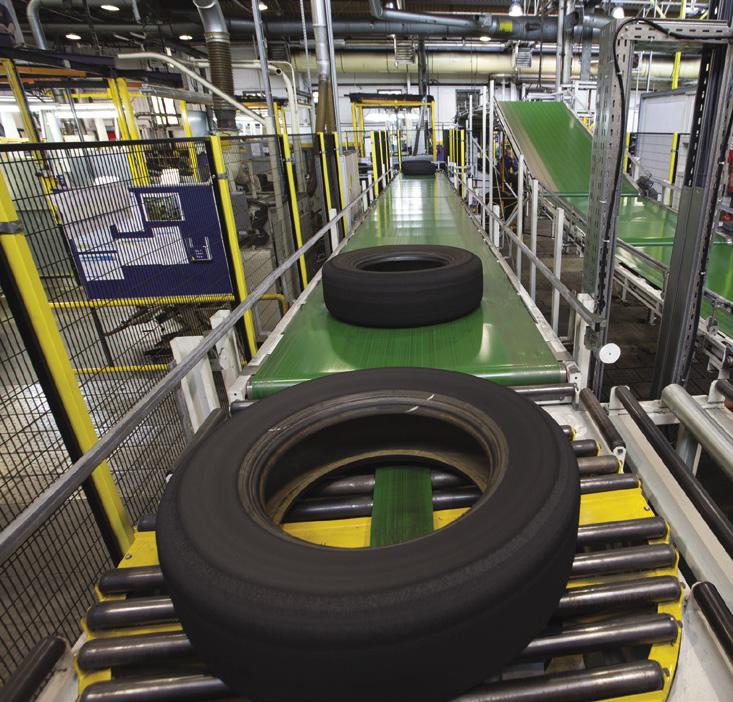
For the most environmentally and cost-conscious fleets this is significant because a retread truck tyre uses 70% fewer raw materials in the manufacturing process, making it significantly cheaper than a new tyre and contributing to the drive for sustainable transport.

The site’s presence – just a stone’s throw from J15 of the M6 - also supports UK manufacturing with the majority of the tyres manufactured in Stoke remaining in the domestic market.
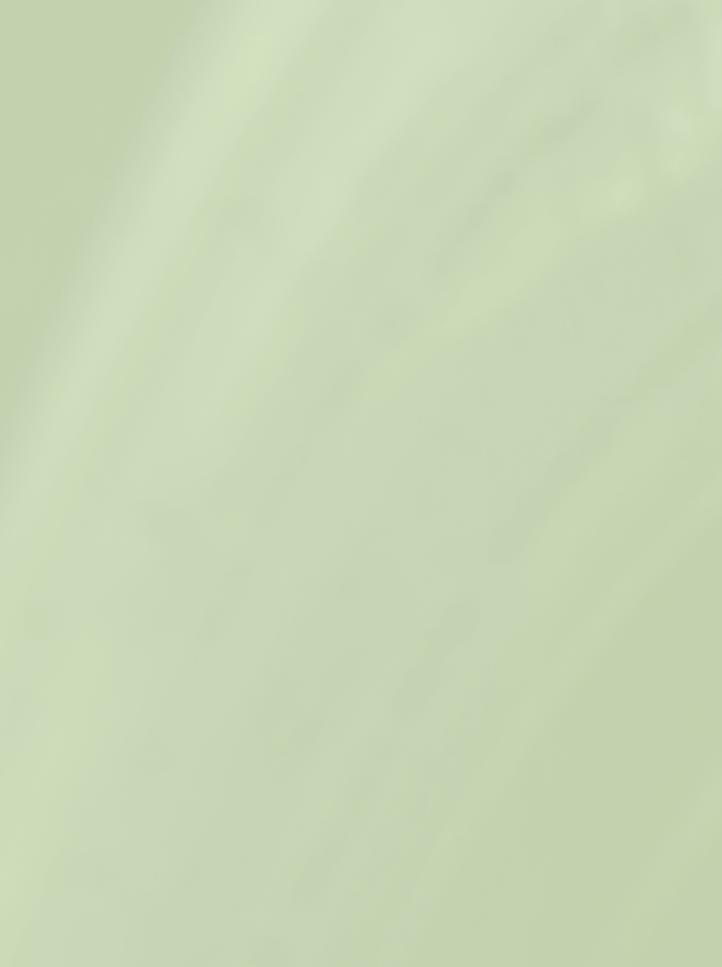
Azeem Khan, Michelin’s UK & Ireland Retread Manager, says: “We believe in a future where every truck rolls on fuel-efficient tyres, offering multiple lives in service. That’s why we’re so focused on manufacturing quality retread tyres as this approach directly supports the government’s target of reaching net zero transport emissions by 2050.”
