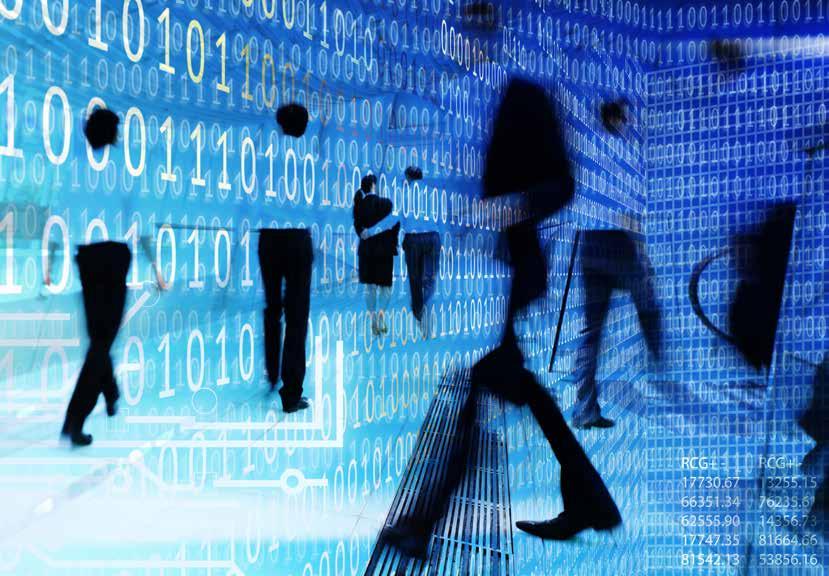
7 minute read
BRIDGING THE GAP BETWEEN PHYSICAL AND DIGITAL
from MARK OF EXCELLENCE
by cxoinsightme
HOW TO UNLOCK THE PROMISE OF DIGITAL TWINS
Adigital twin is a virtual replica of a physical system or process. Using sensors, digital twins gather realtime data from physical assets that can be used to run simulations, study performance issues, and improve products or processes. The rapid adoption of digital twins technology is reflected in the market numbers.
Advertisement
The research firm, MarketsandMarkets, says the global digital twin market was $3.1 billion in 2020 and is expected to reach $63.5 billion by 2027. According to the Global Market Trajectory and Analytics Report 2022 by Business Wire, the global digital twins market will reach $35.5 Billion by 2026 - growing by 36.9% over this period.
There are different definitions of digital twins, and the concept is not new. To put it simply, it’s a digital representation of a physical product and all its environment representing the entire life cycle of products, including the bidirectional links between the physical asset and its correspondence digital twin. Furthermore, it allows for simulation with actual real-time data instead of prototype.
“Digital twin is not limited to one industry or vertical it spans across all industries; the trend initially is embraced where the value is in assets and more complex systems. It’s designed to improve speed to market, reduce cost, improve performance, predict problems, and open new design capabilities by leveraging data coming from the field,” says Nidal Azba, Head of Solution for Middle East Africa and Turkey at Kyndryl. The digital twin concept is driving innovation and transforming the industries across verticals in terms of market trends. As a result, we are seeing increasing interest in digital twins solutions and that the market is investing, he adds.
Stephen Gill, Academic Head of the School of Mathematical and Computer Sciences, Heriot-Watt University
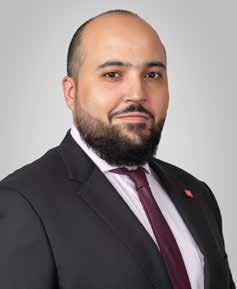
Khaled AlShami
Dubai, says digital twin technology is gaining significant attention due to its ability to support innovation and facilitate product development. “It is being embraced by several industries, including manufacturing, automobiles, aerospace, energy and power, oil and gas, and others. Digital twin technology is also increasingly adopted in the energy industry as it can expedite the transition towards renewable energy and net-zero emissions.”
The digital twins market is being shaped by advances in technology on the one hand and demand for more useful data on the other, says Khaled AlShami, vice president of solution consulting, MEA, Infor. “We are seeing fast-growing development of digital twin solutions because of the convergence of new technologies including 5G, Internet of Things, Edge, and Cloud. When integrated, these technologies give organisations all the key components they need to develop a digital twin of their operations, or aspects of their operations.”
What challenges do digital twins solve?
The key drivers for Digital twin technology are clearly in the areas of cost optimisation, increasing process efficiency and customer experience.
AlShami from Infor says the use of digital twins is becoming increasingly important in sectors including healthcare, manufacturing, and logistics. It makes interaction between machines and humans more understandable, helping users to visualise what is happening, take away key insights, and share insights with others, enabling collaboration.
“Digital Twin technology can be very beneficial for driving digital transformations, business model innovation, and operational optimisation,” says Vijay Jaswal, CTO, Middle East and Turkey, Software AG. “For example, a virtual digital representation of a supply chain can enhance the visibility that all stakeholders know exactly where a delivery is, which route it has taken, and when it will arrive at its destination.”
