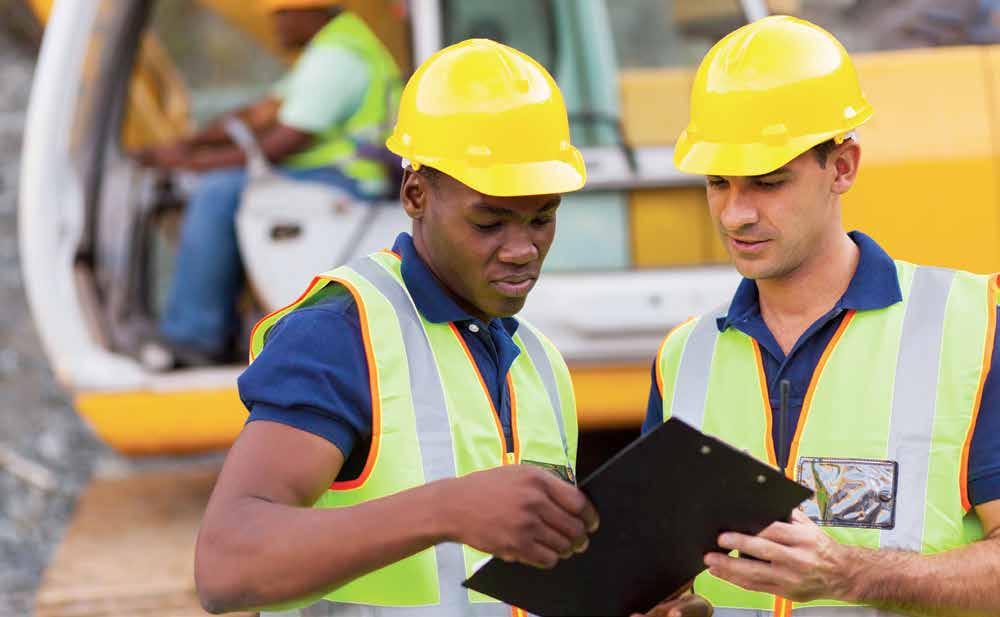
4 minute read
CAMPAIGN LAUNCHED TO EDUCATE MIDWEST EMPLOYERS AND WORKERS ON EXCAVATION SAFETY
By Subcontractors USA News Provider
Thirty-nine people died doing trench or excavation work in the U.S. in 2022 – four in Illinois and two others in Ohio. In fact, the number of worker fatalities more than doubled since 2021, continuing a troubling trend cited by the Bureau of Labor Statistics that found 166 workers died in trench cave-ins from 2011-2018, an average of 21 each year.
To address injuries and fatalities in the industry, the U.S. Department of Labor's Occupational Safety and Health Administration is launching an outreach campaign in its Midwest region today to work directly with employers, workers, state agencies and industry associations to reduce and prevent serious injuries and fatalities suffered by workers in one of the nation's most hazardous industries.
By launching this trench and excavation safety campaign as the spring construction season gets into full swing, OSHA and its partners are determined to make sure industry workers finish their daily shifts safely,
Donovan added.
In 2022, OSHA conducted 311 trenching and excavation inspections at sites in Illinois, Ohio and Wisconsin. Six of the inspections followed incidents in which workers suffered fatalities after falling into a trench, being pinned between equipment, trapped by a cave-in, or asphyxiated by naturally occurring, hazardous gases in the trench. Industry employers and workers should remember the following essential trench safety standards: explained OSHA Regional Administrator Bill Donovan in Chicago. "With proper training and use of required safety procedures, incidents like these can be prevented. OSHA and industry employers are working hard to raise awareness of hazards and protective measures and educate employers on how they must protect workers."
Protective systems must be in place for trenches 5-feet deep or deeper. These systems include benching, sloping, shoring, and shielding.