Michelin says its Remix tyres (the name it gives to a retread tyre it produces on a first life Michelin casing) will give the same mileage potential as a brand new Michelin tyre, albeit the cost is around 35% less. And for this saving, operators can unlock a 100% increase in mileage potential from the same casing, whilst also reducing the waste sent for recycling by around 50kg per tyre.
Commenting on market demand, Khan explains: “More and more fleets are talking to us about the benefits of retreads – even those businesses which have previously always run a new-only policy.”
But that’s not the only factor driving up demand. The other, Khan says, is consolidation amongst 3PLs.
“Larger fleets tend to place much greater focus on sustainability, and as more small- to medium-sized operators are acquired by the bigger players, so their fleets grow, and the demand for retreads rises.
“In many cases it’s being driven by the big blue-chip customers putting pressure on the 3PLs to drive down carbon footprints at every stage. Put simply, they want reassurance that their logistics operations are being run as sustainably as possible.”
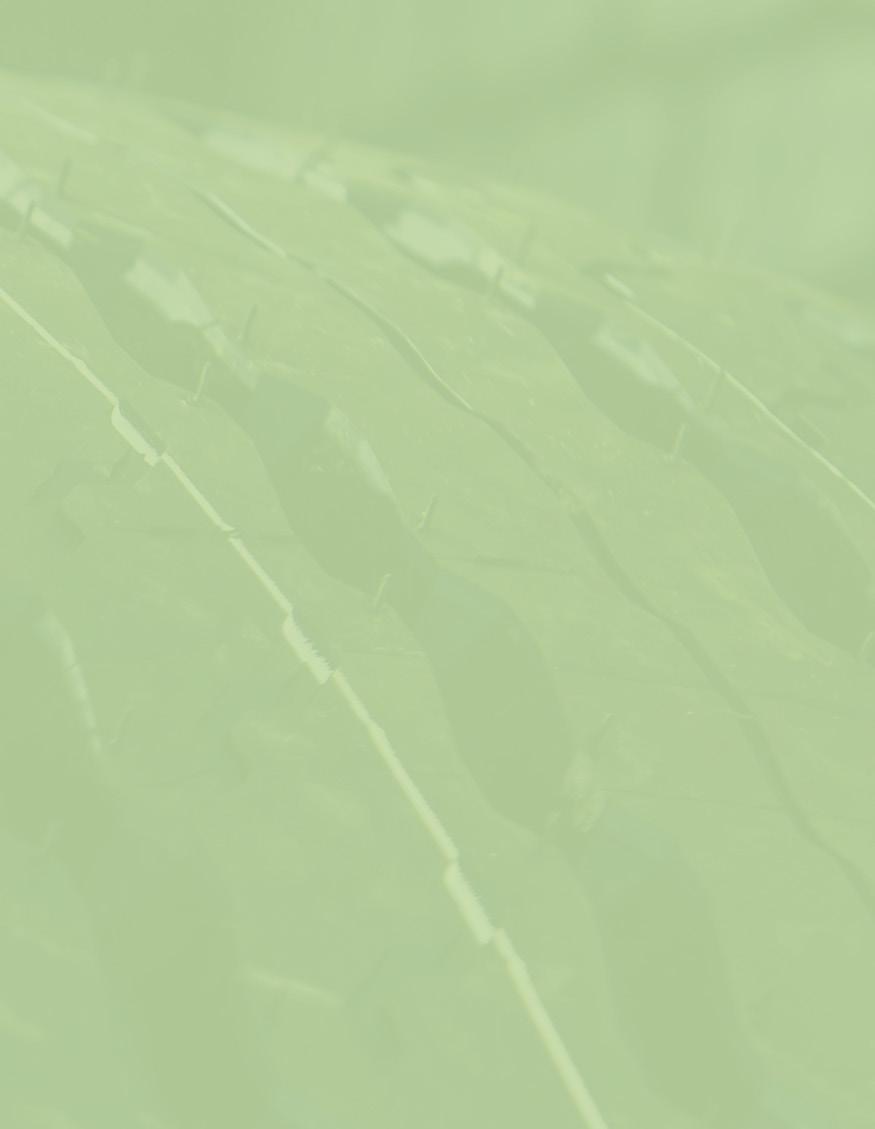
But unlike buying a new tyre, an operator can’t just call up a truck tyre dealer and buy a quality retread. Most manufacturers, Michelin included, operate a casing bank, requiring customers to deposit a worn casing in the bank for retreading, before taking a finished retread tyre back out.
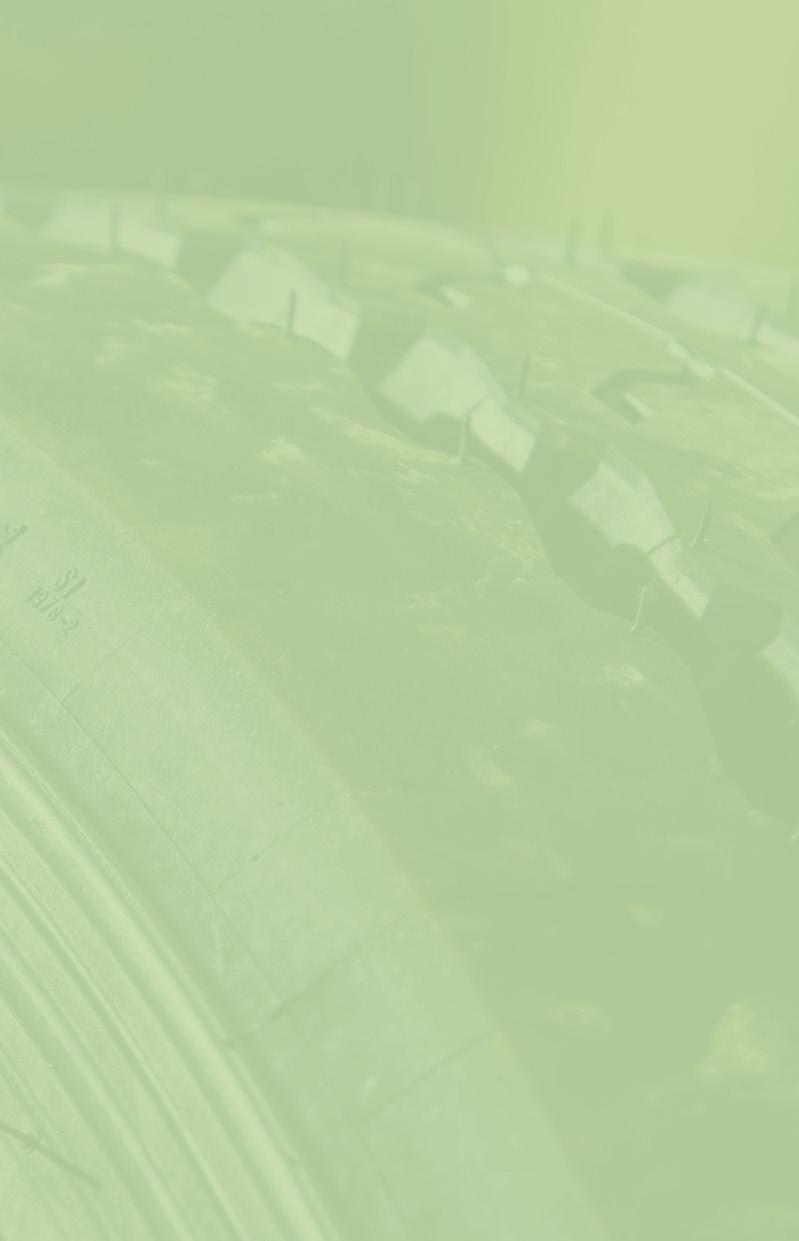
You also don’t get the same casing back again – but given Michelin’s rigorous casing verification process, which includes x-ray imaging and shearography to check the casing for damage, before the Remix process begins – there’s no need to either. If any damage is detected, the majority of it can be repaired by Michelin’s skilled team – with any casings declined for retreading being recycled.
