
12 minute read
WHY YOU NEED A SMART VENDOR STRATEGY
WHY YOU NEED A SMART VENDOR STRATEGY
FINDING THE RIGHT VENDOR IS KEY TO DIGITAL TRANSFORMATION SUCCESS IN IT AND TELECOMS, SAYS ANTONY BOURNE, SENIOR VICE PRESIDENT, INDUSTRIES AND PRODUCT MARKETING AT IFS
Advertisement
Firms in the IT and telecommunications sectors often deliver services that are at the forefront of technology to their customers and clients. Many of these services will rely on complex and evolving technologies like artificial intelligence, machine learning and virtual reality. It would not seem unreasonable to expect such firms to be highly attuned to the value that digital tools can provide in everyday work.
We recently carried out a survey examining firms’ experience of digital transformation across a range of sectors including IT and telecommunications. We also looked at construction, healthcare, energy and utilities, travel and transport, and manufacturing, and we focused on the
US, UK, France, Germany, the Nordics and
Australia. What we learned threw up some interesting questions for any organisation contemplating a digital transformation project, and interestingly we found that the
IT and telecommunications sector is not that different from the others in terms of its experience.
The price of failure
When a firm enters into a digital transformation project, it has a set of expectations that include time to completion, anticipated return on investment, and some clear understanding of how the project will be implemented and how staff and stakeholders will be involved.
In our survey we found that 74% of firms in IT and telecommunications that had engaged in past digital transformation projects felt that they had completed on time, 50% had delivered on budget, and 49% had delivered real results and a return on investment.
Of those firms in the sector that experienced project failure, 45% felt it took between 1 to 2 years to fully recover from the impacts on the business. Globally across all sectors we learned that among companies that experienced timeline overruns there were serious consequences for the business. 40% said budgets were cut in other areas, 35% said other projects were stopped, 32% said headcount was frozen and 31% said it deterred investment in similar projects. For 22% there were job losses.
This is concerning. No vendor of digital transformation solutions should be content to its projects fail to meet expectations, nor any of the other consequences that businesses can suffer as a result. We were keen to understand where the problems might lie.
Why projects go wrong
Something that came out of our research very loud and clear is that the vendor has a critical role to play in ensuring project success. Accepting that it is hardly likely that clients would give themselves a poor rating for project management, we were still intrigued to see that 37% in our survey said poor advice from vendors was a reason for project failure. This topped the list of reasons which also included stakeholders losing confidence in the project (36%), the technology used being outdated (32%), employees not being engaged in the project (30%), running out of budget (30%), and poor change management (19%).
When we drilled into the IT and telecommunications sector we found that the most frequently cited reason for project failure was poor advice from vendors (42%), followed by stakeholders losing confidence in the project (41%), and the use of outdated technology (40%).
We can’t, of course, comment on every single experience, but it seems very clear to us that some of what is presenting here is a result of a lack of cultural fit between client and vendor. For example, what is identified as poor advice from the vendor might be the result of inefficient communications.
Made to measure, not off the rail
Just 38% in the IT and telecommunications sector told us that successful transformation involved engaged and productive stakeholders, a rather low figure, though only one other scored more highly - fast on time delivery at 39%. We also found that 34% in the sector told us that having ethics than align with the business would help them trust vendors more.
This points us towards what seems to be the critical factor. The fit between vendor and client must be based on shared ethics, strong communication and trust. Finding the right vendor should involve seeing how they measure up on the first two of those qualities, and from this the third should flow. One factor that can stand in the way of this style of selection is if vendors are chosen by boards on the basis of being widely known names. Another is selection on the basis of cost alone.
In the end, what we are talking about here is forming a partnership in which both vendor and client share the same definition of a good outcome, the same understandings of the strategies that will get that outcome, and, vitally, the same ethic around open, ongoing, communication with people at all levels of the client organisation.
Our survey found that even in the current economic climate 59% of respondents from the IT and telecommunications sector have plans in place to spend more on digital transformation. We’re hopeful that recognition of the importance of shared ethics, trust and communication will help firms in the sector get the outcomes they desire from digital transformation.