The new campaign is a collaboration between OSHA and on-site consultation projects across OSHA Region 5 including: Illinois On-site Consultation Program, Indiana Occupational Safety and Health Administration and INSafe: Safety and Health Consultation; Michigan Occupational Safety and Health Administration and Michigan Consultative Services; Minnesota Occupational Safety and Health Administration and Minnesota Workplace Safety Consultation Program; Ohio Bureau of Workers' Compensation On-Site Consultation Program; Wisconsin On-Site Consultation Program, as well as trenching and excavation industry employers and other stakeholders such as the National Utility Contractors Association, Wisconsin Utility Contractors Association.
A registered professional engineer must approve trenches of 20-feet deep or deeper. A competent person must inspect trenches daily – and as conditions change – before anyone enters a trench. The competent person must be able to identify existing and predictable hazards, soil types and protective systems, and have authority to take prompt corrective action to eliminate those hazards.
Excavated soil must be kept at least two feet from trench edges.
Underground utilities must be located and marked before digging begins. Ladders must be positioned every 25 feet of lateral travel for safe entrance and exit from the trench.
OSHA has a national emphasis program on preventing trenching and excavation collapses and developed a series of compliance assistance resources in English and Spanish to help keep workers safe from these hazards.
OSHA's trenching and excavation webpage provides additional information on trenching hazards and solutions. including a safety video and safety alert.
OSHA participates in the National Utility Contractors Association Trench Safety Month each June.
Source: osha.gov
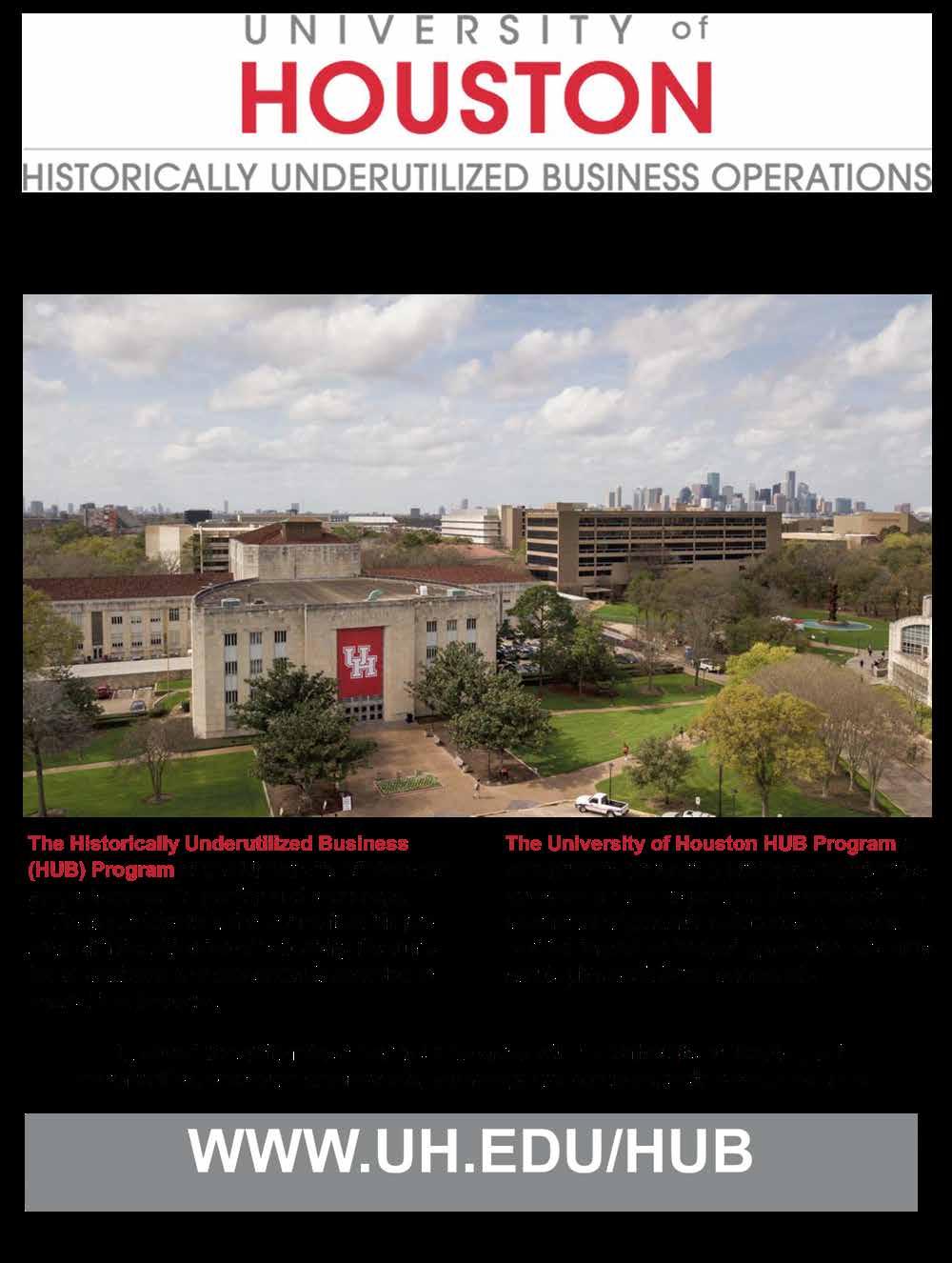
NAVIGATING FORT WORTH PERMITTING: 3 THINGS CONTRACTORS MUST KNOW
process and the city's requirements before applying.