During the complex, multi-stage, Remix process, Michelin will strip the original tread away to leave between 2-3mm of tread above the protective steel cords, before the new rubber is reapplied using materials which match those for new tyres. The curing process then follows with the retread tyres being baked for about an hour and a half with temperatures as high as 200 degrees Centigrade.
So retreading aside, how else can fleets adjust their tyre policy to unlock improvements in fuel efficiency and sustainability? Steve Chadwick, Brand Manager at Michelin, says: “The minimum legal tread depth for truck tyres is 1mm, but we still see fleets which change tyres at around 4mm as they wrongly believe it is safer.
“As a business we’ve invested hundreds of millions of Euros into R&D, to ensure our tyres deliver reliable performance right down to the last millimetre of legal tread. And crucially, it’s these final few millimetres which deliver the most fuel-efficient performance.
“Our advice is that once a tyre is worn to around 3-4mm of tread, it should be regrooved to unlock around 25% more tyre life. And then the regrooved tyre can be safely managed to a 1-2mm removal, bringing tangible savings on fuel and tyre costs.”
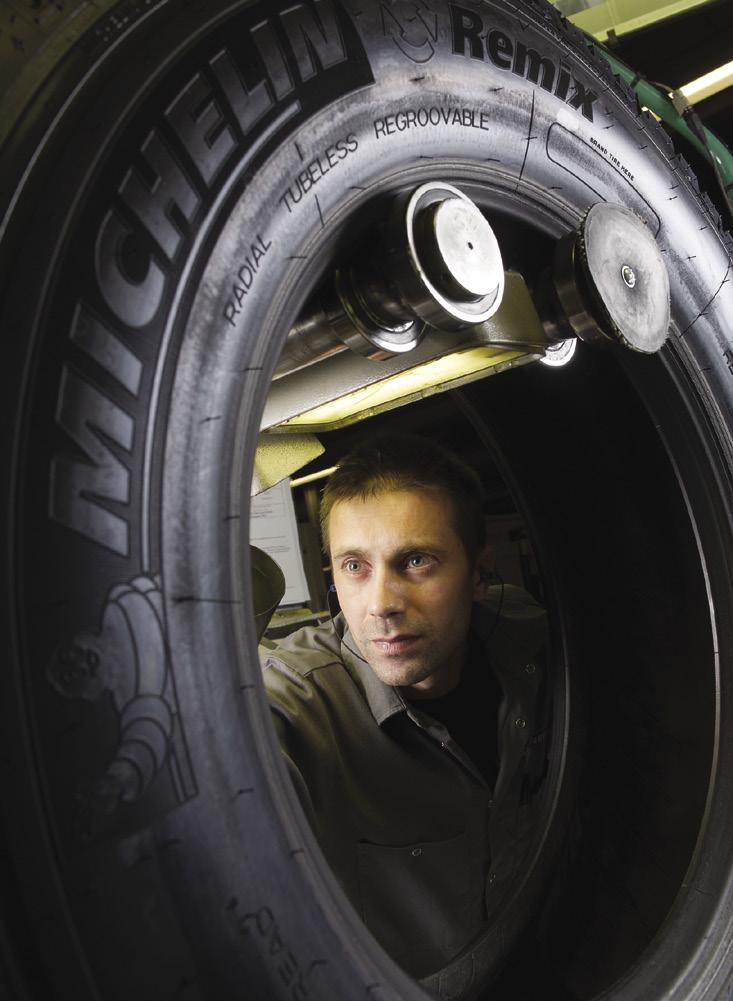
So does this mean every truck fleet should be retreading and regrooving its tyres?