CREATING VALUE WITH INDUSTRIAL DATA ANALYTICS
ELLIOTT MIDDLETON, DIRECTOR OF PRODUCT MANAGEMENT, AVEVA, SETS OUT SEVEN STEPS TO DATADRIVEN DECISION MAKING
There is a lot of buzz surrounding industrial analytics, artificial intelligence (AI) and machine learning (ML). However, companies are not limited to taking large and costly decisions when it comes to exploring the possibilities. There are smaller, incremental steps that may be taken along the journey of digital transformation.
Until recently, more mature process industries have pursued AI and ML initiatives, while others are only using some basic levels of automation. The unrelenting pressure to keep production lines moving, especially at a time when businesses are responding to changes driven by the Covid-19 crisis, means there is little time or headspace to consider implementing new technology. Automating the collection of sensor data, spotting problems and patterns can result in faster troubleshooting and major process improvement for all sizes of operation. It is possible to start with small incremental steps that add immediate value.
The journey to adding value through data analytics
Here are seven steps to generating incremental value with industrial analytics and ML:
1. Automate data collection from
sensors. This is a critical prerequisite. An infrastructure for automated data collection requires multiple sensors to feed through the data that is needed for meaningful analysis.
2. Record measurements from the
sensors over time. The challenge for many organisations is collecting the data and making sure that data is captured throughout the process so that the workforce has the option to draw some useful inferences at a later stage. You may not have an immediately obvious use case but if you start collecting all the data, additional insights are likely to arise.
3. Accelerate
Diagnostics: Once you have collected the data, diagnostics can greatly reduce the time required to pinpoint and correct operational problems—and lead you to make process changes that prevent them from happening again in the future.
4. Make the Data More Accessible:
As the key efficiency metrics are better understood, it is important to make them readily available to a broader group within the operational staff, so they can independently monitor and react to potential problems earlier. Many sites use a large screen display showing a dashboard of live metrics or an automated email report. Others take it a step further and deliver alerts to mobile devices.
5. Add alarm history to the process history to give more context and
significance to the data. Traditionally, data historians just record sensor values, they don’t record the alarm state. But combining sensor and alarm data makes it easier to understand the potential impacts on quality, safety, cost or the environment. 6. Add Operational Context: In some applications, differences in recipes, equipment, or personnel can further complicate identifying root causes or improvement opportunities: was the yield lower because it is a different product, operator, or production line? By including information about this kind of operational context, you can begin to consider these other factors in your analysis. 7. Add machine learning: Making this detailed information available to people has tremendous value, but it still requires them to actually spend time looking at it. Although it can’t do everything, in many cases, you can automate that analysis process so that it is continuously analyzed. Some systems have unsupervised machine learning (ML) capabilities: simply provide the data and the system will look for and report anomalies. This style of ML has the significant advantage of simplicity: no expertise required. Other applications warrant investment in process and technology expertise to add supervised ML, commonly as early failure predictions. 8. Compare like for like: Building on process analytics successes at individual sites, many organisations advance to analysis and comparison across their fleet. The more homogeneous the sites, the more direct the comparisons can be, but few industries actually have “cookie cutter” plants. So, before making these comparisons, there must be some effort to normalise information—whether that is standardising on “m3/day” vs. “liter/ minute” or agreeing on how to calculate Overall Equipment Efficiency (OEE). In global businesses, with multiple operations and multiple sites, being able to do peer to peer comparison – in a standardised manner - is a real value add. Previously, this would have been a task of overwhelming complexity and cost for smaller businesses. Now, with the cloud, this type of comparison is much more accessible and achievable.
Eating the elephant
Tackling sensor data analytics automation can feel overwhelming, but there is no need to eat the elephant in one sitting. It is quite possible to take single, exploratory steps on this journey as the need arises and the budget is available. You might stop for a while, having implemented one step, and see how it works out for you. Most of the incremental steps can be self-service and don’t need external expertise.