Working with a permit expediter like Permit Us Now can help streamline the process and ensure that all necessary documentation is submitted correctly and on time. A permit expediter can also help you navigate the city's regulations and requirements, ensuring that your application is compliant, and your project is approved as quickly as possible.
Fort Worth Has Strict Building Codes
Fort Worth has strict building codes that must be followed when constructing or renovating a building. These codes cover everything from the height and placement of the building to the materials used in construction. Failure to comply with these codes can lead to permit denials, delays, or fines.
As a contractor, you must familiarize yourself with these codes and ensure your plans comply before submitting your application. Working with a permit expediter can help ensure that your plans meet all the city's codes and regulations, avoiding costly mistakes and ensuring your permits are approved on time.
Permit Fees Can Be Costly
By Helen Callier Contributing Writer
We’re excited about pulling building permits for Architects, Contractors, and Project Owners across the state of Texas. And to support our clients and the industry, we are kicking off a 6-part series to assist contractors with upcoming projects in Fort Worth, Texas.
Here’s what we know, if you're a contractor in Fort Worth, pulling permits is an essential part of the construction process. However, navigating the permitting process can be complicated and time-consuming, and mistakes can lead to costly delays. Below are three things’ contractors should know before pulling permits in the City of Fort Worth.
The Permitting Process Can Be Complicated
The permitting process in Fort Worth can be complex and time-consuming, with a lot of paperwork and regulations to navigate. Each permit has its own set of requirements and may require multiple inspections. It's essential to familiarize yourself with the
The fees associated with pulling permits in Fort Worth can be a significant cost for contractors. These fees can vary depending on the type of permit and the size and scope of the project. It's important to factor these fees into your project budget and ensure they are paid on time to avoid delays or fines.
Working with a permit expediter can help ensure that you are aware of all the fees associated with your project and that they are paid on time. A permit expediter can also help you navigate the city's fee structure and ensure you are not overcharged.
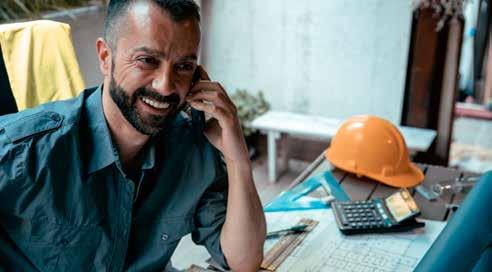
In Conclusion
In summary, pulling permits in Fort Worth is a necessary but complex process that requires a lot of paperwork and adherence to strict regulations. However, working with a permit expediter can help simplify the process and ensure your project is approved without delay.
