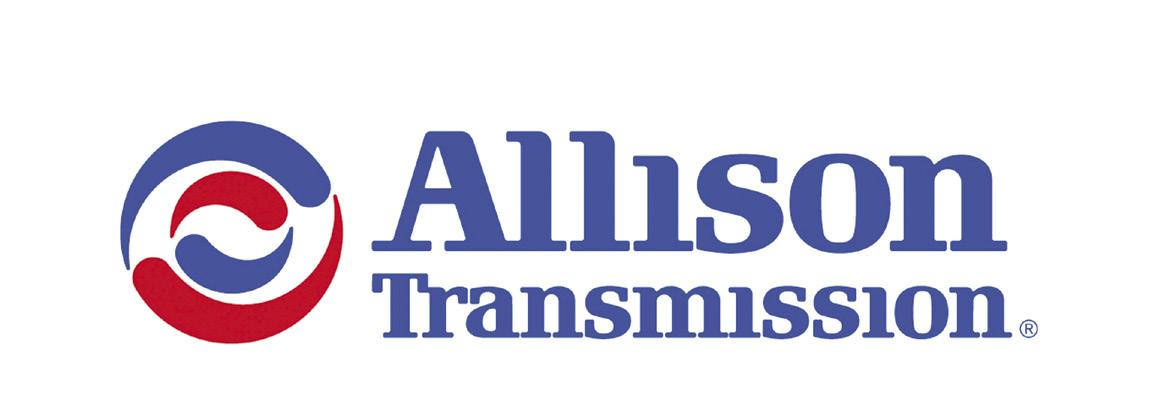
4 minute read
Allison Q&A
In very basic terms can you explain how E-axle technology works?
It re-imagines conventional truck powertrain layouts. Diesel trucks have an engine at the front, with a gearbox bolted to the back of it. A propshaft connects the gearbox to the drive-axle, which features a differential that turns the drive through 90 degrees while allowing the driven wheels to rotate at different speeds.
While e-Axles differ in their detailed layout from manufacturer to manufacturer, the key feature is that the motors, gearbox and drive-axle are contained in one, compact and integrated, assembly towards the rear of the chassis.
What is the main benefit of E-axle technology over a traditional BEV power train?
The first generation of electric trucks mostly followed the diesel layout of front-mounted engine and gearbox and rear drive-axle connected with a propshaft running almost the length of the chassis.
This legacy layout isn’t necessarily the most rational for an electric vehicle: electric motors are more compact and have simpler cooling needs than a diesel engine (there is no intercooler, for example) so they don’t need to be under the cab at the front of the vehicle.
Integrating a centrally mounted electric motor in-line and closer to the axle saves chassis-space. These are usually named central drive motors but still connect to the axle via a propshaft and require a conventional differential, both of which can be mechanical weak points in a conventional driveline. The Allison eGen Power e-Axle maximises chassis space even further by integrating the electric motor(s) directly inside the axle casing, removing the parasitic drag of 90-degree helical gears, and also allowing energy recovery by regenerative braking to be maximised without fear of differential damage.
Chassis space is at a premium on electric vehicles, whether battery or hydrogen fuel cell, and the chassis space liberated by installing an e-Axle can be put to good use in installing extra batteries or gas tanks. The absence of an engine ‘hump’ in the cab improves cross-cab access, particularly for crew-cabs, and simplifies the engineering of low-entry vulnerable-road-user-friendly cabs.
Are there any payloads benefits using an E-Axle?
Zero emission vehicles require different forms of energy storage systems and there will be many iterations in terms of how many tanks or batteries are offered in vehicles. An e-Axle will free up chassis space for additional storage, which will increase range. Therefore, one benefit could be payload and how that payload is used in terms of weight distribution.
What is the best operating environment for e-axle, e.g. urban, inner city etc?