The journey to getting value from applying AI and ML to sensor data starts with a single step. As the benefits start to accrue, cost savings will mount and productivity will rise, demonstrating clear business value from intelligent sensor data analytics. It will become a no-brainer to progress further along the route to optimum data-driven decision making.
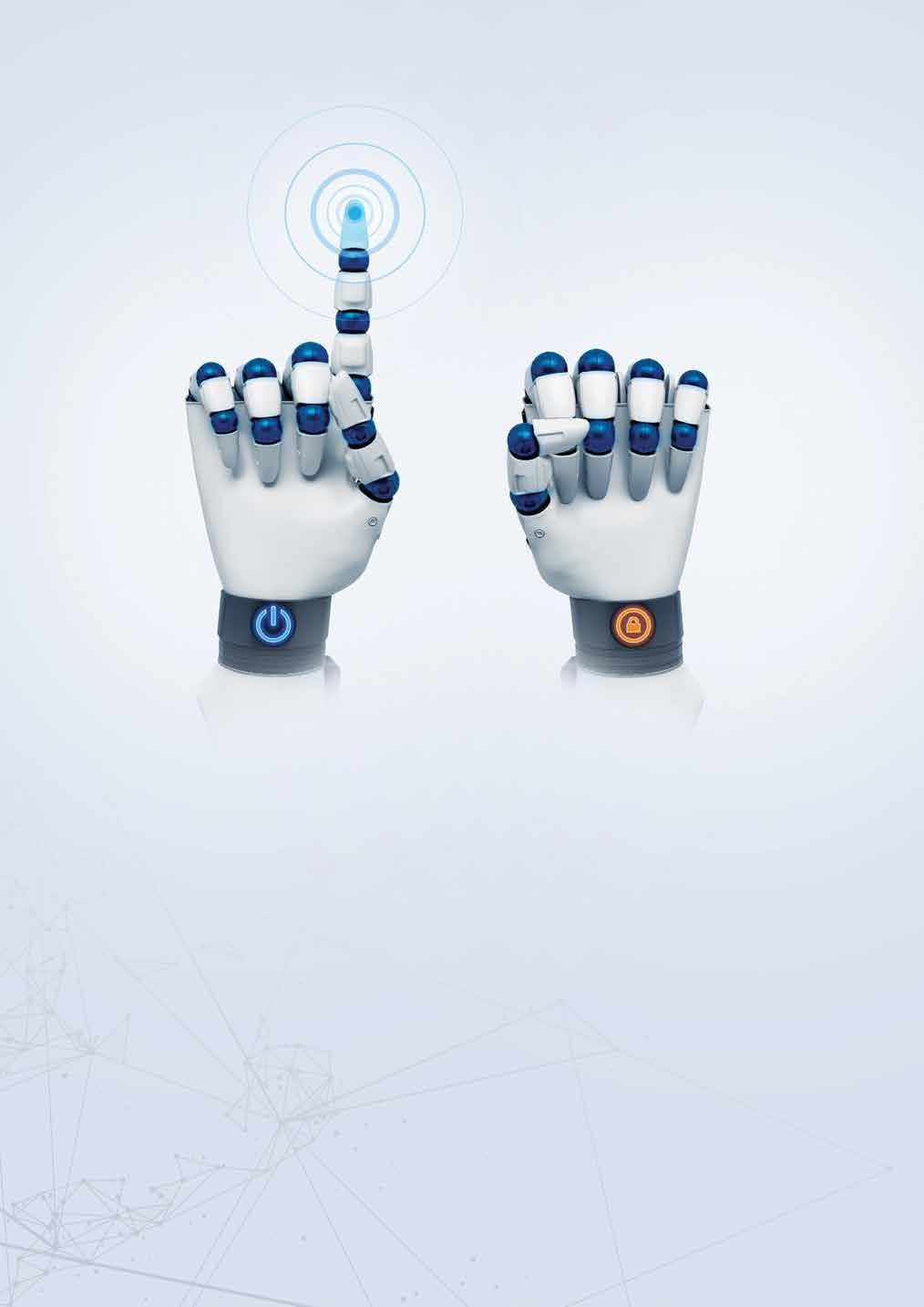
GETTING DATA RIGHT
DARRAGH FEGAN, GULF AND SAUDI SENIOR MARKETING MANAGER AT VERITAS, TALKS ABOUT WHY AN EFFECTIVE DATA MANAGEMENT AND PROTECTION STRATEGY IS MORE IMPORTANT THAN EVER NOW.