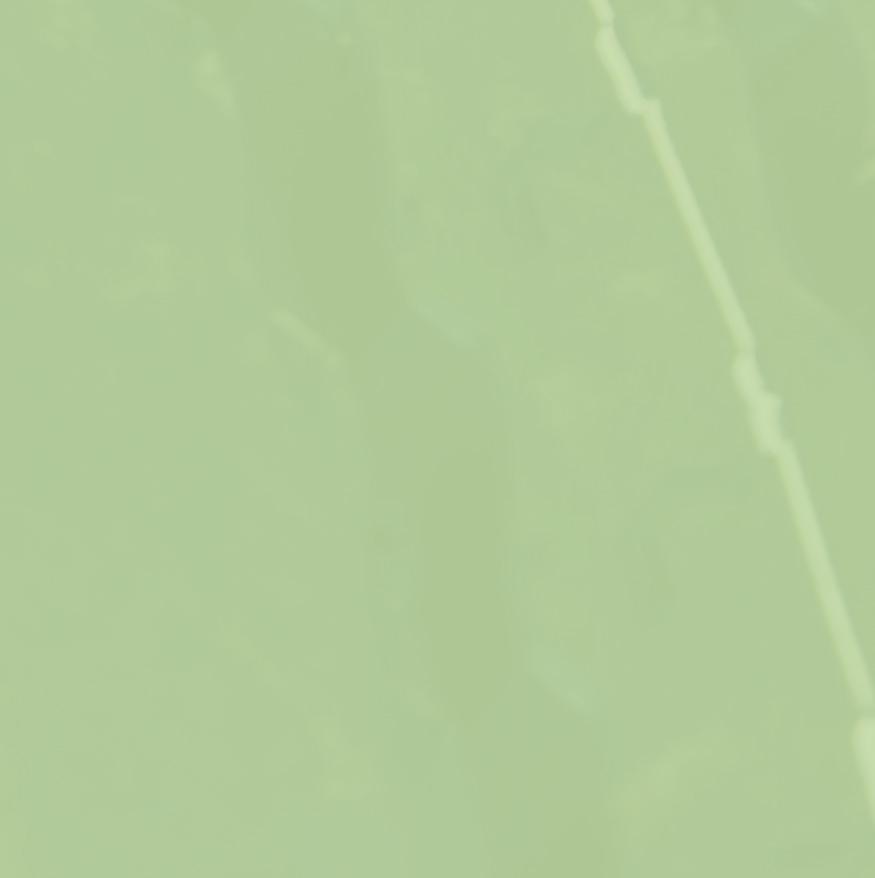
“The larger fleets are leading the way, but the fact remains there’s not a single haulage operation I can think of where we wouldn’t recommend fitting retreads,” adds Khan.
“Of course, it needs to be a quality retread where the casing is rigorously inspected and the manufacturing is to the same high standards as a new, premium tyre.”
Indeed, the only difference between using a new and a Remix tyre is that, in line with long-standing recommendations from the BRMA trade organisation, Michelin advises against the use of Remix tyres on the steer axle.
When Michelin defines a new tyre policy for a customer, it will typically prescribe new tyres for the steer axle, as they wear the fastest, and also for the rearmost trailer axle, as they endure the most lateral scrub.
“This strategy works well for most businesses. With Remix tyres you need a flow of product to feed your casing bank, so by fitting new tyres on the steer and rear trailer axle, you should always have a supply of Remix for your drive axles and first and second trailer axles. It’s the perfect way to make your tyre policy more efficient, and more sustainable.”