Digital twin technology can help avoid potential issues in product development by means of receiving input from sensors. The sensors gather the physical product data and simulate the object in real-time, providing valuable insights into performance and potential problems.
“Digital twin capabilities can eliminate many aspects of prototype testing using 3D simulations, augmented reality (AR) and virtual reality (VR), allowing for better streamlining of the design process. For example, engineers can identify potential quality and manufacturing issues even before finalising the designs. This saves costs as prototyping is accelerated and production is done more efficiently with real-time data, “ says Gill.
He adds another way that digital twins can resolve issues is through predictive maintenance. Digital twins can help identify malfunctions even before they happen. Sensors embedded in machines feed performance data into the digital twin in real-time. This helps to tailor service and maintenance plans, enhance worker safety, reduce the risk of accidents and lower maintenance costs. Examples include
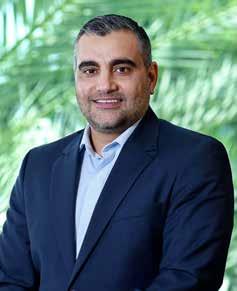
Mehmood Khan
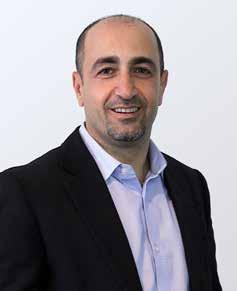
Nidal Azba

Stephen Gill
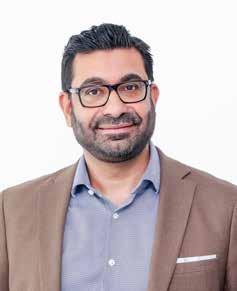
Vijay Jaswal
pumps, engines, power plants, and manufacturing lines.
The possibilities of solving problems are endless, says Azba from Kyndryl. “Engineers can leverage the digital twin to inspect the state of the real-world object, and to me, this is extremely valuable. As a result, you can imagine the number of problems that can be solved. The connection between physical and virtual drives instantaneous perspective of manufacturing combined with AI and machine learning will deliver optimum performance and use of resources to provide the right solution at the right time.” THE MANUFACTURING INDUSTRY CONTINUES INVESTING IN RESEARCH AND DESIGN TO EXPAND THE TRADITIONAL SIMULATION TO A DIGITAL TWIN MODEL LEVERAGING THE RAPID ADAPTION OF 3D PRINTING TECHNOLOGY, WHICH BROUGHT REVOLUTIONARY CHANGES TO THE INDUSTRY.
What is the difference between simulations and digital twins?
While a simulation replicates what could happen to a product, a digital twin provides real-time data by replicating what is happening to an actual product in the real world. Simulations can be used to analyse the shortest distance between workstations or the impact of having more storage facilities.
“A digital twin, however, can recreate digital representations of existing shop floors and can run multiple simulations. The regular transfer of information between a digital twin and its corresponding physical environment makes real-time simulation possible. This can help improve multiple aspects in operations from staff training, customer service to scheduling and more,” says Gill from Heriot-Watt University.
In terms of product design, while advanced simulations can analyse thousands of variables, digital twin technology can do more. For example, Boeing integrated digital twin technology in aircraft design and production to analyse how diverse materials will fare throughout the aircraft’s life cycle. As a result, Boeing achieved a 40% improvement in the quality of certain parts it designed - as quoted in Aviation Today. Additionally, Tesla uses digital twin technology for each vehicle to optimise design, predictive maintenance, and enhance self-driving initiatives.
New use cases
The manufacturing industry continues investing in research and design to expand the traditional simulation to a digital twin model leveraging the rapid adaption of 3D printing technology, which brought revolutionary changes to the industry. 3D vendors are collaborating and integrating their capabilities with digital twin technology using a software solution to reduce production cost and eliminate the need for multiple physical prototypes using sensor. Internet of things (IOT) technology, the availability of increased bandwidth, compute power and storage are also enabling such solutions.
“We see an increasing demand in healthcare and pharmaceutical industries. The FDA, for example, is working with researchers to develop digital twins of drugs to improve medical product safety. The FDA is also actively working with Siemens to demo drug production with a digital factory line,” says Azba.
Mehmood Khan, IFS Managing Director, Middle East, says it’s less about new use cases and more about the increased scope that comes through data interoperability and the potential to link digital twins together. Simulations can now cover broader processes than just a single asset, such as an entire supply chain.
“The fact that so many machines are now connected through IIoT means a much richer source of data for modeling as well. In manufacturing for example, any individual machine may be relatively simplistic and in the past may not have warranted a digital twin in its own right, but in the aggregate, those machines provide crucial information for monitoring and optimising entire production plans,” he concludes.