How can CIOs master the complexity of multi-cloud environments?
Once an organisation has decided to migrate data and applications to the cloud, understanding what data you have and where it lives inside your infrastructure is the first step. Having this visibility will greatly assist in any migration.
Whether organisations are moving one cluster of applications or an entire data centre, another consideration is speed and uptime. Applications aren’t built for modern portability, and the complexity and dispersed nature of the underlying infrastructure can pose potential problems. Ensuring availability and avoiding downtime is critical.
After a successful migration, it’s time to make the most of your new environment.
However, there are always risks. It is an organisations own responsibility to protect their data in the cloud and not the cloud providers. Protecting and recovering data from a single interface is of paramount importance.
Finally, while the original end goal may now be complete, an organisation’s cloud journey is just the beginning. Regardless of what they have already accomplished, there will always be the “next” project.
The environment should support the current and future projects allowing one to ideate and move into future projects with ease. Doing so means having an open setup with workload portability so you can easily migrate, move on and adopt the next greatest thing.
How has backup and recovery planning changed during the pandemic?
Organisation have higher expectations of the brands they do business with during challenging times. These include solutions they can trust, a brand purpose that aligns to their values, and an experience that is second to none. As part of a digital transformation strategy, organisations look for single platforms they can trust and that do more for them rather than multiple point products that do less. Digital transformation, and especially cloud adoption, has accelerated due to the global pandemic.
The newly published Veritas 2020 Ransomware Resilience study determined that as this shift accelerates, resiliency planning has not kept pace, creating a significant resiliency gap. There are several reasons, but the key one, is that while enterprises have found the cloud to be an easy-to-adopt platform for running applications and information storage, they’ve found it much more difficult to implement a platform for resiliency. There is an urgent need for enterprises to close this resiliency gap by accelerating their resiliency planning to keep pace with today’s speed and increasing complexity of IT.
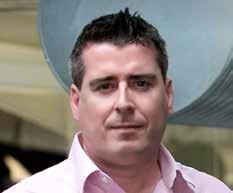
What are some of the key steps enterprise must take to protect against ransomware attacks?
Ransomware attacks are an increasingly prevalent threat. It is imperative for enterprises to focus more on recovery while simultaneously mitigating threats preemptively. As we see daily, despite measure in place to prevent malware, ransomware can strike anywhere an organisations data lives, and this includes the cloud. If an attack is successful and the backup and recovery systems aren’t robust enough often there is no choice but to pay the ransom in the hope of getting the data back.
The Veritas 2020 Ransomware Resilience study showed an astonishing 42% of IT leaders said their companies had suffered ransomware attacks. Worryingly, two-thirds of respondents said it would take longer than five days to fully recover. Veritas recommends that enterprises should consider adopting more robust methods of ransomware attack mitigation. These include: Enterprises should review their resiliency strategy to ensure that it is predictable and based on real-time visibility, monitoring and recovery automation; companies should follow a “3-2-1” backup approach: a minimum of three copies of their data, in two disparate locations, with at least one offsite; ideally, enterprises should test their DR plan once per month; and IT teams should stay current with security patches and new releases with security updates.
It is also important that enterprises should implement in-transit encryption to protect data from being compromised on the network, and IT teams should use immutable and indelible storage technology to prevent ransomware from encrypting or deleting backups. We recommend implementing role-based access control and limit access to only required functionality for individuals and personas.
What are the key data storage trends to watch out for in 2021?
As mentioned, the shift to cloud has accelerated and this will continue into 2021. Another trend is 5G being adopted. We will experience data transfer speeds ten times faster than 4G. This will result in more AI, internet of things, robotics, AR all being transformed for mass consumption. The inevitable result will be exponential data growth requiring more storage and a greater need to manage and protect this data.