At PermitUsNow, we are committed to pulling permits for our architect, contractor, and project owner clients without delay, eliminating their frustrations with the permitting process. Plus, we make it easy for you to work with us.: 1) Email us your plans, 2) Follow up on our feedback for any missing items, and 3) Let us get your permitting done for you. So, send us your plans today, and we will free your time to focus on doing what you love—building your customers' dreams. Call 1.844. PERMIT.4 to get started! #BuildSafe

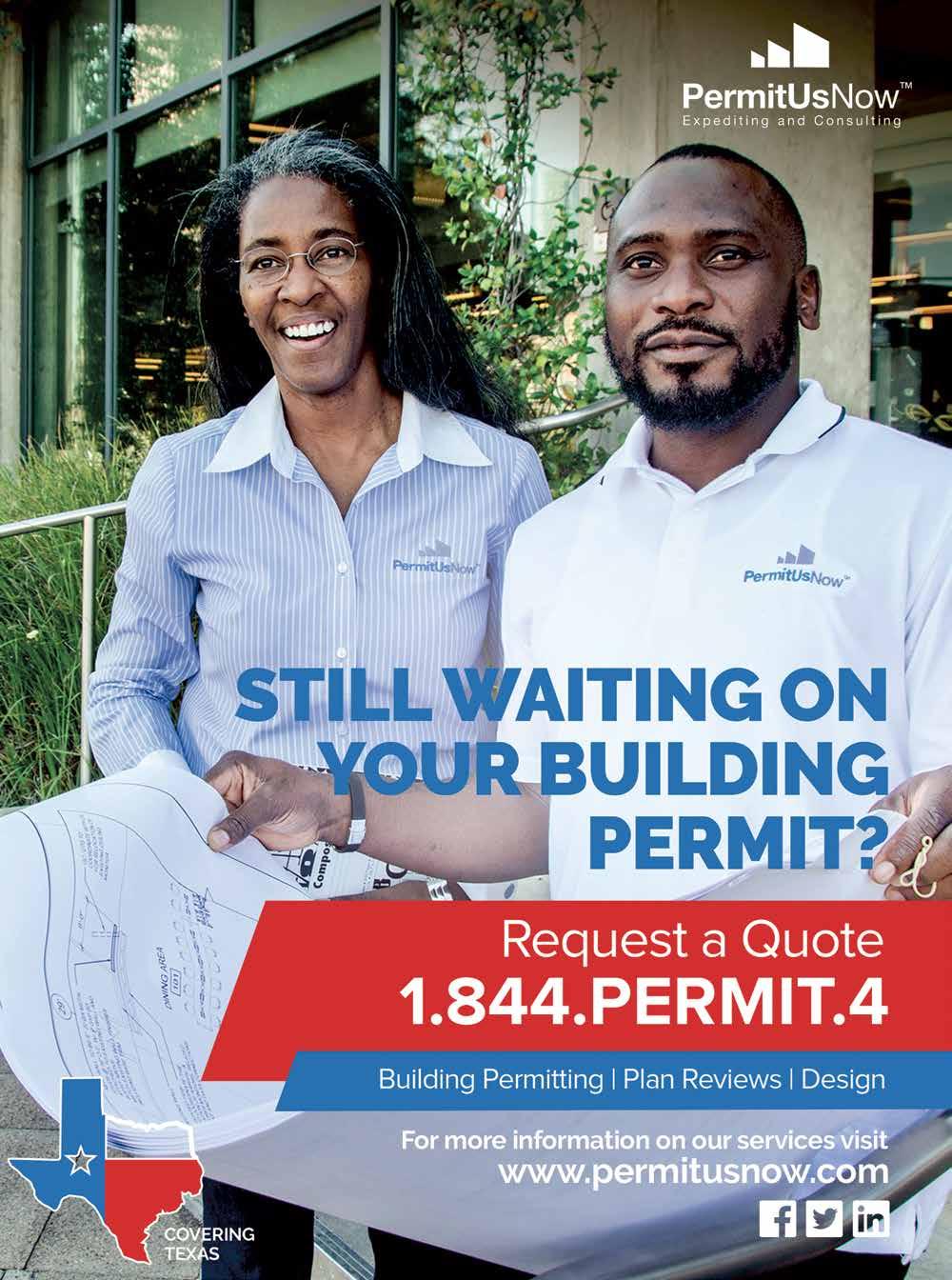