There is no one ‘best’ environment or use for the Allison e-Axle. It’s ideal for any application requiring an emissions-free, compact and efficient driveline. It can handle tasks ranging from refuse collection to long-haul trucking. A variety of wheel-ends can be supplied: for disc or drum brakes, for instance; to suit the enduser’s preference and the design adapted to suit various suspension layouts.
One obvious application is in fire appliances. The e-Axle delivers maximum torque from cold and zero rpm, plus its compact design maximises space for equipment and watertanks. The Allison two-speed gearbox integrated into the design enables both outstanding acceleration and a high top-speed.
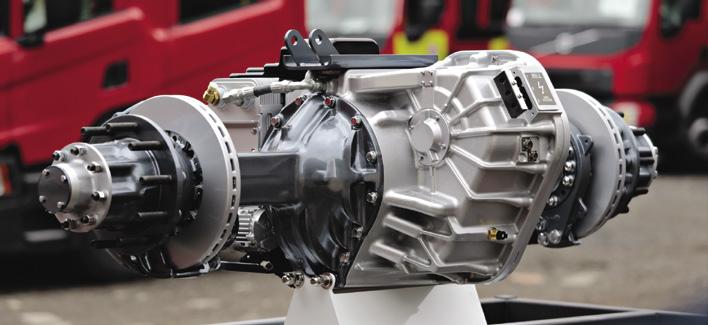
However, it would be a mistake to see the Allison e-Axle as a niche product. It’s very versatile and can undertake wide range of transport tasks with a great deal of efficiency.
What axle weights/GVW can your E-axle operate with?
The current eGen Power models include the single-motor 100S, with a 10,433 kg axle weight, and the dual-motor 130D and singlemotor 130S 13,000 kg axles specifically for European and Asia Pacific markets.

Additionally, the eGen Power 100D is best suited to trucks in the American Class 7 and Class 8 weight segments or where trucks have up to 36-tonnes GVW. It is rated for an axle weight of 10,433 kg.
What is the USP of your e-Axle?
Allison uses its vast experience in transmission technology in developing the eGen product line. For instance, we use the sixth-generation control hardware from our automatic transmissions on the eGen Power e-Axles. So, we already have a proven controller that’s produced in high volumes and can use our existing knowledge in developing control software for the eGen products.
We can also provide the confidence that comes from having a global technical support network already in place, with workshops well used to dealing with end-users in the field.
Can you mention which OEMs you are working with?
Allison has made many announcements with a variety of OEMs and applications. Additionally, there are multiple projects in place where Allison is working hand in hand with OEMs to meet customer needs related to full electrification.
How long has the system been under development, R&D, field test etc?
Allison has over 100 years of experience in the powertrain business and tapped into years of e-Axle technology development in 2019 when it took over the AxleTech electric vehicle systems division business. Since then, Allison has continued to validate and improve the design of its eGen Power family of e-Axles by reinforcing AxleTech’s advancements with Allison’s disciplined approach to product validation. All Allison products are extensively validated internally and externally to ensure the reliability and durability Allison is known for. Internally, Allison leverages considerable resources including testing in its Vehicle Electrification + Environmental Test Center, which opened in 2020 and features two environmental chambers capable of BEV and hydrogen fuel cell vehicle testing. Externally, all products are further validated via real-life testing in customer integrations and trials.
Where do you see battery technology moving over the next 5 years, chemistry, KWh, range?
It will evolve, that’s for sure. But our e-Axles are fuel agnostic. They will work with any suitable type or capacity of battery, or with a hydrogen fuel-cell power source, or indeed with an ICE range-extender charging the vehicle’s traction batteries in a hybrid truck. Our axles are an offthe-shelf solution to suit any power source, and pretty much any transport application.
Do you have any maximum power capacity?
Currently, our 130S heavy-duty product uses a single motor to generate 225 kW of continuous power, with a peak power of 325 kW, and 26,000 Nm of torque at the wheels. The dual-motor 130D produces a total of 450 kW continuous power, 650 kW of peak power and a maximum torque at the wheels of 47,000 Nm.